
Литература / Комар_строймат
.pdfняют поделочный камень: яшму, родонит (орлец), лазурит,
нефрит, малахит, янтарь и др. Необыкновенно обширная палитра красок, включающая практически все цвета спектра и бесконечно разнообразное количество оттенков, позволяет создавать из поделочного камня высокохудожественные произведения искусства. Многие его разновидности обладают выявляемым в разрезе после полировки природным рисунком и узором, чарующим своей фантастичностью, неповторимостью сюжета и необычностью сочетания красок.
Яшмы цветные и пестроцветные, зеленого и красного цветов, обладающие высокой твердостью и прочностью, представляют большой интерес. Встречается яшма на Урале, в Караганде, Крыму, Закарпатье и других местах.
Родонит (орлец) представляет собой мелкозернистую породу, обладающую широким диапазоном красных расцветок древовидного рисунка от бледно-розового до интенсивно красного. Орлец является полупрозрачным материалом. Благодаря значительным запасам этого камня в нашей стране его широко использовали при отделке станции «Маяковская» Московского метрополитена им. В. И. Ленина и других зданий.
Нефрит — природный камень зеленого цвета. Обладая высокой твердостью и вязкостью, он трудно поддается обработке, однако это же его свойство обеспечивает возможность добиться исключительных эффектов в результате получения тончайших узоров.
Лазурит от бледно-голубого до ярко-синего цвета с вкраплениями золотистого обладает сравнительно небольшой твердостью.
Янтарь желтый прозрачный имеет большую твердость. Известны случаи применения янтаря для отделки внутренних помещений дворцов.
Природный гипс от белого до голубого цвета является широко распространенным поделочным камнем. Низкая твердость гипсового камня позволяет легко изготовлять из него сложные скульптурные изделия для интерьеров зданий, а также применять его в качестве облицовочного материала, более экономичного, чем мрамор.
Поделочные камни применяют не только для отделки интерьеров общественных зданий, но и в различных областях техники.
Материалы и изделия для дорожного строительства — бортовые камни, брусчатку, колотый или булыжный камень, щебень,
песок и минеральный порошок — получают из изверженных и
осадочных горных пород. Изверженные горные породы должны обладать следующими свойствами: предел прочности при сжатии глубинных горных пород — не менее 100, излившихся — не менее 60 МПа, коэффициент размягчения — не менее 0,9, водопоглощение — не более 1,0%, морозостойкость — не менее F25, сопротивление удару—не менее 150 Н·см/см3, плотность — 2300 кг/м3 и более. Осадочные горные породы должны иметь плотность 2100 кг/м3, коэффициент размягчения не менее 0,75,
— 51 —
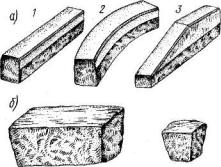
|
водопоглощение не более 4%, |
|||
|
морозостойкость не менее F25 |
|||
|
и сопротивление удару 150 |
|||
|
Н·см/см3. Горные породы не |
|||
|
должны |
быть |
затронуты |
|
|
выветриванием. |
|
|
|
|
Бортовые камни применяют |
|||
|
для отделения проезжей части |
|||
|
улиц от тротуаров, а также |
|||
|
автомобильных |
дорог |
от |
|
|
тротуаров |
на |
уникальных |
|
|
мостах и в туннелях. По форме |
|||
|
бортовой |
камень |
пред- |
|
Рис. 2.11. Изделия для дорожного строи- |
ставляет |
собой |
брус |
(рис. |
тельства: |
2.11, а) длиной |
70...200 см с |
||
а — бортовой камень; 1 — прямой; 2 — ле- наклонной |
или |
вертикальной |
||
кальный; 3 — для съездов; б — брусчатка |
Лицевой гранью в поперечном |
сечении. Верхняя часть бортового камня, выступающая над дорожным покрытием, обтесана чисто, а нижняя часть — грубо. По размерам бортовой камень бывает низкий — 30 см и высокий — 40 см с шириной по верху 10, 15 и 20 см.
Брусчатка — колотые или тесаные бруски (рис. 2.11, б) высотой 10...16 см, шириной 12...15 см и длиной 15...25 см, по форме близки к параллелепипеду, а лицевая поверхность имеет форму прямоугольника. Предел прочности при сжатии исходной породы не ниже 100 МПа, водопоглощение не более 0,6%. Применяют при устройстве мостовых (особенно часто при крутых подъемах
испусках), трамвайного полотна, посадочных площадок трамвая
ипр.
Колотый булыжный камень используют для укрепления откосов земляных покрытий и оснований. Колотый камень по форме близок к многогранной призме или усеченной пирамиде с площадью лицевой поверхности 100, 200 и 400 см2 при соответствующей высоте 16, 20 и 30 см. Лицевая поверхность и постель должны быть параллельны, на боковых гранях не должно быть выступов, препятствующих плотному примыканию к другому камню. Булыжный камень имеет овальную форму, его лицевая сторона должна быть больше поверхности постели. Размеры булыжного камня такие же, как и колотого камня. Для подземных
сооружений и мостов применяют плиты и камни из изверженных и осадочных горных пород. Для облицовки туннелей и надводных частей мостов используют гранит, диорит, габбро, диабаз, базальт с пределом прочности при сжатии не ниже 100 МПа. Морозостойкость указанных горных пород для этих целей F150....500. При изготовлении облицовочных плит из плотного известняка или песчаника их прочность должна быть не ниже 60, а морозостойкость не менее F100. Для облицовки подводных частей мостов применяют изделия из гранита, диори-
— 52 —
та базальта и диабаза с пределом прочности при сжатии не менее 100 МПа и морозостойкостью не менее F150. Лицевые камни и облицовочные плиты для туннелей и мостов обрабатывают под фактуры «скала», бороздчатую или рифленую. Размеры и формы плит и камней устанавливают проектом.
Для гидротехнических сооружений применяют природные камни правильной или неправильной формы (рваные, обкатанные, колотые и пиленые, а также щебень), получаемые из изверженных, метаморфических или осадочных пород. Камни не должны иметь признаков выветривания, прослоек мягких пород — глины, гипса и других размокаемых и растворимых включений, а также рыхлых включений ракушек и видимых расслоений и трещин.
Камни для гидротехнического строительства, используемые для внутренней части набросанных плотин, могут быть из осадочных пород прочностью 60...80 МПа с коэффициентом размягчения не менее 0,7...0,8.
Каменные материалы проверяют на влияние веществ, растворенных в воде (морской, грунтовой, речной, болотной).
Жаростойкие и химически стойкие материалы и изделия
изготовляют из горных пород, не затронутых выветриванием. Для материалов и изделий, работающих в условиях высоких температур, используют хромит, базальт, диабаз, андезит, туф. Для защиты конструкций зданий от кислот (кроме плавиковой
икремнефтористоводородной) применяют облицовочные плиты из гранита, сиенита, диорита, кварцита, андезита, трахита, базальта, диабаза и кремнистого песчаника. Защита от щелочей достигается применением изделий из плотных известняков, доломитов, мрамора, магнезита и известкового песчаника. Для защиты от действия высокой температуры и агрессивных сред используют камни правильной формы и фасонные, плиты облицовочные
иплиты для полов (гладкие и рифленые), камень, щебень и песок для бетонов и растворов, а также тонкомолотые порошки в качестве наполнителя для бетонов, растворов, мастик, замазок, шпаклевок и грунтовок.
Щебень получают дроблением различных горных пород до размера 5(3) ...70 мм. Прочность щебня характеризуют маркой, соответствующей пределу прочности исходной горной породы при сжатии в насыщенном водой состоянии и определяемой по дробимости щебня при сжатии (раздавливании) в цилиндре. По этому показателю щебень подразделяется на марки: из изверженных пород — 1400, 1200, 1000, 800 и 600; из осадочных и мета-
морфических пород — 1200, 1000, 800, 600, 400, ЗОО и 200.
Щебень высшей категории качества должен иметь марку по прочности не ниже 600 для щебня из осадочных пород и не ниже 800 для щебня из изверженных и метаморфических пород.
Кроме того, щебень, предназначенный для строительства автомобильных дорог, характеризуется износом в полочном
—53 —
барабане. По этому показателю установлено четыре марки щебня: И-I, И-II, И-Ш и И-IV.
В зависимости от назначения качество щебня определяют по следующим показателям: гранулометрическому составу, форме зерен, содержанию зерен слабых пород, наличию пылевидных и глинистых частиц, прочности и морозостойкости; кроме того, по петрографической характеристике плотности: истинной (без пор), средней (включая поры), насыпной (включая поры и межзерновые пустоты); пористости, пустотности и водопоглощению.
Гравий — это рыхлое скопление обломков горных пород размером 5(3) ...70 мм, обкатанных в различной степени.
Песок — рыхлая масса, состоящая из зерен минералов и пород размером 0,16...5 мм. В зависимости от минералогического состава различают кварцевые, полевошпатовые, карбонатные пески. Применяют их для приготовления растворов и бетонов, для устройства оснований дорожных покрытий, дренажных сооружений.
Перевозка и хранение материалов и изделий из природного
камня. Облицовочные плиты, камни и другие изделия после их изготовления маркируют. Для этого на тыльной стороне облицовочной плиты или на торцовой части камней несмываемой краской указывают тип камня, плиты или блока, основные размеры (длину, ширину). На блоке, предназначенном для распиловки, также указывают объем его и наименование (шифр) карьераизготовителя.
Изделия при перевозке следует предохранять от загрязнения
иповреждений. Бутовый и валунный камень, щебень, брусчатку
иколотый камень необходимо перевозить навалом или в контейнерах. Бутовый камень хранят в штабелях навалом по маркам и породам, а брусчатку — в штабелях по сортам и классам.
Блоки для распиливания, крупные стеновые блоки, бортовые камни разрешается перевозить на открытых платформах без тары с укладкой правильными рядами на подкладках и прокладках с учетом обеспечения предохранения от повреждений. Хранение их разрешается на открытых спланированных площадках, обеспечивающих отвод ливневых вод. Облицовочные плиты перевозят в прочной таре в вертикальном положении попарно, лицевыми поверхностями друг к другу, с прокладкой бумаги между ними и закрепленными клиньями. Плиты изверженных пород разрешается перевозить без тары, установленными на ребро и разделенными деревянными прокладками; хранить их можно на открытых складах. Плиты из мрамора, известняков
итуфа хранят в закрытых складах.
§ 2.8. Методы защиты природных каменных материалов от разрушения
Разрушение каменных материалов может происходить под действием воды как растворителя. Особенно активно действует на карбонатные породы вода, содержащая углекислоту, серни-
— 54 —
стые и другие кислотные соединения. Каменные материалы разрушаются также при переменном действии воды и мороза. Если горная порода состоит из нескольких минералов, то разрушение ее может происходить от изменения температуры вследствие того, что коэффициент линейного расширения разных минералов не одинаков.
Горные породы разрушаются также от воздействия органических кислот. Частицы пыли неорганического и органического происхождения, являющиеся бытовыми или промышленными отходами города, оседают на поверхности и в порах камня; при смачивании их водой возникают бактериологические процессы с зарождением микроорганизмов, которые разрушают камень за счет образования органических кислот. Скорость разрушения горной породы зависит также от качества и структуры ее, выражающихся в наличии микротрещин, микрослоистости и размокающих и растворимых веществ.
Для защиты каменных материалов от разрушения необходимо прежде всего предотвратить проникновение воды и ее растворов в глубину материала, для этого применяют так называемое флюатирование. При обработке известняка флюатами (например, кремнефтористым магнием) образуются нерастворимые в воде соли, которые закрывают поры в камне и тем самым повышают его водонепроницаемость и атмосферостойкость.
От воздействия углекислоты и образования сульфатов облицовочные камни предохраняют путем пропитки их на глубину до 1 см горячим льняным маслом. Для предохранения от проникновения воды поверхность камня покрывают слоем раствора воска в скипидаре, парафина в легком нефтяном дистилляте или каменноугольном дегте. Защищают каменные материалы от разрушения также конструктивными мерами, например путем образования хорошего стока воды с поверхности камня, придания камню гладкой поверхности и т. д.
§ 2.9. Экономика производства и применения природных каменных материалов и изделий
Наличие природных ресурсов и уровень развития сырьевых отраслей — важный фактор, определяющий экономическую мощь народного хозяйства. СССР располагает разнообразными ресурсами минерального сырья и топлива, большими запасами нерудных ископаемых и гидроэнергетических ресурсов, лесного сырья. В СССР имеются фактически неограниченные запасы нерудных ископаемых для производства различных строительных материалов и изделий.
О значении нерудных строительных материалов в широкой индустриализации строительства, осуществляемой в нашей стране, можно судить по следующим данным. В общем весе сооружаемых объектов масса материалов и конструкции, получаемых на основе минерального нерудного сырья, составляет
всреднем 70%, достигая для некоторых объектов 90%.
—55 —
Производство нерудных строительных материалов, насчитывающее около 6 тыс. предприятий, организовано во всех экономических районах страны и в связи с ростом выпуска бетона и сборного железобетона развивается быстрыми темпами. Известно, что лишь за период 1980—1985 гг. суммарный объем производства сборного и монолитного бетона и железобетона возрос до 270 млн. м3, причем опережающими темпами увеличивается производство сборных железобетонных конструкций, а среди последних — спецжелезобетона, для изготовления которого требуются заполнители мелких фракций.
Изменение структуры производства и применения железобетонных конструкций обусловило опережающее развитие производства щебня и гравия мелких фракций, удельный вес которых возрос с 8% в 1955 г. примерно до 20...25% в настоящее время. На развитие производства нерудных строительных материалов требуются большие единовременные затраты.
Кратко рассмотрим технико-экономическое состояние промышленности по переработке природного камня по основным видам — заполнители для бетона, материал для стен (пильный камень) и облицовочные материалы.
Затраты на заполнители в общей себестоимости железобетонных изделий составляют в СССР около 20%. Такая высокая стоимость щебня, гравия и песка обусловлена невысоким уровнем механизации производственных процессов и низким коэффициентом извлечения полезного продукта из горной массы. За последние годы достигнуто значительное снижение себестоимости нерудных строительных полезных ископаемых за счет внедрения комплексной механизации, ликвидации мелких карьеров, обусловливающих низкое использование основного оборудования (экскаваторов, самосвалов, автопогрузчиков), внедрения прогрессивных технологических методов добычи, например гидромеханизации. Достигнуто значительное снижение транспортных расходов на перевозку нерудных строительных материалов за счет улучшения размещения заводов сборного железобетона и карьеров нерудных ископаемых, а также в результате использования в качестве транспортных средств более эффективных автомобилей грузоподъемностью свыше 5 т.
Помимо транспортных затрат и затрат по добыче важное место в общей себестоимости нерудных строительных материалов занимают работы по дроблению, фракционированию, выработке мелких фракций, организации процессов мойки и обогащений. Низкое качество заполнителей для бетона (песка, гравия, щебня) влечет за собой значительный перерасход цемента, повышенный процент брака, увеличение трудоемкости в производстве железобетонных изделий и конструкций, кладочных, монтажных и штукатурных работ. В связи с этим щебень, гравий и песок на заводы железобетонных изделий должны поступать отсортированными по фракциям, без глинистых и других засоряющих примесей.
- 5 6 -
На себестоимость продукции в промышленности нерудных строительных материалов оказывает влияние ряд факторов, прежде всего техническая оснащенность предприятий, совершенство технологии, условия добычи ископаемых и др. Значительные резервы снижения себестоимости и удельных капитальных вложений заключены в применении новых, более совершенных технологических методов и, в частности, метода гидромеханиза-
ции.
По сравнению с сухим способом добычи нерудных ископаемых гидромеханизация позволяет снизить удельные капитальные вложения примерно на 20...25%; себестоимость — на 30...
35% и сократить сроки строительства примерно на 1/3. Значительное снижение себестоимости продукции на гидромеханизированных предприятиях объясняется непрерывностью технологического процесса, сокращением численности обслуживающего персонала, попутной, без затрат, промывкой песка и снижением амортизационных отчислений вследствие меньших удельных капитальных вложений.
Большое влияние на технико-экономические показатели разработки нерудных материалов оказывают горно-геологические условия (величина запасов, мощность пласта полезного ископаемого, глубина залегания, плотность и крепость породы, ее химический и минералогический составы и др.).
При добыче природного пильного камня открытым способом разработки при коэффициенте вскрыши 0,3, коэффициенте извлечения полезного продукта из горной массы 0,4 и механической прочности камня 5 МПа для карьера годовой мощностью 100 тыс. м3 удельные капитальные вложения составляют 35 руб/м3. При увеличении коэффициента вскрыши на 0,1 удельные капитальные вложения возрастают на 30...50%; при уменьшении выхода полезного продукта из горной массы до 0,2 удельные капитальные вложения возрастают на 25%, а при росте выхода полезного продукта снижаются на 20% и т. д., отсюда исключительно важно выбрать наиболее эффективные месторождения с максимально благоприятными горно-геологическими условиями.
В настоящее время более 30% заводов сборного железобетона применяют заполнители, не удовлетворяющие требованиям стандарта по гранулометрическому составу и содержанию пылевидных частиц. Вместе с тем, по расчетам НИИЦемента, на каждый процент запыленности заполнителя (в пределах до 12%) расход цемента возрастает от 1 до 1,5%. Дополнительный перерасход цемента вызывается также недостатками гранулометрического состава заполнителей. Выпуск фракционированных заполнителей позволяет снизить расход цемента в бетоне примерно на 13... 15% и повысить качество бетона. Капитальные вложения на дополнительную обработку щебня и гравия в связи с усложнением технологической схемы производства являются значительными. Они экономически оправданы, поскольку от качества
— 57 —
нерудных непосредственно зависят качество и стоимость возведенных зданий и сооружений.
Увеличение степени концентрации производства является одним из решающих факторов снижения удельных капитальных вложений в промышленности нерудных строительных материалов. Рост степени концентрации производства происходит на основе внедрения нового высокопроизводительного оборудования — горно-транспортных агрегатов непрерывного действия, новых типов станков ударно-канатного бурения, мощных экскаваторов и земснарядов, автосамосвалов большой грузоподъемности, эффективных видов безрельсового транспорта, щековых дробилок крупного дробления, одно- и двухроторных дробилок ударного действия и т. п.
Одним из факторов, обеспечивающих улучшение качества продукции и снижение ее стоимости, является дальнейшее совершенстование автоматизации производственных процессов дробильно-сортировочных заводов, а также контроль качества выпускаемой продукции. В настоящее время разработана система автоматического регулирования режима работы конусной дробилки.
Система включает устройства для изменения размера разгрузочной щели конусной дробилки, разгрузочной щели с автоматическим управлением и стопорения регулирующего кольца конусной дробилки. Эта система обеспечивает получение заданного массового соотношения фракций продуктов дробления или заданного зернового состава по среднему диаметру куска на выходе дробилки; увеличивает до 20% выход щебня мелких фракций (5... 10 и 10...20 мм) за счет сохранения постоянного размера разгрузочной щели дробилки при износе дробящих поверхностей конусов; обеспечивает автоматическое регулирование размера щели при поступлении в дробилку исходного материала с различными физико-механическими свойствами; позволяет повысить производительность дробилки на 15...20% за счет снижения коэффициента циркуляции.
Снижение себестоимости щебня получено также от внедрения системы автоматического регулирования загрузки щековой дробилки. Эта система обеспечивает автоматическое поддерживание любого заданного уровня загрузки горной массы рабочей камеры дробилки, что создает благоприятные условия для работы всего технологического оборудования.
Разработана и внедрена на дробильно-сортировочном заводе Сокского карьероуправления Куйбышевской области автоматическая станция контроля качества щебня по содержанию отмучиваемых примесей (АСК-8), с помощью которой можно не только оперативно определять в лабораториях качество заполнителя бетонных и дробильно-сортировочных заводов, но она может служить датчиком в системах автоматического контроля и регулирования процессов промывки щебня, гравия и других сыпучих материалов.
— 58 —
В основу работы станции положен принцип отмучивания глинистых и пылевидных частиц под действием выпрямленного электрического тока с последующим измерением плотности образовавшейся суспензии фотоэлектрическим компенсационным методом. Применение автоматической станции контроля качества щебня по содержанию отмучиваемых примесей примерно в 40 раз повышает производительность, позволяет своевременно выявить брак продукции дробильно-сортировочных заводов и снизить перерасход цемента на бетонных заводах.
Наконец, улучшение показателей эффективности капитальных вложений может быть достигнуто в результате более широкого использования передвижных механизированных предприятий нерудных строительных материалов. В настоящее время этими предприятиями обеспечивается лишь 5...6% потребности отдаленных районов, причем передвижные предприятия оснащены таким же оборудованием, которое предназначено для стационарных заводов. В то же время в США более 1/3 щебня выработано на передвижных заводах, характеризующихся высоким уровнем комплексной механизации при сравнительно небольших удельных капитальных вложениях. По расчетным данным, использование передвижных предприятий позволит снизить себестоимость щебня в ряде районов до 4...5 руб/м3, а также обеспечить снижение удельных капитальных вложений примерно на
2руб/м3 производственной мощности.
Впоследние годы по песку и гравию имеет место рост себестоимости производства, что объясняется повышением качества нерудных, увеличением выпуска более дорогого в производстве, но эффективного в применении промытого и классифицированного заполнителя. Вместе с тем такое положение свидетельствует о больших резервах возможного снижения себестоимости нерудных строительных материалов усовершенствованием технологии промывки и обогащения.
Значительными темпами в последние 7...8 лет развивается производство природных легких заполнителей — на базе туфов, вулканических шлаков и пемзы (главным образом в Армянской ССР). Вулканические шлаки и пемза имеют плотность
400...900 кг/м3, что обеспечивает получение теплоизоляционных
иконструкционно-теплоизоляционных бетонов. Возможно использование шлаков и пемзы в качестве компонента для тепло- и звукоизоляционных и жароупорных изделий, а также активной минеральной добавки к вяжущим и наполнителя пластмасс. В 1980 г. было добыто 6,4 млн. м3 шлаковых и пемзовых заполнителей естественного происхождения.
Важным резервом покрытия дефицита и экономии искусственных стеновых материалов является развитие производства
легких камней для стен из природного камня. Общие запасы его по
СССР составляют более 1,3 млрд. м3, в том числе в Молдавии
— 0,55, на Украине — 0,3, в Азербайджане — 0,2 млрд. м3. Себестоимость 1 м3 природного стенового камня намного ниже,
— 59 —
чем керамического кирпича, поэтому в ряде районов целесообразно применять природные каменные стеновые материалы и обеспечивать ими потребности строительства. Однако при радиусе перевозки природных стеновых каменных материалов, большем 350...400 км, их эффективность падает в связи с ростом транспортных расходов. Удельные капитальные вложения на организацию добычи пильного камня в зависимости от местных условий в 1...2 раза меньше, чем по кирпичу. В ряде случаев
оказывается весьма эффективным применение в общественных и жилых зданиях облицовочных материалов из
природного камня — туфов, известняков, гранитов, габбро, мрамора и других декоративных пород. Высокая долговечность этих облицовок обеспечивает незначительный уровень затрат на эксплуатацию — в 5...8 раз меньший, чем на отделку зданий цветными растворами и бетонами, а также силикатными и известковыми красками. В 1985 г. было выпущено более 60 млн. м2 этих облицовок. Расчеты показывают, что при производстве туфовых облицовочных плит на заводе мощностью 1 млн. м2 плит в год, оснащенном станками с алмазным инструментом, себестоимость 1 м2 готовой плиты составит в зависимости от типа туфа примерно 1 руб. Благодаря теплообработке гранита себестоимость 1 м2 бортового камня составит 1,3...
1,5 руб., а по менее долговечному и менее декоративному бетонному бортовому камню — 1,8...2,4 руб. Потребность строительства в облицовочном камне с каждым годом увеличивается. Удовлетворение ее возможно лишь на основе строительства крупных высокомеханизированных предприятий, оснащенных новейшим оборудованием с широким использованием алмазных инструментов.