
РАМАЗАНОВА К.Р
..pdf31
отходов для современного производства является недопустимым как по экономическим, так и по экологическим соображениям. Трудность переработки фенольной смолы термическим крекингом (происходит коксование), при использовании в качестве котельного топлива, в технический углерод – наполнитель композитов и в другие высоколиквидные продукты промышленного назначения, связана с высоким содержанием в ней сульфата натрия, что ограничивает область её широкого использования в качестве сырья [1а, 70, 71]. Известный промышленный способ обессоливания фенольной смолы до содержания иона натрия 0,003 масс.% [147] имеет ряд недостатков, среди которых - многоступенчатость и множество рециклов водного слоя, образование стойкой межфазной эмульсии и осложнение фазового разделения органического и водного слоя, повышенный расход эфира, энергоёмкость и длительность проведения процесса при температуре 40-50°С, сложность и громоздкость аппаратурного оформления с низкой производительностью и т. д. Поэтому разработка эффективного процесса регенерации или обессоливания фенольной смолы с целью повышения её качества до содержания ионов натрия 6•10-4 масс.% и расширения области применения в качестве функциональных добавок к композитам является актуальной и первостепенной задачей кумольного процесса синтеза поликонденсационных мономеров.
В настоящее время проблема переработки и утилизации органических некондиционных продуктов или отработанных растворителей, содержащих ацетон, является одним из актуальных экологических вопросов для промышленных предприятий. Поэтому создание установки регенерации ацетона и других растворителей из органических отходов или отработанных растворителей промышленных предприятий является важной и актуальной задачей экономического и экологического характера.
К проблемам принципиального характера современного кумольного процесса синтеза поликонденсационных мономеров [1а, 27-36, 70-77] относится использование низко селективного и коррозионно-активного гомогенного катализатора - катализаторного комплекса на основе хлорида алюминия на стадии получения кумола и серной кислоты на стадии разложения технического ГПК. При этом следствием являются образование множества побочных продуктов, ухудшение и нестабильное качество целевых продуктов, трудно утилизируемых органических отходов и экологически опасных сточных вод, необходимость организации многократных рециклов, их нагрева, охлаждения и транспортировки, громоздкость аппаратурного оформления. Применение гомогенных кислотных катализаторов приводит к усиленной коррозии и большим капитальным затратам на ремонт оборудования, необходимости периодической пропарки оборудования от минеральных отложений, переработки сточных вод, высоким расходным коэффициентам сырья на 1 тонну конечных продуктов, затратам холода и тепла, воды и энергии. Прямые энергетические затраты в себестоимости целевых продуктов составляют более 30 %, хотя основные стадии кумольного процесса протекают с выделением большого количества тепла более – 900 кДж на кг бензола на стадии алкилирования и более 2000 кДж на кг ГПК на стадии разложения, которые не используются в процессе синтеза поликонденсационных мономеров. Эти обстоятельства сдерживают и не позволяют существенно наращивать объёмы производства поликонденсационных мономеров, особенно в России. Поэтому разработка на активных и высокоселективных гетерогенных катализаторах безотходного кумольного процесса синтеза кумола алкилированием бензола пропиленом и поликон-
32
денсационных мономеров разложением технического ГПК, способного использовать экзотермический потенциал реакции, минимальным количеством рециклов с простотой аппаратурного оформления, которые позволяют увеличить производительность действующих или вновь проектируемых реакторов, является актуальной технологической и экологической задачей.
Проблемы сернокислотного процесса синтеза полимеризационных моно-
меров. Важной стадией процесса синтеза полимеризационных мономеров является стадия нейтрализации, от эффективности которой зависит качество (мет)акриловых мономеров. В условиях непрерывного производства одной из актуальных проблем является обеспечение стабильного качества товарного ММА и соответствие его требованиям ГОСТ 20370-74 по содержанию кислотных примесей (муравьиная, уксусная, метакриловая кислоты, диоксид серы, сульфированные органические примеси кислотного характера и др.), состав и концентрация которых зависят от технологического режима. Попадание кислотных примесей в товарный продукт, особенно метакриловой кислоты и диоксида серы, выше нормы существенно снижает стабильность ММА к полимеризации, требует увеличения дозы ингибитора при транспортировке и энергетических затрат на переработку на месте производства или потребления. Сложность нейтрализации кислотных примесей сырца ММА обусловлена тем, что априори неизвестны природа, состав и концентрация кислотных примесей, а также отсутствием инструментального контроля pH на стадии нейтрализации действующего производства ММА.
Поэтому разработка физико-химических основ процессов, протекающих при фазовом разделении и очистке сырца (мет)акриловых мономеров от кислотных примесей раствором соды с практическими рекомендациями по устранению причин повышения кислотности, является актуальной технологической задачей для стабилизации качества выпускаемого ММА.
Сложности при нейтрализации кислотных примесей сырца ММА связаны:
-с трудоёмкостью приготовления раствора соды (ручная загрузка соды);
-с неэффективным режимом смешения сырца ММА и содового раствора; отсутствием контроля рН в процессе нейтрализации;
-с перерасходом соды, перещелачиванием, образованием трудноразделимой межфазной эмульсии эфир-вода;
-с высоким содержанием кислотных примесей и низкой степенью чистоты
ММА;
-с загрязнением сульфатом натрия сернокислотного маточника.
Поэтому разработка физико-химических основ «бессульфатного» процесса проведения исследований по замене содового раствора на аммиачный раствор, разработка технологии нейтрализации кислотных примесей с повышением качества или чистоты ММА по содержанию основного вещества без диоксида серы и создание промышленной установки с внедрением в действующее производство ММА являются актуальными технологическими задачами.
Бесперебойное обеспечение производства полимеров и их композитов мономерами требует для (мет)акрилатного комплекса постоянного совершенствования технологического процесса переработки сернокислотного маточника, поиска новых направлений и внедрения передовых технологий.
33
До сих пор основное внимание исследователей было уделено термическому разложению разбавленных растворов сернокислотного маточника с повышенным содержанием воды и приблизительным составом регламентных значений органических примесей с целью регенерации серной кислоты, которые вообще-то предназначены для переработки в сульфат аммония. В литературе не уделено внимания исследованию качественного и количественного состава, природы органических примесей, зольности (содержания в нем металлов) концентрированного сернокислотного маточника (мет)акриловых мономеров, хотя и для разбавленных растворов сернокислотного маточника имеются недостаточные сведения и отсутствует системный анализ примесей. В России, несмотря на многочисленные теоретические и экспериментальные разработки, подробно рассмотренные нами в обзоре [1а], для предприятий нефтепереработки и нефтехимии, основанных на сернокислотных процессах, так и не созданы отечественная технология и промышленная установка регенерации серной кислоты из отработанной серной кислоты [1а, 102, 153-181].
Поэтому исследование физико-химических свойств, органического и неорганического состава, природы органических примесей концентрированного сернокислотного маточника является актуальной проблемой для обоснованного выбора направления переработки.
В России единственным методом является переработка растворов сернокислотного маточника (мет)акриловых мономеров в сульфат аммония (СА). Проблемой действующей технологии [1а, 97, 98] является получение низкого качества сульфата аммония из-за наличия загрязнений органическими примесями и присутствия в фракционном составе значительного количества мелких фракций, склонных к слёживанию при хранении, хотя известны методы укрупнения кристаллов в процессах нейтрализации и кристаллизации под действием иона металлов, к примеру, иона алюминия [1а]. Кроме того, влияют переход органических примесей в процессе переработки из жидкого в твёрдое взвешенное состояние, малое время пребывания насыщенного раствора в кристаллоприёмнике, что явно недостаточно для роста и выхода крупных кристаллов, измельчение их в циркулирующем растворе, забивка ими и взвешенными полимерами оборудования. Поэтому выявление причин образования мелких кристаллов и перехода органических примесей в твёрдое состояние, положительного влияния иона алюминия на укрупнение кристаллов на стадии нейтрализации и кристаллизации, установление оптимальных технологических критериев переработки, разработка научно-практических рекомендаций их устранения, с апробированием при опытно-промышленных испытаниях являются актуальными технологическими задачами.
Главной проблемой действующей технологии переработки сернокислотного маточника в сульфат аммония [1а, 97, 98] является малый период производственного цикла (2-3 суток) из-за накопления в циркулирующем насыщенном растворе растворенных органических примесей от 2-3 до 24 масс.% с повышением его вязкости от 0,075 до 1,1 мм2/с, что снижает коэффициент диффузии сульфата аммония к поверхности растущего кристалла с получением к концу производственного цикла мелких и тёмных кристаллов сульфата аммония низкого качества, загрязнённых органическими примесями, и приводит к технологическим затруднениям переработки, вынужденной остановке переработки для откачки из рецикла 150-250 м3 отработанного раствора с содержанием до 36% сульфата аммония и до 24 масс.% органических
34
примесей на шламонакопитель. Предложенные способы переработки отработанного раствора [1а] не устраняют главного недостатка – накопления органических примесей в рецикле рабочего раствора и малого периода производственного цикла, и они настолько неэффективны, экологически опасны с получением загрязнённого примесями сульфата аммония и пластификатора, что не нашли применения в промышленности. В настоящее время из-за переполнения до предельного уровня отработанным раствором шламонакопителей в России производства (мет)акриловых мономеров приостановлены. Поэтому исследование процесса и разработка физико-химических и технологических основ безотходной технологии переработки сернокислотных отходов производства (мет)акриловых мономеров с очисткой от органических примесей и получением из них качественной функциональной добавки для композитов, а также повышение качества сульфата аммония являются приоритетной технологической и экологической задачей, прежде всего для создания предпосылок реанимации сернокислотного процесса синтеза полимеризационных мономеров в России.
Проблемы синтеза ПМА присадок. (Мет)акриловые мономеры из-за присутствия в них кислотных примесей характеризуются лабильностью или способностью
кполимеризации при транспортировке, поэтому актуальна проблема дальнейшей их глубокой переработки на месте их производства, например, в полимерные присадки
кнефти и нефтепродуктам. Сернокислотный периодический процесс производства ПМА присадок [1а] не выдерживает никакой критики в экологическом, технологическом плане и по качеству конечного продукта. Промышленный периодический способ синтеза АМА на боргидриде натрия или его эфире [1а, 64] характеризуется многостадийностью и энергоёмкостью. При этом требуется предварительная осушка сырья из-за чувствительности катализатора к влаге с выделением водорода, снижение его активности и превращение в гелеобразную массу, что затрудняет отделение отработанного катализатора фильтрацией, а также возникают проблемы утилизации отходов жидких в виде азеотропов и загрязнённых твёрдых - отработанного катализатора и осушителя.
Визвестных промышленных процессах синтеза на второй стадии получение ПМА присадок полимеризацией АМА в масле [65, 67-69] связано с предварительным приготовлением смеси мономера и инициатора, использованием дополнительного серосодержащего агента переносчика полимерной цепи, проведением полимеризации дробной загрузкой и дробной дозировкой реакционной смеси. При этом возникают проблемы стабилизации температурного режима экзотермического процесса полимеризации. При этом неконтролируемы нагрев и контролируемое охлаждение реакционной массы приводит к нестабильному качеству ПМА присадки по молекулярным характеристикам, неэффективному использованию тепла экзотермической реакции из-за конструктивного несовершенства аппаратурного оформления. В промышленных условиях реализация процедур дробной загрузки и дробной дозировки при полимеризации является сложной и нетехнологичным процессом усложняющим выдерживание оптимальных параметров полимеризации [65, 67-69]. Поэтому исследование и разработка безотходного непрерывного процесса синтеза АМА из ММА на термостойком катионите, разделения азеотропа с возвратом ММА на стадию синтеза и получения метанола, полимеризацией АМА в масле и синтез стабильных по качеству ПМА присадок, установление регулируемых технологических параметров реакции синтезов являются актуальными технологическими и экологическими задачами.
35
Таким образом, проведённый анализ литературы и промышленных технологий показал следующие нерешённые технологические и экологические проблемы в производстве метакриловых мономеров и полиалкилметакрилатов на базе кумольного производства фенола:
1.В России базовое кумольное производства фенола, на основе его побочного продукта ацетона – сернокислотное производство метакриловых и алкилметакриловых мономеров, а также производство полиалкилметакрилатов или ПМА присадок имеют низкий технический и экологический уровень. В кумольной технологии на основных стадиях до сих пор используются низко селективные и коррозионноактивные гомогенные катализаторы – катализаторный комплекс хлорида алюминия на 1-ой стадии и серная кислота на заключительной 3-ей стадии. Это приводит к образованию трудно утилизируемых отходов, сточных вод и множества побочных продуктов, требующих организации рецикловых потоков, их нагрева и охлаждения, связанные с энергетическими затратами, а также попаданием их в виде примесей в целевые продукты, извлекаемые из многокомпонентной смеси. При этом с органическими отходами и газовыми выбросами теряются безвозвратно и ценные целевые продукты. Также отсутствуют оценки кинетики накопления серосодержащих примесей в промышленных потоках производства кумола и не выработаны критерий качества углеводородного сырья (бензола и пропилена) по их содержанию для стабильного производства качественных поликонденсационных мономеров (фенола и ацетона) по кумольной технологии.
2.До сих пор не разработаны эффективные технологий повышения качества основного отхода кумольного производства – фенольной смолы, а известные технологии регенерации (обессоливания) громоздки в аппаратурном оформлении и энергозатратны с низким качеством обессоленной фенольной смолы, а для неликвидного отхода – алюмохлорида вообще отсутствует технология переработки.
3.В России для сернокислотной технологии производства метакриловых мономеров единственным направлением переработки сернокислотных отходов (маточников) является переработка их в сульфат аммония, который имеет малый период производственного цикла 2-3 суток с последующей остановкой для вывода отработанного раствора на шламонакопитель. В настоящее время в России из-за заполнения шламонакопителей отработанным раствором – производства метакриловых мономеров приостановлены. С другой стороны, несмотря на многочисленные теоретические
иэкспериментальные разработки, в России для предприятий нефтепереработки и нефтехимии, основанных на сернокислотных процессах, так и не созданы отечественная технология и промышленная установка регенерации серной кислоты отработанной серной кислоты, в частности, из сернокислотных маточников метакриловых мономеров.
4.Существующая технология получения полиалкилметакрилатов или ПМА присадок реализуется в две стадии, где на 1-ой при использовании в качестве катализатора серной кислоты образуется на 1 тонну алкилметакрилового мономера 2 тонны токсичного жидкого отхода. При использовании гетерогенного катализатора – боргидрида натрия весьма чувствительного к влаге и кислотным примесям ММА (выделяется взрывоопасный водород, катализатор резко активность, превращаясь в геле подобную массу), что усложняет процесс, который становится периодическим и многостадийным. При этом отогнанный азеотроп метанола с ММА сжигается, а от-
36
фильтрованные от реакционной массы осушители и геле подобный катализатор направляются в отвал. Технология полимеризации, которая применяется на 2-ой стадии получения полиалкилметакрилата, связанная с предварительным приготовлением и подогревом реакционной смеси с инициатором связана с трудностью управления температуры экзотермического процесса полимеризации, что приводит к невоспроизводимым по молекулярным характеристикам синтезируемого полимера, как следствие, эксплуатационным свойствам ПМА присадок.
5. Отсутствуют экспресс-методы аналитического контроля в цеховых условиях роданида натрия в технологических растворах солевого или роданидного способа получения акрилового волокна/жгутика, а также ММР акриловых сополимеров – ПАН волокно/жгутик, поли-м-фениленизофталамида – волокно фенилон и др.
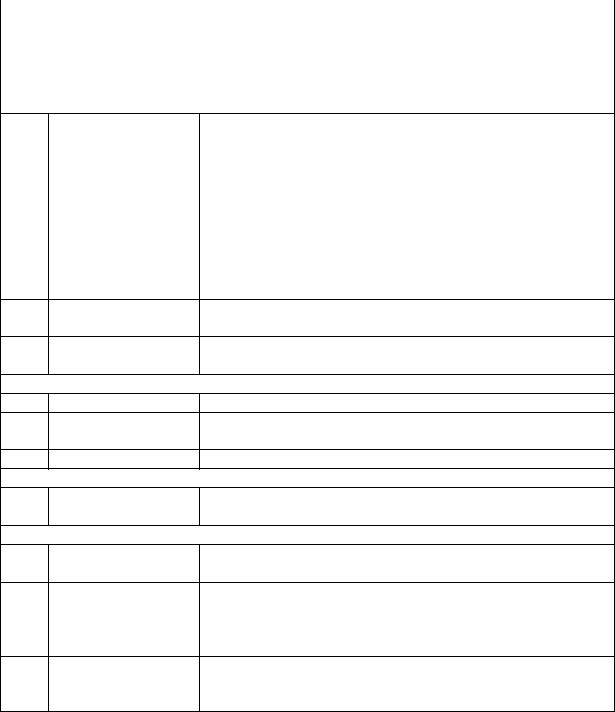
37
Глава 2. ОБЪЕКТЫ И МЕТОДЫ ИССЛЕДОВАНИЯ
2.1. Физико-химические и эксплуатационные свойства объектов исследований (сырья, полупродуктов и продуктов производства)
Физико-химические и эксплуатационные свойства объектов исследований (сырья, полупродуктов и продуктов производства), а также методы и методики исследований соответствовали нормативам отечественных стандартов и другим нормативнотехническим документациям (табл. 2.1).
|
|
|
Таблица 2.1 |
|
|
Система нормативно-технической документации (стандартов), применённых |
|||
|
|
при решении поставленных в работе задач |
|
|
№ |
Нормативно- |
|
Название нормативно-технической документации (ГОСТ, |
|
|
техническая доку- |
|
ТУ, стандарт предприятия, технологический регламент, |
|
|
ментация |
|
методики выполнения измерений) |
|
1 |
2 |
|
3 |
|
1.Регуляторы проектирования любых объектов, включая материальные объекты
итехнологии их создания
1. |
ГОСТ Р СО/МЭК |
Информационная технология. Системная инженерия. |
|
5268-2005 |
Процессы жизненного цикла системы |
2. |
ГОСТ Р ИСО |
Система автоматизации производства и их интеграция. |
|
10303-46-2002 |
Представления данных об изделии и обмен этими данны- |
|
|
ми. Часть 46. Интегрированные обобщённые ресурсы. Ви- |
|
|
зуальное представление |
3. |
ГОСТ Р ИСО |
Система автоматизации производства и их интеграция. |
|
10303-11-2000 |
Представления данных об изделии и обмен этими данны- |
|
|
ми. Часть 11. Методы описания. Справочное руководство |
|
|
по языку EXPRESS |
4.ГОСТ Р 53723-2009 Информационные технологии. Руководство по примене-
нию ГОСТ Р 53625-2009 (ИСО/МЭК 19796-1:2005).
5. ГОСТ Р 52292-2004 Информационная технология. Электронный обмен информацией. Термины и определения
2.Электронная модель исследования
6.ГОСТ 2.052-2006 ЕСКД. Электронная модель изделия. Общие положения
7.ГОСТ 2.102-68 ЕСКД. Виды и комплектность конструкторских докумен-
тов
8.ГОСТ 2.103-68 ЕСКД. Стадия разработки
3.Стандарты проведения НИР
9.ГОСТ 7.32-2001 СИБИД. Отчёт о научно-исследовательской работе.
Структура и правила оформления
4.Стандарты на создание новых видов продукции
10.ГОСТ Р 15.000-94 Система разработки и постановка продукции на произ-
водство. Основные положения
11.ГОСТ Р 15.201Система разработки и постановка продукции на произ-
2000 |
водство. |
Продукция |
производственно-технического |
|
назначения. Порядок разработки и постановки продукции |
||
|
на производство |
|
12.ГОСТ Р 15.011-96 Система разработки и постановка продукции на произ-
водство. Патентные исследования. Содержание и порядок проведения
|
|
38 |
|
|
|
1 |
2 |
3 |
13. |
ГОСТ Р 53791-2010 |
Ресурсосбережения. Стадии жизненного цикла изделий |
|
|
производственно-технического назначения. Общие поло- |
|
|
жения |
|
5. Стандарты на организацию производства |
|
14. |
ГОСТ Р 1.0-2004 |
Стандартизация в Российской Федерации. Основные по- |
|
|
ложения |
15. |
ГОСТ Р 150995.0.1- |
Технологическое обеспечение создания продукции. Ос- |
|
96 |
новные положения |
16. |
ГОСТ Р 150995.3.1- |
Технологическое обеспечение создания продукции. Тех- |
|
96 |
нологическая подготовка производства |
17. |
ГОСТ 14.322-83 |
Нормирование расхода материалов. Основные положения |
|
|
(с Изменением N 1) |
18. |
ГОСТ Р ИСО |
Менеджмент организации. Системы менеджмента изме- |
|
10012-2008 |
рений. Требования к процессам измерений и измеритель- |
|
|
ному оборудованию |
19. |
Р 50.1.051-2010 |
Система сертификации ГОСТ Р. Регистр систем качества. |
|
|
Порядок сертификации производств |
20. |
ГОСТ Р ИСО/МЭК |
Общие требования к компетентности испытательных и |
|
17025 -2009 |
калибровочных лабораторий |
|
6. Стандарты обеспечения качества |
|
21. |
ГОСТ Р ИСО 9000- |
Системы менеджмента качеств. Основные положения и |
|
2008 |
словарь |
|
7. Стандарты изготовления композиционных материалов |
|
22. |
ГОСТ Р 50583-93 |
Материалы композиционные полимерные. Номенклатура |
|
|
показателей |
23. |
ГОСТ 25.604-82 |
Расчёты и испытания на прочность. Методы механиче- |
|
|
ских испытаний композиционных материалов с полимер- |
|
|
ной матрицей (композитов). Метод испытания плоских |
|
|
образцов на растяжение при нормальной, повышенной и |
|
|
пониженной температурах |
|
8. Измерение электропроводности |
|
24. |
ГОСТ 30501-97 |
Материалы электроизоляционные твёрдые. Метод изме- |
|
|
рения электрического сопротивления и удельного сопро- |
|
|
тивления при повышенных температурах |
25. |
ГОСТ 6433.2-71 |
Материалы электроизоляционные твёрдые. Методы опре- |
|
(СТ СЭВ 2411-80) |
деления электрического сопротивления при постоянном |
|
|
напряжении |
|
9. Стандарты на объекты, сырье, полупродукты и продукты |
|
26. |
ГОСТ 9572-93 |
Бензол нефтяной. Технические условия. |
27. |
ГОСТ 8448-78 |
Бензол каменноугольный и сланцевый. Технические |
|
|
условия |
28. |
ГОСТ 25043-87 |
Пропилен. Технические условия |
29. |
ГОСТ 20491-75 |
Изопропилбензол технический. Технические условия |
30. |
ГОСТ 23519-93 |
Фенол синтетический технический. Технические условия |
31. |
ГОСТ 2768-84 |
Ацетон технический. Технические условия |

39
32.ГОСТ 13198-77 Ацетонциангидрин технический. Технические условия
1 |
2 |
3 |
33. |
ГОСТ 2222-95 |
Метанол технический. Технические условия |
34. |
ГОСТ 20370-74 |
Эфир метиловый метакриловой кислоты. Технические |
|
|
условия |
35. |
ГОСТ 19627-74 |
Гидрохинон (парадиоксибензол). Технические условия. |
36. |
ГОСТ 1625-89 |
Формалин технический. Технические условия |
37. |
ГОСТ 19710-83 |
Этиленгликоль. Технические условия |
|
|
|
38. |
ГОСТ 8581-78 |
Масла моторные для автотракторных дизелей. Техниче- |
|
|
ские условия |
|
|
|
39. |
ГОСТ 10585-75 |
Топливо нефтяное. Мазут. Технические условия |
40. |
ГОСТ 20799-88 |
Масла индустриальные. Технические условия |
41. |
ГОСТ 2184-77 |
Кислота серная техническая. Технические условия |
42. |
ГОСТ 6221-90 |
Аммиак жидкий технический. Технические условия |
43. |
ГОСТ 5100-85 |
Сода кальцинированная техническая. Технические усло- |
|
|
вия |
44. |
ГОСТ 19397-99 |
Купорос медный. Технические условия |
45. |
ГОСТ 20298-74 |
Смолы ионообменные. Катиониты. Технические условия |
46. |
ГОСТ 10900-84 |
Иониты. Методы определения гранулометрического со- |
|
|
става. Технические условия |
47. |
ГОСТ 10898.1-84 |
Иониты. Методы определения влаги |
48. |
ГОСТ 20255.1-84 |
Иониты. Метод определения статической обменной ёмко- |
|
|
сти |
49. |
ГОСТ 18995.2-7 |
Продукты химические жидкие. Метод определения пока- |
|
|
зателя преломления |
|
|
|
50. |
ГОСТ 13380-81 |
Нефтепродукты. Метод определения микропримесей серы |
51. |
ГОСТ 21261 |
Нефтепродукты. Метод определения высшей теплоты сгорания |
|
|
и вычисление низшей теплоты сгорания |
52. |
ГОСТ 3900-85 |
Нефть и нефтепродукты. Методы определения плотности |
53. |
ГОСТ 33-82 |
Нефтепродукты. Метод определения кинематической и |
|
|
расчёт динамической вязкости |
|
|
|
54. |
ГОСТ 20284-74 |
Нефтепродукты. Метод определения цвета на колоримет- |
|
|
ре ЦНТ |
|
|
|
55. |
ГОСТ 6258-85 |
Нефтепродукты. Метод определения условной вязкости |
|
|
|
56. |
ГОСТ 20287-91 |
Нефтепродукты. Метод определения температуры засты- |
|
|
вания |
|
|
|
57. |
ГОСТ 25371-97 |
Нефтепродукты. Расчёт индекса вязкости по кинематиче- |
|
|
ской вязкости. |
58. |
ГОСТ 2177-82 |
Нефтепродукты. Методы определения фракционного со- |
|
|
става |
59. |
ГОСТ Р 52487-2010 |
Материалы лакокрасочные. Определение массовой доли |
|
(ИСО 3521-2008) |
нелетучих веществ |
60. |
ГОСТ Р ИСО |
Воздух замкнутых помещений |
|
16000-52009. |
|

40
61. |
Сертификаты |
ком- |
|
|
пании Pohm |
and |
Полимерные катализаторы и ионообменные смолы |
|
Haas (ISO 9002) |
||
|
|
1 |
2 |
3 |
62.Сертификаты комИонообменные смолы пании Lanxess (ISO
9002)
10. Технические условия на объекты, сырье, полупродукты и продукты
63. ТУ 2411-51- Фракция пропиленовая
0566793-2000
64.ТУ 38.10276-87 Фракция пропиленовая
65. |
ТУ-38.402-62-140- |
Изопропилбензол (кумол) технический. Технические |
|
92 |
условия |
66. |
ТУ 6-01-2-88 марки |
Алюминий хлористый, безводный, технический |
|
А-1, А-5, А-15. |
|
67. |
ТУ 2414-020- |
Этилбензольная фракция. Технические условия |
|
47773778-2006 |
|
68. |
ТУ 2453-011- |
Смола полиалкилбензольная. Технические условия |
|
47773778-2004 |
|
69. |
ТУ 2411-019- |
Бутилбензольная фракция. Технические условия |
|
47773778-2006 |
|
70. |
ТУ 2152-005- |
Алюмохлорид. Технические условия |
|
47773778-2002 |
|
71. |
ТУ 2424-020- |
Смола фенольная. Технические условия. (ООО «Сарато- |
|
05757601-98 |
воргсинтез») |
72. |
ТУ 2424-018- |
Альфаметилстирол. Технические условия |
|
47773778-2006 |
|
73.ТУ 38.402-62-133- Эфир диизопропиловый. Технические условия
92
74. ТУ 2181-008- Сульфат аммония, побочный продукт акрилатных произ- 47773778-2003 водств. Технические условия
75.ТУ 6-01-24-63-82 Пластификатор бетонных смесей
76.ТУ 6-09-01-744-88 Фосфорно-вольфрамовая кислота (Н3РW12О40• nН2О).
Технические условия
77.ТУ 6-09-638-80 Цезий углекислый квалификации чистый, химически чи-
стый (цезий карбонат). Технические условия
78.ТУ 6-01-270-94 Присадка полиметакрилатная марки «Д». Технические
|
|
условия |
79. |
ТУ 6-09-13-930-87 |
Лаурилмеркаптан (регулятор молекулярной массы). Тех- |
|
|
нические условия |
|
|
|
80 |
ТУ 6-09-3840-74 |
Азобисизобутиронитрил (порофор ЧХЗ-21). Технические |
|
|
условия |
|
|
|
81. |
ТУ 6-09-3506-78 |
Октанол-1. Технические условия |
11.Стандарты предприятия ООО «Саратоворгсинтез»
82.СТП-47773778- Маточник цеха метилметакрилата. Маточник отделения
16Т-2005 |
получения метилакрилата. Стандарт предприятия |