
Конспект лекций
.pdf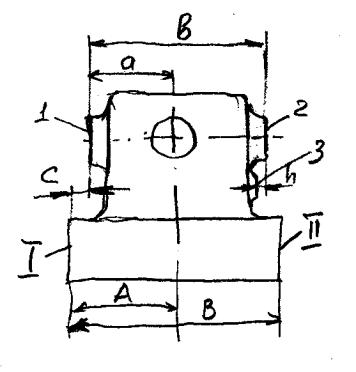
Рис. 5.18. Обробка призматичної заготовки при зміні баз
По першому варіанту обробки послідовність обробки наступна:
-Обробка торцевої поверхні 1 при базуванні по поверхні І. Похибка базування при отримання розміру а складає εδ = ТА (тобто допуску на розмір А);
-Обробка торцевої поверхні 2при базуванні по поверхні 2. Похибка
базування при отримання розміру в складає εδ = ТВ + ТС (тобто сумі |
допусків |
на розміри В та С); |
|
- Обробка торцевої поверхні 3 при базуванні по поверхні 1. |
Похибка |
базування при отримання розміру h складає εδ = Тв + ТС (тобто сумі |
допусків |
на розміри в та С). |
|
По другому варіанту обробки послідовність обробки як і першому варіанті але при незмінній базі 1. Тоді похибка базування будуть складати для розмірів а та h ті ж самі, а для розміру в εδ = ТС, тобто менша.
5.2.4. Принцип суміщення баз
Принцип суміщення баз полягає в тому, щоб для різних видів баз (конструкторські, складальні, технологічні) по можливості застосовувати одні й
ті ж поверхні заготовки. Те ж стосується і вибору технологічних баз (установчі,
131
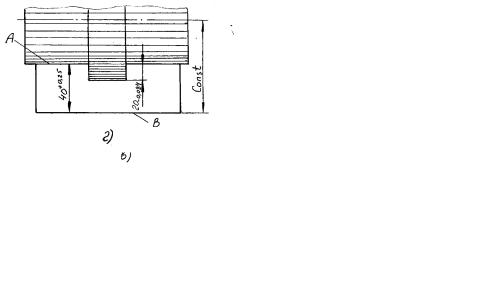
вимірювальні). При невиконанні цього принципу виникає додаткова складова похибки при отриманні розміру заданої точності, яка відноситься до похибки базування. Ця похибка чисельно може дорівнювати допуску на розміри, які з’єднують на кресленні не суміщенні бази (конструкторська і технологічна, установча і вимірювальна). Кращі результати з точки зору точності розташування деталі у складальному виробі досягаються коли вимірювальна і складальна бази суміщені (наприклад, центральний отвір і торець ступеці зубчатого колеса).
Якщо технологічна база не співпадає з конструкторською, то при обробленні заготовки виникає необхідність витримувати з необхідною точністю технологічні розміри, які не співпадають з конструкторськими. В цьому випадку для отримання з заданою точністю конструкторських розмірів технологічні розміри повинні бути більш жорсткими. Приведену залежність можна прослідкувати на наступному прикладі (рис. 5.19).
Рис.5.19. Вплив суміщення конструкторських та технологічних баз на точність обробки
При обробленні паза з дотриманням розміру на його глибину 20H10 (рис. 5.19а) за установчу базу зручно прийняти нижню поверхню В. Обробка здійснюється циліндричною фрезою на налагодженому горизонтально-
132
фрерному верстаті. Вісь фрези при обробленні партії деталей відносно установчої бази В займає незмінне положення то розмір S між дном паза і установчою базою В, який відсутній на кресленні буде, те ж незмінним. Дно паза задано розміром 20h10 від поверхні А, яка є конструкторською базою. Тобто конструкторська та технологічні бази не співпадають. У даному випадку розмір а = 20H10 не може бути дотриманий (рис. 5.19б), так як на нього впливає похибка розміру 40h12, яка складає 250 мкм що перевищує допуск на встановлений конструктором розмір 20, який складає 84 мкм. Для досягнення заданої точності розміру 20-0,084 необхідно щоб допуск на розмір 40 був значно менший за 84 мкм, наприклад 39 мкм. Це означає, що поверхню А потрібно обробити з дотриманням розміру з більш жорстким допуском 40H8, а це потребує додаткових витрат.
Значне підвищення точності обробки може привести до значного підвищення собівартості обробки та зниженню продуктивності. У цьому випадку буде доцільно застосувати спеціальний пристрій, який дозволить сумістити конструкторську та технологічну бази на одній поверхні А (рис. 5.19в). Виключається похибка базування при отриманні розміру 20-0,084, а точність його досягнення буде залежати тільки від точності застосованого способу обробки. У цій схемі є свій недолік. Сили різання відривають заготовку від установчих базових поверхонь пристрою зменшуючи жорсткість закріплення.
Цю задачу можна вирішити і інакше, якщо об’єднати обробку поверхні В з отриманням розміру 40 H12 і паза з дотриманням розміру 20h10 набором фрез (рис. 5.19г).У даному випадку поверхня А є конструкторською базою і одночасно налагоджувальною, а розмір 20-0,084 досягається інструментальною фрезерною наладкою і похибка базуванні відсутня.
Вплив на точність обробки суміщення установчих та вимірювальних баз приведений на рис.5.20. При обробленні отворів з суміщенням установчої та вимірювальної баз на поверхні А (рис. 5.20а) і отриманням розмірів розташування осей від вимірювальної бази з точністю ±0,05 мм точність
133
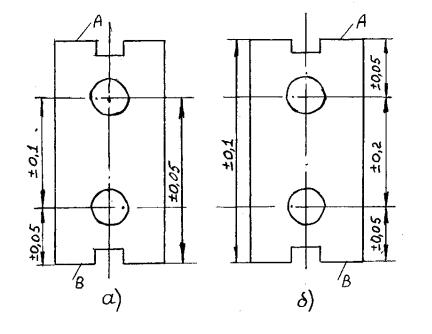
міжосьової відстані становить ±0,1 мм. Якщо при установчій базі В вимірювальна база при обробленні одного з отворів буде В а іншого А (рис. 5.20б), то на точність розміру на
Рис.5.20. Вплив суміщення установчих та вимірювальних баз на точність обробки
міжосьову відстань буде додатково впливати допуск на розмір між установчою та вимірювальною базами, який складає ±0,1 мм. Тому похибка на міжосьову відстань буде складати ±0,2 мм, що у два рази вище чим у випадку суміщення установчої та вимірювальної баз.
5.3. Способи установки заготовок
Існують різні способи установок заготовок при обробленні на верстатах. Одним із способів є установка заготовки безпосередньо на столі верстата
або в універсальному пристрої з вивіркою її розташування відносно вузлів верстата і інструмента. Цей спосіб застосовується в основному в одиничному та дрібносерійному виробництві і відзначається значною трудомісткістю, відповідно малою продуктивністю, потребує високої кваліфікації робітника.
Існує спосіб установки заготовки на столі верстата після попереднього розмічання. Розмічання заготовки здійснюється на спеціальній розмічальній
134
плиті для позначення розташування поверхонь деталі у заготовки з метою щоб припусків для обробки кожної поверхні було достатньо. При розмічанні на заготовку наносять крейдову фарбу. Після висихання фарби на заготовку наносять лінії поверхонь, осей, центрів майбутньої деталі за допомогою штангенрейсмусу, циркуля, кутника, штангенциркуля а також інших вимірювальних інструментів. Для фіксації нанесених ліній уздовж них спеціальним інструментом (керном) наносять лунки. Розмічання потребує високої кваліфікації робітника. Установка заготовки після розмічання не забезпечує високу точність. Такий спосіб доцільно застосовувати при обробленні крупно габаритних складної форми заготовок у одиничному, дрібносерійному та важкому машинобудуванні.
У серійному, крупносерійному та масовому виробництвах установка заготовок при обробленні як правило здійснюється у спеціальних пристроях. Пристрої дозволяють, згідно принципу базування «правило шести точок», установити заготовку у задане положення і закріпити її з високою точністю і високою продуктивністю. Пристрої дозволяють значно скоротити час на установку заготовки, виключити попереднє розмічання, вести обробку на більш високих режимах різання, скорочують допоміжний час, дають можливість застосування автоматизації і механізації процесу механічної обробки. При установленні заготовок у пристроях точність виготовлення пристрою впливає на точність обробки поверхонь. Тому для забезпечення заданої точності обробки заготовок допуски на розміри деталей пристрою повинні бути, як правило, у два рази менші за допуски розмірів поверхонь, які оброблюються на даному пристрої.
На рис. 5.21 приведені способи установок заготовок по двом поверхням. На рис.5.21а заготовка установлена по двом паралельним плоским
поверхням. Стрілками показано напрямок сил затискання. Заготовка базується по плоскості А, а до плоскості В підводиться додаткова пружна опора –штифт 1 з пружиною 2, яка фіксується для підвищення жорсткості установки гвинтом 3 через вкладиш 4.
135
а
б
в
г
д
є
Рис. 5.21. Види установок заготовок по двом поверхням
На рис.5.21б заготовка установлена і базується по плоскій та циліндричній поверхням. При цьому плоска поверхня є установчою (опорною) базою, а циліндрична поверхня є напрямною базою.
На рис.5.21в заготовка установлена і базується по циліндричній поверхні, якою є палець 1, та плоскій поверхні 2. У цьому випадку застосовується ще клин 3 для компенсації зазору між плоскою поверхнею заготовки і пристрою, який виникає внаслідок похибки розміру між плоскою поверхнею і віссю циліндричного отвору заготовки.
136
На рис.5.21г заготовка теж установлена і базується по циліндричній та плоскій поверхням, але палець 1 зрізаний у напрямку розміру між плоскою поверхнею і віссю циліндричного отвору заготовки, що компенсує похибку цього розміру.
На рис.5.21д заготовка 1 установлена на дві циліндричні поверхні, якими служать пальці 2 і 3. Один з пальців для компенсації міжосьової похибки зрізаний. Для зручності установки пальці мають різну довжину.
Циліндричні заготовки при обробленні їх на свердлувальних і фрезерувальних верстатах базуються у пристроях як правило по зовнішнім розвинутим циліндричним поверхням (рис. 5.21є). У даному випадку для цього застосовуються призми опорні поверхні яких розташовані переважно під кутом α = 900 (див. рис. 5.14).
Для базування заготовок по плоским поверхням плоскі поверхні пристроїв заміняють точеними опорами
5.4.Теоретичні та технологічні схеми базувань заготовок
Для розроблення теоретичних та технологічних схем базувань заготовок стандартами передбачено позначення зв’язків, затискних та установчих устроїв, які приведені на рис. 5.22 (теоретичні зв’язки вид збоку - а і зверху - б, опора нерухома – в, опора рухома – г, опора плаваюча – д, опора регулююча - є, центр нерухомий – ж, центр обертальний – з, оправка циліндрична – к, оправка шарикова, роликова – л, оправка шліцьова – м, патрон поводковий – н, патрон кулачковий, цангова оправка з кількістю кулачків 2, 3, 4 – о, опора рухома з затисканням по призматичній робочій поверхні – п, патрони та оправки цангові
– р, оправка конічна роликова - с).
Для спрощення ескізів теоретичних та технологічних схем базувань зображення декількох однойменних опор або опорних точок, які розташовані на одній базовій поверхні, можуть бути показані одним символом з зазначенням
137

справа від нього кількості однойменних опор, які необхідні для відповідного розташування заданої поверхні (рис. 5.22).
Рис. 5.22. Приклади позначення одночасно декількох теоретичних зв’язків та декількох точених опор
в)
г)
д) є)
ж)
з)
і) |
к) |
л) |
138
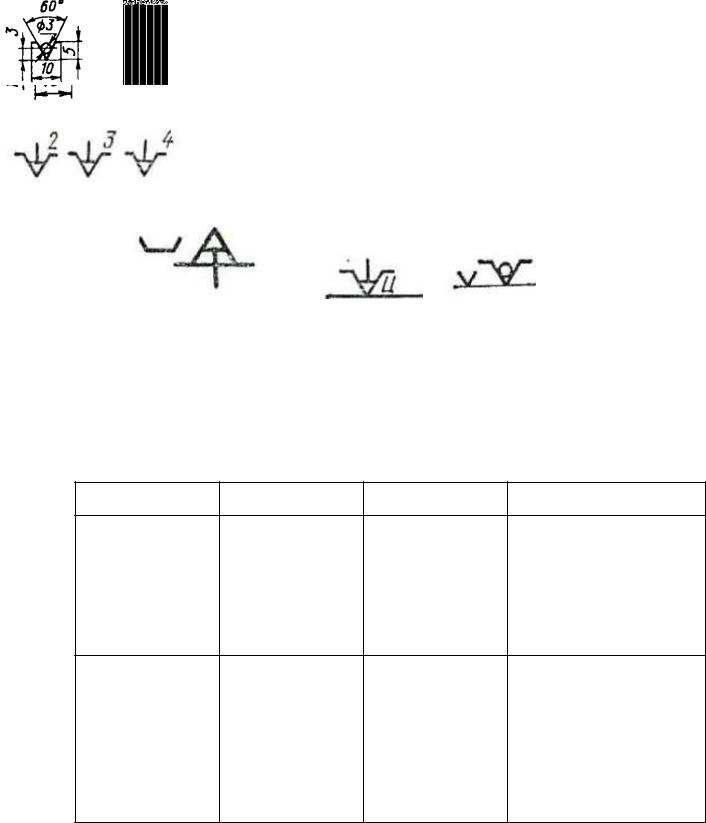
м) |
н) |
о) |
П) |
р) |
с) |
Рис. 5.23. Приклади позначень теоретичних зв’язків, опор та установчих устроїв
139
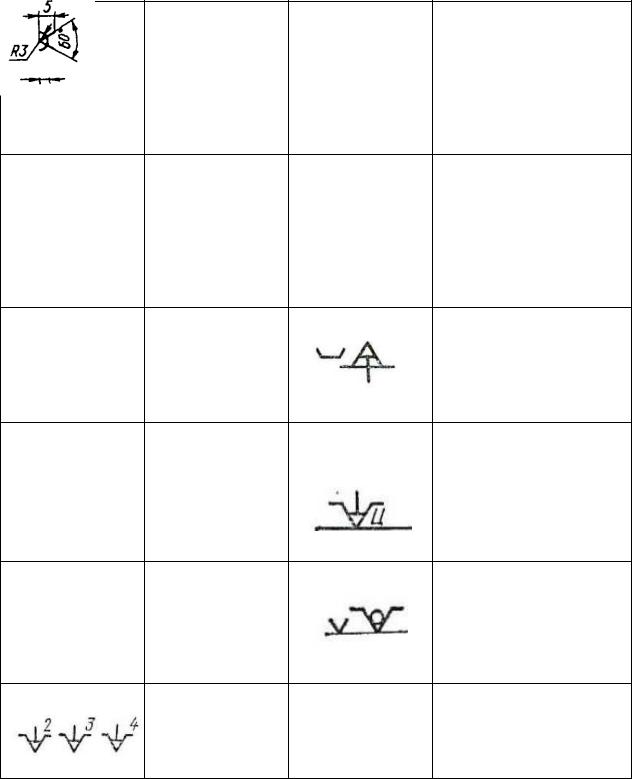
140