
методички / 4021 ЭИ
.pdf
Кдефекту 14 относятся выкрашивания металлы и местные выработки на поверхности катания головки, вызванные боксованием или юзом колеса при торможении.
Кдефекту 16.1-2 относятся выкрашивание в сварном стыке. Из дефекта 16.1-2 выделены дефекты 17.1-2, образовавшиеся в рельсах до пропуска гарантийного тонножа.
Дефект 18 является причиной некачественной приварки соединителей сбоку головки рельса.
Дефект 19.0-1-2 – поверхностный деформированный слой металла с трещинами, который создает акустические шумы и другие помехи, что снижает надежность дефектоскопного контроля.
Поперечные усталостные трещины (дефекты 20, 21, 22) являются наиболее опасным видом повреждений, поскольку они возникают и развиваются внутри головки рельсов без каких-либо внешних признаков и могут быть выявлены только с помощью специальных дефектоскопов. Выявление и оценка влияния концентратора напряжения в фокусе образования усталостной трещины являются наиболее ответственной частью анализа усталостного излома. Для того чтобы отличить дефект 20 от дефекта 21, необходимо по рубцам и усталостным линиям определить место образования усталостной трещины. Если фокус усталостного излома представляет собой зернистый надрыв, который обычно располагается на глубине более 10–20 мм от поверхности катания, то поврежденный рельс имеет дефект 20 (рис. 33).
Если же фокус усталостного поперечного излома представляет собой продольную трещину, которая на поперечном изломе выглядит как наклонный или горизонтальный рубец, то поврежденный рельс имеет дефект 21 (рис. 34).
Рис. 33. Дефекты 20 на начальной |
Рис. 34. Типичная усталостная трещина в головке рельса: |
стадии развития |
1 – фокус усталостного излома; 2 – зона постепенного |
|
развития усталостной трещины; 3 – зона долома; |
|
4 – ступеньки и рубцы на поверхности усталостной |
|
трещины; 5 – усталосные линии или кольца постепенного |
|
развития; 6 – участок хрупкого проскальзывания |
41
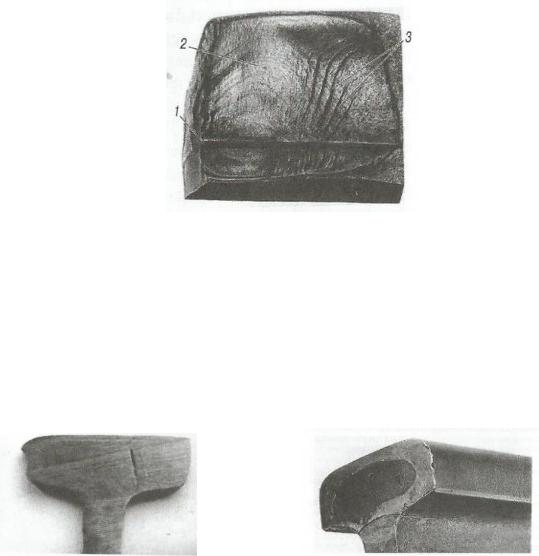
Дефекты 22 имеют ту же природу, что и дефекты 21, но возникают на ранней стадии эксплуатации до пропуска гарантийного тонножа.
В некоторых случаях усталостные трещины образуются и развиваются от хрупких надрывов. К повреждениям этого вида относятся дефекты 24 и 25, возникающие в головке рельсов в результате термомеханических (боксование колес локомотивов или юза при торможении) и механических повреждений при ударах.
Дефекты 26 и 27 – поперечные трещины в головке, возникающие вблизи сварного шва по обе стороны от него, учитывают как дефекты сварного стыка и относят к дефекту
26.3-4 или 27.3-4.
Продольные усталостные трещины в головке рельсов, приводящие к образованию так называемых вертикальных и горизонтальных расслоений, относятся к давно известным повреждениям рельсов, причины образований которых хорошо изучены.
Дефект 30 – продольные горизонтальные расслоения головки рельсов (дефекты 30.1-2) возникают вследствие грубых металлургических дефектов, расположенных в относительно малонапряженных центральных зонах головки рельсов (рис. 35).
Рис. 35. Раскрытая продольная трещина в головке вне стыка (дефект 30.2)
1 – фокус возникновения продольной усталостной трещины в виде волокнистой полоски; 2 – усталосные линии; 3 – рубцы на поверхности усталой трещины
Дефект 31 – вертикальные продольные расслоения, возникая внутри головки рельса (дефект 31.1-2), развиваются как продольные вертикальные усталостные трещины (рис. 36).
Дефект 33.1 – продольные трещины в месте перехода шейки в головку в стыках начинается с образования коррозионно-усталостной трещины (рис. 37).
Рис. 36. Продольная вертикальная |
Рис. 37. Трещина, развивающаяся |
трещина в головке рельса |
в торце под головкой рельса (дефект 33.1) |
|
42 |
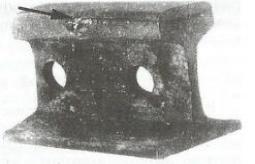
Вособую группу трещин в головке рельсов выделены повреждения, развивающиеся
врезультате приварки рельсовых соединителей в стыках. Они объединены в дефект 38.1 (рис. 38).
Рис. 38. Продольная усталосная трещина от места приварки соединителя в стыке (дефект 38.1)
В особую группу дефектов и повреждений объединены все виды износа и смятия рельсов.
Дефект 40 – динамическое воздействие подвижного состава на рельсы и образуется волнообразный износ.
Дефекты 41 и 43 – чрезмерное смятие концов рельсов в результате усиления динамического воздействия колес в болтовых стыках.
Дефект 44 – повышенный боковой износ головки рельса, возникающий у рельсов, лежащих на наружной (упорной) нити кривых радиусом менее 1000 м, под воздействием трения скольжения гребней набегающих колес.
К дефекту 46.3-4 относится характерное местное смятие, связанное с недостатками технологии сварки рельсов.
Описание измерительного инструмента и образцов
В качестве исходных образцов для проведения работы применяются разрушенные рельсы с характерными выкрашиваниями на их головке. Для измерения глубины и длины выщербин используется штангенциркуль типа ШЦ-1 (диапазон измерений 0–150 мм) и металлическая линейка.
Правила безопасности выполнения работы
Для безопасного выполнения работы запрещается перемещать образцы рельсов. В ходе работы следует соблюдать общие правила безопасности при работе с металлоконструкциями.
43
Порядок выполнения работы
В процессе выполнения работы группа студентов, состоящая не более чем из трёх человек, изучает разрушенный образец, определяет дефект и даёт обоснованное заключение о характере и причинах разрушения рельса. После чего на основании установленных причин делается вывод о характере появления и развития дефекта, определяется стадия возможного зарождения дефекта, время его развития вплоть до момента наступления повреждения. Параллельно генерируется решение по оптимизации исходных поперечных профилей головок рельсов. В заключение приводится вывод по изменению условий работы рельсов и повышению качества их изготовления.
Требования к отчёту
Отчёт должен содержать эскиз дефекта головки рельсов, описание данного дефекта, причины его появления и методы технического контроля.
Контрольные вопросы
1.Назовите повреждения головки рельсов?
2.Какие дефекты относятся к выкрашиванию металла на поверхности катания рельсов?
3.Перечислите причины появления поперечных трещин в головке рельсов.
4.Какой механизм образования продольных усталостных трещин в головке рельсов?
5.Расскажите о совершенствовании контакта колеса и рельса, улучшающий условия их взаимодействия.
ЛАБОРАТОРНАЯ РАБОТА № 7
ПОВРЕЖДЕНИЕ ШЕЙКИ РЕЛЬСОВ
Цель работы: определение причин повреждения шейки рельсов.
Задача работы: выявление трещин в шейки, вызванных заводскими дефектами, от болтовых отверстий и эксплуатационных повреждений.
Краткие теоретические сведения
Изменение условий эксплуатации и введение новых конструкций верхнего строения пути иногда приводят к видоизменению повреждений и появлению дефектов в шейке рельсов.
44
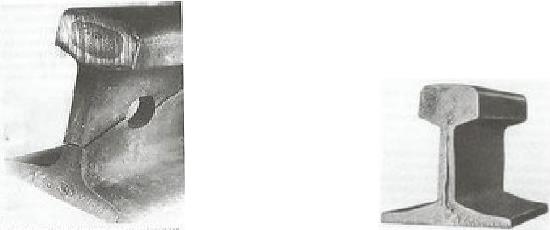
Дефект 50, вызванный заводскими дефектами, относится к самым старым (рис. 39). Его возникновение ранее было связано с остатками усадочной раковины в шейках, после перехода на непрерывную разливку стали – с резко выраженной осевой ликвидации. Обнаружить некоторое выпучивание шейки, которое иногда сопровождает образование вертикального расслоения шейки, достаточно трудно. поэтому основным средством
выявления дефекта является дефектоскопирование.
Все трещины, возникающие в шейке рельсов в стыках от болтовых отверстийнеизбежных концентраторов напряжений при болтовом соединении рельсов накладками, представляют собой дефекты 53.1 (рис. 40).
К дефекту 55 относятся разнообразные трещины, возникающие в шейке и не связанные с болтовыми отверстиями. Они могут образовываться в местах сопряжений шейки с головкой, возникать от ударов и других воздействий на шейку, от маркировочных знаков, отверстий вне зоны болтовых стыков или иных концентратов напряжений.
Рис. 39. Вертикальное продольное |
Рис. 40. Усталостная трещина, развивающаяся |
расслоение шейки рельса (дефект 50.2) |
от первого болтового отверстия под углом 45 градусов |
|
к оси рельса (дефект 53.1) |
Описание измерительного инструмента и образцов
В качестве исходных образцов для проведения работы применяются различные рельсы с дефектами 50, 53 и 55. Для измерения длины трещин используется штангенциркуль типа ШЦ-1 (диапазон измерений 0–155 мм) и металлическая линейка.
Правила безопасного выполнения работы
Для безопасного выполнения работы запрещается перемещать образцы рельсов. В ходе работы следует соблюдать общие правила безопасности при работе с металлоконструкциями.
45
Порядок выполнения работы
В процессе выполнения работы группа студентов, состоящая не более чем из трёх человек, изучает разрушенный образец, определяет дефект и даёт обоснованное заключение о характере и причинах разрушения рельса. После чего на основании установленных причин делается вывод о характере появления и развития дефекта, определяется стадия возможного зарождения дефекта, время его развития вплоть до момента наступления повреждения. Одновременно формируются решения по упрочнению болтовых отверстий и уменьшению механических повреждений шеек рельсов.
Требования к отчёту
Отчёт должен содержать эскиз дефекта шейки рельсов, описание данного дефекта, причины его появления и методы технического контроля.
Контрольные вопросы
1.Назовите повреждения шейки рельсов.
2.Перечислите причины появления трещин в шейке рельсов, вызванных заводскими дефектами?
3.Назовите характер возникновения трещин от болтовых отверстий в шейке рельсов?
4.Какие бывают трещины в шейке рельсов от эксплуатационных повреждений?
5.Как влияет маркировка рельсов на образование усталостных трещин?
ЛАБОРАТОРНАЯ РАБОТА № 8
ДЕФЕКТЫ И ПОВРЕЖДЕНИЯ ПОДОШВЫ РЕЛЬСА
Цель работы: является определение дефектов и повреждений подошвы рельсов. Задача работы: выявление трещин в подошве, вызванные заводскими дефектами,
от эксплуатационных повреждений и в процессе коррозионной усталости.
Краткие теоретические сведения
Подошва рельсов по сравнению с остальными его частями при работе в пути подвергается наибольшим растягивающим напряжениям. В связи с этим большую опасность представляют различные металлургические дефекты в ней.
46
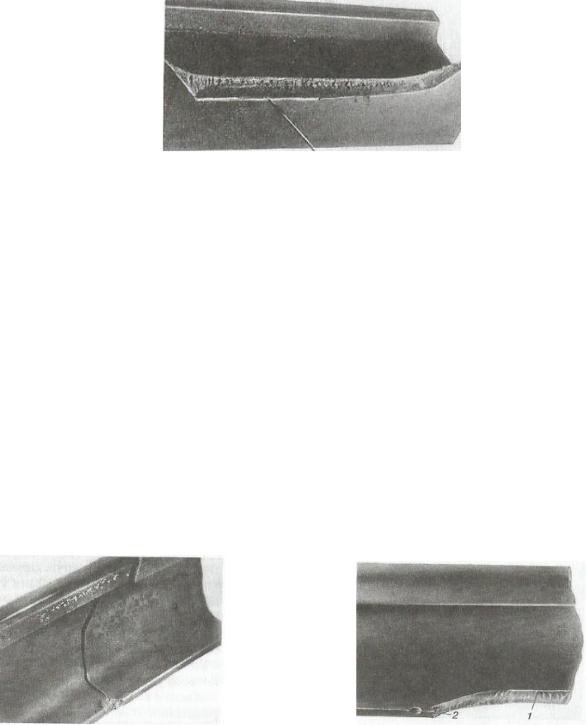
Дефект 60 возникает от волосовин или закатов различной глубины, расположенных в средней трети подошвы рельсов. От этих пороков образуются продольные хрупкие трещины с кристаллической поверхностью в изломе, которые могут привести к выколу куска подошвы (рис. 41).
К дефекту 64 относятся две группы повреждений рельсов: местные выработки и местная коррозия в местах контакта с элементами скреплений – клеммами. ребордами подкладок, упорными скобами.
Рис. 41. Выкол куска подошвы вследствие наличия волосовин на нижней поверхности подошвы в её средней трети
Рельсы, поврежденные общей коррозией, отнесены к дефекту 98. Трещины и выколы подошвы могут быть вызваны механическими повреждениями или ожогами (дефект 65). Иногда выколы происходят в результате сочетаний удара по перу подошвы и наличия металлургического порока типа заката на верхней поверхности подошвы. Пример такого разрушения рельса показан на рис. 42 и 43.
Наибольшую опасность представляют коррозионно-усталостные повреждения, развивающиеся на подошве рельсов при совместном воздействии коррозии и циклических напряжений (дефект 69). Имеются два вида коррозионно-усталостных повреждений подошвы рельсов. Первый вид – поперечные трещины, развивающиеся от коррозионных каверн на нижней поверхности подошвы рельсов. Ко второму виду коррозионноусталостных повреждений подошвы относятся трещины, начинающиеся на внешне гладкой, неповрежденной кавернами поверхности.
Рис. 42. Поперечный излом рельса |
Рис. 43. Выкол куска подошвы, вызванный закатом |
от механического повреждения подошвы |
на верхней поверхности подошвы в зоне перехода |
|
в шейку: 1 – закат в виде гладкой волокнистой |
|
полоски; 2 – след от удара по перу подошвы |
|
47 |
Описание измерительного инструмента и образцов
В качестве исходных образцов для проведения работы применяются разрушенные рельсы с дефектами 60, 64, 65, 69 и 98. Для измерения длины трещин используется штангенциркуль типа ШЦ-1 (диапазон измерений 0–155 мм) и металлическая линейка.
Правила безопасного выполнения работы
Для безопасного выполнения работы запрещается перемещать образцы рельсов. В ходе работы следует соблюдать общие правила безопасности при работе с металлоконструкциями.
Порядок выполнения работы
В процессе выполнения работы группа студентов, состоящая не более чем из трёх человек, изучает разрушенный образец, определяет дефект и даёт обоснованное заключение о характере и причинах разрушения рельса. После чего на основании установленных причин делается вывод о характере появления и развития дефекта, определяется стадия возможного зарождения дефекта, время его развития вплоть до момента наступления повреждения.
Кроме того, формируются решения, направленные на предотвращение образования дефектов и повреждений подошвы рельсов.
Требования к отчету
Отчёт должен содержать эскиз дефекта или повреждения подошвы рельса, их описание, причины появления и методы технического контроля.
Контрольные вопросы
1.Назовите дефекты и повреждения подошвы рельсов.
2.Какие повреждения в подошве рельсов вызваны заводскими дефектами?
3.Какое влияние оказывает контакт подошвы с элементами скреплений?
4.Отчего происходят коррозионно-усталостные трещины в подошве рельсов?
5.Какие действия могут быть направлены на предотвращение образования дефектов подошвы рельсов?
48
ЛАБОРАТОРНАЯ РАБОТА № 9
ИЗЛОМЫ РЕЛЬСОВ
Цель работы: является изучение изломов рельсов изъятых с пути. Задача работы: определение причин внезапных изломов рельсов.
Краткие теоретические сведения
Случаи выхода из строя рельсов по излому немногочисленны – менее 0,1 % всех изъятых с пути рельсов. Однако опасность внезапных изломов рельсов заставляет очень внимательно относится даже к единичным случаям разрушений. Особенно опасны разрушения рельсов на большое число фрагментов.
Взависимости от того, какая из трещин оказала решающее влияние на разрушение рельса, поперечные изломы относят к дефектам 70, 71, 72, 73, 74, 75, 76, 77 или 79.
Если решающее влияние на хрупкий поперечный излом рельса оказали внутренний опасный концентратор напряжения в виде крупного шлакового включения, другие явные дефекты металла или волосовина в подошве, то такая поломка должна быть классифицирована как дефект 70.1-2 / 20.1-2 или дефект 70.1-2 / 60.1-2. Код дефекта дополняет (через косую линию) номером дефекта, от которого он возник.
Втом случае, когда поперечная усталостная трещина, растущая в головке рельса, вовремя не была обнаружена при дефектоскопировании и привела к излому рельса, его классифицируют как дефект 71.1-2 / 21.1-2 или 72.1-2 / 22.1-2. Если излом произошёл вследствие пропущенной при дефектоскопировании вертикальной продольной трещины в головке, то причиной излома стал дефект 71.1-2 / 31.1-2.
Разрушение рельса в болтовых стыках, вызванное вовремя не выявленными дефектами 33.1 и 53.1, классифицируются как дефект 73.1 / 33.1 или 73.1 / 53.1.
Своевременно не обнаруженные дефекты 24.1-2 и 64.1-2 могут приводить к изломам рельсов (дефекты 74.1-2 / 24.1-2 и 74.1-2 / 64.1-2). Механическими повреждениями головки, шейки и подошвы (дефекты 25,55,65) могу быть обусловлены изломы по дефектам 75/25, 75/65. Изломы сварных швов относятся к дефектам 76.3-4 и 77.3-4.
Поперечные изломы вызваны коррозионно-усталостными трещинами в подошве (дефект 69), обозначают как дефект 79.1-2/69.1-2. К особой группе дефектов относятся изгибы рельсов, которые в свою очередь разделены на изгибы несварных рельсов (дефект 85) и нарушения прямолинейности , допущенные при сварке (дефект 86). Новые виды повреждений, ещё не нашедших отражения в классификации, относят к дефектам 98 и 99. Дефекты оставленных в пути рельсов, опасность эксплуатации которых может быть оценена по ближайшему типу размера дефекта, в том числе и общая коррозия, относятся
кдефекту 98. К дефекту 99 относя дефекты, которые не укладываются в классификацию,
49
но при наличии их рельсы не могут быть оставлены в пути; в их числе, в частности, поперечные износы без видимых дефектов и без усталостных трещин в изломах.
Описание измерительного инструмента и образцов
В качестве исходных образцов для проведения работы применяются разрушенные рельсы с дефектами 70, 71, 72, 73, 74, 75, 76, 77, 79, 85, 86, 98 и 99. Для измерения длины дефектов и повреждений используется металлическая линейка и рулетка.
Правила безопасного выполнения работы
Для безопасного выполнения работы запрещается перемещать образцы рельсов. В ходе работы следует соблюдать общие правила безопасности при работе с металлоконструкциями.
Порядок выполнения работы
В процессе выполнения работы группа студентов, состоящая не более чем из трёх человек, изучает излом рельса, определяет дефект и причину, от которого он возник. Параллельно сравниваются изломы рельсов в прямых и кривых участках, а также в звеньевом и бесстыковом пути.
Требования к отчёту
Отчёт должен содержать эскиз излома рельса, его описание причины появления и методы технического контроля.
Контрольные вопросы
1.Назовите причины изломов рельсов.
2.Какие последствия изломов рельсов в пути?
3.Как влияет пропущенный тоннаж (наработка) на изломы рельсов?
4.Какие особенности строения различных изломов рельсов?
5.Какие изломы рельсов могут возникать в результате воздействий подвижного состава с неисправными колёсами?
50