
методички / 4021 ЭИ
.pdf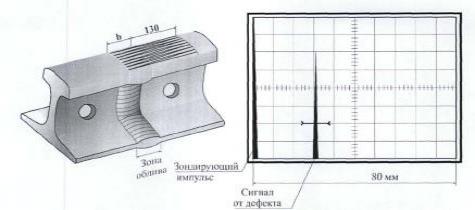
2.Проконтролировать сварной стык эхо-методом PC ПЭП П112-2,5 в области головки, шейки и ее продолжения в подошву с поверхности катания рельса
2.1.Включить дефектоскоп в режим, соответствующий работе с PC ПЭП П112-2,5.
2.2.Установить на экране дефектоскопа развертку длительностью, соответствующей глубине 190 мм.
2.3.Проконтролировать сварной стык с поверхности катания рельса, перемещая PC ПЭП с шагом сканирования 3–4 мм по всей ширине головки в пределах зоны сварки и обеспечивая акустический контакт, вести наблюдение за экраном дефектоскопа.
2.4.Признаком обнаружения дефекта является появление на экране дефектоскопа эхо-сигнала, амплитуда Идз которого превышает уровень срабатывания АСД (кроме эхосигнала от облива и от подошвы рельса).
2.5.При обнаружении дефекта в любой зоне сварного стыка необходимо измерить глубину Н залегания, условный размер AL выявленного дефекта, при обнаружении его в головке рельса и коэффициент Кдэ выявляемости, зарегистрировать в Карте дефектного стыка .
3.Проконтролировать сварной стык эхометодом ПЭП П121-2,5-70°.
3.1. Переключить дефектоскоп в режим, соответствующий работе
сПЭП П121-2,5-70°.
3.2.Установить на экране дефектоскопа развертку длительностью, соответствующей глубине 80 мм.
3.3.По схеме поперечно-продольного перемещения ПЭП с шагом продольного сканирования 3–4 мм, обеспечивая акустический контакт, проконтролировать сварной стык
сдвух сторон, ведя наблюдение за экраном дефектоскопа, в следующей последовательности: в области головки рельса с поверхности катания (рис. 23) и с боковых поверхностей (рис. 24), шейки с боковых поверхностей (рис. 25) и перьев подошвы (рис. 26).
Примечание. При наличии первого болтового отверстия на расстоянии менее 115 мм от торца рельса зона сварного стыка, расположенная напротив отверстия, оказывается проконтролированной только прямым лучом, поэтому выявление дефектов в шейке рельса не гарантируется.
Рис. 23. Контроль сварного стыка ПЭП П121-2,5-70° в области головки с поверхности катания рельса
31
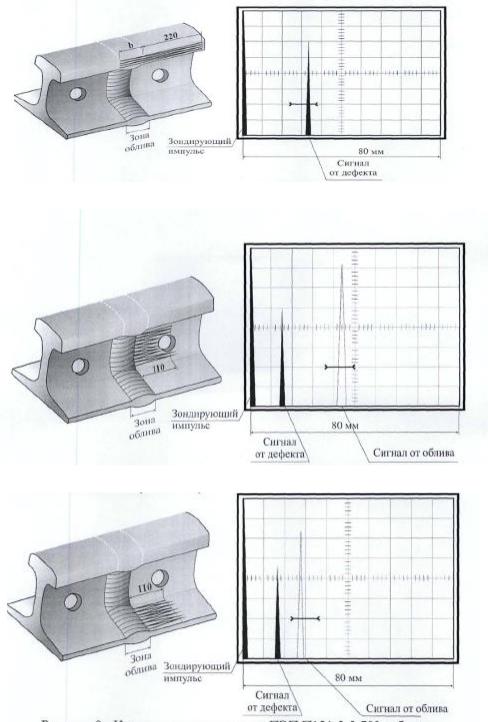
Рис. 24. Контроль сварного стыка ПЭП П121-2,5-70° в области головки с боковых поверхностей рельса
Рис. 25. Контроль сварного стыка ПЭП П121-2,5-70° в области шейки с боковых поверхностей рельса
Рис. 26. Контроль сварного стыка ПЭП П121-2,5-70°в области перьев подошвы сверху рельса
3.4. Признаком обнаружения дефекта является появление на экране дефектоскопа эхо-сигнала, амплитуда Пдэ которого превышает уровень срабатывания АСД и перемещающегося по экрану при поперечном сканировании ПЭП.
Примечание. На экране возможно возникновение ложных эхосигналов, обусловленных отражениями от неровностей облива как поперечной волны, так и, в ряде случаев, поверхностной волны (для уточнения причины возникновения эхо-сигнала следует проконтролировать сечение с предполагаемым дефектом с двух сторон сварного стыка и определить координаты L расположения предполагаемого дефекта).
32
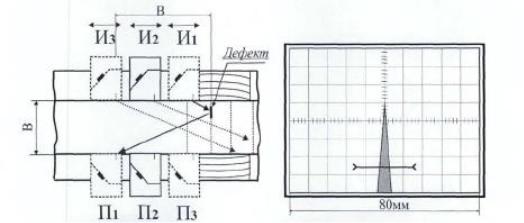
3.5.При обнаружении дефекта в любой зоне сварного стыка необходимо измерить глубину Н залегания, условный размер AL выявленного дефекта и коэффициент Кдэ выявляемости, зарегистрировать в Карте дефектного стыка. При контроле сварного стыка
вобласти перьев подошвы и шейки с боковых поверхностей глубину Н расположения дефекта не измеряют.
4.Проконтролировать сварной стык зеркальным методом двумя ПЭП П121-2,5-45°
вобласти головки рельса.
4.1.Переключить дефектоскоп в режим, соответствующий работе по раздельной схеме с двумя ПЭП П121-2,5-45°. Подключить один ПЭП П121-2,5-45° к излучающему каналу дефектоскопа, а другой ПЭП П121-2,5-45° к приемному каналу дефектоскопа.
4.2.Установить на экране дефектоскопа развертку длительностью, соответствующей глубине 80 мм (рис. 26).
4.3.Проконтролировать сварной стык в области головки по схеме, показанной на рис. 27, для чего:
- установить приемный ПЭП и излучающий ПЭП на противоположные грани головки рельса так, чтобы акустические оси ПЭП были направлены в сторону сварного стыка;
- проконтролировать сварной стык следующим образом: установить приемный ПЭП от сварного стыка на расстояние равное ширине головки рельса и зафиксировать его неподвижно, излучающим ПЭП провести сканирование по противоположной грани головки рельса в зоне возможного приема сигнала, зеркально отраженного от дефекта. Затем, передвинуть приемный ПЭП на 10 мм в сторону сварного стыка, снова провести сканирование излучающим ПЭП и т.д.
Примечание. Для соблюдения параметров сканирования рекомендуется использовать сканирующее устройство.
Рис. 27. Контроль сварного стыка зеркальным методом двумя ПЭП П121-2,5-45° в области головки с боковых поверхностей рельса
33
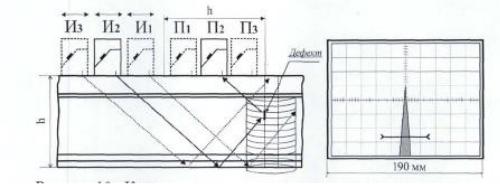
4.4.Признаком обнаружения дефекта является появление в средней части развертки на экране дефектоскопа зеркально отраженного от дефекта сигнала, временное положение которого на экране дефектоскопа при сканировании не меняется.
4.5.Провести сканирование с противоположной стороны сварного стыка согласно п.п.8.4.3-8.4.4.
4.6.При обнаружении дефекта измерить максимальную амплитуду Пдз зеркально отраженного сигнала и записать коэффициент Кдз выявляемости выявленного дефекта в Карту дефектного стыка .
5.Проконтролировать сварной стык зеркальным методом двумя ПЭП П121-2,5-45°
вобласти шейки и ее продолжения в подошву рельса (для сварных стыков, в которых расстояние от торца рельса до первого болтового отверстия составляет 330 мм и более).
5.1.Установить на экране дефектоскопа развертку длительностью, соответствующей глубине 190 мм (рис. 28).
Рис. 28. Контроль сварного стыка зеркальным методом двумя ПЭП П121-2,5-45°
вобласти шейки и ее продолжения в подошву с поверхности катания рельса
5.2.Проконтролировать сварной стык в области шейки с поверхности катания рельса по схеме, указанной на рис. 28, для чего:
- установить приемный ПЭП и излучающий ПЭП на головку рельса так, чтобы акустические оси ПЭП были направлены в сторону сварного стыка;
- проконтролировать сварной стык следующим образом: установить приемный ПЭП от сварного стыка на расстояние равное высоте h контролируемого рельса и зафиксировать его неподвижно, излучающим ПЭП провести сканирование по головке рельса в зоне возможного приема сигнала, зеркально отраженного от дефекта. Затем, передвинуть приемный ПЭП на 10 мм в сторону сварного стыка, снова провести сканирование излучающим ПЭП и т.д. Сканирование вести по поверхности катания строго над шейкой рельса.
Примечание. Для соблюдения параметров сканирования рекомендуется использовать сканирующее устройство.
34
5.3.Признаком обнаружения дефекта является появление на развертке экрана дефектоскопа зеркально отраженного от дефекта сигнала, временное расположение которого на экране дефектоскопа при сканировании не меняется.
5.4.Переставить ПЭП на противоположную сторону сварного стыка и проконтролировать сварной стык в области шейки рельса
5.5.При обнаружении дефекта измерить максимальную амплитуду Пдз зеркально отраженного сигнала и записать коэффициент Кдз выявляемости выявленного дефекта в Карту дефектного стыка.
6.Если в процессе УЗК температура окружающего воздуха изменилась более чем на 10 °С относительно температуры, при которой осуществлялась проверка (настройка) дефектоскопа, необходимо проверить угол ввода и настройку чувствительности для всех используемых ПЭП и, при необходимости, ввести соответствующие поправки в настройки глубиномера и чувствительности.
Требования к отчету
При обработке результатов контроля следует сверять достоверность полученных значений глубины дефекта по установленной погрешности, которая не должна отличаться от заданного более чем на 20 % или более чем на 0,2 мм. В этом случае необходимо произвести настройку дефектоскопа повторно в соответствии с требованиями инструкции по эксплуатации. Отчет должен содержать карту объекта контроля с указанием места расположения дефекта, его формы, размеров, глубины залегания и оформленным в соответствии с требованиями нормативной документацией.
Контрольные вопросы
1.Что представляет из себя метод ультразвуковой дефектоскопии?
2.Перечислите основные методы сварки рельсов?
3.Какая структура сварного шва?
4.Назовите дефекты сварного шва, полученные электроконтактной сваркой?
5.Назовите дефекты сварного шва, полученного алюминотермитной сваркой?
6.Как устроен ультразвуковой дефектоскоп?
7.Какие особенности ультразвукового контроля стыков после алюминотермитной сварки рельсов?
35
ЛАБОРАТОРНАЯ РАБОТА № 5
ДЕФЕКТЫ ШЛИФОВАЯ РЕЛЬСА
Цель работы: ознакомление и изучение способов шлифования рельсов.
Задачи: выявление дефектов шлифования как новых рельсов, так и рельсов, шлифованных в процессе эксплуатации.
Краткие теоретические сведения
Шлифование не относится в операциям технологии их производства, а периодически выполняется в процессе эксплуатации. Однако в последние годы, особенно с развитием скоростного пассажирского движения, кроме профильного восстановительного шлифования все больше начинают применять профилактическое шлифование новых рельсов. При этом шлифование становится, в какой то степени, завершающей технологической операцией в процессе производства рельсов.
Целью профилактического профильного шлифования новых рельсов, уложенных при капитальном ремонте, является удаление обезуглероженного слоя и уменьшение заводских геометрических неровностей до уровня требований, соответствующих максимальной разрешенной скорости на данном участке пути.
Первоначальное шлифование новых рельсов выполняется сразу после укладки и выправки пути в плане и профиле. Шлифование производится рельсошлифовальными поездами, снабженными активными рабочими органами производства фирмы «СПЕНО» и ОАО «Калужский завод» «Ремпутьмаш». Рельсошлифовальные вагоны такого поезда имеют по две рельсошлифовальных тележки, каждая из которых содержит четыре рельсошлифовальные головки на каждую рельсовую нить. Рельсошлифовальные головки, являющиеся рабочими органами, могут быть наклонены к вертикальной оси под различными углами, что позволяет получить заданный профиль головки рельсов после шлифования.
Основными параметрами шлифования являются: число проходов рельсошлифовального поезда, рабочая скорость, усилия прижатия шлифовальных кругов, заданный профиль головки и периодичность шлифования.
Шлифование новых рельсов позволяет:
удалить обезуглероженный слой; при этом снимается 0,1-0,3 мм металла с поверхности рельсов, что заметно замедляет образование в процессе эксплуатации коротких неровностей (рифлей);
устранить неровности в зоне сварных стыков;
устранить дефекты, возникшие в процессе укладки пути, и в частности, обеспечить постоянство подуклонки рельсов, несмотря на несимметричные допуски на профиль рельсов и шпал.
36

Абразивный круг представляет собой режущий инструмент, состоящий из множества абразивных зерен, соединенных синтетическим связующим веществом. На определенном этапе эксплуатации зерна становятся слишком мелкими для того, чтобы могли образовываться режущие крошки. При этом, в процессе шлифования возрастает трение, приводящее к интенсивному выделению тепла на контактирующих поверхностях и их нагреву. Нагрев поверхности катания и выкружки рельса до температуры выше критической (723°С) и последующее охлаждение поверхностных слоев вследствие теплоотвода в головку рельса приводят к образованию белых слоев, т.е.к фактической закалке поверхностного слоя металла головки рельса в зонах контакта с шлифовальными кругами.
Описание лабораторной установки и измерительного оборудования
Для измерения твердости рельсов по методу Бринелля на железнодорожном полотне широко применяется переносной твердомер типа ТШП-4 Техническими характеристиками твердомера являются.
|
Таблица 10 |
|
Технические характеристики твердомера ТШП-4 |
||
|
|
|
Модель |
ТШП-4 |
|
|
|
|
Диапазон измерения твердости |
8~450 НВ |
|
|
|
|
Испытательные нагрузки |
2452; 7355; 9807; 29420 Н |
|
|
|
|
Пределы допускаемой погрешности твердомера от числа |
|
|
твердости образцовой меры твердости 2-разряда МТБ-1 |
|
|
НВ 100+25 при нагрузке 9807 Н |
4 % |
|
НВ 200+50 при нагрузке 29420 Н |
4 % |
|
НВ 400+50 при нагрузке 29420 Н |
5 % |
|
|
|
|
Предел допускаемой погрешности нагрузок, не более |
+1 % |
|
|
|
|
Продолжительность выдержки испытуемого образца под |
_ |
|
нагрузкой |
|
|
|
|
|
Диаметры твердосплавных шариков |
5; 10 мм |
|
|
|
|
Расстояние от индентора до опорного столика |
0~12 мм (свободный ход шпинделя с |
|
|
наконечником) |
|
|
до 140 мм (со струбциной) |
|
|
до 500 мм (с цепным захватом длиной 1,52 м) |
|
|
|
|
Расстояние от центра отпечатка до станины |
_ |
|
|
|
|
Габаритные размеры, мм. (ДхШхВ) |
155х300х345 (испытательной головки) |
|
|
|
|
Масса |
10 кг (испытательной головки) |
|
|
9,15 кг (струбцины) |
|
|
9,0 кг (цепного захвата) |
|
|
5,2 кг (рельсового захвата) |
|
|
4,4 кг (конуса Морзе) |
|
|
|
|
Электропитание |
_ |
|
|
|
|
Мощность |
_ |
|
|
|
|
37 |
|
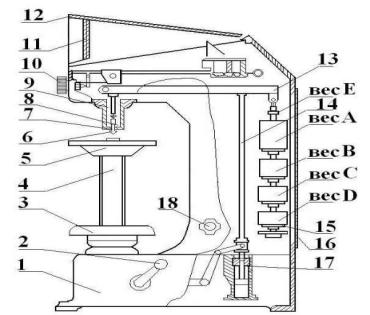
Рис. 29. Конструкция твердомера ТШП-4: 1 – рама; 2 – Ручка подачи и снятия нагрузки; 3 – Колесо подъѐмного винта; 4 – Винтовой стержень; 5 – Рабочий столик; 6 – Индентор; 7 – Зажимной винт; 8 – Основной шток; 9 – Пружина; 10 – Рукоятка микро-настройки; 11 – Проекционный экран;
12 – Верхняя крышка; 13 – Рычаг; 14 – Толкатель; 15 – Стойка для весов; 16 – Задняя панель; 17 – Поршень; 18 – Ручной маховик изменения
Порядок подготовки твердомера к работе
Твердомер транспортируется без весов и стойки, которые упакованы отдельно. Нагрузочный рычаг и нивелирная рейка находятся в неподвижном состоянии посредством фиксации их завязками, во избежание колебаний во время транспортировки. Для подготовки твердомера к работе, необходимо выполнить следующие операции:
1.Твердомер должен быть установлен в помещении, без вибраций и агрессивных газов, температура окружающего воздуха должна быть от +10 °С до +35 °C. Твердомер должен быть установлен на жестком столе, в котором вырезается отверстие диаметром около 80 мм для размещения винтового стержня 4, подымающий рабочий столик 5.
2.С помощью отвертки открутите верхнюю крышку 12 и заднюю панель 16 твердомера, затем развяжите завязки и удалить их. Ручку 2 толкните взад и вперед для удаления воздуха из буфера.
3.Повесьте стойку для грузов на место и веса А, В, C, D по порядку (сверху вниз). Небольшой вес E вешается непосредственно под крюк стойки весов.
4.Установите рабочий столик в отверстие винтового стержня и выставьте твердомер по уровню 0.2/1000, затем закрутите верхнюю крышку и заднюю панель.
5.Подключите питание и включите источник света, переключатель на правой стороне внизу корпуса. Если свет на экране не равномерен, отрегулируйте его гайкой на патроне (на верхней левой стороне корпуса) или вытащите или нажмите патрон вдоль оси. Патрон может быть снят для замены лампочки.
38
6. Корректировка буфера Скорость буфера хорошо отрегулирована до отправки. И корректировать ее нет необходимости. Если температура окружающего воздуха сильно колеблется, пользователь может подрегулировать ее. Метод проверки буфера перед испытанием представляет собой следующее: выберите нагрузку 980.7N (100 кг); положите стандартный блок твердости по HRB на рабочий столик; и поднимайте его пока основная линия не совпадает с горизонтальной линией на проекционном экране; потяните ручку 2 вперед, продолжительность движения картинки на экране должна быть 4–8 секунд, если нет, то настроить маховик демпфера («Load speed»), поворачивая его по часовой (уменьшаем время нагрузки) или против часовой (увеличиваем время нагрезки) стрелке, до тех пор пока вышеуказанные требования не будут удовлетворены. Масло в буфере может быть загрязнено после длительного периода эксплуатации, слейте отработанное масло и залейте новое примерно до 3/4 высоты буфера. Нажмите и потяните ручку 2 взад и вперед, чтобы избавится от воздуха в нем. Отрегулируйте скорость нагрузки в соответствии с процедурой, упомянутой выше.
Порядок выполнения работы
Преподаватель выдает каждому студенту задания на выполнение работы: режим определения дефектов и координаты точек измерения твердости на головке испытуемого образца рельсов.
Производится непосредственное измерение. Результаты отмечаются на эскизе образца, выраженного в определенном масштабе и приведенного в отчете о выполнении лабораторной работы.
Требования к отчету
Отчет по лабораторной работе состоит из следующих пунктов:
1.Цель работы.
2.Краткие сведения о шлифовании рельсов.
3.Краткое описание конструкции прибора.
4.Параметры прибора для определения твердости рельсов.
5.Эскиз образца с нанесенными точками твердости.
6.Выводы.
Контрольные вопросы
1.Для чего производится шлифование рельсов?
2.Какие дефекты шлифования рельсов?
3.Какой инструмент применяется для шлифования рельсов?
4.Опишите устройство твердомера.
5.Как работает твердомер?
6.Какова точность и достоверность измерения?
7.Как вычисляется и от чего зависит погрешность измерений?
39
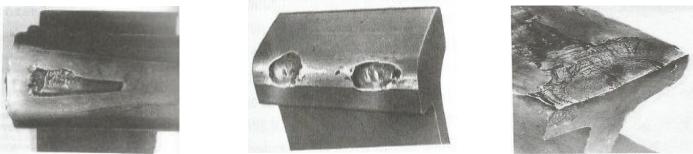
ЛАБОРАТОРНАЯ РАБОТА № 6
ПОВРЕЖДЕНИЕ ГОЛОВКИ РЕЛЬСА
Цель работы: определение причин повреждения головки рельсов по результатам анализа имеющейся информации и данных выкрашивания металла на поверхности катания, поперечных и продольных трещин.
Задача работы: выявление повреждения головки рельсов, а также классификация дефектов по группам и видам.
Краткие теоретические сведения
Повреждения головки рельсов происходят в виде выкрашивания металла на поверхности катания, поперечных и продольных трещин.
Выкрашивание металла на поверхности катания относятся к дефектам 10,11,12,13,14,16,17,18 и 19.
Дефект 10 – отслоение и выкрашивания металла на поверхности катания головки вследствие нарушения технологии изготовления рельсов. (рис. 30).
Дефект 11 – выкрашивания металла на рабочей выкружке головке, обусловленные недостаточным сопротивлением рельсов образованию внутренних трещин контактной усталости (рис. 31).
Дефекты 12 имеют ту же природу, что и дефекты 11, но возникают на ранней стадии эксплуатации до пропуска гарантийного тонножа. К дефектам 13.1 относятся выкрашивания металла на поверхности катания в стыках (рис. 32).
Рис. 30. Выкрашивание металла |
Рис. 31. Выкрашивание металла |
Рис. 32. Выкрашивание |
на поверхности катания |
из-за недостаточного сопротивления |
рельсового металла |
из-за наличия поверхностного |
рельсов образования внутренних |
в болтовом стыке |
дефекта металлургического |
трещин контактной усталости |
(дефект 13.1) |
происхождения вблизи стыка |
(дефект 11) |
|
(дефект 10,1) |
|
|
40