
Материалка
.pdf
Температурный интервал деформации |
выбирают по |
табличным данным |
(табл.1.2). Ориентировочно температурный |
интервал |
горячей деформации |
можно определить по критическим точкам |
по диаграммам состояния сталей |
(рис.1.6). Максимально допустимая температура начала деформации углеродистых сталей Тр = Тс – 150 оС, где Тс – температура, соответствующая линии солидуса диаграммы железо-углерод, оС.
Температура окончания деформации для доэвтектоидных сталей Тк = Аr3 + 30 оС; эвтектоидных – Тк = Аr1 + 30 оС; заэвтектоидных – Тк = Аr1+ 60 оС;
где Аr1 – температура, определяющая температуру конца перехода аустенита в перлит (линия РS); Аr3 – температура начала перехода аустенита в феррит (ли-
ния GS) (рис. 1.6).
Основными видами дефектов брака при нагреве является образование окалины, обезуглероживание, недогрев.
Продолжительность и скорость нагрева и охлаждения назначают, исходя из марки стали и размеров заготовки.
Продолжительность выдержки обычно берут из расчета 1 мин на 1 мм условной толщины заготовки.
Рис. 1.6. Диаграмма состояния железоуглеродистых сплавов и температурные интервалы ковки и штамповки:
1 – зона пережога; 2 – зона перегрева; 3 – зона горячей деформации; 4 – зона наклепа
Для легированных сталей скорость нагрева и охлаждения до550–600 оС должна быть медленной (15–50 оС/мин). Для углеродистых и легированных сталей при температуре свыше 550–600 оС скорость нагрева следует принимать максимально возможной.
10

Таблица 1.2
Температурный интервал ковки и штамповки для конструкционных сталей
|
Температура |
Температура конца |
Рекоменду- |
||
|
ковки, |
оС |
емый ин- |
||
Марка стали |
начала ковки |
||||
|
|
тервал тем- |
|||
|
(максимальная) |
не выше |
не ниже |
||
|
ператур |
||||
|
оС |
|
|
ковки, оС |
|
1 |
2 |
3 |
4 |
5 |
|
Ст.0,1,2,3 |
1300 |
800 |
700 |
1280-750 |
|
10,15 |
1300 |
800 |
700 |
1280-750 |
|
20,25,30,35 |
1280 |
830 |
720 |
1250-800 |
|
40,45,50,55,60 |
1260 |
850 |
760 |
1200-800 |
|
15Г,20Г,30Г,40Г,50Г |
1260 |
850 |
760 |
1200-800 |
|
60Г,65Г,50ХФА |
1200 |
850 |
760 |
1180-800 |
|
10Г2,30Г2, 35Г2, 15Х2, |
|
|
|
|
|
20Х, 30Х,50Х, 15ХА, |
1220 |
870 |
750 |
1200-800 |
|
10ХА, 30ХА |
|
|
|
|
|
40Х, 45Х, 50Х |
1200 |
870 |
800 |
1130-830 |
|
40Г2, 45Г2, 50Г2, 18ХГ |
1200 |
870 |
800 |
1180-830 |
|
18ХГТ, 40ХГ |
1200 |
870 |
800 |
1180-800 |
|
20ХФ, 20ХФА, 40ХФА |
1240 |
850 |
760 |
1200-800 |
|
38ХС, 40ХС, 20ХГС, |
1200 |
870 |
800 |
1150-830 |
|
25ХГС |
|
|
|
|
|
30ХМ,35ХМА,35Х2МА |
1220 |
880 |
830 |
1180-850 |
|
20ХН, 27СГ,35СГ |
1250 |
850 |
780 |
1200-800 |
|
40ХН, 45ХН, 50ХН, |
|
|
|
|
|
12ХН2, 12ХН3 |
1250 |
850 |
780 |
1180-800 |
|
30ХН3, 37ХН3А, |
|
|
|
|
|
12Х2Н4 |
1180 |
900 |
800 |
1160-850 |
|
38ХМЮА, 35ХМФА, |
|
|
|
|
|
1Х13, 2Х13, 3Х13, |
1180 |
950 |
850 |
1160-880 |
|
Х10С2М |
|
|
|
|
|
18ХНВА, 25ХНВА |
1200 |
900 |
800 |
1180-850 |
|
32ХН3МА, |
|
|
|
|
|
40ХНМА,30ХН2МФА |
1200 |
900 |
850 |
1150-870 |
|
ШХ4, ШХ10, ШХ15 |
1180 |
870 |
830 |
1120-850 |
|
1Х18Н9, Х9С2 |
1200 |
950 |
870 |
1180-900 |
1.2.3. Оборудование для горячей деформации
Штамповку осуществляют на молотах, кривошипных горячештамповочных прессах (КГШП), горизонтально-ковочных машинах (ГКМ). Вид оборудо-
11

вания и соответствующий технологический процесс изготовления поковки выбирают, исходя из конфигурации и массы деталей, годовой программы, техни- ко-экономических показателей, требований к размерам, форме и свойствам (механическим и эксплуатационным) изделия.
Горячештамповочный пресс
Поковки круглые в плане в условиях массового и серийного производства штампуют на горячештамповочных прессах(КГШП) (рис.1.7; табл. П 5–3) , имеющих высокую производительность. Кривошипные прессы деформируют заготовку давлением рабочих органов ползуна с закрепленным на нем инструментом – штампом. Ползун приводится в движение кривошипно-шатунным механизмом, преобразующим вращательное движение электродвигателя в воз- вратно-поступательное движения.
Прессы – машины статического действия. Поэтому окалина, образующаяся, вследствие окисления стали во время нагрева, может вдавливаться в поверхность поковки (на молотах окалина удаляется в промежутках между первыми ударами). В связи с этим целесообразно применять безокислительный нагрев или удалять окалину после нагрева механическим способом.
Рис. 1.7. Внешний вид горячештамповочного пресса КГШП 8542
Усилие КГШП можно определить по массе поковки(табл. 1.3), а модель пресса – по табл. П 5–3. В соответствии с ГОСТ 7505-89 масса М поковки определяется из выражения
12

Мпр = кр • Мд, |
(1.2) |
где Мд – масса детали, кг; кр – расчетный коэффициент, устанавливаемый в соответствии с приложе-
нием I.
Таблица 1.3
Приблизительные данные для выбора усилия пресса Р в зависимости от массы поковки М
Номинальное уси- |
6300 |
10000 |
16000 |
20000 |
25000 |
31500 |
40000 |
лие пресса Р, кН |
|
|
|
|
|
|
|
Масса поковки М, |
до |
0,5-2 |
2-3 |
3-8 |
8-12 |
12-20 |
20-25 |
кг |
0,5 |
|
|
|
|
|
|
Кузнечный молот
Молотами называют кузнечные машины, предназначенные для обработки металлов ударами падающих частей. Энергия падающего тела тем выше, чем больше его масса и чем выше скорость. Для усиления удара падающие части молотов принудительно разгоняются действием пара, сжатого воздуха и другими энергоносителями.
Рис. 1.8. Внешний вид паровоздушного молота
Штамповочные молоты являются основным оборудованием для горячей штамповки (рис.1.8). Штамповку поковок на молотах выполняют в подкладных
и закрепленных штампах. Подкладной штамп (рис. 1.9) состоит из двух частей
–верхней 2 и нижней 6 (их обычно называют верхним и нижним штампами), которые устанавливаются на нижнем бойке7 молота. В каждой части сделаны рабочие полости – ручьи. Ручьи верхнего и нижнего штампов в совокупности
13
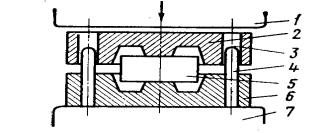
соответствуют форме и размерам готовой поковки. Штамповку ведут ударами верхнего бойка 1 по верхней половине штампа (рис. 1.9).
Рис. 1.9. Подкладной штамп:
1 – верхний боек, 2 – верхняя половина штампа; 3 – отверстие под направляющую колонку, 4 – направляющая колонка, 5 – заготовка,
6 – нижняя половина штампа, 7 – нижний боек
При определении массы падающих частей штамповочного молота ориентируются на последний удар, когда полость окончательного ручья заполнена и металл вытекает в облойную канавку. Предполагают, что работа деформации пропорциональна полной поверхности получаемой поковки. В упрощенном виде расчетная формула имеет вид:
G = α • F, |
(1.3) |
где G – масса падающих частей молота, кг;
F – площадь проекции поковки на плоскость разъёма штампа, включая площадь мостика канавки см2;
α – эмпирический коэффициент (для молота двойного действия от 5до 6 кгс/см2, для молота простого действия равен10 кгс/см2, часто усредняют и принимают равным 8 кгс/см2).
По массе падающих частей молота можно выбрать модель молота(см.
табл. 1.4; табл. П 5–4).
1.2.4. Завершающие операции
К завершающим операциям относится обрезка заусенца, образующегося у поковок при открытой штамповке, пробивка отверстий в поковках, очистка от окалины и термическая обработка. При необходимости применяется правка и калибровка.
Для обрезки и пробивки применяется кривошипный пресс(см. табл. 1.6; табл. П 5–2) или фрикционный винтовой пресс, для калибровки рычажный чеканочный или фрикционный пресс. Правку поковок осуществляют в последнем ручье штампа основного оборудования, либо используют дополнительное
14
оборудование: фрикционный молот, фрикционный винтовой или гидравлический прессы.
Таблица 1.4
Молоты штамповочные паровоздушные двойного действия для объёмной горячей штамповки
Основные параметры и |
|
|
Модель |
|
|
|
размеры |
М 210 |
М 211 |
М 212 |
М 213 |
17 КП |
|
Номинальная масса па- |
630 |
1000 |
2000 |
3150 |
5000 |
|
дающих частей, кг |
||||||
|
|
|
|
|
||
Наибольшее число |
85 |
80 |
70 |
60 |
50 |
|
ударов в минуту |
||||||
|
|
|
|
|
||
Наибольший ход бабы, |
1000 |
1200 |
1200 |
1250 |
1300 |
|
мм |
||||||
|
|
|
|
|
||
Высота зеркала нижне- |
840 |
840 |
840 |
840 |
870 |
|
го штампа над уровнем |
||||||
пола, мм |
|
|
|
|
|
|
Габариты молота в |
2000 • |
2380 • |
2960 • |
3400 • |
3700 • |
|
плане, мм |
1280 |
1390 |
1660 |
1900 |
2000 |
|
|
|
|
|
|
|
|
Масса молота без ша- |
7,36 |
10,54 |
18,3 |
25,79 |
40,71 |
|
бота, т |
||||||
|
|
|
|
|
||
Масса шабота, т |
12,6 |
20,0 |
40,0 |
63,0 |
100 |
Усилие, необходимое для обрезки облоя или прошивки отверстий, можно определить по формуле
Р > 1,7 • П • S • σср , |
(1.4) |
где П – периметр реза, мм;
S – толщина реза, мм; S = 1,5• h3 (1,5 – коэффициент, учитывающий срез по телу и недоштамповку);
h3 – высота перемычки мостика, мм;
σср – сопротивление стали при срезе; σср » 0,8• σв.кг/мм2.
Значения временного сопротивления σв зависимости от температуры для различных сталей приведены в табл. 1.5.
Выбрать вид пресса, применяемого для обрезки облоя и пробивки отверстия, можно по табл. 1.6 и табл. П 5–2.
15
Таблица 1.5
Марка |
|
σв, кгс/мм2, при разных температурах (о С) |
|
|||||
стали |
20 |
|
600 |
800 |
900 |
1000 |
1100 |
1200 |
Ст5 |
55 |
|
21 |
8 |
7 |
5 |
4 |
3 |
20 |
42 |
|
25 |
10 |
8 |
5 |
4 |
3 |
30 |
50 |
|
27 |
10 |
8 |
5 |
4 |
3 |
40 |
60 |
|
32 |
11 |
8,3 |
5,1 |
3,1 |
2,1 |
45 |
61 |
|
32 |
12 |
9 |
5 |
4 |
3 |
40Х |
100 |
|
38,1 |
14,9 |
9,3 |
5,95 |
4,37 |
2,7 |
40ХГН |
80,5 |
|
36,4 |
13,5 |
9,27 |
6,32 |
4,59 |
3,23 |
12ХН3А |
64 |
|
22 |
9 |
5 |
4 |
3 |
2 |
20ХН3А |
95 |
|
|
|
|
|
|
|
18ХГТ |
115 |
|
|
|
|
|
|
|
|
|
|
|
|
Таблица 1.6 |
|
|
|
|
|
|
|
|
Основные пара- |
|
|
Модель |
|
|
|
метры |
К2130А |
9532К |
КБ9534 |
К9536 |
К9538 |
|
Номинальное |
1000 |
1600 |
2500 |
4000 |
6300 |
|
усилие, кН |
||||||
|
|
|
|
|
||
Ход ползуна, мм |
130 |
220 |
280 |
360 |
420 |
|
Число ходов пол- |
40 |
37 |
32 |
25 |
20 |
|
зуна в минуту |
||||||
|
|
|
|
|
||
Мощность элек- |
10,5 |
10 |
28 |
40 |
55 |
|
тродвигателя, кВт |
||||||
|
|
|
|
|
||
Высота над уров- |
2725 |
3610 |
4950 |
5800 |
6100 |
|
нем пола, мм |
||||||
|
|
|
|
|
||
Масса, т |
6,93 |
10,33 |
25,74 |
32 |
493 |
|
|
|
Прессы |
обрезные |
|
|
1.2.5. Отделочные операции Отделочными операциями являются правка, калибровка и очистка поко-
вок.
Очистка поковки от окалины
Для придания поковке лучшего вида и повышения стойкости режущего инструмента, заготовки подвергают очистке от окалины, которая образуется как при термической обработке, так и нагреве на температуры горячей деформации. Существует несколько видов очистки поверхности поковки от окалины
– очистка дробью, в галтовочных барабанах и травление.
Очистка дробью осуществляется чугунными дробинками диаметром до 2 мм, летящими со скоростью до 60 м/с в специальных метательных барабанах. Бывает дробеструйная очистка, когда дробинки подаются воздушной средой.
16

Обработку поковок во вращающемся барабане с металлическими звездочками, абразивным боем и .т д. применяют для мелких заготовок простой конфигурации.
Травление осуществляют воздействием кислоты на металл. Для стальных заготовок применяют 20 %-й раствор серной кислоты при температуре от 60 до 90 оС, реже 15 %-й раствор соляной кислоты или смесь кислот.
Травление широко используется для очистки от окалины поковок из цветных сплавов.
Правка
Для устранения искривлений, возникших в результате штамповки и термообработки, применяют правку поковок, которая бывает горячей и холодной.
Наиболее целесообразно проводить правку на обрезном прессе после или вместе с обрезкой заусенца; иногда правку проводят в чистовом ручье штампа.
1.3. Разработка чертежа поковки
Чертеж поковки разрабатывается на основании чертежа готового изделия. Размеры поковки отличаются от размеров готовой детали на величину припусков на механическую обработку и величину напусков, упрощающих конфигурацию поковок.
Рис. 1.10. Эскиз поковки шестерни Для примера рассмотрим эскиз поковки шестерни, получаемой штампов-
кой на молоте в открытом штампе(рис. 1.10). Шестерня в готовом виде представляет собой цилиндрическую деталь1 (штриховка сеткой) диаметром D и высотой Н с отверстием диаметром d.
Для получения точных размеров и высокого качества состоянияпо верхности шестерня подвергается обработке на станках. Для этого предусматривается припуск 2. Для облегчения удаления поковки из штампа проек-
17
тируются штамповочные уклоны α и β, это вызывает образование напусков 3 и 4, максимальное значение которых находится на линии разъема штампа АА.
Напуск 4 внутри отверстия шестерни образуется не только штамповочным уклоном β, но и пленкой металла, предусмотренной для обеспечения лучшей стойкости штампа.
Значком на эскизе обозначены допуски, которые характеризуют точность поковки.
Изменив все размеры спроектированной поковки на величину усадки, составляющей для стали 1,5 %, получают эскиз горячей поковки, по которому изготовляют полость штампа.
Расчет поковки включает в себя назначение припусков, допусков и кузнечных напусков и производится для штампованных поковок в соответствии с ГОСТ 7505-89. Припуски и допуски назначаются исходя из параметров поковки
иисходного индекса.
1.3.1.Выбор и обозначение поверхности разъема
Вначале проектирования определяют способ штамповки, который может влиять на конфигурацию, размеры и точность поковки. Затем определяют положение поверхности разъема штампа.
Поверхностью разъёма называют поверхность соприкосновения верхней
инижней половины штампа между собой. Обычно эта поверхность бывает плоскостью или сочетанием плоскостей. Плоскость разъема должна быть выбрана так, чтобы поковка свободно вынималась из штампа. Желательно, чтобы плоскость разъёма совпадала с плоскостями детали, меющими наибольшие габаритные размеры. При этом глубина полости штампа будет наименьшей, что облегчит заполнение металлом полости штампа и хорошую выемку штампованной поковки из неглубокой полости. При несимметричной поковке глубокие полости должны быть расположены в верхней половине штампа, так как металл вверх течет лучше.
При штамповке возможен сдвиг одной половины штампа относительно другой. Чтобы такой сдвиг можно было легко контролировать по внешнему виду поковки, плоскость разъёма должна пересекать вертикальную поверхность поковки (рис. 1.10).
Плоскость разъёма изображают на чертеже поковки тонкой -штрих пунктирной линией, обозначенной на концах знаком Х – • – •·– X.
1.3.2. Параметры поковки
Масса поковки вычисляется по формуле
Мпр = М д · кр , (1.5),
где Мп.р – расчетная масса поковки, кг;
18
Мд – масса детали, кг; Кр – расчетный коэффициент, устанавливаемый в соответствии с приложением I.
Класс точности поковки (5 классов Т1...Т5) устанавливается в зависимости от технологического процесса и оборудования для ее изготовления (приложение 2).
Группа стали (3 группы М1...МЗ) устанавливается исходя из среднего массового содержания углерода и легирующих элементов (Si, Mn, Сг, Ni, Мо, W, V) (табл.1.7).
|
|
|
Таблица 1.7 |
|
|
|
|
|
|
Группа |
Массовая доля |
и/или |
Суммарная массовая доля |
|
стали |
углерода, % |
легирующих элементов, % |
||
|
||||
М1 |
до 0,35 |
и |
до 2,0 |
|
М2 |
св. 0,35 до 0,65 включ. |
или |
св. 2,0 до 5,0 включ. |
|
М3 |
св. 0,65 |
или |
св. 5,0 |
Степень сложности поковки (4 степени С1...С4) определяют путем вычисления отношения массы (объема) Мпр поковки к массе (объёму) Мф геометрической фигуры, в которую вписывается форма поковки. Геометрическая фигура может быть шаром, параллелепипедом, цилиндром или прямой правильной призмой.
Степени сложности поковок соответствуют следующие численные значения отношения Мпр / Мф:
С1 – свыше 0,63;
С2 – от 0,32 до 0,63 включительно; СЗ – от 0,16 до 0,32 включительно; С4 – меньше 0,16.
Конфигурация поверхности разъема штампа. П – плоская, Ис – сим-
метрично изогнутая, Ин – несимметрично изогнутая.
1.3.3. Определение исходного индекса
Исходный индекс определяется для последующего назначения припусков на механическую обработку и допускаемых отклонений размеров. Исходный индекс зависит от массы поковки, марки стали, степени сложности и класса точности поковки и устанавливается по табл. 1.8.
19