
Производство заготовок. Литье. Серия учебных пособий. Книга 3. Проектирование и производство отливок (литых заготовок)
.pdf
4.2.1.3.1 Индукционные печи
Преимуществом индукционных печей является то, что в процессе плавки происходит интенсивное перемешивание расплава, что делает его однородным и повышает качество отливок.
3
а) |
б) |
а) – стационарная; б) – поворотная
1 – корпус; 2 – тигель; 3 –индуктор; 4 – поворотный механизм
Рисунок 54 – Вид индукционных печей
Другим преимуществом индукционных печей является легкий перевод печи с плавки одного сплава на плавку другого, но из-за быстрой изнашиваемости и высокой стоимости тиглей эти печи широко не применяют.

Более стойкие чугунные тигли, но и они имеют существенный недостаток
— способствуют обогащению алюминиевых сплавов железом. Перед плавкой алюминия на чугунные тигли наносят жаростойкое покрытие, которое предотвращает насыщение расплава железом. В состав покрытий входят каолин, жидкое стекло и вода или графит, каолин и вода.
4.2.1.3.2 Дуговые печи
Малые дуговые печи предназначены для литья и часто работают одну или две смены, поэтому они выполняются не только с механизированной загрузкой, но и с ручной.
1 – корпус; 2 – футеровка; 3 – электроды; 4 – механизм поворота
Рисунок 55 – Дуговая печь косвенного нагрева
Корпус печи прямого действия цилиндрический цельный со сферическим днищем. Механизм наклона печи боковой. Двигатель наклона печи через редуктор приводит во вращение барабан, наматывающий трос.
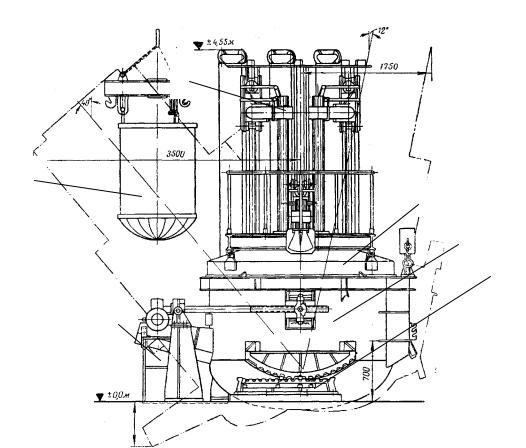
2
3
6
4
5
1
1 – каркас; 2 – электрододержатели с электродами; 3 – загрузочная корзина; 4 – корпус печи; 5 – механизм подъема и поворота печи; 6 – свод печи
Рисунок 56 – Дуговая сталеплавильная печь типа ДСП вместимостью 1,5 т
Кольцо обода со сводом подвешено к поворотной площадке, на которой закреплены также три неподвижные коробчатые стойки. По стойкам перемещаются каретки с трубчатыми рукавами, несущие электрододержатели с зажатыми в них электродами. Механизм перемещения электродов тросовый с электромеханическим приводом. Механизм зажима электрода пружиннопневматический. Загрузка печи верхняя с помощью бадьи с секторным дном. При загрузке несущий свод и стойки поворотной площадки приподнимают и поворачивают на угол 85° с помощью механизма подъема и поворота свода с двумя двигателями переменного тока. Дверца рабочего отверстия имеет ручной механизм подъема с противовесом. Металл разливают через сливное отверстие и желоб. Ток подводится к электрододержателю двумя медными водоохлаждаемыми трубами, закрепленными на рукаве и каретке; гибкий токоподвод состоит из четырех кабелей МГЭ сечением 500 мм2 каждый.
Влитейном производстве используют дуговые печи косвенного действия,
вкоторых дуга горит между электродами (рисунок 55), что позволяет выплавлять более чистые сплавы.

4.2.1.3.3 Печи сопротивления
Печи сопротивления позволяют плавить качественные сплавы цветных металлов с температурой плавления ниже 1000 0С. Они бывают камерные и тигельные.
5
3
б) 2
а)
а) – поворотная камерная; б) – тигельная
1 – корпус; 2 – футеровка (тигель); 3 – нагревательные элементы; 4 – поворотный механизм; 5 – рабочее пространство печи
Рисунок 57 – Плавильные электрические печи сопротивления
Наряду с плавильными печами прямого нагрева, в которых металл плавится в ванне печи, в литейном производстве широко применяют камерные печи косвенного нагрева, в которых металл плавят в специальных тиглях (пламенные или электрические печи сопротивления, рисунок 58). Рабочая температура последних менее 1000 0С и применяют такие печи для плавки сплавов цветных металлов с температурой плавления ниже 1000 0С.

5
6
а) – пламенная; б) – электрическая; в) - вид камерной печи 1 – горелка; 2 – загрузочное (выгрузочное) окно; 3 – нагревательная камера;
4 – теплообменник; 5 – тигель с расплавляемым металлом; 6 – нагревательный элемент; 7 – дверца, закрывающая окно
Рисунок 58 - Схемы и вид камерной печи

4.2.2 Раздаточно-подогревательные печи
Этот тип печей предназначен для заливки жидкого металла непосредственно в форму. Изготовляет индукционные канальные печи для выдержки и перегрева чугуна ИЧКМ 6 / 0,5; ИЧКМ-16 / 0,5; ИЧКМ-40 / 1,0. Их производительность при перегреве жидкого чугуна на 100 °С составляет 1.4; 12; 24 т/ч. Для выдачи металла из печи применяют механизмы наклона печи, электродинамические насосы и избыточное давление газа над уровнем металла в печи. На рисунке 59 показана схема индукционной канальной печи.
3 |
4 |
|
5
6
2
1
8
1 – индуктор; 2 – заливочный сифон; 3 – герметичная крышка; 4 – трубка для подачи сжатого воздуха; 5 – ванна; 6 – верхняя часть разливочного сифона (ванна с отверстием); 7 – заливаемая форма; 8 - разливочный сифон
Рисунок 59 - Схема индукционной канальной раздаточной печи
Ванна 5 печи закрыта герметичной крышкой 3. Металл заливают в печь через заливочный сифон 2, а в форму — через разливочный сифон 8, верхняя часть которого выполнена в виде ванны с отверстием 6.
Через трубку 4 в рабочее пространство печи подается сжатый воздух или инертный газ. Под действием давления воздуха жидкий металл вытесняется из ванны в разливочный сифон. Количество металла, вытекающего через отверстие 6 в форму 7 регулируется с достаточной точностью по заданной программе. Обогрев печи осуществляется индуктором 1.
Для использования печи с различными транспортными системами формовочной линии печь может быть установлена на тележку, перемещающуюся в продольном и поперечном направлениях. Печи подобного типа имеют вместимость до 20 т.
Отечественная промышленность изготовляет печи для заливки жидкого чугуна непосредственно в литейные формы.
4.3 Подготовка сплава
Для выплавления чугуна и стали в качестве исходных материалов (шихты) используют литейные или передельные доменные чугуны, чугунный и стальной лом, отходы собственного производства и ферросплавы. Для понижения температуры плавления образующихся шлаков используют флюсы
— известняк, доломит и др.
Для плавления цветных сплавов используют как первичные (полученные на металлургических заводах), так и вторичные (после переплавки цветного лома) металлы и сплавы, кроме того, применяют лигатуры (специально приготовленные сплавы из двух или нескольких металлов) и флюсы (обычно хлористые и фтористые соли щелочных и щелочноземельных металлов).
В процессе плавки и после ее проводят подготовку сплава, которая заключается в их модифицировании, легировании или рафинировании.
Модифицирование - введение в жидкий металл добавок (десятые и сотые доли процента), которые существенно изменяют свойства сплава за счет изменения условий кристаллизации т.е. внутреннее строение. В качестве модификаторов используют частицы тугоплавких металлов, тем самым увеличивают число центров кристаллизации или поверхностно-активные элементы, которые образуют на поверхности кристаллов пленки, чем сдерживают их рост. Также в качестве модификаторов часто используют комплексные соединения, которые состоят из нескольких элементов обладающих раскисляющей, дегазирующей и графитизирующей способностями.
Легирование - введение в жидкий сплав различных добавок от единиц до десятков процентов, что повышает прочность, износостойкость, коррозийную стойкость и другие свойства. Бывает комплексное легирование. Легирование в отличие от модифицирования меняет не только свойства, но и химический состав.
Рафинирование (очистку) проводят различными способами (добавлением реагентов, продувкой аргоном или другими газами, обработка флюсами, выдержкой в вакууме).

4.4 Заливка форм
Заполнение металлом литейных форм проводят из ковшей разной конструкции, в которые металл заливают из печей, а также непосредственно из плавильных агрегатов. Особую сложность в литейном производстве вызывает заливка форм сплавами, склонными к окислению. В этом случае плавку металла и заливку форм совмещают в одном агрегате, работающем в вакууме или в среде инертных газов.
Использование заливочных литейных печей перед ковшевой заливкой дает ряд следующих преимуществ:
-снижается потребность в рабочей силе;
-улучшаются условия труда;
-повышается качество отливок;
-исключается попадание шлака в формы;
-уменьшаются потери металла;
-выдерживается заданная температура.
Литейное производство обладает высокопроизводительными автоматическими линиями, в которых формовка и заливка осуществляются автоматически, это стратегическое направление развития ЛП. Однако автоматизация производства для некоторых процессов бывает или малоэффективной или неприемлемой, особенно для мелкосерийного производства.
Заливка форм при специальном литье бывает свободной и под действием сил (центробежных, вакуума). Иногда формы заливают непосредственно из печи. При необходимости формы очищают от случайного мусора. Форы заливают на конвейере или на специальной площадке. Температура форм при заливке зависит от сплава и толщины стенок отливки. Часто заливают горячие формы, сразу после прокалки. Залитые формы охлаждаютвспециальныхкамерах.
Заливку форм производят различными (ручными и крановыми) ковшами (рисунок 60).
б)

в) |
г) |
а) — ручные; б) — стопорный; в) — чайниковый; г) — барабанный 1—рукоятка; 2 — ковш; 3, 5 — рукоятка и штурвал для поворота ковша; 4 — рама; 6—футеровка
Рисунок 60 - Разливочные ковши
Для свободной заливки используют обычные носковые и чайниковые ковши. Первые состоят из стального кожуха и футеровки, а вторые имеют перегородку для удержания шлака при заливке сплава в форму. Ковш перед заливкой сушат и прогревают при температуре 800 0C.
Залитые литейные формы определенное время выдерживают для затвердевания расплава и охлаждения отливки. Параметры этих процессов устанавливаются техническими условиями и зависят от массы, толщины стенок и конфигурации отливок, свойства металлов и других факторов.
4.4 Выбивка отливок из форм и стержней из отливок
После кристаллизации металла в литейной форме образуется отливка, которую затем извлекают из формы. Процесс извлечения отливок из форм называется выбивкой. Длительное охлаждение отливок в форме экономически не выгодно, но ранняя выбивка может привести к деформации и разрушению отливок ввиду недостаточной их механической прочности, возникновения больших внутренних напряжений и повышенной пластичности металла. Чугунные отливки извлекают из форм при температуре 500—800 оС, бронзовые
—при температуре 300—500 °С, алюминиевые — при 200—300 °С, магниевые
—при 100—150 °С.
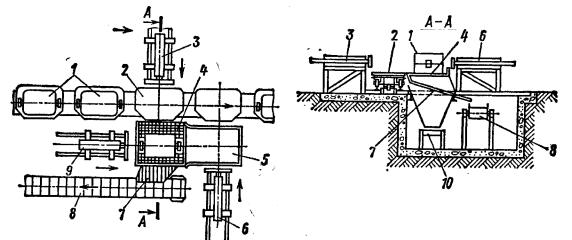
Способ извлечения отливок из форм зависит от размеров и способов изготовления форм, характера производства и сплавов, из которых получены отливки. Из металлических постоянных форм при литье в кокиль, центробежным способом и под давлением отливки извлекают без разрушения форм. Разовые формы — оболочковые, песчано-глинистые, по выплавляемым моделям разрушают при извлечении из них отливок. Для выбивки из песчаноглинистых разовых форм широко используют автоматические выбивные установки с решетками инерционного и встряхивающего типов. Применяют также подвесные вибрационные коромысла и скобы, закрепляемые на формах; содержимое опок выбивают путем их вибрации.
Выбивка — это извлечение отливок, сопровождающееся разрушением форм на специальном оборудовании. Выбивка форм производится пневматическим молотком или на выбивных решетках. Сыпучие наполнители и отливки удаляются из опок после кантовки в специальных приспособлениях. Дальнейшая обработка производится в зависимости от вида формы. Мелкие и средние отливки извлекают на выбивных решетках, крупные отливки—на инерционно-ударных решетках. После выбивки пустые опоки поступают обратно в формовочное отделение. Выбитую из форм горелую формовочную смесь охлаждают, просеивают и подают на приготовление формовочных смесей, а отливки—к месту очистки и обрубки.
На рисунке 61 показан пример выбивки отливок из форм.
1 - литейные формы; 2 – конвейер; 3, 6, 9 – толкатель; 4 - выбивная решетка; 5 – стол; 7 - наклонная решетка; 8 - пластинчатый конвейер;
10 - ленточный конвейер
Рисунок 61 - Выбивное устройство для извлечения отливов из форм