
Материалка
.pdf
Таблица 1.8
Определение исходного индекса
20
Для определения исходного индекса по таблице1.8 в графе «Масса поковки» находят соответствующую данной массе строку ,исмещаясь по горизонтали вправо или по утолщенным наклонным линиям вправо вниз до пересечения с вертикальными линиями, соответствующими заданным значениям группы стали М, степени сложности С, класса точности Т, устанавливают исходный индекс (от 1 до 23).
Примеры (см. табл. 1.8):
1.Поковка массой 0,5 кг, группа стали М1, степень сложности С1, класс точности Т2.
Исходный индекс – 3.
2.Поковка массой 1,5 кг, группа стали М3, степень сложности С2, класс точности Т1.
Исходный индекс – 6.
1.3.4. Припуски на механическую обработку
Величина припуска назначается дифференцированно на каждую обрабатываемую поверхность детали (на сторону).
Припуск на механическую обработку зависит от исходного индекса, линейных размеров и шероховатости поверхности детали и устанавливается по табл. 1.9.
На чертеже поковки припуск на механическую обработку изображается сплошной основной линией, при этом контур детали наносят тонкой штрихпунктирной линией с двумя точками. Проставляют размер поковки с учетом припуска. Под размером поковки в круглых скобках проставляют размер дета-
ли (рис. 3.5).
Линейные размеры поковки округляют с точностью до 0,5 мм.
В припуски входят дефектный поверхностный слой металла, вмятины от окалины, обезуглероженный слой.
1.3.5. Кузнечные напуски
Кузнечный напуск – дополнительный объем металла (слой) на обрабатываемых и необрабатываемых частях поверхности поковки, необходимый для осуществления формоизменяющих операций.
Кузнечные напуски образуются на поковке штамповочными уклонами, радиусами закругления внутренних углов, непробиваемой перемычкой в отверстиях и невыполнимыми при штамповке полостями и подвнутрениями.
Штамповочные уклоны назначают на все вертикальные поверхности поковки сверх припуска на механическую обработку (см. рис.1.10).
21

Припуски на механи
22
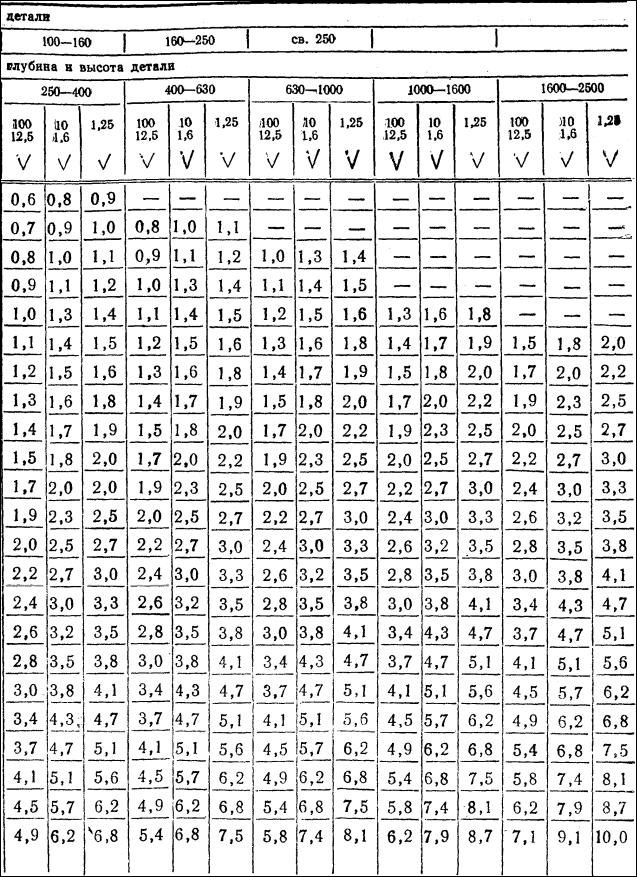
Таблица 1.9
ческую обработку (на сторону)
23
Штамповочные уклоны облегчают заполнение полости штампа металлом, выемку готовой поковки из штампа и предохраняют штамп от преждевременного износа и поломки. Уклоны утяжеляют поковку и увеличивают отходы металла при механической обработке. Поэтому их принимают минимально возможными.
Штамповочные уклоны не должны превышать величин, приведенных в табл. 1.10. Они стандартизированы и составляют: 1,3, 5,7,10 и 12°.
|
|
Таблица 1.10 |
|
|
|
|
|
|
Штамповочные уклоны, град |
||
|
|
|
|
Оборудование |
на наружной |
на внутренней по- |
|
|
поверхности |
верхности |
|
|
|
|
|
Штамповочные молоты, прессы без |
7 |
10 |
|
выталкивателей |
|||
|
|
||
Прессы с выталкивателями, горизонталь- |
5 |
7 |
|
но-ковочные машины |
|||
|
|
||
Горячештамповочные автоматы |
1 |
2 |
|
|
|
|
Величина штамповочного уклона зависит от глубины и формы полости штампа, смазки штампов и применяемого оборудования.
Для наружных поверхностей поковки штамповочные уклоны принимаются на 1 – 3о меньшими, чем для внутренних. Это объясняется температурной усадкой: при остывании металла наружная поверхность поковки отходит от поверхности ручья штампа, а внутренняя – прижимается к поверхности выступа штампа, и снять поковку с этого выступа становится затруднительным при малом внутреннем уклоне.
Радиусы закругления. Все пересекающиеся поверхности поковки сопрягаются по радиусам. Радиусы закруглений подразделяют на наружные и внутренние (см. рис. 1.10). Наружные радиусы закруглений r устанавливаются в зависимости от массы поковки и глубины полости ручья штампа по табл. 1.11. Внутренние радиусы закруглений R приблизительно в 3 раза больше соответствующих наружных радиусов, числовые данные округляются до0,5 мм (табл. 1.11).
Наметка отверстия. При штамповке в штампах с одной плоскостью разъема нельзя получить сквозное отверстие в поковке, поэтому наносят только наметку отверстия с перемычкой-пленкой(рис. 1.10), удаляемой впоследствии
в специальных штампах. Толщина перемычки S по отношению к диаметру отверстия D составляет S/D = 0,1, но не менее 4 мм.
Сквозные отверстия диаметром меньше 30 мм в поковках не выполняют.
24
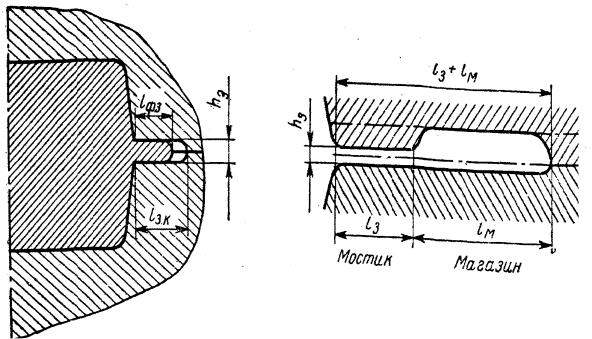
Углубления в поковке выполняются диаметром не менее30 мм и глубиной до 0,8 от внутреннего диаметра поковки
|
|
|
|
Таблица 1.11 |
|
|
|
|
|
|
Минимальная величина радиусов закруглений, мм, |
|||
Масса поковки, кг |
при глубине полости ручья штампа, мм |
|||
|
до 10 включ. |
10-25 |
25-50 |
св. 50 |
до 1,0 включ. |
1.0 |
1,6 |
2,0 |
3,0 |
св 1.0 >> 6,3 |
1,6 |
2,0 |
2,5 |
3,6 |
>> 6,3 >> 16,0>> |
2,0 |
2,5 |
3,0 |
4,0 |
>> 16,0 >> 40,0>> |
2,5 |
3,0 |
4,0 |
5,0 |
>> 40,0>>100,0>> |
3,0 |
4,0 |
5,0 |
7,0 |
>>100,0>>250,0>> |
4,0 |
5,0 |
6,0 |
8,0 |
Высота (толщина) заусенца. При штамповке в открытых штампах вдоль внешнего контура полости окончательного(чистового) ручья выполняют специальную заусенечную (облойную) канавку, предназначенную для расположения в ней заусенца (рис.1.11).
а |
б |
Рис. 1.11. Заусенечные канавки:
а – канавка без магазина; б – канавка с магазином; lф.з. – фактическая ширина заусенца; lз.к. – ширина заусенечной канавки
Заусенец имеет технологическое назначение. Он создает сопротивление истечению металла из полости по всему периметру поковки, вследствие чего заполняется полость штампа.
25
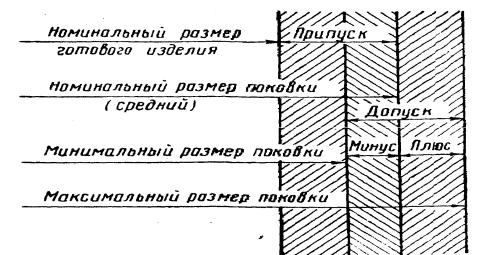
Высота (толщина) заусенца на поковке по контуру обрезки облоя зависит от массы поковки и не должна превышать:
2 |
мм – для поковок массой до 1,0 кг включ.; |
|||
3 |
мм – >> |
>> |
>> |
св. 1,0 кг до 5,6 кг включ.; |
5 |
мм – >> |
>> |
>> |
>> 5,6 кг >> 50,0 кг >>; |
6 |
мм – >> |
>> |
>> |
>> 50,0 кг, |
апри пробивке отверстия эта величина может быть увеличена в 1,3 раза.
1.3.6.Допуски
Допуски на поковку необходимы в связи с возможными отклонениями от номинальных размеров поковки вследствие недоштамповки по высоте, сдвига штампов, их износа и т.п.
Допуски назначаются на все номинальные размеры поковки.
Рис. 1.12. Схема размеров поковки с припуском и допуском
Номинальный линейный размер поковки– геометрический параметр, из-
меряемый в единицах длины и определяемый исходя из номинального линейного размера детали с прибавлением установленного припуска и кузнечного напуска (рис. 1.12).
Предельные размеры поковки – два предельно допускаемых размера(минимальный и максимальный), между которыми должен находиться или быть одним из них номинальный размер.
Допуск (поле допуска) размера поковки – абсолютная величина разности между наибольшим и наименьшим предельными размерами.
Допуски и допускаемые отклонения линейных размеров поковок зависят от исходного индекса и размера поковки, назначаются по таблице 1.12 и про-
ставляются на чертеже поковки, например, 132 + 1,7 .
- 0,7
26
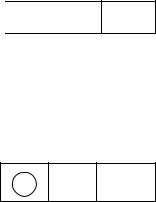
На чертеже поковки указывают также допускаемые отклонения формы и расположения поверхностей, которые устанавливают по приложениям 3 и 4.
Наиболее часто встречаются на чертежах поковок указания на допускаемые отклонения:
–от плоскостности, например
0,5 А
–допуск плоскостности поверхности относительно базовой поверхности
Асоставляет 0,5 мм;
–от концентричности пробитого отверстия относительно внешнего контура поковки, например,
0,8 А
– допуск соосности 0,8 мм.
27

Таблица 1.12
Допуски и допускаемые отклонения линейных размеров поковок, мм
28
2. Расчет размеров исходной заготовки и заготовки после осадки
2.1. Определение объёма исходной заготовки
Размеры заготовки для получения поковки должны учесть объём металла, идущего на поковку, облой, перемычку, потери на угар. Объём заготовки равен;
V |
=V |
+ V |
+ V |
+ V |
угар |
= (V |
+ V |
+ V |
) × |
δ % + 100 % |
, |
(2.1) |
|
||||||||||||
з |
пок |
обл |
пер |
|
пок |
обл |
пер |
100 % |
|
|
||
|
|
|
|
|
|
|
|
|
|
|
|
где Vз – объём исходной заготовки, см 3; Vпок , Vобл ,Vпер. – объёмы поковки, облоя, перемычки, соответственно, см 3; δ – потери металла на угар, %.
Объём поковки:
М
V |
= |
пр |
, |
(2.2) |
|
||||
пок |
|
ρ |
|
где М пр – расчетная масса поковки (см. формулу 1.5), кг; ρ – плотность стали
(7,8 г/см 3 для черных металлов).
Потери на угар рассчитывают в зависимости от условий нагрева заготовок. При нагреве в электрических и пламенных печах2–3 %; при скоростном нагреве в пламенных печах1–1,5 %; при безокислительном нагреве в пламенных печах 0,25–0,3 %; при электронагреве (индукционном, контактном)
0,2–0,5 %: |
|
|
|
|
δ % |
|
|
|
V = (V |
+ V |
+ V ) × |
. |
(2.3) |
||||
|
||||||||
угар |
пок |
обл |
пер |
100 % |
|
|
||
|
|
|
|
|
Объём облоя (избытка металла) равен:
= к × П × S3 , (2.4)
где к = 0,7 – коэффициент заполнения металлом (облоем) заусеничной канавки; П – периметр поковки в плоскости разъема штампа, см:
П = π × Dп , |
(2.5) |
где Dп , – наружный диаметр поковки, см; S3 – площадь поперечного сечения облоя, равная площади поперечного сечения заусеничной канавки штампаSк, см 2 (см. табл. 2.1).
Заусеничные канавки штампов КГШП (рис. 2.1) стандартизованы. Номер канавки с готовыми размерами выбирают после определения высоты мостика заусеница h3 по зависимости (табл. 2.1):
а) для поковки круглой в плане
h |
= 0,0133 × d п , |
(2.6) |
3 |
2 |
|
где d2п наружный диаметр поковки в плоскости разъема штампа, мм; |
|
|
б) для поковки квадратной в плане |
|
|
|
h3 = 0,0133× Ап , |
(2.7) |
29