
методички / 4021 ЭИ
.pdfКонтрольные вопросы
1.Назовите средства контроля геометрии рельсов.
2.Как влияет геометрия рельсов на эксплуатационную надежность железнодорожного пути?
3.Перечислите причины разрушения рельсов.
4.На каком расстоянии контролируют шаблонами размеры и форму поперечного сечения от торца рельса?
5.Какие стандарты на рельсы предъявляют высокие требования к их геометрии?
ЛАБОРАТОРНАЯ РАБОТА № 4
ДЕФЕКТЫ СВАРКИ РЕЛЬСОВ
Цель работы: ознакомление с теоретическими и практическими аспектами сварки рельсов и получение первоначальных навыков выявления дефектов.
В ходе работы студенту необходимо научится достоверно определять наличие, форму и расположение дефекта, а также его природу и условия, способствующие появлению (доэксплуатационные, эксплуатационные).
Краткие теоретические сведения
Для соединения рельсов широко применяются электроконтактная и алюминотермитная сварка. При сварке рельсов вследствие нагрева металла до высоких температур, достигающих температуры плавления, и большой пластической деформации происходит значительное изменение микроструктуры в зоне шва и прилегающих зонах, называемых зонами термического влияния. При этом образуется следующая зональная структура сварного шва (рис. 8).
К дефектам, полученным электроконтактной сваркой, сварного шва относятся:
рыхлости (пережог);
холодная сварка;
пузыри (в головке, шейке и подошве);
непровары (обычно в головке);
кратерная усадка и поры (в головке, шейке и подошве). Дефектами алюминотермитной сварки рельсов являются:
газовые раковины, пузыри, поры;
непровары;
оплавление;
горячие трещины в литом металле и усадочная раковина;
21
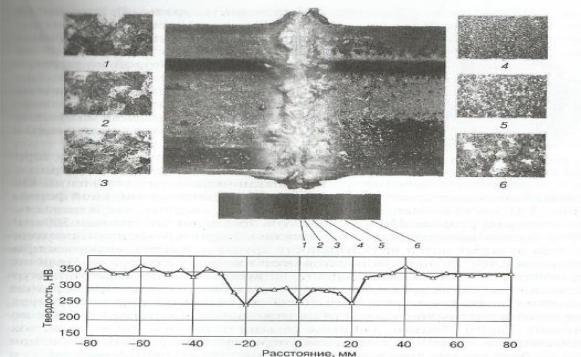
шлаковые включения;
повышенная хрупкость;
недостача металла;
смещение половин облива, смещение головок рельсов и образование киля.
Рис. 8. Сварной шов и его зональная структура: 1,2,3,4,5 – зоны соответственно сварного соединения, неполного расплавления металла, сорбитизации после перегрева, сорбитизации без
перегрева, высокого отпуска; 6 – основной металл
Взоне сварных штыков, полученных электроконтактной сваркой, возникают следующие дефекты: 16.3, 17.2 – выкрашивания; 26.3, 27.3 – трещины в головке; 46.3, 47.3 – местное смятие и износ; 56.3, 57.3 – трещины в шейке; 66.3, 67.3 – трещины в подошве; 76.3, 77.3 – изломы; 86.3 – изгибы. Эти дефекты различаются местом начала разрушений (в головке, в шейке или в подошве), а также временем возникновения – до или после окончания срока гарантий, устанавливаемого рельсосварочным предприятием. В тех случаях, когда в пути не удается определить место начала и причину разрушений сварного стыка, дефекты регистрируют под кодом 99.3.
Взоне сварных стыков, полученных алюминотремитной сваркой, могут возникнуть следующие дефекты: 16.4, 17.4 – выкрашивание; 26.4, 27.4 – трещины в головке; 46.4, 47.4 – местное смятие и износ; 56.4, 57.4 – трещины в шейке; 66.4, 67.4 – трещины в подошве; 76.4, 77.4 – изломы; 86.4 – изгибы. Если в пути не удается определить место начала и причину разрушений сварного стыка, дефекты регистрируют под кодом 99.4.
22
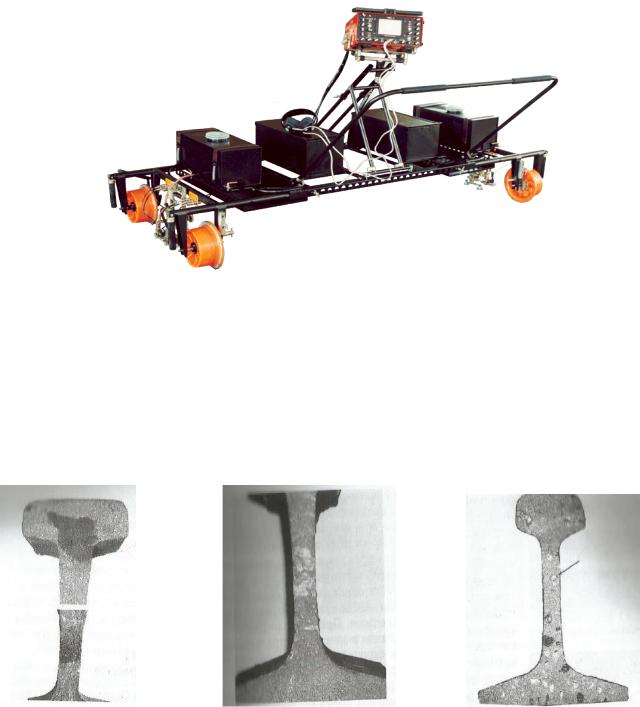
Описание лабораторной установки, измерительного оборудования и образцов
Для выполнения работы необходимы: ультразвуковой дефектоскоп РДМ-3 (рис. 9), который применяется для выявления дефектов в стыках рельсов, свариваемых контактным способом в условиях РСП и в полевых условиях – ПРСМ.
Рис. 9. Ультразвуковой дефектоскоп РДМ-3
Для выполнения поиска дефекта используются образцы с изломами сварных стыков, полученных электроконтактной и алюминотермитной сваркой (рис. 10–18).
Рис. 10. Излом сварного |
Рис. 11. Излом сварного шва |
Рис. 12. Пузыри в изломе |
шва из-за рыхлости, |
вследствие холодной сварки |
сварного шва |
возникшей в результате |
|
|
пережога, дефекты 26,3 и 56,3 |
|
|
23

Рис. 13 . Излом сварного стыка |
Рис. 14. Продольное расслоение |
Рис. 15. Усталостная трещина |
из-за кратерной усадки |
шейки в сварном шве |
от кромки подошвы, дефект 66.3 |
Рис. 16. Разрушение алюминотермитного стыка, связанное с газовыми раковинами, пузырями и порами
Рис. 17. Разрушение алюминотермитного |
Рис. 18. Разрушение алюмотермитного |
стыка, связанное с непроваром |
стыка, связанное со шлаковыми включениями |
включениями |
|
24
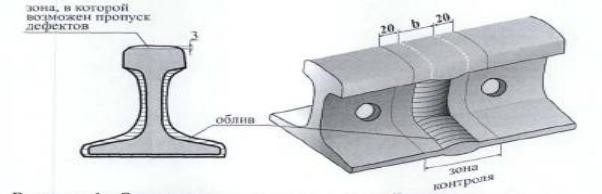
ОБЩИЕ ПОЛОЖЕНИЯ
1.УЗК применяют для выявления дефектов типа пор, шлаковых включений, непроваров и трещин в сварных стыках рельсов,образовавшихся при сварке или развившихся в процессе эксплуатации в головке, в шейке и подошве (соответственно коды: 26.4, 56.4 и 66.4).
2.При УЗК используют:
-эхо-метод для выявления внутренних дефектов по всему сечению сварного стыка;
-зеркальный метод для выявления несплавлений торца рельса с металлом шва в области головки, шейки и продолжения ее в подошву.
Примечания
1 Дефекты сварки могут быть не выявлены, если они расположены у поверхности катания головки рельса на глубине до 3 мм (рисунок 19).
2 При УЗК сварных стыков рельсов, имеющих болтовые отверстия в концевых участках на расстоянии менее 330 мм от торцов рельсов, зеркальный метод контроля стыков в области шейки и ее продолжения в подошву не применяют, поэтому выявление непроваров в этих зонах не гарантируется.
Рис. 19. Зона стыка алюминотермитной сварки рельсов, в пределах которой должно быть обеспечено прозвучивание при УЗК
3.При УЗК сварных стыков рельсов применяют схемы прозвучивания в соответствии с таблицей 8.
4.Концевые участки рельсов длиной 300 мм, подлежащие алюминотермитной сварке, должны быть проверены переносными дефектоскопами по методике вторичного контроля рельсов или при сплошном контроле рельсов съемными дефектоскопами с регистраторами не более чем за 10 дней до производства сварочных работ.
5.Приемочный УЗК стыков алюминотермитной сварки рельсов осуществляют при отсутствии на них предохранительных накладок, при температуре металла в области сварного стыка не более плюс 60 °С и при температуре окружающего воздуха не ниже плюс 5 °С.
25
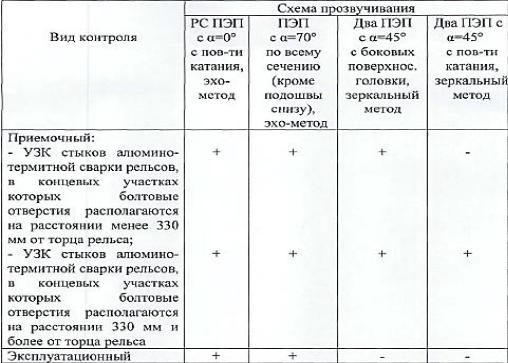
Таблица 8
Схемы прозвучивания УЗК при проведении приемочного и эксплуатационного контроля
6.Стыки алюминотермитной сварки рельсов подвергают УЗК после обрезки прибыльной части сварного шва, удаления литниковой системы и механической обработки в области поверхности катания и боковых поверхностей головки в соответствии
стребованиями ТУ 0921-127-01124323-2005
7.На время проведения УЗК стыков алюминотермитной сварки рельсов со снятыми предохранительными накладками разрешается пропуск поездов со скоростью не более 40 км/час.
8.К контролю стыков алюминотермитной сварки с оценкой их качества по результатам НК допускаются операторы не ниже 6-го разряда, имеющие опыт работы по контролю стыков электроконтактной сварки рельсов не менее 1 года, прошедшие специальное практическое обучение по УЗК стыков алюминотермитной сварки рельсов и получившие документ установленного образца, изучившие ТУ 0921-127-01124323-2005 и данную ТИ.
9.Приемочный УЗК стыков алюминотермитной сварки рельсов выполняют операторы дистанции пути.
10.УЗК стыков алюминотермитной сварки рельсов выполняет бригада из двух операторов, один из которых приказом начальника дистанции пути назначается руководителем бригады.
11.Ответственность за выполнение и оформление результатов контроля в соответствии с требованиями ТИ возлагается на оператора, непосредственно
проводившего контроль.
26
12.Обеспечение контролепригодности и подготовка сварных стыков к контролю в условиях эксплуатации (снятие, при необходимости, клеммных болтов, очистка от грязи, мазута, балласта) не входят в обязанности оператора, а осуществляются монтерами дистанции пути.
13.Ответственность за организацию УЗК стыков алюминотермитной сварки рельсов возлагается на начальника дистанции пути.
Правила безопасного выполнения работы
К работе с дефектоскопом допускаются студенты, прошедшие инструктаж по технике безопасности и пожарной безопасности при работе с электроустановками. Перед началом работы следует ознакомиться с общим устройством прибора и методами работы с ним. Запрещается разбирать прибор, наносить механические повреждения и нарушать алгоритмы работы.
Порядок выполнения работы
Перед началом работы с дефектоскопом РДМ-3 следует одеть спецодежду, получить целевой инструктаж, в ходе которого определяется порядок работы, правила безопасного производства работ. Получение целевого инструктажа подтверждается подписью. ВНИМАНИЕ! Производить подключение электронного блока к дефектоскопной тележке следует только в отключенном состоянии аккумуляторных батарей. При проверке работы дефектоскопа запрещается касаться открытых токоведущих частей. При работе с дефектоскопной тележкой на оператора могут воздействовать следующие вредные факторы: ультразвук, генерируемый электронным блоком дефектоскопа; электромагнитное поле, формируемое контактным проводом; локальная нагрузка на слуховой и 23зрительный аппарат; интенсивная физическая нагрузка; ветер, осадки и низкая температура окружающей среды; испарения от железнодорожного полотна. К опасным факторам относятся: высокое напряжение в контактном проводе над головой; высокое напряжение в электронном блоке дефектоскопа; движение поездов по контролируемому участку пути.
Ультразвуковой контроль качества алюминотермитной сварки выполняется согласно инструкции ТИ 07.22-2000
ПОДГОТОВКА К КОНТРОЛЮ
1) Провести подготовку дефектоскопа:
а) выполнить внешний осмотр дефектоскопа;
27
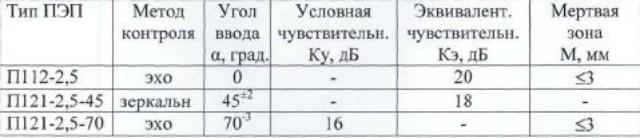
б) проверить работоспособность ПЭП и техническое состояние соединительных кабелей, устранить замеченные неисправности;
в) настроить (проверить) значения основных параметров контроля на соответствие требованиям таблицы
Таблица 9
Значения основных параметров УЗК стыков алюмино-термитной сварки рельсов
Примечание. Если измеренное значение угла ввода луча не соответствует требуемому, то ПЭП необходимо изъять из эксплуатации. Результаты проверки основных параметров контроля занести в Рабочий журнал.
ПРИМЕЧАНИЯ
1.Угол ввода и мертвую зону необходимо проверять, а условную и эквивалентную чувствительность настраивать ежедневно перед проведением УЗК и в случае замены ПЭП
2.Эквивалентную чувствительность эхо-метода для ПЭП с углом ввода α = 0 необходимо настраивать по донному сигналу от подошвы рельса на бездефектном участке вне области сварного стыка.
3.Условную чувствительность эхо-метода для ПЭП с углом ввода α = 70° необходимо настраивать по отверстию диаметром 6 мм, расположенному в СО-ЗР на глубине 44 мм.
4.Эквивалентную чувствительность зеркального метода при контроле стыков алюминотермитной сварки в области головки рельса двумя ПЭП с углами ввода а=45° необходимо настраивать при установке ПЭП на противоположные боковые поверхности головки рельса вне зоны сварного стыка в положения, соответствующие максимальной амплитуде прошедшего (опорного) сигнала.
5.Эквивалентную чувствительность зеркального метода для контроля стыков алюминотермитной сварки в области шейки и подошвы рельса двумя ПЭП с углами ввода
α= 45° необходимо настраивать при установке ПЭП на поверхность катания головки рельса навстречу друг другу в положения, соответствующие максимальной амплитуде донного (опорного) сигнала.
28
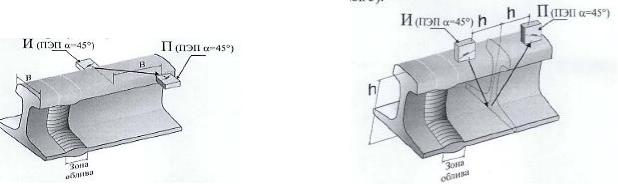
Рис. 20. Схема расположения ПЭП П121-2,5-45° |
Рис. 21. Схема расположения ПЭП П121-2,5-45° |
при настройке на эквивалентную чувствительность |
при настройке на эквивалентную чувствительность |
для контроля сварного стыка зеркальным методом |
для контроля сварного стыка в области |
в области головки рельса |
шейки зеркальным методом |
6.Провести визуальный осмотр стыков алюминотермитной сварки рельсов: осмотр качества обработки и очистки поверхностей рельса в области сварного стыка; осмотр с целью поиска в области сварного стыка возможных трещин, непроваров, раковин и шлаковых включений, выходящих на поверхность.
7.Проверить выполнение требований контролепригодности стыков алюминотермитной сварки рельсов.
8.Температура металла в зоне сварного стыка должна быть не выше плюс 60 °С.
9.Стыки алюминотермитной сварки рельсов считаются контролепригодными, если: - облив стыка в области поверхности катания и боковых поверхностей головки
механически обработан в соответствии с требованиями ТУ 0921-127-01124323-2005;
-ширина облива в области шейки и подошвы не превышает 85 мм;
-на поверхностях шейки и перьев подошвы в пределах 300 мм от облива отсутствуют остатки литниковой системы, брызги металла, грязь. Примечание - Стыки алюминотермитной сварки рельсов, в концевых участках которых болтовые отверстия располагаются на расстоянии менее 330 мм от торца рельса, являются контроленепригодными в области шейки для зеркального метода контроля.
10. Подготовить поверхности сварного стыка к УЗК: с помощью металлической щетки, шабера и ветоши очистить контролируемые поверхности рельса в пределах 300 мм от центра сварного стыка.
11. При удовлетворительном состоянии поверхностей рельса в области сварного стыка протереть их ветошью и покрыть слоем контактирующей жидкости. В качестве
контактирующей жидкости может быть использовано трансформаторное масло ГОСТ 982-80 или любое минеральное масло без механических включений, вязкость которого должна подбираться с учетом температуры окружающего воздуха и металла контролируемых рельсов.
Примечание. Средний расход контактирующей жидкости для обеспечения акустического контакта при УЗК одного стыка алюминотермитной сварки рельсов составляет не более 200 мл.
29
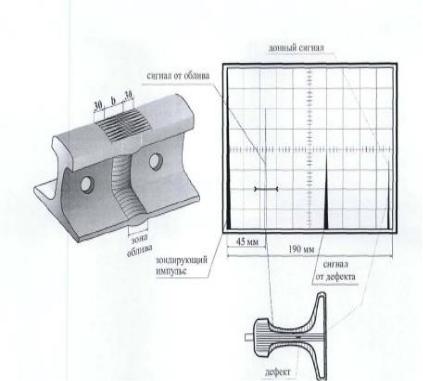
ПРОВЕДЕНИЕ ПРИЕМОЧНОГО УЗК СТЫКОВ АЛЮМИНОТЕРМИТНОЙ СВАРКИ РЕЛЬСОВ
1. УЗК стыков алюминотермитной сварки рельсов выполняют в последовательности:
1.1.Контроль сварного стыка эхо-методом PC ПЭП П112-2,5 в области головки, шейки и ее продолжения в подошву с поверхности катания рельса;
1.2.Контроль сварного стыка эхо-методом при перемещении ПЭП П121-2,5-70° по всему периметру рельса (кроме подошвы снизу);
1.3.Контроль сварного стыка зеркальным методом в области головки при сканировании двумя ПЭП П121-2,5-45° по боковым поверхностям головки;
1.4.Контроль сварного стыка зеркальным методом в области шейки при сканировании двумя ПЭП П121-2,5-45° с поверхности катания головки (для сварных стыков, в которых расстояние от торца рельса до первого болтового отверстия составляет 330 мм и более).
Примечание. При УЗК сварных стыков рельсов, имеющих болтовые отверстия в концевых участках на расстоянии менее 330 мм от торцов рельсов, зеркальный метод контроля стыков в области шейки и ее продолжения в подошву не применяют.
Рис. 22. Контроль сварного стыка PC ПЭП П112-2,5 в области головки, шейки и ее продолжения в подошву с поверхности катания рельса
30