
Производство заготовок. Литье. Серия учебных пособий. Книга 3. Проектирование и производство отливок (литых заготовок)
.pdf
V1 = р4 (0,16 2 −0,12 ) 0,06 ≈735 10−6 м3
V2 = р4 (0,12 −0,06 2 ) 0,04 ≈ 201 10−6 м3
V3 = р4 (0,06 2 −0,02 2 ) 0,08 ≈ 201 10−6 м3
Vд = (735 + 201 + 201) 10 6 = 1137 10 −6 м3 mд = 1137 10 −6 7850 ≈ 8,925кг
Для удобства выполнения расчетов массы готовой детали и заготовки его проводим по их чертежам и по единому алгоритму.
Находим массу готовой детали по её чертежу:
QЗ = γЗ 10−3 π / 4 (1802 15 +1052 65 −602 (80 −70) −852 |
40 − |
−802 (70 −40) −4 152 15 −4 (302 −152 ) 3) = γЗ π / 4 102 |
5,27 г |
Здесь и далее γЗ – плотность детали, заготовки в кг/м3; размеры - в мм. Для первого варианта изготовления масса заготовки:
QЗI =γЗ 10−3 π / 4 (1802 22,9 +110,62 62,2 −53,22 (62,2 − 49,0) − −852 40 −72,42 (49 + 21,2 − 40) =γЗ π / 4 102 10,23 г
Исходя из этого определим коэффициент использования металла.
4.1 Коэффициент использования металла
Разность масс заготовок:
QЗI −QЗII =γЗ π / 4 102 (10,23 −7,54)=1490 г = 1,49 кг; (при γ З = 7,08).
КИМ в ЛП часто выражается двумя коэффициентами. Коэффициентом выхода годного - процентным отношением массы
отливок к массе залитого в форму металла, и коэффициентом использования заготовок - отношением массы детали к массе отливок.
ИПК ГОУ ОГУ 1201. 51 05. 04 ПЗ |
Лист |
13 |
|
Изм. Лист № докум. Подп. Дата |
|

По аналогии со штамповкой, когда коэффициент использования металла представляют в виде
ким = |
mд |
= kв.т. kв.г. |
|
||
|
mиз |
где mз , mп , mд – масса заготовки, поковки и детали, кг;
kв.г., kв.т. – коэффициенты выхода годного и весовой точности
определяются по формулам: kв.г mд kвт = mп ,
mп mиз
При специальных видах литья эти коэффициенты выше, чем при литье в обычные песчаные формы (экономия до 10-15 %).
KИМ = |
γ |
З |
π / 4 102 5,27 |
= 0,515 |
, |
||
γЗ π / 4 10 |
2 |
10,23 |
|||||
|
|
|
|
||||
следовательно ким = 0,515 , |
что является не хорошим (низким) |
||||||
показателем. |
|
|
|
|
|
|
|
ИПК ГОУ ОГУ 1201. 51 05. 04 ПЗ |
Лист |
14 |
|
Изм. Лист № докум. Подп. Дата |
|

1.Отливку залить в оболочковую форму с сухими песчаными стержнями.
2.Точность отливки 6-6-3-2
ГОСТ 26645-85.
3.Место отлома питателя зачистить заподлицо с
поверхностью 105; уступ не более 1,2 по ширине питателя.
4. Материал - чугун СЧ ГОСТ 1412-85
АКИ ГР01ТМ

Список использованных источников
1ГОСТ 26645-85 Отливки из металлов и сплавов. Допуски размеров, массы и припусков на механическую обработку. Стандартгиз, 1989. 55с.
2ГОСТ 3.1126 - 88. ЕСТД. Правила выполнения графических документов на отливки. - Введ 01.01.89 – М.: Издательство стандартов, 1988. - 4 с.
3ГОСТ 321292клоны формовочные.
5 Абрамов Г.Г., Панченко Б.С. Справочник молодого литейщика - М.: Высшая школа, 1991 – 319 с.
7Справочник технолога-машиностроителя / Под ред. А.Г. Косиловой, Р.К. Мещерякова. – М.: Машиностроение, 1985. – T.1. – 656 с.
8Литейное производство / Под ред. И.Б.Куманина. – М.: Машиностроение, 1971. – 319 с.
9Килов А.С. Обработка материалов давлением в промышленности – Оренбург.: ГОУ ОГУ, 2003 – 267 с.
10Килов А.С, Вольнов С.В., Килов К.А.. Производство заготовок. Объемная штамповка – Оренбург.: ГОУ ОГУ, 2004 – 155 с.
ИПК ГОУ ОГУ 1201. 51 05. 04 ПЗ |
Лист |
16 |
|
Изм. Лист № докум. Подп. Дата |
|
Приложение Г
(справочное)
Лабораторная работа «Изготовление литейной формы спроектированной отливки»
Г.1 Цель работы
Практически освоить основные положения и общие принципы методики проектирования литых заготовок, литейной формы в целом и отдельных её элементов.
Научиться определять размеры литой заготовки по чертежу детали. Научиться разрабатывать простейшую литейную технологию.
Г.2 Оосновные сведения
Для изготовления разовой литейной формы необходимо иметь модельный комплект, состоящий из литейной модели, стержневых ящиков, модели литниковой системы, модели, подмодельных плит.
В зависимости от сложности и конфигурации отливки модели могут быть целиком или разъемными. Конструкция модели должна обеспечить легкость ее извлечения из формы. Для получения в отливках отверстий и внутренних полостей в форму помещают стержень. Стержни изготавливаются в стержневых ящиках из стержневой смеси.
При выборе способа формовки необходимо учитывать размеры детали, ее конфигурацию и серийность производства.
Различают следующие виды серийности производства:
1)единичное – до 200 отливок в год;
2)мелкосерийное – от 200 до 1000 отливок;
3)серийное – от 1000 до 20000 отливок;
4)крупносерийное – от 20000 до 100000 отливок;
5)массовое – от 100000 отливок.
Для единичного производства применяют ручную формовку по деревянной модели. При серийном и массовом производстве разовые формы изготавливают на формовочных машинах по металлическим или пластмассовым модельным платам.
Основой для проектировния отливки является чертеж детали (рисунок Г.1а). На чертеже детали кроме основных размеров указана шероховатость поверхности и в зависимости от ее величины студент решает вопрос о необходимости механической обработки данной поверхности. Остальные поверхности, которые не подлежат механической обработке, указаны знаком в правом верхнем углу чертежа.
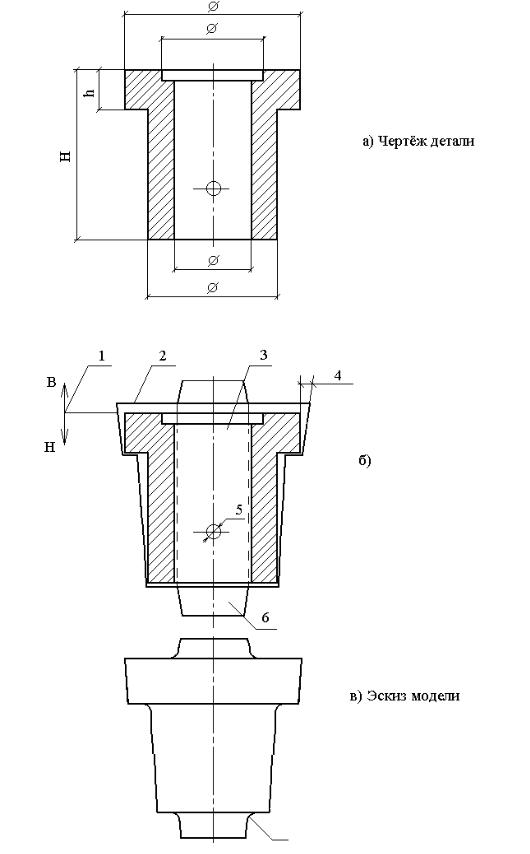
РМФ
Контуры отливки
7
1 – плоскость разъема модели и формы; 2 – контур отливки; 3 – стержень; 4 – формовочный уклон; 5 – не отливаемое отверстие; 6 – стержневой знак; 7 – радиус закругления (галтели)
Рисунок Г.1 – Чертеж детали и эскизы отливки и модели
На чертеже детали (рисунок Г.1 а) условным обозначением наносят: припуски на механическую обработку; технологические припуски (литейные уклоны, напуски, галтели); линии разъема формы и контуры стержней и их знаковых частей (рисунок Г.1 б); и установки прибылей (если они необходимы); все размеры, марку сплава, и т.п.
Припуск на механическую обработку – дополнительный слой металла, который удаляют в процессе механической обработки отливки. Припуски на механическую обработку назначают только на поверхности, где указана шероховатость или квалитет точности ниже 10. На чертеже детали припуск на механическую обработку указывают тонкой линией, штриховой или красным карандашом. Величина припуска на механическую обработку регламентируется ГОСТом 26645-85 в зависимости от класса точности, способов литья, размера отливки, а также положения обрабатываемой поверхности в процессе отливки.
В таблицах Б.5 Б.7 приведены классы точности отливок и величины припусков на механическую обработку чугунных и стальных отливок.
Литейные уклоны на отливке облегчают извлечение моделей из формы без разрушения ее, и для свободного удаления стержня из стержневого ящика. Уклоны выполняют в направлении извлечения модели из формы. На чертеже формовочные уклоны указывают, как и припуски на механическую обработку, - красным карандашом или тонкими линиями. Величина формовочных уклонов регламентируется ГОСТ 3212 - 92 и ГОСТ 26645 – 85 в зависимости от высоты боковых поверхностей (таблица Б.4).
Напуск – увеличение размера служит для упрощения изготовления отливки. Так отверстия в отливке диаметром 20-30 мм в условиях массового и серийного производства и диаметром до 50 мм в условиях единичного производства можно не делать, так как их целесообразнее просверлить в процессе механической обработки. В этом случае на чертеже отливки отверстия зачеркивают тонкими линиями по диагонали.
Галтели – закругления внутреннего угла отливки в модели (рисунок Г.1 в) для получения плавного перехода в сопрягаемых стенках. С помощью галтелей исключается осыпание формовочной смеси в углах модели при ее извлечении из формы. Нормативные материалы рекомендуют пользоваться нормальным рядов радиусов: 1,2.3,5,10,15,20,25,30,40 мм. Радиусы галтелей составляют от 1/5 до 1/3 средней арифметической толщины сопряженных стенок отливки.
Плоскость разъема формы и модели обозначают на чертежах буквами РМФ и двумя стрелками с буквами В (верх) и Н (низ).
Литейный стержень – элемент литейной формы для образования отверстий, полости или иного сложного контура в отливке. Стержни бывают вертикальные и горизонтальные в зависимости от их положения при установке в форму. Конфигурацию и размеры стержней регламентированы справочной литературой. Для правильной установки и крепления стержней в форме служат знаковые части стержня, которые у горизонтальных стержней делают прямыми, а у вертикальных с уклоном для удобства сборки формы. Длину знаков определяют в зависимости от длины стержня (таблица Г.4 и Г.5).
Таблица Г.4 - Высота нижних вертикальных знаков стержня В миллиметрах
Диаметр |
|
Длина стержня, мм |
|
|
стержня, мм |
До 150 |
151-500 |
501-1000 |
1001 и выше |
До 100 |
20-30 |
50-70 |
100-120 |
|
101-400 |
20-40 |
40-60 |
70-100 |
140-190 |
401-1000 |
40-50 |
40-50 |
60-100 |
110-180 |
1001 и выше |
60-100 |
60-110 |
60-110 |
80-150 |
Высоту верхнего знака принимают равной 60 % от высоты нижнего знака. На чертеже стержни в разрезе штрихуют по контуру. Если стержней несколько, для каждого стержня применяют номер и свою, отличающуюся от
других штриховку.
Таблица Г.5 - Длина горизонтальных стержневых знаков В миллиметрах
Диаметр |
|
|
Длина стержня, мм |
|
|
|
стержня, мм |
До50 |
51-150 |
151-300 |
301-500 |
501-750 |
750-1000 |
До 25 |
15 |
25 |
40 |
- |
- |
- |
25-50 |
20 |
30 |
45 |
60 |
- |
- |
51-100 |
25 |
35 |
50 |
70 |
90 |
110 |
101-200 |
30 |
40 |
55 |
80 |
100 |
120 |
201-300 |
- |
50 |
80 |
90 |
110 |
130 |
Литейная модель – приспособление для получения в форме отпечатка, конфигурацией, соответствующей внешней поверхности отливки.
Чертеж модели составляют по наружным очертаниям детали с технологическими указаниями, причем все размеры увеличивают на коэффициент линейной усадки. В среднем коэффициент линейной усадки принимается: для серого чугуна – 1 %; для цветных сплавов от 1до 1,5 %; для стали – 2 %.
На рисунке Г.1 в дан эскиз деревянной модели для ручной формовки. Конструкция отливки должна иметь плавные переходы от больших
сечений к меньшим (ребра жесткости, окна) с целью равномерного охлаждения
ипредотвращения внутренних напряжений и трещин.
Сцелью повышения точности отливок и упрощению моделей и процесса формовки необходимо стремиться к неразъемным моделям.
Сборкой называется процесс соединения отдельных частей формы в одно целое и подготовка формы к заливке металла. Сборка формы состоит из следующих операций: установка и крепление стержней, накрывание верхней опоки, крепление опок, установка литниковой чаши, контроль правильности сборки. Форма в сборе должна быть показана на чертеже так, чтобы было видно положение стержней и литниковых каналов, выпоров, прибылей и способов крепления опок. На рисунке Г.2 показана форма в сборе, а на рисунке Г.3 – готовая отливка.

Г.3 Порядок выполнения работы
Г.3.1 Получить чертеж детали.
Г.3.2 Определить линии разъема модели и формы, положение отливки в форме и выбрать способ формовки.
Г.3.3 Определить количество стержней, их контуры, размеры знаков.
Г.3.4 Указать какие исправления внесены в чертеже отливки, чтобы она была технологична.
Г.3.5 Определить припуски на механическую обработку.
Г.3.6 Разработать чертеж отливки и нанести технологические указания на чертеж.
Г.3.7 Определить размеры уклонов и галтелей.
Г.3.8 Рассчитать размеры модели и стержня, вычертить их. Г.3.9 Разработать чертеж «форма в сборе».
Г.4 Содержание отчета
Г.4.1 Чертеж литейной формы в сборе.
Г.4.2 Чертеж детали с разработанной литейной технологией: указать разъем, величину уклонов, галтелей, припусков на механическую обработку, определить контур стержня и его границы.
Г.4.3 Провести характеристику металла. Г.4.4 Эскиз модели и стержня с размерами. Г.4.5 Начертить эскиз «форма в сборе.
Рисунок Г.1 – Литейная форма в сборе

Рисунок Г. 2 – Эскиз отливки
Г. 5 Контрольные вопросы
Г.5.1 Что относится к модельному комплекту.
Г.5.2 Назначение модели и требования, предъявляемые к ее изготовлению. Г.5.3 Назначение стержней и стержневых знаков.
Г.5.4 В каких случаях назначаются припуски на механическую обработку и их определения.
Г.5.5 Назначение формовочных уклонов и их определение. Г.5.6 Назначение галтелей и их определение.
Г.5.7 Как учитывается усадка металла при изготовлении моделей. Г.5.8 Чем размеры модели отличаются от размеров отливки.
Г.5.9 Чем размеры отливки отличаются от размеров конструкторского чертежа.