
- •Contents
- •Preface
- •1. Main dimensions and main ratios
- •1.3 Depth, draught and freeboard
- •1.7 The design equation
- •1.8 References
- •2. Lines design
- •2.1 Statement of the problem
- •2.2 Shape of sectional area curve
- •2.3 Bow and forward section forms
- •2.4 Bulbous bow
- •2.5 Stern forms
- •2.6 Conventional propeller arrangement
- •2.7 Problems of design in broad, shallow-draught ships
- •2.8 Propeller clearances
- •2.9 The conventional method of lines design
- •2.10 Lines design using distortion of existing forms
- •2.12 References
- •3. Optimization in design
- •3.1 Introduction to methodology of optimization
- •3.2 Scope of application in ship design
- •3.3 Economic basics for optimization
- •3.4 Discussion of some important parameters
- •3.5 Special cases of optimization
- •3.6 Developments of the 1980s and 1990s
- •3.7 References
- •4. Some unconventional propulsion arrangements
- •4.1 Rudder propeller
- •4.2 Overlapping propellers
- •4.3 Contra-rotating propellers
- •4.4 Controllable-pitch propellers
- •4.5 Kort nozzles
- •4.6 Further devices to improve propulsion
- •4.7 References
- •5. Computation of weights and centres of mass
- •5.1 Steel weight
- •5.3 Weight of engine plant
- •5.4 Weight margin
- •5.5 References
- •6. Ship propulsion
- •6.1 Interaction between ship and propeller
- •6.2 Power prognosis using the admiralty formula
- •6.3 Ship resistance under trial conditions
- •6.4 Additional resistance under service conditions
- •6.5 References
- •Appendix
- •A.1 Stability regulations
- •References
- •Nomenclature
- •Index
52 Ship Design for Efficiency and Economy
for the ship without bulbous bow, are disregarded for the time being. If the freeboard is not limiting, there is greater freedom in optimization:
1.A proposed bulbous bow ship can be compared with a ship with normal bow and the normal bow lengthened until power equivalence is achieved. This shows immediately which alternative is more costly in terms of steel. All other cost components remain unchanged.
2.The propulsion power can be compared to that for a normal bow with the equivalent amount of steel.
In both cases the differences in production costs and in the ship's characteristics can be estimated with reasonable precision, thus providing a basis for choice. Throughout, only ships with bulbs projecting forward of the perpendicular and ships with normal bulbless bows have been compared. If a comparative study produces an equivalence of production costs or power, then the ship without bulbs will suffer smaller operational losses in a seaway (depending on the type of bulb used in the comparative design) and possess better partial loading characteristics. A more extensive study would also examine non-projecting bulbous bows. The savings in power resulting from these can be estimated more precisely, and are within a narrower range.
2.5 Stern forms
The following criteria govern the choice of stern form:
1.Low resistance.
2.High propulsion efficiency.
(a)Uniform inflow of water to propeller.
(b)Good relationship of thrust deduction to wake (hull efficiency H).
3.Avoiding vibrations.
Development of stern for cargo ships
In discussing stern forms, a distinction must be made between the form characteristics of the topside and those of the underwater part of the vessel. The topside of the cargo ship has developed in the following stages (Fig. 2.22):
1.The merchant or elliptical stern.
2.The cruiser stern.
3.The transom stern.
In addition there are numerous special forms.
The elliptical stern
Before about 1930, the `merchant stern', also known as elliptical or `counter' stern, was the conventional form for cargo ships. Viewed from above, the deck line and the knuckle line were roughly elliptical in shape. The length between the perpendiculars of the merchant stern is identical with the length of the waterplane. The stern is still immediately vertical above the CWL, then flares sharply outwards and is knuckled close to the upper deck. A somewhat modified form of the merchant stern is the `tug stern', where the flaring at the upper
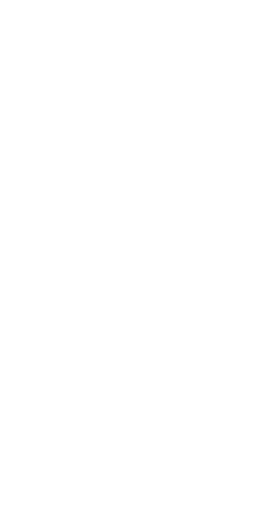
Lines design 53
Figure 2.22 Stern contours on cargo ships. Elliptical, cruiser stern (1) and transom stern (2)
part of the stern is even more pronounced (Fig. 2.23). The knuckle occurs at the height of the upper deck. The bulwark above it inclines inwards. This form was still used on tugs and harbour motor launches after World War II.
Figure 2.23 Tug stern
Cruiser stern
The cruiser stern emerged in the latter half of the nineteenth century in warships, and was initially designed only to lower the steering gear below the armour deck, located at approximately the height of the CWL. The knuckle above the CWL disappeared. The cruiser stern had better resistance characteristics than the merchant stern and consequently found widespread application on cargo ships. The length of the waterplane with a cruiser stern is greater than Lpp. The transition from merchant stern to cruiser stern on cargo ships took place between the world wars. The counter, situated lower than on the merchant stern, can be used to reduce resistance chiefly on twin-screw and single-screw vessels with small propeller diameters.

54 Ship Design for Efficiency and Economy
Transom stern
The term transom stern can be understood both as a further development of the cruiser stern and as an independent development of a stern for fast ships. The further development of the cruiser stern is effected by `cutting off' its aft-most portion. The flat stern then begins at approximately the height of the CWL. This form was introduced merely to simplify construction. The transom stern for fast ships should aim at reducing resistance through:
1.The effect of virtual lengthening of the ship.
2.The possibility this creates of countering stern trim.
The trim can be influenced most effectively by using stern wedges (Fig. 2.24). The stern wedge gives the flow separation a downward component, thereby decreasing the height of the wave forming behind the ship and diminishing the loss of energy. The stern wedge can be faired into the stern form. As a result of the stern wedge influencing the trim, the bow is pressed deeper into the water at high speeds, and this may have a negative effect on seakeeping ability.
Figure 2.24 Transom stern with stern wedge
Recommendations for transom stern design
Fn < 0:3 Fn 0:3 Fn 0:5
Stern above CWL. Some stern submergence during operation.
Small sternÐonly slightly below CWL.
Deeper submerging stern with average wedge.
Submergence t D 10±15%T:
Fn > 0:5 Deep submerging stern with wedge having approximately width of ship:
Submergence t D 15±20%T:
Further with regard to the deeply submerged square stern:
1.The edges must be sharp. The flow should separate cleanly.
2.Ideally, the stability rather than the width should be kept constant when optimizing the stern. However, this does not happen in practice. The ship can be made narrower with a transom stern than without one.

Lines design 55
3.The stern, and in particular its underside, influences the propulsion efficiency. There is less turbulence in the area between propeller and outer shell above the propeller.
4.Slamming rarely occurs. In operation, the flowlines largely follow the ship's form.
5.During slow operation, strong vortices form behind the transom, causing it to become wet. The resistance in slow-speed operation is noticeably higher than that of the same ship with cruiser stern.
6.The centre of pitching is situated at roughly one-quarter of the ship's length from aft as opposed to one-third of the length from aft on normal vessels. The forward section gets wetter in heavy seas.
7.The deck on transom stern ships can easily get wet during reversing operations and in a heavy sea. The water is `dammed up'. Flare and knuckle deflect the water better during astern operations avoiding deck flooding (Fig. 2.25).
Figure 2.25 Transom stern with flared profiles
The reduction in power compared with the cruiser increases with the Froude number. Order of magnitude: approx. 10% at Fn D 0:5. This reduction in power is less due to reducing the resistance than to improving the propulsive efficiency.
Advice on designing the stern underwater form
Attention should be paid to the following:
1.Minimizing flow separation.
2.Minimizing the suction effect of the propeller.
3.Sufficient propeller clearance.
Separation at the stern
Separation at the stern is a function of ship form and propeller influence. The suction effect of the single-screw propeller causes the flowlines to converge.

56 Ship Design for Efficiency and Economy
This diminishes or even prevents separation. The effect of the propeller on twin-screw ships leads to separation. Separation is influenced by the radius of curvature of the outer shell in the direction of flow, and by the inclination of flow relative to the ship's forward motion. To limit separation, sharp shoulders at the stern and lines exceeding a critical angle of flow relative to the direction of motion should be avoided. If the flow follows the waterlines rather than the buttocks, a diagonal angle or a clearly definable waterline angle is usually the criterion instead of the direction of flow, which is still unknown at the design stage. The critical separation angles between waterline and longitudinal axis for cruiser sterns and similar forms are:
iR D 20° according to BakerÐabove this, separation is virtually inevitable. iR D 15° according to KempfÐseparation beginning.
An angle of less than 20° to the longitudinal axis is also desirable for diagonal lines. Adherence to these two angles is often impossible, particularly for full hull forms. Most critical is the lower area of the counter, the area between the counter and the propeller post (Fig. 2.26). In areas where the flow mainly follows the buttocks, no separation will occur, regardless of the waterline angle. This happens, for example, below a flat, transom stern and in the lower area of the stern bulb. If a plane tangential to the ship's form is assumed, the angle between longitudinal axis of the ship and this tangential plane should be as small as possible.
Figure 2.26 Position of greatest waterline angle
Figure 2.27 Separation zone with stern waterlines, above the propeller

Lines design 57
The stern waterlines above the propeller should be straight, and hollows avoided, to keep waterline angles as small as possible. Where adherence to the critical waterline angle is impossible, greatly exceeding the angle over a short distance is usually preferred to marginally exceeding it over a longer distance. This restricts the unavoidable separation zone (Fig. 2.27) to a small area.
The waterline endings between counter and propeller shaft should be kept as sharp as possible (Fig. 2.28). The outer shell should run straight, or at most be lightly curved, into the stern. This has the following advantages:
Figure 2.28 PlatingÐstern post connections
1.Reduced power requirements. Reduced resistance and thrust deduction fraction.
2.Quieter propeller operation.
Methods of reducing waterline angles
Single-screw ships
If the conventional rudder arrangement is dispensed with, the inflow angle of the waterlines in the stern post area of single-screw ships can be effectively reduced by positioning the propeller post further aft. The following arrangements may be advantageous here:
1.Nozzle rudder with operating shaft passing through the plane of the tips of the propeller blades. The nozzle rudder requires more space vertically than the nozzle built into the hull, since the propeller diameter to be accommodated is smaller. The gap between propeller blade tip and nozzle interior must also be greater in nozzle rudders. For these two reasons, propulsion efficiency is not as high as with fixed nozzles.
2.Rudder propellerÐand Z propulsion.
Centre-line rudder with twin-screws
Where twin-screw ships are fitted with a central rudder, it is advisable to make the rudder thicker than normal. In this way, the rudder has a hull-lengthening effect on the forward resistance of the ship. This results in a lower resistance and higher displacement with steering characteristics virtually unchanged. The
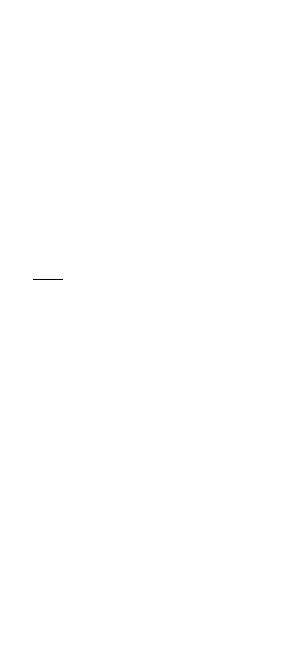
58 Ship Design for Efficiency and Economy
ratio of rudder thickness to rudder length can be kept greater than normal (Fig. 2.29).
Figure 2.29 Centre-line rudder on twin-screw ships
Propeller suction effect
The lines in the area where the flow enters the propeller must be designed such that the suction remains small. Here the propeller regains some of the energy lost through separation. The following integral should be as small as possible for the suction effect (Fig. 2.30):
Z sin
ax dS
where:
dS is the surface element of the outer shell near the propeller,
is the angle of the surface element to the longitudinal axis of the ship, a is the distance of the surface element from the propeller, x 2.
Hence it is important to keep the waterlines directly forward of the propeller as fine as possible. The waterlines forward of the propeller can be given light hollows, even if this causes a somewhat greater maximum waterline angle than straight lines. Another way of minimizing the suction is to increase the clearance between the propeller post and the leading edge of the blade.
Figure 2.30 Effect of propeller suction on shell element

Lines design 59
Wake distribution as a function of ship's form
A non-uniform inflow reduces propulsion efficiency. In predictive calculations, the propeller efficiency 0 is derived by systematic investigations which assume an axial regular inflow. The decrease in propulsion efficiency caused by the irregular direction and velocity of the inflow is determined using the `relative rotative efficiency' R in conjunction with other influencing factors. As well as diminishing propeller efficiency, an irregular wake can also cause vibrations. Particular importance is attached to the uniformity of flow at a constant radius at various angles of rotation of the propeller blade. Unlike tangential variations, radial variations in inflow velocity can be accommodated by adjusting the propeller pitch. The ship's form, especially in the area immediately forward of the propeller, considerably influences the wake distribution. Particularly significant here are the stern sections and the horizontal clearance between the leading edge of the propeller and the propeller post. See Holden et al. (1980) for further details on estimating the influence of the stern form on the wake.
In twin-screw ships, apart from the stern form, there are a number of other influential factors:
1.Shaft position (convergent±divergent horizontal-inclined).
2.Shaft mounting (propeller brackets, shaft bossings, Grim-type shafts).
3.Distance of propellers from ship centre-line.
4.Size of clearance.
Stern sections
The following underwater sections of cruiser and merchant sterns are distinguished (Fig. 2.31):
1.V-section.
2.U-section.
3.Bulbous stern.
On single-screw vessels, each stern section affects resistance and propulsion efficiency differently. The V section has the lowest resistance, irrespective of Froude number. The U section has a higher and the bulbous form (of conventional type) the highest resistance. Very good stern bulb forms achieve the same resistance as U-shaped stern section. On the other hand, the V section has the most non-uniform and the bulbous form the most uniform wake distribution,
Figure 2.31 Stern sections