
методички / 4027 ЭИ
.pdf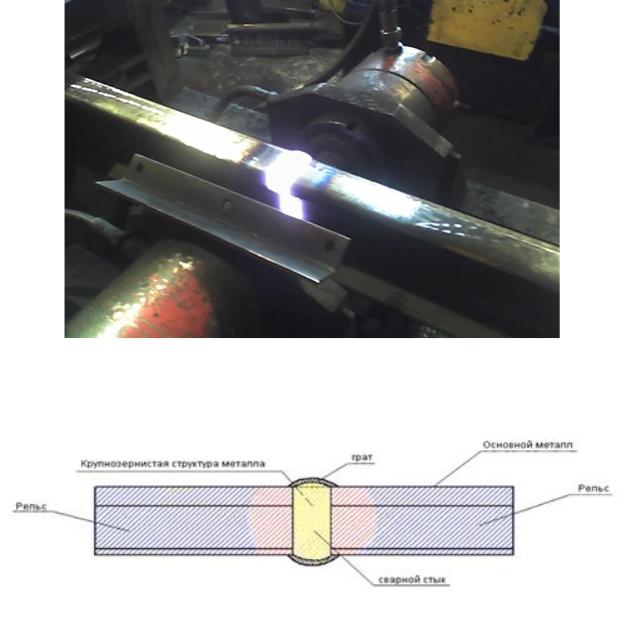
Рис. 2. Сварной шов при электроконтактной сварке
Рис. 3. Зона термического влияния при электроконтактной сварке
Для предотвращения образования крупнозернистой структуры разработан способ сварки давлением с индукционным нагревом.
Для повышения механических свойств на сварных стыках выполненных сваркой давлением рекомендуется применять термообработку (в том числе дифференцированную с закалкой головки рельса в зоне термического влияния).
Алюминотермитный способ основан на получении металлов и сплавов восстановлением их окислов в экзотермической реакции с алюминием. Реакция проходит с выделением большого количества тепла. Расплавленный металл заливается в зазор между соединяемыми рельсами.
Наиболее высокой прочностью и надежностью обладают рельсы, сваренные электроконтактным и индукционным способами, на которые приходится более 85 % всех сварных стыков.
Способы применяются как в РСП, так и в пути с помощью ПРСМ.
21
Сварка рельсов ПРСМ – затратна, потому что для доставки на место работ крупногабаритного оборудования и сварки требуется окно продолжительностью более 3,5 часов.
Для уменьшения количества сварных швов металлургические комбинаты России освоили выпуск рельсов длиной 100 м.
Технология сварки рельсов в пути должна удовлетворять требованиям: а) оборудование-компактное и минимальной массы; б) окно-минимальной продолжительности;
в) соответствие структуры сварного шва требованиям по прочности и надежности.
Контрольные вопросы
1.Назовите основные виды сварки рельсовых плетей.
2.Назовите преимущества и недостатки электроконтактной сварки.
3.Какую термообработку рекомендуется применять после сварки?
4.Можно ли применять алюминотермитную сварку на путях 4–5 классов?
5.Можно ли применять алюминотермитную сварку на путях 1–2 классов?
ЛАБОРАТОРНЫЕ РАБОТЫ № 8–9
ТЕРМОМЕХАНИЧЕСКАЯ ОБРАБОТКА ЭЛЕМЕНТОВ ВСП
Цель и задачи работы
Цель работы: повышение надежности, работоспособности и морозостойкости элементов ВСП железнодорожного пути.
Изучить:
а) современные способы термической обработки сварных швов; б) термомеханической обработки; в) методику расчета параметров термомеханической обработки;
г) влияние параметров ТМО на эксплуатационные свойства элементов ВСП.
Краткие теоретические сведения
Для изделий, работающих в условиях Сибири и Крайнего Севера, особую актуальность приобретает обеспечение высокой прочности и надежности рельсовых плетей, эксплуатируемых в условиях крайне низких температур (ниже –40 °С) /11/.
В таких условиях наиболее вероятны возникновения в отдельных случаях изломов рельсовых плетей (в т.ч. в местах сварных швов), а также срезка стыковых болтов.
Основными факторами, влияющими на излом рельсовых плетей, трещинообразование являются:
-крайне низкая температура в зоне обслуживания;
-воздействие циклических нагрузок на рельсовые плети;
-образование крупнозернистой структуры в сварном шве изделия;
22
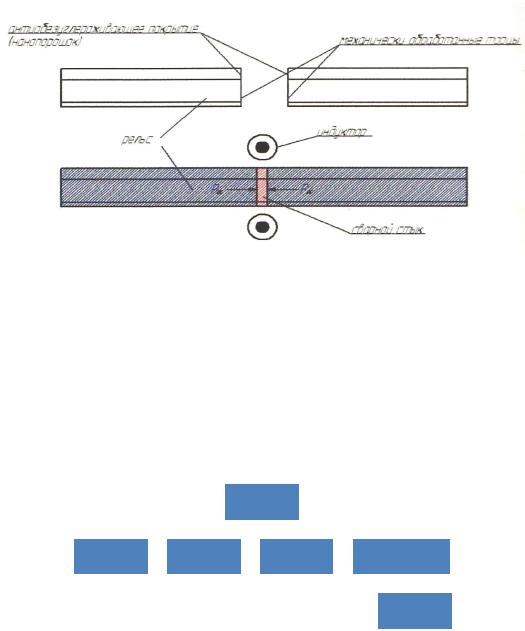
-возникновение микротрещин усталостно-контактного происхождения;
-образование дефектов поверхностного происхождения (вмятин, рисок, волосовин
ит.д.).
Для предотвращения образования грубой крупнозернистой структуры и ряда других негативных факторов в сварном шве рельсовых плетей на кафедре «ПСЖД» СамГУПС разработан и запатентован способ сварки давлением с подогревом (рис. 4).
Рис. 4. Способ сварки давлением с подогревом
Для осуществления более значительного эффекта сварки давлением с подогревом все более широкое применение находят макро- и нанопорошки.
Схема производства порошков по азидной технологии представлена на рис. 5.
|
|
|
|
Горение |
|
||||||
|
|
|
|
|
|
|
|||||
|
|
|
|
|
|
|
|
||||
|
|
|
|
|
Спеки |
||||||
|
|
|
|
|
|
|
|
|
|
||
|
|
|
|
|
|
|
|
|
|
||
|
|
|
|
|
|
|
|
|
|
||
Si3N4 |
BN |
|
|
|
TiC0,5N0,5 Дробление |
||||||
|
|
|
|
|
|
|
|
|
|
|
Размол |
|
|
|
|
|
|
|
|
|
|
|
|
|
|
|
|
|
|
|
|
|
|
Рис. 5. Схема производства порошковых материалов
Примеры реакций происходящих при азидной технологии представлены ниже:
8В + 3NaN3 + KBF4 = 9BN + 3NaF + KF,
16Si + 6 NaN3 + (NH4)2SiF6 = 5Si3N4 + 6NaF + 4H2,
8Al + 3NaN3 + AlF3 = 9AlN + 3NaF,
12Ti + 2NaN3 + 6C + 2NH4Cl = 12TiC0,5N0,5 + 2NaCl + N2 + 4H2.
23

В результате, применение указанного способа сварки давлением с подогревом способствует повышению надежности и прочности бесстыкового пути, а также позволяет увеличить межремонтный ресурс сварных стыков до 1000 млн.т.пропущенного груза /10/.
Модифицированные скрепления
Для решения поставленных задач генеральным направлением разработки оптимизированной конструкцией скреплений выбрано – снижение динамической нагрузки.
Для предотвращения излома упругих клемм при эксплуатации пути, в том числе в климатических температурах в условиях Сибири и Крайнего Севера особо важное значение имеет снижение динамических нагрузок. Одним из путей снижения таких нагрузок является разработка и внедрение промежуточных бесподкладочных скреплений с повышенными демпфирующими свойствами.
Поэтому на кафедре «ПСЖД» СамГУПС разработаны и запатентованы промежуточные скрепления с демпфирующими прокладками (рис. 6), обеспечивающие снижение воздействия циклических динамических нагрузок на рельсы на 30–40 %, снижение шума до 30 %, уменьшение объемов работ по подтягиванию гаек и болтов до 50 %. Принципиальным отличием скрепления типа АБ1 от существующих отечественных и зарубежных конструкций является обеспечение эффекта самозаклинивания, т.е. максимальная степень прижата подошва рельса к подкладке в момент нажатия колеса на рельс.
Скрепление АБ1 |
Скрепление АБ2 |
Рис. 6. Промежуточное скрепление с демпфирующими свойствами:
а– вид узла скрепления типа АБ1 в свободном состоянии; б – вид узла скрепления типа АБ2
вмомент прохождения состава
Использование таких скреплений увеличивает работоспособность бесстыкового пути, а также повышает его межремонтный ресурс до 900–1000 млн т пропущенного груза, т.е. он становится соизмеримым с межремонтным ресурсом рельс /10/.
Современные методы упрочнения элементов верхнего строения пути
Отличительной особенностью строительства и эксплуатации бесстыкового пути в современных условиях (при более высоких осевых нагрузках, скоростях перевозки гру-
24
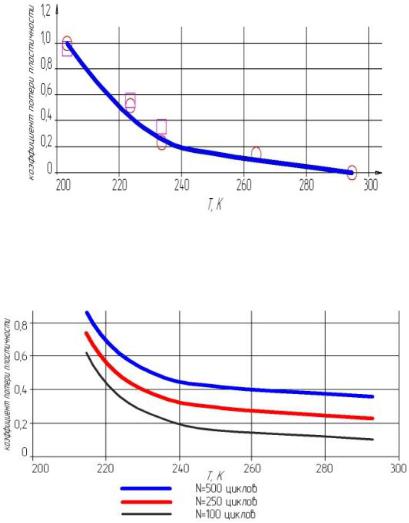
зов, грузонапряженностях) является необходимость применения рельсовых плетей, обладающих более высокой твердостью, износостойкостью, хладостойкостью.
В настоящее время при строительстве новых железнодорожных путей, как правило, применяются только термоупрочненные рельсы, удовлетворяющие вышеуказанным требованиям.
Однако, все еще остаются актуальными проблемы предотвращения хрупких разрушений рельсов, упругих клемм промежуточных скреплений, элементов стрелочных переводов и т.д. при низких климатических температурах (хладостойкость) и, особенно в условиях Сибири и Крайнего Севера. Расчеты рельсовых плетей в основном базируются на неизменности свойств и сопротивляемости зарождению, развитию и распространению трещин и в полной мере не учитывают влияния структуры рельсовой стали, циклических нагрузок и неоднородности напряженно-деформированного состояния на предельные характеристики рельсовых сталей при низких температурах /9/.
Экспериментально установлено, что на хладостойкость существенное влияние оказывает не только температура, но и воздействие как циклической, так и динамической нагрузок, структура стали, а также наличие и величина повреждений в элементах верхнего строения (рис. 7, 8).
Рис. 7. Зависимость коэффициента потери пластичности от температуры, с трещиной, материал-16Г2САФ
Рис. 8. Зависимость коэффициента потери пластичности температуры, материал – 09Г2С
25
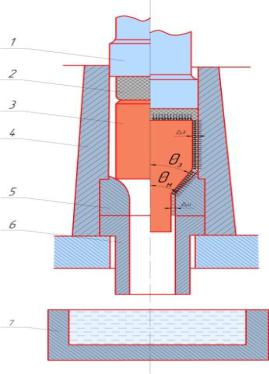
Хладостойкость мелкозернистой стали существенно выше по сравнению с крупнозернистой. Эксплуатационные свойства рельсовых сталей (твердость, прочность, износостойкость) определяются такими параметрами ТМО как температура нагрева, скоростью нагрева при аустенизации, скоростью и температурой охлаждения /10/.
Схема термомеханического упрочнения элементов верхнего строения пути представлена на рис. 9.
Рис. 9. Схема термомеханического упрочнения высокоуглеродистых сталей: 1 – пуансон; 2 – графитовая шайба; 3 – заготовка; 4 – контейнер; 5 – матрица; 6 – калибрующая втулка; 7 – устройство для охлаждения
При обработке элементов по такой схеме формируется мелкозернистая структура, которая обеспечивает повышение ударной вязкости в 1,5–1,8 раза, прочности на 20–40 %.
На рисунках 10 и 11, показано влияние степени деформации рельсов на ударную вязкость и предел прочности на изгиб.
Особо эффективно применение высокоэнергетических методов упрочнения элементов верхнего строения пути прямыми и косыми ударными волнами. Для этой цели разработано соответствующее устройство, а методы и технические устройства для их осуществления защищены тремя патентами.
Для повышения твердости, износостойкости, хладостойкости рекомендуется применение метода динамического микролегирования износостойкими карбидами и нитридами. Для легирования применяюся износостойкие микро- и нанопорошки.
Схема проникания частицы в упрочняемые изделия представлена на рис.12.
26
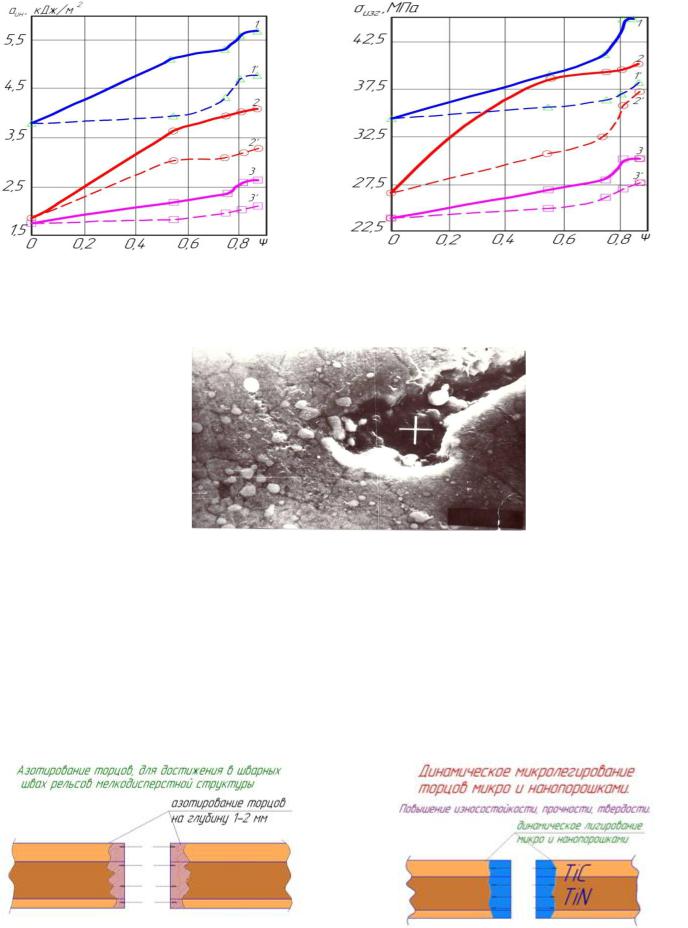
Ударная вязкость |
Предел прочности на изгиб |
Рис. 10. Влияние степени деформации ψ |
Рис. 11. Влияние степени деформации ψ |
на ударную вязкость сталей Р6М5(1) |
на изгиб сталей сталей Р6М5(1) |
Рис. 12. След микрочастицы при динамическом микролегировании
Азотирование (рис. 13), динамическое микролегирование износостойкими микро- и нанопорошками торцов под сварку (рис. 14) повышает хладостойкость сварных соединений.
Азотирование торцов перед сваркой также повышает ударную вязкость высокоуглеродистых рельсовых сталей (рис. 15).
Рис. 13. Азотирование торцов перед сваркой |
Рис. 14. Динамическое микролегирование торцов |
давлением с подогревом |
перед сваркой давлением с подогревом |
27
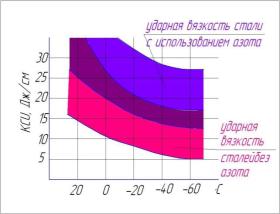
Рис. 15. Влияние азотирования на ударную вязкость высокоуглеродистых сталей
Упрочнение сварных швов ударными волнами, динамического микролегирования износостойкими. На кафедре «ПСЖД» СамГУПС разработаны и запатентованы способы упрочнения микропорошками, которые существенно повышают физико-механические свойства рельсовых сталей: твердость, прочность, износостойкость, хладостойкость /12/.
Применение современных методов упрочнения, повышения хладостойкости элементов верхнего строения пути позволяет существенно (в 1,8–2 раза) повысить эксплуатационную стойкость рельсовых плетей.
Контрольные вопросы
1.Назовите основные виды термомеханического упрочнения сварных швов рельсовых плетей.
2.Назовите основные способы упрочнения упругих клемм скреплений.
3.Влияет ли величина зерна на прочность, морозостойкость рельсовых сталей?
4.Назовите оборудование, применяемое для ТМО.
ПРАКТИЧЕСКАЯ РАБОТА
ОБОСНОВАНИЕ ОБЪЕМОВ И ФОРМИРОВАНИЕ ОРГСТРУКТУРЫ ДИСТАНЦИИ ПУТИ
Цель работы: изучить основы и освоить навыки формирования оргструктуры дистанции пути.
Задачи:
1)в соответствии с исходными данными рассчитать приведенную длину пути;
2)обосновать участковую оргструктуру и определить необходимое количество участков.
3)произвести расчет затрат на текущее содержание пути.
28
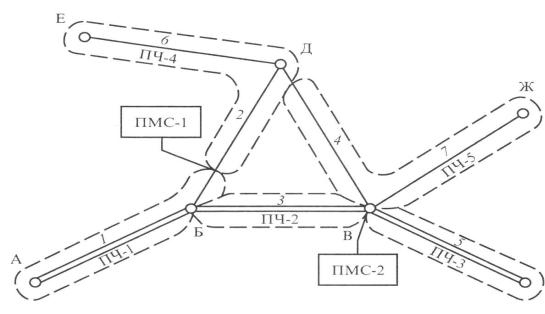
Краткие теоретические сведения
Обоснование объемов путевых работ и их распределение по участкам дистанции пути, отделения или дороги – исходный этап проектирования производства работ. Объемы, а также периодичность различных видов путевых работ в пределах любого железнодорожного участка зависят от его протяженности, числа путей, грузонапряженности, скоростей движения поездов, конструкции и состояния пути.
Возможны два метода определения объемов путевых работ и сроков их выполнения: по наработке, измеряемой прошедшим по пути тоннажом, и по фактическому состоянию пути, оцениваемому величиной накопленных отступлений от нормы. Первый метод предпочтителен при перспективном, а второй – при текущем планировании путевых работ.
Нормативную основу для планирования путевых работ составляют Технические условия на работы по ремонту и планово-предупредительной выправке пути (ТУ). Состав, объемы и сроки выполнения путевых работ предопределяют потребность в трудовых, технических и других ресурсах, а также комплекс мер по эффективному их использованию. Порядок определения объемов путевых работ в пределах участков и дороги в целом по прошедшему тоннажу иллюстрируется на примере условной дороги, схема которой представлена на рис. 16, а характеристика участков дана в табл. 10.
Рис. 16. Схема условной железной дороги
В рассматриваемом примере приняты допущения: двухпутные участки одинаковые, однопутные также; протяженность станционных путей и количество стрелочных переводов приняты равными соответственно 0,5 км и 1,5 шт. на 1 км главного пути (что близко к среднесетевым соотношениям); доля стрелочных переводов на главных путях 40 % и на станционных 60 %.
29
|
|
|
|
|
Таблица 10 |
|
Характеристика участка дороги |
|
|||
|
|
|
|
|
|
Участки |
Протяженность |
Грузонапряженность |
|
Скорость поездов |
Класс, группа |
|
L, км |
Г, млн т·км бр./км |
|
v, км/ч |
и категория пути |
|
|
в год |
|
|
(согласно ТУ) |
|
|
|
|
|
|
А–Б |
200 |
70 |
|
130/85 |
1Б1 (бесстыковой) |
|
|
|
|
|
|
Б–А |
200 |
70 |
|
130/85 |
1Б1 (бесстыковой) |
|
|
|
|
|
|
Б – Д |
180 |
20 |
|
70/55 |
ЗГ4 (звеньевой) |
|
|
|
|
|
|
В–Ж |
180 |
20 |
|
70/55 |
ЗГ4 (звеньевой) |
|
|
|
|
|
|
Протяженность станционных путей: 0,5·1920 = 960 км (1920 км – протяженность |
5Б7 – 5Е7 |
||||
главных путей, в т.ч. 1200 км двухпутных и 720 км однопутных) |
|
|
|||
|
|
|
|
|
|
Стрелочные переводы на путях |
|
|
|
720 шт., 1Б1, ж.-б.; |
|
главных: А–Б–В–Г – 1200–1,5–0,4 и |
|
|
|
||
|
|
|
432 шт., ЗГ4, дер.; |
||
Е–Д–Б, Д–В–Ж – 720–1,5–0,4 |
|
|
|
||
|
|
|
1728 шт., Б7 – Е7 |
||
станционных: 1920–1,5–0,6 |
|
|
|
||
|
|
|
|
||
|
|
|
|
|
|
Виды путевых работ, их периодичность и объемы для отдельных участков и всей дороги согласно среднесетевым нормам представлены в табл. 10. Здесь класс, группа и категория путей приняты на основе действующей классификации (табл. 2) в зависимости от грузонапряженности и скорости движения поездов. При этом для путей 1 и 2-го классов предпочтение отдано бесстыковой конструкции. Период в годах между капитальными ремонтами определится отношением:
tki = Tkj / Гi,
где Tkj – периодичность капитального ремонта пути на i-м участке, млн т брутто прошедшего груза (табл. 11);
Гj – средняя за межремонтный период грузонапряженность того же участка, млн т·км брутто/км в год.
Годовой объем капитального ремонта при этом обусловлен отношением:
Lki = Li /T ki .
Удельные объемы среднего и подъемочного ремонтов пути, сплошной замены рельсов и металлических частей стрелочных переводов, а также плановопредупредительной выправки пути обусловлены зависимостями:
Lс I = nci Lki ; Lni= nniLki ; Lрс= nрсК ni ; Lbi= nbiLki ,
где nci , nni , nрс, nbi – число повторений каждого из перечисленных видов работ в одном межремонтном цикле.
Итоговые значения (табл. 10) отражают среднегодовые объемы путевых работ в пределах дороги при неизменной грузонапряженности. Уточнение их по годам, участкам и отдельным километрам с учетом динамики грузонапряженности достигается сопоставлением прошедшего тоннажа и фактического состояния пути. При этом допускается, опираясь на критерии в ТУ, замена одного вида ремонта другим, менее трудоемким, или смещение ремонтов по времени в пределах межремонтного цикла.
30