
Производство заготовок. Литье. Серия учебных пособий. Книга 3. Проектирование и производство отливок (литых заготовок)
.pdf1 – смесь; 2 – опока; 3 – модель; 4 – стол; 5 - станина машины служащая цилиндром; 6 – поршень; 7 – воздушный подводящий и 8 выхлопной канал
а) — встряхивающие машины; б) — машина с верхним прессованием; в) — машина с нижним прессованием; г) - диафрагменные машины; д) - прессование многоплунжерной головкой
Рисунок 22 - Способы уплотнения формовочной смеси в опоках
На встряхивающих машинах (рисунок 22 а) уплотнение смеси 1 в опоке 2 на поверхности модели 3 происходит благодаря кинетической энергии ударов стола 4 о станину машины 5, которая одновременно служит цилиндром. Стол 4 соединен с поршнем 6, который поднимается сжатым воздухом, поступающим в цилиндр через канал 7. При поднятии поршня выше выхлопного канала 8 сжатый воздух выходит из полости цилиндра, поршень вместе со столом 4, моделью3 и опокой 2, наполненной смесью 1, падая, ударяется о станину машины 5. Для достижения желаемой плотности смеси циклы повторяются.
На прессовых машинах (рисунок 22 б и в), имеющих гидравлический привод, уплотнение смеси происходит моделью или верхней колодкой благодаря статическому воздействию их на формовочную смесь, помещенную в опоку. Уплотнение прессованием со стороны плоской или профильной колодки 5, закрепленной на верхней траверсе 6 машины, осуществляется с использованием наполнительной рамки 4, содержащей такое дополнительное количество смеси 7, которое необходимо для получения нужной плотности в опоке 2 над моделью 3.
Уплотнение прессованием со стороны модели 3 (рисунок 22 в) происходит за счет сжатия смеси 1 между моделью 3 и траверсой 6 машины. Предварительно модель 3 вместе со столом 4 опускается в станину 5 машины. Образовавшееся в станине 5 пространство и опока 2 заполняются смесью. После этого модель 3 столом 4 поднимается и спрессовывает смесь, прижимая ее к верхней траверсе 6 машины.
На пневматических прессовых машинах (рисунок 22 г) универсальным уплотняющим элементом является эластичная диафрагма 4, которая под воздействием сжатого воздуха в резервуаре 5 уплотняет смесь 1 в опоке 2 на поверхности модели 3.
Дифференциальное прессование многоплунжерной головкой изображено на рисунке 22 д. Прессующие колодки 9 уплотняют формовочную смесь 1 над моделью 3 (установленной на столе машины) в опоке 2 под действием жидкости 6, которая заполняет корпус 5 прессующей головки и оказывает давление на поршни (плунжеры) 7, связанные штоками 8 с прессующими колодками 9. Дополнительный объем формовочной смеси, необходимый для уплотнения, помещен в наполнительной рамке 4. Многоплунжерная прессовая головка дает возможность развивать высокие давления на формовочную смесь и равномерно уплотнять ее по всему сложному контуру модели.
При изготовлении форм применяют также машины с комбинированными методами уплотнения (прессование под высоким давлением в сочетании с пескодувным или встряхивающим прессованием с амортизацией удара). Для получения форм также используют и автоматические формовочные линии.
После уплотнения формовочной смеси в опоке тем или иным способом полученную полуформу снимают с модели. Для облегчения этого процесса к модельной плите подключают вибраторы. Извлечение модели из полуформы осуществляется разными способами: протяжкой, штифтовым съемом, поворотом модельной плиты, опрокидыванием стола машины.
В цехах массового производства отливок используют комплексные автоматизированные линии, где происходит изготовление и сборка форм, заливка их металлом, охлаждение и выбивка отливок из форм.
Машинная формовка — основной метод изготовления литейных форм в парных опоках — осуществляется по модельным плитам. Машинная формовка позволяет механизировать уплотнение формовочной смеси в опоках и удаление модели из формы (самые трудоемкие операции), а также произвести вспомогательные операции.
2.3.1.3 Пленочно-вакуумная формовка
Новым направлением в ЛП является пленочно-вакуумная формовка. Она исключает смесеприготовительный участок и обеспечивает безопасную формовку
Сущность способа показана на рисунке 23.

1 – перфорированная плита; 2 – модель; 3 и 6 – эластичная пленка; 4 – опока; 5 – кварцевый песок
Рисунок 23 – Схема пленочно-вакуумной формовки
Перфорированную модель 2 устанавливают на перфорированную плиту 1 внутрь опоки 4 и накрывают эластичной пленкой 3, способной выдерживать без разрушения контакт с расплавленным металлом и обеспечивать чистую и гладкую поверхность отливке. Через модель и плиту отсасывается воздух, что способствует плотному прилеганию пленки к поверхности модели. После этого на поверхность пленки, обтянувшей модель, засыпают кварцевый песок 5 до верхнего края опоки 4. Для уплотнения песка применяют легкую вибрацию. Опоку 4, заполненную песком сверху, закрывают пленкой 6 и вновь отсасывают воздух из опоки, что приводит к уплотнению песка и плотному прилеганию пленки 6. Так изготовляют верхнюю и нижнюю полуформы, затем их собирают и заполняют металлом. Образовавшаяся отливка легко удаляется из песчаной формы, а наполнительный песок может быть многократно использован. При таком способе изготовления форм не требуется применения смесеприготовительного оборудования и дорогих материалов, входящих в состав формовочных смесей.
В зависимости от типа производства, размеров отливки сборку форм осуществляют на конвейерах, сборочных стендах или плацу (специально отведенная площадка в литейном цехе). Перемещение и установка тяжелых стержней и наложение тяжелых полуформ механизированы.
Наряду с машинным получением литейных форм в опоках широко применяют получение форм без опок.

2.3.1.4 Безопочная формовка
На автоматических линиях пространство между полумоделями заполняется формовочной смесью и прессуется, причем каждая из полумоделей представляет собой одну из частей полуформы (верхняя - нижняя, левая - правая), которые, как бы, поменяны местами. После поднятия полумодели образуется часть двухсторонней формы. Пространство, между спрессованными частями образует литейную полость. Многократные повторения операций позволяют получить заготовки для пакетов из двухсторонних форм.
Принцип получения безопочных форм и отливок в них представлен на рисунке 24.
а) |
б) |
в) |
А В |
1 2
а) – получение двусторонней формы; б) – сборка пакета; в) – заливка формы металлом
1 и 2 – полумодели; 3 – бункер; 4 – плунжер гидроцилиндра;
5 – задвижка бункера; 6 - пакет из сомкнутых двусторонних форм; 7 – заливаемый металл; 8 - ковш
А – двусторонняя форма; Б – исходная формовочная смесь; В – отливки
Рисунок 24 - Схема изготовления безопочных форм с вертикальным разъемом и отливок в них
Безопочная формовка отличается высокой производительностью и экономичностью. При таком способе изготовления форм достигается достаточная точность отливок, сокращаются производственные расходы на изготовление опок, сокращаются площади цеха из-за отсутствия транспортных операций по передаче опок от выбивки к машинам. Упрощаются процессы выбивки отливок из форм.
Существует два типа автоматических машин, изготовляющих формы с вертикальным и горизонтальным разъемами. В безопочных формах может быть получена широкая номенклатура отливок, начиная от ключей дверных замков до блоков цилиндров двигателей малолитражных автомобилей.
Безопочные формы с вертикальным разъемом изготовляют на автоматах проходного и карусельного типов. Производительность первых автоматов достигает до 300 форм в час, а вторых – до 540 форм в час.
2.3.2Специальные способы литья
Влитейном производстве широко применяют специальные способы изготовления отливок, имеющие ряд преимуществ по сравнению со способом литья в песчаные формы. К таким особенностям относятся: возможность механизации и автоматизации производственного процесса; улучшение условий труда; увеличение производительности; значительное снижение расходов формовочных материалов (а иногда полное исключение их из процесса литья) и получение отливок с минимальными припусками на механическую обработку.
К специальным видам литья относят литье в оболочные формы, литье по выплавляемым моделям, литье в кокиль, литье под давлением, центробежное, непрерывное и полунепрерывное литье, а также литье в керамические разъемные формы, литье вакуумным всасыванием, литье выжиманием, литье с направленной кристаллизацией, жидкая штамповка.
2.3.2.1 Литье в оболочковые формы
Оболочковая форма представляет собой две скрепленные рельефные полуформы с толщиной стенок от 5 до 15 мм. Технологический процесс получения оболочковой формы показан на рисунке 25.
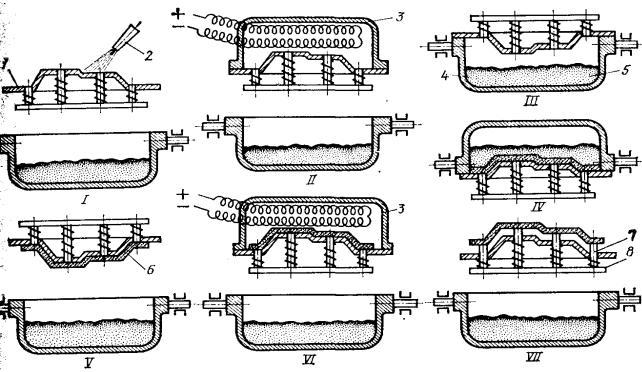
1 - модельная плита; 2 – пульверизатор; 3 - электрическая печь; 4 - поворотный бункер; 5 - песчано-смоляная смесь;
6 - образовавшаяся оболочка; 7 – толкатели; 8 – опорная плита
Рисунок 25 - Последовательность изготовления оболочковых полуформ
Формовка состоит из следующих операций:
1)очистка металлической модельной плиты 1 и покрытие ее из пульверизатора 2 специальным термостойким разделительным составом для легкого отделения и снятия оболочки с плиты;
2)нагрев модельной плиты в электрической печи 3 до температуры 220—
250 0С;
3)установка и закрепление нагретой модельной плиты на поворотном бункере 4, содержащем песчано-смоляную смесь 5;
4)поворот бункера с моделью на 180°, нанесение песчано-смоляной смеси на нагретую модельную плиту и формирование оболочки;
5)возврат бункера с модельной плитой в исходное положение, удаление излишней песчано-смоляной смеси и снятие плиты с образовавшейся на ней оболочкой 6 с бункера;
6)поворот модельной плиты на 180° и установка ее в электрическую печь 3 для окончательного отвердения оболочки при температуре до 350 °С в течение времени до 180 с;
7)съем оболочки с модельной плиты с помощью толкателей 7 с опорной
плиты 8.
Аналогичным образом изготовляют вторую (парную) полуформу.
Такие формы изготовляют из песчано-смоляной смеси на специальных полуавтоматических и автоматических машинах. Изготовление оболочковых форм основано на свойствах термореактивной смолы, плавиться при нагревании и обволакивать зерна песка. Затем смола затвердевает, связывая зерна песка, образует прочную оболочку.
В полученные оболочковые полуформы устанавливают стержни. Соедение полуформ производят по фиксаторам, с помощью скоб, струбцин или склеиванием. Перед заливкой крупных отливок нижние полуформы обкладывают металлической дробью или песком, а верхние—нагружают, чтобы предупредить их размыкание. После охлаждения отливки ее выбивают из формы и направляют на последующую обработку.
Литье в оболочковые формы обеспечивает получение точных отливок с чистыми (гладкими) поверхностями, уменьшение расхода формовочных материалов, сокращение производственных площадей, высокую производительность труда при изготовлении форм, возможность длительного хранения оболочковых форм и стержней, экономию металла из-за уменьшения расхода его на литниковую систему и прибыли, сокращение длительности процессов обрубки и очистки. При этом способе получения отливок расход формовочных материалов в 20 раз меньше, чем при литье в сырую формовочнуюсмесь.
К недостаткам литья в оболочковые формы относят высокую стоимость смолы, оснастки, оборудования, длительность доводки процесса. Способ литья в оболочковые формы применяют только в условиях крупносерийного и массового производства.
Кроме оболочковых форм этим способом изготовляют оболочковые стержни, при изготовлении которых используют нагреваемые металлические стержневые ящики. При сборке форм полуформы склеивают специальным клеем на прессах, что обеспечивает высокую прочность шва.
В промышленности внедрены многопозиционные автоматические машины и автоматические линии изготовления оболочковых форм и стержней. Литье в оболочковые формы обеспечивает высокую точность отливок, малую шероховатость поверхности, снижает расход формовочных материалов и объем механической обработки, повышает производительность труда. В оболочковых формах изготовляют отливки массой от 0,20 до 50 кг и толщиной стенок от 3 до 15 мм из всех литейных сплавов для приборов, автомобилей, тракторов, металлообрабатывающих станков и др.
2.3.2.2 Литье по выплавляемым моделям
Отливки по выплавляемым моделям характеризуются высокой точностью (допуски на размеры от ± 0,075 до ±0,2 мм) и возможностью получения сложных отливок. Модель получают из легкоплавкого материала, ее покрывают пленкой из огнеупорного материала. Затем из оболочки выплавляют модель. Оболочку прокаливают для придания прочности и огнеупорности, а затем заливают металлом. Основными составляющими выплавляемых моделей является парафин, стеарин, воск. Для изготовления выплавляемой модели легкоплавкий пастообразный состав запрессовывают в металлическую разъемную пресс-форму, изготовленную обычно из стали или алюминиевых сплавов, реже из гипса или пластмасс, и имеющую полость, которая по конфигурации и размерам точно соответствует модели отливки. После затвердевания модельного состава форму раскрывают и из нее извлекают модель.
Таким образом, изготавливают в условиях массового производства в одной пресс-форме несколько моделей, соединенных каналами литниковой системы. Затем отдельные модели 3 (звенья) устанавливают на металлический стояк 1 (рисунок 26 а) центральными втулками литниковых каналов 2. Нижнюю часть стояка закрывают колпачком 4, который изготовляют из модельного состава и припаивают к литнику верхней модели (звена).

а) - собранный блок выплавляемых моделей; б) - неразъемная форма в сборе 1 – металлический стояк; 2 – центральные втулки литниковых каналов; 3 – модели; 4 – колпачок; 5 – неразъемная форма; 6 – опока; 7 – засыпка песка
Рисунок 26 – Схемы формы для получения отливок по выплавляемым моделям
Сверху на металлический стояк устанавливают модель литниковой воронки. Собранный блок покрывают 3—4 раза тонким слоем обмазки, которая состоит из огнеупорного пылевидного кварца и связующего материала (обычно гидролизованного раствора этилсиликата).
После каждого покрытия модель для упрочнения посыпают сухим мелким кварцевым песком и сушат. Полученная таким образом оболочка имеет толщину 3—5 мм. После сушки из моделей извлекают металлический стояк, а легкоплавкие модели вытапливают из оболочковых форм. Для этого используют горячую воду, имеющую температуру около 90 °С, или производят выплавление в расплаве модельного состава, паром, горячим воздухом. В ряде

случаев модели выжигают или растворяют.
Неразъемную форму 5 (рисунок 26 б) устанавливают в опоку, засыпают песком 7 и помещают в электропечь для прокаливания при температуре от 850 до 900 °С до необходимой прочности и выжигания остатков модельного состава. Затем нагретую форму подают на заливку. После охлаждения отливки ее выбивают из формы и направляют на последующую обработку.
Литье по выплавляемым моделям применяют для получения отливок, конфигурация которых при изготовлении их из сортового металла или поковок потребовала бы большой и сложной механической обработки. Этим способом изготовляют отливки с толщиной стенок от 0,5 до 10 мм и массой от 2 г до 100 кг. Наиболее экономично применение литья по выплавляемым моделям в серийном и массовом производстве мелких стальных отливок.
1 – деталь; 2 – металлическая форма для получения выплавляемой модели 3; 4 – блок выплавляемых моделей с литниковой системой; 5 – модели с огнеупорным покрытием; 6 - керамическая оболочка формы; 7 – опока; 8 - засыпка;
9 – форма с отливками
Рисунок 27 - Схема технологического процесса изготовления формы и отливок по выплавляемым моделям
Металлическую пресс-форму 2 изготавливают по размерам детали 1 с учетом усадки модельного состава и сплава. Внутрь рабочей полости прессформы при помощи шприцев через литниковые каналы запрессовывают модельный состав. После кристаллизации состава пресс-форму раскрывают и модель 3 извлекают. Отдельные модели собирают в блоки 4 с общей литниковой системой при помощи пайки. В одном блоке может быть несколько десятков и даже сотен моделей.