
Производство заготовок. Литье. Серия учебных пособий. Книга 3. Проектирование и производство отливок (литых заготовок)
.pdfПри верхнем положении плунжера 3 через отверстие в камере прессования сплав заполняет ее. При движении плунжера вниз отверстия 4 перекрываются, сплав под давлением от 10 до 30 МПа заполняет полость пресс-формы 5. Полости в отливке получают металлическим стержнем. После затвердевания отливки плунжер возвращается в исходное положение, остатки расплавленного металла из канала сливаются в тигель, а отливка, после раскрытия пресс-формы удаляется из нее выталкивателями 6.
После извлечения отливки и закрытия пресс-формы цикл повторяется. Машины с холодной камерой прессования применяют для изготовления
отливок из медных, алюминиевых, магниевых и цинковых сплавов массой до 45 кг. Давление плунжера на расплавленный металл составляет до 200 МПа. Машины с горячей камерой прессования используют для изготовлении отливок из легкоплавких сплавов (свинцово-сурьмянистых, алюминиевых, цинковых и других). От мелких до сложных массой от нескольких грамм до 25 кг.
Литье под давлением является высокомеханизированным процессом. Автоматизируют заливку расплавленного металла, очистку рабочих поверхностей пресс-формы, нанесение смазки и т. д. Литье под давлением позволяет получать отливки, максимально приближающиеся по форме, массе и размерам к готовой детали, дает возможность изготовлять сложные тонкостенные отливки с толщиной стенки от 0,8 до 0,6 мм и отверстиями диаметром до 1 мм. Литьем под давлением изготовляют корпуса приборов, декоративные изделия, детали двигателей легковых автомобилей и др.
Недостатком этого способа является высокая стоимость пресс-форм, сложность их изготовления, ограниченный срок их службы, опасность появления трещин в отливках
Литье под давлением широко используют не только для получения заготовок из металлов и сплавов, но и для переработкипластмас.
2.5.2.1 Литье под низким давлением
Литье под низким давлением применяют для получения крупных тонкостенных корпусных заготовок из легкоплавких сплавов.
Процесс характеризуется простотой и основан на том, что расплав под действием инертного газа по литнику подается в зазор между формой и стержнем и кристаллизуется вней (рисунок 36).

1 – расплавленный металл; 2 – плавильный тигель; 3 – электронагреватели; 4 – металлопровод; 5 – рабочая полость; 6 – форма; 7 - стержень
Рисунок 36 - Установка для литья под низким давлением
Расплавленный металл 1 из плавильного тигля 2, который нагревается электронагревателями 3, под давлением 0,01—0,08 МН/м2 инертного газа или воздуха выжимается по металлопроводу 4 в рабочую полость формы 5, где он кристаллизуется в пространстве между формой 6 и стержнем 7. Стержень может быть из обычной стержневой песчаной смеси. Давление инертного газа должно быть невысоким по той причине, что площадь зеркала расплавленного металла в тигле 2 во много раз больше площади металлопровода 4. Незначительное перемещение металла в тигле вызывает высокий подъем жидкого металла внутри металлопровода и в литейной форме. После кристаллизации отливки давление инертного газа снимается, металл из литника стекает в тигель, литейная форма раскрывается и из нее извлекают отливку.
2.5.2.2 Метод литья выдавливанием (Литье выжиманием)
Литью под низким давлением тождественно литье выдавливанием (рисунок 37) и штамповка из жидкого металла (штамповка в период кристаллизации рисунок 38, 39). Метод литья выдавливанием и жидкая

штамповка занимает промежуточное положение между литьем и объемной горячей объемной штамповкой.
Литье выдавливанием применяют для получения тонкостенных, с толщиной стенки от 2 до 5 мм, отливок типа панелей с большими габаритными размерами (2500 мм) преимущественно из алюминиевых и магниевых сплавов. Установки для литья выжиманием применяют двух конструкций: с угловым и плоскопараллельным перемещением подвижной полуформы. Сущность способа литья выдавливания с угловым перемещением полуформы (рисунок 37) заключается в том, что отливка образуется между двумя полуформами, одна из которых подвижна, а вторая - неподвижная.
1 – подвижная и 2 – неподвижная полуформы; 3 – стержень, образующий полости в отливке; 4 – металлоприемник
Рисунок 37 - Установка для литья выжиманием с угловым перемещением подвижной полуформы
На неподвижной полуформе устанавливают стержень 3. Металл заливают в металлоприемник 4 между полуформами 1 и 2, и они начинают соединяться. При этом из металлоприемника расплав выжимается в уменьшающийся зазор между полуформами 1 и 2, где и кристаллизуется после соединения полуформ.
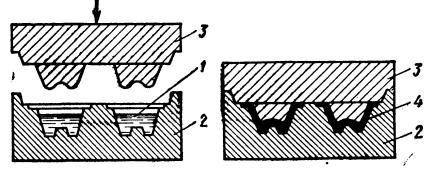
2.5.2.3 Жидкая штамповка
При литье в период кристаллизации (жидкой штамповке) порцию жидкого металла заливают в металлическую форму (матрицу), а затем пуансоном вытесняют металл, заставляя его течь в зазор между пуансоном и матрицей имеющий форму отливки. Ее применяют для получения крупных тонкостенных корпусных деталей из легкоплавкого материала.
Отличие штамповки жидкого металла от обычной штамповки заключается в том, что деформируемый материал затвердевает и приобретает кристаллическое строение в процессе штамповки.
Схема процесса жидкой штамповки показана на рисунке 38.
а) – заливка металла; б) - штамповка 1 – жидкий металл; 2 – нижняя часть металлической формы (матрица);
3 – верхняя часть формы (пуансон); 4 – заготовка (отливка)
Рисунок 38 - Схема процесса жидкой штамповки
Порцию жидкого металла 1 заливают в металлическую форму (матрицу) 2, в которую затем вводят металлический пуансон 3 или поршень, который выдавливает металл, вынуждая его заполнить все полости формы. В результате между формой 2 и пуансоном 3 образуется заготовка 4 (отливка).
К преимуществам литья под низким давлением (штамповки жидкого металла в период кристаллизации) относятся: отсутствие предварительной обработки исходного материала; небольшое удельное усилие и работа; возможность получения глубоких полостей малого диаметра, тонких и высоких

ребер; возможность получения очень крупных отливок и запрессовки в отливку различной арматуры. Все это обеспечивает высокую экономичность процесса.
Недостатки - быстрый износ формы (штампов) особенно при получении отливок из стали и возможность сваривания отливки со штампом, сложность точной дозировки объема и более низкое качество заготовки по сравнению с изделиями, имеющими волокнистое строение.
Устранить последний недостаток жидкой штамповки позволяют ее другие варианты. По одному из таких вариантов процесса жидкой штамповки в металлической форме получают предварительную литую заготовку (рисунок 39), которая сразу же в горячем виде подвергается горячей объемной штамповке в открытом штампе с получением окончательной заготовки (поковки). Такие заготовки приобретают высокую плотность и хорошие механические свойства благодаря интенсивному теплоотводу (в 20 раз превышающему теплоотвод обычного кокиля) и одновременному горячему деформированию литой структуры в период кристаллизации.
|
1 |
4 |
2 |
|
3 |
5
1 - верхняя и 3 - нижняя части штампа (формы); 2 – стержень;4 - отливка;5 – выталкиватель
Рисунок 39Схема штамповки предварительной заготовки в период кристаллизации (жидкой штамповки, литья под низким давлением)
2.5.2.4 Литье вакуумным всасыванием
Литье вакуумным всасыванием - получение простых отливок в виде втулок, колец, заготовок зубчатых колес из сплавов цветных металлов (бронзы, латуни) и т.д. путем заполнения формы расплавленным металлом за счет разряжения, создаваемого в форме (рисунок 40).

1 –расплавленный металл; 2 - огнеупорное керамическое плоское кольцо; 3 - металлическая полая водоохлаждаемая литейная форма (кристаллизатор); 4 — отливка
Рисунок 40 – Схема установка для литья вакуумным всасыванием
Для этого на поверхность расплавленного металла 1 помещают огнеупорное керамическое плоское кольцо 2, на которое вертикально устанавливают металлическую полую водоохлаждаемую литейную форму 3 — кристаллизатор. Внутри формы вакуум-насосом создается разрежение и расплавленный металл 1 втягивается внутрь холодной формы, где и кристаллизуется. Форму удаляют с поверхности расплавленного металла, разрежение устраняют и отливку 4 свободно извлекают из формы. Кристаллизация отливки происходит последовательно от холодной стенки к центру, по этому в отливке отсутствуют раковины, пористость и хорошо удаляются газы. Кроме этого, не расходуется металл на литниковую систему.
2.5.2.5 Литье намораживанием
Литье намораживанием применяют для изготовления труб с внутренними и наружными ребрами и других сложных профилей из малопластичных сплавов. На поверхность расплавленного металла помещают плиту из огнеупорного материала, в которой имеется отверстие требуемого профиля будущего литого изделия. Внутрь отверстия вводят затравку, к которой приваривается металл. При вытягивании затравки со скоростью, не превышающей скорости кристаллизации металла, из отверстия плиты извлекается заготовка соответствующего профиля так как за счет сил

поверхностного натяжения на границе жидкость – твердое тело создается небольшое разряжение, а за счет атмосферного давления жидкость втягивается за вытягиваемым твердым телом.
На этом принципе основано производство листового стекла.
2.5.3 Непрерывное и полунепрерывное литье
Литье непрерывное и полунепрерывное применяют для изготовления различного профиля (круглого, квадратного, прямоугольного, шестигранного и др.) с поперечным размером (диаметром) до 1000 мм из железоуглеродистых и цветных сплавов.
2.5.3.1 Непрерывное литье
Процесс непрерывного литья заключается в том, что жидкий металл поступает в кристаллизатор и из него отливка непрерывно вытягивается тянущим устройством.
Непрерывное литье осуществляют на установках вертикального или горизонтального типов (рисунок 41).
1 – расплав; 2 – металлоприемник; 3 - водо-охлаждаемый кристаллизатор; 4 - графитовая вставка; 5 – заготовка; 6 - тянущее устройство (валки)
Рисунок 41 - Схема установки непрерывного литья

Расплав 1 заливают в металлоприемник 2, откуда под действием гидростатического напора он поступает в водо-охлаждаемый кристаллизатор 3 с графитовой вставкой 4. Применение графита обусловлено тем, что он обладает высокой теплопроводимостью и термостойкостью, достаточной прочностью при высоких температурах и низким коэффициентом теплового расширения, плохо смачивается расплавленным металлом и не требует смазки. Кристаллизатор легко отделяется от металлоприемника, что позволяет быстро переналаживать установку на любой профиль. Из кристаллизатора заготовка 5 непрерывно вытягивается тянущим устройством 6, а кристаллизатор постоянно заполняется жидким металлом. Таким образом, процесс литья может протекать непрерывно. Металлоприемник выполняет роль постояннодействующей прибыли, что способствует получению плотной и качественной заготовки.
2.5.3.1.1 Литье методом жидкой прокатки
Литье методом жидкой прокатки - представляет совмещенный способ литья и прокатки (рисунок 42) и является разновидностью непрерывного литья
7
6
1 – ковш; 2 – металлоприемник; 3, 4 – водо-охлаждаемые прокатные валки; 5 – получаемая прокатанная отливка; 6 – расплавленный металл; 7 – охлаждающая вода
Рисунок 42 - Схема процесса жидкой прокатки
Расплавленный металл из ковша 1 наливают в приемник 2,
установленный между водо-охлаждаемми валками 3 и 4. Поступая в зазор между валками, металл кристаллизуется в получаемую прокатанную отливку 5. Скорость роста заготовки при непрерывном литье составляет от 0,5 до 1,5м/с.
Применяют для изготовления ленты, листов, фасонных заготовок. Ширина ленты до 750 мм, толщина от 0,7 до 2,5 мм.
2.5.3.2 Полунепрерывное литье
Полунепрерывным способом получают крупные чугунные трубы на вертикальных установках. Металл заливают в зазор между водоохлаждаемой формой кристаллизатора и стержнем на так называемое «ложное дно», по мере кристаллизации оно (дно) с отливкой медленно (со скоростью от 0,9 до 3,0 мм/мин) опускается. Тем самым получается труба длинной до 10 м.
Схема вертикальной установки для полунепрерывного литья показана на рисунке 43.

1 - кристаллизатор (литейная форма); 2 - пустотелый (охлаждаемый водой) стержень; 3 - жидкий сплав; 4 - ложное дно-затравка; 5 - ковш
Рисунок 43 - Схема установки полунепрерывного литья
Расплавленный металл при температуре до 1300 °С заливают в пустотелый охлаждаемый водой кристаллизатор 1, выполняющий функции литейной формы, внутрь которого вставлен стержень 2, также пустотелый и охлаждаемый водой. Между внутренней стенкой формы-кристаллизатора 1 и стержнем 2 образуется зазор, в который заливается жидкий сплав 3 из ковша 5. Для начала процесса литья в зазор между формой и стержнем перед заполнением его металлом вводят ложное дно - затравку 4. Затравка соединяется с расплавленным металлом и помере кристаллизации сплава постепенно со скоростью от 1 до 3 м/мин извлекается из кристаллизатора. Вытягивание затравки и соединившейся с ней отливки осуществляется приводными валками или столом, на котором была закреплена затравка. Диаметр труб достигает 1000 мм, а их длина до 10 м.