
- •Введение к учебнику «Производство гидротехнических работ»
- •4.1. Общие положения по выбору типа транспорта
- •4.2. Автомобильный транспорт
- •4.3. Другие виды транспорта
- •Конвейерный транспорт, конвейерные поезда
- •Трубопроводный контейнерный пневмотранспорт. Подвесные канатные дороги
- •4.4. Строительные дороги
- •10.1. Общие положения
- •10.2. Плотины с противофильтрационными элементами из асфальтобетона
- •10.3. Плотины с железобетонными экранами
- •10.4. Плотины с металлическими противофильтрационными элементами
- •10.5. Плотины с противофильтрационными элементами из геосинтетических материалов
- •10.6. Плотины на вечно мерзлом основании с мерзлотными противофильтрационными завесами
- •10.7. Плотины с завесами возводимыми методом струйной цементации
- •13.1. Общая классификация бетонов
- •ГЛАВА 25. Совершенствование технологии бетонных работ при возведении высоких бетонных плотин.
- •25.1. Особенности возведения высоких бетонных плотин и совершенствование технологий их бетонирования
- •25.2 Добавки для бетонов и их эффективность
- •25.3 Применение литых бетонов в гидротехническом строительстве
- •Тенденции совершенствования технологии строительства бетонных плотин из укатанного бетона
- •Дополнительная литература по Главе 10
- •Дополнительная литература по Главе 24
- •В параграфе 7.6 «Производительность экскаваторов» дан общий подход к определению оптимальных параметров забоев экскаваторов различных типов.
- •Объем захваченного ковшом грунта
РАЗДЕЛ III. ПРОИЗВОДСТВО БЕТОННЫХ РАБОТ
ГЛАВА 13. Бетон гидротехнических сооружений и требования, предъявляемые к нему
13.1. Общая классификация бетонов
Бетоном называется искусственный камень , получаемый в результате затвердевания смеси вяжущего, заполнителей (крупного и мелкого) и воды. Это один из строительных материалов, применяемый во всех видах строительства ,в том числе и в гидротехническом.
В зависимости от назначения и условий эксплоатации все бетоны можно разбить на три группы.
А) Обычные констукционные и конструкционно – теплоизоляционные бетоны,к которым не предъявляются какие-либо специальные требования, кроме прочности и плотности. Они подразделяются на:
-Тяжелые, плотностью 2500-2200 кг\ м.куб. -Облегченные, плотностью 2200-1800кг\ м.куб. -Легкие, плотностью 1800-500 кг \м.куб.
-Особо легкие, плотностью 500 и менее кг\м.куб.(для ограждающих теплоизоляционных конструкций)
Б) Тяжелые конструкционные бетоны для гидротехнического и транспортного строительств, которые должны обладать еще и специальными требованиями
В) Специальные бетоны, приготавляемые на основе особых вяжущих:
- Силикатные бетоны с вяжущими из смеси извести и тонкомолотого кремнезема при добавке пористых заполнителей, применяемые как теплоизолятор в ограждающих конструкциях.
-Жаростойкий бетон –для работы при воздействии высоких температур, приготовляемый из смеси цементов и жидкого стекла.
-Особо жесткие бетоны –для защиты от радиоактивного заражения с плотностью более 2500кг\ м. Куб с заполнителями из тяжелых горных пород, чугуна, стали.
-Фибробетоныбетоны с дисперсным армированием для увеличения сопротивляемости трещинообразованию. Фибра изготовляется из обрезков металлических или иных волокон диаметром 0,1- 0,5 мм и длиной 10-50 мм.
-Цементно полимерные бетоныэто цементные бетоны с добавками из различных органических
соединенийполимеров., имеющие повышенную прочность на растяжение и изгиб. - Полимербетоны с вяжущими из полимерных смол,имеющие высокую химическую и коррозионную стойкость
Для всех бетонов применяются добавки для регулирования технологических свойств бетонов, улучшения физико-механических свойств и экономии цемента.
В последнее время появились так называемые высоко прочные бетоны-это бетоны, приготовляемые из смеси с ограниченным водосодержанием и обладающин высокими эксплоатационными свойствами, высокой прочностью и долговечностью. Их прочность в возрасте 28 суток может достигать 150Мпа, морозостойкость 600 и более. Срок службы такого бетона превышает 100лет. Получение такого бетона требует применения новых материалов и технологий. В них используются композиционные вяжущие вещества, химические модификаторы структуры,активные минеральные компоненты и добавки
Появление высоко прочных бетонов открыло эру нового поколения зданий и сооружений, небоскребов с каркасом из монолитного бетона, большепролетных мостов, железобетонных платформ для добычи нефти и др.
13.2 Требования к бетонам гидротехнических сооружений
Особенности бетона и бетонных работ в гидротехническом строительстве
К гидротехническим сооружениям относят сооружения, находящиеся в воде или постоянно, или временно (периодически). Эти сооружения возводятся в самых различных условиях и помимо силовых воздействий подвергаются воздействиям воды, мороза, агрессивных сред, кавитации, увлажнению-высушиванию и т.д. Вследствие этого бетоны для гидротехнических сооружений
238
должны обладать свойствами, отличающими их от обычных бетонов, рассчитываемых в основном на силовые воздействия.
Так, эти бетоны должны обладать такими дополнительными свойствами, как водонепроницаемость, морозостойкость, кавитационная стойкость и трещиностойкость. Выполнение этих требований обеспечивается соответствующим подбором состава бетона, специальной технологией его приготовления и технологией производства бетонных работ.
Гидротехническое строительство в нашей стране характеризуется укладкой огромных объемов бетона. Особенно большие объемы бетонных работ имеют место на гидроузлах с бетонными плотинами. Так, например, объем бетона на строительстве Братской ГЭС с бетонной гравитационной плотиной составил 4,9 млн. м³, а на строительстве Саяно-Шушенской ГЭС с арочно-гравитационной плотиной – более 9,0 млн. м³. Таким образом, одной из основных особенностей бетонных работ в гидротехническом строительстве является большой объем этих работ вследствие массивности гидротехнических сооружений и их больших размеров.
Отсюда вытекает и вторая особенность бетонных работ в гидротехническом строительстве – необходимость предусматривать в комплексе бетонных работ технологические мероприятия по обеспечению трещиностойкости и монолитности массивных бетонных сооружений. Известно, что твердение бетона идет с выделением тепла гидратации цемента, т.е. бетон в период твердения разогревается. При массивных конструкциях бетон разогревается до 40 и даже 50-60°С. Затем этот бетон подвергается внешнему воздействию температур наружного воздуха и начинает остывать до эксплуатационной температуры, причем остывание протекает неравномерно, вызывая температурные перепады и, как следствие, температурные напряжения. Технология производства бетонных работ должна обеспечить такой температурный режим в блоках бетонирования и в целом в сооружении, который не вызвал бы недопустимых температурных перепадов и трещинообразования в блоках и обеспечил монолитность этих конструкций. Поэтому в комплексе бетонных работ имеются технологические мероприятия по регулированию температуры бетонной смеси на бетонном заводе и бетона в блоках бетонирования.
Третьей особенностью производства бетонных работ в гидротехническом строительстве является необходимость обеспечения однородности бетона с требуемыми его качествами, опять же с целью повышения трещиностойкости и монолитности. Поэтому комплекс бетонных работ должен включать технологические операции по обеспечению такой однородности. Это точное фракционирование заполнителей и точное дозирование составляющих и др.
Существенной особенностью, вытекающей также из больших объемов работ, является необходимость комплексной механизации всех технологических операций и всей технологий бетонных работ, так как только комплексная механизация всех процессов с механизмами большой производительности может обеспечить укладку таких больших объемов работ с большой интенсивностью. Например, годовая укладка бетона на строительстве СаяноШушенской ГЭС составила 1200 тыс. м³/год, а месячная – 154 тыс. м³/мес.
Таким образом, как по требованиям к свойствам бетона, так и к технологии его приготовления и укладки, бетон для гидротехнических сооружений имеет значительные отличия от обычных бетонов.
Особое место в гидротехническом строительстве занимают сооружения из укатанных бетонов, позволяющих значительно повысить интенсивность работ при одновременном упрощении технологии и мер борьбы трещинообразованием.
В общем, технология бетонных работ включает в себя целый комплекс различных технологических операций и мероприятий, а именно: приготовление и хранение заполнителей, приготовление и транспортирование бетонной смеси, укладку и уплотнение бетонной смеси в блоках, уход за уложенным бетоном. Сюда же входят арматурные и опалубочные работы, подготовка блоков бетонирования и др. Каждая операция из этого комплекса имеет свое определенное влияние на качество бетона и его свойства, поэтому в целом качество и свойства бетона обеспечиваются соблюдением определенных требований именно во всей цепочке технологии бетона, а не только в какой-то одной.
Требования, предъявляемые к бетону гидротехнических сооружений
239
Требования к бетонам гидротехнических сооружений устанавливаются на основе анализа условий службы сооружений в соответствии с указаниями нормативных документов.
Основным при установлении требований к бетону является правильное определение комплекса внешних факторов, воздействующих на бетон гидротехнических сооружений в период строительства и последующей эксплуатации. В зависимости от характера воздействующих факторов и их интенсивности устанавливают соответствующие требования к бетону и назначают марки бетона.
Бетон подразделяют по следующим признакам:
а) в зависимости от расположения в конструкциях по отношению к уровню воды на подводный бетон, бетон зоны переменного уровня воды и бетон надводный;
б) по массивности конструкций на бетон массивный и немассивный; в) по действию напора воды на бетон напорных и бетон безнапорных конструкций;
г) по расположению в массивных конструкциях на бетон наружной и бетон внутренней зоны. Основными техническими требованиями к бетону гидротехнических сооружений являются:
механическая прочность и предельная растяжимость (предельная относительная деформация), водонепроницаемость, морозостойкость, допустимая степень водопоглощения и линейных изменений при увлажнении и высыхании, стойкость против агрессивного воздействия воды данного состава, отсутствие вредного взаимодействия щелочей цемента с заполнителями, допустимая степень разогрева, специальные, устанавливаемые в проекте (например, стойкость против кавитационного разрушения при больших скоростях воды, стойкость против истираемости потоком воды с донными и взвешенными наносами).
Прочность бетона характеризует сопротивляемость бетона сжимающим и растягивающим напряжениям, а также его деформативность. В зависимости от гарантированной прочности бетона при сжатии, измеряемой в мегапаскалях (МПа), ГОСТ устанавливает следующие классы: В5; В7,5; В10; В12,5; В15; В25; В30; В35. Эти классы по прочности на сжатие отвечают
гарантированной прочности бетона в МПа с обеспеченностью q = 0,95 . Для массивных
сооружений допускается q = 0,9 . Классы бетона по прочности для речных гидротехнических сооружений, как правило, устанавливаются в возрасте 180 дней. В случае сокращенных сроков строительства и быстрого ввода сооружений в эксплуатацию допускается устанавливать их в возрасте 28 и 90 дней. Для бетона морских сооружений классы по прочности устанавливаются в возрасте 28 дней.
Классы по прочности на осевое растяжение устанавливаются в тех случаях, когда они имеют главенствующие значения и контролируются на производстве. Предусматриваются следующие классы: Вz0,8; Вz1,2; Вz1,6; Вz2; Вz2,4; Вz2,8; Вz3,2.
Кроме классов бетона по прочности ГОСТ допускает в особых случаях применять показатели прочности по маркам М, характеризующим сопротивляемость бетона сжимающим и растягивающим напряжениям в кг/см² (в соответствии с ранее существовавшей классификацией). По прочности на сжатие ранее предусматривались следующие марки: М 50, 100, 150, 200, 250, 300, 350, 400, 450, 500, 550, 600, 700, 800; по прочности на растяжение: Рz 5, 10, 15, 20, 25, 30, 35, 40, 45.
При этом между классами бетона по прочности В и марками М имеются примерно следующие соответствия: М100 соответствует В7,5; М150 соответствует В10, В12; М200 соответствует В15; М250 соответствует В20; М350 соответствует В25.
Предельная растяжимость бетона (предельная относительная деформация), характеризующая сопротивляемость бетона деформациям (например, температурным), должна быть не менее: 5∙10-5 – для бетонов внутренних зон, 7∙10-5 – для бетонов наружных зон.
Методы определения различных характеристик бетона по образцам в лабораторных условиях регламентируется соответствующими нормативными документами.
Водонепроницаемость бетона характеризует сопротивление бетона воздействию напоров воды. ГОСТом устанавливаются следующие марки по водонепроницаемости: W 2, 4, 6, 8, 10, 12, 16. Марки устанавливаются в зависимости от напорного градиента J, определяемого как
240

отношение максимального напора в метра к толщине конструкции в метрах, и от температуры
воды tв: |
|
|
|
|
W=φ(J, tв, агрессивности среды) (13.1) |
(табл.11). |
|
|
|
|
|
Таблица 11. Марки по водонепорницаемости |
||
Температура воды, ºС |
Марки бетона по водонепроницаемости при градиентах напора |
|||
|
До 5 |
Свыше 5 |
Свыше 10 |
Свыше 20 до 30 |
|
включительно |
до 10 |
до 20 |
включительно |
До 10º включительно |
W 2 |
4 |
6 |
8 |
Свыше 10º до 30º |
4 |
6 |
8 |
10 |
включительно |
|
|
|
|
Свыше 30º |
6 |
8 |
10 |
12 |
Примечание: Для конструкций с градиентом напора свыше 30 следует назначить марку бетона по водонепроницаемости W 16 и выше.
Для речных гидротехнических сооружений марки бетона по водонепроницаемости устанавливают в возрасте 180 дней, для морских – в возрасте 28 дней. Для бетона внутренних зон может приниматься марка по водонепроницаемости W-2 (при соответствующем обосновании). Для конструкций морских гидротехнических сооружений марки бетона по водонепроницаемости устанавливают в зависимости от зоны расположения и типа конструкций, но не ниже W4.
Морозостойкость бетона – это сопротивляемость бетона воздействию попеременного замораживания и оттаивания. ГОСТ устанавливает следующие марки по морозостойкости: F 50, 75, 150, 200, 300, 400, 500. Марка по морозостойкости для речных гидротехнических сооружений устанавливается в зависимости от климатических условий района и числа расчетных циклов попеременного замораживания и оттаивания или перехода через нуль температуры воздуха в течение года, т.е.
F=φ (климатических условий, числа циклов замораживания и оттаивания) (13.2) (табл.12).
|
|
|
|
Таблица 12. Марки по морозостойкости |
|
Климатическме |
Марки бетона по морозостойкости при числе циклов попеременного |
||||
условия |
|
замораживания и оттаивания в год |
|
||
|
До 50 |
Свыше |
Свыше |
Свыше 100 |
Свыше 150 до 200 |
|
включительно |
50 до 75 |
75 до 100 |
до 150 |
включительно |
Умеренные |
F 50 |
F 100 |
F 150 |
F 200 |
F 300 |
Суровые |
100 |
150 |
200 |
300 |
400 |
Особо суровые |
200 |
300 |
400 |
500 |
600 |
Примечание: 1. Климатическме условия, характеризующиеся среднемесячной температурой наиболее холодного месяца: умеренные – выше минус 10ºС, суровые – от минус 10 до минус 20º, особо суровые – ниже минус 20 ºС.
2.Среднемесячная температура определяется по СНиП 2.01.01-82, а также по данным гидрометеорологической службы.
3.При числе циклов более 200 следует применять специальные виды бетонов или конструктивныю теплозащиту.
Срок твердения бетона по марке морозостойкости принимается равным 28 суткам, а для массивных сооружений в теплой опалубке – 60 суткам.
Стойкость бетона к агрессивной среде характеризует его сопротивляемость разрушению от действия подземных или иных вод, содержащих различные агрессивные включения. Агрессивность воды устанавливается в соответствии со специальными инструкциями. В зависимости от рода агрессивности выбирают соответствующий вид цемента, стойкий против этого воздействия, а также проводят другие мероприятия для повышения сопротивляемости
241

воздействию агрессивной среды (повышают водонепроницаемость, плотность и др.) или в случае необходимости применяют гидроизоляцию конструкции.
Существенным требованием к бетону гидротехнических сооружений в массивных конструкциях является требование пониженного тепловыделения при твердении бетона для снижения перепадов температур и вследствие этого облегчения борьбы с трещинообразованием. Это требование обеспечивают применением соответствующего вида цемента с пониженной теплотой гидратации, тщательным подбором состава бетона с минимально необходимым расходом цемента при применении различных добавок, снижающих расход цемента. По этому показателю особенно ценным и являются укатанные бетоны с расходом цемента – 60-120кг/м³.
13.3. Зональное расположение марок бетона
Одним из наиболее важных мероприятий по снижению общего расхода цемента при строительстве массивных сооружений является зональное расположение различных марок бетона по поперечному профилю сооружения.
В зависимости от требований, предъявляемых к отдельным частям сооружений, в частности к телу плотины, различают следующие зоны (рис. 13.1): I – наружные части сооружения выше уровней воды, находящиеся под воздействием всех атмосферных факторов; 2 – наружные части сооружения в пределах переменных уровней воды; 3 – наружные части и подошва сооружений, находящиеся постоянно ниже уровня воды; 4 – внутренняя часть сооружения; 5 – части сооружений, подверженные особым воздействиям.
Размеры отдельных зон (толщину и высоту) назначают в зависимости от величины действующего напора, конструктивных размеров элементов плотины, схемы разрезки плотины на блоки бетонирования, размеров последних и климатических условий района строительства. Как правило, границы зон совмещают с границами блоков бетонирования по технологическим соображениям, однако в принципе вполне возможна укладка 2 марок бетона в один блок.
Рис. 13.I. Схема зонального расположения марок бетона:
а – глухая плотина, б – водосливная плотина, в – здание ГЭС, г – шлюз Зона 1 – определяющее требование по прочности или морозостойкости (для суровых
климатических условий); Зона 2 – определяющая требование по морозостойкости; Зона 3 –
242

определяющая требование по водонепроницаемости; Зона 4 – определяющая требование по прочности и минимальному тепловыделению; Зона 5 – специальные требования
Требования к бетону каждой зоны можно подразделить на определяющие (основные) и дополнительные.
Копределяющим относятся требования, которые в конечном итоге играют решающую роль при назначении марки бетона и его состава. Для каждой зоны, как правило, возможно выделить эти определяющие требования. Так, для зоны I определяющим требованием, как правило, является или требование по прочности, или по морозостойкости (для суровых климатических условий), для зоны 2 – требование по морозостойкости, для зоны 3 – требование по водонепроницаемости, для зоны 4 – требование по прочности и минимальному тепловыделению, для зоны 5 – специальные требования.
Кдополнительным требованиям относятся такие, которые не оказывают существенного влияния на состав бетона, но которые также должны быть учтены при назначении марки бетона и проектировании. Так, бетон зоны 2, безусловно, должен обладать определенной водонепроницаемостью, прочностью и другими свойствами.
Поскольку в каждой зоне сооружения бетон работает в различных условиях и к нему предъявляются различные требования, то, как правило, для каждой зоны устанавливаются свои классы и марки бетона. Каждое требование к бетону выражается через свои характеристики, поэтому в принципе каждая марка бетона должна включать все эти характеристики. Однако, как показывают исследования и опыт проектирования, большинство требований взаимосвязаны между собой, и удовлетворение многих требований можно выразить через ограниченное количество характеристик. Поэтому, как правило, марка бетона содержит три основные характеристики: классы по прочности и марки по водонепроницаемости и по морозостойкости и записывается в виде: В15, W6, F150. Все прочие требования к бетону различных зон, не вошедшие в явном виде в характеристики марки бетона, должны быть проверены и удовлетворены при подборе состава бетона и при необходимости выражены через те же основные характеристики путем их корректировки. Например, требование кавитационной стойкости может сочетаться с требованиями повышения класса или марки по прочности и марки по морозостойкости. Увязка марок бетона по различным признакам производится лабораторными испытаниями. На рис. 13.1.а. дано зональное распределение бетона в плотине Зейской ГЭС.
Рис. 13.1.а. Зональное распределение бетона в плотина Зейской ГЭС
Зональное распределение марок бетона в сооружениях из укатанного бетона имеют свои особенности, которые будут рассмотрены в специальной главе №24.
243
244

ГЛАВА 14. Теоретические основы определения требований к технологии бетонных работ
14.1. Температурный режим блоков бетонирования
Процесс твердения бетонной смеси происходит с выделением тепла. Вначале под влиянием тепла экзотермии бетонный блок после укладки смеси разогревается, а затем под воздействием внешних условий (воздух, вода) бетон будет остывать. При этом можно выделить четыре характерных периода (рис.14.I): 1) период экзотермического разогрева; 2) период снижения температуры в блоке до средней эксплуатационной; 3) переходный период; 4) эксплуатационный.
Рис. 14.1. Изменение температурного режима бетона в блоках бетонирования (в блоках внутренней части массивных сооружений)
I – температура в центре блока (точка I); 2 – температура у наружной грани (точка 2); 3 – средняя температура бетона в блоке; 4 – средняя температура бетона в блоке в период эксплуатации сооружения; 5-8 – продолжительности первого-четвертого периодов
В первый период наблюдается значительный подъем температуры в блоке за счет тепла, выделяемого при гидратации цемента. Максимальная интенсивность тепловыделения наблюдается в первые сутки, и основное выделение тепла происходит в первую неделю (7 дней), а к месячному возрасту выделение тепла настолько ничтожно, что может практически не учитываться. Интенсивность тепловыделения и общее количество тепла зависят от марки и типа цемента (рис. 14.2).
245
Рис.14.2. Тепловыделение цементов и бетона: а – интенсивность тепловыделения различных марок, б – интегральные кривые тепловыделения в бетоне при температурах бетонной смеси 7 и 14°С для шлакопортландцемента марки 250
Во второй период под воздействием температуры окружающего воздуха (среды) происходит остывание блока до эксплуатационных температур. Установлено, что внутри сооружений с течением времени устанавливается температура, близкая к среднемноголетней температуре воздуха. Эта температура является той температурой, при которой необходимо омоноличивать все строительные швы, чтобы в будущем не наблюдалось их раскрытие. Продолжительность этого периода зависит от массивности сооружения и колеблется от нескольких месяцев до года и более.
В третий период температура в блоках колеблется в зависимости от условий теплообмена с наружным воздухом и готовности сооружения в целом. В блоках, расположенных внутри массива сооружения и не подвергающихся уже открытому воздействию воздуха, колебания температуры в этот период небольшие и, как правило, не опускаются ниже среднегодовой. В отдельных же точках и даже блоках, расположенных на наружной грани, возможны в этот период значительные колебания от существенного разогрева в летний период до глубокого промерзания зимой. Если строительные швы уже омоноличены, то такое промерзание блоков в зимний период уже вредно, и для его исключения необходимо предусматривать соответствующую теплозащиту. Продолжительность этого периода обычно несколько лет до момента полного окончания сооружения и установления в нем эксплуатационного температурного режима.
Четвертый период – эксплуатационный, изменение температуры бетона в этот период происходит закономерно с колебаниями по сезонам года вокруг средней эксплуатационной с большей или меньшей амплитудой колебаний в зависимости от условий теплообмена. Внутри массивных сооружений колебания температур практически равны нулю, и только в зоне 3-5 м от наружной грани сказываются сезонные колебания наружного воздуха.
Определение температурного режима блоков на различных этапах с учетом всех факторов производится на основе выполнения специальных теплотехнических расчетов. Не останавливаясь здесь на методах расчетов и отсылая заинтересованных к специальной литературе, укажем здесь, что существуют специальные программы для расчета температурного режима на ЭВМ
14.2. Термонапряженное состояние блоков. Причины трещинообразования
Как и в любом физическом теле, изменение температуры бетона ведет к изменению его объема, и если свободному изменению объема и размеров что-то препятствует, то в этих блоках появляются сжимающие или растягивающие температурные напряжения. Главным требованием к технологии бетонных работ в этом плане является обеспечение таких условий бетонирования, которые не привели бы к появлению трещин.
Из теории прочности бетона и железобетона известны два вида температурных напряжений – "собственные" и "вынужденные". Для тех и других напряжений имеются формулы для их определения. В функциональном виде эти формулы выглядят следующим образом:
|
|
æ αi , DTi , Ei , KЗi, K pi ö |
|
|
|
Rp |
|
|
||||
Dσ |
i |
= ϕç |
|
|
÷ |
å Dσ |
i |
£ |
|
|
|
|
|
|
|
|
|
|
|||||||
|
ç |
μi |
÷ |
|
|
Kтр |
(14.1) |
|||||
|
|
è |
ø , |
|
|
|
||||||
|
|
|
|
|
|
|
|
|
|
|||
где: |
σ i – приращение |
напряжений |
на i-м интервале |
возраста бетона в блоке; |
DTi – |
|||||||
приращение температурного перепада на этом интервале; Ei |
– модуль упругости; |
KЗi – |
коэффициент защемления; K pi – коэффициент релаксации; μi – коэффициент Пуассона; αi –
коэффициент линейного расширения; Rр – условная прочность бетона на растяжение; Kтр – коэффициент запаса на трещинообразование.
246

Для инженеров-технологов, занимающихся вопросами технологии бетонных работ, интерес представляют не столько сами напряжения, сколько те перепады температур, которые вызывают опасные напряжения и приводят к трещинообразованию. Поэтому, переходя к допустимым
напряжениям и через них к допустимым перепадам температур [ T ] и заменяя Rр на ε пр. E , т.е.
Rр = εпр Е , получаем общую формулу для допустимых перепадов температур: |
|
||||||||
|
æ |
|
ε пр μ |
ö |
|
||||
|
ϕç |
|
|
|
|
|
|
÷ |
|
|
αK |
|
K |
|
K |
|
|
||
[ T ] = |
ç |
|
|
÷ |
(14.2) |
||||
è |
|
з |
|
р |
|
тр ø , |
|||
где: ε пр |
– предельная растяжимость. |
|
Как показал опыт гидростроительства, непосредственные причины образования трещин зависят от условий "защемления" и от места положения блока в теле плотины (рис. 14.3, а):
1) для блоков "защемленных" и расположенных в основании плотины основной причиной
трещинообразования является |
перепад |
между осредненной температурой |
в блоке в |
период |
|||||||||
экзотермии |
T макс |
и осредненной температурой в период эксплуатации |
T ср |
(рис. 14.3.б) |
|
|
|||||||
б.экз |
б.экспл |
|
|
||||||||||
DТ |
| |
= Т |
макс - Т ср |
|
|
|
|
|
|
(14.3) |
|
||
|
|
б.экз |
б.экспл ; |
|
|
|
|
|
|
|
|||
2) для блоков в свободной зоне – перепад между температурой в центре блока |
T макс |
и |
|||||||||||
б.ц. |
|||||||||||||
|
|
|
|
|
|
|
|
|
|
|
|
||
температурой бетона на гранях блока в данный период Tб.гр. (рис. 14.3.в) |
|
|
|
||||||||||
|
|
|
|
DТ |
|| |
= Т макс - Т |
б.гр ; |
|
|
(14.4) |
|
||
|
|
|
|
|
|
б.ц |
|
|
|
Рис. 14.3. Расположение блоков и опасные температурные перепады в них:
а – зоны расположения блоков: I зона – прискальная h1 » lбл , |
II зона – переходная |
h2 » (0,5 -1,0)lбл , III зона – свободная h3 > lбл , б, в – графики изменения температур в блоке и опасные перепады температур для блоков "защемленных" и для "свободных", Tср – изменение средних температур в блоках I зоны; T1 – изменение температур на наружной части блоков III зоны; T2 – изменение температур в центре блоков III зоны
Кроме того, образование трещин на наружных гранях всех блоков в раннем возрасте возможно от высокой интенсивности (скорости) остывания бетона на гранях:
247
J = |
T |
(14.5) |
где: T – перепад температуры; t |
Dt , |
|
– продолжительность остывания по времени. |
|
14.3.Определение допустимых температурных перепадов
Всоответствии с 14.2 при решении задачи предотвращения трещинообразования в блоке прежде всего следует определить допустимые перепады температур для конкретных условий и технологию, которая бы обеспечила выполнение этого условия.
Обычно задачу решают таким образом. Для заданных конкретных условий бетонирования блока (состав бетона, температура бетонной смеси, условия тепловыделения и теплоотдачи из блока и т.д.) рассчитывают изменение температурного поля в блоке во времени. Далее по детальным формулам семейства (14.1) определяют температурные напряжения. При этом продолжительность времени, за которое определяют температурные напряжения, делят на ряд интервалов и для каждого интервала определяют приращения напряжений с учетом конкретного
измерения температуры бетона, модуля упругости E во времени и всех других характеристик бетона и коэффициентов, входящих в формулы.
Для блоков, расположенных на "жестком основании", приращение вынужденных напряжений составит:
а) при полном "защемлении": |
Dσ i = Ei Dεi = αEi DTi K pi ; |
б) при "неполном защемлении": |
Dσ i = αEi DTi K зi K pi . |
Задаваясь различными мероприятиями по регулированию температурного режима в блоке и, как следствие, изменяя температурное поле и приращение, определяют суммарные напряжения при различных наборах мероприятий и выбирают тот вариант, при котором суммарные напряжения не превосходят допустимых:
σ макс = å Dσ i £ [Rp ]/ Ктр .
Указанные подробные расчеты термонапряженного состояния блоков достаточно трудоемки и их выполняют обычно с помощью программ на ЭВМ. То же касается расчетов температурных полей в блоках бетонирования. Однако практика проектирования выработала и более простые, приближенные методы решения практических задач, возникающих при определении требований к температурному режиму блоков и назначении различных мероприятий по их обеспечению, которые дают приемлемые для предварительных прогнозов результаты. Один из этих методов изложен ниже.
|
Основным допущением в этом методе является принятие осредненных значений величин E , |
||||||||||||||||||||||||||||
K |
з , |
K p |
, |
T |
для всего интервала времени. Тогда |
|
|
|
|
|
|
|
|
||||||||||||||||
|
|
|
б |
|
|
|
|
|
|
|
|
||||||||||||||||||
|
|
σ |
|
|
= αDT ср Е |
|
К |
|
К |
|
£ |
Rp |
|
|
|
|
|
|
|
|
|
|
|
|
|
|
|||
|
|
макс |
ср |
з.ср |
р.ср |
|
|
|
|
|
|
|
|
|
|
|
|
|
|
||||||||||
|
|
|
|
б |
|
|
|
|
Ктр |
|
. |
|
|
|
|
|
|
|
|
|
|
|
|||||||
|
|
|
|
|
|
|
|
|
|
|
|
|
|
|
|
|
|
|
|
|
|
|
|
|
|
||||
|
|
|
|
|
|
|
|
|
|
|
|
|
|
|
|
|
|
|
|
|
|
|
|
|
εпр Eср |
|
|||
|
|
|
|
|
|
|
|
|
|
|
|
|
|
|
σ |
макс |
= αDT ср E K |
з.ср |
K |
р.ср |
£ |
|
|||||||
|
|
|
|
|
|
|
|
|
|
|
|
|
|
|
|
||||||||||||||
|
Приняв Rр = εпр Е |
, получим: |
|
|
|
б ср |
|
|
|
Kтр . |
|||||||||||||||||||
|
|
|
|
|
|
ε пр |
|
|
|
|
|
|
|||||||||||||||||
|
|
|
|
|
|
|
|
|
|
|
|
σ |
|
|
= [σ |
|
] = |
= α[DT ср ]K |
|
|
K |
|
|
||||||
|
|
|
|
|
|
|
|
|
|
|
|
макс |
доп |
|
з.ср |
р.ср |
|||||||||||||
|
|
|
|
|
|
|
|
|
|
|
|
|
|
|
|
|
Kтр |
|
б |
|
|
||||||||
|
В предельном случае: |
|
|
|
|
|
|
|
|
|
|
|
|
|
|
|
, |
||||||||||||
|
откуда допустимый температурный перепад средних температур в блоке |
||||||||||||||||||||||||||||
|
|
[T ср ] = |
ε пр |
|
|
|
|
|
|
|
|
|
|
|
|
|
|
|
|
|
|
|
|
|
|
||||
|
|
|
|
|
|
|
|
|
|
|
|
|
|
|
|
|
|
|
|
|
|
|
|
|
|
||||
|
|
|
б |
|
|
αK з.ср K р.ср Kтр |
, |
|
|
|
|
|
|
|
(14.6) |
|
|
|
|
|
|
|
|
||||||
|
|
|
|
|
|
|
|
|
|
|
|
|
|
|
|
|
|
|
|
|
|||||||||
|
а допустимый перепад максимальных температур в блоке |
|
|
|
|||||||||||||||||||||||||
|
|
[DT макс |
] = [DT ср ]K |
т.перех , |
|
|
|
|
|
|
(14.7) |
|
|
|
|
|
|
|
|
||||||||||
|
|
|
|
б |
|
б |
|
|
|
|
|
|
|
|
|
|
|
|
|
|
|
|
248

где K – переходный коэффициент от средней температуры в блоке в период экзотермии к максимальной. Этот коэффициент зависит от условий теплообмена блока с окружающей средой и определяется по результатам расчета температурного поля в блоке или для предварительных расчетов – по аналогам.
14.4. Факторы, влияющие на величину допустимого перепада температур
Для того чтобы выявить эти факторы, рассмотрим последовательно все члены, входящие в формулы (14.2) – (14.6).
Предельная |
растяжимость |
бетона |
εпр = |
[Rp ] |
определяется |
лабораторными |
||
E |
|
|||||||
|
|
|
|
|
|
|||
исследованиями |
при подборе состава |
бетона. |
При быстром приложении |
внешней силы |
предельная растяжимость бетона меняется в пределах от 0,6 ×10−4 до 1,1×10−4 в зависимости от состава и марки бетона.
Нормативными документами рекомендованы следующие средние значения предельной растяжимости бетона:
Марка бетона |
200 |
250 |
300 |
Предельная растяжимость |
0,7 ×10−4 |
0,8 ×10−4 |
0,9 ×10−4 |
В то же время опытами установлено, что предельная растяжимость несколько увеличивается, если нагрузка возрастает медленно, как это обычно имеет место при температурных воздействиях. Как и прочность бетона и модуль упругости бетона, предельная растяжимость
изменяется с возрастом бетона. Рост предельной растяжимости ε пр , происходит несколько медленнее, чем рост модуля упругости E , и быстрее, чем рост прочности R (рис. 14.4).
Рис. 14.4. Зависимость механических характеристик бетона от возраста I – изменение модуля упругости;
2 – изменение предельной растяжимости; 3 – изменение прочности бетона
Опытами установлена также зависимость предельной растяжимости бетона от градиента напряжений в нем. Это особенно важно учитывать при расчете термонапряженного состояния блоков, так как температурные напряжения часто характеризуются высокими градиентами. При наличии значительного градиента температурных напряжений предельная растяжимость бетона при расчете его трещиностойкости может быть принята в 1,5 – 2 раза больше, чем соответствующая величина, определенная при одноосном растяжении.
249

Из других факторов, влияющих на фактическую предельную растяжимость в блоке, существенное влияние оказывают состав бетона и его однородность. Чем выше однородность бетонной смеси, тем при прочих равных условиях выше предельная растяжимость. Однородность бетонной смеси можно повысить целым рядом технологических мероприятий: применением большего количества фракций как крупного, так и мелкого заполнителя, обеспечением тщательного перемешивания бетонной смеси, обеспечением условий нерасслаиваемости бетонной смеси при транспортировании и укладке и др.
|
∂σ |
|
Таким образом, εпр = φ(M, |
¶n , состава, однородности, возраста бетонной смеси), |
(14.8) |
Коэффициент линейного |
расширения α изменяется в зависимости от состава |
бетона и |
колеблется в пределах (0,75 -1,1) ×10−5 . При выдерживании высокой однородности состава бетона и положительной температуры коэффициент линейного расширения относительно стабилен. Однако он существенно возрастает после замерзания бетона. Так, при температуре (– 5… – 20)°С значение коэффициента линейного расширения увеличивается на 40 – 50%, а при дальнейшем понижении температуры снижается. При этом он все же на 20% выше, чем для талого бетона. В целом α =φ (состава бетонной смеси, однородности, и температуры бетона). (14.9)
Коэффициент релаксации Кр является следствием ползучести бетона. Под коэффициентом
релаксации Кр понимают степень изменения напряжения σ за время τ , считая от момента приложения нагрузки при условии, что относительная деформация за это время остается постоянной. Это явление характеризуется кривой релаксации напряжений изображенной на рис. 14.5, причем изменение различно для бетона разных возрастов. Таким образом, функционально коэффициент релаксации
K р |
= ϕ(τ о ,τ к , Dt) |
, |
(14.10) |
|
|
где: τ о – возраст бетона в момент начала охлаждения бетонной кладки; τ к – возраст бетона к моменту остывания бетонной кладки до средней эксплуатационной температуры (до температуры
омоноличивания); Dt = τ к -τ о – продолжительность остывания блока.
Рис.14.5. График для определения значений коэффициентов релаксации (затухания) температурных напряжений τ о – возраст бетона к началу интенсивного охлаждения бетонной кладки; τ к – возраст бетона к моменту охлаждения бетонной кладки до температуры омоноличивания строительных швов; τк – продолжительность охлаждения.
250

Коэффициент защемления Кз характеризует степень ограничения свободы деформаций из-за укладки его на жесткое основание (скалу, старый бетон). Как показывают исследования, этот
коэффициент зависит от относительной длины блока Hбл lбл , т.е. от размеров блока бетонирования и от отношения модулей деформации бетона и основания (рис. 14.6)
æ Hбл |
, |
Eбет |
ö |
|
ç |
|
÷ |
(14.11) |
|
Кз=φè |
lбл |
|
Eосн ø , |
Рис. 14.6. График для определения коэффициента защемления в нижней точке А
η = |
Eб |
= 0,5 - 5,0 |
|
||
прискального блока при равномерном остывании – нагреве: |
Eосн |
Из рис. 14.6 следует, что коэффициент защемления тем выше, чем выше относительная длина блоков и чем выше модуль упругости основания Eосн по отношению к модулю упругости бетона
Eбет.
Модуль упругости бетона Ебет, как было сказано ранее, зависит от возраста бетона. В возрасте 7-10 сут. модуль упругости составляет 0,6 - 0,7 от годичного а в возрасте 3-4 сут. он еще меньше. В зрелом возрасте модуль упругости гидротехнического бетона составляет 200 000 – 400 000
кг/см². Средние значения его зависят от марки бетона: |
|
|
|||
Марка бетона |
MI00 |
М200 |
М250 |
М300 |
М400 |
Модуль упругости |
1,7∙105 |
2,4∙105 |
2.65∙I05 |
2,9∙105 |
3,3∙I05 |
При замерзании бетон становится более жестким вследствие превращения части воды, заполняющей поры, в лед, и ожесточения структурных связей внутри цементного камня. При этом его модуль упругости возрастает по сравнению с его значениями для талого бетона
примерно в полтора раза. Таким образом, |
|
Eбет = φ (М, возраст бетона, Tбет). |
(14.12) |
Модуль упругости Eосн существенно зависит от категории основания (скальное, нескальное, бетонное). Для естественных оснований модуль упругости к моменту строительства уже сформировался и не зависит о времени. Это обстоятельство определяет изменение соотношения характеристик бетона и скального основания в первые моменты после укладки бетона. Если вначале скальное основание может рассматриваться как достаточно жесткое относительно бетона, то в возрасте месяца и более картина меняется и жесткость бетона становится равной жесткости
251

основания или больше ее. В зависимости от трещиноватости скальных оснований модуль их деформации изменяется в пределах З∙104 – З∙105кг/см², а средние значения колеблются для малотрещиноватой скалы в пределах (180-300)∙103 кг/см², для скалы средней трещиноватости в пределах (100-180)∙103 кг/см², а для сильнотрещиноватой скалы – (30-100)∙103 кг/см². Модуль деформации нескальных грунтов изменяется в пределах (0,6-6,0)∙103 кг/см². Таким образом,
Eосн = φ (категорий пород, их трещиноватости). (14.13)
14.5. Приближенный метод определения величины необходимого снижения максимальной температуры в блоке по условиям его трещиностойкости
Для инженера, занимающегося производством бетонных работ, задача обеспечения трещиностойкости блока может быть сформулирована следующим образом: на какую величину нужно снизить температуру в блоке за счет технологических мероприятий, чтобы в блоке не возникли трещины? Для этого необходимо знать максимальную возможную температуру в блоке при отсутствии каких-либо мероприятий и максимальную допустимую температуру в блоке исходя из условий обеспечения трещиностойкости. Разница этих величин температур и дает искомую величину.
Приближенно эту задачу удобно решать, используя схему и обозначения рис.14.7.
Рис. 14.7. Расчетная схема к определению параметров допустимого температурного режима в блоках на жестком основании.
Чтобы определить максимальную температуру в блоке, примем допущение об отсутствии теплопотерь из блока, т.е. адиабатические условия повышения температуры. Тогда
T а |
= T |
|
+ |
T а |
(14.14) |
б.э |
б.нач |
|
б.э , |
||
|
где: |
T а |
– максимальная |
температура в блоке в период экзотермического разогрева |
|
|
|
б.э |
в адиабатических условиях; Tб.нач – начальная температура бетона после укладки бетонной смеси
в блок; |
T а |
– повышение температуры в блоке от экзотермического разогрева в адиабатических |
|||
б.э |
|||||
условиях. |
|
|
= Цq |
|
|
|
|
|
T а |
|
|
Для известного состава бетонной смеси: |
б.э |
cγ . |
(14.15) |
||
|
Здесь Ц – расход цемента, кг/м³; q – удельное тепловыделение цемента, ккал/кг; c – удельная теплоемкость свежеуложенного бетона, ккал/(кг∙°C); γ – плотность бетонной смеси, кг/м³.
Максимально допустимая температура в блоке:
[T макс ] = T ср |
+ [ T макс ] |
, |
(14.16) |
|
б |
б.экспл |
б |
252
где: Tбср.экспл – средняя эксплуатационная температура в блоке, до которой будет
остывать бетон в блоке (сооружении); [ Tбмакс ] – допустимый максимальный перепад температур блока, определяемый согласно п. 14.3 и формуле (14.7).
Тогда необходимое снижение температуры в блоке за счет дополнительных технологических мероприятий для обеспечения отсутствия трещинообразования составит
T техн = T а |
− [T макс ] |
. |
(14.17) |
|
б |
б.э |
б |
T техн
В зависимости от величины б назначают комплекс технологических мероприятий, обеспечивающих такое снижение.
14.6. Принципиальные направления конструктивных и технологических мероприятий по обеспечению трещиностойкости и монолитности бетонных гидротехнических сооружений
Ранее отмечалось, что на трещиностойкость бетона влияет масса взаимосвязанных факторов, начиная от запроектированных конструкций, их размеров, состава бетона и всей технологической цепочки от приготовления бетона до ухода за уложенным бетоном. Следовательно, на всех этапах проектирования и возведения бетонных гидротехнических сооружений должны учитываться требования, вытекающие из необходимости обеспечения в конечном итоге монолитного сооружения без трещин, и назначаться соответствующие мероприятия и решения как конструктивного, так и технологического характера, обеспечивающие эти требования.
Конструктивные решения должны быть направлены на создание конструктивных форм, в наибольшей мере обеспечивающих благоприятное термонапряженное состояние как в период строительства, так и эксплуатации.
Технологические мероприятия должны быть направлены на повышение предельной растяжимости бетона εпр, на обеспечение условий приготовления бетона с наименьшим расходом цемента, на повышение однородности бетона, на обеспечение необходимых темпов укладки бетона, на соблюдение необходимого температурного режима и других условий.
К конструктивным решениям относятся:
а) выбор типа сооружения или конструкции в зависимости от климатических и других местных условий;
б) разрезка сооружений постоянными температурными швами на отдельные секции или части;
в) выбор соответствующих конструкций и их элементов, исключающих резкие изменения сечений, и соответствующую им концентрацию температурных напряжений;
г) рациональное размещение и конструктивное оформление различных отверстий и полостей в сооружении;
д) армирование бетона.
К технологическим мероприятиям относятся:
впериод заготовки заполнителей и приготовления бетона – заготовка и применение максимально возможного количества фракций крупных заполнителей с тщательным фракционированием, промывкой, хранением; применение контрольного грохочения; применение среднетермичных и малотермичных цементов; применение различных добавок, снижающих расход цемента; охлаждение или подогрев составляющих бетонной смеси; применение холодной воды затворения и льда; точное дозирование и тщательное перемешивание составляющих бетонной смеси с целью обеспечения ее однородности;
впериод транспортирования и укладки бетонной смеси – применение транспортных
средств и условий перегрузок, обеспечивающих нерасслаиваемость бетонной смеси; разбивка сооружения на блоки бетонирования с применением наиболее рациональной системы разрезки и размеров блоков; применение средств уплотнения, обеспечивающих требуемую плотность бетона и ее равномерность; ведение бетонных работ с интенсивностью, благоприятно влияющей на термонапряженное состояние;
253

в период набора прочности, экзотермического разогрева и охлаждния – применение трубного и поверхностного охлаждения уложенного бетона в летний период; защита бетона от прямого действия солнечных лучей; увлажнение бетона; применение шатров, теплой опалубки и электрообогрева в зимний период. Обеспечение оптимальных сроков опалубки для предохранения бетона от теплового удара при его распалубке; применение оптимальной системы и условий омоноличивания временных строительных швов.
Принципиально большинство из этих мероприятий намечается в период составления проекта. Практическая же их реализация осуществляется в процессе подбора состава бетона и выполнения всей технологии бетонных работ в период строительства.
Наибольшее количество мероприятий в период строительства связано с обеспечением нужного температурного режима. Для блоков на жестком основании (рис. 14.8) это можно сделать (при прочих равных условиях) за счет снижения начальной температуры бетонной смеси на бетонном заводе или за счет естественного или искусственного охлаждения бетонной кладки в блоке в период ее твердения. (Рис. 14.8)
Рис. 14.8. Снижение максимальной температуры в блоке на скальном основании при применении различных технологических мероприятий
1 – изменение температуры без технологических мероприятий; 2 – влияние естественного и искусственного охлаждения; 3 – влияние снижения Tб.нач
Для блоков, удаленных от жесткого основания, как следует из 14.1, основной причиной трещинообразования являются перепады между центром блока и гранями Tб.гр . В этих условиях
снижение Tб.гр возможно за счет искусственного охлаждения в центре блока и за счет снижения степени естественного охлаждения (увеличения теплозащитных свойств опалубки) (рис.14.9).
254

Рис. 14.9. Изменение температурного режима в блоке, удаленном от жесткого основания 1,2 – температуры в центре и на гранях блоков без искусственного охлаждения; 1’,2’ – то же при наличии искусственного охлаждения.
14.7. Расчетное обоснование дополнительных мероприятий по регулированию температурного режима в блоках бетонирования в зимний период
Дополнительные требования к температурному режиму блоков бетонирования в зимний период
Кроме изложенных ранее требований к перепадам температур в блоках бетонирования температурный режим в зимний период должен дополнительно обеспечить: положительную температуру бетонной смеси при укладке ее в блок с учетом транспортировки бетонной смеси от бетонного завода до блока; набор прочности бетона до его замораживания не менее 40–50% от его марочной прочности.
Для обеспечения этих требований бетон в зимнее время укладывают или методом «термоса» в открытых блоках, или под защитой шатров или тепляков. Бетонирование в открытых блоках методом «термоса» применяют при температуре до минус 10°С, а иногда при принятии дополнительных мероприятий (добавок, периферийного электрообогрева) и при более низких температурах. При температурах ниже минус 10-15°С укладка бетона в блоки, как правило, производится под защитой тепляков или шатров.
Температурный режим блоков бетонирования в зимний период и мероприятия по его обеспечению требуют соответствующего расчетного обоснования. В частности, необходимо обосновать температуру бетонной смеси в блоке и на выходе из бетонного завода, необходимость подогрева составляющих бетонной смеси, теплозащитные свойства опалубки и т.д.
Определение необходимой температуры бетонной смеси на выходе из бетонного завода
T треб
Необходимую начальную температуру бетонной смеси на выходе из бетонного завода б.с.нач можно определить по формуле
|
|
T треб |
= T треб + |
T |
+ T |
(14.18) |
|
|
T треб |
б.с.нач |
б.нач |
б.с. укл |
б.с.тр , |
||
где: |
– требуемая начальная температура бетона в блоке при перекрытии уложенного |
||||||
б.нач |
|||||||
слоя; Тб.с. укл. , |
Тб.с.тр. |
– снижение температуры (тепловые потери), бетонной смеси при укладке |
|||||
и транспортировании. |
|
|
|
|
Температуру бетона при перекрытии уложенного слоя в блоке Tб.нач устанавливают исходя из общих требований к температурному режиму блоков. В связи с тем, что в гидротехническом строительстве превалируют массивные блоки бетонирования, для снижения подъема
255
температуры от экзотермического разогрева в таких блоках требуется, чтобы начальная температура бетонной смеси при укладке в блок была возможно низкая. Как показывает опыт, эту температуру рационально поддерживать в пределах 3–7°С. Такая же температура поддерживается в шатрах и тепляках.
Требования защиты бетона от промораживания в массивных блоках целиком обеспечиваются за счет применения соответствующей опалубки и других мер теплозащиты (электрообогрев, термическая опалубка и др.). Поэтому для массивных блоков степень подогрева составляющих бетонной смеси определяется именно условием обеспечения температуры бетонной смеси при перекрытии слоя на уровне 3–7°С, с учетом всех потерь при транспортировке и укладке смеси.
Для тонкостенных конструкций и отдельных элементов с небольшим объемом бетона, встречающихся в других видах промышленного строительства, температура бетонной смеси должна быть проверена и уточнена, как и условия обеспечения требуемого набора прочности бетона до его замораживания. Указанные расчеты выполняют по специальной методике. Специальными расчетами определяются также тепловые потери при транспортировании и укладке бетонной смеси, зависящие от температуры окружающего воздуха и условий теплообмена. Для предварительных расчетов тепловых потерь при транспортировании возможно использовать эмпирические формулы, установленные на основе обработки данных натурных наблюдений на ряде строительств:
Tб.с. укл = |
K укл (Tб.нач − Tнв )τ укл |
|
Tб.с.тр = |
Kтр (Tб.с.укл |
− Tнв )τ тр |
|
|
|
hсл |
; (14.19), |
hсл |
, |
(14.20) |
||||
|
|
|||||||
где: K укл , Kтр – соответствующие коэффициенты, выражающие |
снижение |
температуры |
бетонной смеси на каждый градус перепада температур за 1 мин. При высоте ее слоя 1 м;
Kтр = 0,001 град / мин |
K укл = 0,002 град / мин |
– при укладке; hсл – |
||
град / м – при транспортировании; |
|
град / м |
||
толщина слоя соответственно при перевозке и |
укладке |
смеси; τ укл , |
τ тр – время |
укладки |
(перекрытия слоев) и транспортирования, мин.; |
Tнв – |
температура |
окружающего |
воздуха |
(наружного или в шатре); Tб.с.укл = Tб.нач + Tб.с.укл |
– температура бетонной смеси в начальный |
|||
период укладки (при поступлении в блок). |
|
|
|
|
Определение необходимого подогрева (охлаждения) составляющих бетонной смеси
Температура бетонной смеси на выходе из бетоносмесителя зависит от температуры составляющих бетонной смеси, их веса и теплотехнических характеристик и определяется из рассмотрения теплового баланса:
T |
= åci qiTi + åcв qiTi + åQпл qл + Qц qц + Qмτ |
|
|
||
б.с |
|
åci qi + åcв qвi |
, |
|
(14.21) |
|
|
|
|||
где: ci , qi , |
Ti – теплоемкость, вес 1 м³ бетонной |
смеси и |
температура составляющих |
||
бетонной смеси |
(песка, крупного заполнителя, |
цемента, |
воды); |
qвi – вес свободной воды |
затворения, содержащейся в составляющих бетонной смеси; qл – вес замерзшей части воды (льда) в составляющих бетонной смеси; cв = 1 ккал/(кг∙°С) – теплоемкость воды; qц – вес цемента; Qпл – теплота плавления льда; Qц = 2 ккал/кг – удельное тепловыделение цемента в
результате ранней гидратации; Qм ≈ 250 ккал/мин – удельное тепловыделение в результате превращения механической энергии в тепловую при перемешивании в бетономешалке; τ – время перемешивания смеси в бетономешалке, мин.
Для приближенных расчетов температуру бетонной смеси в зависимости от температур составляющих смеси можно определить по следующей формуле (для осредненного состава бетонной смеси и средней теплоемкости твердых составляющих Сб = 0,22 ккал/(кг∙°С)):
256
Tб.с = 0,25Tп + 0,55Tк.з + 0,10Tв + 0,10Tц , |
(14.22) |
где: Tп , Tк.з , Tв , Tц – расчетные температуры песка, крупного заполнителя, цемента и воды. Этой же формулой можно пользоваться для определения величины изменения температуры
бетонной смеси при изменении температуры составляющих:
Tб.с = 0,25 Tп + 0,55 Tк.з + 0,10 Tв + 0,10 Tц , |
(14.23) |
Из этих формул следует, что наибольшее влияние на температуру бетонной смеси оказывает температура крупных заполнителей (55%), затем песка (25%) и уже затем воды (10%) и цемента (10%).
Требуемый подогрев (охлаждение) составляющих бетонной смеси |
T треб |
можно определить |
||||
б.с |
||||||
из условия: |
T треб |
= T треб |
− T ест |
, |
|
(14.24) |
б.с |
б.с.нач |
б.с |
|
где: Tбест.с – естественная (условная) температура бетонной смеси, определенная по формулам (14.21) и (14.22) при условии отсутствия какого-либо подогрева составляющих бетонной смеси.
T ест
При определении б.с температура воды затворения принимается равной температуре воды в источнике водоснабжения. Естественная начальная температура заполнителей зависит от ряда различных факторов, в том числе от климатического района строительства, периода формирования штабеля, его конструкции и размеров, типа склада (закрытый, открытый), гранулометрического состава и влажности материала. Результаты обследований складов заполнителей в различных климатических районах показали, что для предварительных расчетов можно принимать температуру заполнителей для зимнего периода, равную половине расчетной зимней температуры наружного воздуха, а для летнего периода – на 2° ниже расчетной летней температуры воздуха. За расчетную температуру принимают среднесуточную температуру за наиболее холодную и теплую пятидневки соответственно для зимнего и летнего периодов. При длительном хранении больших объемов заполнителей в зимнее время, что часто имеет место на гидростроительствах, часть материала, находящегося внутри штабеля, не промерзает. В приближенных расчетах количество несмерзшегося материала можно принимать равным примерно 50% от общего объема склада.
Наибольшая допускаемая температура воды и бетонной смеси устанавливается из условия сохранения активности цемента и всех требуемых свойств бетонной смеси.
При сухих несмерзшихся заполнителях можно применять отдельные фракции заполнителей с отрицательной температурой при соблюдении условия положительного теплового баланса во всей массе при ее перемешивании в бетоносмесителе. Камень, применяемый в качестве «изюма», должен иметь температуру не ниже 0°С.
Выбор средств для регулирования температуры составляющих бетонной смеси
Выбор средств для регулирования температуры составляющих бетонной смеси прежде всего зависит от величины требуемого подогрева по формуле (14.24). По мере возрастания требуемой
величины регулирования температуры Tб.с рекомендуется определенная последовательность набора этих средств: подогрев воды затворения; подогрев крупного заполнителя; подогрев песка.
Технологические схемы будут даны в гл. 19. Если расчетами установлено, что в данных конкретных условиях требуется регулировать температуру бетонной смеси как летом (охлаждение), так и зимой (подогрев), то в качестве установок регулирования следует выбирать те из них, которые могут обеспечивать и то, и другое, т.е. выбирать обратимые установки.
В принципе выбор системы установок для регулирования температуры бетонной смеси должен производиться на основе технико-экономического сопоставления различных вариантов.
Определение требований к теплозащите бетона
Особое внимание при разработке технологических мероприятий по регулированию температурного режима в блоках бетонирования должно уделяться теплозащите бетона от его чрезмерного переохлаждения или нагрева с целью выдерживания допустимых температур и температурных перепадов в блоке. Выбор оптимальных теплозащитных свойств опалубки
257
достаточно сложен, так как температура наружного воздуха изменяется в довольно широких пределах, соответственно чему и должны изменяться теплозащитные свойства опалубки. Однако практически это делать неудобно, и обычно используют два типа опалубки – неутепленную (холодную) и утепленную (теплую).
Неутепленную опалубку применяют в весенне-летний период, когда среднесуточная температура воздуха положительная.
Осенью, примерно за 1 – 1,5 мес. до наступления отрицательных температур и в течение всего периода с отрицательными температурами, применяют утепленную опалубку.
В суровых климатических условиях утепленную опалубку часто применяют и летом. Применение неутепленной опалубки в этих случаях с последующим ее утеплением нецелесообразно, так как приводит к повышению затрат труда при неизбежном худшем качестве утепления. Поэтому для опалубливания наружных граней плотины (верховая, низовая), подверженных колебаниям температур в течение всего строительства, в суровых климатических условиях применяют обычно утепленную опалубку. Утепленную опалубку применяют и для внутренних блоков плотины, если их боковые грани не закрыты бетоном соседних блоков.
Теплозащитные свойства опалубки для зимнего периода назначают исходя из наиболее низких температур воздуха. Однако излишнее утепление также вредно, так как уменьшает перепад температур ядро – грань в раннем возрасте и соответственно снижает технологическое обжатие бетона на боковых гранях после выравнивания температур в массивах. Поэтому теплозащитные свойства опалубки в этих зонах должны соответствовать перепадам температур, близким к предельным, обеспечивая тем самым максимальное обжатие бетона, подверженного впоследствии неблагоприятным внешним воздействиям.
Теплозащитные свойства опалубки характеризуются коэффициентом теплопередачи. По опыту строительства требуемый коэффициент теплопередачи опалубки зависит от температуры
наружного воздуха и, как правило, не должен быть менее следующих значений: |
|
|||
Температура наружного |
|
|
|
|
Воздуха, °С |
– 10 |
– 75 |
–35 |
–45 |
Коэффициент теплопередачи |
|
|
|
|
опалубки, ккал/((м²∙ч)°С) |
1,20 |
0,75 |
0,60 |
0,50 |
По коэффициенту теплопередачи определяют тип и конструкцию опалубки, которые в дальнейшем проверяют на соответствие их теплозащитных свойств требованиям к температурному режиму блоков в данных конкретных условиях. Коэффициент теплопередачи
опалубки или укрытия определяют по формуле |
|
||||||||
K = |
|
|
|
1 |
|
|
|
|
|
1 |
|
+ åδi |
|
||||||
|
|
|
|
i=n |
|
|
|
|
|
|
α |
i=1 |
λ |
i , |
(14.25) |
||||
|
|
|
|
|
|||||
где δi – толщина слоя |
ограждения, м; λi – коэффициент теплопроводности |
материала |
|||||||
каждого слоя ограждения, ккал/(м∙ч∙°С), зависящий от скорости ветра. |
|
Существенное значение при определении коэффициента теплопередачи имеет коэффициент внешней теплопередачи α . Он характеризует интенсивность передачи тепла от поверхности опалубки (бетона) к внешней среде – воздуху (или воде). Коэффициент α зависит главным образом от скорости ветра. Значения α колеблются в следующих пределах: при теплообмене с воздухом и отсутствии ветра α =3,25; при ветре средней скорости 3 – 5 м/с α =13–23 ; при сильном ветре 10–15 м/с α =28–37 ккал/((м2∙ч)°С).
В качестве теплоизоляционных материалов в опалубке применяют дерево, минеральную вату, опилки, шлак, различного вида пенопласты и др.
Наибольшее распространение на гидростройках получил утеплитель из фенольно-резольного поропласта ФРП-I. Применение поропластов позволяет снизить трудозатраты на опалубочных работах за счет использования индустриальных типов опалубки и широкой механизации этих работ. Применение этих материалов позволило создать новую конструкцию теплой несъемной железобетонной опалубки, которая в широких масштабах применялась на строительстве массивно-контрфорсной плотины Зейской ГЭС. Теплозащита боковых граней блоков остается
258
одним из наиболее трудоемких процессов. В особенности это имеет место при возведении облегченных конструкций бетонных плотин, для которых характерны значительное увеличение опалубливаемых поверхностей, усложнение установки и демонтажа опалубки в узких и глубоких полостях. В этих условиях широкое применение несъемной утепленной железобетонной опалубки является одним из путей повышения технологичности таких конструкций плотин.
После укладки бетона в блок должна быть обеспечена теплозащита не только боковых граней, но и горизонтальных поверхностей. При укладке бетона в шатрах в начальный период (3–7 дней) теплозащиту горизонтальных поверхностей обеспечивают поддержанием определенных температур в этих шатрах. Перед снятием шатра поверхности обычно утепляют. В первую очередь к ним следует отнести рулонную пористую резину, покрытие упрочненной пленкой, плиточный и заливочный пенопласты, минеральные маты, маты из полиэтиленовых подушек, пневмоматы с воздушными прослойками и т.д. Трудозатраты при использовании указанных материалов в 3–6 раз меньше, чей при утеплении поверхностей опилками.
Определение требований к распалубке блоков
Существенное значение для предотвращения трещинообразования имеет правильное назначение сроков распалубки блоков бетонирования. Характерной особенностью температурного режима бетонного массива при снятии опалубки и любого другого утепления является так называемый тепловой удар, обусловленный неизбежной разностью между температурой воздуха и температурой поверхности бетона. Если температура воздуха заметно ниже температуры поверхности бетона, то при снятии утепления на бетонной поверхности появятся растягивающие напряжения, которые могут вызвать образование поверхностных трещин. Опасность образования таких трещин зависит от срока бетонирования соседнего блока. Так, если тепловой удар возникает при снятии утепления горизонтальной поверхности блока непосредственно перед началом бетонирования вышележащего блока (менее чем за сутки), то образование поверхностных трещин хотя и нежелательно, но не может считаться практически опасным, так как последующее бетонирование блока прекратит их развитие и ликвидирует уже образовавшиеся трещины. Значительно опаснее образование трещин при распалубке боковых поверхностей массива, если последующее бетонирование соседнего массива будет производиться через неделю или еще позднее. В этом случае поверхностные трещины имеют возможность развиваться в глубь массива и при неблагоприятных условиях превратиться в крупные или даже сквозные трещины.
Другой особенностью рассматриваемого процесса является «ударный» характер воздействия. Быстрое возникновение растягивающих напряжений – менее чем за сутки – практически исключит благотворное влияние ползучести бетона, и релаксации напряжений почти не произойдет. Таким образом, возникающие напряжения будут чисто упругими.
На образование трещин при тепловом ударе существенное влияние оказывают условия теплообмена бетонной поверхности с окружающим воздухом. Понижение температуры поверхностных слоев бетона происходит не мгновенно, а в течение некоторого времени, существенно зависимого от скорости ветра. Натурными наблюдениями установлено, что при умеренном ветре (до 4 м/с) в течение 2–3 ч. может быть допустима разность температур более 20°С, что, конечно, совершенно недопустимо при длительном выдерживании массива в холодном воздухе после распалубки. Следовательно, условия распалубки боковых поверхностей бетонной кладки могут быть определены на основе температурных расчетов проводимых с учетом условий теплообмена с окружающей средой. На основе эпюр температурного поля вычисляют термонапряженное состояние поверхностного слоя бетона, которое добавляется к термонапряженному состоянию, сформировавшемуся в блоке к моменту снятия опалубки. Расчеты выполняют для разных скоростей ветра, определяющих коэффициенты внешней теплопередачи от бетонной стены в воздух. Такое исследование проводят за период не менее недели. По результатам таких расчетов устанавливают осредненные требования к условиям распалубки.
Часто условия распалубки решаются на основании общих рекомендаций или непосредственно по данным наблюдений на каждом строительстве. Например, для сурового климата практика строительства выработала следующие рекомендации: опалубка боковых поверхностей отдельных
259
блоков и столбов не снимается вплоть до подготовки соседних столбов к бетонированию, опалубка на низовой грани плотин снимается не ранее, чем через один год после бетонирования и только в теплое время года – в начале лета, на верховой грани плотин опалубка выдерживается везде, где это возможно по производственным условиям, вплоть до затопления водохранилища. Должны предусматриваться также специальные меры для предотвращения теплового удара при распалубке поверхности галерей в теле сооружений. Опасность теплового удара на них усугубляется тем, что в галереях, как правило, возникает воздушный поток с достаточно большой скоростью, способствующей быстрому переохлаждению поверхностных слоев бетона.
Особенности теплозащиты бетона в условиях сухого и жаркого климата
Остановимся на некоторых особенностях теплозащиты бетона в условиях сухого и жаркого климата. В этих условиях особое внимание следует уделять технологическим мероприятиям по температурному регулированию твердеющего бетона, позволяющим существенно снизить максимальную температуру при экзотермическом разогреве бетона. Здесь используют все возможные мероприятия из изложенных ранее, в том числе такие, как искусственное охлаждение уложенного бетона, непрерывный полив горизонтальных и вертикальных поверхностей блока, бетонирование в периоды суток с минимальными температурами (ночью), соблюдение соответствующих перерывов между бетонированием блоков по высоте для повышения эффекта поверхностного охлаждения.
В условиях жаркого климата обычно применяют секционную систему разрезки на блоки бетонирования, поэтому теплозащитные свойства боковой опалубки мало влияют на температурный режим блоков в целом. Наибольшее влияние оказывают условия теплообмена по горизонтальным поверхностям блоков, поэтому применение поверхностного искусственного охлаждения в данных условиях наиболее эффективно. Для того чтобы устранить воздействие солнечных лучей на укладываемую бетонную смесь, блок бетонирования затеняют специальным шатром любой конструкции. В этом случае под шатром создается микроклимат, где температура может быть ниже на 4–5°С температуры наружного воздуха. Относительная влажность воздуха под шатром в жаркие дни может быть выше влажности наружного воздуха на 20–30%. Например, для затенения блоков Токтогульской плотины был применен самоподъемный шатер.
260

ГЛАВА 15. Разрезка сооружений на блоки бетонирования
15.1. Основные причины разрезки сооружений постоянными и временными швами
Существенное влияние на термонапряженное состояние сооружения, его трещиностойкость и монолитность в период строительства и эксплуатации оказывает разрезка сооружений на блоки бетонирования.
Причины, вызывающие необходимость разрезки сооружения на блоки бетонирования, можно разделить на две основные группы. Первая группа – производственные причины, связанные с обеспечением условий возведения сооружения. Вторая группа – причины, связанные с обеспечением трещиностойкости и монолитности сооружений в период строительства и эксплуатации. Обе группы причин требуют возведения сооружения отдельными частями, ограниченными как в плане, так и по высоте, и называемыми блоками бетонирования.
По производственным причинам практически невозможно обеспечить непрерывное возведение массивных сооружений на всю их длину, ширину и высоту. Здесь сказываются ограничения по рациональной высоте опалубки, арматурных конструкций, по очередности возведения сооружений, по производительности бетонного завода и бетоноукладочных средств и др.
По условиям борьбы с трещинообразованием также невозможно обеспечить монолитность массивных сооружений без разрезки их на отдельные блоки системой швов. Швы могут быть постоянными и временными.
Постоянные швы называют температурно-осадочными и осадочными и предназначают для обеспечения возможности взаимных перемещений частей сооружений от температурных деформаций и осадки основания как в период строительства, так и в период постоянной эксплуатации. Постоянные швы устраиваются сквозными, разрезающими все тело сооружения до основания, и несквозными – в виде надрезов, проходящих либо только в верхней части сооружений и не доходящих до ее основания, либо вдоль наружных граней сооружений на глубину распространения существенных колебаний температуры бетона в период эксплуатации (обычно 4–6 м.).
Применительно к плотинам эти швы устраивают, как правило, плоскими нормально к оси плотины и делят ими плотину на отдельные секции или части (рис.15.1). Швы снабжают уплотнениями, обеспечивающими их водонепроницаемость и необходимую свободу деформаций. Расстояние между сквозными и несквозными температурными швами определяют расчетом с учетом климатических и геологических условий, высоты плотины, ее конструктивных особенностей и производственно-технологических условий, определяющих температурноосадочные деформации плотины и ее основания.
261
Рис. 15.1. Принципиальные схемы разрезки массивных бетонных плотин постоянными швами: а – высоконапорной на скальном основании, б – низконапорной на мягком основании
1, 2, 3 – глухая, станционная, водосливная части плотин соответственно; 4 – сквозные вертикальные температурно-осадочные швы; 5,6 – температурные швы-надрезы на гребне и на гранях плотины; 7 – водоприемники; 8 – водосливные отверстия
Для сооружений на скальных основаниях расстояния между постоянными швами определяются в зависимости от вышеперечисленных факторов и колеблются в пределах от 9 до 30 м. В табл.15.1 приведены данные о размерах секций плотины (расстояние между температурными швами) по построенным и строящимся высоким плотинам на скальных основаниях. Расположение постоянных температурных швов увязывают с намечаемой схемой пропуска строительных расходов, схемой расположения основных водопропускных отверстий с размерами турбинных блоков здания ГЭС и насосных станций и т.д. Обычно в этих случаях в каждой секции располагают по одному водосливному пролету или по одному агрегату ГЭС (рис.15.I,а).
Для сооружений на мягких основаниях расстояние между постоянными осадочными швами может быть значительно большим, чем на скальных основаниях (до 60 м. и более). В этом случае каждая секция может включать в себя несколько водосливных пролетов или блоков агрегатов (рис15.1,б).
Временные швы называют строительными и устраивают для тех же целей, что и постоянные, но только для строительного периода. Поэтому они в основном рассчитываются на восприятие температурных деформаций, связанных с температурными колебаниями от экзотермического разогрева бетона в строительный период и последующего его остывания под воздействием наружного воздуха.
В период остывания блоков вертикальные строительные швы раскрываются, образуя между блоками щели. Поэтому к моменту нагружения сооружения эксплуатационными нагрузками эти «щели» должны быть ликвидированы или конструкция и взаимные расположения швов должны быть таковы, чтобы обеспечивать совместную монолитную работу отдельных блоков при наличии между ними небольших щелей.
Процесс ликвидации щелей в вертикальных строительных швах между блоками бетонирования обычно называют омоноличиванием сооружения. Омоноличивание швов осуществляется заполнением щелей материалом, способным передавать возникающие между блоками усилия. При этом при небольших раскрытиях швов применяют нагнетание цементного раствора под давлением (способ цементации), а при наличии широких объемных швов – метод заполнения бетоном.
Монолитность горизонтальных межблочных швов достигается специальной обработкой поверхности, обеспечивающей хорошую связь блоков бетонирования. На поверхности блоков после окончания бетонирования образуется так называемая цементная пленка, обладающая большой «пористостью». Обработка поверхности и преследует цель ликвидации такой пленки. Для этого используют различные методы обработки поверхности сжатым воздухом, водой под давлением, механическими щетками или с помощью пескоструйного аппарата. Как показали исследования, прочность горизонтального шва и его водонепроницаемость существенно зависят от длительности перерывов в бетонировании блоков. При регулярной укладке бетона и перерывах в бетонировании, не превышающих 15 дней, обработанный шов мало отличается от монолитного бетона по водонепроницаемости и прочности. Наоборот, при больших перерывах в бетонировании строительный шов существенно отличается по свойствам от монолитного бетона.
262

Таблица 15.1 Размеры секций плотин
|
|
Среднегодовая |
Размеры секций, м |
|
|
|
|
||||
|
|
температура воздуха, |
Водосливная часть |
Станционная часть |
Глухая часть |
|
|||||
|
|
°С |
|
|
|
|
|
|
|||
Плотины |
Породы основания |
Амплитуда |
|
|
|
|
|
|
|||
колебаний |
|
|
|
|
|
|
|||||
|
|
|
|
|
|
|
|
||||
|
|
температуры |
Ниже УМО Выше УМО Ниже УМО Выше УМО |
Ниже УМО |
Выше УМО |
||||||
|
|
наружного воздуха, |
|
|
|
|
|
|
|||
|
|
°С |
|
|
|
|
|
|
|||
|
|
|
|
|
|
|
|
|
|
|
|
Бухтарминская |
Габбро, амфиболиты |
|
+ 2 |
|
|
18 |
- |
19–20 |
- |
13–15 |
- |
|
|
|
80(+35... − 45) |
|
|
|
|
|
|
||
Мамаканская |
Криссталические |
|
− 5,6 |
|
|
|
|
|
|
|
|
|
сланцы |
|
15 |
6–9 |
14 |
6–9 |
15 |
7,5 |
|||
|
|
97(+37... − 60) |
|||||||||
|
|
|
|
|
|
|
|
|
|||
Братская |
Диабазы |
|
− 2,6 |
|
22 |
22 |
22 |
22 |
11 |
11 |
|
|
|
|
93(+37... − 56) |
|
|
|
|
|
|
||
Красноярская |
Граниты |
|
− 0,4 |
|
15 |
15 |
15 |
15 |
15 |
7,5 |
|
|
|
|
91(+37... − 54) |
||||||||
|
|
|
|
|
|
|
|
|
|||
Зейская |
Диариты |
|
− 4,1 |
|
15 |
6–9 |
11 + |
22 |
15 |
7,5 |
|
|
|
|
22 |
||||||||
|
|
|
87(+35... − 52) |
||||||||
|
|
|
|
|
|
|
|
||||
|
|
|
|
|
|
|
|
|
П р и м е ч а н и е: «+» В числителе – до водоприемника; в знаменателе – выше водоприемника.
15.2. Основные принципы разрезки сооружений на блоки бетонирования
Размеры блоков бетонирования во многом зависят от системы разрезки сооружений на блоки бетонирования. В практике гидротехнического строительства применяются следующие основные системы разрезки: с перевязкой швов («днепровская»), столбчатая, секционная (длинными блоками), послойная а также ряд комбинаций и разновидностей этих систем.
Особенности разрезки на блоки бетонирования при различных системах будут даны ниже, в соответствующих разделах. Здесь же отметим только некоторые общие принципы разрезки, касающиеся всех систем.
Форма блоков бетонирования должна быть по возможности простой. Обычная форма блока – прямоугольный параллелепипед, иногда с одной или двумя скошенными гранями.
Размеры блоков бетонирования в плане определяются как чисто производственными условиями (мощность бетонного хозяйства, сроки перекрытия слоев и т.д.), так и требованиями к температурному режиму блоков с точки зрения обеспечения условий отсутствия трещинообразования
Максимальные плановые размеры блоков по производственным условиям определяются прежде всего производительностью комплекса бетоносмесительных и бетоноукладочных машин. По этим условиям площадь блока и производительность этих машин связаны следующей зависимостью:
Fбл = |
Пэ (τ схв −τ тр )nN |
|
|
|
hсл |
, |
(15.1) |
||
|
где: Fбл – площадь блока, м²; hсл – толщина укладываемого слоя, м; Пэ – эксплуатационная производительность определяющей машины на стадии приготовления, транспорта, подачи и уплотнения бетона, м³/ч; n – число одновременно бетонируемых
слоев в блоке (обычно 1, реже 2); τ схв – время начала схватывания бетонной смеси (ч); N
– число одновременно работающих машин; τ тр – время транспортирования бетонной смеси (ч). Эта формула выражает требование о том, чтобы перекрытие нижележащего слоя бетона вышележащим при укладке происходило за время до начала схватывания бетона
Высота блоков бетонирования по производственным условиям определяется главным образом конструкцией и условиями крепления опалубки
В целом при выборе систем разрезки на блоки бетонирования и размеров блоков следует иметь в виду следующее:
1.Любой строительный шов может стать слабым сечением в сооружении в отношении водопроницаемости и прочности. По указанным причинам следует всячески стремиться к уменьшению числа строительных швов.
2.Взаимное расположение блоков должно обеспечить свободу раскрытия швов между ними в строительный период и монолитную работу в период эксплуатации, что обеспечивается или омоноличиванием швов, или специальными условиями расположения блоков.
3.С точки зрения производства бетонных работ в блоке их размеры должны быть максимально большими, что обеспечивает лучшую механизацию всех работ внутри блока, повышает производительность и интенсивность работ, уменьшает их стоимость.
4.С точки зрения обеспечения условий трещиностойкости размеры блоков должны быть как можно меньше.
5.Противоречивые требования к размерам блоков по п. 3 и 4 должны разрешаться технико-экономическим сопоставлением различных вариантов разбивки на блоки. Чем больше размеры блоков при прочих равных условиях, тем меньше материальные и трудовые затраты на опалубочные работы, на укладку бетона в блоки, но выше затраты на
264

технологические мероприятия по обеспечению трещиностойкости блоков данных размеров..
6. В принципе в большинстве случаев может быть применена любая известная система разрезки при достаточно широком диапазоне размеров блоков бетонирования. Задача состоит в выборе оптимальной разрезки, обеспечивающей возведение монолитного бетонного сооружения в заданные сроки при наименьшей стоимости.
15.3. Разрезка ярусная «вперевязку» («днепровская»)
Сущность. Эта система предусматривает разрезку сооружения на блоки с взаимной их перевязкой (перекрытием) по типу кирпичной кладки (рис. 15.2, 15.3).
Рис. 15.2. Схема ярусной «вперевязку» разрезки для сооружений на мягких основаниях
1 – вертикальные межблочные строительные швы; 2 – горизонтальные межблочные швы; 3 – высота блоков; 4 – длина блоков; 5 – длина секций; 6 – постоянные температурно-осадочные швы; 7 – постоянные швы-надрезы; 8 – площадка скольжения; 9
– направление температурных деформаций граней блоков; 1, 2…9 – последовательность бетонирования блоков в плане
Обеспечение монолитности. Совместная работа блоков и монолитность сооружения обеспечивается наличием и соблюдением определенных конструктивных и технологических условий: а) условий, исключающих образование трещин на продолжении межблочных швов; б) температурных условий для минимального раскрытия этих швов.
Для выполнения первого условия требуется, чтобы система укладки допускала взаимные смещения (проскальзывание) блоков относительно друг друга в период их температурных деформаций, т.е. в период их остывания до принятия нагрузок. В строительный период по горизонтальным плоскостям скольжения между блоками действуют вертикальные напряжения от собственного веса вышележащих блоков. Общее
265

сопротивление |
проскальзыванию Т |
пропорционально этим напряжениям σ x , длине |
|||||
участка перевязки блоков |
lпер |
и коэффициенту трения бетона по бетону |
f |
, т.е. |
|||
|
|
||||||
T = ϕ(σ x , |
lпер , f ) |
. |
|
|
|
|
|
|
|
|
|
|
|
|
Для обеспечения «проскальзывания» это сопротивление не должно быть больше сопротивления разрыву вышележащего блока, в противном случае в нем образуется трещина. Сопротивление разрыву вышележащего блока зависит от прочности бетона на
растяжение и |
высоты |
блока. Из |
этих |
условий при данной |
системе разрезки |
||
ограничивается |
высота |
сооружений, |
т.е. |
σ |
x , и перекрытие блоков |
lпер |
. Расчеты и |
|
|
практика показывают, что при наиболее распространенных условиях высота сооружений не должна превышать 50 м., а перекрытие шва по величине не должно превышать половины высоты блока бетонирования.
lпер ≤ Hбл / 2 |
. |
(15.2) |
|
Рис. 15.3. Схема ярусной «вперевязку» разрезки в плотинах на скальных основаниях I – вертикальные межблочные строительные швы; 2 – горизонтальные межблочные
швы; 3 – высота блоков; 4 – длина блоков; 5 – длина секции; 6 – постоянные температурно-осадочные швы; 7 – возможные постоянные швы-надрезы; 8 – площадка скольжения; 9 – направление температурных деформаций граней блоков; 10 – участок глухой плотины; 11 – участок водосливной плотины; 12 – возможное дополнительное армирование над швом
В конкретных условиях эти ограничения можно обосновать расчетами, исходя из указанных требований. Для уменьшения трения по плоскости скольжения полезно также проводить «заглаживание» участка перехлеста в нижележащем блоке. При невозможности выдерживания данного условия необходимо предусматривать дополнительное армирование этого блока на участке над нижележащим швом. Для выдерживания второго условия по минимальному раскрытию швов требуется выдерживание определенного температурного режима.
266
Обеспечение необходимого температурного режима. Основным средством регулирования температурного режима в блоках при данной системе является естественное и искусственное поверхностное охлаждение горизонтальных поверхностей блоков в период перерывов в бетонировании смежных по высоте блоков. При этом рекомендуется, чтобы укладка соседнего и вышележащего блоков производилась после остывания ранее уложенного и прохождения в нем основных температурных деформаций. Для этого укладку блоков в одном ярусе ведут в строго определенном шахматном порядке, обеспечивающем значительные временные разрывы в укладке смежных блоков. Опыт строительства показывает, что такие перерывы должны быть не менее 7–14 дней (1– 2 недели) в зависимости от конкретных условий. Это обстоятельство значительно ограничивает интенсивность ведения бетонных работ по высоте.
В случае возможных значительных температурных деформаций в строительный период применяют так называемые «замыкающие блоки», которые бетонируются после прохождения температурных и осадочных деформаций между соседними блоками.
Размеры блоков. Размеры блоков бетонирования на скальных основаниях определяются как производственными условиями, так и требованиями трещиностойкости. Для скальных оснований по опыту практики в основном применяют блоки с плановыми размерами до 20 м. при высоте 3–4 м. На мягких основаниях размеры блоков обусловливаются практически только производственными условиями и могут достигать значительно больших размеров.
Преимущества и недостатки. Преимуществом данной системы является отсутствие цементации (омоноличивания) швов. Совместность работы отдельных блоков обеспечивается перекрытием, или перевязкой, швов по высоте. Это преимущество обеспечило ее большое распространение для бетонных и железобетонных сооружений небольшой высоты – до 50 м. – как на скальных, так и особенно на мягких основаниях.
Недостатком является ограниченная область применения (для относительно невысоких сооружений) и относительно малая интенсивность роста сооружений по высоте.
Область применения. Система разрезки «вперевязку» впервые была применена при строительстве плотины Днепровской ГЭС, отчего ее часто называют Днепровской. Все плотины на скальных основаниях небольшой высотой возведены с такой разрезкой (Волховская, Ондская, Бухтарминская и др.), а также все плотины на мягких основаниях (плотины каскада Волжских, Днепровских, Камских и других ТЭС).
Особенно широко применяется эта система при возведении таких сооружений, как подпорные стены, здания гидроэлектростанций, водосборные сооружения деривационных ГЭС, судоходные шлюзы и др. Применение ее здесь имеет некоторые особенности для внешне статически неопределенных конструкций, например, отсасывающих труб ГЭС, водозаборных сооружений, днищ шлюзов и др. Такие конструкции разбиваются швами на отдельные статически определимые элементы, в которых не возникает усилий при изменении температуры составляющих ее элементов. Между статически определимыми элементами оставляют объемные швы (замыкающие блоки), которые омоноличиваются (бетонируются) после достижения бетоном омоноличиваемых конструкций температур, назначенных в проекте, из условий получения наименьших температурных напряжений в статически неопределимой системе (рис. 15.4).
267

Рис. 15.4. Схема разрезки с применением замыкающих блоков; а – камер шлюзов; б – рамных конструкций ГЭС, водоприемников 1 – вертикальные межблочные швы; 2 – горизонтальные межблочные строительные швы;
3 – постоянные температурно-осадочные швы; 4 – замыкающие блоки
Соответственно обусловливают и порядок возведения таких сооружений: вначале возводят статически определимые элементы, затем производят омоноличивание швов, после чего система становится статически неопределимой, реагирующей на изменение температуры в любом элементе. Устройство объемных замыкающих блоков является основным методом омоноличивания строительных швов при возведении таких конструкций. В статически определимых конструкциях таких сооружений обычно применяют рассмотренную выше систему разбивки вперевязку. Размер и расположение швов определяют условиями производства работ и конструктивными особенностями каждого элемента. Во всех случаях следует стремиться к возможно большей высоте блоков бетонирования, особенно в стенах и бычках. Часто высота блоков бетонирования определяется размерами отдельных армоконструкций или армопанелей, служащих опалубкой блока, и достигает 9–12 и более метров.
Решение вопросов трещиностойкости блоков бетонирования зависит от наличия или отсутствия арматуры в конструкциях, В случае армированной конструкции, к которой не предъявляется требование трещиностойкости, специальных мер для обеспечения ее трещиностойкости можно не принимать, ограничиваясь лишь выполнением требований допустимого раскрытия трещин. В неармированных конструкциях или в армированных, к которым предъявляется требование трещиностойкости, необходимо предусматривать соответствующие меры, обеспечивающие их монолитность к моменту ввода в
эксплуатацию.
15.4. Столбчатая система разрезки
Столбчатая система разрезки заключается в разрезке плотины на отдельные «столбы» вертикальными строительными межстолбчатыми швами, параллельными оси плотины. Каждый столб разбивается по высоте на отдельные блоки горизонтальными строительными швами. Применяют два варианта столбчатой разрезки с тонкими межстолбчатыми швами и с объемными межстолбчатыми швами.
А. Система разрезки с тонкими межстолбчатыми швами
Сущность: В столбчатой разрезке с тонкими межстолбчатыми швами столбы бетонируются «впритык» друг к другу (рис. 15.5). В дальнейшем в период остывания блоков после экзотермического разогрева эти швы раскрываются, образуя между столбами «щели» (тонкие швы).
268

Рис. 15.5. Схема столбчатой разрезки с «тонкими» межстолбчатыми швами: а – разрез; б – вид с В.Б.; в – план; г – схема траекторий главных напряжений
I – вертикальные цементируемые межблочные «тонкие» швы; 2 – горизонтальные межстолбчатые швы; 3 – постоянные (температурно-осадочные) межсекционные швы; 4 – прискальная зона с Нбл ≤ 1,5–3,0 м.; 5 – переходная зона с Нбл ≈ 3,0 м.; 6 – свободная зона с Нбл > 3,0 м.
Обеспечение монолитности сооружения. Совместную работу отдельных столбов (монолитность сооружения) обеспечивают путем заполнения «щелей» в межстолбчатых швах цементным раствором. Этот процесс называется омоноличиванием швов (сооружения). Поскольку, как следует из гл.14, в массивных сооружениях в период эксплуатации устанавливаются температуры, близкие к среднегодовой, то и омоноличивание швов во избежание их дальнейшего раскрытия должно осуществляться при температурах в омоноличиваемых столбах, близких к эксплуатационной, т.е. к среднегодовой для данной зоны сооружения. При этом допускается превышение этих температур не более чем на 2–5°С в зависимости от удаления от контактной зоны со скалой. Для проведения работ по омоноличиванию предусматривают заблаговременную укладку в межстолбчатые швы специальных клапанов – выпусков с системой труб для подачи раствора. Для передачи усилий от одного столба к другому в плоскости межстолбчатых швов предусматривают горизонтальное штрабление. С целью исключения в плоскости швов больших скалывающих напряжений направление граней горизонтальных штраб должно быть перпендикулярно траекториям главных напряжений (см. рис. 15.5,г).
Обеспечение температурного режима. Температурный режим блоков бетонирования обеспечивают широким комплексом мероприятий, начиная от охлаждения составляющих бетонной смеси на бетонном заводе, выбором размеров блоков и кончая применением трубного охлаждения в блоках. Наиболее часто применяют трубное охлаждение. Оно наиболее эффективно тогда, когда необходимо снизить не только температуру экзотермического разогрева, но и сократить сроки охлаждения массива до температур омоноличивания.
Размеры блоков в плане в принципе определяются факторами, изложенными выше, и зависят в основном от климатических условий, технологии работ и намечаемых мероприятий по регулированию температурного режима. Размер блока вдоль оси плотины обычно равен размеру секции, т. e. расстоянию между постоянными температурноосадочными швами. В этих же пределах принимают размеры поперек оси плотины.
269
Исходя из опыта строительства плановые размеры блоков колеблются в основном от 12 до 15 м. для особо суровых климатических условий и от 20 до 25 м. – для средних и благоприятных. Меньшие величины имеют место для блоков, расположенных на более жестких основаниях, большие – на более податливых. В конкретных условиях при наличии усиленных мероприятий по регулированию температурного режима максимальные размеры блоков могут быть значительно больше, но, как правило, не превосходят 25–30 м.
Размеры блоков по высоте должны выбираться технико-экономическим сравнением в увязке с типом опалубки, мощностью бетоноукладочных механизмов и требуемой интенсивности укладки бетона с обязательным обеспечением требований трещиностойкости. Исследования показывают, что при применении в качестве основных бетоноукладочных механизмов кранов КБГС-450, КБГС-1000м. оптимальная высота блоков в удалении от жесткого основания из условия обеспечения максимальной интенсивности бетонных работ составляет 6–12 м. При применении одной из наиболее перспективных опалубок – консольной двухъярусной «саянского» типа, позволяющей осуществлять ее установку, т.е. наращивание, в процессе бетонирования, высота блоков из тех же условий может быть еще выше. Практически на строительстве Саяно-Шушенской ГЭС высота блоков достигла 18 м. При этом, безусловно, должны применяться усиленные мероприятия по обеспечению требуемого температурного режима для обеспечения трещиностойкости блоков.
При использовании обычной щитовой опалубки высота блоков в основном составляет 3–4 м, редко больше. При выборе высоты блоков, укладываемых на «жесткое» основание (скала, «старый бетон»), следует иметь в виду следующее. Опыт расчетов термонапряженного состояния прискальных блоков показывает, что при увеличении относительной высоты блока температурные напряжения падают, поэтому для обеспечения благоприятного термонапряженного состояния бетонной кладки целесообразно производить регулярное бетонирование блоков в основании с малыми перерывами. Это дает право принимать относительную высоту блока исходя из общей суммарной высоты нескольких блоков, для которых можно гарантировать непрерывную укладку. С другой стороны, такая укладка ведет к повышению температуры разогрева и тем самым к увеличению температурных напряжений при остывании. Поэтому без проведения расчета, учитывающего конкретные условия, нельзя сказать, что выгоднее принимать для данного конкретного случая – низкие блоки, бетонируемые с большими перерывами, дающие наибольшее естественное остывание бетона, или более высокие блоки, бетонируемые с малыми перерывами, дающие наиболее выгодное термонапряженное состояние бетона.
В американской практике строительства принято прискальные блоки укладывать высотой 1,0 – 1,5 м. Отечественный опыт имеет примеры, показывающие выгодность укладки прискальных блоков высотой 3 м. с максимальным темпом укладки по высоте. В целом можно считать, что при отсутствии регулирования температуры бетона в прискальных блоках следует принимать блоки с достаточно большими перерывами в бетонировании. При наличии достаточно эффективного регулирования температуры и основания средней жесткости выгоднее применять бетонирование высокими блоками с малыми перерывами.
Преимущества и недостатки. Основное преимущество столбчатой разрезки – простота и независимость бетонирования отдельных столбов, что обеспечивает высокие темпы возведения сооружения при одновременном обеспечении условий трещиностойкости блоков бетонирования. Иногда, при наличии условий для зависания соседних столбов друг на друга и недопустимого перекоса столбов при их несимметричном остывании, превышение одного столба над соседним при бетонировании ограничивают 9–12 м.
270
Недостаток этой системы – необходимость проведения дополнительных работ по омоноличиванию (цементации) швов и относительно малый плановый размер блоков. Последнее обстоятельство ограничивает возможность полной механизации внутриблочных работ.
Область применения. Возможность применения широкого спектра мероприятий по регулированию температурного режима и обеспечению трещиностойкости блоков бетонирования обусловливают широкую область применения этой системы. Она может применяться практически в любых климатических условиях. Наибольшее распространение в отечественной практике она получила в суровых климатических условиях, где по условиям трещинообразования затруднено применение других более технологичных решений (например, плотины Братской, Усть-Илимской, Красноярской, Саяно-Шушенской и других ГЭС).
Необходимость омоноличивания швов с помощью цементации накладывает некоторые ограничения на область применения этой системы разрезки для особо суровых климатических условий. Это связано с тем, что качественная цементация швов при обычной технологии требует наличия положительных температур бетона в околошовном объеме. Обеспечить эти условия в особо суровых условиях очень сложно. Поэтому до последнего времени в особо суровых условиях при среднегодовых температурах ниже 3– 4° эта система не применялась.
В последнее время успешно отрабатываются методы отогрева околошовного пространства с помощью электрообогрева или горячим паром и водой. При освоении указанных методов эта система с плотными швами при прочих равных условиях может применяться и в особо суровых климатических условиях.
Разновидностью системы столбчатой разрезки с вертикальными тонкими швами является система столбчатой разрезки с наклонными швами. При этой системе межстолбчатые швы располагают не вертикально, а наклонно, примерно по направлению траекторий главных напряжений. При соответствующих условиях применение такой системы в плотинах может позволить отказаться от цементации (омоноличивания) межстолбчатых швов, так как обеспечивает независимую работу столба при восприятии напора на плотину. Такая система применялась при строительстве ряда массивноконтрфорсных плотин в Италии.
Б. Столбчатая разрезка с объемными межстолбчатыми швами
Сущность. При этой системе столбы бетонируются отдельно друг от друга с оставлением между ними полостей, так называемых объемных межстолбчатых швов, шириной 1,2 – 1,5 м. (рис. 15.6).
Обеспечение монолитности. Омоноличивание сооружения осуществляют бетонированием межстолбчатых швов при температурах в омоноличиваемых столбах ниже среднегодовой температуры воздуха. Имеется практическая возможность бетонирования объемных межстолбчатых швов – т.е. омоноличивания бетонной кладки – не только при положительных, но и при отрицательных температурах бетона в омоноличиваемых столбах (см. рис.15.6). Опыт показал, что для качественного омоноличивания объемных швов в условиях промороженного бетона в столбах плотины достаточно отогреть боковые поверхности столбов, что не представляет никаких сложностей.
271

Рис. 15.6. Схема столбчатой разрезки с объемными межстолбчатыми швами в массивных контрфорсных плотинах.
I – объемные межстолбчатые швы; 2 – горизонтальные межблочные швы; 3 – постоянные (температурно-осадочные) межсекционные швы; 4 – прискальная зона с Нбл ≤ 1,5–3,0 м.; 5 – переходная зона с Нбл ≈ 3,0 м.; 6 – свободная зона с Нбл > 3,0 м.; 7 – замыкающие блоки
Обеспечение необходимого температурного режима. Температурный режим обеспечивают теми же средствами, что и в разрезке с тонкими швами. В то же время наличие объемных швов улучшает условия охлаждения бетонной кладки и уменьшает потребность в искусственном трубном охлаждения, По существу трубное охлаждение в этих случаях требуется только в прискальных блоках и в особо массивных блоках, в частности в верховом оголовке. В остальной части бетонной кладки удается обойтись подбором надлежащей опалубки и температуры бетонной смеси. Температура омоноличивания швов достигается за счет остывания бетона в столбах в течение однойдвух зим.
Размеры блоков. Все рассуждения, касающиеся плановых и высотных размеров блоков бетонирования и конструкций швов, изложенные ранее применимы и при этой системе.
Преимущества и недостатки. Основное преимущество этой системы по сравнению с тонкими швами – возможность омоноличивания сооружений при полностью промороженном бетоне в столбах, что обусловливает ее применение в особо суровых климатических условиях.
Кроме того, имеется возможность независимого возведения отдельных столбов практически на всю высоту без ограничений, которые имеются в первом варианте.
Особым преимуществом данной системы является возможность обжатия верховой грани плотины и улучшения ее напряженного состояния за счет бетонирования замыкающих блоков при температурах столбов ниже эксплуатационных и последующего отогрева этих столбов до постоянных эксплуатационных температур. Регулируя температурные условия столбов при омоноличивании и вызывая тем самым предварительные горизонтальные деформации (наклоны) столбов, можно целенаправленно влиять на напряженное состояние верхового столба плотины в нужном направлении. Это преимущество во многом было реализовано при строительствах плотин Мамаканской и Зейской ГЭС.
272

Основной недостаток этой системы – трудоемкость устройства объемных межстолбчатых швов и последующего их бетонирования. Для снижения этого недостатка межстолбчатые швы рекомендуется выполнять не в деревянной опалубке, а в железобетонной несъемной опалубке. Такое решение было реализовано на строительстве Зейской ГЭС и показало его рациональность и эффективность.
Область применения. Применяется в основном там, где затруднено использование столбчатой системы с тонкими швами. А именно в особо суровых климатических условиях при среднегодовых температурах воздуха ниже минус 3– 4°С.
Система была разработана и внедрена при строительстве массивно-контрфорсных плотин Мамаканской и Зейской ГЭС, расположенных в районах вечной мерзлоты.
15.5. Секционная система разрезки длинными блоками
Сущность. Секционная система разрезки длинными блоками предусматривает разрезку плотины горизонтальными блоками, имеющими в плане размеры, равные размеру секции и более. При размерах блоков, более чем размер секции, межсекционные швы образуются путем предварительной установки в них специальпой опалубки или путем нарезки этих швов после бетонирования.
Система имеет ряд разновидностей. Основными из них являются;
-секционная система с многослойными длинными блоками;
-секционная система с однослойными длинными блоками из обычного бетона;
-секционная система с однослойными длинными блоками из укатанного жесткого бетона.
А. Секционная система с многослойными длинными блоками
Сущность системы. Укладываются блоки, размер которых в плане равен размеру
секции, а высота – до 3 м, небольшими по толщине слоями (0,3–1,0 м) из обычного бетона (рис. 15.7).
Рис. 15.7. Схема секционной разрезки с многослойными длинными блоками
I – межсекционные температурно-осадочные швы; 2 – горизонтальные блочные швы; Нбл – высота блока; hсл – толщина слоя
Обеспечение монолитности. Поскольку размер блока в плане равен размеру секции без дополнительных строительных швов в пределах секции, то вопрос об омоноличивании тела гравитационных и массивно-контрфорсных плотин при этой системе вообще отпадает. Необходимо только обеспечить отсутствие в строительный период трещин в блоках бетонирования.
При возведении арочных плотин монолитность работы плотины вдоль оси обеспечивают цементацией межсекционных швов, как и в столбчатой разрезке, для чего в эти швы закладывают соответствующую арматуру.
Обеспечение температурного режима. Основным средством регулирования температурного режима в блоках бетонирования при больших площадях блоков является
273

искусственное поверхностное и трубное охлаждение. Поэтому эта система предусматривает блоки небольшой высоты – до 1,5–3,0 м., с укладкой бетона в несколько слоев. Расчеты показывают, что при бетонировании длинных низких блоков в прискальной зоне должен соблюдаться более жесткий температурный режим, чем в варианте столбчатой разрезки с блоками ограниченных размеров.
Преимущества и недостатки. Преимуществами данной системы являются:
-большие плановые размеры блоков, что улучшает условия механизации внутриблочных работ;
-отсутствие межстолбчатых строительных швов в пределах секции, а следовательно, отсутствие необходимости в омоноличивании блоков (в цементации) для массивных и массивно-контрфорсных плотин.
Для арочных плотин вопрос омоноличивания сводится только к цементации межсекционных швов. Отсутствие межстолбчатых швов в арочных плотинах уменьшает в целом количество швов и обеспечивает более определенную пространственную работу плотины.
Недостатком данной системы являются производственные сложности в обеспечении температурных условий в блоках.
Область применения. В связи со сложностью обеспечения необходимого
температурного режима для исключения трещинообразования эта система в основном применяется в средних и благоприятных климатических условиях, где отсутствуют резкие колебания температур и где легче выполнение технологических мероприятий, обеспечивающих условия трещиностойкости длинных неразрезных блоков. Наиболее широкое применение эта система нашла в основном в зарубежной практике, в частности в США, где высота блоков бетонирования принята 1,5 м. В отечественной практике эта система не нашла широкого применения. Имеется только опыт бетонирования блоков длиной около 50 м с площадью около 750 м² (плотина Бухтарминской ГЭС) и опытной укладки небольшого числа длинных блоков (Братская ГЭС, Красноярская ГЭС).
Б. Секционная система с однослойными длинными блоками из обычного бетона
Сущность системы состоит в укладке блоков возможно больших плановых размеров с высотой блока, равной толщине слоя укладываемого обычного бетона (рис. 15.8). В этом случае сроки перекрытия слоев не регламентируют, так как блок состоит из одного слоя и укладку его можно вести достаточно длительное время, в зависимости от мощности бетонного хозяйства.
Рис. 15.8. Схема секционной разрезки с однослойными блоками: а – вид с В.Б.; б – план;6 в – Разрез
274
1 – межсекционные температурно-осадочные швы, образуемые двухрядной железобетонной опалубкой; 2 – горизонтальные межблочные швы; 3 – железо-бетонная опалубка в два ряда; 4 – проемы в железо-бетонной опалубке; 5 – уплотнения температурно-осадочных швов
Толщина слоя – высота блока – зависит от типа и мощности средств уплотнения (вибраторов, пакетов вибраторов) и составляет 0,75 – 1,5 м.
Температурный режим обеспечивается теми же мероприятиями, что и в схеме с многослойными блоками, т.е. поверхностным охлаждением, а при необходимости – трубным охлаждением.
Преимущества и недостатки. Основным преимуществом этой системы является возможность практически полной комплексной механизации всех элементов бетонных работ и получения высоких темпов укладки. На строительстве плотины Альпа-Джера в Италии среднесуточная интенсивность укладки бетона достигала 3825 м³, а максимальная
– 7620 м³.
Недостатком этой системы является трудность создания температурных условий для предотвращения трещинообразования. Требуется или сезонная работа или устройство шатра над всей бетонируемой частью плотины, что затрудняет ее применение в суровых условиях Сибири и Дальнего Востока.
Область применения. Так же как и в предыдущей системе, область ее применения ограничивается теми же условиями. Впервые такая система разрезки была применена в Италии на строительстве плотины Альпа-Джера. В плотину укладывался тощий жесткий бетон в один слой толщиной 70 см. от берега до берега. Бетон к месту укладки подавали автосамосвалами, разравнивали бульдозерами и уплотняли пакетами вибраторов, укрепленных на тракторе. Через несколько часов после бетонирования в уложенном слое нарезали усадочные швы, для чего использовали специальные машины. Необходимый температурный режим обеспечивали, применяя тощий бетон с малым расходом цемента (расход в центральной части 113 кг/м³) и естественным поверхностным охлаждением. При низких температурах в зимний и весенний периоды бетонирование плотины прекращали. Для обеспечения водонепроницаемости такой плотины предусматривался металлический экран.
В отечественной практике эта система разрезки применялась при возведении сооружений так называемым «токтогульским» методом. «Токтогульский» метод укладки бетона заключается в том, что так же, как и на Альпа-Джера, укладка бетона ведется одним слоем, но в отличие от Альпа-Джера предусматривается наличие как межсекционных, так и – в случае необходимости – межстолбчатых строительных швов. Эти швы образуются путем установки сборной железобетонной опалубки. В межсекционных швах предусматривают установку двух рядов плит с наличием соответствующих уплотнений между ними, что исключает необходимость устройства противофильтрационных экранов. При необходимости создания межстолбчатых швов в них устанавливают однорядную железобетонную опалубку с заложенной в ней цементационной арматурой. Омоноличивание этих швов производится их цементацией, как и в столбчатой системе с плотными швами. Высота железобетонной опалубки, образующей отдельные карты бетонирования, значительно выше укладываемых слоев бетонной смеси, что позволяет возобновлять бетонирование, не устанавливая опалубку каждый раз заново. Бетон к месту укладки подают автосамосвалами или кранами. Для проезда транспорта через швы в опалубке швов предусматривают проезды – в этих местах опалубку просто не устанавливают. Разравнивание и уплотнение бетонной смеси ведут горизонтальными или слабонаклонными слоями толщиной 0,5 – 1,0 м. в определенной последовательности с таким расчетом, чтобы разница в высоте смежных блоков (карт) была не более толщины одного слоя. Это обеспечивает равномерное наращивание сооружения по высоте и возможность перемещения бетоноукладочных механизмов из
275
одной карты в другую. При необходимости используют инвентарные мостики, пандусы и другие устройства.
Поверхность уплотненного слоя укрывают полиэтиленовой пленкой для предотвращения испарения из него воды и выдерживают под ней свежеуложенный бетон до набора того минимума прочности, который позволяет машинам типа тротуароуборочных или поливомоечных быстро и качественно снять цементную пленку с поверхности блока и тем самым обеспечить монолитность горизонтальных швов.
Температурный режим блоков бетонирования обеспечивают в основном созданием искусственного микроклимата над блоками бетонирования, поверхностным охлаждением и применением жестких бетонов с малым расходом цемента. Искусственный микроклимат создают с помощью самоподъемного шатра над всей площадью в пределах контура сооружения, и укладка бетона ведется под прикрытием этого шатра. Зимой в подшатровом пространстве поддерживают положительные температуры, летом шатер служит защитой от солнечной радиации, ветра и осадков. Рассеивание тепла экзотермии обеспечивается в основном за счет поверхностного охлаждения в период между укладкой слоев. Каждый блок до укладки на него следующего выдерживают до 3–7 сут. За это время бетон приобретает необходимую прочность к началу движения по нему бетоноукладочных машин и механизмов, и благодаря относительно малой толщине слоя за этот период рассеивается до 70–80% тепла экзотермии. В летнее время используют искусственное поверхностное охлаждение путем полива водой, систематического увлажнения, создания «водяной рубашки» и др. Для окончательного охлаждения бетонной кладки до температур омоноличивания может применяться искусственное трубное охлаждение путем укладки труб через определенные интервалы по высоте сооружения (через несколько слоев). Все технологические операции при «токтогульском» методе бетонирования выполняют в определенной строгой и взаимоувязанной последовательности, что обеспечивает равномерный график укладки и ритмичность бетонных работ. Организуется непрерывный циклично-поточный технологический процесс, приближающийся к заводской технологии в цехе. Темпы роста сооружения по высоте могут достигать 6–8 м/мес. при значительно меньших трудозатратах на внутриблочные работы, чем при столбчатой системе разрезки и других методах бетонирования.
В. Секционная система разрезки с однослойными длинными блоками из укатанного жесткого бетона
Основная суть та же, что и для предыдущей системы (см. рис. 15.8). Разница заключается в том, что в блок укладывают не обычный, а жесткий бетон, уплотняемый катками (так называемый укатанный жесткий бетон). Толщина слоя при этом равна, по данным практики, 0,3–0,5 м. в зависимости от состава бетона и мощности катков для уплотнения.
Температурный режим блоков обеспечивается в основном малым расходом цемента (до 100–120 кг/м³) и дополнительно заменой части этого цемента золой – уноса, что сильно снижает температуру экзотермического разогрева, а следовательно, температурные перепады.
Основные преимущества и недостатки те же, что и в предыдущей системе. Кроме того, применение укатанного бетона по всей ширине плотины, в том числе и в напорной грани, вызывают определенные технологические осложнения, особенно в суровых климатических условиях.. Обычно для напорной грани предусматривают укладку обычного вибрируемого бетона. В этих случаях для суровых климатических условий наиболее рациональной может оказаться смешанная система разрезки с комбинацией столбчатой и секционной разрезок.
276
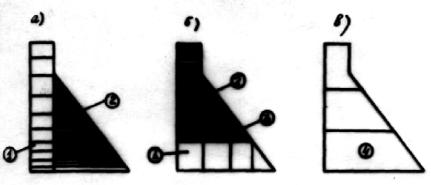
15.6. Смешанные системы разрезки
Кроме изложенных выше трех основных систем разрезки на блоки бетонирования и их разновидностей существуют различные их сочетаний (рис. 15.9). Наиболее перспективна из них смешанная система разрезки из комбинации столбчатой разрезки и секционной длинными блоками. При этой системе напорная грань выполняется в виде монолитного столба из обычного бетона с соблюдением всех технологических требований по предотвращению трещинообразования для столбчатой системы разрезки. Основная низовая часть плотины возводится с секционной разрезкой длинными блоками. В зависимости от применяемого типа бетона это могут быть или длинные блоки из обычного бетона («токтогульский» метод) или длинные блоки из укатанного бетона.
Рис. 15.9. Смешанные системы разрезки из комбинаций столбчатой разрезки и секционной длинными блоками
1 – столбчатая система; 2 – длинные блоки; 3 – арматурный пояс; 4 – высокие длинные блоки («канадская» система)
Смешанная система разрезки позволяет применять прогрессивную технологию с разрезкой длинными блоками в районах с суровыми климатическими условиями. При этом для выдерживания требуемого температурного режима возможна такая организация работ, при которой блоки в верховых столбах бетонируют в зимнее время, а длинные блоки в остальной части – в летнее время. Такая система предложена и осуществляется на строительстве Бурейской ГЭС.
Возможна и другая конструктивная схема комбинации этих систем (рис. 15.9,б), при которой в прискальной зоне сооружение бетонируется столбами, а в верхних частях в удалении от основания – длинными блоками из обычного бетона.
В первом ярусе длинных блоков над столбами устраивают армированный пояс для предотвращения трещинообразования в этом и вышестоящих ярусах от деформаций нижних столбчатых массивов. Это позволяет вести бетонные работы по столбчатой системе при неполностью законченном и организованном бетонном хозяйстве с переходом на длинные блоки в удалении от основания при хорошем развитии и организации всего бетонного хозяйства по полной проектной схеме. Такая система частично применялась на строительстве плотины Красноярской ГЭС.
Смешанной системой разрезки является также так называемая «канадская» система длинными и одновременно высокими блоками (рис. 15.9,в). В этой системе предусматривается возможность увеличения не только длины блоков до размеров секций, но и высоты блоков до предельных размеров по условиям организации работ и крепления опалубки (из практики канадского плотиностроения – до 22 м.). Бетонирование ведут в опалубке специальной конструкции, которая крепится на жестких металлических фермах. Такая система применялась при строительстве ряда контрфорсных плотин в Канаде. Для этой системы необходимо особенно хорошая организация массовых бетонных работ с самого начала строительства. В практике отечественного строительства такая система не
277
нашла распространения из-за сложности и дороговизны устройства опалубки с большой несущей способностью и сложностью обеспечения необходимого температурного режима.
278

ГЛАВА 16. Омоноличивание временных швов бетонных плотин
16.1. Общие положения
Как следует из гл.14, в период твердения бетон в блоках разогревается, а затем остывает до эксплуатационной температуры. В процессе остывания происходят деформации отдельных блоков и столбов, швы между ними раскрываются и для обеспечения монолитности работы требуется исключить отрицательное влияние этих раскрытий швов. При различных системах разрезки на блоки бетонирования условия раскрытия швов разные, а следовательно, мероприятия также разные.
Особенно сильно раскрытие швов сказывается при столбчатой разрезке. В связи с этим после остывания бетона до температур, ниже которых в будущем бетон в сооружении остывать не будет, производят так называемое омоноличивание швов, т.е. заполнение швов ("щелей") каким-то материалом. Для плотин с тонкими межстолбчатыми швами омоноличивание осуществляют путем цементации, а для плотин с объемными швами – путем бетонирования,
При секционной системе разрезки межблочные швы в пределах секции отсутствуют и раскрываются только межсекционные швы. В гравитационных типах плотин отдельные секции работают самостоятельно, поэтому омоноличивание межсекционных швов не требуется.
Для арочных плотин необходима совместная работа секций как в консольном, так и в арочном направлении. Поэтому для этих плотин требуется омоноличивание, также и межсекционных швов.
Омоноличивание может потребоваться и при смешанной системе разрезки, например, при комбинации столбчатой и секционной.
В связи с трудностью обеспечения в швах хорошего сцепления цементного раствора с бетоном столбов необходимо создавать условия, при которых материал в швах работал бы только на сжатие. Для этого в плоскости шва создают штрабы с ориентацией плоскостей по траектории главных напряжений. В результате по этим площадкам отсутствуют скалывающие напряжения и имеются только сжимающие (рис.16.1).
Рис. 16.1. Схема траекторий главных напряжений в плотине и ориентировка плоскостей штрабления в швах
I – траектории главных напряжений; 2 – узел I и II – ориентировка плоскостей штрабления в различных частях плотин
279

16.2. Омоноличивание швов с помощью цементации
Омоноличивание тонких межстолбчатых (для гравитационных плотин) и межсекционных (для арочных) швов осуществляют путем цементации этих швов. Как следует из предыдущего, бетон в сооружении в процессе эксплуатации принимает температуру, близкую к среднегодовой. Поэтому цементацию швов во избежание будущего дополнительного раскрытия в принципе необходимо проводить именно при температурах, близких к среднегодовой или ниже, когда дальнейшие температурные деформации в столбах уже не будут иметь места.
Омоноличивание выполняют до принятия напора омоноличиваемой части сооружения. Обычно в качестве расчетной температуры омоноличивания сооружения принимают среднемноголетнюю температуру бетонной кладки в районе расположения швов.
Качество цементации в значительной степени зависит от величины раскрытия шва. Максимальное раскрытие швов от равномерных температурных деформаций (без учета перекосов столбов от неравномерного распределения температуры) можно определить,
используя общую формулу температурных деформаций: |
l = αl |
T . |
||||||||||||
Подставляя значения l и |
T для нашего случая, получаем: |
|
|
|||||||||||
δ = |
L1 + |
L2 |
= α |
L1 |
(T1нач − T1кон ) + α |
L2 |
(T2нач − T2кон ) |
|
|
|
|
|||
|
|
|
|
|
(16.1) |
|||||||||
где: |
1 и |
|
|
2 |
|
2 |
|
, |
и |
|
|
|||
L |
2 |
– длина блоков в столбах 1 и 2; |
T1нач |
T2 |
нач |
– начальные средние |
||||||||
|
L |
|
|
|
|
|
|
|
|
|
температуры в соседних столбах, соответствующие моменту начала раскрытия шва; T1кон
и T2кон – конечные средние температуры в соседних столбах, соответствующие моменту омоноличивания плотины (рис. 16.2).
Рис.16.2. К определению величины раскрытия межстолбчатого шва: а) расчетная схема столбов, б) температурный режим в столбах
1, 2 – номера столбов плотины; 3 – цементируемый шов; 4 – высота яруса цементации; 5 – раскрытие шва при равномерном остывании столбов; 6 – дополнительное раскрытие шва от перекоса столба из-за неравномерности температуры по толщине столба; 7,8 –
T1 = ϕ(τ ) , |
T2 = ϕ(τ ) – кривые изменения средних температур в омоноличиваемых |
частях (картах); 9,10 – T1нач , T2нач – средние температуры в столбах 1 и 2 в период начала раскрытия швов, τ нач , τ омон – время начала раскрытия швов и время омоноличивания; 11,
12 – T1омон , T2омон – средние |
температуры в столбах 1 и 2 в период омоноличивания |
280
За момент начала раскрытия шва следует принимать момент достижения максимальной температуры экзотермии во втором столбе, укладываемом с отставанием по времени от первого.
Фактически по данным натурных наблюдений на ряде плотин деформации несколько меньше, и поэтому необходимо вводить корректирующий коэффициент, равный 0,25–0,5. В то же время дополнительно необходимо учитывать перекос столбов от неравномерности изменения температуры в столбе (блоке) как в горизонтальном сечении, так и в вертикальном (рис. 16.2). Дополнительное раскрытие швов может достигать существенной величины.
Желательно, чтобы средняя температура в омоноличиваемых столбах была как можно ближе к среднегодовой эксплуатационной, т.е. для массивных сооружений близкой к среднегодовой температуре воздуха. Однако из-за сложности охлаждения до такой температуры часто температуру назначают несколько выше, если выполняется условие, при котором температурные напряжения от последующего дополнительного остывания бетона после цементации не превышают напряжений по плоскости шва от гидростатического давления и было исключено дополнительное раскрытие зацементированных швов. Исходя из этого температура омониличивания швов остается в пределах 5–10°С. Например, температура ононоличивания на плотинах Братской и Красноярской ГЭС 5–8°С, Ланджанурской – 13°С, Ингурской – 14°С, Саяно-Шушенской – 2–7°С.
Поскольку омоноличивание таких швов осуществляют нагнетанием в шов цементационного раствора, то качественная цементация зависит и от величины раскрытия и от проникающей способности растворов. Как показывают экспериментальные исследования, полное заполнение шва обычным цементным раствором без добавок возможно при раскрытиях швов более 0,5 мм. При меньших раскрытиях для полного заполнения шва необходимо применять специальные растворы с пластифицирующими добавками или даже суперпластификаторами.
Среднее раскрытие швов на строительстве Красноярской ГЭС составило 1–1,5 мм.; на Саяно-шушенской 1,5–3,0 мм.
Раскрытие швов зависит от температурного режима блоков, а, следовательно, от сезона укладки. Поскольку разогрев бетонных блоков, укладываемых в летний период, больше, чем блоков, укладываемых в зимний период, то и соответственно раскрытие летних швов больше, чем зимних, и их легче цементировать.
Нагнетание цементного раствора в шов осуществляется через специальную систему труб с выпусками, закладываемыми в бетон при бетонировании плотины. Выпуски должны располагаться равномерно, чтобы обеспечить подачу раствора во все части шва. Для обеспечения равномерного заполнения шва и возможности создания давления при нагнетании раствора омоноличиваемые швы делят на отдельные участки на так называемые карты цементации. Карты цементации, находящиеся на одном уровне по всей длине плотины, образуют ярус цементации (рис.16.З).
281

Рис. 16.3. Схема разбивки межстолбчатых швов на ярусы и карты цементации
I – секции плотины; 2 – межстолбчатые швы; 3 – ярус цементации; 4 – карта цементации; 5 – уплотнение по контуру карты
По контуру каждой карты устанавливают шпонки – уплотнения. Шпонки выполняют из различных материалов: металлических листов, синтетических материалов, резины, дерева.
Длина карты цементации обычно равна ширине секции. Высоту карты выбирают из условия отсутствия растягивающих напряжений в столбах от давления раствора при нагнетании более 0,1 МПа. По опыту высота ярусе колеблется в пределах 8–20 м., площадь карты 80–600 м² (табл. 16.1).
Таблица 16.1. Размеры карт цементации на построенных плотинах |
|
||||
Наименование |
Высота |
Тип плотины |
Высота яруса |
Площадь карты |
|
гидроузла |
плотины, м |
цементации, м |
цементации,м² |
||
|
|||||
Братская ГЭС |
127 |
Гравитационная |
9 |
130–200 |
|
Красноярская ГЭС |
121 |
То же |
9–12 |
100–180 |
|
Усть-Илимская ГЭС |
100 |
То же |
15 |
165 |
|
Ланджанурская ГЭС |
67 |
Арочная |
12 |
80 |
|
Чиркейская ГЭС |
230 |
То же |
13 |
450 |
|
Ингурская ГЭС |
271,5 |
То же |
15 |
200–300 |
|
Шаста (США) |
181 |
Гравитационная |
15 |
225 |
|
Глен-Каньон |
216 |
То же |
15 |
До 600 |
|
Боулдер |
226 |
То же |
15 |
225 |
Все карты оборудуются трубной цементационной системой с выпусками для подачи цементного раствора. Система включает подводящий и отводящий коллекторы, систему разводящих труб – питателей, цементационные выпуски и воздухоотводящую трубу (рис. 16.4). Число выпусков определяется из расчета 3–6 кв. м на один выпуск. Применяют различные конструкции выпусков (рис. 16.5, а, б, в). Наибольшее применение при цементации швов получили точечные тарельчатые выпуски однократного действия.
282

Рис.16.4. Схема трубной цементационной системы
I – подводящий коллектор; 2 – питатели; 3 – выпуски; 4 – воздухоотводящая штраба; 5 – шпонки; 6 – отводящий коллектор; 7 – цементируемые швы
В случае если первичная цементация проходила при более высоких температурах по сравнению с требуемыми, предусматривают вторичную цементацию. Для этого применяют специальные выпуски с автономной системой труб, позволяющие производить промывку этой системы после первичной цементации (рис. 16.5, в, г).
Рис. 16.5. Схемы цементационных выпусков (клапанов): а, б – выпуски для первичной цементации; в, г – выпуски для вторичной цементации (а – тарельчатый; б – линейный; в – типа «капитен»; г – с резиновым клапаном (Гидроспецстрой))
283
I – крышка; 2 – обмазка цементным раствором; 3 – тройник; 4- питательная труба; 5 – хомут; 6 – резиновый клапан; 7 – шпилька; 8 – фланец корпуса; 9 – треугольный короб; 10
– цементируемый шов
Возможно и совмещение первичной и вторичной систем цементации, но это не всегда возможно, так как первичная цементация производится при значительных раскрытиях швов с применением густых растворов, которые могут засорить трубы и клапаны.
Технология цементации. Перед проведением инъекции производят промывку системы, водонасыщение бетона со стороны шва и гидравлическое опробование. Промывку трубной цементационной системы осуществляют через отводящий коллектор сверху вниз. Воздухоотводящую трубку промывают нагнетанием воды через подводящий коллектор. Промывку ведут до полного осветления вытекающей из трубы воды. При гидравлическом опробовании определяют общее водопоглощение шва и утечки при разных режимах движения, расход воды из воздухоотводящей штрабы, который характеризует проходимость шва.
Показатель хорошей проходимости шва – расход через воздухоотводящую штрабу не менее 30 л/мин. Опробование начинают с нагнетания воды при давлении 0,5 – 0,7 от допустимого, увеличивая далее ступенями по 0,1 – 0,2 МПа. Продолжительность опробования не менее 30 мин. Нагнетание раствора начинают не позднее 12 ч после промывки.
Раствор приготовляют на стационарных и передвижных установках. Для повышения проникающей способности в раствор добавляют пластификаторы. Цементацию обычно начинают с жидких растворов при В/Ц = 5:1. Циркуляцию раствора продолжают до выравнивания плотности нагнетаемого раствора и раствора, выходящего из воздухоотвода, после чего переходят на следующую ступень густоты раствора, и так постепенно сгущают его до конечной консистенции, которая обычно составляет 1:0,6. При омоноличивании плотины Братской ГЭС применялись следующие консистенции: В/Ц = 5:1, 3:1, 2:1, 1:1, 0,8:1, 0,6:1. На строительстве Красноярской ГЭС – 5:1, 1:1, 0,8:1, 0,6:1. Нагнетают раствор до достижения отказа или конечной консистенции. За отказ принимают момент, когда расход раствора не превышает 1 л/мин. В этот период обычно прекращается выход раствора через воздухоотводящую трубу. Далее производят еще сгущение раствора и опробование его в течение 10-15 мин.
Очередность омоноличивания швов по профилю плотины определяют по принципу от низового столба – к верховому и снизу вверх. Инъекция может осуществляться как раздельно по каждой карте, так и по групповой схеме. Более качественная цементация имеет место при раздельной схеме. Недостатки групповой – в наличии разных раскрытий швов, что требует разной технологии (давлений) и составов растворов.
Цементационное оборудование обычно размещают в дренажных и инспекционных галереях плотин или в специальных галереях. Растворные узлы располагают в галереях через 150 – 200 м по длине плотины, а при облегченных плотинах – в полостях.
В процессе цементации необходимо строго соблюдать технологический режим, следить за допустимыми давлениями. Для этого швы снабжают соответствующей контрольно-измерительной аппаратурой (КИА) в виде щелемеров, тензометров и др.
Для улучшения условий проходимости шва и соответственно качества цементации предусматривают предварительное дополнительное его раскрытие до допустимых размеров путем повышения давления при цементации.
Работы по омоноличиванию очень трудоемки и продолжительны по времени. Например, трудозатраты на плотине Красноярской ГЭС составили 0,4 чел/дня на 1 м² при общей площади 280000 м², что требовало около трех лет при численности бригады 100 человек.
Контроль качества омоноличивания. Основным показателем качества омоноличивания является соответствие напряженного состояния тела плотины расчетным проектным предпосылкам. Однако прямая проверка этого критерия возможна только
284

после наполнения водохранилища. Поэтому для оценки качества применяют косвенные методы, заключающиеся в контроле выдерживания всех технологических требований на всех этапах цементации, особенно температурного режима в омоноличиваемых столбах и блоках и проходимости системы при конкретных раскрытиях шва.
В период цементации особенно важен контроль за расходом и плотностью раствора, подаваемого в шов, и раствора, выходящего из воздухоотводной трубы. По замеренным значениям плотности определяют водоцементное отношение
В / Ц = |
1− ρ р / ρ |
ц |
|
|
||
ρ р |
−1 |
, |
(16.2) |
|||
|
||||||
где ρ р и ρц |
|
|||||
– |
|
плотности раствора |
и цемента. Результаты цементации обычно |
характеризуют общей массой израсходованного цемента на 1 м² площади шва. По опыту этот расход составляет в среднем 5–10 кг/м² (Братская плотина – 7,7–7,8 кг/м², ГрандДиксан 5,7–10,8 кг/м²).
Для конечного контроля качества проходят контрольные скважины, подсекающие зацементированные швы в различных зонах с отбором и испытанием кернов. В результате определяют сплошность цементации, прочность контакта и водопроницаемость.
16.3. Омоноличивание с помощью объемных замыкающих блоков
Условия, обусловливающие столбчатую разрезку с объемными замыкающими блоками, изложены выше. Суть заключается в том, что в особо суровых климатических условиях, когда среднегодовая температура значительно ниже нуля (минус 3–5°С и ниже), возникают сложности в проведении цементации промороженного бетона, поэтому между столбами в секции плотины оставляют объемные швы шириной 1,2–1,5 м. (рис. 16.6).
Рис.16.6. Схема омоноличивания плотины с помощью объемных замыкающих блоков 1 – столбчатые массивы; 2 – объемные межстолбчатые швы; 3 – ярусы бетонирования; 4 –
железобетонная опалубка швов; T1 и T2 << Tэкспл – температура в омоноличиваемых столбах
Омоноличивание таких швов осуществляют их бетонированием при полностью промороженном бетоне в соседних столбах.
Технология омоноличивания включает следующие элементы:
-промораживание бетона в столбах до температуры ниже среднегодовой;
-закрытие полости шва и обогрев бетонных поверхностей до положительных температур на глубину (20–30 см.), обеспечивающую гарантированный набор прочности бетона в шве при его твердении;
-подготовка блоков к бетонированию (очистка поверхности, установка КИА и др);
-бетонирование блоков соответствующим составом бетона.
285

Если применяют электрообогрев в швах, размораживания бетона в столбах по глубине не требуется, необходимо только обеспечить начальный поверхностный прогрев с дальнейшим электрообогревом стенок в период твердения. Такой метод омоноличивания применялся на строительстве плотин Мамаканской и Зейской ГЭС. Применение этого метода обеспечивает гарантированное качество омоноличивания.
Большое преимущество этого метода – возможность целенаправленно влиять на улучшение напряженного состояния плотины путем регулирования температурного режима с обжатием столбов плотины. Обжатие столбов можно обеспечить за счет их глубокого промораживания значительно ниже эксплуатационной температуры и последующего их отогрева после омоноличивания до эксплуатационных, а также за счет специального наклона верхового столба путем целенаправленного нагрева со стороны шва (рис.16.7).
Рис. 16.7. Влияние способов и условий омоноличивания на напряженное состояние плотины: а – схема плотины; б – напряжения в основании плотины при столбчатой разбивке с тонкими швами; в – напряжения в основании плотины при разрезке
286
с |
объемными |
|
межстолбчатыми |
швами |
и омоноличивании промороженных |
|||||
столбов |
|
|
|
|
|
|
|
|
|
|
1 |
– Межстолбчатый шов; 2 – ярус омоноличивания (бетонирования); 3 – |
|||||||||
целенаправленное |
дополнительное |
раскрытие |
объемного |
межстолбчатого |
шва; |
|||||
4 |
– эпюра напряжений (нормальных) в основании от собственного веса; 5 – эпюра |
|||||||||
напряжений |
от |
гидростатического |
давления; |
6 |
– |
суммарная |
эпюра |
Главное требование при этом, чтобы соблюдалась допустимая неравномерность напряжений в основании столбов и отсутствовали растягивающие напряжения в основании верховой грани. Использование указанного преимущества данного метода омоноличивания при возведении плотин Мамаканской и Зейской ГЭС позволило значительно улучшить напряженное состояние верхового столба плотины и в связи с этим сократить объемы бетонных работ к пуску первых агрегатов ГЭС.
287
ГЛАВА 17. Вспомогательные работы
17.1. Заготовка заполнителей
Общие положения по подбору состава бетона
Бетон представляет собой сложную смесь - конгломерат, состоящий из крупного заполнителя (гравия, щебня), мелкого заполнителя (песка), цемента, воды и различных добавок. Подбор состава бетона в конечном итоге заключается в установлении количества всех составляющих материалов, необходимых для получения 1 м³ бетонной смеси, отвечающей заданным требованиям. Наиболее дорогой из этих материалов - цемент. Поэтому при подборе состава бетона и при дальнейшей технологии его приготовления и укладки на всех этапах должны быть предусмотрены мероприятия, обеспечивающие минимально возможные расходы цемента. Снижение расхода цемента является одним из ряда комплекса мероприятий, обеспечивающих трещиностойкость и монолитность массивных бетонных гидротехнических сооружений. Первоначально расход цемента определяют в проекте на стадии подбора состава бетона и в дальнейшем уточняют на строительстве бетонной лабораторией применительно к конкретным производственным условиям.
Большое влияние на расход цемента, однородность бетонной смеси и ее свойства оказывает состав как крупных, так и мелких заполнителей по таким характеристикам, как: максимальная крупность, плотность и разнородность, форма частиц, отношение доли крупного и мелкого заполнителя.
Влияние всех этих факторов возможно рассматривать исходя из того условия, что объем цементного теста, а следовательно, расход цемента должен быть достаточен для обволакивания поверхности всех частиц заполнителей. Отсюда чем больше суммарная поверхность частиц заполнителей, тем больше расход цемента. Анализ этих факторов позволяет сделать следующие общие выводы по требованиям к заполнителям с точки зрения уменьшения расхода цемента и обеспечения однородности смеси:
∙Максимальный диаметр частиц - максимально возможный.
∙Заполнители должны быть разнозернистые, для чего необходимо предусматривать фракционирование.
∙Количество фракций - максимально возможное.
∙Количественное соотношение фракций различной крупности должно
обеспечивать максимальную плотность (минимальную пустотность) и должно быть постоянно для данной марки бетона.
∙Гравий предпочтительнее щебня (при отсутствии прочностных ограничений).
∙Лещаднооть вредна и должна быть ограничена.
∙Содержание пыли вредно и должно быть ограничено.
Требования к заполнителям
Практические требования к заполнителям регламентируются рядом нормативных документов.
Крупные заполнители. В качестве крупного заполнителя могут применяться щебень, гравий и щебень из гравия. Выбор крупных заполнителей производят по зерновому составу, плотности, прочности, содержанию зерен слабых пород, содержанию зерен пластинчатой (лещадной) и игловатой формы, водопоглощению, морозостойкости, содержанию пылевидных и глинистых частиц и петрографическому составу, в том числе содержанию вредных примесей включая органические примеси и потенциально реакционно-способные породы и минералы.
Проверку пригодности материалов производят по соответствующим ГОСТам при изыскании карьеров и подборе состава бетона.
В технологии приготовления крупных заполнителей должно быть предусмотрено разделение заполнителей на фракции для обеспечения постоянства зернового состава и, следовательно, однородности состава бетонной смеси. Модуль шкалы фракционирования,
288
как правило, принимают не более двух (иногда четырех), поэтому рекомендуется следующее количество фракций в зависимости от максимального диаметра Днаиб:
20 мм - 2 фракции (5-10; 10-20 мм), 40 мм - 3 фракции (5-10; 10-20; 20-40 мм),
70 (80 мм) - 4 фракции (5-10; 10-20; 20-40; 40-70; 40-80), 120 мм - 5 фракций (5-10; 10-20; 20-40; 40-80; 80-120),
150 мм - 6 фракций (5-10; 10-20; 20-40; 40-80; 80-120; 120-150).
Количественное соотношение фракций определяют экспериментально для конкретного карьера из условия получения наибольшей плотности.
В отечественной практике обычно применяется Дмах ≤ 120 мм из-за сильного утяжеления конструкции бетоносмесителей при большей крупности. Для массивных гидротехнических сооружений разрешается Дmах = 150 мм. Диаметр Дмах >150 мм разрешается только для добавления непосредственно в блок.
Мелкие заполнители. В качестве мелкого заполнителя для бетона применяют крупные, средние и мелкие пески, природные и дробленые, отвечающие требованиям ГОСТа. Принципиальные требования к песку те же, что и к крупному заполнителю. Особенно существенное значение для оценки качества песка имеет его гранулометрический состав. Числовой характеристикой гранулометрического состава является модуль крупности Мк- частное от деления суммы полных остатков на всех ситах стандартного набора (5; 2,5; 1,2; 0,6; 0,3; 0,15 мм) на общий вес материала, т.е.
|
|
i=5 |
|
|
|
|
åPi |
|
|
M k |
= |
i=0,15 |
|
|
|
|
P |
; |
(17.1) |
где Рi - вес полного остатка материала на сите |
i -го стандартного размера; Р - общий |
вес материала.
Модуль крупности колеблется в основном в пределах 1,0 – 3,5. Чем больше модуль крупности, тем выгоднее с точки зрения экономии цемента. Применение песка с модулем крупности менее 1,0 требует специального экономического обоснования.
Технология заготовки заполнителей
На крупных гидротехнических стройках заготовку заполнителей обычно осуществляют собственными силами путем разработки и переработки материалов из карьеров местных строительных материалов. В зависимости от конкретных инженерногеологических условий и гранулометрического состава месторождений могут быть следующие основные варианты заготовки заполнителей:
∙заготовка заполнителей из раздельных естественных песчаных карьеров и карьеров крупных заполнителей;
∙заготовка крупных и мелких заполнителей из общих карьеров песчаногравийной смеси;
∙заготовка тех или иных видов заполнителей из скальных пород путем их
дробления.
Возможны и другие варианты и комбинации.
Наиболее распространены карьеры песчано-гравийной смеси. В зависимости от места расположения карьеров и их положения по отношению к уровню грунтовых вод разработку этих карьеров можно вести обычными сухими способами или методом гидромеханизации. Последний применяют в основном при расположении карьеров в русле реки.
При разработке карьеров сухим способом добычу материалов из карьера можно осуществлять круглогодично, при разработке способом гидромеханизации - только в теплый период года с созданием складов этих материалов для обезвоживания и для возможности их дальнейшей переработки в зимний период.
289

Если в районе строительства отсутствуют карьеры песчано-гравийной смеси, но имеются горные породы, заполнители готовят из этих скальных пород путем их дробления. Необходимость дробления может возникнуть и при использовании песчаногравийных смесей при наличии в них излишнего количества отдельных фракций.
Имеющиеся в природе естественные карьеры редко удовлетворяют требованиям к заполнителям для бетона, изложенным выше. Поэтому возникает необходимость доведения качества этих материалов до требуемых. Процесс доведения естественных качеств и свойств смеси материалов из карьеров до требуемых называется обогащением, а комплекс зданий и оборудования для этого - обогатительными заводами или установками (хозяйствами). В зависимости от естественных свойств смеси материалов в карьере на обогатительных установках предусматривают соответствующий набор технологических операций для их переработки и доведения до требуемых: дробление, промывка, сортировка по фракциям, складирование по фракциям на складе, выдача материала со склада. В зависимости от набора технологических операций на заводах (установках) их называют сортировочными (при отсутствия дробления) и дробильно-сортировочными (при наличии дробления). В соответствии с назначением установок определяют их технологическую схему и оборудование.
Самая простая - сортировочная установка, включающая только сортировку (рис. 17.1). Сортировка может быть сухая и мокрая. Сухая - при отсутствии пыли и глинистых частиц, мокрая - при необходимости отмыва мелких частиц. При сильном загрязнении, особенно песка, применяют специальную промывочно-сортировочную установку. Основное оборудование таких установок - виброгрохоты с различным набором сит требуемых видов и размеров для фракционирования крупных заполнителей. При необходимости разделения песка на фракции вводят гидроклассификаторы.
Рис.17.1. Технологическая схема сортировочной установки, 1 - бункер; 2 - питатель; 3 - транспортеры; 4 – вибрационные грохоты; 5 - вода для промывки; 6 - бункера с рacсортированными фракциями; 7 - склады заполнителей
Технологическая схема дробильно-сортировочных установок более сложна (рис. 17.2). Основным оборудованием таких установок, кроме оборудования для сортировки, являются камнедробилки.
290

Рис.17.2. Технологическая схема дробильно-сортировочной установки для горной массы
I - бункер; 2 - питатель; 3 - транспортеры; 4 - вибрационные грохоты; 5 - бункер с рассортированными фракциями; 6- склады щебня; 7 - дробилки первой ступени; 8 - дробилки второй ступени
Технологическая схема дробильно-сортировочных установок обычно предусматривает следующую последовательность. Песчано-гравийную смесь или горную массу доставляют автотранспортом в приемный бункер. Из приемного бункера смесь с помощью питателя поступает на сортировочную решетку. Сортировочная решетка отделяет фракции, идущие на сортировку и дробление, а некоторые фракции в отвал или на другие цели. Обычно дроблению подвергают фракции до 300 мм, более крупные фракции отделяют для других целей. Технологическая схема дробления может быть одноступенчатой или многоступенчатой в зависимости от исходной и необходимой конечной крупности. После первичного дробления щебень поступает на виброгрохоты, сортирующие его на нужное количество фракций, и далее - в бункера и на склады - отдельно по фракциям. В случае необходимости промывки щебня над виброгрохотами устанавливают перфорированные трубы, через которые поступает вода для промывки. Дополнительно предусматривают промывку мелких фракций.
При переработке песчано-гравийной смеси на сортировочной установке излишнее количество отдельных фракций можно также направлять на дробление. Однако сортировку и хранение гравия и щебня, как правило, следует производить раздельно.
При добыче песчано-гравийной массы средствами гидромеханизации промывку обычно не делают, производя только сортировку.
Обогатительные установки для заполнителей могут быть стационарными и передвижными. Стационарные установки предусматривают обычно на крупных строительствах, а передвижные - на мелких (рис. 17.3).
291

Рис. 17.3. Технологическая схема гравийно-сортировочного обогатительного хозяйства с передвижным сортировочным агрегатом 1 - приемный бункер; 2- питатель лотковый: 3 - передвижные транспортеры; 4 - передвижной сортировочный агрегат; 5 - конусы заполнителей; 6 - погрузчик на пневмоколесном ходу.
17.2. Арматурные работы
Состав работ. Материалы
Арматурные работы - это комплекс мероприятий, включающих: прием и хранение арматурной стали; изготовление арматурных конструкций; транспортирование их к месту установки; монтаж арматурных конструкций на месте установки; сдачу арматурных конструкций под бетонирование.
Для большинства конструкций гидротехнических сооружений процент армирования
составляет обычно μ = 0,1-0,5%, достигая для отдельных тонкостенных конструкций μ = 1%. Средняя насыщенность арматурой составляет: 10-15 кг/м³ - для массивных плотин; 50-80 кг/м³ - для железобетонных конструкций зданий ГЭС, шлюзов стенок и т.д. Арматурные работы в комплексе бетонных работ составляют около 30% от суммарных трудовых затрат и примерно 20% от стоимости.
Взависимости от прочностных характеристик арматурная сталь подразделяется на классы, а в зависимости от содержания легирующих добавок, улучшающих качество арматурной стали - на марки.
Для армирования бетонных гидротехнических сооружений применяют в основном горячекатанную сталь гладкого и периодического профиля классов A-I, А-П, А-Ш, А-1У.
Типы арматурных конструкций и их изготовление
Вгидротехническом строительстве применяют следующие типы арматурных конструкций: армосетки и армопакеты; армофермы; армокаркасы (рис.17).
292

Рис.17.4. Арматурные конструкции: а - армосетки; б - армопакеты; в - армофермы; г – армокаркасы,
1 - рабочая арматура: 2 - распределительная арматура; 3 - раскосы; 4 - профильное железо
Армосетки и армопакеты - плоские арматурные конструкции с расположением рабочей арматуры в двух направлениях (армосетки) и в одном направлении (армопакеты).
Армофермы - объемные конструкции, состоящие из плоских сеток, соединенных между собой монтажной арматурой.
Армокаркасы - объемные конструкции значительных размеров, состоящие из нескольких сеток и усиленные профильным металлом (уголки, швеллеры) для повышения несущей способности в период монтажа и бетонирования. Армокаркасы обычно применяют в случаях, если эти конструкции используются дополнительно как несущие конструкции в период производства работ (раскрепление опалубки, плит-оболочек и т.д.).
Изготавливают арматурные конструкции на арматурных заводах или в мастерских из арматурной стали (Рис 17.5).
293

Рис. 17.5. Технологическая схема арматурной мастерской
В целом оборудование заводов или цехов включает станки для резки, станки для гибки, станки для сварки, сварочные трансформаторы, стенды и кондукторы для сборки арматурных конструкций.
Производительность арматурного завода (цеха) определяется из условия обеспечения расчетной месячной потребности в армоконструкциях. Для этого определяют потребности в арматурных конструкциях по диаметрам, типам конструкций, типам швов, на основании чего определяют расчетную производительность станков на отдельных операциях и линиях.
Чтобы определить объемы арматурных работ, в проектах составляют принципиальную схему армирования каждого сооружения с указанием типа конструкций и основных их размеров (рис. 17.6; 17.7).
294

Рис. 17.6. Схема армирования водосливной части плотины I - армосетки; 2 - армопакеты; 3 - армофермы; 4 – армокаркасы с навесными плитами-оболочками; 5 - плиты-оболочки; 6 - железобетонные балки перекрытия; 7 - поддерживающие конструкции
Рис. 17.7. Схема армирования водосливной части плотины на мягких основаниях 1 - армопакеты продольные; 2 - армопакеты поперечные; 3 - армосетки; 4 -
армофермы; 5 - поддерживающие конструкции (стойки, колонны, фермы)
На схемах указывается также тип поддерживающих конструкций для монтажа арматурных конструкций в блоках бетонирования.
Общая сменная производительность завода по выпуску арматуры (т/смену):
(17.2) где Jмес- расчетная месячная интенсивность ведения бетонных работ, м³ /мес; qа-
удельный расход арматуры на 1 м³ бетона, кг/м³ ; п - чиcло рабочих смен в месяц. Осредненный удельный расход арматуры qa для предварительных расчетов по
данным практики составит от 5 до 30 и более кг/м³ (табл. 17.1). Таблица 17.1
Осредненный удельный расход арматуры на 1 м бетона |
|
|
|
|
|
Номер |
Типы конструкций |
Удельный расход |
п/п |
|
арматуры qa , кг/м³ |
|
|
|
295

1 |
Бетонные плотины на скальном основании: |
|
|
а) гравитационные |
5-10 |
|
б) облегченные |
10-15 |
|
в) арочные |
15-20 |
2 |
Бетонные плотины на мягких основаниях |
20-25 |
3 |
Здания ГЭС, шлюзы |
25-30 |
Транспортировка и монтаж арматурных конструкций
Все изготовленные армоконструкций проверяются на заводе ОТК и снабжаются бирками-паспортами.
Транспорт арматурных конструкций осуществляют грузовыми автомашинами непосредственно в кузове автомашины или на специальных прицепных платформах в зависимости от размеров и веса конструкций. Основным требованием к перевозке армоконструкций является исключение деформаций и повреждений при перевозке, для чего применяют специальные прокладки и контейнеры. Погрузку и разгрузку армоконструкций осуществляют, как правило, имеющимися общими кранами.
Монтаж армоконструкций на месте установки в блоках бетонирования осуществляют или основными бетоноукладочными кранами или кранами, специально предусмотренными для установки и монтажа опалубки и арматуры. При больших объемах целесообразнее второй вариант. При монтаже сеток, пакетов применяют специальные поддерживающие конструкции (стойки, армофермы). Монтаж армоконструкций включает следующие операции: приемку, разгрузку, подачу в блок; установку в проектное положение; раскрепление монтажными растяжками; выверку и сварку стыков; контроль качества; сдачу комиссии одновременно со сдачей блока под бетонирование.
Контроль качества армоконструкций на монтаже осуществляют техинспекция и авторский надзор. Проверке подвергаются, сортамент стали, качество сварных стыков, соответствие конструкции проекту, правильность монтажа. Сортамент стали проверяется сравнением с паспортом, качество сварных стыков - путем выборочной вырезки и проверки на разрыв в лаборатории на разрывных машинах. На смонтированную конструкцию составляют соответствующий паспорт при сдаче блока под бетонирование (акт на скрытые работы).
17.3. Опалубочные работы
Назначение опалубки и требования к ней
Опалубка - это временная конструкция, которой ограждается бетонируемый блок и в которую укладывают бетонную смесь. Она обеспечивает размеры и форму блоков, которые в своей совокупности обеспечивают размеры и форму сооружения в целом. Поверхности блока, подлежащие ограждению опалубкой, называются опалубливаемыми поверхностями, а отношение площади опалубливаемой поверхности блока S (м²) к его
объему V (м³) - коэффициентом опалубливаемой поверхности |
Коп (м² /м³ ): |
|
Коп=S/V; |
|
(17.3) |
Этот коэффициент характеризует массивность конструкций. При К< |
I м²/м³ |
конструкции относят к массивным, при К > 1 м²/м³ – к тонкостенным. Для массивных бетонных плотин (Красноярская, Братская, Усть-Илимская) Коп= 0,15-0,30; для блоков здания ГЭС - Коп =0,4-0,6 м²/м³. В отдельных конструкциях (стенки, бетонные крепления) Коп > 1,0 и может достигать 5,0 м²/м³ (колонны, балки, перекрытия). По данным практики осредненный расход опалубки для гидротехнических сооружений составляет (в m2/m3): для массивных плотин- 0,26; для массивных частей здания ГЭС - 0,68; для шлюзов- 0,43; в целом для гидроузлов- 0,5 м²/м³.
296
Внутри огражденного опалубкой пространства бетонная смесь твердеет, превращаясь в бетон. После набора бетоном определенной прочности опалубка может быть снята. Такая опалубка называется съемной.
Некоторые виды опалубки не снимают, а оставляют в бетоне в качестве элемента конструкции. Такая опалубка называется несъемной
Операция по снятию съемной опалубки называется распалубкой. Сроки распалубки регламентируются соответствующими техническими условиями и правилами, исходя из условий сохранности и трещеностойкости бетонируемых конструкций. Так, распалубливание бетонных конструкций массивных гидротехнических сооружений допускается после набора бетоном прочности не менее 1,5 МПа и условии соблюдения требований теплового режима блока. Снятые опалубочные щиты очищают от налипшего бетона и грязи, ремонтируют, после чего повторно используют для опалубливания следующих блоков. Повторное использование опалубочных щитов называется оборачиваемостью опалубки. Для разных типов опалубки она колеблется в широких пределах: от 8-10 для деревянной опалубки до 50 для металлической.
Таким образом, в целом комплекс опалубочных работ включает:
∙изготовление отдельных опалубочных щитов на специальных подсобных
предприятиях - опалубочных цехах лесозаводов или деревообделочных мастерских;
∙их транспортировку к мосту установки;
∙установку и закрепление щитов в заданном положении;
∙снятие щитов (распалубку);
∙очистку и ремонт опалубочных щитов.
Всоответствии со своим назначением опалубка должна удовлетворять следующим требованиям:
∙быть жесткой, неизменяемой в пространстве под воздействием нагрузок при укладке бетонной смеси (в пределах допустимых отклонений по СНиПУ);
∙обеспечивать точность размеров конструкции сооружения (в зависимости от требований к конструкции сооружения);
∙обеспечивать плотность стыков между отдельными щитами и исключать утечку цементного раствора;
∙обеспечивать легкость сборки, раскрепления, распалубки и очистки, т.е.
технологичность и малую трудоемкость.
Опалубка - неотъемлемая составляющая комплекса бетонных работ на всех видах строительства, однако в каждом виде строительства имеются свои особенности и специальные требования к опалубке, а потому и применяемые типы и конструкций применяемой опалубки отличаются друг от друга.
Особенностью гидротехнического строительства являются большие общие объемы бетонных работ, большие размеры бетонируемых блоков, относительная простота форм блоков и их большая повторяемость, Отсюда - одно из основных требований к опалубке в гидротехническом строительстве: максимальная оборачиваемость применяемого типа опалубки, технологичность сборки, установки и распалубки. Это обусловило наибольшее распространение для бетонирования массивных сооружений таких типов опалубки, как сборно-разборная щитовая, сборно-разборная консольная.
В отдельных частях сооружений к опалубке применяют специальные требования, вытекающие из требований к опалубливаемой поверхности бетона. Так, к водосливным поверхностям плотин предъявляются требования по обеспечению повышенной прочности бетона на внешней поверхности и стойкости против кавитации. Это достигается применением специальных видов опалубки.
Виды и типы опалубки
297

Съемная опалубка конструктивно состоит из несущего каркаса, сплошного настила, непосредственно соприкасающегося с бетоном и называемого палубой, элементов крепления между собой каркаса и палубы и крепления щита на месте установки (рис. 17.8). В зависимости от материала изготовления щитов различаются следующие виды опалубки: деревянная; металлическая; деревометаллическая; бетонная или железобетонная.
Рис.17.8 Схемы щитовой опалубки: а- общая схема опалубочного щита; б- схема деревянного щита
1- несущий каркас; 2- палуба (обшивка); 3- анкерные болты для крепления; 4- ребра; 5- прогоны; 6-положение крайнего ребра при двухъярусной опалубке; 7- диагональные откосы (схватки)
Первые три вида опалубки относятся к съемным; бетонная и железобетонная опалубка, а иногда и специальная металлическая (металлическая облицовка различных труб, отверстий, штраб), относятся к несъемной и остаются в сооружениях в качестве элемента конструкции. По конструктивным признакам, условиям разборки и крепления опалубку подразделяют: на разборно-переставную (щитовую); подъемно-переставную (консольную); передвижную (катучую); скользящую; стационарную.
Разборно-переставная (щитовая) опалубка состоит из отдельных деревянных или деревометаллических щитов (рис.17.9), которые раскрепляют на месте установки с помощью тяжей. Тяжи крепят к анкерам или выпускам из ранее уложенного бетона или к другим жестким конструкциям (например, армокаркасам). В зависимости от возможности установки опалубки вышележащего по высоте блока со, снятием или без снятия опалубки нижележащего блока (яруса) различают одноярусную и двухъярусную (многоярусную) опалубку (рис.17.9).
298

Рис. 17.9. Основные схемы крепления опалубочных щитов: а - при одноярусной щитовой опалубке; б - при двухъярусной щитовой опалубке; в - при одноярусной консольной опалубке; г - при двухъярусной консольной опалубке
1 - несущий каркас; 2 - палуба; 3 - анкерные болты для крепления; 4 - тяжи для крепления; 5 - соединение анкеров и тяжей с помощью тальрепов или сваркой; 6 - анкерные болты или анкеры, закладываемые в бетон; 7 - опалубочный щит нижележащего блока; 8 -опалубочный щит бетонируемого блока; 9 - крепление верхнего щита к нижележащему; 10плавающий анкерный болт; 11 - регулировочное устройство (домкрат)
Подъемно-переставная (консольная) опалубка по конструкции самого щита мало отличается от щитовой. Принципиальное отличие заключается в способе крепления. Если
вщитовой опалубке для крепления применяют тяжи, стесняющие внутреннее пространство блока, то в консольной опалубке такие тяжи отсутствуют. Крепление опалубки осуществляют с помощью несущего каркаса, выполненного в виде консольных балок или ферм и скрепляемого с нижележащим блоком с помощью анкеров, заложенных
внижележащий блок. Так же как и щитовая опалубка, эта опалубка может быть одноярусной и двухъярусной (многоярусной). Наибольшее распространение в гидротехническом строительстве получила двухъярусная опалубка "чиркейского" или "саянского" типа (рис. 17.10.).
Рис. 17.10.Двухъярусная консольная опалубка "чиркейского" и "саянского"типа 1 - несущий каркас; 2 - подвижной щит-палуба; 3 – щит утеплитель; 4 - плавающий
анкерный болт; 5 – регулировочное устройство (домкрат)
Передвижная (катучая) опалубка конструктивно состоит из передвижной тележки, перемещающейся, как правило, по рельсам, несущей рамы и закрепляемых на ней щитов. На несущей раме предусматривают домкратные устройства, устанавливающие
299

опалубочные щиты требуемого очертания в нужное проектное положение. Эти же домкраты, поддерживающие щиты в период бетонирования, используются для отрыва щитов (распалубки) и перевода их в транспортное положение (рис 17.11).
Рис. 17.11. Передвижная катучая опалубка тоннелей 1 – передвижная рама; 2 – опалубка, 3 - домкраты
Скользящая опалубка представляет собой систему щитов, перемещающуюся с помощью домкратов по специальным направляющим конструкциям (рис.17.12). Такая опалубка эффективно применяется при бетонировании высоких конструкций постоянного сечения (труб, трубопровода ГЭС, стен и т.п.).
Рис. 17.12. Схемы скользящей опалубки для высоких конструкций: тонкостенных (а); толстостенных (б)
1 - передвижные опорные конструкции и рамы; 2 –опалубочные щиты; 3 - шагающий домкрат; 4 - опорные арматурные стержни
Стационарная опалубка - опалубка, собираемая на месте (по месту) из отдельных элементов - досок и брусьев. Применяется для опалубливания элементов сооружений, имеющих сложную форму (переходные криволинейные участки, колена отсасывающих труб, прискальные блоки и т.п.). Конструктивно состоит из тех же элементов, что и щитовая.
Кроме перечисленных в гидротехническом строительстве применяют съемную опалубку и других видов, в частности, специальную опалубку для бетонирования водосливных граней плотин (опалубку водосливных граней о.в.г.) (рис. 17.13). Конструктивно этот тип опалубки представляет собой большие щиты, перекрывающие
300

весь водосливной пролет, не имеющие никаких креплений и выпусков в пролете и закрепляемые вне водосливного пролета на участке разделительных быков.
Рис. 17.13. Схема специальной опалубки для водосливной грани плотины; а - положение блока; б - узел «А»
I - забетонированная часть плотины; 2 - бетонируемый блок; 3 - несущий каркас опалубки; 4 - палуба; 5- адсорбирующий сдой; 6 - направляюще конструкции; 7 - крепление; 8- соседние блоки водосливной грани; 9 - бычки водосливных пролетов
Для возможности упрочнения поверхностного слоя бетона на поверхность палубы опалубки накладывают влагопоглощающий (адсорбирующий) слой, отсасывающий в период твердения часть свободной воды из бетона и тем самым снижающий водоцементное отношение в поверхностном слое бетона, что ведет к повышению его прочности. Такая опалубка называется адсорбирующей. Опыт применения такой опалубки свидетельствует о больших качественных преимуществах бетона, уложенного в адсорбирующей опалубке. Такой бетон отличен от обычного уже по внешнему виду. Поверхность его ровная, гладкая, без песчаных жил и раковин, пор и пустот, являющихся следствием защемленных в наружном слое бетона воздушных пузырьков. Дополнительной обработки (торкрет, штукатурка, затирка) такие поверхности не требуют. Прочность бетона, уложенного в адсорбирующей опалубке, в среднем выше обычной на 30-60%, Значительно увеличивается плотность, а, следовательно, морозостойкость и водонепроницаемость. Материалом адсорбирующей облицовки опалубки могут служить различные легковесные деревоволокнистые плиты, листы картона, геотекстиля.
На криволинейных участках водосливных пролетов (на оголовках и носках) с той же целью применяют вакуум-опалубку (рис. 17.14.).
301

Рис. 17.14. Схема вакуум-опалубки оголовка и носка водосливной плотины: а - общая схема; б - принципиальная схема щита вакуум-опалубки
I - несущий каркас; 2 - щиты вакуум-опалубки; 3 - палуба; 4 - уплотнения; 5 - фильтрующий слой; 6 - штуцер вакуум-разводки; 7 - шланги или трубы; 8 - соединение с вакуум-установкой
Щиты бетонирования такой опалубки имеют внутреннее замкнутое пространство, соединенное с поверхностью бетона через фильтровальный слой, В этом замкнутом пространстве с помощью вакуум-насоса создается вакуум (разрежение). Разрежением через фильтровальный слой отсасывается часть свободной воды и воздуха из поверхностного слоя бетона, что ведет к его дополнительному уплотнению и упрочнению за счет снижения водоцементного отношения. В благоприятных условиях вакуумированием удается упрочнить слой бетона до 20-25 см и извлечь из него до 15-17% воды от того количества, которое было введено в бетонную смесь при затворении. Бетон, обработанный вакуумированием, имеет большие преимущества по сравнению с обычным. Повышенная плотность обеспечивает его высокую сопротивляемость истиранию и попеременному действию воды и мороза, что увеличивает его долговечность. Кроме того, повышенная прочность бетона в раннем возрасте позволяет осуществлять более быстрое распалубливание и увеличивать темпы бетонирования.
Типы несъемной опалубки
К несъемной относится такая опалубка, которая после бетонирования не снимается, а остается на месте установки в бетоне и становится элементом конструкции сооружения. Эта опалубка состоит из отдельных сборных бетонных, железобетонных или металлических элементов (плит, балок, коробов, облицовок, сеток и т.п.). В зависимости от конструктивного исполнения опалубки она может выполнять или роль только опалубки или дополнительно участвовать и в работе будущей конструкции. В первом случае конструкция опалубки и ее армирование рассчитываются только на условия работы и нагрузки при бетонировании. Во втором случае - дополнительно на условия работы в сооружении с расположением в ней основной рабочей арматуры.
Примером первого типа опалубки являются бетонные и железобетонные плиты и балки, при опалубливании ими межблочных и межстолбчатых швов, при столбчатой и секционной разрезке, при укладке укатанного бетона и т.д., а также металлические сетки в межблочных швах (рис. 17.15).
302
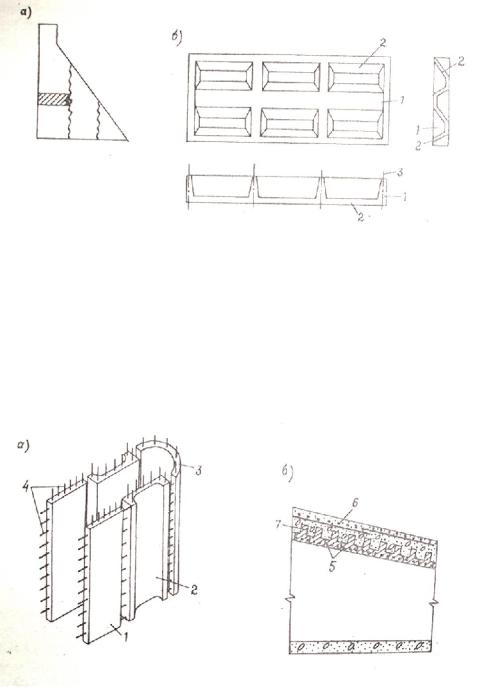
Рис. 17.15. Несъемная железобетонная опалубка межстолбчатых швов: а - общая схема расположения опалубки; б - схема железобетон ной плиты-опалубки
1 - ребра; 2 - стенки; 3 - выпуски для крепления
Примером опалубки второго типа являются плиты-оболочки, армо-плиты, обетонированные закладные части на лицевых поверхностях бетонных и железобетонных конструкций и различные металлические облицовки как снаружи, так и внутри конструкций (рис. 17.16, 17.17).
Рис. 17.16. Сборно-монолитные конструкции: а) армопанели для бетонирования бычка; б) сборно-монолитное перекрытие отсасывающей трубы
1 - плоские армопанели; 2 - предварительно омоноличенные пазовые конструкции; 3 - армопанель оголовка бычка; 4 - рабочая арматура; 5 - нижняя продольная арматура балок; 6 - верхняя поперечная и продольная арматура; 7- балки
303

Рис. 17.17. Схемы опалубливания бычков водосливной плотины плитами-оболочками и армоплитами: а - схема с применением плит-оболочек; б - схема с применением армоплит
1 - плита-оболочка; 2 - арматурная змейка; 3 - обрамление; 4 - армоплита; 5 - выпуски рабочей арматуры; 6 – рабочая арматура армоплиты; 7 - стыки рабочей арматуры; 8 - нащельники; 9 - железобетонные короба пазов затворов с омоноличенными закладными частями; 10 - закладные части
Железобетонная опалубка является, безусловно, дорогой по сравнению со съемной опалубкой. Поэтому ее применение оправдывается тогда, когда это дает значительные преимущества в темпах возведения сооружений, в сокращении трудозатрат и других ресурсов.
Расчет опалубки
Основными расчетными нагрузками на опалубку являются: горизонтальное статическое боковое давление бетонной смеси; горизонтальные динамические нагрузки от сотрясений при выгрузке бетонной смеси; вертикальные нагрузки от расположенного на ней оборудования, инженерных и транспортных коммуникаций (при их наличии).
Суммарная горизонтальная нагрузка может быть определена по эпюре максимальной интенсивности бокового давления в зависимости от высоты блока бетонирования (рис.17.18):
304

Рис 17.18. Эпюра давления бетонной смеси на опалубку. Hбл -выоота блока; R - радиус действия вибратора; Рд – динамическая нагрузка
(17.4) (17.5)
где γ - плотность бетонной смеси (приблизительно 2,5 т/м³ для гидротехнического
бетона); Н. - высота слоя уложенного бетона, мм; |
R-радиус действия вибраторов (для |
поверхностных 1,0 м, для глубинных около 0,76 м); |
Рдин - динамическая нагрузка от |
бетонной смеси при разгрузке бадьи (равная примерно 0.4 т/м² для бадей емкостью до 0,8 м³, 0,6 т/м² для бадей > 0,8 м³, 0,2 т/м² - при спуске по хоботам, лоткам).
Вертикальная нагрузка определяется по конкретным условиям технологии производства работ, но чаще всего ее можно не учитывать.
Главными расчетными элементами опалубки являются обшивка (палуба), ребра, прогоны, тяжи и анкеры крепления. Обшивку, ребра и прогоны рассчитывают как неразрезную конструкцию на прочность и проверяют на допустимый максимальный прогиб. Для наружных поверхностей бетона этот прогиб не должен быть более 1/400 пролета, а для внутренних - не более 1/250.
Определение мощности предприятий по изготовлению опалубки
Для определения типов и размеров опалубки для каждого сооружения составляют схемы опалубливания, на которых указывают принципиальные типы опалубки и их размеры. На основании этой схемы определяют объемы работ по изготовлению и монтажу опалубки различных типов (рис. 17.19).
Рис. 17.19. Общая схема распределения типов опалубки: а - высокая гравитационная плотина; б - низконапорная плотина на мягких грунтах
305
- верховая грань-консольная двухъярусная опалубка; 2- межстолбчатые швы - щитовая опалубка со штрабами (консольная); 3 - межсекционные швыщитовая опалубка (консольная); 4 - прямолинейная часть водосливной плотины-специальная адсорбирующая опалубка водооливной грани; 5 - криволинейные участки водосливной грани- вакуум-опалубка; 6 -бычки плотины-плиты оболочки; 7 - межблочные швы - щитовая опалубка; 8 - верховая грань - щитовая опалубка, армоплиты
Для приготовления различных типов опалубки в составе производственной базы предусматривают соответствующие предприятия.
Деревянную опалубку изготавливают в опалубочных мастерских, железобетонную - на заводах или полигонах сборного железобетона. Производительность этих предприятий зависит от интенсивности бетонных работ с учетом оборачиваемости данного типа опалубки. Мощность предприятий обычно рассчитывается на среднемесячную потребность опалубки данного типа в пиковый год строительства. Общую среднемесячную потребность в опалубке различного вида можно определить по формуле
(17.6) а производительность отдельных цехов
(17.7) где J - среднемесячная интенсивность бетонных работ в пиковый год строительства,
м³/мес; qоп - средний удельный расход опалубки в м² на I м³ бетона (по расчету или аналогам: 0,3 - для гидроузлов о массивными бетонными сооружениями; 0,5 -.для гидроузлов иного типа);
Ki - доля данного типа опалубки в общей опалубливаемой поверхности; Кнер - коэффициент неравномерности опалубочной мастерской в течение года (по опыту Кнер=1,2); 0i - оборачиваемость опалубки i -го типа.
По аналогичной формуле определяется и потребность в железобетонной опалубке.
306

ГЛАВА 18. Приготовление бетонной смеси
18.1 Требования к бетонной смеси
Приготовление бетонной смеси осуществляется на бетонных заводах. При этом должны быть выполнены определенные условия, обеспечивающие получение гидротехнического бетона требуемых свойств.
Основными показателями требуемых свойств бетона для разных зон сооружений являются марки бетона по прочности, морозостойкости, водонепроницаемости, а также специальные дополнительные качества для отдельных зон, такие, как трещиностойкость, кавитационная стойкость и др. (см. главы I3 и 14).
Для каждой зоны, отличной по условиям работы, назначают марку и подбирают соответствующий состав компонентов. При подборе состава бетона должны быть учтены также производственные условия приготовления смеси, ее транспортирования, условия укладки и набора прочности. Все эти условия и соответствующие составы бетона должны быть откорректированы бетонной лабораторией строительства непосредственно перед бетонированием сооружений при конкретных производственных условиях на строительстве в данное время. Так, максимальный размер крупного заполнителя должен быть увязан с применяемыми типом и емкостью бетоносмесителя, с размерами бетонируемых элементов сооружения и со степенью их армирования (табл. 18,1).
Для получения однородной смеси при укладке в блок состав приготовляемой бетонной смеси должен обеспечивать также удобство транспортирования, распределения и уплотнения бетонной массы, т.е. обеспечивать так называемую удобоукладываемость. Последняя характеризуется подвижностью и жесткостью бетонной смеси, значения которых для различных конструкций даны в табл. 18.2.
Таблица 18.1. Предельная крупность заполнителей
Условия приготовления, |
|
Максимальный диаметр зерен заполнителя, мм |
|
|||
транспортирования |
и |
|
|
|
|
|
укладки |
|
|
|
|
|
|
Бетоносмесители емкостью |
|
|
|
|
||
(по загрузке), л |
|
|
|
|
|
|
до 500 |
|
|
|
80 |
|
|
до 1200 |
|
|
|
120 |
|
|
до 2400 |
|
|
|
150 |
|
|
Трубопроводный транспорт |
|
1/3 диаметра бетоновода 0,5 расстояния в свету |
||||
|
|
|
между стержнями арматуры |
|||
Тонкостенные конструкции |
|
1/3 минимального размера элемента конструкции |
||||
Армированные конструкции |
|
3/4 расстояния между стержнями арматуры |
||||
|
|
|
|
|
|
|
|
|
|
|
|
Таблица 18.2.: |
|
Ориентировочные величины подвижности (осадки конуса) бетонной смеси |
|
|||||
|
|
|
|
|||
Характеристики |
бетонируемых |
Осадка стандартного конуса, см |
|
|||
конструкций |
|
|
|
|
|
|
Массивные |
бетонные конструкции |
1-3 |
|
|||
без рабочей арматуры |
|
|
|
|||
Массивные |
|
армированные |
3-6 |
|
||
конструкции |
с |
содержанием |
|
|
||
арматуры до 0,5% |
|
|
|
|
|
|
Железобетонные |
конструкции |
с |
6-8 |
|
||
содержанием арматуры до 1% |
|
|
|
307

Железобетонные конструкции с 8-12 содержанием арматуры более 1%
В соответствии с вышеизложенными положениями перед приготовлением бетонной смеси прежде всего необходимо проверить готовность бетонного завода к выпуску бетона требуемого состава как по качеству, так и по количеству. Для обеспечения качественного состава бетонной смеси, бетонный завод должен иметь в наличии все компоненты смеси требуемых свойств в соответствии с составом бетона (фракционированные заполнители, цемент определенных марок, добавки и т.д.). Для обеспечения количественного состава бетонной смеси должна быть выдержана определенная точность дозирования всех составляющих.
18.2. Технологические схемы бетонных заводов и их оборудование
Приготовление бетонной смеси - комплексный технологический процесс, включающий ряд подготовительных операций и операций по непосредственному приготовлению смеси. В состав первых операций входят, кроме заготовки составляющих бетонной смеси, их хранение и подача в бункера бетонного завода.
Операции по непосредственному приготовлению смеси включают дозирование составляющих, их загрузку в бетоносмеситель, перемешивание в бетоносмесителе и выдачу готовой смеси. Оборудование для осуществления этих операций обычно монтируется в одном сооружении, называемом бетонным заводом или бетоносмесительной установкой.
По принципу действия различают бетонные заводы двух типов: периодического (цикличного) действия и непрерывного действия.
Заводы первого типа приготовляют и выдают бетонную смесь отдельными порциями, второго - приготовляют и выдают бетонную смесь непрерывно. Заводы включают оборудование и устройства для выполнения упомянутых выше отдельных операций.
Заводы циклического действия компонуется по двум схемам: одноступенчатой (вертикальная или башенная компоновка) – рис. 18.1,а и двухступенчатого (партерная компоновка) - рис. 18.1, б.
308

Рис. 18.1. Одноступенчатая (а) и двухступенчатая (б) схемы компоновки бетонного завода
I - транспортер со склада заполнителей; 2 - транспортер для подачи заполнителей на завод; 3 - поворотная воронка; 4 - цементопровод; 5 - наддозаторные (расходные) бункера крупного и мелкого заполнителей; 6 - дозатор воды; 7 - дозатор заполнителей; 8 - доза тор цемента; 9 - воронка сухой смеси; 10 - бетоносмеситель; 11 - буккер бетонной смеси; 12 - транспортное средство; 13 - склад заполнителей; 14 - склад цемента.
Одноступенчатая (башенная) схема характеризуется тем, что все составляющие бетонной смеси сразу, в одну ступень, поднимаются на командную высоту (башню) в бункера и затем под действием собственного веса (вертикально) последовательно поступают в дозаторы, смесители и другое оборудование. Отсюда и название схемы. Применяют ее обычно на стационарных бетонных заводах.
При двухступенчатой схеме весь процесс приготовления смеси разбивается на две ступени. В первой ступени обычно предусматривают дозирование заполнителей с получением сухой смеси. Далее эта смесь транспортируется (поднимается) на вторую ступень, где расположены бетоносмесители и осуществляется перемешивание и выдача бетонной смеси. Эту схему применяют в основном на бетоносмесительных установках и небольших заводах (цехах).
По принципу перемешивания бетоносмесители делятся на два типа:
∙бетоносмесители гравитационные или свободного перемешивания;
∙бетоносмесители принудительного перемешивания.
Принцип действие гравитационных бетоносмесителей - перемешивание за счет падения составляющих смеси и их смешения при вращении барабана (рис. I8.3, а). Вращающийся барабан имеет на своих стенках лопасти, с помощью которых составляющие захватываются и поднимаются в верхнее полонение, а затем падают под действием силы тяжести (отсюда и название - гравитационные). Скорость вращения барабана должна быть такой, чтобы составляющие под действием центробежной силы прижимались к стенкам барабана и поднимались на возможно большую высоту, и только затем падали. При малой скорости вращения процесс перемешивания замедлится, а при слишком большой - вообще прекратится, так как все составляющие прижмутся к стенкам барабана под действием центробежной силы. Поэтому скорость вращения долина быть оптимальной, соответствующей получению наибольшего эффекта перемешивания.
Принцип действия бетоносмесителей принудительного действия - перемешивание в неподвижной чаше за счет вращения ротора с лопастями (рис. 18.3,6).
Рис. 18.3. Схемы бетоносмесителей циклического действия: гравитационного (а) и принудительного (б) перемешивания
1 - станина; 2 - привод для выгрузки бетонной смеси; 3 - шестерня вращения барабана; 4 - барабан; 5 - загрузочное и разгрузочное отверстия; 6 - лопасти; 7 - привод вращения барабана; 8 - ротор; 9 - внутренняя и внешняя стенки корпуса; 10 - смесительная чаша; 11
-загрузочное отверстие; 12 - привод вала ротора; 13 - редуктор; 14 - электродвигатель; 15
-смешивающие лопасти; 16 - затвор; 17 -разгрузочное отверстие.
309

Те и другие типы цикличных бетоносмесителей применяются для приготовления смесей различных составов и консистенций. Однако гравитационные бетоносмесители наиболее эффективны для приготовления пластичных смесей, а принудительного действия - для жестких бетонных смесей. В то же время практика показывает, что гравитационные бетоносмесители более надежны по износоустойчивости рабочих органов, наиболее пригодны для применения крупных заполнителей размером до 150 мм, имеют меньшую массу и большую производительность по сравнению с бетоносмесителями принудительного действия. Поэтому на крупных гидротехнических стройках наибольшее применение нашли именно гравитационные бетоносмесители и заводы на их основе. Бетоносмесители принудительного перемешивания способны обеспечить большую однородность смеси и поэтому наиболее широко распространены на заводах сборного железобетона.
Все цикличные бетоносмесители различаются по емкости барабана. Причем последняя выражается как по загрузке qз , так и по выгрузке qв. Первая означает сумму объемов составляющих бетонной смеси до их перемешивания, вторая – объем готовой смеси после перемешивания всех составляющих.
(18.1)
где - коэффициент выхода бетонной смеси, равный 0,67-0.7. Выпускаемые цикличные бетоносмесители имеют обычно емкость по загрузке
500, 700, 1200, 1500, 3000 л, из которых и компонуются секции бетонных заводов.
Для дозировки составляющих бетонной смеси при использовании цикличных бетоносмесителей применяют весовые дозаторы.
Промышленность выпускает полные комплекты оборудования для отдельных секций бетонных заводов и в зависимости от общей мощности бетонного завода, они компонуются из разных количеств секций. Выборочная номенклатура отечественных бетоносмесителей дана в табл. 18.3.
Таблица 18.3. Выборочная номенклатура отечественных бетоносмесителей |
|
||||
Марка |
Объем по |
Объем |
Максим. |
Ориентиров. |
Технич. |
смесителя |
загрузке |
готового |
Крупность |
производительность |
|
|
|
замеса |
заполнителя |
|
|
|
л |
л |
мм |
м³/час |
|
|
|
Гравитационные |
|
|
|
СБ-174* |
100 |
65 |
40 |
|
|
СБ-161* |
500 |
330 |
70 |
8,25 |
|
СБ-91Б |
750 |
500 |
70 |
12,5 |
|
СБ-10В, С-302 |
1200 |
800 |
120 |
32 |
|
СБ-150, С-230 |
2400 |
1600 |
120 |
32 |
|
СБ-162 |
4500 |
3000 |
150 |
60 |
|
|
|
Принудительные |
|
|
|
СБ-80 |
250 |
165 |
70 |
|
|
СБ-35, С-773 |
500 |
330 |
70 |
13,2 |
|
СБ-146А |
750 |
500 |
70 |
20 |
|
СБ-62,951 |
1200 |
800 |
70 |
32 |
|
СБ-163А |
1500 |
1000 |
70 |
40 |
|
Бетоносмесители непрерывного действия по принципу перемешивания схожи с циклическими бетоносмесителями принудительного действия и состоят из горизонтального барабана и вращающегося в нем ротора с лопастями, обеспечивающими
310
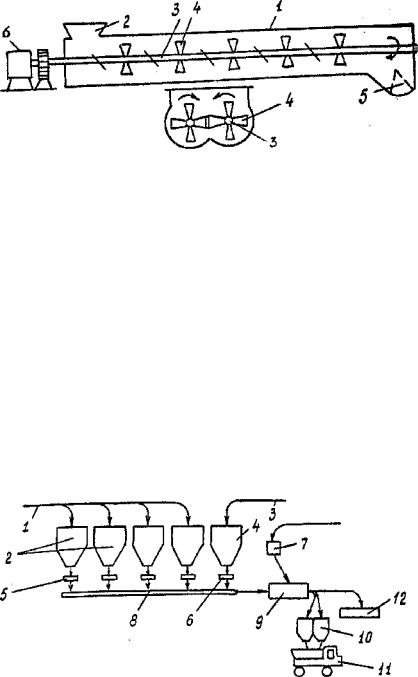
перемещение смеси и ее перемешивание вдоль барабана (рис. 18.4). Время перемещения определенной порции бетонной смеси вдоль барабана должно соответствовать времени, необходимому для ее перемешивания до требуемой однородности. Эти требования обусловливают длину барабана, скорость вращения вала барабана и углы расположения лопастей.
Рис. 18.4. Бетоносмеситель непрерывного действия 1 - корпус; 2 - загрузочное отверстие; 3 - вал; 4 - лопасти; 5 - накопитель с затвором; 6 - электропривод
На бетонном заводе непрерывного действия преобладает оборудование, обеспечивающее именно непрерывность процесса приготовления бетонной смеси: конвейерные линии подачи составляющих, дозаторы непрерывного действия, бетоносмесители непрерывного действия и т.д. (рис. 18.5). Отсутствие ряда операций по сравнению с цикличными заводами (в частности, цикличной загрузки и выгрузки смеси) делает заводы непрерывного действия высокопроизводительными, и с этой точки зрения при больших интенсивностях работ они предпочтительнее. Однако они имеют тот недостаток, что требуют остановки и регулировки при изменении марки бетона, т.е. состава бетонной смеси. Поэтому на гидротехнических стройках они находят применение при больших объемах и интенсивностях укладки одной марки бетона, и обычно в комплексе о заводом циклического действия. При этом бетонные смеси тех марок, которые требуется в небольших объемах, готовят на заводах циклического действия, а на заводе непрерывного действия приготовляют бетонные смеси марок, имеющих большой объем и укладываемых непрерывно длительное время.
Рис. 18.5. Технологическая схема бетонного завода непрерывного действия 1 - подача заполнителей со склада; 2 - расходные бункера заполнителей; 3 -
цементопровод; 4 - расходный бункер цемента; 5 - дозаторы заполнителей; 6 - дозатор цемента; 7 - дозатор воды; 8 - сборный транспортер; 9 - бетоносмеситель; 10 -раздаточные бункера бетонной смеси; 11 - порционный транспорт; 12 - непрерывный транспорт (транспортеры, бетононасосы)
311

Промышленность выпускает бетоносмесители непрерывного действия производительностью 15, 30, 60 м³/ч. Бетонные завода с одной технологической линией такой производительности применяются в промышленном строительстве. Для гидротехнического строительства применяются заводы с двумя-тремя технологическими линиями производительностью 100-150 м³/ч. Выборочная номенклатура бетоносмесительных установок приведена в табл. 18.4.
Таблица 18.4. Выборочная номенклатура бетоносмесительных установок
Модель |
Ориентир. |
|
|
Бетоносмеситель |
Количес |
Максим. |
|
|
технич. |
|
Марка, |
Объем |
Количество |
тво |
Крупность |
|
производ. |
|
тип |
по |
|
фракций |
заполнителя |
|
|
|
|
загрузке |
|
|
|
|
м³/час |
|
|
л |
ст |
|
|
|
|
|
Цикличного действия |
|
|
||
СБ-51 |
7 |
|
СБ-80, |
250 |
1 |
2 |
70 |
|
|
|
пр |
|
|
|
|
СБ-70 |
15 |
|
СБ-16 |
500 |
2 |
4 |
70 |
|
|
|
пр |
|
|
|
|
СБ-185 |
26,5 |
|
СБ- |
750 |
1 |
3 |
70 |
|
|
|
169, пр |
|
|
|
|
СБ-4 |
35 |
|
СБ- |
1200 |
2 |
4 |
120 |
|
|
|
100, гр |
|
|
|
|
М-1 |
52 |
|
Т- |
1500 |
1 |
4 |
|
|
|
|
1000М, |
|
|
|
|
|
|
|
пр |
|
|
|
|
БЗ |
96 |
(2х |
СБ-94, |
1500 |
4 |
4 |
120 |
|
секционный) |
|
гр |
|
|
|
|
СБУ- |
- |
|
- |
4500 |
2 |
6 |
150 |
150 |
|
|
|
|
|
|
|
АБСУ- |
132 |
|
СБ- |
4500 |
2 |
6 |
150 |
2*3000 |
|
|
162,гр |
|
|
|
|
|
|
|
СБ- |
1500 |
1 |
6 |
70 |
|
|
|
138А,п |
|
|
|
|
|
|
|
р |
|
|
|
|
|
|
|
Непрерывного действия |
|
|
||
СБ-61 |
5 |
|
двухва |
|
1 |
2 |
40 |
|
|
|
льный |
|
|
|
|
СБ-75А |
30-35 |
|
Тоже |
|
1 |
4 |
40 |
СБ-78 |
60 |
|
Тоже |
|
1 |
4 |
70 |
СБ- |
135 |
|
Тоже |
|
1 |
3 |
70 |
109А |
|
|
|
|
|
|
|
СБ-118 |
240 |
|
тоже |
|
2 |
4 |
70 |
18.З. Определение производительности бетоносмесителей и бетонных заводов
Расчет производительности бетоносмесителей производится в соответствии с общими положениями по определению производительности строительных машин (см. главу 5). Для бетоносмесителей циклического действия техническая производительность Пт (в м³/ч)
(18.2)
312

Здесь - объем продукции за один цикл бетоносмесителя
qв - объем одного замеса бетоносмесителя по выгрузке, qз - то же по загрузке; - коэффициент загрузки бетоносмесителя, равный коэффициенту выхода бетонной смеси Квых=0,66-0,7.
- число циклов в час при определении
в секундах
(I8.3)
где tзагр - время загрузки бетоносмесителя; tперем - время перемешивания;- время
выгрузки; - время возврата бетоносмесителя. По данным практики
tзагр =ϕ(qз ) =15 −20с;
tпарем =ϕ(qз ,ОК, типа _ смесителя) = 50 −150с(табл.18.4.а);
Таблица 18.4.а. Наименьшая длительность перемешивания бетонной смеси
Объем готового |
|
Продолжительность перемешивания, с |
||
замеса |
Гравитационные смесители с |
В смесителях |
||
|
подвижностью, см |
принудительного действия |
||
|
4 и менее |
5 - 9 |
10 и более |
для всех смесей |
500 и менее |
90 |
75 |
60 |
50 |
Более 500 |
150 |
120 |
90 |
50 |
Продолжительность перемешивания должна обеспечивать однородность бетонной смеси, оцениваемую коэффициентом вариации прочности образцов бетона одного замеса:
(18.4)
где- среднеквадратичное отклонение прочности образцов бетона, взятых из различных мест одного замеса;
- среднее значение прочности этих образцов;
- прочность образцов, взятых из различных мест замеса;
- количество образцов.
Эксплуатационная часовая производительность бетоносмесителя
(18,5) Где kв - коэффициент использования внутрисменного рабочего времени, равный
0,85-0,90.
Часовая эксплуатационная производительность бетонного завода
(I8.6)
где- количество бетоносмесителей.
313
ГЛАВА 19. Бетонное хозяйство
19.1 Состав бетонного хозяйства и определение мощности бетонного завода
Бетонное хозяйство крупного современного строительства представляет собой довольно сложный комплекс взаимосвязанных производственных предприятий и сооружений, в состав которого входят:
∙бетонный завод;
∙склады заполнителей;
∙склады цемента;
∙установки для приготовления добавок;
∙установки по термообработке составляющих бетонной смеси (подогрев, охлаждение);
∙установки контрольного грохочения;
∙другие сооружения и предприятия, необходимые для обеспечения работы
завода (котельная, компрессорная, кузовомоечная, административный и бытовой корпуса, лаборатория и др.).
Вгидротехническом строительстве организация бетонного хозяйства осуществляется обычно по следующей схеме: на начальном этапе подготовительного периода для строительства объектов производственной базы, поселка, транспортных коммуникаций предусматривают пионерное бетонное хозяйство. В дальнейшем строят основное бетонное хозяйство для возведения основных сооружений гидроузла.
Для строительства объектов подготовительного периода обычно применяют небольшие бетонные заводы комплектной поставки или передвижные бетоносмесительные установки. Их расчетная мощность определяется по потребности в бетоне объектов производственной базы и поселка строителей.
Основное бетонное хозяйство рассчитывается по потребности строительства основных сооружений гидроузла. Бетонное хозяйство размещается обычно компактно, на сравнительно небольшой площадке, с максимально возможным приближением к основным сооружениям. При расположении обогатительного завода на площадке бетонного завода предусматривают общую компоновку бетонно-обогатительного хозяйства с совмещением базисных и расходных складов заполнителей.
На рис. 19.I приведена общая принципиальная схема бетонно-обогатительного хозяйства.
Мощность бетонного завода и других предприятий бетонного хозяйства рассчитывают
всоответствии с общими положениями по определению мощности производственных предприятий.
Обычно, производительность бетонного завода и ее предприятий рассчитывают по средней интенсивности укладки бетона за теплый период года, наиболее напряженного по объему бетонных работ. Покрытие отдельных кратковременных пиков рекомендуется производить за счет более плотного режима работы бетонного завода и подключения других возможных источников.
314

Рис. 19.1. План бетонно-обогатительного хозяйства (а)и разрезы по сооружениям (б, в) 1 - приемный бункер гравийной массы; 2 - транспортеры для подачи на завод; 3 - гравийно-сортировочный завод; 4 - транспотеры от гравийно-сортировочного завода на склады; 5 - подземные подштабельные галереи с транспортерами; 6 - склады заполнителей (эстакадные); 7,8- помещение для подогрева (охлаждения) заполнителей, 9 - узел контрольного грохочения; 10 - бетонный завод; 11 - цементныесклада; 12 - компрессорная, бадьемоечная; 13 - бытовые помещения; 14 - бетонная лаборатория; 15 -
315

склад льда; 16 - сбрасывающая тележка; 17 -приемные бункера; 18 - питатели; 19 - транспортеры; 20 - разделительная стенка; 21 - узел перегрузки; 22 - бетонная подготовка
Исходя из изложенного расчетная месячная интенсивность ведения бетонных работ для определения мощности бетонного хозяйства определяется по формуле
(19,1)
где • объем бетонных работ за расчетный (теплый) период года (по календарному
графику), - продолжительность расчетного (теплого) периода, мес (в зависимости от климатической зоны).
За теплый период года принимают период со среднесуточной температурой выше +5°С и определяют по СНиП II 2.01.01-82. Строительная климатология и геофизика.
Необходимая часовая эксплуатационная производительность бетонного завода (в
м³/ч)
|
(19.2) |
Где |
- число расчетных часов работы бетонного завода в месяц при нормальном |
режиме работы (фонд рабочих часов в месяц), определяемое по годовому режиму работы оборудования бетонного завода. По расчетам института "Гидропроект" колеблется в
пределах 440-388 ч/мес в зависимости от климатической зоны ;- расход бетонной смеси на 1 м³ бетона в деле, равный по нормативам 1,02.
Тогда при определении производительности одного бетоносмесителя по формуле (I8.4) число бетоносмесителей равно
(19.3)
где |
-число бетоносмесителей, - часовая производительность одного |
бетоносмесителя, м³/ч; - часовая производительность бетонного завода, м³/ч. Выбранная расчетная мощность бетонного завода должна быть проверена на
удовлетворение максимальной месячной интенсивности ведения бетонных работ при форсированном режиме работы.
|
|
(19.4) |
где |
максимальное число часов работы бетонного завода в |
месяц при |
форсированном режиме работы. По расчетам института "Гидропроект” - |
|
|
Желательно, чтобы |
(19.5) |
В противном случае следует изыскать возможности увеличения максимальной производительности бетонного завода за счет других источников (например, использовать бетонный завод пионерной базы) или откорректировать мощность бетонного завода и выбрать его из условия обеспечения максимальной (пиковой) потребности.
Для предварительных расчетов при отсутствии подробного календарного графика расчетные и пиковые интенсивности работ (в м³/мес) можно с некоторым приближением определить исходя из общих объемов и сроков работ, применяя соответствующие коэффициенты неравномерности.
316

(19.6)
где общий объем бетона в м³;
__ - общий срок ведения бетонных работ в месяцах;
- коэффициент среднегодовой неравномерности бетонных работ;
- коэффициент сезонной среднемесячной неравномерности бетонных работ внутри года по сезонам;
- коэффициент месячной неравномерности бетонных работ внутри сезона. Эти коэффициенты зависят от конкретных климатических и организационных условий ведения бетонных работ и по данным практики при нормальной организации
строительства колеблются в пределах:
19.2. Склады заполнителей
Расходные склады заполнителей на бетонном хозяйстве предназначаются для регулирования несоответствия между поступлением заполнителей и потреблением их бетонным заводом. Они должны обеспечивать прием, складирование и хранение рассортированных по фракциям заполнителей, сохранность их качества и постоянство зернового состава,
Объем склада заполнителей, как и других предприятий бетонного хозяйства, рассчитывают на удовлетворение расчетной интенсивности ведения бетонных работ при нормативном запасе этих материалов на складах. Общий объем склада крупных заполнителей
(19.7)
где■ расчетная месячная потребность в бетоне, определяемая по формулам
(I9.I) или (19.6); - удельный расход крупных заполнителей на 1 м³ бетона, принимаемый по расчету состава бетона и равный в среднем 0,9 м³ /1 м³ бетона; Тзан - нормативный запас материалов в долях от месячной потребности, равный 10-30% в зависимости от условий поставки. В соответствии с составом бетона общий объем склада распределяется по фракциям па отдельные секции, или бурты.
Таким же образом рассчитывают объем склада песка. При зтом в среднем равен 0,45м³ песка (на I м³ бетона), если он не определяется расчетом.
Основные склады заполнителей по конструктивным особенностям делятся на следующие виды: траншейные открытые; кольцевые открытые, или конусные; штабельные эстакадные; штабельные с двухконсольными штабелеукладчиками; закрытые склады (рис. 19.2).
317

Рис. 19.2. Типы складов заполнителей: а) траншейны, б) кольцевой, в) эстакадный склад с транспортерной загрузкой, г) эстакадный склад с автомобильной загрузкой; д) штабельный склад со штабелеукладчиком 1 - конусы отсыпки заполнителей; 2 - транспорт доставки; 3 -подштабельная галерея: 4 -
бункер; 5 - питатель; 6 - конвейер для подачи на бетонный завод; 7 - загрузочный конвейер; 8 -разделительные стенки; 9 - конвейер; 10 - хоботы; 11 - сбрасывающая тележка; 12 - автомобильная эстакада; 13штабелеукладчик; 14, 15 - продольный и поперечный конвейеры штабелеукладчика.
Все виды складов должны удовлетворять следующим требованиям: иметь в основании дренажную систему и уклоны для отвода дождевых и талых вод; иметь удобную систему загрузки и выдачи заполнителей; не допускать сегрегации заполнителей при их сбросе с большой высоты; иметь возможность отогрева смерзшихся заполнителей (при необходимости); исключать возможность смешивания заполнителей разных фракций.
Склады траншейного типа и конусные устраивают при небольших объемах работ. При значительных объемах работ предпочтительнее эстакадные склады. Этот тип складов наиболее распространен на гидротехнических стройках. Все транспортные операции на складах обычно выполняются конвейерами. Продольные транспортеры имеют сбрасывающую тележку, передвигающуюся вдоль транспортера и обеспечивающую сброс материала в нужном месте. Для исключения сегрегации при сбросе заполнителей с высоты более 5 м предусматривают соответствующие хоботы. Для выдачи заполнителей со склада на бетонный завод, под складами (штабелями) обычно устраивают подштабельные галереи, располагая в них транспортеры. Подача заполнителей на эти конвейеры осуществляется через бункера, снабженные питателями. Для подогрева заполнителей в зимний период бункера обычно снабжают специальной системой труб
318

(регистрами). В суровых климатических условиях для совмещения хранения заполнителей с тепловой обработкой применяют закрытые склады шатрового типа или бункерные (рис.19.3).
Рис. 19.3. Закрытый теплый оклад заполнителей с наземными галереями, совмещенный о установкой подогрева - охлаждения 1 - подштабельные галереи; 2 - транспортеры для подачи заполнителя на бетонный завод;
3 - уплотненная насыпь из местного грунта; 4 - каркас; 5 - конусы отсыпки заполнителей; 6 - загрузочные транспортеры со сбрасывающими тележками; 7 - регистры для термообработки заполнителей 8 – питатели
19.3.Склады цемента
Обязательная принадлежность бетонного хозяйства - склады цемента. Для гидротехнического бетона в зависимости от требований к нему используют цементы различных типов (портландцемент, шлакопортландцемент, пуццолановый портландцемент) трех-четырех марок: М300, М400,М500, а в отдельных случаях и М600. Цементы всех типов и марок отличаются по составу, и даже цемент одной и той же марки и типа, получаемый с разных заводов, отличается по химическому составу в связи с различием сырья. Поэтому на складах необходимо обеспечивать раздельное хранение всех этих типов и марок цемента, что должно найти отражение при определении количества отдельных емкостей.
По назначению и объему цементные склады разделяют на основные (базисные) и приобъектные (расходные). Основные склады располагаются у центрального бетонного завода, а приобъектные - вблизи соответствующих установок с доставкой к ним цемента с основных складов. Цемент завозят на основные склады непосредственно по железной дороге или автотранспортом от пристанционных складов перевалочной базы. Для перевозки по железной дороге применяют в основном специальные вагоны, оборудованные системой пневматической разгрузки.
Автомобильные перевозки цемента осуществляют в специализированных автоцементовозах, которые также имеют собственную пневматическую систему, обеспечивающую выгрузку цемента из цистерны и подачу его в склады цемента.
Для определенных районов практикуют доставку цемента водным путем. В этих случаях перевозки осуществляют в специальной таре - мешках, контейнерах или россыпью. В последнем случае цемент возят в трюмных баржах с двойным дном. Для разгрузки применяют также пневмотранспорт.
По конструктивному признаку цементные склады делятся на амбарные, бункерные и силосные. Для всех видов складов обязательны следующие элементы: устройства для приемки цемента с транспорта; собственно склады; установки для подачи цемента к бетонному заводу и другим местам.
319
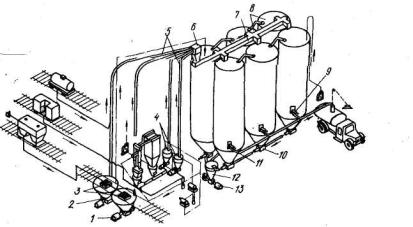
Амбарные и бункерные склады устраивают на небольших объектах.
Основные склады имеют, как правило, силососную конструкцию и выполняются из отдельных ячеек цилиндрической формы диаметром от 3 до 10 м, емкостью 100-1000 т (рис. 19.4). Для обеспечения влажностных условий хранения цемента склады оборудуют системой вентиляции. Для улучшения условий выгрузки нижнюю часть силосов выполняют в виде воронки с углом наклона стенки не менее 55-60° к горизонту и оборудуют специальной системой для рыхления цемента (аэроднище).
Для транспорта, разгрузки и погрузки цемента в пределах цементного склада применяют в основном различное пневмотранспортное оборудование - камерные и винтовые насосы, эрлифты.
Рис. 19.4. Технологическая схема силосного склада цемента 1- пневмоприемник цемента (Эрлифт), 2 – бункер приемный, 3 – рукав приемный, 4 –
пневморазгрузчик цемента, 5 – цементопроводы на подаче цеменита в силосы, 6 – бункер осадитель, 7 – аэрожелоб, 8 – силосы, 9 – пневморазгружатель боковой выгрузки, 10 – пневморазгружатель донной выгрузки, 11 – цементопроводы на выдаче, 12 – бункер выдачи, 13 – насос пневмовинтовой
Общая емкость складов цемента рассчитывается на удовлетворение расчетной интенсивности бетонных работ при нормативных запасах с учетом возможной неравномерной поставки в зависимости от вида транспорта:
(19.8) где
- расчетная интенсивность бетонных работ по формуле (I9.I) или (19.6) в
м³/мес, принятая при расчете производительности бетонного завода; - осредненный расход цемента на I м³ бетона (приблизительно 0,3т/м³),
- нормативный запас цемента в долях от месячной потребности
Количество отдельных емкостей (силосов)в соответствии с вышеизложенным должно быть минимум на одну единицу больше, чем количество типов и марок цемента.и зависит от общего объема склада и принятых единичных емкостей силосов (бункеров).
19.4. Установки для регулирования температуры составляющих бетонной смеси
В зависимости от требований к температурному режиму бетонной кладки - по условиям обеспечения трещиностойкости или по условиям зимнего бетонирования - необходимо регулировать температуру составляющих бетонной смеси. В летний период - это охлаждение составляющих, в зимний период - их подогрев. Для этих целей создают
320
специальные установки только для подогрева или охлаждения, или, как правило, служащие для той и другой цели.
Подогрев воды осуществляется в элоктробойлерной или котельной, а охлаждение - в холодильной установке. Для охлаждения бетонной смеси вместо части воды можно применять лед. Лед заготавливают намораживанием в зимнее время в буртах или специальных установках.
Охлаждение или подогрев крупного заполнителя и песка осуществляют: в штабелях на складах заполнителей с помощью регистров (паровых, водяных); в наддозаторных бункерах бетонного завода; в специальных бункерах, используя теплоносители (вода, воздух) и вакуум-установки.
Каждый из способов имеет свои области применения, как по возможностям снижения (повышения) температуры бетонной смеси, так и по экономической эффективности. Способ подогрева или охлаждения выбирают на основе технико-экономического сравнения вариантов.
19.5. Прочие установки и сооружения
Установки для приготовления добавок. Для улучшения основных требуемых свойств бетона по прочности, водонепроницаемости, морозостойкости, а также для улучшения технологических свойств бетонной смеси (удобоукладываемости, пластичности, нерасслаиваемости и др.) в бетонную смесь при ее приготовлении вводят дополнительно различные добавки.
На строительство добавки поступают в виде порошка или растворов высокой концентрации. На бетонном заводе на специальных установках (в цехах) из них готовят водные растворы нужной концентрации. Цехи для приготовления добавок оборудуются специальными смесительными баками с мешалками. Концентрации растворов контролируют по его плотности с помощью ареометров. Готовый раствор специальными насосами перекачивается в соответствующие расходные бункера бетонного завода, далее дозируется и подается в бетоносмеситель одновременно с водой.
Установки контрольного грохочения. В процессе складирования и транспортирования крупных заполнителей происходит их дополнительное дробление при различных перегрузках и перемещениях. В результате этого в крупных фракциях появляются мелкие фракции и чистота проведенного ранее разделения заполнителей на фракции нарушается. Это может привести к нарушению требуемой однородности бетона и снижению его
предельной растяжимости а также и других свойств. Для ответственных конструкций, где требование к однородности очень велико с целью исключения этого неблагоприятного фактора применяют дополнительную контрольную сортировку крупного заполнителя на установках контрольного грохочения. Это те же сортировочные установки, что и на сортировочных заводах, но более компактные и меньшей мощности. Иногда контрольному грохочению подвергают не все фракции, а только мелкие. Применение контрольного грохочения обесточивает кроме повышения качества бетонной смеси снижение расхода цемента.
Установки контрольного грохочения обычно устанавливают в технологической линии подачи заполнителей непосредственно перед бетонным заводом, поэтому режим их работы соответствует режиму работы конвейерных линий и бетонного завода.
Прочие сооружения. Кроме указанных выше установок бетонное хозяйство должно иметь различные вспомогательные установки и сооружения, обеспечивающие функционирование всего комплекса бетонного хозяйства. Основные среди них:
-компрессорная - для получения воздуха, необходимого для работы различных пневмоустановок;
-бадьемочная - для промывки, очистки кузовов машин, бадей и прочих транспортных средств от налипшей бетонной смеси;
321
-бытовые помещения для персонала завода с раздевалками, душами и прочими сантехническими устройствами;
-бетонная лаборатория - обычно совместно со строительной лабораторией;
-различные производственные помещения для обслуживания инженерных коммуникаций бетонного завода.
Необходимость тех или иных установок в составе бетонного хозяйства определяется проектом в зависимости от условий строительства, типа сооружений и качества исходных материалов.
322
ГЛАВА 20. Транспортирование бетонной смеси
20.I. Выбор транспортной схемы бетонных работ
Транспортная схема бетонных работ представляет собой комплекс машин, механизмов, транспортных коммуникаций и приспособлений, обеспечивающих доставку бетонной смеси от бетонного завода до места укладки. Иногда доставку обеспечивает один вид транспорта, иногда приходится применять несколько видов. В связи с этим в общем случае транспортную схему можно разбить на две составные части:
-транспорт от бетонного завода до сооружения (горизонтальный транспорт);
-подача бетонной смеси в блоки бетонирования (вертикальный транспорт).
Для каждой из этих составляющих имеются свои типы машин, выполняющие или функции только одной части или совмещающие общие функции. Транспортная схема не остается постоянной, изменяясь для разных этапов строительства и для различных частей сооружения по мере роста сооружений по высоте.
Выбор транспортной схемы и конкретных типов машин зависит, прежде всего, от дальности транспортировки, компоновки и размеров сооружений, а также от свойств бетонной смеси, топографических, климатических и организационных условий. Наибольшее распространение в процессе строительства нашли транспортные схемы с использованием для горизонтального транспорта различных видов специальных автомобилей, а для подачи в блок стреловых и башенных кранов, кабель-кранов, конвейеров, бетононасосов и пневмобетоноукладчиков.
При небольших дальностях транспортировки (в пределах 1-2 км) можно рассматривать применение конвейерного вида как горизонтального, так и вертикального транспорта. При меньших дальностях (в пределах 0,5 км) возможно применение бетононасосного вида транспорта или пневмобетоноукладчиков.
Выбранная транспортная схема бетонной смеси и средства транспорта должны обеспечивать для данных конкретных дорожных и климатических условий доставку бетонной смеси требуемой подвижности (жесткости) на всем пути от бетонного завода до места укладки. В соответствии с общими положениями, транспортная схема должна удовлетворять следующим требованиям:
-обеспечивать требуемую расчетную интенсивность бетонных работ;
-гарантировать транспортировку смесей требуемой подвижности и крупности зерен заполнителя;
-обеспечивать сохранность однородности смеси, т.е. нерасслаиваемость смеси в пути;
-исключать потери раствора и смеси в пути и при перегрузках;
-предохранять бетонную смесь от прямого воздействия атмосферных осадков, ветра, прямых солнечных лучей, мороза и др.
Разнообразные виды транспорта по своим конструктивным особенностям в различной
степени удовлетворяют этим требованиям, поэтому при выборе конкретного вида транспорта для определенных условий требуется проверить его технические характеристики на соответствие этим требованиям и при необходимости предусмотреть дополнительные приспособления или дорожные и организационные мероприятия для обеспечения конкретных требований (тенты, обогрев, уплотнения, тип дорожного покрытия, уклоны дорог и т.д.).
Особенности конструкций и технические характеристики различных видов транспорта приводятся в соответствующих справочниках, каталогах. Здесь приведем краткие рекомендации по их выбору.
323

20.2. Выбор типа горизонтального транспорта
Для транспортировки бетонной смеси от бетонного завода до сооружения применяют как циклические виды транспорта (автомобильный, ж/д) так и непрерывные (ленточные конвейеры).
Автомобильный транспорт
Выбор конкретного вида автотранспорта зависит от его технико-экономических характеристик, свойств бетонной смеси, дальности транспортировки. В принципе желательно для транспортировки бетонной смеси использовать специализированные виды транспорта - автобетоновозы и автобетоносмесители.
Допустимые время и расстояния транспортирования бетонной смеси с использованием автотранспорта при различных дорожных покрытиях и подвижностях бетонной смеси приведены в табл. 20.1. и 20.2.
Таблица 20.1. Допустимая продолжительность транспортирования бетонной смеси температурой 180С (при температуре воздуха 20-300С)
Дорожное |
Средняя скорость |
Продолжительность транспортировки, мин |
|||
покрытие |
транспортирования, |
Автосамосвалы |
Автобетоновоз |
Автобетоно- |
|
|
км/ч |
|
ы |
смесители |
|
Жесткое |
|
60 |
90 |
200 |
|
(асфальтобетонное |
30 |
35 |
50 |
140 |
|
, цементобетонное |
20 |
30 |
90 |
||
|
|||||
и т.п.) |
|
|
|
|
|
Мягкое (грунтовое |
|
30 |
45 |
Не рекомендуется |
|
улучшенное) |
15 |
20 |
30 |
|
|
|
|
10 |
15 |
|
Таблица 20.2. Допустимые расстояния транспортирования бетонных смесей при
температуре воздуха 20-300С |
|
|
|
|
|
|
|
|
|||
|
|
|
|
|
|
|
|
|
|
|
|
|
Подвижн |
Вид |
|
Скорость |
|
|
Расстояние, км |
|
|||
|
ость |
дорожного |
|
транспорт |
Автоса |
Автобет |
|
Автобетоносмесители |
|||
|
бетонной |
покрытия |
|
ирования, |
мосвал |
оновозы |
|
|
Режим |
|
|
|
смеси, см |
|
|
км/ч |
ы |
|
|
А |
|
Б |
В |
|
1-3 |
Жесткое |
|
|
30 |
До 45 |
|
Не |
|
До |
До |
|
|
(асфальтобет |
|
|
|
|
|
ограничи |
|
120 |
100 |
|
4-6 |
онное, |
|
30 |
20 |
30 |
|
вается |
|
100 |
80 |
|
7-9 |
цементобето |
|
|
15 |
20 |
|
|
|
80 |
60 |
|
10-14 |
нное) |
|
|
10 |
15 |
|
|
|
60 |
45 |
|
1-3 |
Мягкое |
|
|
7,5 |
12 |
|
|
|
|
|
|
4-6 |
(грунтовое |
|
15 |
5,0 |
8 |
|
Не рекомендуется |
|||
|
7-9 |
улучшенное) |
|
3,7 |
5,4 |
|
|||||
|
|
|
|
|
|
|
|
||||
|
10-14 |
|
|
|
2,5 |
4,0 |
|
|
|
|
|
Примечание. Режимы работы автобетоносмесителя:
А – сухие бетонные смеси с подачей воды за 10-20 мин до разгрузки; Б – частично затворенные смеси с перемешиванием в пути; В – готовые бетонные смеси с перемешиванием в пути
Автосамосвалы. Наиболее распространен автомобильный вид общестроительного транспорта - самосвалы (рис.20.1., табл.20.3.). Общестроительные самосвалы используют обычно при дальности транспортировки до 15 км без применения замедлителей схватывания бетонной смеси. При применении замедлителей схватывания (в частности,
324

кормовой сахарной патоки) дальность транспортировки может быть увеличена до 50-70 км.. В связи с тем, что общестроительные самосвалы конструктивно не полностью удовлетворяют требованиям к транспорту бетонной смеси , требуется их частичное дооборудование (наращивание бортов на 40-50 см, дополнительные резиновые уплотнения щелей, тенты, обогрев кузова и т.д.). Объем бетонной смеси перевозимый автосамосвалами, принимается кратным объему бетоносмесителей бетонного завода по выходу.
Рис. 20.1. Автосамосвал МАЗ-551605.
Таблица 20.3. Технические характеристики некоторых автосамосвалов Марки
|
|
Параметры |
ЗИЛ - |
КАМАЗ- |
МАЗ- |
КрАЗ- |
УРАЛ |
БелАЗ- |
Татра |
|
|
|
55160 |
815- |
|
||||||
|
|
|
45085 |
65111 |
65032 |
-583106 |
75406 |
|
||
|
|
|
5 |
290S8T |
||||||
|
|
|
|
|
|
|
|
|||
|
|
1 |
2 |
3 |
4 |
5 |
6 |
7 |
8 |
|
|
1. |
Грузоподъемность |
6 |
14 |
20 |
18 |
25 |
30 |
30 |
|
|
, т |
|
|
|
|
|
|
|
|
|
2. |
Объем кузова (без |
|
|
|
|
|
|
|
|
|
|
надставки), м3 |
3,8 |
8,2 |
10,5 |
12 |
16 |
15 |
18 |
|
|
3. |
Направление |
Назад |
Назад |
Назад |
Назад |
Назад |
Назад |
Назад |
||
|
разгрузки |
|||||||||
4. |
Максимальная |
85 |
90 |
92 |
75 |
100 |
50 |
- |
|
|
|
скорость км/ч |
|
Основных производителей на рынке большегрузных самосвалов не много. Первенство по числу выпускаемых машин держит БелАЗ, в состав которого еще в 2004 году вошел Могилёвский автозавод. На рынке зарубежных крупных самосвалов лидирует Caterpillar. Деятельность этой компании в сфере производства таких автосамосвалов началась в 1963- м с выпуска 35-тонного самосвала Caterpillar 769. До этого компания выпускала одно- и двухосные тягачи для самосвальных прицепов и полуприцепов Athey. Сейчас компания выпускает девять моделей большегрузных автосамосвалов и четыре базовые модели строительных самосвалов с шарнирно-сочлененной рамой, не считая машин Elphinston, собираемых в Австралии.
Следом за Caterpillar идет компания Komatsu, и основу ее производства составляют самосвалы грузоподъемностью 25...300 т, в том числе модели, доставшиеся в наследство от Dresser. Активно конкурируют с этими гигантами на рынке компании Terex и Hitachi. В секторе сочлененных самосвалов выделяются компании CNH, Bell и Volvo, но основной упор они делают на использование своих машин в дорожном строительстве.
Автобетоновозы (рис. 20.2., табл. 20.4) - специализированные машины и являются наиболее современным видом транспортирования готовой бетонной смеси. Они имеют
325

высокие закрытые кузова каплевидной формы, расположенные в зоне минимальной вибрации рамы автомобиля, благодаря чему обеспечивается сохранность бетонной смеси от расслоения. Последнее позволяет увеличить дальность транспортирования бетонной смеси по сравнению с автосамосвалами. Для предохранения смеси от воздействия атмосферных осадков и ветра кузов снабжен крышкой, а для предохранения смеси от воздействия низких отрицательных температур — двойной обшивкой, образующей термоизолирующие полости между ее листами, которые позволяют утеплить кузов термоизоляционным материалом в особо суровых климатических условиях. Так же, для сохранения температуры смеси в холодное время года емкость может иметь двойные стенки, между которыми циркулируют выхлопные газы автомобиля. Разгрузка емкости осуществляется ее опрокидыванием (как у самосвала) с помощью двух телескопических гидроцилиндров. Угол наклона днища емкости при разгрузке составляет 90°, что обеспечивает практически полную выгрузку бетонной смеси.
Автобетоновозы обеспечивают как порционную, так и непрерывную выгрузку бетонной смеси. При транспортировке по дорогам с жестким покрытием автобетоновоз может перемещаться со скоростью до 50 км/ч.
Рис.20.2. Автобетоновоз СБ-113.
а - транспортное положение; б - положение разгрузки; в - поперечный разрез кузова. 1- открытая часть кузова; 2- кузов; 3- упор; 4- телескопический подъемник; 5 –
гидравлический цилиндр для открывания и закрывания крышки кузова; 6 – шасси; 7- крышка в закрытом положении; 8- закрытая часть кузова; 9- крышка в открытом положении.
Таблица 20.4. Технические характеристики некоторых автобетоновозов
Показатели |
|
|
Марки |
|
|
|
СБ-113 |
СБ-113М |
АБ-2 |
СБ-124 |
СБ-128 |
||
|
||||||
1 |
2 |
3 |
4 |
5 |
6 |
|
Базовый автомобиль |
ЗИЛ-130Д |
МАЗ-504Г |
МАЗ 503А |
КАМАЗ |
КрАЗ 6505 |
|
Вместимость кузова, |
|
|
|
5511 |
|
|
1,6 |
3 |
3,2 |
4 |
6 |
||
м3 |
||||||
|
3,8 |
6,6 |
8 |
8,5 |
14 |
326

Грузоподъемность, т
Автобетоносмесители (рис. 20.3., табл. 20.5.) предназначены для приготовления бетонной смеси в пути следования из отдозированных исходных материалов или для транспортировки готовой бетонной смеси с периодическим перемешиванием ее в пути. Автобетоносмесители применяются при больших дальностях или времени транспортировки, при строительстве рассредоточенных и линейно протяженных сооружений и перевозки сильно расслаиваемых высокоподвижных и литых бетонных смесей (с осадкой конуса > 16 см). Дальность транспортирования зависит от времени схватывания бетонной смеси (до 15—25 км). В случае перевозки сухой смеси барабан загружают сухими составляющими, а воду заливают в дозировочно-промывочный бак 3. В пути (за 5—10 мин до подъезда к месту назначения) барабан приводится во вращение и заливается необходимое количество воды. В результате этого к месту строительства доставляется готовая бетонная смесь. Выгрузка готовой смеси осуществляется при вращении барабана в обратную сторону. Для транспортировки бетонной смеси к массивным бетонным сооружениям их использование нерационально. Серьезным недостатком автобетоносмесителей является их большая масса и малая проходимость, что усложняет и ограничивает их использование на дорогах с грунтовым покрытием.
Рис.20.2. Автобетоносмеситель
1 - базовый автомобиль; 2 - центробежный насос; 3 - бак для воды; 4 - смесительный барабан; 5 - загрузочная воронка; 6 - разгрузочное устройство; 7 - переходная рама; 8 -дозатор:воды; 9 - цепной привод смесительного барабана; 10 – редуктор
Таблица 20.5. Технические характеристики некоторых автобетоносмесителей.
Показатели |
|
|
Марки |
|
|
|
СБ-159 |
СБ-127 |
АМ-6ЕН |
42184-03 |
АМ-9НА |
||
|
||||||
1 |
2 |
3 |
4 |
5 |
6 |
|
Модель автомашины |
КАМАЗ |
КАМАЗ |
КрАЗ-250 Седельный КрАЗ-258 |
|||
|
5511 |
5412 |
|
тягач |
|
|
Объем барабана, м3 |
8 |
10 |
10 |
11,6 |
15 |
|
Выход смеси |
5 |
6 |
6 |
7 |
9 |
Конвейерный транспорт
Конвейерный транспорт может применяться как для транспортирования бетонной смеси от бетонного завода до сооружения, так и для ее подачи в блок и распределения по блоку (рис.20.4). Рационально применять этот вид транспорта в сочетании с бетонными заводами непрерывного действия. Главное преимущество конвейерного транспорта - большая пpoизводительность. Недостатками являются большое количество перегрузок и, следовательно, повышенное расслоение бетонной смеси, сложность прокладки трасс и
327

обеспечения условий незамерзания смеси (утепление галерей). Кроме того, область применения ограничивается транспортировкой относительно жестких бетонных смесей с осадкой конуса до 4-6 см. При серийно выпускаемых в настоящее время конвейерах общего назначения рациональная дальность транспортирования не превышает 2 км.
Рис. 20.4. Общий вид использования конвейерных бетоноукладчиков.
Магистральные конвейеры общего назначения выпускаются секциями длиной 400500 м с шириной ленты до 1200 мм, со скоростью 1 м/с.
Для приема бетонной смеси с магистральных конвейеров и распределения ее по блокам применяют переставные конвейеры длиной 10-15 м или ленточные бетоноукладчики с конвейером, смонтированным на стационарной или выдвижной стреле.
По мере совершенствования конструкций транспортеров и выпуска специальных транспортеров для транспортировки бетонной смеси область их применения будет значительно расширяться. Так, в практике работы заграничных фирм "Ротек", "Свингер" и других в последнее время находят широкое применение высокоскоростные конвейеры со скоростями до 5 м/с, специально сконструированные для транспортировки бетонных смесей. Конструктивные решения таких конвейеров позволяют компоновать их как для горизонтального транспорта, так и вертикального подъема и распределения смеси по блоку. Применение высокоскоростных конвейеров уменьшает расслоение бетонной смеси и позволяет увеличить допустимый угол наклона до 30° вместо 18° при обычных конвейерах. Имеется эффективная установка мобильной конвейерной системы для укладки бетонной смеси на телескопической стреле пневмоколесного крана (рис.20.5, табл. 20.6).
328

Рис. 20.5. Мобильный 5-ти секционный телескопический ленточный транспортер фирмы “Путцмайстер” – TB 39/130 (Telebelt)
Таблица 20.6. Технические характеристики самоходных ленточных бетоноукладчиков
|
Показатели |
СБ- |
ЛБУ- |
ТБС- |
S- |
Rotek |
Путцмайстер |
|||
|
|
|
|
|
131 |
20 |
30/500 |
Swinger |
(США) |
ТB 39/130 |
|
|
|
|
|
|
|
|
(США) |
|
Германия |
Производительность, м³/ч |
20 |
25 |
100 |
90 |
>100 |
275 |
||||
Вместимость |
|
|
приемного |
2,0 |
2,4 |
3,0 |
- |
- |
- |
|
бункера, м³ |
|
|
|
|
|
|
|
|
|
|
Вылет |
стрелы |
ленточного |
12 |
3-20 |
30 |
9,8-23 |
35 |
39 |
||
конвейера, м. |
|
|
|
|
|
|
|
|
|
|
Наибольший |
угол |
подъема |
18 |
18 |
18 |
30 |
30 |
30 |
||
конвейера, град. |
|
|
|
|
|
|
|
|
||
Наибольший |
угол |
опускания |
12 |
12 |
20 |
4 |
- |
- |
||
конвейера, град. |
|
|
|
|
|
|
|
|
||
Угол |
поворота |
стрелы или |
160 |
180 |
60 |
220 |
300 |
- |
||
платформы в плане, град. |
|
|
|
|
|
|
Бетононасосный транспорт
Бетононасосный транспорт обеспечивает в определенных пределах как горизонтальное, так и вертикальное перемещение (перекачку) бетонной смеси.
По конструктивному исполнению бетононасосы подразделяются на стационарные и мобильные автобетононасосы (рис.20.6), а по используемому приводу перекачки смеси на бетононасосы:
-с механическим приводом;
-роторные (рис. 20.7)
-c гидравлическим приводом (рис.20.8).
Внастоящее время бетононасосы с механическим приводом не нашли своего применения.
Роторные имеют ряд недостатков главным, из которых является небольшой срок службы гибких шлангов. Наибольшее применение нашли бетононасосы с гидравлическим (двухпоршневым) приводом, установленные на шасси грузового автомобиля – автобетононасосы.
Вкомплект автобетононасоса входит секционная распределительная стрела (Рис. 20.8)
истационарные бетоноводы с диаметром, в основном, 125мм, состоящие из звеньев труб длиной 3 м, соединяемые быстроразъемными замками.
329

Рис. 20.6. Общий вид автобетононасоса.
Рис. 20.7. Схема роторного привода 1- транспортный бетоновод; 2- ролики; 3- насосная камера; 4- вал; 5- ротор; 6-
нейлоново - неопреновый шланг; 7- приемный бункер бетононасоса
На рис. 20.7 показана схема работы роторного привода. Бетонная смесь из приемного бункера 7 за счет вращения ротора 5 и прохождения роликов 2 по гибкому шлангу 6 выталкивается в транспортный бетоновод 1.
330

Рис. 20.8. Схемы поршневого гидропривода
а– такт нагнетания в правом (по ходу движения смеси в бетоноводе 4); б – наоборот; в
–3D вид такта всасывания и нагнетания смеси.
1, 2- поршни; 3- бетонотранспортные цилиндры; 4- бетоновод; 5- окно вертикальной заслонки; 6- горизонтальная заслонка; 7- приемный бункер бетононасоса
На рис. 20.8. даны схемы гидравлического привода.
На рис.20.8, а - показан такт нагнетания в правом (по ходу движения смеси в бетоноводе 4) бетонотранспортном цилиндре и такт всасывания в левом; рис.20.8 б – наоборот. Поршень 2 (рис.20.8,а) засасывает бетонную смесь из приемного бункера в левый бетонотранспортный цилиндр через окно горизонтальной заслонки 6 (такт всасывания), а поршень 1 синхронно выталкивает смесь из правого цилиндра в бетоновод 4 через окно вертикальной заслонки 5 (такт нагнетания). При изменении направления движения поршней (рис.20.8, б) соответственно меняется и положение заслонок: поршень 1 через окно горизонтальной заслонки 6 засасывает смесь из приемного бункера, а поршень 2 выталкивает ее в бетоновод 4 через окно вертикальной заслонки 5.
331

Рис. 20.. Рабочие зоны 5-ти секционной распределительной стрелы автобетононасоса SERMAC 5TR62
Преимуществами использования бетононасосного транспорта являются удобство применения его в стесненных условиях, независимость от погодных условий, меньшие энерго- и трудозатраты по сравнению с другими видами, применимыми в этих условиях.
К недостаткам можно отнести использование удобоперекачиваемого бетона с повышенным содержанием долей цемента и песка и ограничением по крупности максимальной фракции крупного заполнителя (1\3 диаметра бетоновода).
На рис.20.8 приведена диаграмма рабочих зон автобетононасоса SERMAC 5TR62. Максимальная высота подачи с использованием распределительной стрелы по вертикали
– 61,25м, по горизонтали – 52,5 м и подача вниз – 43м.
332

Бетононасосный вид транспорта в гидротехническом строительстве до последнего времени применялся в основном для отделок туннелей. Совершенствование конструкции бетононасосов расширило область их применения и привело к эффективности их использования при бетонировании и наземных густоармированных конструкций и элементов сооружений в труднодоступных местах (при возведении зданий ГЭС, трубопроводов и других тонкостенных конструкций)
Ранее действующими техническими условиями ограничивалась перекачка высокоподвижных и литых бетонных смесей. Однако новейшие исследования показали возможность и целесообразность перекачки таких смесей с применением специальных воздухововлекающих добавок, супердобавок и комплексных, предотвращающих расслоение бетонной смеси (ЛХД, С-3, ЛХД+10-03 и т.д.).
Российские производители выпускают размерную линейку машин для разных областей бетонных работ, как правило, по кооперации с зарубежными фирмами. Производительность отечественных бетононасосов изменяется в пределах 5-120 м³/ч. Приведенная длина горизонтального транспорта - до 450 м, вертикальный подьем до 95 м (табл.20.7.). Так, серия автобетононасосов выпускается Россией совместно с итальянской фирмой “АNTONELLI s.r.l.”. В автобетононасосах АБН 37, АБН 42 и АБН 47 применяется металлоконструкция распределительных стрел и опор фирмы “АNTONELLI s.r.l.” (Италия).
Таблица 20.7.Технические характеристики некоторых отечественных бетононасосов
|
|
Показатели |
|
|
Марки |
|
|
|
|
СБ-161 |
БН 80-26 |
АБН-32 |
АБН-47 |
||
|
|
|
|||||
|
|
1 |
2 |
3 |
4 |
5 |
|
|
1. |
Тип |
стацион. |
с распр.стр. |
с распр.стр. |
с распр.стр. |
|
2. |
Техническая |
||||||
|
|
|
|
||||
|
производительность, м3 / час |
5-65 |
5-80 |
75 |
120 |
||
3. |
Вылет распределительной |
||||||
- |
26 |
32 |
47 |
||||
|
стрелы (высота), м |
||||||
|
|
|
|
|
|||
4. |
Наибольшая дальность |
|
|
|
|
||
|
подачи: |
350 |
400 |
450 |
450 |
||
|
-по горизонтали |
||||||
|
80 |
80 |
95 |
95 |
|||
|
-по вертикали |
5.Объем приемного бункера 0,7 0,4 0,7 0,7
Внастоящее время, наряду с зарекомендовавшими себя зарубежными фирмами: “Vibay”, “Schwing-Shtetter”, “ Putzmeister ”(Германия) на российский рынок выходят ведущие итальянские (Sermac, Cifa, Coime) и южно-корейские производители (KCP, DCP) (Табл. 20.8.) с высоким уровнем соотношения цена/качество и оперативного сервиса. Преимущества спецтехники Coime:
- простота и надежность (не используется сложное электронное оборудование, которое затрудняет эксплуатацию и ремонт в условиях России);
- приспособленность к суровым климатическим условиям (Coime выпускает совместно с финской компанией Saraka строительную технику для скандинавских стран и уверенно лидирует на этих рынках); использование высокоэффективных шасси и комплектующих ведущих европейских производителей. По заказу возможно исполнение автобетононасосов в специальной “зимней” комплектации с существенно переработанной системой управления.
Значительное место в производстве бетононасосов занимают производители из Южной Кореи DCP, KCP (Кей Си Пи). В их производственной линейке присутствуют машины, с распределительной стрелой начиная от 24-х метров и до рекордных 65-и. Эта машина является уникальной по длине стрелы и производительности, 225 м3/ч. Для
333

изготовления насосных групп используется шведская сталь и гидравлическое оборудование ведущих японских (Kavasaki) и европейских (Bosch-Rexroth) производителей. Cifa - компания наряду с немецкими производителями, такими как Putzmeister и Schwing, является мировым лидером в производстве бетонной техники. На рынках США и Италии она занимает одно из ведущих мест по количеству проданных автобетононасосов. В качестве несущего шасси используются автомобили производителей: Astra, Iveco, MAN, Volvo, Mercedes-Benz и Scania. Ассортиментный ряд самих насосных установок позволяет удовлетворить практически любые потребности современного строительного строительства.
Таблица 20.8. Технические характеристики некоторых автобетононасосов зарубежных фирм
|
|
|
Марки |
|
|
Показатели |
Швинг- |
Путцмайстер |
Сермак |
Daewoo |
Cifa |
Штеттер |
M 70-5 |
6TR65 |
DCP 52 RZ |
K52 L |
|
|
S 61 SX |
Германия |
Италия |
Ю.Корея |
XRZ |
|
Германия |
|
|
|
Италия |
1 |
2 |
3 |
4 |
5 |
6 |
1. Регулируемая тех. |
до 138 |
до 200 |
до 184 |
до 225 |
до 179 |
произв. м3 / час |
|
|
|
|
|
2. Вылет |
|
|
|
|
|
распределительной |
61 |
69,3 |
65 |
52 |
52 |
стрелы, м |
|||||
3. Наибольшая |
|
|
|
|
|
дальность подачи: |
450 |
400 |
- |
- |
- |
-по горизонтали, м |
|||||
-по вертикали, м |
80 |
60 |
- |
- |
- |
4. Объем приемного |
0,5 |
0,5 |
0,6 |
0,6 |
0,65 |
бункера |
Впоследнее время все более широкое применение находят распределительные стрелы
-манипуляторы (присоединяются к магистральному бетоноводу, идущему от бетононасоса), обеспечивающие подачу бетонной смеси в различные точки бетонируемых блоков. Радиус, действия таких стрел до 35м.
Другим видом машин для трубопроводного транспорта являются пневмобетоноукладчики (рис. 20.9, а, б, табл.20.9). Условия применения пневмобетоноукладчиков практически те же, что и для бетононасосов, при ограничении дальности транспортирования по горизонтали до 300 м и по вертикали до 35 м. Производительность серийных пневмобетоноукладчиков колеблется от 3 до 15 м³/ч. Рекомендуемая подвижность бетонной смеси 6-12 см. Разработаны специальные конструкции пневмонагнетателей для транспортировки более жестких бетонных смесей с подвижностью 3-5 см..
Пневмонагнетательные установки имеют преимущества при бетонировании тонкостенных бетонных и высоких железобетонных конструкций в стесненных условиях (тоннельные обделки, башни и т.д.).
Таблица 20.9.Технические характеристики некоторых отечественных пневмобетоноукладчиков
Показатели |
|
|
Марки |
|
|
ПН-0,5 |
СМБ-006 |
ПН-10.80 |
СО-50ПБН |
||
|
|||||
1 |
2 |
3 |
4 |
5 |
|
1. Техническая |
|
. |
|
|
334

производительность, м3 / час |
15 |
До 8 |
До 15 |
6 |
2. Наибольшая дальность |
|
|
|
|
подачи: |
До 200 |
150 |
100 |
150 |
-по горизонтали |
||||
-по вертикали |
35 |
30 |
15 |
35 |
3. Объем приемного бункера |
0,62 |
0,6 |
0,5 |
0,3 |
Рис. 20.9: а - пневмонагнетательная установка; б - схема бетонирования сооружения с помощью пневмонагнетателя, в - пневмобетононасос
1 - корпус; 2 - загрузочная воронка; 3 - затвор; 4,5 - подводящий и отводящий трубопроводы; 6 - секция бетоновода; 7 - гаситель; 8 - компрессор; 9 - ресивер; 10 - пневмонагнетатель; 11 - вибропитатель; 12 - автобетоновоз; 13 - бетоновод; 14 - гаситель; 15 - хобот; 16 – опалубка
20.3. Подача бетонной смеси в блоки бетонирования
Рассмотренные выше горизонтальные виды транспорта при определенных условиях могут использоваться также и для подачи бетонной смеси в блоки бетонирования или вообще употребляться только для этой цели. При этом можно выделить следующие основные способы подачи бетонной смеси в блоки бетонирования:
-автотранспортный со специальных бетоноукладочных мостиков или эстакад;
-конвейерный;
-бетононасосный;
-крановый.
Автотранспортный способ может быть использован для подачи смеси в блоки невысоких распластанных сооружений и в блоки, расположенные в основании сооружений. Для этой цели устраивают специальные бетоноукладочные мостики или эстакады для въезда автотранспорта (рис.20.10). Разгрузку бетонной смеси осуществляют или непосредственно в блок свободным сбрасыванием через специальные окна в мостиках (при высоте сброса не более 6м для неармированных конструкций и 2 м для армированных) или в бункера с последующей подачей в блок по хоботам или виброхоботам (рис.20.11). Однако следует заметить, что устройство бетоноукладочных мостиков или эстакад требует расхода большого количества металла, а также соответствующего времени для их монтажа. Поэтому наблюдается тенденция отказа от таких решений – они применяются только в случае нецелесообразности других решений.
335

Рис. 20.10. Схема установки бетоноукладочных мостиков для подачи бетонной смеси автосамосвалам 1 - опалубка; 2 - опоры мостика; 3 - несущие балки; 4 -съемный настил; 5 - приемный
бункер; 6 - хоботы; 7 - бетоновозный транспорт
Рис. 20.11. Схемы подачи бетонной смеси с высоких эстакад: а) общая; б) схема хобота; в) схема виброхобота 1 - опоры эстакады; 2 - пролетное строение; 3 - приемный бункер; 4 - хобот или
виброхобот; 5 - бетонируемый блок; 6 - звенья хобота; 7 - звенья виброхобота: (7а - с вибраторами, 7б - с гасителями; 7в - с обогревом; 7г - звено с кольцевым гасителем)
Конвейерный и бетононасосный способы применяются при использовании соответственно конвейерного или бетононасосного оборудования (рис.20.12, 20.13). Условия их использования для подачи в блок обуславливаются техническими возможностями соответствующего оборудования. При использовании обычного серийного конвейерного транспорта со скоростью 1 м/с угол наклона транспортеров не должен превышать 18˚. При применении новых высокоскоростных конвейеров угол наклона может быть увеличен до 30˚.
Имеют свои области применения и гибридные машины на базе автобетоносмесителей
– автобетоносмеситель - бетононасос с распределительной стрелой (рис. 20.14), автобетоносмеситель – конвейер (рис.20.15).
336

Рис. 20.12. Схема конвейерного транспорта бетона 1 - бетонный завод; 2- магистральные стационарные конвейеры 3 - перегрузочные узлы; 4
- продольные распределительные транспортеры со сбрасывающими тележками; 5 - поперечные распределительные транспортеры; 6- эстакада; 7 – хоботы
Рис. 20.13. Схема подачи бетонной смеси в блоки бетононасосами: 1 - автобетоновоз; 2 - приемный бункер бетононасоса; 3 - бетононасос; 4 - бетоновод; 5 - бетонируемый блок; б - последовательность наращивания бетоновода
337

Рис. 20.14. Автобетоносмеситель с бетононасосом
Рис.20.15. Автобетоносмеситель с ленточным конвейером 1 - приводной барабан транспортера; 2 - ось поворота лотка; 3 - опорный
барабан; 4 - бандаж смесительного барабана; 5 - ролики; 6 - двигатель и гидросистема смесительного барабана; 7 - базовый автомобиль: 8 - гидросистема транспортера; 9 - смесительный барабан; 10 - пульт управления смесительным барабаном и раздаточным транспортером; 11 - поворотная колонка транспортера
Крановый способ наиболее широко применяется для подачи бетонной смеси в блоки бетонирования. Общая транспортная схема выглядит следующим образом. Автосамосвалы доставляют бетонную смесь к месту работы кранов, разгружают ее в бадьи, которые затем кранами различных видов подаются в блок. При этом в зависимости от размеров сооружений и их компоновки могут быть применены схемы
срасположением кранов:
-на поверхности земли (рис.20.16, 20.18а);
-на эстакадах (рис.20.17, рис. 20.19);
-на бетонируемых сооружениях (рис.20.20);
-на бортах долины (кабель - крановый) (рис.20.21, рис. 20.22).
338

Рис.20.16. Схема возведения бетонных сооружений кранами, расположенными на поверхности земли: гусеничными (а) и башенными (б):1 – сооружение; 2 – кран; 3 – бадья; 4 – приемная площадка; 5 – опалубка; 6 – хобот; 7 – бункер.
Рис.20.17. Схема возведения бетонных сооружений с размещением кранов на бетоновозных эстакадах:1 – сооружение; 2 – эстакада; 3 – кран; 4 – бадья; 5 – опалубка; 6
– бетонируемый блок
339

Рис. 20.18. Схемы расположения кранов при строительстве русловой ГЭС А – до затопления котлованов, б – после затопления котлованов, 1 – бетоновозные
пути, 2 – бетоновозная автодорога, 3- башенный кран
340

Рис. 20.19. Схема размещения кранов на Саяно-Шушенской ГЭС с башенными кранами КБГС-1000 на самоподъемной эстакаде 1 – арочно-гравитационная плотина, 2 – опоры высокой эстакады, 3 – поднимаемая
платформа высокой эстакады, 4 – кран КБГС-1000, 5 – кран БК-1425, 6 – станционарная эстакада, 7 – площадка для приема бетона
В последнее время, при возведении высоких бетонных плотин со столбчатой разрезкой на блоки бетонирования, получила распространение схема с размещением бетоноукладочных кранов на бетонных сооружениях (рис.20.20). В этой схеме наибольшее применение нашли самоподъемные краны (рис.20.21).
341

Рис. 20.20. Схема возведения бетонных сооружений с поэтапным размещением на них (а,б,в) бетоноукладочных кранов
1 – краны; 2, 3, 4 – возводимые части сооружения на 1, 2, 3 уровнях стоянки крана; 5 – подъезная автодорога; 6 – транспортный тоннель; 7 – площадки расположения крана и движения автотранспорта.
342

Рис. 20.20а. Схема возведения бетонных сооружений с размещением бетоноукладочных кранов на бетонных сооружениях Красноярской ГЭС
а-в – этапы возведения сооружений, г – продольный разрез, 1 – краны КБГС; 2,3,4 – блоки, возводимые соответственно на 1,2,3 этапах; 5 – отверстия для пропуска строительных расходов; 6 – подъемник кранов
343

Рис.20.20.б. Схема самоподъема крана А - соседние бетонируемые столбы (выравниваются по верхней отметке); б - башня
открепляется от портала и опускается на основание, портал крана поднимается выше отметки столбов; в - между столбами прокладываются балки с крановыми рельсами, на которые опускается колеса портала. Башня поднимается в исходное положение и закрепляется с порталом.
1 - соседние бетонируемые столбы; 2 - портал крана; 3 - вертикальный столб крана; 4 - балки с крановыми рельсами
Рис. 20.22. Схема возведения бетонных сооружений с применением кабель-крана: I - башни кабель-крана; 2 - грузовой трос; 3 -грузовая тележка; 4 - транспортный трос; 5 - бадья; 6 -секции плотины; 7 - рельсовые пути; 8 - строительный тоннель для пропуска строительного расхода
344

Рис. 20.23. Схема размещения кабель - крана на Чиркейской ГЭС а – продольный профиль по оси арочной плотины, б – план.
1 – опоры, 2 – разгрузочная площадка, 3 – отверстие для пропуска строительных расходов, 4 – бадья, вместимостью 8 куб.м, 5 – грузовой канат, 6 – блоки бетонирования, 7- подкрановые пути, 8 – водоприемник, 9 – помещения затворов, 10 – границы действия крана, 11арочная плотина, цифры в кружках – очередность бетонирования блоков
Рис. 20.23. Схемы бадей: цилиндрическая бадья (а); бадья камского типа в положении загрузки из самосвала (б) и в транспортном положении (в)
1 - корпус; 2 - затвор; 3 - опорная рама; 4 - подвески; 5 - салазки; 6-автосамосвал; 7 - крюк бетоноукладочного крана
345
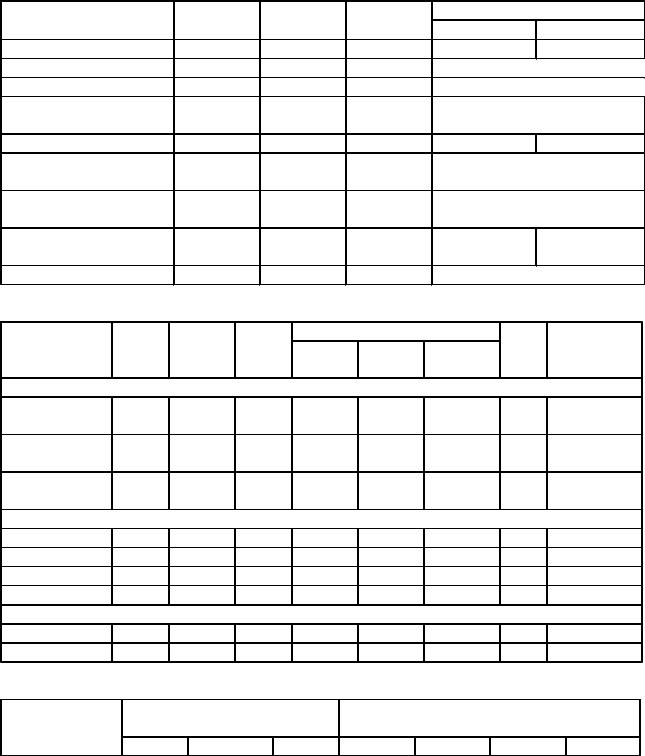
В крупном гидротехническом строительстве для подачи бетонной смеси используют в основном специальные башенные краны типа КБГС (краны башенные для гидротехнического строительства) и кабель-краны, а также башенные и стреловые краны. Технические характеристики некоторых из них даны в табл.20.10 и табл.20.11. Основные применяемые типы бадей приведены на рис. 20.23 и в табл.20.12. При этом следует стремиться к тому, чтобы производительность и грузоподъемность всех элементов в комплексе (бетоносмеситель бетонного завода – горизонтальный автотранспорт – бадья – бетоноукладочный кран) хорошо согласовывались друг с другом и обеспечивали расчетную интенсивность бетонирования.
Таблица 20.10. Некоторые технические характеристики башенных кранов типа КБГС
Показатели |
|
КБГС- |
КБГС-450 |
КБГС- |
|
КБГС 1000А |
|
||||
Вылет крюка, м: |
101М |
|
|
500ХЛ |
Исполнение 1 |
Исполнение2 |
|||||
|
|
|
|
|
|
|
|
|
|||
наибольший |
|
40 |
|
40 |
40 |
|
|
|
40 |
|
|
наименьший |
|
6,7 |
|
7,0 |
6,0 |
|
|
|
6,0 |
|
|
при |
наибольшей |
18 |
|
18 |
- |
|
|
|
20 |
|
|
грузоподъемности |
|
|
|
|
|
|
|
|
|
||
Грузоподъемность, т: |
|
|
|
|
|
|
|
|
|
||
при |
наибольшем |
10,0 |
10,0 |
12,0 |
|
|
|
25,0 |
|
||
вылете |
|
|
|
|
|
|
|
|
|
|
|
при |
наименьшем |
25,0 |
25,0 |
25,0 |
|
|
|
50,0 |
|
||
вылете |
|
|
|
|
|
|
|
|
|
|
|
Высота |
|
подъема |
45,0 |
45,0 |
45,0 |
|
33,5 |
|
18,5 |
||
крюка, м |
|
|
|
|
|
|
|
|
|
|
|
Колея, м |
|
|
10,0 |
10,0 |
10,0 |
|
|
|
11,6 |
|
|
Таблица 20.11. Характеристики отечественных кабель-кранов |
|
|
|
|
|||||||
Тип крана |
|
Грузоп |
Пролет, Высота |
Скорость движения, м/мин |
Бадья, Производит |
||||||
|
|
одъем |
м |
башен, |
тележки подъема |
опускания м³ |
ельность |
||||
|
|
ность |
|
м |
|
|
|
|
|
|
|
|
|
|
|
Эллинговые |
|
|
|
|
|
||
Красноярски |
25 |
1100 |
До 95 |
360-600 |
90-120 |
120 |
|
8,0 |
13-15 |
|
|
й |
|
|
|
|
|
|
|
|
|
циклов/ч |
|
Ингурский |
25 |
954 |
|
То же |
75-150 |
135-150 |
8,0 |
8-11 |
|
||
|
|
|
|
|
|
|
|
|
|
циклов/ч |
|
Чиркейский |
25 |
500 |
40 |
330-400 |
90-150 |
90-150 |
8,0 |
17,7-23,2 тыс. |
|||
|
|
|
|
Параллельно-передвижные |
|
|
|
м³/мес |
|
||
|
|
|
|
|
|
|
|
|
|||
|
|
7,5 |
320 |
40/30 |
280 |
40 |
- |
|
2,0 |
- |
|
|
|
10 |
450 |
27/15 |
320 |
40 |
- |
|
3,21 |
- |
|
|
|
15 |
575 |
69/69 |
360 |
35 |
- |
|
4,0 |
- |
|
|
|
|
500 |
50/50 |
240 |
35 |
- |
|
6,4 |
- |
|
|
|
|
|
Радиальные |
|
|
|
|
|
||
|
|
7,5 |
500 |
87/67 |
320 |
- |
- |
|
2,0 |
- |
|
|
|
10 |
230 |
20/- |
360 |
90 |
- |
|
3,2 |
- |
|
Таблица 20.12. Техническая характеристика бадей |
|
|
|
|
|
||||||
Параметры |
|
Цилиндрические бадьи |
|
Опрокидные |
(ковшовые) |
бадьи |
|||||
|
|
|
|
|
|
емкостью, м³ |
|
|
|
|
|
|
|
БГ-8 |
БГРУ-6,4 Т-103 |
8,0 |
6,4 |
|
3,2 |
1,6 |
|
346
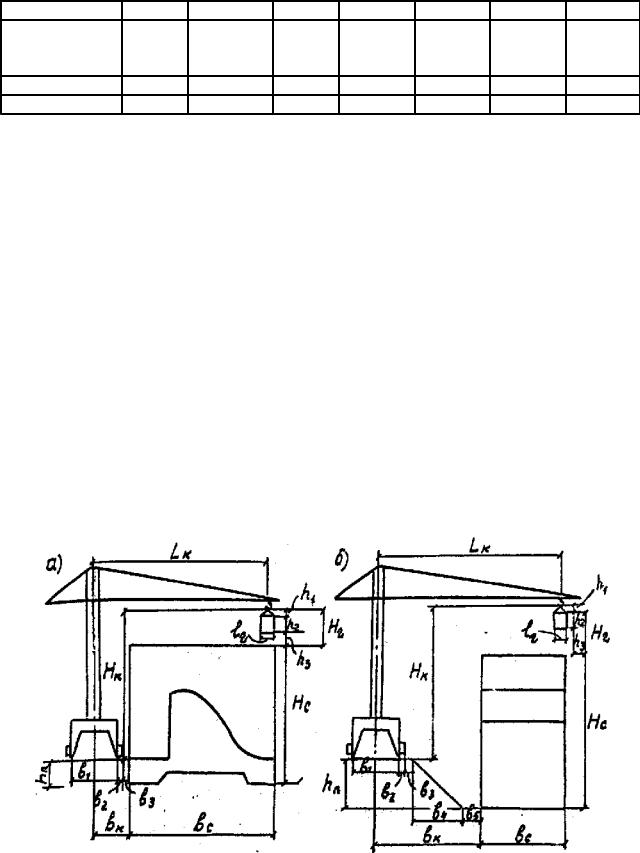
Емкость, м³ |
8,0 |
6,4 |
3,2 |
8,0 |
6,4 |
3,2 |
1,6 |
Высота, мм: |
|
|
|
|
|
|
|
С траверсой |
5406 |
5150 |
3545 |
5800 |
5660 |
5000 |
4000 |
Без траверсы |
4264 |
3350 |
2240 |
4030 |
4340 |
4000 |
3250 |
Масса бадьи, т |
4778 |
3300 |
1697 |
2850 |
2782 |
9000 |
5350 |
То же с бетоном |
24000 |
18700 |
8000 |
20050 |
18150 |
9000 |
5350 |
20.3. Выбор кранов
Выбор кранов производят в два этапа. На первом этапа устанавливают техническую возможность использования крана данной размерной группы. На втором выполняют технико-экономический расчет и определяют экономическую целесообразность применения крана данного типоразмера и марки.
Исходные данные для выбора крана на I этапе:
-габариты и конфигурация сооружений (подземных и надземных частей);
-параметры блоков бетонирования и монтируемых в них конструкций (геометрические размеры, масса).
-условия доставки бетонной смеси (и иных грузов) и ее перегрузки
-тип горизонтального транспорта, его грузоподъемность и объем бетонной смеси;
-тип бадьи и ее масса;
-тип горизонтального транспорта других грузов;
-условия производства работ на площадке (степень сосредоточенности сооружений, грунтово-климатические условия, места складирования грузов и др.).
Для определения необходимых параметров кранов составляют графическую схему рабочей зоны при возведении конкретных сооружений (рис. 20.24, 20.25). Затем
рассчитывают требуемые высоту подъема крюка Н К и вылет крюка LK , а также грузоподъемность выбранного крана на требуемом вылете крюка Q .
Рис.20.24. Определение рабочей зоны и необходимых параметров башенных кранов при их расположении в котловане (а); у бровки котлована (б)
347

Рис. 20.25. Определение рабочей зоны башенных кранов при больших размерах сооружений: I, II – этапы бетонирования и соответствующее расположение кранов; 2 - кран; 3 - эстакада
Рекомендуется следующая последовательность выбора крана. |
|
|||||||
1. |
Определяют |
габаритные |
размеры |
частей |
сооружений, |
возводимых |
||
на разных |
этапах, и |
возможные места |
и отметки |
расположения |
крановых |
|||
путей |
(для |
1 |
этапа |
- в |
котловане |
или на |
бровках котлована, для |
IIэтапа - на эстакадах или на частях сооружений).
2.Рассчитывают требуемую высоту подъема крюка
Н К = НС + Н Г ; Н Г = h1 + h2 + h3 , |
(20.1) |
где: |
|
НС - наибольшая высота бетонируемой части сооружения над уровнем стоянкикрана;
Н Г - условная высота груза;
h1 - высота грузозахватных устройств (колеблется от 2 до 4,5 м);
h2 - высота детали переносимой кранами (бадьи, опалубки, армоконструкций и т.д.);
h3 - запас по высоте по условиям техники безопасности (принимается в пределах
2,5-3,0 м).
3. Находят требуемый вылет крюка. При возведении надземной части сооружения (рис. 20.23,а)
LК = ВК + ВС − 0,5 ВГ |
(20.2) |
Здесь ВК - расстояние от оси вращения поворотной платформы крана до сооружения (условная ширина крана);
ВС - ширина сооружения;
348
ВГ - ширина транспортируемого (монтируемого) груза - ширина бадьи монтажного элемента и т.д.
Величина ВК зависит от конструктивного исполнения крана и размеров рельсового
пути. |
|
Для башенных кранов |
|
ВК = 0,5в1 + в2 + в3 |
(20.2´) |
где в1 - ширина колеи; |
|
в2 - размер выступающей за колею ходовой части; |
|
в3 - величина допустимого приближения крана к сооружению. |
|
Для кранов с поворотными башнями |
|
ВК = RX + в3 |
(20.2) |
Где: |
|
RX - радиус хвостовой части - платформы или противовесной консоли. При возведении подземных частей сооружений (рис. 20.23,6)
ВК = 0,5в1 + в2 + в3 + в4 + в5 |
(20.3) |
где:
в1 и в2 - то же, что в формуле (20.2);
в3 - допустимое приближение крана, к откосу котлована;
в4 - величина заложения откоса котлована;
в5 - расстояние от откоса котлована до сооружения.
4. Определяют требуемую грузоподъемность |
крана QK с учетом массы |
транспортируемых грузов и грузозахватных устройств: |
|
QK ³ QГ К Н , |
(20.4) |
где: QK - наибольшая масса транспортируемого груза;
KН - коэффициент, учитывающий массу грузозахватных устройств и возможное от-
клонение массы транспортируемого элемента от проектной (К= 1,08-1,12).
При использовании крана для подачи бетонной смеси грузоподъемность крана должна быть увязана с грузоподъемностью горизонтального автотранспорта и емкостью бадьи для бетонной смеси. Объем бадьи должен быть равен объему бетонной смеси, доставляемой одним автосамосвалом. В отдельных случаях допускается разгрузка двух автосамосвалов в одну бадью. В свою очередь объем бетонной смеси в автосамосвале должен быть кратным объему готовой смеси, выдаваемой бетоносмесителем бетонного завода; тогда
QK = (QC + QБ) К Н ; QC =V C γ C |
(20.4´) |
349

где: QC - масса бетонной смеси;
QБ - масса бадьи;
V C - объем смеси;
γC - плотность смеси.
5.По имеющейся номенклатуре кранов выбирают наиболее подходящий по грузоподъемности и назначению и проверяют соответствие его характеристик требуемым
QK H K . По грузовой характеристике крана проверяют соответствие вылета крюка
требуемой высоте подъема крюка. Для кранов с балочной стрелой высота подъема не зависит от вылета крюка. При отсутствии грузовой характеристики проверку производят по грузовому моменту:
QK LK ≤ M K
где Mк - грузовой момент крана для данного типоразмера.
Существенное значение при выборе крана имеют скоростные характеристики кранов - скорости подъема, опускания грузов, передвижения тележки. Для подачи бетонной смеси в блоки должны применяться высокоскоростные краны, для монтажных работ - низкоскоростные.
6.Для выбранного крана уточняют схему размещения, область охвата и составляют расчетную схему для определения производительности крана (рис. 20.26).
Рис. 20.26. Расчетная схема к определению производительности башенного (а) и гусеничного крана (б)
1 - бетонируемая часть сооружения; 2 - расчетный блок; 3 -положение бадьи при загрузке; 4 - положение бадьи при переносе (опускании)
20.5. Определение производительности кранов
Краны относятся к машинам цикличного действия, поэтому, согласно общему подходу (глава 7), техническая производительность:
ПТ = qЦ nЦ = QГ nЦ = QK K З nЦ |
(20.5) |
где: |
|
350
qЦ = QГ - фактическая масса транспортируемого груза за один цикл, т; |
|
|||
QK - грузоподъемность крана, т; |
|
|
|
|
КЗ = QГ / QK - |
коэффициент |
использования |
грузоподъемности |
крана |
(коэффициент загрузки); |
|
|
|
|
nЦ = 3600 /tЦ - |
количество циклов |
в час (при определении времени-цикла в |
||
секундах); |
|
|
|
|
tЦ - время одного цикла, с, |
|
|
|
|
tЦ = tЗ + (tПД + tПВ + tТ + tО) KC + tР + (t'ПД + t'ПВ + tТ' + tО' ) КC' + tM |
(20.5’) |
|||
где: |
|
|
|
|
tЗ - время загрузки бадьи; |
|
|
|
tПД - время подъема бадьи (груза) до уровня переноса;
tПВ - время поворота стрелы крана;
tТ - время перемещения грузовой тележки по стреле крана;
tO - время опускания бадьи (груза) до уровня разгрузки (монтажа);
tР - время разгрузки бадьи (закрепления при монтаже);
t'ПД - время подъема бадьи без смеси (крюка без груза);
t'ПВ - время поворота бадьи без смеси (крюка без груза);
tТ' - время перемещения грузовой тележки без груза;
tO' - время опускания бадьи без смеси;
tM - время маневрирования крана при установке бадьи для последующей загрузки;
' |
|
|
KC , KC |
- коэффициенты совмещения операций |
в груженом состоянии и в |
порожнем. |
|
|
Эксплуатационная часовая производительность: |
|
|
ПЭ = ПТ К В , |
(20.6) |
|
где: |
|
|
К В - коэффициент использования внутрисменного рабочего времени, зависящий от типа крана и периодов строительства (0,8-0,9).
Эксплуатационная сменная и месячная производительность: |
|
ПСМ = ПЭТЧ ; ПМЕС = ПСМ ТСМ , |
(20.7) |
где Тч, Тсм - расчетное число рабочих часов в смену и рабочих смен в месяц, определяемое по годовому режиму работы.
По данным института "Гидропроект" расчетное число рабочих смен кранов при различных режимах работы может быть принято по табл. 20.13.
351

Расчетное количество кранов для укладки бетона
NКР |
= |
J МЕС qС |
(20.8) |
|
|
ПМЕС |
|
|
|
|
Производительность и количество кранов, определенные для нормального расчетного режима работы кранов, должны быть проверены на удовлетворение максимальной (пиковой) месячной интенсивности бетонных работ при форсированном режиме:
|
|
N макс кр = |
J макс |
|
|
|
|
|
|
|
||
Псммакс = ПсмТсммакс ; |
|
мес |
|
|
|
|
|
|
|
|||
|
Пмаксмес |
. |
|
|
(20.9) |
|
||||||
Таблица 20.13. Расчетное число рабочих смен кранов на укладке бетонной смеси |
||||||||||||
|
|
Тип |
|
|
|
|
Климатические зоны |
|
||||
Режим |
Период |
кранов |
|
|
|
|
I |
П |
III |
1V |
V |
V1 |
Расчетный |
Летний (пиковый |
Башенные |
|
|
66 |
66 |
64 |
64 |
61 |
52 |
||
|
год), см/мес |
Гусеничные |
|
68 |
67 |
67 |
66 |
65 |
61 |
|||
|
|
Кабельные |
|
|
68 |
68 |
66 |
66 |
62 |
54 |
||
|
Зимний (пиковый |
Башенные |
|
|
59 |
56 |
51 |
51 |
46 |
36 |
||
|
год), см/год |
Гусеничные |
|
61 |
57 |
54 |
53 |
49 |
43 |
|||
|
|
|
||||||||||
|
|
Кабельные |
|
|
61 |
58 |
53 |
53 |
46 |
38 |
||
|
Расчетное число |
Башенные |
|
|
771 |
742 |
690 |
677 |
627 |
496 |
||
|
рабочих смен кранов |
Гусеничные |
|
795 |
754 |
726 |
701 |
668 |
588 - |
|||
|
в год |
|
|
|
|
|
|
|
|
|
|
|
|
|
Кабельные |
|
|
795 |
766 |
714 |
701 |
632 |
520 |
||
Форсиро- |
Летний (пиковый |
Башенные |
|
|
82,5 |
81,0 |
79,5 |
79,0 |
78 |
75 |
||
ванный |
год), см/мес |
Гусеничные |
|
82,5 |
81,0 |
81,0 |
81,0 |
79,5 |
78,0 |
|||
|
|
|
||||||||||
|
|
Кабельные |
|
81,0 |
79,5 |
78,0 |
78,0 |
76,5 |
73,5 |
|||
|
|
|
|
|
|
|
|
|
|
|
|
|
20.6. Определение комплексной производительности кранов
Бетоноукладочные краны часто выполняют весь комплекс работ по бетонированию сооружений, включающий помимо собственно подачи бетонной смеси, работы по подаче, установке и снятию опалубки, подаче и монтажу арматуры, металлоконструкций, закладных деталей, средств утепления блока в зимний период и т.п.
При выполнении этих вспомогательных работ кран, как правило, используется неэффективно как по грузоподъемности, так и по времени, поэтому целесообразно использовать основной кран в комплексе с переносным вспомогательным краном. В этом случае основной объем вспомогательных работ - установка и снятие опалубки, монтаж легких армоконструкций и закладных деталей и т.п. - выполняется вспомогательным краном, а основной бетоноукладочный кран осуществляет подачу бетонной смеси, переносит вспомогательный кран из блока в блок и подает к нему грузы. С целью уменьшения занятости основного крана целесообразно осуществлять их контейнеризацию, т.е. собирать грузы (вспомогательные материалы и оборудование) в
352
специальные контейнеры, подаваемые бетоноукладочными кранами в блок, в зону действия вспомогательных кранов.
Как показывает практика, при выполнении основным бетоноукладочным краном всего комплекса бетонных работ занятость его на вспомогательных операциях составляет 3040% от всего времени работы крана. При использовании вспомогательных кранов занятость его на вспомогательных операциях уменьшается до 10-15%. Однако как в том, так и в другом случае основной бетоноукладочный кран принимает участие в доставке вспомогательных грузов и материалов, поэтому при расчете потребности в бетоноукладочных кранах должна быть определена не просто производительность только на укладке бетона, а комплексная производительность крана с учетом его занятости на вспомогательных операциях. С этой целью должны быть определены объемы вспомогательных работ, единичные массы всех подаваемых грузов, продолжительность циклов на каждом виде работ, сменная производительность и соответствующая потребность в машино - сменах основного крана.
Рекомендуется следующая последовательность расчетов.
1.Определяются объемы работ для обеспечения расчетной месячной интенсивности работ.
Объем V C (м3/мес) и масса QC (т/мес) бетонной смеси
V C = J МЕС qC ; |
QC =V C γ C |
(20.10) |
|
|
где J МЕС - расчетная месячная интенсивность бетонных |
работ; |
γС - плотность |
||
бетонной смеси. |
|
|
|
|
Масса арматурных конструкций |
|
|
|
|
Qa = J МЕС qa , |
|
(20.11) |
|
|
где qa - расход арматуры |
на 1м3 бетона |
в зависимости |
от типа |
и конструкции |
сооружения. |
|
|
|
|
Площадь FO (м2/мес) и масса QO (т/мес) опалубочных щитов |
|
|||
FO = J МЕС qO ; |
QO = FOγ O , |
(20.11) |
|
|
где qO - площадь опалубки, приходящаяся на 1 м3 бетона; γ O - удельный вес 1м2 опалубки, т/м2.
2.Определяются полезные массы грузов, передаваемых за один цикл, и коэффициенты использования грузоподъемности (коэффициенты загрузки).
Масса бетонной смеси Q1 =V Б γ C |
; K3.1 |
= |
Q1 |
(20.12) |
|
|
QК |
|
|||||
|
|
|
Q2 |
|
||
Масса пакета опалубочных щитов Q2 = f O γ O n ; K3.2 = |
(20.13) |
|||||
QК |
||||||
|
|
|
|
|
где f O - площадь одного щита опалубки; n - количество щитов опалубки в пакете;
V б - объем бетонной смеси, загружаемый в бадью и передаваемый за один цикл. Масса пакета арматуры или арматурных конструкций
353

Q3 |
= Pа n ; K3.3 = |
Q3 |
(20.13) |
QК |
|||
где |
Pа - масса одной арматурной конструкции; n - количество армоконструкций в |
пакете.
3.Составляются технологические схемы подачи бетонной смеси и различных
вспомогательных грузов со строительной площадки расчетный блок бетонируемой в данный период части сооружения, определяются необходимые данные для расчета продолжительности цикла для каждого из видов грузов.
4.Составляется циклограмма работ на выполнение всех операций комплекса бетонных работ (подача и установка пространственных и плоских армоконструкций, щитов опалубки, шатров, вспомогательного оборудования и прочих грузов). При определении циклов на выполнение этих работ к операциям, рассмотренным при подаче бетона, вместо операции разгрузки добавляется операция по монтажу.
5.Определяется эксплуатационная сменная производительность и потребность в машино – сменах на выполнение расчетного объема работ при нормальном режиме работы (табл. 20.14 )
Таблица 20.14. Расчет потребности в машино-сменах |
|
|
|
|
|
|
|
|||||
Вид работ |
Рас |
Объем |
Число |
Число |
Сменная |
|
|
Общая |
||||
|
чет |
работ |
цикло |
рабоч |
производительность, |
потребность в |
||||||
|
ный |
за 1 |
в в час |
их |
ПСМ |
|
|
машино-сменах, М |
||||
|
объ |
цикл |
|
часов |
|
|
|
|
|
|
|
|
|
ем |
|
|
в |
|
|
|
|
|
|
|
|
|
раб |
|
|
смену |
|
|
|
|
|
|
|
|
|
от, |
|
|
|
|
|
|
|
|
|
|
|
|
т/ме |
|
|
|
|
|
|
|
|
|
|
|
|
с |
|
|
|
|
|
|
|
|
|
|
|
1 |
2 |
3 |
4 |
5 |
6 |
|
|
|
|
7 |
|
|
Укладка |
QC |
Q1 |
Ц1 |
ТЧ |
ПСМ 1 = Q1 |
Ц1 |
К |
|
|
|
QC |
|
бетонной |
М1 |
= |
|
|||||||||
смеси |
|
|
|
|
|
|
|
|
|
|
||
|
|
|
|
|
|
|
|
ПСМ .1 |
||||
|
|
|
|
|
|
|
|
|
|
|
||
армокаркасУстановка |
Qa |
Q2 |
Ц 2 |
ТЧ |
ПСМ 2 =Q2 |
Ц 2 |
К |
М 2 |
= |
|
QC |
|
ов |
|
|
|
|
|
|
|
|
|
|
||
|
|
|
|
|
|
|
|
ПСМ .2 |
||||
(армосеток |
|
|
|
|
|
|
|
|
|
|
||
) |
|
|
|
|
|
|
|
|
|
|
|
|
Установка |
QO |
Q3 |
Ц 3 |
ТЧ |
ПСМ 3 =Q3 |
Ц 3 |
К |
|
|
|
QC |
|
опалубки |
М 3 |
= |
|
|||||||||
|
|
|
|
|
|
|
|
|
ПСМ .1 |
|||
|
|
|
|
|
|
|
|
|
|
|
||
Комплекс |
QC |
|
|
|
å М = α (М1 + М 2 + М 3) |
|||||||
работ |
|
|
|
|||||||||
|
+ |
|
|
|
|
|
|
|
|
|
|
|
|
Qa |
|
|
|
|
|
|
где α =1.05-1.1- |
||||
|
+ |
|
|
|
|
|
|
коэффициент |
||||
|
|
|
|
|
|
|
на неучтенные |
|||||
|
QO |
|
|
|
|
|
|
|||||
|
|
|
|
|
|
|
(прочие) работы |
|||||
|
|
|
|
|
|
|
|
|
|
|
|
|
354

+
QП
6.Определяется сменная комплексная производительность крана ПСМ .К м3/см
ПСМ .К = V C å М |
(20.14) |
7.Рассчитывается месячная комплексная производительность ПМЕС.К , м3/месс
|
|
ПМЕС.К = ПСМ .К ТСМ |
(20.15) |
|
где TСМ - расчетное число машино – смен крана в месяц (табл.20.13). |
||||
8. Определяется необходимое количество кранов |
|
|||
NКР |
= |
QКР |
ПМЕС.К |
(20.16) |
|
|
|||
|
|
|
|
355

ГЛАВА 21. Подготовка блоков к бетонированию. Укладка и уплотнение бетонной смеси
21.1. Состав мероприятий по подготовке блоков к бетонированию
До укладки бетонной смеси в блоки последние долины быть соответствующим образом подготовлены для приема смеси. В общем случае мероприятия по подготовке блоков имеют своей целью обеспечить условия для нормального ведения бетонных работ в блоке и для набора бетоном и конструкцией проектной прочности, включая получение прочного и плотного сцепления свежеуложенной смеси с ранее уложенным бетоном или с естественным основанием.
Эти мероприятия могут быть подразделены на следующие группы:
-установка требуемого типа опалубки и заделка щелей;
-установка и зачистка проектных арматурных конструкций;
-установка арматуры и аппаратуры для регулирования температурного режима и омоноличивания швов - при необходимости (трубы охлаждения, цементационная арматура и др.);
-установка закладных частей для различного оборудования;
-установка контрольно-измерительной аппаратуры;
-подготовка площадок и оборудования для приема бетонной смеси;
-подготовка поверхностей оснований блоков;
-приемка блоков к бетонированию;
-проверка готовности всего тракта приготовления - транспорта и подачи бетонной смеси в блок и их соответствия проектным условиям.
В зимний период дополнительно добавляется группа мероприятий по установке тепляков или шатров и поддержанию в них необходимого температурного режима.
Каждая группа мероприятий имеет свой набор работ, обеспечивающих в итоге нормальный ход бетонных работ и требуемые качества бетона и бетонных конструкций.
Установка (монтаж) типа арматурных конструкций и опалубки осуществляется на основе чертежей и схем армирования и схем опалубки блоков. Для этого на основе принципиальных схем армирования и опалубливания данного сооружения или элемента (см.гл. 17) в составе проектов производства работ (ППР) составляется схемы армирования
иопалубливания отдельных блоков с учетом конкретной конструкций блока (рис. 21.I - 21.3). Детальные схемы составляются и для других перечисленных мероприятий (рис. 21.4).
Рис. 21.1. Принципиальная конструктивная схема блока: а - схема плотины и положение блока, б - конструктивная схема блока
1 - галерея; 2 - штрабы в межстолбчатом шве; 3 - металлические уплотнения; 4 - битумная шпонка; 5 - металлические уплотнения горизонтальных межблочных швов
356

Рис. 21.2. Принципиальная схема опалубливания блока. Опалубка: ОК - консольная, ОС - стационарная, Ощ - щитовая, Ож/б - опалубка железобетонная
Рис. 21.3. Принципиальная схема армирования блока
I - арматурные сетки напорной грани; 2 - арматурные сетки галереи; 3 - поддерживающие конструкции в виде ферм
357
Рис. 21.4. Принципиальная схема цементационной арматуры для цементации межстолбчатого шва
1 - трубы разводящей системы; 2 - выпуски (клапаны); 3 - металлические уплотнения; 4 - воздухостводящая штраба; 5 -штрабы в межстолбчатых швах
Особое место в перечисленном комплексе работ занимает подготовка поверхности оснований. При этом основанием блоков могут быть естественные породы (скальные, мягкие) и ранее уложенный бетон. Готовый к бетонированию блок сдается комиссии по приемке блоков с составлением соответствующих актов и схем. При приемке блоков к бетонированию комиссия проверяет выполнение всех перечисленных выше мероприятий.
21.2. Подготовка оснований блоков
Подготовка естественных оснований заключается в обеспечении требуемых условий для получения в контактном слое требуемых прочностных и противофильтрационных свойств. Характер и состав работ зависят от типа оснований - скальные или мягкие грунты.
При наличии скальных оснований предусматриваются следующие операции: разработка защитного слоя; удаление всех продуктов выветривания (рыхлой скалы, бухтящих кусков); отвод ключей грунтовых напорных вод; очистка, промывка, продувка воздухом; сдача комиссии по приемке блока к бетонированию с составлением акта и геологической схемы основания.
При наличии мягких оснований предусматриваются: разработка защитного слоя; удаление илистых грунтов и грунтов органического происхождения; замена непригодных по физико-механическим свойствам грунтов песком и его уплотнение; сдача основания комиссии с составлением акта и геологической схемы; устройство бетонной подготовки - 5-10 см; очистка, промывка, продувка бетонной подготовки; сдача блока комиссии с составлением акта.
Подготовка поверхности ранее уложенного бетона должна предусматривать: удаление опалубки, штраб, пробок, и других деревянных закладных частей; удаление наплывов, раковин (до здорового бетона); удаление пятен мазута, нефти, битума; удаление цементной пленки; очистку от мусора; окончательную промывку струей воды под напором и продувку сжатым воздухом.
Цементная пленка удаляется различными способами в зависимости от возраста бетона в основании: в возрасте бетона 6-12 ч - водяной или воздушной струей под давлением 0,4-0,5 МПа; в возрасте бетона 8-20 ч - металлическими механическими щетками; в возрасте бетона более 3 сут - с применением гидропескоструйного аппарата.
Разрешается не удалять цементную пленку для внутренних зон гравитационных плотин при условии укладки в этой зоне бетонной смеси с осадкой конуса меньше 5 см (или жесткого малоцементного бетона) и укладки со стороны напорной и низовой грани плотного бетона.
21.3. Уплотнение бетонной смеси
Укладываемая в бетонируемую конструкцию бетонная смесь в начальном состоянии не полностью заполняет форму, имеет рыхлую структуру с высокой пористостью и большим объемом вовлеченного воздуха, что без дополнительной обработки ведет к снижению качества бетона в частности его прочности и внешнего вида - появлению каверн. Поэтому бетонная смесь в блоке должна подвергаться дополнительной обработке с целью повышения плотности и полного заполнения формы. Это достигается путем введения технологической операции, называемой уплотнением. Таким образом, уплотнение бетонной смеси является одним из основных технологических процессов при бетонировании конструкций, в значительной мере определяющим качество уложенного бетона.
358

Известны следующие способы уплотнения бетонной смеси: ручное трамбование; механическое трамбование; вибрирование; вибровакуумирование; центрифугирование; самоуплотнение. Применение тех или иных способов уплотнения зависит от подвижности бетонной смеси и типа конструкций. В табл. 21.1 приведены принципиальные рекомендуемые способы уплотнения в зависимости от пластичности (0К) и содержания воды в смеси.
Таблица 21.1 Рекомендуемые способы уплотнения в зависимости от пластичности бетонных смесей
Наименование |
Осадка |
Содержание воды в |
Способ уплотнения |
|
смеси |
конуса, |
смеси, л/м³ |
|
|
|
см |
на гравии |
на щебне |
|
|
|
|
|
|
Жесткие |
- |
120-130 |
130-140 |
Механическое трамбование и |
|
|
|
|
вибрирование с пригрузом |
Малопластичные |
1-3 |
130-145 |
145-155 |
Вибрирование |
Среднепластичные |
3-6 |
145-160 |
155-170 |
Вибровакуумирование |
Высокопластичные |
6-12 |
160-185 |
175-200 |
Центрифугирование, штыкование |
Литые |
14-16 |
220 |
240 |
Самоуплотнение |
Поскольку в гидротехническом строительстве для возведения массивных бетонных сооружений применяются в основном жесткие и малопластичные бетонные смеси, то основным методом уплотнения при возведении таких конструкций является виброуплотнение.
Виброуплотнение заключается в передаче бетонной смеси механических колебаний от источника этих колебании - вибратора. Процесс виброуплотнения сводится к разрушению первоначальной структуры укладываемой смеси (трехфазной) и в переводе ее в разжиженное состояние (пластично-вязкое течение), при которой смесь подчиняется действию силы тяжести, растекается, занимая всю возможную форму, уплотняется и приобретает более устойчивую, плотную (приближающуюся к двухфазной) структуру. При этом зерна заполнителя перемещаются в результате чего достигается заполнение межзернового пространства цементным тестом с одновременным вытеснением воздуха, отделением части воды на поверхность уплотняемой смеси. Таким образом, вибрирование позволяет уменьшить содержание воздуха (рис. 21.6) и расход воды для приготовления бетонной смеси, а следовательно, повысить плотность и прочность бетона (рис. 21.7).
Рис.21.6.Влияние продолжительности |
|
Рис.21.7. Влияние продолжительности |
359

вибрирования |
смеси |
на |
потерю |
|
вибрирования смеси на прочность и |
вовлеченного |
воздуха |
|
(крупность |
|
плотность бетона: 1 – теоретический |
заполнителя до 40 мм, В/Ц=0,53; |
|
бетон (без пустот); 2 – бетон, |
|||
содержание |
добавок |
|
различное): |
|
уплотнявшийся вибрированием; 3 – |
1 – ОК=1,5 см; 2 – ОК=2 см; 3 – ОК=3 см. |
|
бетон, уплотнявшийся штыкованием. |
Улучшается не только механическая прочность бетона, но и его морозостойкость, водонепроницаемость и стойкость к агрессивным средам. Эффективность и степень уплотнения зависят от таких факторов, как амплитуда колебаний, частота колебаний и длительность вибрирования. В принципе, чем выше частота колебаний, тем эффективнее идет процесс уплотнения и тем меньше продолжительность уплотнения (рис. 21.8). Однако очевидно, что каждой крупности зерна соответствует собственная частота колебаний, поэтому наибольший эффект обеспечивается при поличастотном вибрировании ,когда в резонанс вовлекаются все зерна смеси. Но конструктивное решение поличастотных вибраторов довольно сложно. Поэтому режим вибрирования рассчитывается на средний размер частиц заполнителя. Оптимальные амплитуды колебаний вибраторов зависят не только от размера частиц, но и от подвижности смеси. Для смесей с крупным заполнителем, а также малоподвижных и жестких смесей необходима более низкая частота колебаний с большой амплитудой (до 0,7 мм). Для смесей с мелким заполнителем и подвижных эффективнее более высокая частота с меньшей амплитудой (0,15-0,40 мм).
Рис. 21.8. Зависимость между продолжительностью и частотой вибрирования
По способу воздействия на бетонную смесь вибраторы подразделяются на: глубинные, поверхностные, наружные, виброплощадки (вибростенды) (рис. 21.9) .
Глубинные вибраторы для уплотнения погружаются в бетонную смесь и передают колебания вибронаконечником или корпусом (рис.21.10). Это наиболее распространенные вибраторы для уплотнения бетонной смеси в армированных и неармированных блоках массивных сооружений (в частности, гидротехнических). фундаментах, колоннах.
Поверхностные вибраторы устанавливается на уложенную бетонную смесь и переда ют колебания с поверхности через рабочую площадку. Они действует на глубину 10-20 см. Применяются при бетонировании плит, панелей, дорожных и аэродромных покрытий.
360

Рис.21.9. Типы вибраторов: глубинные (а), наружные (б), поверхностные (в), вибростенд (г): 1 – бетонная смесь, 2- опалубка, 3 – корпус вибратора.
Рис.21.10 Глубинный вибратор: ИВ-59 1 – корпус, 2 – амортизатор, 3 – штанга, 4 – выключатель, 5 – электрокабель, 6 –
верхняя рукоять.
Наружные вибраторы прикрепляются к опалубке или другим устройствам и передают колебания через опалубку. Глубина уплотнения смеси 10-20 см. Применяются для уплотнения при бетонировании тонких элементов с повышенной густотой армирования, а также для побуждения выгрузки, бетонной смеси из бункеров, бадей, автосамосвалов.
Виброплощадки (вибростенды) применяют главным образом при изготовлении сборных элементов в заводских условиях.
Наиболее распространенными вибраторами для уплотнения смесей при бетонировании массивных гидротехнических сооружений являются глубинные. Глубинные вибраторы наиболее просты, экономичны и эффективны. Они представляют собой вибробулавы или виброиглы длиной 40-80 см и диаметром 18-150 см (наиболее распространены вибраторы длиной 60-80 см) (табл. 20.2). В мировой практике частота колебаний этих вибраторов с годами непрерывно увеличивается с целью привести в движение все более мелкие частицы смеси (6000 кол/мин в 1940 г., 10000 кол/мин в 1955 г. и 20000 кол/мин в настоящее время). Колебания низких частот воздействуют на крупные частицы, высоких - на более мелкие.
361

Таблица 20.2. Технические характеристики некоторых вибраторов.
Тип |
Частота |
Вибро- |
|
Предельная |
Ориентировочная |
|
наконечники |
Масса, |
толщина слоя |
техническая |
|||
вибратора. |
колебаний |
|||||
диаметр/длина |
кг |
бетонирования |
производительность, |
|||
Марка |
кол./мин. |
мм |
|
см |
м3 |
|
|
|
|
|
|
|
|
Ручные |
|
|
|
|
|
|
ИВ-59 |
5700 |
114/520 |
22 |
50 |
12-16 |
|
ИВ-60 |
5700 |
133/520 |
30 |
50 |
до 18 |
|
ИВ-79 |
11000 |
75/500 |
15 |
50 |
|
|
ИВ-80 |
11000 |
100/510 |
22 |
50 |
|
|
Подвесные |
|
|
|
|
|
|
ИВ-34 |
8000 |
133/750 |
130 |
75 |
18-25 |
|
ИВ-90 |
8000 |
130/1140 |
132 |
100 |
18-25 |
|
В-1-697 |
2910 |
194/1600 |
250 |
150 |
20-30 |
Радиус действия вибраторов, определяющий размер зоны уплотнения смеси, зависит от частоты колебаний и диаметра вибратора. Для ручных вибраторов он невелик и составляет 25-35 см. Радиус действия вибратора легко определить экспериментально. Для этого достаточно поместить в бетонную смесь стержни диаметром 20 мм длиной, равной длине вибратора, на все более увеличивающемся расстоянии от вибратора. После 1 мин вибрирования все стержни в радиусе действия полностью погрузятся в смесь, вне радиуса действия - частично.
При работе с вибраторами рекомендуется соблюдать следующие правила.
Погружать вибратор в смесь следует вертикально. При этом конец вибронаконечника углубляют в ранее уложенный (но не схватившийся) слой на глубину около 5 см. Этим обеспечивается совместное вибрирование контактного слоя ранее уложенного и уплотняемого слоя и стирание границы между слоями.
Толщина слоя вибрирования должна соответствовать длине рабочей части вибратора и при ручном вибрировании не должна превышать 50 см. Шаг перестановки вибраторов не должен превышать 0,5 радиуса его действия и зависит от толщины слоя, подвижности смеси, крупности заполнителя, вида применяемого цемента и добавок. Поэтому в каждом случае радиус действия следует уточнять на месте.
Лучше вибрировать смесь короткими "рывками" в точках, как мокло ближе расположенных друг к другу, чем длинными в более отдаленных друг от друга точках.
Извлекать вибратор следует медленно, так как иначе образуются впадины, которые заполняются цементным молоком.
Не следует вибрировать смесь, расположенную ближе 10 см от поверхности опалубки. Продолжительность вибрирования зависит от многих факторов, в частности от частоты колебаний (рис. 21.8). Она сокращается с повышением частоты, подвижности смеси, увеличением количества мелких фракций в смеси, уменьшением массы бетона, а также с повышением густоты армирования. Для отечественных ручных вибраторов она в
среднем составляет 15-30 с.
362

Рис.21.11. Влияние чрезмерного вибрирования на расслоение бетона: при избытке (а) и при нехватке раствора (б).
Не следует вибрировать смесь слишком долго. Излишняя вибрация может вызвать расслоение смеси в связи с различной плотностью цементного теста, и заполнителя (рис. 21.11). При этом наиболее тяжелые крупные зерна опускаются на дно формы. Расслоение усиливается при недостаточной однородности смеси, а также при перерасходе воды. Введение добавок, особенно воздухововлекающих, позволяет уменьшить это явление. В зависимости от продолжительности вибрирования часть вовлеченного воздуха выделяется из смеси (главным образом крупные пузырьки). Эти потери тем больше, чем выше энергия уплотнения, чем пластичнее смесь и чем дольше проходит вибрирование (рис. 21.6).
Для уплотнения бетонной смеси при возведении крупных гидротехнических сооружений применяют пакеты вибраторов, закрепленные на специальной траверсе. Траверса подвешивается к крюку крана или к концу телескопической подъемной стрелы, установленной на полноповоротной платформе с пневмоколесным или гусеничным шасси (рис. 21.12, рис. 21.12.а). Применение вибропакетов с подвесными глубинными вибраторами позволяет повысить механизацию процесса, качество уплотнения и производительность труда.
Рис. 21.12. Машины для разравнивания и уплотнения бетонной смеси: малогабаритный бульдозер (а): малогабаритный трактор с подвесным пакетом вибраторов (б); механический манипулятор с телескопической стрелой и подвешенным на ней пакетом тяжелых вибраторов (в)
363

Рис. 21.12.а. Манипулятор с телескопической стрелой и пакетом электромеханических вертикальных вибраторов ИВ-90 для уплотнения бетонной смеси на строительстве плотины Саяно-Шушенской ГЭС
Для повышения качества бетона при определенных условиях применяют так называемое повторное вибрирование. Этот метод предусматривает вторичное вибрирование бетона через 1,5-3,0 ч после первого. По исследованиям ряда авторов повторное вибрирование повышает его прочность при сжатии и растяжении в раннем возрасте. По этим исследованиям повторное вибрирование приводит к увеличению плотности смеси за счет уменьшения пор. Оно позволяет снова закрыть волосяные трещины, которые образуются в результате усадки до схватывания.
Однако повторное вибрирование вызывает изменения в кристаллическом теле, которые могут привести к неблагоприятным последствиям для определенных видов цемента и составов бетонной смеси. Считается, что повторное вибрирование нежелательно для смесей с высокой степенью жесткости. И наоборот, оно весьма эффективно для смесей пластичной консистенции. Весьма полезно введение в смесь добавок, выполняющих одновременно воздухововлекающие и пластифицирующие функции. Вибрирование можно повторять как один, так и два, три раза, но в течение непродолжительного времени, составляющего 1/2 и 1/3 времени первого вибрирования. Операция эта требует большой осторожности, необходимы предварительные испытания на строительной площадке.
21.4. Технологические схемы (способы) укладки бетонной смеси в блоки бетонирования
Различают следующие технологические схемы - способы укладки бетонной смеси в блоки бетонирования: укладка последовательными горизонтальными слоями; ступенчатая укладка; укладка однослойными блоками (рис. 21.13) .
Рис. 21.13. Схемы укладки бетонной смеси в блок: последовательными горизонтальными слоями (а); ступенчатая (б); однослойная (в) I - опалубка; 2 - укладываемые слои бетонной смеси, hсл- толщина слоя, Нбл~высота блока
Укладка последовательными горизонтальными слоями заключается в том, что полная высота блока разбивается на несколько слоев, а бетонная смесь укладывается последовательно в каждом из этих слоев. Причем одновременно смесь укладывается только в одном слое на всю площадь блока и только после окончания этого слоя начинается укладка в следующий вышележащий слой. Высота слоя зависит от мощности и типа вибраторов и примерно соответствует длине рабочей части вибратора. При применении ручных вибраторов hсл < 50 см, а при применении пакетов навесных вибраторов - до 100-150 см
364

Разравнивание и уплотнение бетонной смеси в блоке осуществляется механизированными способами с применением электротракторов с бульдозерным отвалом и пакетами вибраторов или манипуляторов с пакетами вибраторов. При малых размерах блоков применяют ручное разравнивание и уплотнение. Краткие технические характеристики малогабаритных тракторов и манипуляторов даны в табл. 21.3.
Таблица 21.3. Технические характеристики малогабаритных тракторов и манипуляторов
В соответствии с общими положениями данной схемы, интенсивность подачи бетонной смеси в блок должна быть достаточна для полного перекрытия предыдущего слоя за время, не превышающее время схватывания, т.е. минимальная
интенсивностьмин подачи бетонной смеси (м³/ч) должна быть:
(21.1)
где |
- предельно допустимое время перекрытия слоев (время схватывания); |
- |
время транспортировки бетонной смеси до блока; - площадь блока, м² ;
толщина слоя, м.
Необходимая интенсивность должна быть обеспечена всеми элементами схемы приготовления, транспорта и подачи бетонной смеси в блок, т.е. производительность бетонного завода, автотранспорта и крана, работающего на данный блок, должна быть выше минимальной интенсивности. В противном случае нужно менять или параметры блока или принимать другую схему укладки. Поэтому эту схему применяют при относительно небольших размерах блоков для столбчатой и ярусной систем разрезки на блоки бетонирования.
Укладка по ступенчатой схеме заключается в том, что при той же разбивке высоты блока на слои, что и в предыдущей схеме, укладка бетонной смеси одновременно производится в два или более слоев. Это позволяет сокращать время перекрытия слоев в соответствующее число раз или увеличивать его плановые размеры. Поэтому эта схема применяется в основном при секционной разрезке длинными блоками и большой площади, а также в тех случаях, что и предыдущая схема, но при недостаточной интенсивности бетонирования. Разравнивание и уплотнение выполняется, как правило, машинами совмещающими одновременно эти функции, в виде пакетов вибраторов, навешенных на манипуляторы или краны. Ширина уступов при механизированной укладке обычно принимается не менее 3-5 м, а число одновременно укладываемых слоев равным двум.
365

Наименьшая интенсивность бетонирования аналогично предыдущему должна быть:
(21.2) где n - число одновременно бетонируемых слоев.
Схема укладки бетонной смеси однослойными блоками состоит в том, что бетонная смесь укладывается одним слоем, т.е. высота слоя равна высоте блока. Схема применяется в основном при секционной разрезке с однослойными длинными блоками большой площади (см. главу 15) и при применении укатанного бетона. При укладке обычного вибрированного бетона "токтогульским" способом толщина слоя соответствует мощности применяемых вибраторов и составляет до 1,5 м. Разравнивание и уплотнение бетонной смеси выполняется при этом, как правило, раздельно: разравнивание - бульдозером, а уплотнение - пакетами вибраторов, навешенных на электротракторы или манипуляторы (рис. 21.14).
Широкое распространение в мировом гидротехническом строительстве получили укатанные бетоны (см. главу 24). По составу эти бетоны отличаются значительно сниженным содержанием цемента (60-120 кг/м³) по сравнению с обычными вибрированными бетонами. Вследствие этого эти бетонные смеси практически не имеют пластичности (ОК = 0) и обладают большой жесткостью, поэтому их часто называют жесткие бетонные смеси. Вследствие большой жесткости технология их укладки приближается к технологии укладки мягких грунтов в качественные насыпи. Так же как и грунты, эти смеси допускают разравнивание бетонных "куч" бульдозерами, уплотнение слоев катками, движение транспорта по свежеуложенным слоям. Толщина слоя составляет 30-50 см в зависимости от состава бетона и мощности техники для уплотнения. Для уплотнения применяют катки, виброкатки с удельным давлением не менее 0,5 МПа. Технические характеристики соответствующих машин приведены в табл. 21.4.
366
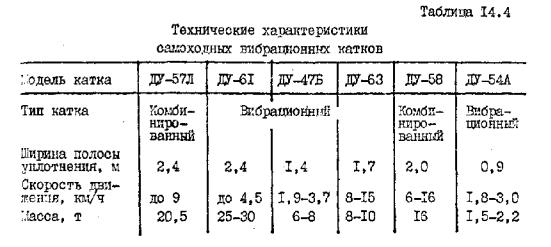
367
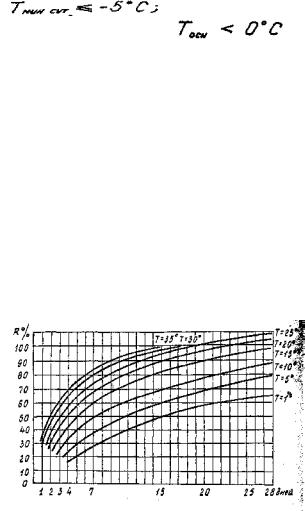
ГЛАВА 22. Особенности производства бетонных работ в зимнее время
22.1. Дополнительные требования
Особые требования к производству бетонных работ предъявляют при наличии одного из следующих условий:
-среднесуточная температура воздуха ниже 0°С
-минимальная температура в течение суток равна или ниже минус 5˚С.
- температура основания ниже 0°С Производство работ и в этот период должно обеспечивать, как и в обычных условиях
нормальный набор прочности, водонепроницаемости, морозостойкости и других свойств бетона в установленные сроки; сохранение монолитности сооружений (отсутствие трещинообразования).
Для этого необходимо выдерживать надлежащий температурный режим и не допускать замораживания бетона до набора им определенной прочности. По нормативам замораживание бетона допускается при наборе не менее 40% его марочной прочности для марок М200 и выше и не менее 50% для более низких марок. Температурный режим в блоках должен обеспечивать ограничение температурных перепадов между ядром и поверхностью блоков при выдерживании бетона в опалубке и между ядром и наружным воздухом при его распалубке. Дополнительные температурные перепады, устанавливаются на основе расчетов по принципам, изложенным в главе 14. Для обеспечения необходимого температурного режима в блоках обычно применяется теплая опалубка.
Рис. 22.1. График твердения бетона на портландцементе. Т - температура бетона
Условия набора прочности зависят как от начальной температуры бетонной смеси, так и ее изменения в процессе твердения (рис. 22.I). При температуре менее плюс 5°С скорость нарастания прочности резко снижается, а при замерзании процесс гидратации полностью прекращается. Если к моменту замерзания бетон не наберет достаточной прочности, то при наличии в порах свободной воды в бетоне появляются трещины вследствие расширения образующихся частиц льда. Вокруг крупных частиц - заполнителей происходит концентрация свободной воды, что нарушает однородность и монолитность бетона. Значительно снижается и сцепление бетона с арматурой. После оттаивания твердение бетона продолжается, но образовавшиеся трещины неустойчивы, что ведет к потере прочности и большей водопроницаемости.
Для возможности набора прочности при отрицательных температурах иногда добавляют противоморозные добавки, которые снижают температуру замерзания смеси. Чаще всего применяют поваренную соль NaCl, CaCl2 поташ K2CO3, аммиачную воду
368

NH4CH. Добавки не должны ухудшать свойства бетона, быть дешевыми и безопасными. Однако добавки нельзя применять для зон переменного горизонта воды, в агрессивных средах, армированных конструкциях, так как они в этих условиях снижают долговечность конструкции. Поэтому в гидротехнических бетонах противоморозные добавки также применяются очень редко.
22.2. Подготовка блоков к бетонированию
Подготовка блоков к бетонированию в зимнее время кроме выполнения обычных мероприятий в летний период (см. главу 21) предусматривает создание условий, обеспечивающих нормальный температурный режим в блоке в период бетонирования и твердения бетона, в уборке всех наледей и отогреве основания на глубину, обеспечивающую требования температурного режима (обычно на менее 30 см). При температурах наружного воздуха выше минус 10-20°С работы выполняются в открытых блоках, а при более низких температурах - под шатром или тепляком.
Температурный режим в блоках бетонирования обеспечивается выбором соответствующей зимней опалубки и режима утепления. Коэффициент теплопередачи зимней опалубки выбирают на основе расчета в зависимости от температур воздуха, устойчивых в течение более одной недели. Примерные значения коэффициента теплопередачи опалубки на основе опыта приведены в табл. 22.I.
Таблица 22.I
Опытные значения коэффициента теплопередачи опалубки
Температура |
Коэффициент |
теплопередачи |
наружного воздуха, °С |
опалубки, ккал/(м² ч град) |
|
-10 |
1.20 |
|
-25 |
0,75 |
|
-35 |
0,60 |
|
-40 |
0,50 |
|
Переход с летней опалубки на зимнюю должен осуществляться заблаговременно, до наступления заморозков. Поверхность бетона, остающаяся в летней опалубке на зимний период, долина дополнительно утепляться с доведением коэффициента теплопередачи до принятого для зимней опалубки. При применении в качестве опалубки сборных бетонных элементов последние должны иметь утепление с необходимым коэффициентом теплопередачи.
На практике часто наружные поверхности массивных сооружений выполняют полностью в теплой опалубке и не снимают ее в течение всего периода строительства до наполнения водохранилища. Например, верховые напорные грани бетонных плотин Мамаканской, Братской, Усть-Илимской и других ГЭС были выполнены в теплой опалубке. Боковые грани контрфорсов Зейской ГЭС опалубливались сборными железобетонными плитами с утеплителем внутри плит (трехслойные плиты). В последнее время широкое распространение получило разделение опалубочных щитов и утеплителя в отдельных конструкциях. При этом опалубочные щиты остаются постоянными для летнего и зимнего периодов, а в зимний период на эти щиты дополнительно накладывается утеплитель в виде плит из пенополистирола и других материалов. В этом случае при распалубке в зимний период снимается только опалубочный щит, а утеплительный щит остается на месте, обеспечивая нужные теплозащитные свойства. Это наиболее прогрессивное направление в совершенствовании конструкций теплой опалубки.
В зависимости от выбранного способа укладки бетонной смеси в блоки в период подготовки блоков должны быть выполнены дополнительно все мероприятия и конструкции, обеспечивающие необходимые условия для соблюдения температурного режима в блоках в период бетонирования и набора прочности.
369

При температурах наружного воздуха ниже минус 10-20°С укладка бетонной смеси ведется обычно под защитой шатров или тепляков, которые также должны быть выполнены при подготовке блоков к бетонированию.
Шатры и тепляки - это конструкции, закрывающие бетонируемый блок или серию блоков со всех сторон и позволяющие поддерживать внутри них постоянную положительную температуру на уровне 5-10°С.
Тепляк представляет собой стационарную конструкцию утепленного перекрытия и бокового ограждения, выполненного из применяемой утепленной опалубки (рис. 22.2,а). Перекрытие опирается на металлические опоры (колонны), установленные в блоке, и являются съемными, используемыми многократно.
Рис. 22.2. Конструктивные схемы тепляка (а) и шатра (б)
1 - металлическая ферма (колонна); 2 - теплая опалубка; 3 - утепленное перекрытие; 4 - люки; 5 - бетонируемый блок; 6 - съемные крышки; 7 - колонны с механизмом для самоподъема; 8 - утепленное полотнище
Шатер - переставная металлическая пространственная конструкция с утепленными стеновыми и кровельными ограждениями (рис. 22.2, б). Современные шатры имеют приспособления для вертикального перемещения по мере бетонирования сооружения по высоте. Внутри шатра к его перекрытию подвешиваются все инженерные коммуникации, необходимые при подготовке, бетонировании блока и уходе за ним. Это электроразводка, водопровод, паропроводы, воздухопроводы и др. Для подачи бетонной смеси и других грузов в шатер или тепляк в перекрытиях предусмотрены соответствующие закрывающиеся люки. Положительную температуру поддерживают калориферами. Шатры являются также эффективным средством защиты бетонных поверхностей от воздействия солнечной радиации в летнее время. В этом случае в шатрах должны предусматриваться дополнительно средства для полива бетонных поверхностей, принудительная вентиляция, установки для охлаждения воздуха и др.
Отогрев основания до требуемых положительных температур осуществляется с помощью электроили парокалориферов. Для массивных блоков с Мп<3 допускается не отогревать основание, но при условии соблюдения дополнительных мер при укладке бетонной смеси: применении в первом слое у основания (прокладочном слое) добавок - ускорителей твердения, воздухововлекающих добавок и повышения температуры
бетонной смеси до 10 -15ºС. В качестве добавки ускорителя применяется (1,5-2% от исхода цемента). В качестве воздухововлекающей добавки применяют СНВ, СДБ + СНВ, ЛХД, СДБ + ЛХД.
22.3. Приготовление и транспорт бетонной смеси
Бетонную смесь в зимнее время, как правило, приготавливают тех же составов, что и в летнее время. Иногда применяют специальные добавки для ускорения твердения или
противоморозные |
Например, для исключения отогрева основания при |
укладке первого слоя. |
|
370

Температура бетонной смеси на выходе из бетонного завода должна обеспечивать поступление бетонной смеси в блок с температурой бетонной смеси не менее 5-7°С. Заполнители не должны содержать лед, снег, мерзлые комья, так как это меняет водоцементное отношение (В/Ц).
Температура бетонной смеси на выходе (Тбс) регулируется подогревом составляющих, что обосновывается расчетом.
Подогрев составляющих осуществляется обычно теми же способами что и охлаждение (см. главу 19). При температуре наружного воздуха выше минус 5°С достаточен только подогрев воды, при более низких температурах подключается обогрев мелких и крупных заполнителей. Вода подогревается в электробойлерах, песок - в бункерах бетонного завода и на складах паровыми регистрами, горячим воздухом или горячими газами. Крупный заполнитель подогревается также на складах и в бункерах бетонного завода паровыми регистрами либо водой и паром в специальных резервуарах, либо горячим воздухом и газами в шахтных нагревателях. Рекомендуются следующие температуры разогрева: воды<85°С, песка < 60°С, крупного заполнителя <50°С.
При транспортировании бетонная смесь должна предохраняться от переохлаждения. Кузова автосамосвалов должны иметь двойную обшивку и обогреваться выхлопными газами, а сверху покрываться крышками, При подаче транспортерами температура в галерее должна быть не ниже плюс 5°С.
22.4. Укладка бетонной смеси
Укладка бетонной смеси в зимний период в зависимости от температуры наружного воздуха осуществляется следующими способами: в открытые блоки методом "термоса" и "активного термоса", в закрытые блоки - под защитой шатров или тепляков.
Укладка методом "термоса". Бетонирование в открытых блоках методом "термоса" производится при температурах до минус 10-15ºС, в отдельных случаях до минус 20°С, в зависимости от модуля опалубливаемой поверхности и дополнительных мероприятий по утеплению отдельных частей блока. Модуль поверхности (м²/м³бетона) равен
(22.1)
где- площадь опалубливаемой поверхности блока;
- объем блока бетонирования.
Сущность метода заключается в том, что бетонная смесь, имеющая температуру плюс 15°-20°С, укладывается в утепленную опалубку. За счет начального тепловыделения бетонной смеси и теплоты в процессе гидратации (теплоэкзотермии) бетон набирает необходимую минимальную прочность до его замораживания. Продолжительность остывания определяется расчетом и зависит от ряда факторов:
(22.2)
где все обозначения - см. главу 2, формулы (14-28). Она должна быть достаточной для достижения минимальной прочности бетона до замораживания. Метод "термоса" наиболее эффективен для массивных конструкций с Мп < 3 с применением в случае необходимости различных дополнительных мероприятий по утеплению углов, ребер, поверхностных слоев и др. (рис. 22.3). Наиболее распространенным из дополнительных мероприятий является устройство электрообогрева в углах и по контуру блока.
371

Рис. 22.3. Дополнительные мероприятия по утеплению блоков при применении метода "термоса": планы блоков (а); разрезы (б)
1 - теплая опалубка; 2 - дополнительное утепление углов; 3 – укрытие; 4 - электрообогрев углов; 5 – электрообогрев периферийный
Укладка бетонной смеси под защитой шатров или тепляков. При более низких температурах, исключающих применение метода "термоса", для массивных конструкций применяется укладка бетонной смеси в закрытые блоки под защитой шатров или тепляков. Поскольку климатические условия в нашей стране, особенно в Сибири и на дальнем Востоке, не позволяют ограничиться только методом термоса, применение шатров и тепляков имеет место практически на всех крупных стройках. Это обстоятельство усложняет укладку бетонной смеси в зимнее время и значительно удорожает работы.
Бетонная смесь подается в блоки через соответствующие закрывающиеся отверстия в перекрытии тепляков и шатров. В случае необходимости устанавливаются приемные бункера и хоботы. Разравнивание и уплотнение бетонной смеси осуществляется теми же методами, что и в летний период.
В процессе бетонирования в шатре или тепляке поддерживается положительная температура в пределах 5-10°С. Такая же температура поддерживается и после бетонирования до удаления цементной пленки. После удаления цементной пленки шатер может не отапливаться, но поверхность бетона должна быть покрыта утеплителем с термическим сопротивлением не менее, чем утепленной опалубки. До недавнего временя для этой цели использовались опилки. Однако это загрязняло блоки, увеличивало трудозатраты. В настоящее время все большее распространение получают различные покрытия из полимерных и теплозащитных материалов, конструируемых а виде отдельных одеял - матов, легко поддающихся монтажу и демонтажу.
Бетонирование тонкостенных элементов. Поскольку объем бетона в тонкостенных элементах относительно небольшой, то запаса тепла экзотермии обычно недостаточно для обеспечения набора прочности до замораживания. Поэтому при бетонировании таких конструкций и элементов обычно применяют различные виды дополнительной термообработки бетона в период твердения.
Методы термообработки можно разделить на ряд групп: электродный прогрев; индукционный прогрев; инфракрасный прогрев; паровой прогрев; греющая термоактивная опалубка.
Электродный прогрев (электротермос) основан на прохождении тока через свежеуложенный бетон. Применяется переменный ток пониженного напряжения 50-100 В, в отдельных случаях 120-220 В. Различают электроды внутренние (стержневые, струнные) и поверхностные (нашивные, плавающие). Струнные электроды состоят из арматурной стали диаметром 6-10 мм (для фундаментов, балок, плит). Стержневые
372
электроды состоят из арматурной стали диаметром 6-16 мм (для колонн и стен). Расстояние между электродами 20-25 мм при напряжении 60 В, до 30-40 см при напряжении 200 В. Расстояние между электродами и арматурой 5-50 см в зависимости от напряжения. Нашивные электроды навешивают на опалубку через 10-20 см. Плавающие электроды втапливают в бетон с поверхности на 2-3 см для прогрева верхних поверхностей бетонных и железобетонных конструкций.
Разновидностью способа электротермоса является метод форсированного электрообогрева бетонной смеси сразу после ее укладки в опалубку с последующим повторным вибрированием. Разогрев смеси непосредственно в опалубке исключает преждевременную потерю подвижности, а повторное вибрирование сводит к минимуму возможности структурных нарушений при форсированном разогреве. Кроме того, он более экономичен.
Индукционный прогрев - прогрев в электромагнитном поле. Для этого вокруг прогреваемого элемента устраивают спиральную обмотку - индуктор из изолированного провода и включают его в сеть. Под воздействием переменного электромагнитного поля опалубка и арматура, выполняющие роль сердечника (соленоида)нагреваются и передают тепловую энергию бетону. Применяется для прогрева густоармированных конструкций и стыков.
Инфракрасный прогрев - прогрев инфракрасным облучением с помощью генератора в виде электроспирали, помещенной в металлический рефлектор на расстоянии 5-8 см от отражательной поверхности
Паровой прогрев - заключается в создании вокруг бетонируемого элемента паровой рубашки. Паровая рубашка обеспечивает благоприятные тепловлажностные условия для твердения бетона, но требует большого расхода пара (0,5-2 т/м³), а также оградительных стенок, прокладки трубопроводов. В основном применяется при изготовлении сборных железобетонных конструкции.
Греющая термоактивиая опалубка применяется вместо теплой опалубки. Она выполняется в виде унифицированных утеплительных щитов, с проложенным в их толще нагревательным кабелем, трубчатыми электронагревателями (ТЭНы) и нагревателями других конструкции. Термоактивная разборно-переставная опалубка может оказаться экономичной для бетонирования различных тонкостенных конструкций. Экономически оправданный срок службы термоактивной опалубки около 1000-1500 ч, что соответствует 20-30-кратной оборачиваемости.
Все изложенные методы термообработки бетона предназначены для предотвращения отрицательного воздствиянизких температур на твердеющий бетон ,т.е.для предотвращения раннего замораживания бетона.Общим недостатком этих методов при производстве тонкостенных конструкций является неизбежность деструктивных ( отрицательных) явлений на ранних стадиях твердения, обусловленные тем , что тепло вносимое в твердеющий бетон , вызывает рпсширение его компонентов, что отрицательно влияет на формирующуюся структуру цементного камня
Недобор прочности в термо обработанном бетоне по сравнению с бетоном нормального твердения составляет от 17 до 23%.Для компенсации потерь прочности термообрабатываемого бетоначасто приходится идти на перерасход цемммента.
Указанные недостатки сводятся к минимуму в методе предварительного разогрева бетонной смеси . Его сущность заключается в том, что непосредственно перед укладой форму или опалубку бетонную смесь подвергают одновременному воздействию температуры (разогрев), вибрации , избыточного давления, пара и электрических полей
.Сочетание указанных технологических воздействий, осуществляемых в непрерывном режиме, позволяет интенсифицировать процесса гидролиза и гидратации цемента, вовлечь в процесс его большее количество на ранних стадях твирдения бетона. Это поозволяет обеспечить ускоренный набор прочности бетона, сократить расход электроэнергии, уменьшить расход цемента на 1-15 %, отказаться от других способов
373
термообработки при возведении тонкостенных конструкций при температуре наружного воздуха до минус 20 град. Бетон полученный с такой обработкой смеси обладает лучшими показателями по плотности, морозостойкости, водонепрницаемости, что очень важно для бетонов гидротехнических сооружений.
Для обеспечения бетона с такой термообработкой в производственых условиях разработаны специальные установки для заводских и построечных условий.
374
ГЛАВА 23. Уход за бетоном и контроль качества бетонных работ
23.1. Основные требования и мероприятия по уходу за бетоном
Основными требованиями по уходу за бетоном являются:
1)обеспечение тепловлажностного режима, определяющего заданное нарастание прочности и предотвращающего значительные температурно-усадочные деформации и трещины;
2)получение температурного режима и температурных перепадов в блоках бетонирования, гарантирующих отсутствие трещинообразования;
3)предохранение твердеющего бетона от ударов и других воздействий, снижающих качество бетона в сооружении.
Тепловлажностный уход за бетоном в начальный период его твердения является
обязательным мероприятием для предотвращения потери им влажности во время ранней относительно быстрой гидратации цемента, что обеспечивает нормальный набор прочности и предотвращает значительные температурно-усадочные деформации и образование усадочных трещин.
Уход за свежеуложенным бетоном в летнее время заключается в поддержании открытых поверхностей во влажном состоянии, что осуществляется следующими способами: распылением воды; заливкой водой; укрытием пленками, брезентом, мешковиной, матами или другими подобными материалами, увлажняемыми в процессе испарения.
Вжаркую сухую погоду во влажном состоянии должна также находиться неснятая деревянная опалубка. Уход за бетоном начинается при достижении прочности 0,5 МПа и продолжается или до перекрытия вышележащим блоком или в течение 10-15 сут в зависимости от климатических условий. При бетонировании в жаркую и сухую погоду открытая поверхность должна сразу укрываться паронепроницаемой (полиэтиленовой) пленкой толщиной 0,15-0,2 мм и находиться под нею в течение 6-8 ч, после чего начинается систематический влажностный уход. В районах с жарким климатом предусматривают также меры для защиты поверхности бетона от воздействия солнечной радиации путем устройства легких ограждающих конструкций или шатров, а также распыления специальных пленкообразующих материалов.
Восеннее и весеннее время года, когда среднесуточная температура наружного воздуха составляет около 5°С и возможны заморозки, влажностный уход заменяется укрытием гидроизоляционными материалами с возможным утеплением.
Обеспечение температурного режима в блоках. Температурный режим твердения
бетона из условия его трещиностойкости обеспечивается комплексом технологических мероприятий, выполняемых как в период приготовления и укладки, так и после укладки, т.е. в период набора прочности. При приготовлении бетона это может быть: охлаждение воды затворения; добавки льда; охлаждение крупного заполнителя; охлаждение мелкого заполнителя.
При необходимости температурный режим блоков в период твердения бетона обеспечивают с помощью искусственного охлаждения путем поверхностного полива или через систему труб-змеевиков.
Необходимость мероприятий по регулированию температуры в блоках бетонирования определяется расчетами, рассмотренными в главе 14. По опыту расчетов и практики строительства допустимые температурные перепады составляют:
- в контактной зоне (на высоте менее 0,2 длины блока) Т <16-18°С - для длинных блоков; T =20-27°С - для столбчатых блоков;
- в свободной зоне (на высоте более 0,5 длина блока) T <20-25°C.
Разность температур между ядром и горизонтальной поверхностью блоков во всех случаях не должна превышать 14-16°С.
375
Поверхностный полив осуществляют посредством выпуска воды из специальных перфорированных труб или струйными или дождевальными установками. Слой воды составляет 8-10 мм. Применяется речная или грунтовая вода. Температура воды рекомендуется ниже максимальной допустимой в бетоне не менее чем на 8-12°С. Поверхностный полив целесообразно применять при больших поверхностях блоков с высотой до 1-1,5 м.
При необходимости более глубокого регулирования температуры высоких блоков применяют трубное охлаждение. Трубное охлаждение осуществляется путем пропуска хладоносителя через систему труб. Предусматривается обычно два этапа охлаждения: в период разогрева и экзотермии; после экзотермического разогрева при остаточном тепловыделении (охлаждении до температуры омоноличивания).
В качестве хладоносителя обычно используется речная или охлажденная вода и реже - различные рассолы. Продолжительность первого этапа - 5-15 дней после укладки бетона в блок в зависимости, от шага змеевиков. Перепад температур между бетоном и охлаждающей водой не должен превышать 30°С. Скорость снижения температуры обычно 0,5-1°С/сут в зависимости от длительности охлаждения (по новым исследованиям - до 2°С/сут).
Второй этап охлаждения продолжается более длительное время (до 1-2 мес) и зависит от шага труб в плане и по вертикали. Перепад температур между бетоном и охлаждающей водой не должен превышать 20-25°С. Интенсивность охлаждения 0,5°С/сут в контактной зоне и не более I˚С/сут в свободной зоне. Для охлаждения часто используется холодная естественная вода из реки или холодная подземная вода. При их отсутствии предусматриваются холодильные установки. Трубное охлаждение второго этапа должно обеспечивать равномерное охлаждение бетона по всему объему, не вызывая недопустимых перепадов температур между смежными блоками в плане и по высоте.
В качестве труб-змеевиков обычно используют стальные газопроводные трубы диаметром 1". Соединяют трубы резьбовыми муфтами, сваркой или специальными уплотнительными муфтами. Горизонтальный и вертикальный шаг 1-3 м. В последнее время широкое распространение получают полиэтиленовые трубы. Трубы-змеевики укладываются или на основание бетонируемого блока или на поверхность укладываемых слоев в процессе бетонирования. Для ускорения монтажа в блоке предварительно заготавливают трубы-змеевики определенного размера, которые подаются затем кранами в блок. Змеевики подключаются к распределительным трубопроводам, а те в свою очередь к магистральному. Оптимальная длина змеевика около 200 м. Входы и выходы змеевика должны оснащаться арматурой, обеспечивающей регулирование расходов воды и изменение направления движения воды, скорость движения воды в трубах в пределах 0,5- 0,9 м/с. Средний расход воды через змеевики примерно 1,5 м³/ч. Для более равномерного охлаждения бетона предусматривается периодическое изменение направления движения в змеевиках.
Предохранение свежеуложенного бетона от повреждений. Для предохранения бетона от повреждений работы на его поверхности могут начинаться только после набора бетоном определенной прочности. Так, удаление цементной пленки до набора прочности 1,5 МПа должно производиться с применением досчатых настилов. Механическое удаление цементной пленки может производиться после набора прочности не менее 1,5 МПа, установка опалубки и перемещение транспорта - при прочности не менее 2,5 МПа.
Распалубка блоков также может производиться только при наличии условий, предотвращающих повреждение поверхности бетона и образование трещин. Сроки распалубки устанавливаются в зависимости от требований к температурному режиму, от условий загружения конструкций и от температуры окружающей среды. Как правило, температурный перепад "центр - поверхность блока" и "центр - окружающая среда" должен быть меньше 25-30°С, что в каждом конкретном случае уточняется расчетами.
376
Обнаруженные при распалубке дефекты бетона должны быть исправлены. Разделка раковин должна иметь расширение - "ласточкин хвост".
Уход за бетоном в зимнее время. Требования, предъявляемые к уходу за бетоном в летнее время, должны выполняться и в зимнее время. Дополнительные требования предъявляются к теплозащите бетона. Промерзание бетона допускается при наборе прочности не менее 40-50% его марочной прочности, при этом должны быть соблюдены все требования к температурному режиму, перепады температур не должны превышать допустимых. Все это обеспечивается выбором соответствующей зимней опалубки и режима утепления.
23.2. Контроль качества бетона и бетонных работ
Общие положения. Контроль качества бетонных работ заключается в систематической проверке и наблюдении за выполнением требования проекта и действующих норм и ГОСТов. Контроль ведется на всех стадиях и видах работ, начиная от проверки качества исходных материалов, приготовления бетонной смеси и кончая уходом за уложенным бетоном.
Проверке подвергаются: качество исходных материалов и их хранения; точность дозирования; качество приготовления, транспортирования и укладки бетонной смеси; выполнение мероприятии по обеспечению температурного режима; выполнение мероприятий по уходу за бетоном; качество бетона путем одновременного отбора проб и проведения необходимых испытании.
Контроль качества материалов и их хранения. Все используемые в бетоне материалы (цемент, заполнители, добавки, арматура и др.) должны удовлетворять по своему составу и свойствам соответствующим требованиям ГОСТов. Условия хранения каждого из материалов должны выдерживаться такими, чтобы сохранялись все необходимые качества этих материалов. Цементы на строительство должны поступать с соответствующими сопроводительными документами и заводскими паспортами, где должны быть указаны результаты испытании данной партии цемента и их соответствие ГОСТам или специальным техническим условиям. Цементы с разных заводов, разных видов и марок должны разгружаться и храниться раздельно с присвоением каждой партии номера с записью в соответствующем журнале. Использовать цемент можно только с разрешения лаборатории после проверки качества поступившей партии. При хранении цемента на складах(в силосах) должен поддерживаться необходимый температурно-влажностный режим и производиться периодическое взрыхление и перекачка цемента из одной банки в другую с целью исключения слеживания и снижения прочностных свойств.
Арматурная сталь, так же как и цементы, поступает с соответствующими документами с завода или базы. Сталь складируется по диаметрам и сортам и должна предохраняться от ржавления и загрязнения.
Контроль качества заполнителей осуществляется в местах заготовки, промывки, сортировки и складирования путем отбора проб. Складировать каждую фракцию нужно раздельно, без перемешивания, расслоения и загрязнения. Перед использованием заполнителей проверяют гранулометрический состав, влажность и другие свойства для корректировки водоцементного отношения и других характеристик состава бетона.
Контроль приготовления бетонной смеси. Текущий контроль предусматривает проверку: соответствия применяемых материалов проектному составу; точности дозирования; соответствие времени перемешивания; температуры бетонной смеси; качества бетонной смеси путем отбора проб.
Периодически проверяется реальный выход бетонной смеси. Регулярно проверяется исправность оборудования, дозаторов.
Регулярный контроль качества бетонной смеси осуществляет лаборатория строительства путем определения подвижности, объемной массы, содержания воздуха и температуры не реже одного раза в сутки
377
Контроль за транспортированием и укладкой бетонной смеси. Контроль предусматривает проверку: исправности всех средств и механизмов; защиты средств от осадков и других атмосферных воздействий; продолжительности транспортирования и подвижности бетонной смеси; изменения температуры бетонной смеси в пути. Пробы для определения подвижности бетонной смеси отбирают у места приготовления и укладки на реке двух раз в смену.
Контроль качества подготовки основания и блоков к бетонированию. Контроль предусматривает проверку: всех участков основания блоков до, в процессе и после бетонирования блока; прочности скального основания; качества монтажа опалубки; качества монтажа арматуры и сварных соединений; качества обработки смежных поверхностей.
Перед началом бетонирования производится окончательная приемка блока комиссией, назначаемой главным инженером строительства, с участием представителей заказчика и проектной организации. Результаты приемки фиксируются в акте с приложением технических документов.
Контроль качества укладки бетонной смеси. Контроль осуществляют перед началом и в процессе бетонирования.
Перед началом бетонирования проверяется: наличие акта приемки блока; готовность бетонного завода; наличие исправного транспорта; обеспечение необходимой интенсивности бетонных работ; качество опалубки; наличие средств по уходу; наличие средств по удалению воды.
Впериод укладки бетонной смеси проверяется; отсутствие расслоения бетонной смеси; качество уплотнения (не реже 1-З раз в смену) плотномером ВНИИГа, атомным плотномером конструкции Оргэнергостроя или другими приборами; выполнение требований по укладке в процессе всего хода бетонирования (перерывы, возобновление работ); прочность и плотность опалубки. По результатам проверки указанных элементов в случае необходимости корректируют состав бетона, толщину слоев, условия бетонирования и др.
Впроцессе бетонирования отбирают пробы каждой марки бетона для испытания прочностных и иных свойств. Отбор производится ежесуточно на бетонном заводе и у места укладки.
Контроль за уходом и за качеством уложенного бетона. После укладки бетонной
смеси в блок контролируют: температурно-влажностный режим твердения с помощью контрольно-измерительной аппаратуры (КИА); трещинообразование на блоках путем визуального осмотра поверхностей и по приборам с составлением актов и фиксированием дефектов; прочностные свойства бетона в сооружении, а также морозостойкость, водонепроницаемость, однородность, объемный вес и др.
Контроль качества бетона в сооружении осуществляют различными методами: с помощью заложенной КИА (тензометров, термометров); испытанием образцов ненарушенной структуры; проведением ультразвуковой, акустической и радиоизотопной дефектоскопии; нагнетанием воды в скважины.
Для определения прочности поверхностных слоев бетона можно использовать различные простые способы и приборы: диск Губбера, эталонный молоток и др.
Контроль качества зимних бетонных работ. Непосредственно перед началом зимних бетонных работ проверяют: готовность бетонного завода и всех механизмов; готовность средств обогрева и отогрева.
В период проведения бетонных работ проверяют температуры: наружного воздуха (не реже двух раз в смену); материалов для бетона (не реже четырех раз в смену); бетонной смеси на выходе из бетонного завода, и перед выгрузкой в блок; бетонной смеси в
уложенном слое до перекрытия следующим слоем (не допускаетсябетона в сооружении (не реже двух раз в смену в первые сутки твердения и один раз - в последующие до снижения температуры до 0°С).
378
Документация. Процесс производства бетонных работ должен фиксироваться в различных документах. На каждый блок составляют акты приемки и паспорт блока, в который заносят все сведения о блоке, результаты испытаний, показания КИА и т.д.
379

ГЛАВА 24. Специальные виды бетонных работ 24А. Производство сборного железобетона
24А.1. Назначение и типы сборных элементов и конструкций
Сборные железобетонные конструкции применяются в отечественном гидротехническом строительстве с 30-х годов прошлого века – при возведении Волховской, Земо-Авчальской, Нижнесвирской и других ГЭС, первоначально как элементы каркасов машинных залов. По мере развития стройиндустрии сфера использования сборного железобетона расширялась. Он нашел применение в плотинах в качестве опалубочных плит–оболочек, балок перекрытия донных и водопропускныъ отверстий, пазовых конструкций, массивных опалубочных блоков, дренажных и противофильтрационных элементов, креплений откосов грунтовых плотин. В 60-70х годах прошлого века объем сборного железобетона в общем объеме бетонных работ достигал 15%.
При строительстве ГЭС Волго-Камского каскада широко применялись пространственные конструкции, объединяющие железобетонные панели в качестве несъемной опалубки с армокаркасами с последующим их обетонированием на месте установки. Также сложные конструкции использовались при бетонировании тора отсасывающих труб, входной части водоприемников, водосбросов зданий ГЭС и т.п. Несмотря на повышенный расход арматуры такие конструкции сокращали трудозатраты на объекте и повышали культуру производства (рис. 24А.1).
380
Рис. 24А.1. Сборные железобетонные элементы в конструкции здания гидроэлектростанции
1 – забральная балка, 2 – перекрытие щитового отделения верхнего бьефа, 3 – элементы верхнего строения ГЭС, 4 – стакан генератора, 5 – перекрытие пола машинного зала, 6 – перекрытие помещения трансформаторов и распределительного устройства, 7 – элементы мостового перехода, 8 – перекрытие щитового отделения нижнего бьефа, 9 – стеновые панели служебных помещений, 10 – перекрытие отсасывающей трубы, 11 – облицовка колена и торца отсасывающей трубы, 12 - забральная балка, 13 – перекрытие спиральной камеры
Технологической вершиной применения сборного железобетона в гидротехническом строительстве явилось создание Саратовской ГЭС, Кислогубской ПЭС и водоводов Загорской ГАЭС. Для монтажа крупногабаритных сборных элементов размером до 2*3,8*8,15 м, весом до 200 т на Саратовской ГЭС применялись специальные козловые краны грузоподъемностью 2*110 т с пролетом 75 м, охватывающие все здание гидроэлектростанции. Сооружение Саратовской ГЭС включали 21 типоразмер крупногабаритных элементов, стыки между ними омоноличивались сваркой и обетонированием. Кислогубская ПЭС выполнена из единого наплавного блока, выполненного в заводских условиях. Многолетняя эксплуатация в агрессивной морской воде показала высокое качество этого сооружения.
На Загорской ГАЭС эксплуатируются напорные сталежлезобетонные трубопроводы диметром 7,5 м длиной 720 м. Шесть ниток этих трубопроводов собраны из отдельных звеньев длиной 4,41 м, с толщиной стенки 0,4 м весом 140 т. Каждые пять состыкованных звеньев объединены температурно-осадочную секцию со специальным стыковочным узлом.
С точки зрения экономики, применение сборного железобетона при возведении массивных гидротехнических сооружений не выгодно, т.к. один кубометр сборного в 1,5-2 раза дороже кубометра монолитного бетона. Однако, его применение оправдывается экономией трудозатрат на стройплощадке, сокращением сроков, повышением культуры производства и архитектурных достоинств сооружения. Сборные бетонные и железобетонные элементы отличаются высоким качеством лицевых поверхностей, поскольку изготавливаются в металлических формах, смазанных специальным составом – эмульсолом, предотвращающим адгезию бетона к металлу.
Многолетняя практика выработала два основных направления в применении сборного бетона и железобетона в гидротехническом строительстве – в виде простых сборных бетонных и железобетонных элементов и виде сборно-монолитных пространственных конструкций. К первому виду относятся различные виды железобетонной опалубки, описанные в главе 17 учебника (рис. 17.15 - 17.17), балки перекрытия донных отверстий (рис. 24А.1а), глубинных водосбросов и других полостей и отверстий в бетонных плотинах, элементы конструкций машинного здания ГЭС (рис. 24А.2), лестничные марши в шахтах плотин, мостовые балки по бычкам водосливных пролетов, плиты крепления откосов грунтовых плотин, дорожные ограждения и т.п. Эти элементы рассчитаны на самостоятельную работу при транспортных, монтажных нагрузках, нагрузках от давления бетонной смеси и практически не имеют выпусков арматуры, кроме закладных частей и монтажных петель.
381

Рис. 24А.1а
Рис. 24А.2. Сборные железобетонные элементы верхнего строения здания ГЭС 1 – кровельная балка, 2 – карнизная плита, 3 – кровельный прогон, 4 – надкрановая стойка,
5 – служебный мостик, 6 – подкрановая балка, 7 - подкрановая стойка, 8 – керамзитобетонные панели, 9 – стеклоблочные панели, 10 – стальная труба диаметром 219 мм, 11 – стальная труба диаметром 146 мм
382

Второе направление - сборно-монолитные конструкции. Это конструкции, образующие наружные поверхности из железобетона с жесткой рабочей арматурой внутри. Изготовление рабочей арматуры в виде каркасов в заводских условиях позволяет экономить трудозатраты и время на стройплощадке. Железобетонный элемент с арматурным каркасом образует пространственную конструкцию, имеющую достаточную жесткость при транспортировке и монтаже. После установки конструкции на место, выверки и раскрепления ее внутренняя часть заполняется монолитным бетоном. Примером этого направления могут служить сборные железобетонные блоки входной части водоприемников с пазовыми конструкциями (рис.24А.3.), армопанельные блоки бычков, армоопалубочные пространственные блоки отсасывающих труб, консоли мостов на гребнях плотин, блоки подпорных стенок, причалов, шлюзовых камер, разного рода ячеистых конструкций. Недостатком таких конструкций являются трудности, возникающие при укладке бетонной смеси, ее качественной проработки в условиях густой арматуры.
Рис. 24А.3. Сборно-монолитные конструкции 1 – водовод, 2 – балки, 3 – первый ярус бетона, 4 – второй ярус бетона, 5 – верхняя
поперечная арматура, 6 - верхняя продольная арматура, 7 – нижняя поперечная арматура, 8 – нижняя продольная арматура, 9 – армофермы, 10 – сварные стыки арматуры, 11 – железобетонный сегмент, 12 – тяги, 13 – ранее уложенный бетон, 14 – опорный узел, 15 – опорные инвентарные стойки, 16 – бетон омоноличивания, 17 – легкие армофермы для связи, 18 – рабочая арматура, 19 – армофермы, 20 – арматурная сетка, 21 – плоские армопанели, 22 – предварительно омоноличенные пазовые конструкции, 23 – металлические закладные части, 24 – армопанель оголовка бычка
В настоящее время развивается и третье направление – изготовление крупных наплавных блоков из железобетона, начало которому положено Кислогубской ПЭС. Такие блоки применяются для морских нефтяных платформ, фундаментов ЛЭП через водные преграды, морских заградительных дамб, причалов, мостовых опор. Существуют предложения о применении таких блоков для малых ГЭС.
383
Опыт эксплуатации первых сооружений с плитами-оболочками обнаружил и серьезные недостатки этих элементов, главными из которых стали недостаточная морозостойкость, нарушения контакта с монолитным бетоном, особенно в зонах переменного горизонта воды. Это вызвано тем, что технология пропарки сборных железобетонных элементов неизбежно формирует поры и каналы в бетонном массиве изделия, которые и становятся очагами нарушения монолитности. Именно поэтому СНиП ll– 5677 и СНиП 2.06.08-87 «Бетонные и железобетонные конструкции гидротехнических сооружений специально подчеркивают, что нормы распространяются на конструкции, находящиеся постоянно или периодически под воздействием водной среды. Предписывалось для обеспечения требуемой долговечности, водонепроницаемости и морозостойкости конструкций, а также для уменьшения парового давления воды предусматривать укладку высокомарочных бетонов, применение поверхностно-активных добавок (воздухововлекающих, пластифицирующих гидроизоляцию и теплогидроизоляцию наружных поверхностей сооружения). Кроме того, технологи отработали режим «мягкого пропаривания», когда температура в камерах пропаривания не вызывала кипения вовлеченной в бетон воды, но цикл выдерживания изделий в камерах по времени увеличивался в 1,5-2 раза. Такие изделия обладали высокой морозостойкостью.
С появлением в гидротехническом строительстве укатанного бетона сфера применения сборных элементов в плотиностроении сократилась за счет исключения или сокращения межсекционных и межблочных швов. Тем не менее для малых ГЭС, различного рода ячеистых конструкций, подпорных стен, каналов и водоводов, даже для арочных плотин применение сборных бетонных и железобетонных конструкций остается актуальным.
24А.2. Производство сборного железобетона
Изготовление сборных железобетонных элементов для гидротехнического строительства желательно организовывать на действующих предприятиях стройиндустрии, размещенных в районе строительства, если дальность возки не превышает 400-500 км. Однако, это не всегда возможно, даже если такие предприятия имеются. Дело в том, что габариты и вес гидротехнических элементов редко могут вписаться в технологию и размеры обычных цехов железобетонных изделий гражданского и промышленного назначения со стандартным крановым оборудованием. В связи с этим в гидротехническом строительстве часто используют открытые временные полигоны сборного железобетона со стендовой технологией, когда изделие полностью изготавливается на стационарном стенде (рис. 24А.4.). Для ускорения процесса твердения бетона применяются электропрогрев бетонной смеси и термовлажностная обработка изделий. Отформованные изделия в опалубке помещают в пропарочные камеры с температурой 60-90 °С при 100% влажности. В этих условиях бетон набирает прочность 70-80 % от марочной за 10-20 часов в зависимости от конфигурации изделий качества бетонной смеси и условий термообработки. По такой технологии изготовлялись, например, опалубочные блоки плотины Братской ГЭС.
384

Рис. 24А.4. Полигон для изготовления сталежелезобетонных элементов трубопровода участки: l – предмонтажных работ, ll – формовочный, 1 – виброплощадка грузоподъемностью 200 т, 2 – установка для электроразогрева бетонной смеси, 3 – трансформаторные подстанции, 4 – посты выдерживания и покраски, 5 – подсобные помещения, 6 – пост гидравлических испытаний, 7 – пост укрупнительной сборки, 8 – тележка грузоподъемностью 300 т, 9 – кантователь, 10 – кран грузоподъемностью 15 т, 11
– кран грузоподъемностью 200 т,
Более многочисленные партии, рассчитанные на нагрузку от свежеуложенного бетона, (например, балки перекрытия данных отверстий в плотине и балки перекрытия диффузоров отсасывающих труб ГЭС) изготавливались в условиях цеха способом непрерывно-поточного производства. При этом способе партии изделий перемещаются от поста к посту, от одной операции к другой. Такой тип производства называют еще агрегатно-поточным. Примером может служить технологический цикл изготовления и монтажа сборных трубопроводов ГАЭС, включавшим следующие операции (рис. 24А.5.):
-изготовление внутренней металлической оболочки толщиной 10 мм и арматурного каркаса из стержней стали класса А-lll диаметром 32-40 мм;
-монтаж внутренней облицовки, арматурного каркаса и наружной металлической опалубки на посту бетонирования;
-бетонирование сборного элемента на виброплощадке грузоподъемностью 200 т. Для формования изделия используется бетонная смесь, разогретая до 40-50°С перед укладкой в форму с многократным включением виброплощадки для гарантированного уплотнения армированного бетона;
-выдерживание бетона до требуемой отпускной прочности в утепленной опалубке, под специальным шатром, снабженным теплоизоляцией;
385

-нанесение противокоррозионного покрытия на полимерной основе на внутреннюю металлическую облицовку элементов;
-монтаж сборных звеньев водоводов, сварка внутренней металлической облицовки, с омоноличиванием швов между звеньями, инъекция швов цементным раствором.
Рис. 24А.5. Схема монтажа сборных железобетонных элементов Саратовской ГЭС 1 – козловой кран грузоподъемностью 200 т, 2 – сборный железобетонный элемент массой
200 т, 3 – сложный железобетонный элемент машинного зала ГЭС массой 25 т, 4 – сборные железобетонные элементы перекрытия, 5 – башенный кран КБГС-450, 6 – сборно-монолитные железобетонные элементы перекрытия помещений здания ГЭС нижнего бъефа, 7 – сборно-монолитные элементы перекрытия отсасывающей трубы
Общая продолжительность изготовления элемента с момента укладки бетонной смеси до последнего включения видроплощадки занимал 3-5 часов, продолжительность
набора 80% прочности от R28 с учетом твердения внутреннего покрытия составляла 7
суток.
Для осуществления описанного технологического процесса на строительной площадке Загорской ГАЭС в непосредственной близости от расположения будущих водоводов был создан специальный полигон с комплексом нестандартного оборудования и оснастки общей массой 1200 т. Комплекс включал две виброплощадки весом по 40 т, 10 комплектов опалубки с поддонами, крышками и формовачными кольцами для формования стыков, 7 комплектов устройств для антикоррозионного покрытия, 10 комплектов шатров, 4 электробадьи, стенд для гидравлических испытаний, кантователь тележка-установщик, три укрупнительных стенда и траверса для грузовых операций. Всего для первой очереди Загорской ГАЭС было изготовлено 368 элементов, смонтированных в две нитки водоводов первой очереди длиной по 720 м.
386
Полигоны открытого типа на строительных площадках гидроузлов чаще предназначены для выпуска простых изделий и имеют небольшой срок эксплуатации. Они оборудуются козловыми кранами, пропарочными камерами – ямными или напольными, небольшим арматурным цехом, площадками для подготовки и распалубки форм, складом готовой продукции. На таких полигонах изготавливаются, например, бетонные опалубочные блоки для внутренних частей массивных плотин, балки, плиты с малым содержанием арматуры, сваи, дорожные и парапетные ограждения, подпорные стенки небольшой высоты, лотки, малые архитектурные формы и другие несложные изделия, рассчитанные только на транспортные и монтажные нагрузки.
Более сложные изделия - с большим содержанием арматуры, с предварительным напряжением или большие партии однотипных изделий требуют заводских условий изготовления. В районах с суровым климатом также необходимо организовывать производство сборного железобетона в отапливаемых помещениях.
Типовой завод железобетонных изделий имеет обычно несколько специализированных пролетов, свой бетоносмесительный узел, арматурный цех, испытательный цех, площади для подготовки опалубки для разопалубки, выдержки изделий и склад готовой продукции. На таком производстве, как правило, применяется металлическая опалубка, бетоноукладчики, вибростолы, мостовые краны, автоматические линии для изготовления арматуры, пропарочные камеры с автоматизированным контролем термовлажностного режима, стенд для натяжения арматуры преднапряженных изделий. В составе такого завода или в отдельном помещении организуется ремонтномеханический цех, в котором изготавливаются закладные части, происходит ремонт металлической опалубки. Бетонная смесь подается во все пролеты по бетоновозной эстакаде или конвейерными линиями до бетоноукладчиков, которые распределяют ее по формам. После цикла пропаривания и распалубки изделия осматриваются, маркируются работниками технического контроля, отправляются на площадку выдерживания и после остывания - на склад готовой продукции. Одно-два изделия из каждой партии подвергается расчетной нагрузке в испытательном цехе.
24А.3. Транспорт и монтаж сборных элементов
Очень важным является процесс складирования и транспортировки готовых изделий к месту монтажа. На складе готовой продукции изделия укладываются на деревянные прокладки с высотой штабеля, не превышающей расчетную нагрузку. При этом строповочные петли должны сохраняться в рабочем положении. Неправильная погрузка, неприспособленное транспортное средство приводит к образованию трещин, околам, повреждению арматурных выпусков. Изделия должны иметь точки опирания в соответствии со схемой расчета на прочность. Перевозка сборных железобетонных изделий осуществляется специально приспособленной к определенной номенклатуре изделий транспортом. Плитные элементы перевозятся в субвертикальном положении на так называемых «пирамидах» с надежным раскреплением, балки и фермы – на балковозах в рабочем положении с опиранием согласно расчетному пролету. Обязательным условием должно быть высокое качество дорог.
Монтаж сборных бетонных и железобетонных элементов желательно проводить «с колес», без промежуточной разгрузки и складирования на стройке (рис.25.6.). Монтажные краны оборудуются специальными приспособлениями (траверсами, контователями и т.п.) для правильной строповки, во избежание повреждения изделий. Место установки элемента заранее подготавливается разметкой, очисткой, выправлением закладных крепежных деталей. После установки элемент временно раскрепляется до освобождения строп с чека монтажного крана. После расстроповки и проверки проектного положения элемент закрепляется сваркой закладных частей и подготавливается к омоноличиванию стыков.
387

Процесс омоноличивания стыков сборных железобетонных элементов заслуживает особого внимания. Для расчетных по прочности тяжело нагруженных элементов заранее проводятся специальные исследования стыков с целью выбора оптимальных параметров сварки, армирования, составов омоноличивающего бетона, режима выдержки стыков до набора проектной прочности. Бетонные поверхности стыкуемых элементов подготавливаются для обеспечения максимально надежного сцепления с омоноличивающим бетоном. На этих поверхностях удаляется цементная пленка и частично обнажается заполнитель. Бетон омоноличивания, как правило, имеет более высокую марку, чем бетон стыкуемых элементов и более высокую подвижность (пластичность). Сварка расчетной рабочей арматуры производится ванным способом с предварительным испытанием образцов ванной сварки. Опалубка стыка должна быть жесткой, герметичной с качественной поверхностью и только внешним раскреплением для того, чтобы не портить лицевых поверхностей изделий и архитектурных достоинств сооружения в целом.
Для вертикальных швов плиточных оболочек и ячеистых конструкций чаще всего употребляется петлевой стык, образуемый перехлестом петлевых выпусков арматуры и вертикальным дополнительным армированием. Стык закрывается опалубкойнащельникой и заполняется пластичным высокомарочным бетоном на мелком заполнителе. Уплотнение бетонной смеси в стыки осуществляется малогабаритным вибратором с гибким шлангом. При монтаже сборно-монолитных армопанельных конструкций стыки омоноличиваются не отдельной операцией, а во время бетонирования всего блока с предварительным перекрытием стыковых швов нащельниками. Омоноличивание стыков является технологически сложным и трудоемким процессом, а потому требует тщательного контроля качества работ.
Примерный состав бетона для омоноличивания стыков сборных железобетонных изделий.
Материал |
Расход на 1 куб. м бетона |
|
|
Лабораторный состав, кг |
Производственная |
|
|
дозировка |
Цемент М500 |
360 |
360 |
Песок |
750 |
0,490 куб.м |
Щебень 5-20 |
1175 |
0,79 куб.м |
Пластификатор, % |
0,3-0,35 |
0,3-0,35 |
От веса цемента |
|
|
Вода, л |
140 |
78 |
Осадка конуса 10-15 см |
|
|
Бетон омоноличивания должен отвечать следующим требованиям: Прочность в возрасте 180 суток В30,
Водонепроницаемость W12 Морозостойкость F300
388
ГЛАВА 24Б. Подводное бетонирование
24Б.1. Подводное бетонирование и требования к нему
Подводным бетонированием называется укладка бетона под водой без устройства перемычек и производства водоотливных работ.
Подводное бетонирование применяется при строительстве и реконструкции сооружений, ремонте сооружений, закреплении оболочек в пробуренных в скальных грунтах скважинах, выравнивании оснований, заполнении пустотелых железобетонных конструкций, при устройстве плит низких свайных ростверков.
Подводное бетонирование производится с применением труда водолазов в задачу которых входит: подготовка блоков бетонирования, установка опалубки, заделка щелей в опалубке, установка бетонолитных труб, наблюдение за производством работ.
В состав подготовительных работ входит: очистка бетонируемого участка от захламления; покрытие каменной постели мелким щебнем, песком, мешками с бетоном; устранение заилённости; снятие слабого слоя ранее уложенного бетона; удаление пятен нефти и мазута; водолазное обследование с составлением акта на скрытые работы.
При производстве подводного бетонирования применяются следующие типы опалубки: щитовая деревянная балластированная; деревометаллическая; металлическая оборачиваемая; железобетонная не оборачиваемая. Опалубка, применяемая при подводном бетонировании должна отвечать следующим требованиям: непроницаемость для цементного раствора, неизменяемость геометрической формы; простота при установке под водой; стыки должны иметь уплотнения. При установке опалубки с внешней стороны её укрепляют двумя рядами мешков, заполненных на 2/3 песком или камнем, которые в свою очередь могут быть дополнительно пригружены камнем. При использовании оборачиваемой опалубки соприкасающаяся с бетоном поверхность прикрывается мешковиной, пропитанной битумом или синтетическими полотнищами.
При укладке бетона должны соблюдаться следующие требования: укладываемый бетон не должен соприкасаться с водой; бетонирование должно производиться без перерывов до достижения проектных отметок.
24Б.2. Способы подводного бетонирования
Различают следующие способы подводного бетонирования:
1.Вертикально перемещающейся трубы (ВПТ).
2.Восходящего раствора (ВР).
3.Укладка бетонной смеси *кюбелями*.
4.Втрамбовывания бетонной смеси (метод *островка*).
5.Укладка бетонана в мешках.
6.Укладка бетона бетононасосами.
7.Инъекционный.
8.Гидровибрационный.
Взарубежной практике применяется подводное бетонирование известное под названиями *Колькрет* (Франция), *Препакт* (США), *Беното*(Франция), *Като* (Япония) и другие, являющиеся в той или иной степени модификациями выше перечисленных способов.
Способ вертикально перемещающейся трубы (ВПТ). Метод ВПТ применяется
при глубинах воды от 1 до 50м. Для подачи бетонной смеси применяются металлические инвентарные трубы Dт=200-300мм, с толщиной стенок 4-6мм. Бетонолитные трубы составляются из звеньев длиной 1-3м. Звенья труб по концам имеют фланцы. При соединении звеньев между фланцами устанавливаются резиновые прокладки. Бетон в трубу подаётся через воронку, диаметр которой назначается не менее 4диаметров бетонолитной трубы (Dв>4Dт ). Воронка выполняется из металла толщиной 3-5мм. Объём воронки назначается приблизительно равным максимальному объёму бетонолитной трубы.
389

Укладка бетона методом ВПТ производится в следующей последовательности: площадка бетонирования оборудуется подъездными путями, краном, лебёдкой, подъёмником; бетонолитная труба устанавливается на дно блока бетонирования; в трубе устанавливается пробка из дерева, опилок пакли или другого плавучего материала; трубу заполняют бетоном; приподнимают трубу; пробка выходит из трубы; бетон растекается по дну блока бетонирования; по достижении бетоном уровня выше конца трубы, трубу приподнимают на следующий уровень и так до окончания бетонирования блока.
Заглубление низа трубы в бетоне должно поддерживаться на уровне 0,8-1,5м. Интенсивность подачи смеси обеспечивают на уровне 0,3 куб.м/час на 1кв.м.
Радиус действия бетонолитной трубы (R) зависит от подвижности бетонной смеси и интенсивности бетонирования и может быть определён по зависимости R = h + 0,6 H, где h – высота расположения верха воронки над поверхностью воды, Н – глубина воды над верхом подводного бетона, но назначается не более 6м (Рис. 24Б.1). На уровне низа трубы давление столба бетона поддерживается в пределах 0,1 – 0,25МПа (10 – 25т/кв.м).
Рис. 24Б.1. Способ вертикально перемещающейся трубы 1 – электрическая лебедка, 2 – опоры эстакады, 3 – автосамосвал-бетоновоз, 4 –
эстакада, 5 – металлическая опалубка, 6 – уложенный бетон, 7 – вертикально перемещающаяся труба, 8 – приемный бункер
При прорыве воды в бетонолитную трубу бетонирование прекращают. Возобновление бетонирования возможно после достижения бетоном прочности 2МПа (200т/кв.м, 20кг/кв.см). Слой бетона толщиной 10 – 15см снимают. Перед возобновлением бетонирования проводят весь комплекс подготовительных работ.
Требования к бетонной смеси. Осадка конуса бетонной смеси должна быть 14 – 20см без применения вибрации и 6 – 12см с применением вибрации. В бетонную смесь, приготовленную из гравия или смеси гравия с 20 – 30% щебня вводят пластифицирующие добавки. Марка подводного бетона назначается на 10% выше, чем предусмотрено в проекте для возводимого сооружения.
Бетонирование прекращается при достижении укладываемым бетоном отметки на 10 – 12см превышающую проектную. При достижении бетоном прочности 2МПа (20кг/кв.см) верхний слой удаляется.
Бетонирование большой площади. Размеры блока бетонирования в плане под одну трубу назначаются не более 2R. При необходимости бетонирования больших площадей устанавливается группа труб с перекрытием всей площади. При этом ширину блока и расстояние между осями труб назначают не более 6м. Приёмный бункер устраивают на
390

несколько труб. Бетон подают с помощью хоботов. Хобот и воронки оборудуются заслонками.
Оборудование для подачи бетона. Место бетонирования оснащается подмостями, понтонами, бадьями, бетононасосами, вагонетками, транспортёрами.
Контроль за ходом бетонирования. Для контроля заглубления трубы на неё наносятся метки. Уровень бетона контролируется отвесом.
Эффект вибрирования. Вибрирование труб позволяет сократить расход цемента на 10 – 12% и увеличить долговечность сооружения. На трубу обычно устанавливают два вибратора – на конце и в середине.
Способ восходящего раствора (ВР) (рис. 26.2). Метод восходящего раствора (ВР) или метод раздельного бетонирования применяется на глубинах от 1 до 50м. Сущность метода заключается в том, что бетонируемый блок заполняется камнем или щебнем, а затем нагнетается цементный раствор, который распространяясь в стороны от трубы и поднимаясь с низу в верх вытесняет из пустот в наброске воду.
Рис. 24Б.2. Способ восходящего раствора 1 – электрическая лебедка, 2 – опоры эстакады, 3 – автосамосвал-бетоновоз, 4 –
эстакада, 5 – металлическая опалубка, 6 – уложенный бетон, 7 – вертикально перемещающаяся труба, 8 – приемный бункер, 9 – трубы для подачи раствора, 10 – каменная наброска
При бетонировании методом ВР применяется камень крупностью 150400мм, щебень крупностью 40150мм, песок крупностью – 2,5мм. Прочность камня должна быть не менее 10МПа (100кг/кв.см ). Объём пустот в каменной отсыпке должен составлять 45%. Прочность бетона должна быть не менее 15МПа (150кг/кв.см).
Для подводного бетонирования методом ВР применяются бетонолитные трубы d=37 – 100мм. Металлические воронки должны иметь скос не менее 30. Пробки в бетонолитные трубы перед началом бетонирования устанавливаются при применении труб d>75мм на глубине H>10м. Радиус действия бетонолитных труб принимается при заполнении блока бетонирования камнем R=3м и при заполнении щебнем R=2м. Расстояние между трубами назначается в пределах 2-2,5м. Предельно рациональная площадь действия одной трубы устанавливается до 18кв.м. Интенсивность подачи раствора обеспечивается на уровне 0,3куб.м/час на 1кв.м бетонируемой площади.
391
Различают две разновидности бетонирования методом ВР – напорный и
безнапорный.
Безнапорный способ. При безнапорном способе бетонирование осуществляется через заранее установленную шахту, исключающую заклинивание трубы при её подъёме. Отверстия в стенках шахты назначаются размером составляющим 2/3 от наименьшего размера заполнителя. Площадь всех отверстий должна быть не менее 50% от общей площади поверхности шахты. Заглубление трубы в укладываемом бетоне поддерживается на уровне 0,8м.
Напорный способ. При этом способе трубы устанавливаются ярусами. По мере подъёма раствора в работу включаются трубы следующего более высокого яруса. После окончания бетонирования трубы из бетонного массива не вытаскивают. Верхняя часть труб, расположенная вне блока бетонирования срезается. Превышение труб над уровнем воды может быть определена по формуле:
h=( R-1,5D H)/3D, где R- радиус действия трубы,
D – средняя крупность заполнителя,
Н – высота воды над уровнем раствора.
Практически рекомендуется превышение трубы над уровнем воды назначать не менее 5м.
По сравнению с ВПТ метод ВР является вспомогательным и применяется при невозможности или не экономичности применения метода ВПТ. При применении метода ВР снижается расход цементного раствора, но увеличивается расход металлических труб, заполнение пустот не достаточно надёжно. Во избежание расслоения блока бетонирования перерывы в работе должы быть абсолютно исключены.
Метод укладки бетона кюбелями. Метод укладки бетона кюбелями применяется на глубинах до 20м в сооружениях не требующих прочности бетона выше 200кг/кв.см. К таким сооружениям относятся конструкции с защитной оболочкой, работающих на вертикальную нагрузку (оболочки большого диаметра, опускные колодцы, колонныоболочки), выравнивающие бетонные подготовки оснований под сооружения.
Для производства работ используется бетон марки М200 с осадкой конуса 1-5см. Первый слой бетона содержит цемента на 15-20% больше расчётного. Кюбели (бункер, ящик, бадья, грейфер) применяются вместимостью 0,1- 3куб.м.
Порядок укладки бетона кюбелями следующий. Полностью заполненный бетонной смесью кюбель подаётся под воду. Вдавливается в ранее уложенную смесь на 5-10см. Производится его раскрытие. Следующая порция смеси укладывается до начала схватывания предыдущей.
При производстве бетонирования исключается вытекание цементного раствора, проникновение воды в кюбель, сбрасывание смеси через толщу воды.
Недостатками метода являются: слоистость укладки, частичный размыв смеси при разгрузке кюбеля, необходимость использовния труда водолазов для контроля за укладкой бетонной смеси, её разравнивания и удаления шлама.
Способ втрамбовывания (способ *островка*) (рис. 24Б.3) . Метод втрамбовывания (*островка*) применяется: при возведении сооружений на глубинах не более 1,5- 2,0м; в сооружениях не требующих армирования; с маркой бетона не выше 300; для выравнивания оснований на отлогих скальных берегах; при проведении ремонтновосстановительных работ на мелководье; при возведении берегозащитных сооружений; при возведении бетонных низких свайных ростверков.
392

Рис. 24Б.3. Способ втрамбовывания 5 – металлическая опалубка (стена ограждения), 8 – приемный бункер
Требование к материалам. Марка укладываемого бетона принимается на 20% выше требуемого в сооружении. Осадка конуса бетонной смеси 5-10см. Наименьший плановый размер блока должен быть больше толщины бетонирования.
Порядок проведения работ. Работы выполняются в следующей последовательности: устанавливается опалубка, предохраняющая смесь от размыва; с помощью бетонолитной трубы или кюбеля в одном из углов блока бетонирования создаётся островок, размеры которого не регламентируются; по контуру островка подаются порции бетонной смеси в пределах времени начала схватывания предыдущей порции; производится втрамбовывание свежей бетонной смеси в ранее уложенный бетон с помощью пневмотрамбовок, электротрамбовок, виброплощадок, вибробулав; уплотнение бетонной смеси глубинными вибраторами.
Для производства работ требуются: кран, плавучий кран, кюбель, грейфер, бадья, вибраторы, бетоновозы, бетоносмесительный узел.
Основные требования при производстве работ. Откос островка должен быть 3545*, возвышение островка над уровнем воды должно быть не менее 30см, порции бетонной смеси укладываются не ближе 20-40см от уреза воды. Работа вибратора вблизи откоса не допускается. Укладка бетона ведётся без перерывов. Зона схватывания и твердения ранее уложенного бетона не затрагивается. Последующая порция бетона укладывается до начала схватывания предыдущей порции. Сплыв смеси поверх откоса в воду не допускается. Продолжение работ после вынужденного перерыва возможно после достижения бетоном 50% прочности и подготовки поверхности ранее уложенного бетона ( снятие верхнего ослабленного слоя бетона, удаление шлама и т.п).
Достоинством метода является отсутствие обязательной необходимости в разбивке на блоки бетонирования. Недостаток – большая трудоемкость и высокая интенсивность подачи смеси.
Метод укладки бетона в мешках. Укладку бетона в мешках применяют при ремонтно-восстановительных работах, ликвидациях аварий, заделке каверн, возведении неответственных конструкций на глубинах до 2м., выравнивании дна, в качестве подводной опалубки, уплотнении инвентарной опалубки.
Мешки применяются вместимостью от 2 до 50л. Для мешков используется прочная, но редкая ткань, способная пропускать воду, воздух и частично цементное молоко. Мешки свежее приготовленным бетоном заполняются на 2/3 объёма. Раствор бетона изготавливается с осадкой конуса 1-7см. Максимальная крупность заполнителя от
393
10 до 200мм. После заполнения мешки завязываются или зашиваются. Мешки вместимостью более 50л заполняются бетоном под водой с помощью бетононасоса.
Укладка мешков производится в следующем порядке: производится подготовка места укладки мешков; краном по одному или в контейнере мешки подаются водолазу под воду с соблюдением мер безопасности; мешки укладываются на основание широкой плоскостью с перевязкой швов; курсы мешков армируются прутьями и прошиваются штырями d=10-20мм, l=30-40cм.
Метод укладки бетона бетононасосами. Метод укладки бетона бетононасосами применяется при ремонтно-восстановительных работах. Для производства работ применяются бетононасосы производительностью 14-20куб.м/час при давлении в бетоноводе 0,7-0,8МПа.
Бетонирование осуществляется в следующем порядке. Готовится место укладки бетона. Над бетононасосом устанавливается бункер бетономешалки. По бетоноводу бетон подаётся в бетонолитную трубу, подвешенную к гаку крана над блоком бетонирования, Конец трубы в начале устанавливается на 10см выше основания блока. После заполнения блока на 1м выше конца трубы её поднимают на 20-30см и так до окончания бетонирования.
Инъекционный метод подводного бетонирования. Инъекционный метод применяется при ремонтных работах. Для производства работ используются бетононасосы производительностью 1-3куб.м/час.
Бетонирование осуществляется в следующем порядке. Производится подготовка места укладки бетона. Устанавливается опалубка. Опалубка в нижней части оснащается штуцером, а в верхней - выходным отверстием. Шланг бетононасоса присоединяется к штуцеру. Раствор бетона беспрерывно подаётся в бетонируемую полость. Подача бетона осуществляется до начала выхода раствора через отверстие в верхней части опалубки. Полость перед бетонированием может заполняться камнем или щебнем. Через 20-25мин. работы бетононасоса призводится его прокачка в течение 15-20сек.
Гидровибрационный метод подводного бетонирования. Известны две модификации гидровибрационного метода: 1. блок бетонирования заполняется инертными составляющими бетона, подаётся цементное молоко с одновременным вибрированием заполнителя; 2. блок бетонирования заполняется цементным раствором, крупный заполнитель подаётся в блок бетонирования с одновременным вибрированием раствора. Главный недостаток этого метода – большой расход цемента.
394