
Конспект лекций
.pdfЗагальні правила розробки технологічних процесів механічної обробки визначені відповідними стандартами (ГОСТ 14.301-83) і мають наступні етапи:
-аналіз вихідних даних, який полягає у вивченні конструкції, службового призначення та технічних вимог до якості;
-визначення типу виробництва;
-відпрацювання конструкції виробу на технологічність;
-визначення до якого типового класу відноситься виріб та вибір аналогів виробничих, типових або групових технологічних процесів;
-вибір економічних наборів методів обробки окремих поверхонь;
-вибір та обґрунтування способів отримання заготовки;
-вибір та розрахунки мінімальних припусків на обробку поверхонь в залежності від вибраних методів обробки і визначення її розмірів;
-розробка варіантів маршрутів обробки та визначення оптимального;
-вибір технологічних баз та розробка схем базування;
-детальна розробка окремих технологічних операцій;
-визначення оптимальних режимів різання;
-вибір обладнання, стандартних пристроїв, різальних та вимірювальних інструментів;
-нормування технологічних операцій;
-розробка технічної документації на виготовлення нестандартного оснащення операцій;
-техніко-економічний аналіз ефективності технологічного процесу;
-оформлення технологічної документації.
При розробленні технологічного процесу виготовлення деталі необхідно вивчити складальне креслення, у склад якого входить деталь та умови її роботи у вузлі машини та використати довідкову літературу, керівні галузеві і заводські матеріали, інструкції, нормативи. Технологічний процес розроблюють з прив’язуванням до конкретного підприємства, або для створення нового. У останньому випадку технолог має більше свободи у розробленні найбільш оптимального технологічного процесу.
191
Додаткові етапи розробки технологічних процесів виготовлення деталей, які відносяться до типових та групових технологій, регламентовані стандартами «Єдиної системи технологічної підготовки виробництва» 14.303-82 і 14.316-82.
7.1.2. Вивчення службового призначення деталі та аналіз технічних вимог та норм точності
Ефективна розробка технологічного процесу механічної обробки деталі неможлива без глибокого вивчення її службового призначення, умов роботи в вузлі машини та аналізу технічних вимог до якості, які визначені кресленням. Тому перед тим як приступити до проектування технологічного процесу механічного виготовлення деталі необхідно вивчити її креслення, складальне креслення, до якого входить деталь та сформулювати її службове призначення. При формулюванні службового призначення необхідно визначити конкретний перелік задач, для вирішення яких призначена деталь, та визначити умови, при яких вона повинна виконувати своє службове призначення на протязі усього терміну служби.
Технічні вимоги аналізують виходячи з умов службового призначення і креслення. Оцінюють обґрунтованість технічних вимог та можливі способи їх виконання та контролю. Виявляють найбільш точні вимоги до розмірів, форми поверхонь, їх взаємного розташування та шорсткості. Відповідно призначення деталі вивчають вплив її параметрів на якість складального виробу і визначають відповідність цих вимог службовому призначенню, а саме:
-твердість (НВ, HRC) поверхонь з урахуванням умов роботи;
-відповідність найбільшої точності розмірів службовому призначенню;
-обґрунтованість вимог до форми та взаємного розташування поверхонь;
-відповідність шорсткості вимогам до точності та службового
призначення.
Виконується класифікація поверхонь відповідно службового призначення.
192
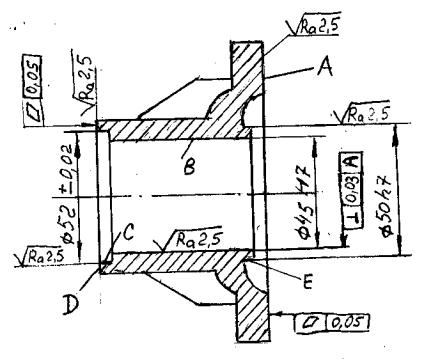
Рис. 7.1. Кришка На рис. 7.1 приведено креслення кришки редуктора. Поверхні А та В є
основними. Вони визначають розташування кришки у складальному вузлі, так як по площині А кришка приєднується до корпусу редуктора, а по поверхні Е здійснюється центрування по осі. Поверхні С і D є приєднувальні, так як визначають положенні інших деталей, які стикуються по цим поверхням. До цих поверхонь установленні найбільш жорсткі вимоги до точності. Стик кришки з корпусом редуктора по поверхні А і з іншою деталлю по поверхні D повинен бути герметичним, тому установлені відхилення від площини 0,05 відповідають умовам роботи кришки. Поверхня В стикується з опорним підшипником валу редуктора, тому точність розміру 45Н7 обумовлена посадкою з валом 45Н7/g6 та умовою роботи пари тертя. Отвір 52±0,02 призначений для установлення кільця з метою ущільнення. Його точність обумовлена забезпеченням герметичності з’єднання (течія мастила). Відхилення від ┴ 0,03 поверхні В відносно поверхні А витікає з аналізу складального креслення. Це обмеження забезпечує лінійний контакт між поверхнями із-за можливого перекосу осей отворів кришки та корпусу при складанні. Шорсткість Ra 2.5 поверхонь А,В, С і Е відповідає нормам точності
193
отворів та умовам герметичності. Результати проведеного аналізу використовуються при проектуванні технологічного процесу виготовлення деталі та вибору засобів контролю.
Визначають якими засобами можна забезпечити виконання кожної вимоги по точності та шорсткості.
Наприклад:
-обробка литого отвору 45Н7(+0,027) і Ra 2.5 може бути забезпечено таким набором методів обробки: а) зенкерування попереднє, б) зенкерування чистове, в) розвертання попереднє, г) розвертання чистове;
-Забезпечення перпендикулярності осі отвору 45Н7 відносно площини А (┴0,03) здійснюється застосуванням у якості установчої бази при обробленні поверхні В поверхні отвору А.
7.1.3. Визначення типу виробництва Приблизно тип виробництва можна визначити керуючись довідниковими
таблицями, які складені на основі роботи багатьох виробництв (таблиця 7.1).
Приблизний вибір типу виробництва
|
Крупні вироби |
Вироби середніх |
Дрібні вироби, до |
Типи виробництв |
важкого |
розмірів, від 20 кг |
20 кг |
машинобудування, |
до 300 кг |
|
|
|
|
||
|
більше 300 кг |
|
|
|
|
|
|
|
|
Кількість виробів |
|
|
|
|
|
Одиничне |
<5 |
<10 |
<100 |
|
|
|
|
Дрібносерійне |
5 - 100 |
10 - 200 |
100 - 500 |
|
|
|
|
Середньосерійне |
100 - 300 |
200 - 500 |
500 - 5000 |
|
|
|
|
Крупносерійне |
300 - 1000 |
500 - 5000 |
5000 – 50 000 |
|
|
|
|
Масове |
1000 |
5000 |
50 000 |
|
|
|
|
194
Крім того тип виробництва прийнято визначати відповідно рекомендаціям стандарту (ГОСТ 14.004-83 у редакції 1988 р.) за коефіцієнтом закріплення операцій Кзо. Цей коефіцієнт визначає ступінь спеціалізації робочих місць і визначається за формулою 2.2.
Основною формою організації крупносерійного та масового виробництва служить потокова форма. При потоковій формі на одному робочому місці виконується одна технологічна операція, а обладнання розташоване по ходу технологічного процесу. Для організації безперервного потоку необхідна однакова або кратна тривалість кожної операції. Якщо досягнути однакову або кратну тривалість досягти не вдається, то це приводить до не однакого завантаження обладнання. Досягнення однакової тривалості на кожному робочому місці можна досягти як диференціацією так і концентрацією технологічних переходів.
Диференціацією операцій називається побудова операцій з невеликої кількості простих технологічних переходів. Тому технологічний процес побудований по цьому принципу складається з великої кількості простих операцій. При диференціації є можливість розділити не точні чорнові і точні чистові переходи та виконувати їх на відповідному за точністю обладнанні. Крім того диференціація операцій дає можливість застосування автоматичних ліній, які складаються з простих вузькоспеціалізованих продуктивних верстатів.
Концентрацією операцій називається з’єднання декількох простих технологічних переходів у одну складну операцію. Таку операцію можна виконувати на багато інструментальному обладнанні з заміною установ позиціями. При цьому значно скорочується основний та допоміжний час на обробку і скорочується тривалість виробничого циклу. Вимоги до кваліфікації робітників високі. В умовах одиничного і дрібносерійного виробництва як правило застосовують концентрацію операцій, яка виконується високо кваліфікованими робітниками. У крупносерійному виробництві технологічні операції, які побудовані по принципу концентрації виконуються на верстатах з ЧПК та оброблювальних центрах.
195
В умовах крупного та важкого машинобудування технологічні процеси будуються, як правило, по принципу концентрації.
Характерною особливістю серійного виробництва є обробка деталей партіями. Кількість деталей у партії може визначатись з умов безперебійної роботи складальних цехів. Виходячи з цього кількість деталей у партії приблизно визначають за формулою (Єгоров с.127)
n = |
Dt |
, |
(7.1) |
|
|||
|
Ф |
|
де: D – кількість деталей відповідно річній програмі разом з запасними частинами; t – кількість днів на які потрібно мати запас деталей на складі; Ф – число робочих днів на рік.
7.1.4. Відпрацювання конструкції виробу на технологічність
Технологічність конструкції виробу являється одною з властивостей, яка дає можливість знизити трудомісткість виготовлення та собівартість. Досвід машинобудування показує, що можна шляхом покращення технологічності конструкції виробу знизити трудомісткість виготовлення на 15 – 25 % і знизити собівартість на 5 – 6%. Поняття технологічності також розповсюджується на процеси технічного обслуговування та ремонту.
Правила, за якими повинно здійснюватись відпрацювання виробу для поліпшення технологічності, регламентується стандартом (ГОСТ 14.201-83). Цими документами установлені основні правила відпрацювання виробу на технологічність, послідовність їх вирішення і системи показників технологічності конструкції виробу.
Відпрацьовуючи конструкцію виробу на технологічність необхідно привести її до рівня, який відповідав би сучасному рівню техніки. При збереженні якості службового призначення конструкція повинна відповідати умовам при яких є можливість застосування сучасних економічних і продуктивних методів виготовлення та умовам мінімальних витрат при її експлуатації та ремонту. Технологічність форм деталі оцінюють з урахуванням
196
вибраних методів обробки, типу виробництва та технологічних можливостей і властивостей обладнання конкретного виробництва. При цьому важливим резервом підвищення продуктивності обробки є при можливості спрощення конфігурації деталі з метою уніфікації різального інструменту, спрощення умов його роботи, можливості застосування багато інструментальної обробки та зменшення об’єму механічної обробки.
Поняття технологічності конструкції не може бути абсолютним. Воно змінюється разом з розвитком технології і самого виробництва. Об’єктивна оцінка технологічності може визначатися кількісними показниками. Приклади поліпшення технологічності та способи її оцінки приведені у розділі 3.
7.1.5. Вибір економічних наборів методів обробки окремих поверхонь
Метою розробки технологічного процесу виготовлення деталі являється вибір таких способів і засобів обробки її поверхонь, які дозволяють самим коротким та економічним шляхом перетворити заготовку у деталь і забезпечити при цьому її якість по усім показникам.
Ідеальним вирішенням цієї задачі булоб перетворення заготовки в деталь шляхом обробки її кожної поверхні за один перехід, якщо тільки сама заготовка не відповідає вимогам готової деталі. На жаль, поки що, в більшості виподків для забезпечення необхідної якості деталі потрібна обробка поверхонь заготовки за декілька переходів.
На вибір способів обробки і необхідної кількості переходів впливають: вимоги до якості готової деталі; особливості та якість заготовки; серійність виробництва; техніко-економічні показники способів обробки.
Вибір способів та засобів обробки кожної поверхні заготовки треба починати з находження такої технологічної системи, яка дозволяє економічним шляхом досягти необхідної якості матеріалу та геометричної точності деталі. Але вибрана технологічна система в змозі забезпечити необхідну якість тільки при визначених вхідних значеннях характеристик заготовки.
Ступінь впливу технологічної системи на заготовку по показнику К в процесі її обробки чисельно виражається передаточним відношенням, яке прийнято називати коефіцієнтом уточнення
εк = |
Кз/ Кд |
(7.2) |
де |
Кд і Кз відхилення параметру К на вході та виході технологічної |
|
системи. |
|
|
У якості параметру |
К найбільш частіше застосовують відповідні допуски |
на розміри заготовки Тз та деталі Тд. Тому можна представити формулу 7.2 у вигляді
197
ε = Тз/ТКд |
(7.2) |
Загальне уточнення можна представити за формулою |
|
ε = Тз/ТКд = Тз/Т1*Т1/Т2****Ті-1/Ті****Тn-1/Тд = |
|
= ε1ε2***εі***εn |
(7.3) |
де ε – загальне уточнення; εі – окремі ступені уточнення; Тз, Тд, Ті – допуски параметру за яким здійснюється уточнення.
Піся кожної обробки (переходу) точність параметру (розміру) збільшується, тобто зменшується відповідний допуск . Величина коефіцієнту уточнення залежить від властивостей технологічної системи і методу обробки. Так для першого ступіню обробки (чорнова обробка) можна досягти коефіцієнта уточнення ε<6, для проміжних ступінів (напівчистова обробка) ε = 3÷4, для
чистової обробки з досягненням точності IT5..IT7 ε = 1,5…2.
Часто вимоги до якості деталі забезпечуються по етапно, вибираючи способи обробки, які дають необхідні результати по окремим показникам чи групам показників. При цьому не повинна порушуватися якість деталі, яка досягнута на попередніх етапах.
Застосовуючи поняття коефіцієнту уточнення до визначення числа переходів по обробці окремої поверхні занотовки, можна виявити не тільки їх склад, але і вимоги до вхідних значень характеристик якості заготовки на усіх переходах. Орієнтовне уявлення о значеннях перехідних відношень технологічних систем, по деяким показникам якості можна отримати в довіднику [3] з таблиць точності обробки та якості поверхонь деталей.
З практичного досвіду необхідне число переходів призначають на основі накопиченого досвіду. Установлено, що в залежності від вимог до якості по тим чи іншим показникам необхідно поверхню заготовки обробити більше чим одним способом, хоча з практичної точки зору бажано обробку різних поверхонь здійснювати одним способом.
Існує також метод найбільш спрямованого вибору числа ступенів обробки за формулою [4]
logε
n = 0,46 . (7.4)
Інший шлях пошуку економічно обґрунтованого набору методів обробки в залежності від технічних вимог полягає у використанні типових планів обробки поверхонь рекомендованих довідниками та технічною літературою. У відповідних таблицях наведені встановлені практикою комплекти параметрів якості на суміжних преходах (Руденко с.86). При розробленні технологічного
198
процесу бажано обробку однотипних поверхонь здійснювати спільно. Це змушує вносити відповідні корективи при виборі методів обробки однотипних поверхонь. Повторюємість методів обробки поверхонь, які належать одній деталі, дає змогу скоротити різноманітність різальних застосованих інструментів скласти технологічний процес за принципом концентрації операцій.
7.1.6.Вибір способів отримання заготовки та розрахунки мінімальних
припусків на обробку
Основні рекомендації по вибору способів отримання заготовок у хімічному машинобудуванні та апаратобудуванні приведені у розділах 4.1.1 та 4.2.1.
Визначення загальних та операційних припусків має велике технікоекономічне значення. Існують два основних способа визначення мінімальних припусків на обробку: розрахунково-аналітичний і дослідно-статистичний. Дослідно-аналітичний, запропонований професором Кованом В.М., приведений урозділах 4.1.2 та 4.2.2.
Дослідно-статистичний дозволяє визначити припуски по таблицям, які складені на основі узагальнення і систематизації роботи передових підприємств. Припуски при застосування цього методу не ураховують конкретні умови побудови технологічних процесів обробки заготовки. Величина припусків у цьому випадку буде завищеною, так як створюються непотрібні підвищені запаси надійності. Дослідно-аналітичний метод простий, але визначення припусків здійснюється без аналізу умов виконання операцій і тому не вирішує задач ефективної економії матеріалу. Цей метод в основному застосовується у одиничному і мало серійному виробництвах.
7.1.7.Розробка варіантів маршрутів обробки та визначення оптимального
199
Маршрут обробки деталі - це установлення способів обробки включаючи термічні, хіміко-термічні, гальванічні та контрольні і порядку їх застосування у технологічному процесі.
Технологічний процес механічної обробки деталі складається на основі типового або групового технологічних процесів. Для цього на основі технологічного класифікатора формують технологічний код деталі. Технологічний класифікатор деталей (ТКД) у машинобудуванні і апаратобудуванні є доповнення до класифікатора ЄСКД (ГОСТ 2.201-80). Технологічний маршрут проектують на основі вибраного аналогу - типового технологічного маршруту.
Види операцій можна скласти на основі вибраних наборів економічно доцільних методів обробки окремих поверхонь при досягненні заданої точності. При цьому необхідно у першу чергу керуватися типовою схемою раціональної послідовності етапів обробки заготовки , що узагальнює багаторічний досвід машинобудування [Руденко]. У першу чергу оброблюють комплекти чистових баз, які служать для установки заготовки на наступних операціях. Послідовність обробки інших поверхонь бажано здійснювати у напрямку підвищення їх точності. Розділяючи чорнову і чистову обробку у технологічному процесі на окремі етапи можна більш раціонально його здійснювати. Так чорнова обробка може виконуватись на менш точному або частково зношену обладнанні робітниками більш низької кваліфікації. Розрив у часі між чорновою та викінчувальними операціями частково зменшує внутрішні остаточні напруження і усуває деформацію деталі на останніх операціях. Але в деяких випадках чистову обробку здійснюють на ранніх стадіях технологічного процесу, якщо є вірогідність отримання браку із-за наявності внутрішніх дефектів і високій трудомісткості обробки всієї деталі. Кількість етапів обробки для конкретної деталі може бути різною в залежності від конструктивних особливостей деталі, виду матеріалу заготовки, точності розмірів поверхонь, точності форм і взаємного розташування поверхонь, шорсткості поверхонь та способів термообробки. На кількість етапів оказує токож вплив застосування
200