
Литература / Комар_строймат
.pdfвают. Формуют плитки на рычажном прессе, затем их сушат и обжигают; далее плитки покрывают глазурью и вторично обжигают. Слой глазури придает плиткам водонепроницаемость и высокие декоративные качества.
Глазури имеют разный состав: они бывают прозрачные и непрозрачные (глухие), глянцевые и матовые, белые и цветные, тугоплавкие и легкоплавкие. Прозрачная глазурь придает лицевой поверхности плитки блеск, однако цвет ее остается таким же, как цвет черепка, а непрозрачная (глухая) глазурь придает лицевой поверхности плитки цвет, отличный от цвета черепка. Глухие глазури могут иметь самый разнообразный цвет — от белого до черного. Тугоплавкие глазури применяют для покрытия фарфоровых изделий и состоят из каолина, кварца и полевого шпата, а легкоплавкие глазури — из легкоплавких глин с добавкой мела и оксидов железа. Ими покрывают облицовочный кирпич, черепицу, канализационные трубы. Цветные глазури получают при введении в их состав красящих оксидов или солей металлов. Глазури применяют в виде суспензий, которые наносят на керамические изделия пульверизатором или кистью. Покрывать глазурью можно как предварительно обожженные изделия, так и сухой сырец. Лучшее качество глазури получают при нанесении ее на обожженные изделия.
Фаянсовые плитки изготовляют из огнеупорных глин с добавкой кварцевого песка и плавней — веществ, понижающих температуру плавления (обычно полевого шпата и известняка или мела). Плитки имеют белый или слабо окрашенный черепок, лицевая поверхность покрыта белой и окрашенной, прозрачной или глухой глазурью. Тыльной стороне облицовочных плиток придают рифленую поверхность.
Плитки в зависимости от формы бывают квадратные, прямоугольные и фасонные для углов, облицовки карнизов и плинтусов. Для внутренней облицовки применяют плитки длиной 150 мм, шириной 25, 50, 75 и 150 мм. Толщина плиток должна быть не более 6 мм, а плинтусных — не более 10 мм; плиток, изготовляемых из легкоплавких глин, — не менее 12 мм.
К качеству плиток для внутренней облицовки стен предъявляют высокие требования. Плитки должны иметь правильную геометрическую форму, четкие грани и углы, не иметь выпуклостей, выбоин и трещин, должны быть термически стойкими, т. е., будучи нагреты до температуры 100°С, а затем помещены в воду с температурой 20°С, не должны иметь на глазурованной поверхности трещин, околов глазури и цека — сетки мелких трещин. Водопоглощение плиток не должно быть более 16%.
Как отмечалось выше, сырьем для изготовления плиток обычно служат массы из пластичной глины, каолина, кварца и полевого шпата. При производстве облицовочных плиток (рис. 3.10) поступающие из карьера сырьевые материалы освобождают от посторонних примесей, подсушивают, дозируют по массе и направляют в шаровые однокамерные мельницы для измельчения
— 81 —

Рис. 3.10. Технологическая схема производства фаянсовых глазурованных плиток: 1 — сырьевые материалы; 2 — вагонетка; 3 — шаровая мельница; 4 — удаление примесей на электромагните; 5 — бассейн для массы с мешалкой; 6— насос; 7— распылительное сушило; 8 — транспортер; 9 — просев порошка; 10 — расходный бункер; 11 — прессова-ние плиток; 12 — сушило; 13 — глазурование; 14 — печь для обжига; 15 — сортировка и
упаковка
и перемешивания с водой до образования суспензии, которую пропускают через вибрационные грохоты и направляют в сборник, оборудованный пропеллерным смесителем. Из сборника суспензию подают мембранным насосом под давлением до 1,2 МПа
вфорсунки распылительных сушил. Суспензия выбрасывается через форсунки вверх с влажностью 40...50%, а затем попадает
всреду с температурой 300...350°С и высушивается, превращаясь в гранулы крупностью до 1...1,5 мм и влажностью до 7%. Эти гранулы оседают в нижнем конусе сушила и, проходя через сито, поступают в бункер вылеживания, а оттуда на конвейерную линию.
Конвейерная линия состоит из прессового участка (рис. 3.11), цепного или сетчатого транспортера, по которому плитка поступает в сушильные камеры, участка глазурования и роликовых обжиговых печей туннельного типа. Обожженную плитку сортируют по размерам, цвету, типу и сорту и упаковывают в ящики. Плитки применяют для внутренней облицовки стен в санузлах, кухнях и других помещениях с повышенной влажностью. Плитки для полов должны иметь правильную форму (квадратную, прямоугольную, шестигранную, восьмигранную, треугольную длиной грани 50...150 мм и толщиной 10...13 мм), четкие грани и углы, без выпуклостей, выбоин и трещин; высокую плотность, водопоглощение не более 4%; повышенное сопротив-
ление истираемости (потери в массе при испытании плиток на истираемость не должны превышать 0,1 г/см2 для полов с повышенной истираемостью и 0,25 г/см2 для полов прочих поме-
—82 —

щений). Однако они имеют и |
|
||||||
некоторые |
|
|
недостатки: |
|
|||
большую |
теплопроводность, |
|
|||||
слабое |
сопротивление |
удару, |
|
||||
малые размеры. Плитки для |
|
||||||
полов применяют в вестибюлях |
|
||||||
общественных зданий, банях, |
|
||||||
прачечных, |
санузлах, |
на |
|
||||
предприятиях |
|
химической |
|
||||
промышленности и т. д. |
|
|
|||||
Сырьем |
для |
изготовления |
|
||||
керамических |
плиток |
для |
|
||||
полов служат высокосортные |
|
||||||
пластичные глины с ото- |
|
||||||
щающими |
и |
понижающими |
|
||||
температуру |
плавления |
до- |
|
||||
бавками. |
Для |
придания |
|
||||
плиткам |
необходимого |
цвета |
|
||||
вводят красители (хромистое |
|
||||||
железо, |
оксид |
кобальта |
и т. |
|
|||
д.). В производстве плиток |
|
||||||
применяют |
два |
|
способа |
Рис. 3.11. Пресс-автомат полусухого прес- |
|||
подготовки |
массы |
для |
фор- |
||||
мования: мокрый и полусухой. |
сования: |
||||||
1 — механический пресс; 2 — бункер пресс- |
|||||||
Мокрый способ используют при |
порошка; 3 — конвейер |
||||||
глинах, |
требующих |
добавок |
|
плавней и красящих веществ. Сухой способ применяют при однородных глинах, не требующих добавок. При полусухом способе вначале глину тщательно измельчают, затем подсушивают до влажности 5...7% и вновь измельчают и просеивают. Измельченная и просеянная масса вылеживается 24...28 ч для выравнивания влажности и поступает на прессование. При мокром способе глину измельчают, а затем разбалтывают в большом количестве воды вместе с добавками. Из резервуара массу подают в фильтр-прессы, где ее обезвоживают до влажности около 20%, а затем подсушивают до влажности 5...7% и размалывают на бегунах. Измельченная масса на 24...28 ч поступает в бункера для вылеживания, а оттуда на прессование.
Более рациональная технология производства плиток для полов (рис. 3.12) предусматривает приготовление пресс-порошка с обезвоживанием шликера не в фильтр-прессах, а в распыли-
тельных сушилах. Формуют плитки из пресс-порошка на полуавтоматических гидравлических или автоматических механических прессах при давлении 25...30 МПа. При таком прессовании плитка превращается в черепок. Обжигают плитки в капселях или без них при температуре 1150...1250°С. Подъем температуры при обжиге и охлаждении ведут медленно в целях получения более высокого качества плиток и уменьшения брака. Обожженные
— 83 —

Рис. 3.12. Технологическая схема производства керамических плиток для полов: 1 —
склад глины; 2 — транспортер; 3 — ящичный подаватель; 4 — дробление глины на зубчатых вальцах; 5— помол глины в шаровых мельницах; 6— распылительное сушило; 7 — расходные бункера; 8 — прессование плиток; 9 — сушка плиток; 10 — обжиг плиток; 11 —сортировка и упаковка
плитки сортируют по сортам, размерам, цвету и тону и упаковывают в пачки по 15 шт.
Плитки керамические мозаичные изготовляют двух видов: квадратные со стороной квадрата 23 и 48 мм и толщиной 6 и 8 мм и прямоугольные размером 48 × 23 и толщиной 6 и 8 мм. Плитки мозаичные обладают высокой плотностью и полным спе канием черепка без остеклования, а следовательно, высоким со противлением истираемости и малым водопоглощением (не более
3...4%).
Производство ковровой мозаики сходно с производством крупных плиток с той лишь разницей, что прессование первых осуществляется в специальных многогнездовых пресс-формах. Мозаичные плитки экономичнее в производстве, так как их малые размеры упрощают изготовление и до минимума снижают брак. Обожженные плитки укладывают в матрицы, затем на них наклеивают картон, который после устройства пола смывают. Ковры изготовляют размером 398 × 598 мм, толщина шва между плитками 2 мм. Упаковывают листы с плитками пачками по 10 листов с прокладками из фанеры или картона. Хранят мозаичные плитки в закрытых помещениях раздельно по типам, узорам и цвету. Применяют мозаичные плитки для облицовки ванных комнат, бань, купальных бассейнов, мест общего пользования — фойе, вестибюлей, станций метрополитена и пр.
§ 3.8. Кровельная черепица
Керамическая черепица является относительно недорогой, с хорошими декоративными качествами, но кровля из нее имеет значительную массу (до 65 кг/м2). Черепицу изготовляют
из глины с добавками или без них.
Встроительной практике широко применяют черепицу четырех
—8 4 —
типов: штампованную, пазовую, плоскую ленточную и коньковую.
В зависимости от назначения черепицу делят на: рядовую — для покрытия скатов кровли; коньковую — для покрытия коньков и ребер; разжелобочную — для покрытия разжелобков; концевую («половинки» и «косяки») — для замыкания рядов и черепицу специального назначения.
Технология изготовления черепиц в основном не отличается от технологии изготовления кирпича, но ввиду малой толщины черепицы глину перед формованием тщательно обрабатывают до получения однородной пластичной массы. Формуют черепицу на ленточных или револьверных прессах, после чего подают в сушило. Сушить черепицу нужно осторожно во избежание коробления, появления трещин и других деформаций. Обжигают черепицу до полного спекания черепка при температуре 950...
1000°С. Кровельная черепица должна быть хорошо обожженной, равномерно окрашенной, иметь ровную и гладкую поверхность (без трещин), быть достаточно прочной (разрушающая нагрузка на излом не менее 7 Н), водонепроницаемой и морозостойкой
(не ниже F25).
Хранят черепицу в деревянной таре, в закрытых помещениях, по сортам.
§ 3.9 Трубы керамические канализационные и дренажные
Трубы керамические канализационные изготовляют из тугоплавких или огнеупорных глин с отощающими добавками (тонкомолотым шамотом или кварцевым песком) или без них, ци-
линдрической формы с раструбом на одном конце.
Сырьевую массу обычно готовят пластическим способом по следующей схеме (рис. 3.13). Глину освобождают от крупных камней и подвергают грубому помолу. Измельченную глину подсушивают, измельчают в дезинтеграторах и просеивают. Наряду с подготовкой глиняного порошка параллельно идет приготовление из глины шамота. Отдозированную глину и шамот подают в смеситель, в котором массу перемешивают, увлажняют и направляют на изготовление валюшек. Выдержанные валюшки следуют в формовочное отделение. Формование труб производят на специальных трубных прессах, на которых одновременно с телом трубы формуют и раструб. Отформованные трубы сушат в искусственных сушильных установках. Высушенные и отделанные трубы покрывают снаружи и внутри глиняной глазурью, после чего обжигают. Обжиг канализационных труб производят в камерных или туннельных печах при температуре
1250...1300°С.
Канализационные трубы в зависимости от показателей внешнего вида и водопоглощения бывают I и II сортов. Водопоглощение черепка для труб I сорта — не более 9%, для II сорта — не более 11 % по массе. Трубы должны выдерживать гидравли-
— 85 —

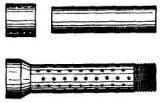
ческое давление не менее 0,2 МПа и иметь кислотоустойчивость черепка не ниже 90%. Керамические канализа ционные трубы изготовляют диаметром
150...600 мм, длиной 800...1200 мм. По казатели механической прочности и гидравлического давления, правила
приемкиимаркировки, храненияиРис. 3.14. |
|
Керамические |
дренажныетрубы |
транспортирования канализационных |
|
труб должны соответствовать требо- |
|
ваниям ГОСТа. |
|
Трубы канализационные применяют для производственных и хозяйственно-фекальных канализационных, а также для водосточных сетей при наличии агрессивных вод. Трубы
керамические дренажные (рис. 3.14) изготовляют из пластичных глин с добавками или без них путем формования на специальных или ленточных прессах и последующего обжига в печах с опрокинутым пламенем. Внешнюю сторону дренажных труб покрывают глазурью. Дренажные трубы изготовляют с раструбами или без них. Раструбные трубы имеют отверстия, через которые вода проникает в трубы, однако отверстия быстро засоряются. В последнее время более широко практикуют изготовление дренажных труб без раструбов. Для соединения этих труб и защиты их от заиливания применяют керамические муфты. Вода в такие трубы поступает через стыки.
Дренажные трубы выпускают диаметром 25...250 мм, длиной 333...335 мм, а иногда до 500 мм. Дренажные трубы должны быть морозостойкими (не ниже 15 циклов).
§ 3.10. Изделия керамические кислотоупорные
Кирпич кислотоупорный применяют для фундаментов и фу теровки химических аппаратов, газоходов, кладки колосников, настилки полов и сточных желобов предприятий химической промышленности. Кислотоупорный кирпич производят двух ви дов: прямой размером 230×113×65 мм и клинообразный (клин торцовый двусторонний и клин ребровый двусторонний) размером 230 × 1 1 3 × 6 5 или 230 × 11З × 55 мм. По физикомеханическим свойствам и внешнему виду кирпич делят на три сорта: I, II и III. Кислотостойкость кирпича должны быть не менее 92...96%, водопоглощение — не более 8...12%, а предел прочности при сжатии — 15, 20 и 25 МПа. Кислотоупорный кирпич I и II сортов должен обладать высокой термической стойкостью (не менее 2 теплосмен).
Плитки керамические кислотоупорные изготовляют трех типов: кислотоупорные (К), термокислотоупорные (ТК) и тер мокислотоупорные для гидролизной промышленности (ТКГ).
По внешнему виду плитки типов К и ТК делят на два сорта: I и II. Кислотоупорные и термокислотоупорные плитки имеют
— 87 —

плотный спекшийся черепок, высокую прочность — предел прочности при сжатии не менее 39 МПа и на изгиб не менее 15 МПа, низкое водопоглощение — не более 6...9% и высокую кислотостойкость — не менее 96...98%, а также высокую термическую стойкость: для плиток К — не менее 2, а для плиток типа ТК — не менее 8 теплосмен. Плитки типа ТКГ должны обладать кислотостойкостью не менее 97%, водопоглощением не более 6%, пределом прочности при сжатии не менее 25 МПа и термической стойкостью не менее 10. Плитки типа К применяют для футеровки аппаратов и газоходов, облицовки панелей и сточных желебов, а ТК и ТКГ — для футеровки варочных котлов целлюлозной, гидролизной и других отраслей промышленности.
Трубы керамические кислотоупорные изготовляют по такой же технологии, как и канализационные, двух сортов: I и II. Они имеют плотный спекшийся черепок, с обеих сторон покрытый глазурью. Кислотоупорные трубы отличаются высокой плот ностью и прочностью, малым водопоглощением и высокой устой чивостью к действию кислот. Так, трубы I сорта должны иметь кислотостойкость не менее 98%, водопоглощение не более 3%, предел прочности при сжатии не менее 40 МПа, термическую стойкость не менее 2 теплосмен и гидравлическое давление не менее 0,4 МПа. Трубы керамические кислотоупорные и фасон ные части к ним применяют для перемещения неорганических и органических кислот и газов при разрежении или давлении до 0,3 МПа.
§ 3.11. Изделия санитарно-технической керамики
Основным сырьем для производства санитарно-технических изделий является беложгущиеся огнеупорные глины, каолины,
кварц и полевой шпат. Различают три группы санитарно-тех нической керамики: фаянс, полуфарфор и фарфор, отличающие ся степенью спекания и пористостью. Изделия из фаянса имеют пористый, а из фарфора плотный сильно спекшийся черепок, плотность полуфарфора занимает промежуточное положение. Различная степень спекания фаянса, фарфора и полуфарфора достигается при одних и тех же сырьевых материалах, но при различном соотношении последних в рабочей массе (табл. 3.1).
Таблица 3.1. Состав массы для изделий санитарно-технической керамики
— 88 —

Сырьевые материалы, идущие на изготовление изделий сани- тарно-технической керамики, подвергают тщательной переработке: помолу, отмучиванию, просеиванию и другим операциям, обеспечивающим получение тонкоизмельченной сырьевой смеси, освобожденной от вредных примесей. Приготовленная смесь представляет сметанообразную массу — шликер. Формуют изделия преимущественно способом литья в гипсовых формах, которые впитывают избыток воды. Затем изделия вынимают из форм, подвяливают, оправляют (обрезают) и направляют в сушильные камеры. Высушенные изделия покрывают сырым глазурным слоем и в капселях обжигают при температуре 1250...1300°С в периодических или непрерывнодействующих печах.
Из твердого фаянса изготовляют преимущественно унитазы, умывальники, смывные бачки, а также ванны. Фаянсовые изделия покрывают глазурью, так как в неглазурованном виде они пропускают воду. Черепок фарфоровых изделий непроницаем для воды и газов, обладает высокой механической прочностью
итермической и химической стойкостью. Используют его для производства изоляторов, химической лабораторной посуды
ит. п.
Свойства изделий санитарно-технической керамики приведены в табл. 3.2.
Таблица 3.2. Физико-механические свойства санитарно-технической керамики
Изделия санитарно-технической керамики белые, иногда светло-желтые, должны иметь правильную форму, ровную, гладкую и чистую поверхность без искривлений, равномерно покрытую глазурью; они должны быть хорошо обожжены.
§ 3.12. Керамзит
Керамзит представляет собой легкий пористый материал ячеистого строения с закрытыми порами. Основное применение он находит как заполнитель для легких бетонов (см. гл. 4). Для получения керамзита применяют легкоплавкие глины, содержащие 6...12% оксида железа, 2...3% щелочных оксидов и до 3% органических примесей. Если в глине недостаточно органических примесей, то в нее вводят угольную пыль, торфяную крошку и другие материалы. При обжиге глины происходит размягчение
— 89 —
материала и выделение газов и паров воды. Последние вспучивают частично расплавленную массу, образуя в ней поры. Спекание материала с образованием закрытых пор заканчивается в момент интенсивного газовыделения.
Производство керамзита осуществляют по трем технологическим схемам. При наличии плотных камнеподобных глин, хорошо вспучивающихся, обжиг ведут по сухому способу без формования, сразу после дробления сырья. При полусухом способе можно применять слабовспучивающиеся глины. В этом случае глину подвергают дроблению, сушке, помолу и вводят органические добавки, затем смесь тщательно перемешивают и гранулируют в виде зерен размером 10...20 мм. Пластический способ применяют при неоднородном влажном сырье. В качестве формующих машин используют дырчатые вальцы и барабанные грануляторы, а также ленточные прессы, у которых выходное отверстие мундштука перекрыто перфорированной плитой. Прессы имеют устройство для резки выходящих жгутов. Иногда полуфабрикат сушат в сушильных барабанах.
Керамзитовый гравий обжигают во вращающихся печах длиной 20...50 м, диаметром 1,5...3,5 м при температуре 1300°С в течение 30...60 мин. После обжига керамзит медленно охлаждают до температуры 60...100°С, затем разделяют на фракции и направляют в силосы.
Различают керамзитовый гравий по размеру зерен, плотности и прочности. Керамзитовый гравий имеет размер 5...40 мм, зерна менее 5 мм называют керамзитовым песком. В зависимости от насыпной плотности гравий делят на марки 250...600. Предел прочности при сжатии (МПа) гравия в зависимости от его марки составляет:
Для марки 250...... |
0,6 |
Для марки 400...... |
1,4 |
||||
» |
» |
З00........ |
0,8 |
» |
» |
500...... |
2,0 |
» |
» |
350....... |
1,0 |
» |
» |
600...... |
3,0 |
Для высокомарочных конструктивных легких бетонов применяют гравий М800 и 1000 с прочностью при сжатии до 4 МПа.
§3.13. Огнеупорные материалы
Когнеупорным относятся материалы, имеющие огнеупорность
выше 1580°С. К ним предъявляют следующие основные требования: огнеупорность, предел прочности при сжатии и изгибе, прочность под нагрузкой при высокой температуре, термостойкость, газонепроницаемость, шлакоустойчивость, а также постоянство объема и формы.
Из огнеупорных материалов наиболее широко применяют кремнеземистые, алюмосиликатные, а также магнезиальные, хромистые и углеродистые. Кремнеземистые (динасовые) огнеупорные материалы содержат не менее 93% SiO2. Эти материалы имеют высокую огнеупорность — 1670...1790°С, однако они обладают рядом недостатков: имеют малую термическую стойкость, при
—90 —