
MROAP_1to38_by_UPAD
.pdf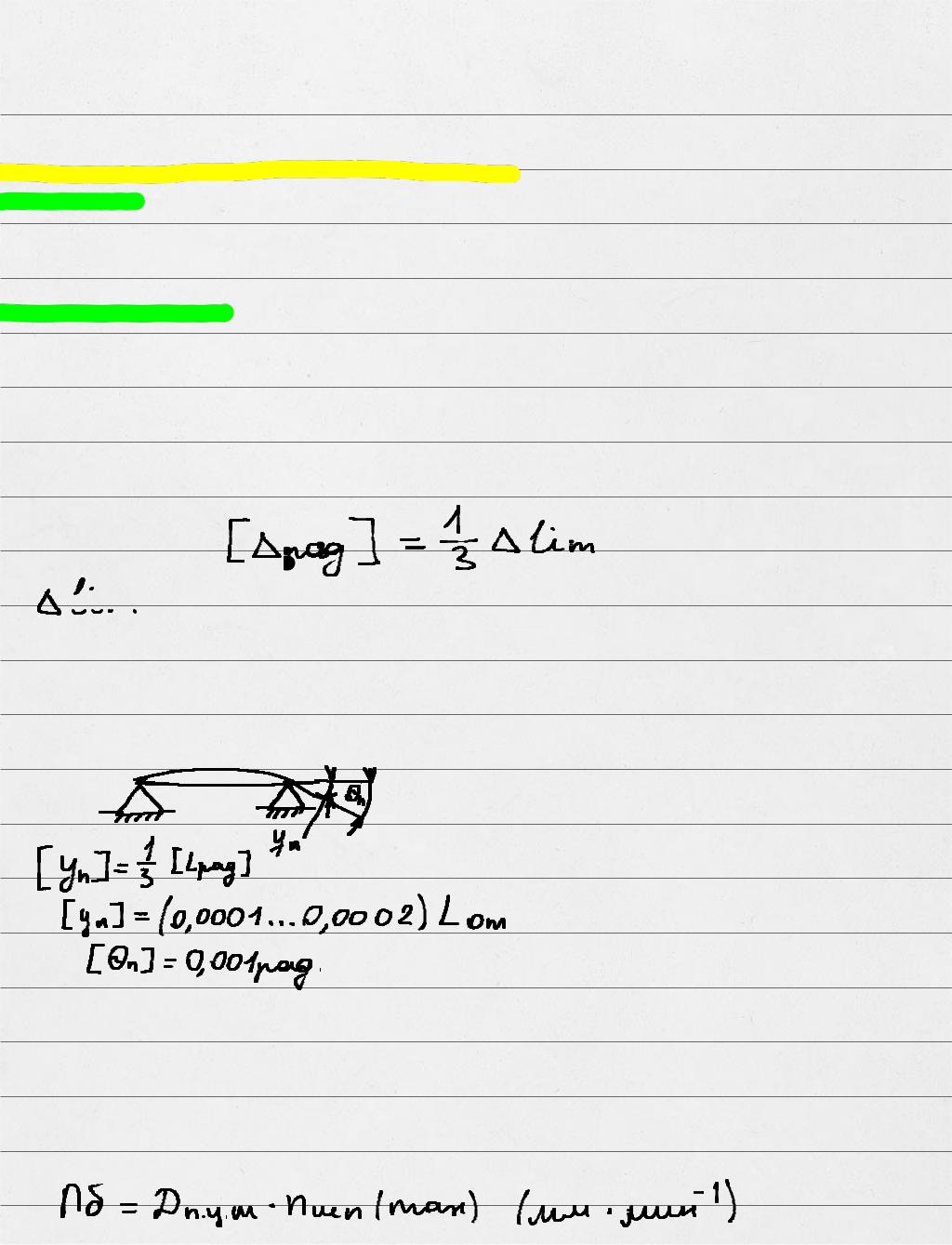
Аналогично изображается и червячная передача. Также ломаной линией возможно изображение постоянных передач, расположенных после множительной части в случае большого их количества.
Шпиндельные узлы станочного оборудования.
Шпинделем называется главный, последний от источника движения вал привода главного движения, служащий для базирования, крепления и передачи крутящего момента режущему инструменту или заготовке. Вместе с опорой и приводными элементами он образует один из важнейших узлов станка - шпиндельный узел.
Шпиндельный узел в значительной степени определяет точность и шероховатость обработки, по-этому к нему предъявляются особые требования.
1. Точность вращения, определяемая величиной радиального и торцевого биения шпинделя. Для серийно выпускаемых станков допустимая величина биения определяется соответствующими стандартами и нормалями станкостроения, для специальных станков определяется из соотношения:
Допуск на лимитирующий размер детали, тоесть на тот размер, который должен быть получен на данном станке с максимальной точностью.
2. Жесткость. Определяется вличиной прогиба и угла поворота переднего конца
шпинделя, как наиболее существенно влияющего на точность и шероховатость обработки.
3.Надежность. Под надежностью, применительно к шпиндельным узлам, понимают сохранение во времени первоначальной точности вращения шпинделя.
4.Быстроходность. Определяет технологические возможности высокоскоростной обработки и производительность. За параметр быстроходности принимают произведение диаметра передней центрирующей шейки шпинделя на его максимальную частоту вращения.

5.Виброустойчивость. Это способность шпиндельного узла препятствовать возникновению вибраций или ограничивать их величину.
6.Теплостойкость. Это способность шпиндельного узла препятствовать возникновению тепловых деформаций или ограничивать их величину.
7.Нагрузочная способность. Определяет максимальный крутящий момент и мощность на шпинделе. За параметр принимают отношение максимально допустимой мощности на шпинделе к диаметру передней центрирующей шейке
шпинделя.
8.Быстрое точное и надежное крепление РИ или заготовки.
9.Технологичность изготовления, сборки и эксплуатации.
Для упрощения процесса конструирования и облегчения его автоматизации шпиндельные узлы подразделяются на следующие подузлы:
1)межопорный участок
2)привод вращения
3)передний конец шпинделя
4)шпиндельная опора
Межопорный участок.
Обычно имеет ступенчатую форму. Основные требования:
-минимальное количество ступеней и концентраторов напряжения в виде кольцевых канавок, шпоночных пазов, шлицев, отверстий.
Привод вращения.
В абсолютном большинстве случаев вращение шпинделю передается через зубчатую или ременную передачу.
Зубчатая передача. Окружная скорость может достигать до 25-30 м/с. Преимущества:
-значительный передаваемый крутящий момент -компактность Недостатки:
-возможность передач вибраций шпинделю -относительная сложность изготовления -низкая ремонтопригодность.
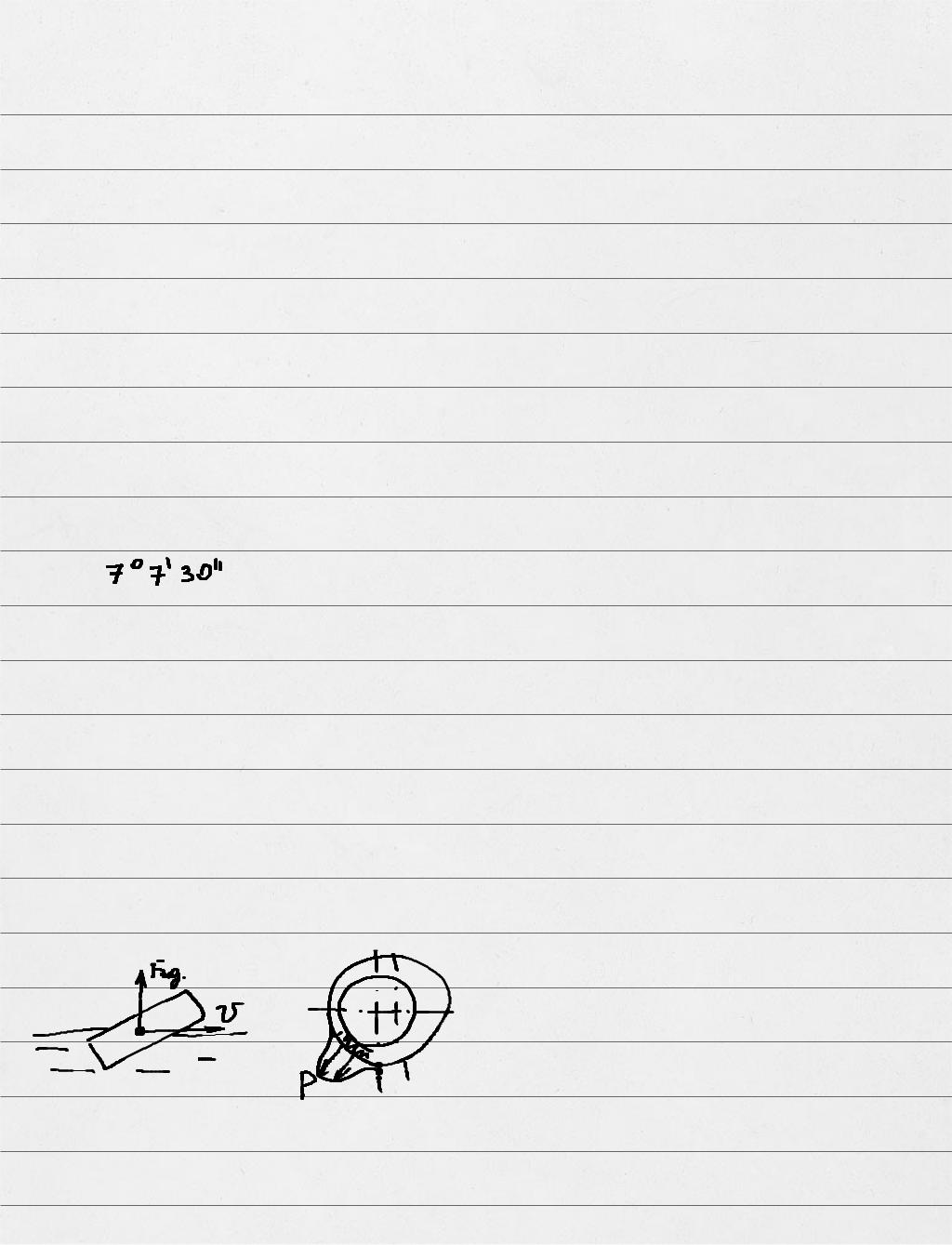
Ременная передача.
Разновидности: плоскоременная, клиноременная, поликлиновая, зубчатым ремнем, сегментные передачи.
Окружная скорость до 40 м/с. Преимущества:
-отсутствие передачи шпинделю вибраций, -относительная бесшумность работы -высокое качество обрабатываемых поверхностей Недостатки:
-проскальзывание некоторых типов ремней -изнашиваемость -значительные габариты.
Передние концы шпинделей. Служат для базирования, крепления и передачи крутящего момента режущему инструменту или заготовке.
Базирование приспособлений осуществляется с помощью цилиндрических или конических поверхностей.
Конические поверхности имеют конус: 7:24, 1:3, конус Морзе, метрический конус
80...120,
Рассмотрим наиболее распространенные конструкции передних концов шпинделей 1) в токарном станке. И
Опоры скольжения шпинделей. Применяются когда опоры качения не обеспечивают требуемую точность и долговечность. К ним относятся: -гидродинамические -гидростатические -аэростатические -электромагнитные опоры.
Гидродинамические опоры. Действие основано на возникновении гидродинамической силы Fгд, действующей на тело, частичо погруженного в жидкость и движущегося с определенной скоростью.
В опорах вал, действуя как насос затягивает жидкость в зазор между шпинделем и опорой. В результате образуется масляный клин с повышенным давлением масла, что компенсирует внешнюю нагрузку.
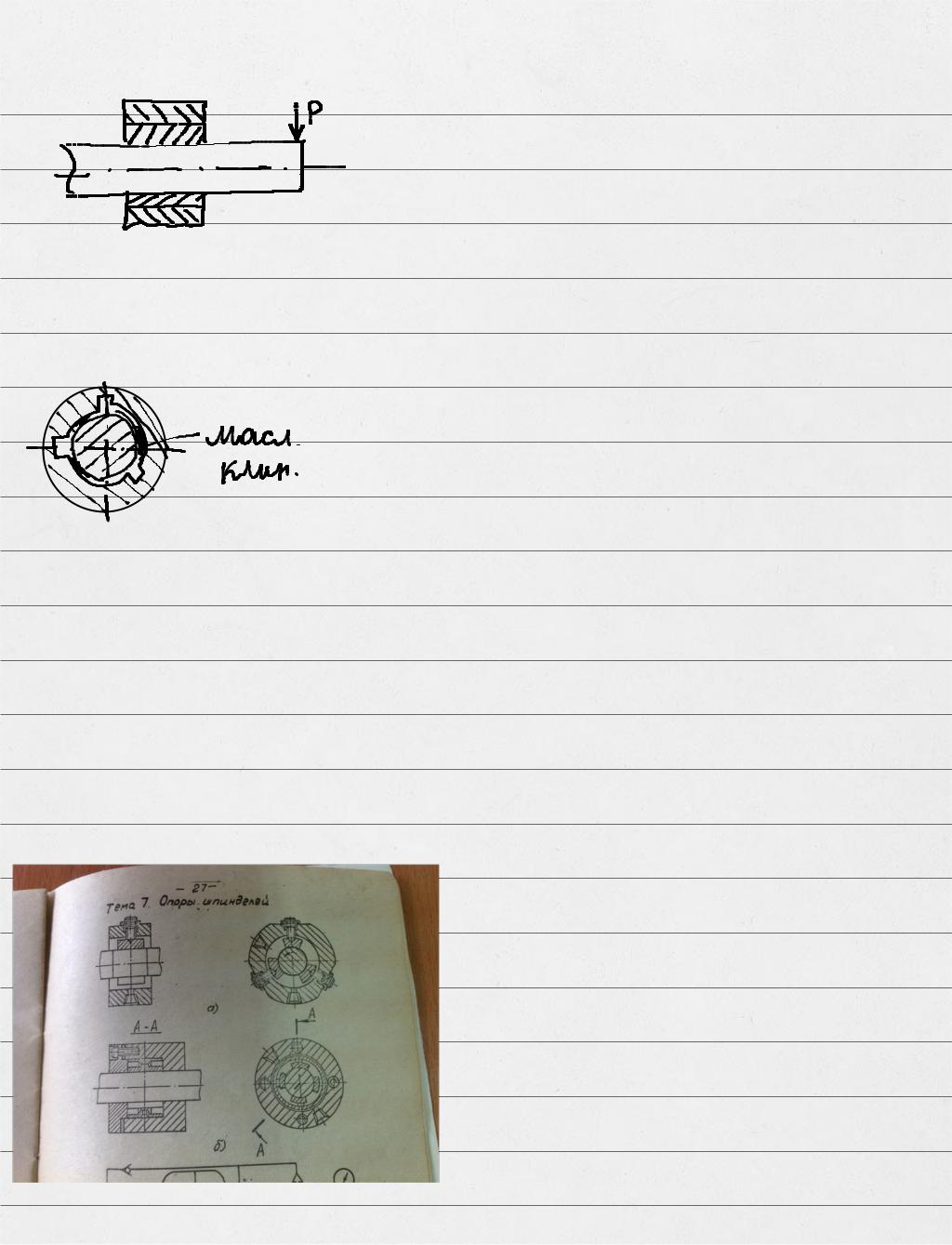
Разновидности:
1) выполненая в виде обычной цилиндрической втулки.
Образуется только один масляный клин, по этому такая опора имеет невысокую нагрузочную способность.
2) для повышения нагрузочной способности используют конструкции, обеспечивающие образование нескольких, обычно 3х, масляных клиньев. Для этого, например выполняют отверстие в подшипнике фасонном
Общие недостатки данных конструкций:
1)сложность или невозможность регулирования зазоров.
2)склонность к кромочным давлениям
3)сложность изготовления.
3) многовкладышные подшипники конструкции Энимс. Имеют 3, реже 4 вкладыша, устанавливаемые обычно на сферических опорах. Это позволяет вкладышам самоустанавливаться в окружном и осевом направлениях. В результате исключаются кромочные давления а форма клина приближается к оптимальной. Кроме того появляется возможность регулирования радиального зазора.

Критерий расчета гидродинамических опор.
1.На нагрузочную способность
2.На жесткость слоя смазки.
Общие недостатки гидродинамических опор:
1)изменение положения оси шпинделя при изменении частоты вращения и внешней нагрузки.
2)ограниченна жесткость, ограничивающая предельно допустимую нагрузку.
3)необходимость периодической подкачки масла в опору.
4)изнашиваемость в режимах пуска, останова, реверса.
В качестве материала опор используются бобиты, оловянистые и свинцовые
бронзы, антифрикционный чугун, цинковые сплавы.
Гидростатические опоры. Масло постоянно, под достаточно высоким давлением подается в зазор между подшипником и шпинделем, это обеспечивает
преимущества:
1)обеспечение постоянного жидкостного трения при пуске, останове, реверсе и низких частотах вращения.
2)практически неограниченный срок службы.
3)высокая нагрузочная способность.
4)высокая точность вращения и демфирующая способность.
Недостатки:
1)большой расход масла
2)необходимость иметь специальную систему для подачи масла под давлением.
3)высокое тепловыделение при больших частотах вращения и нагрузках.
Могут быть радиальными и упорными.
В радиальных опорах равномерно по окружности выполнены полости - карманы.
Карманов обычно 4. В каждый карман, независимо под давлением подается масло. Отвод масла, обычно минерального осуществляется через торцы
подшипника или через специальные какнавки, выполненые на перемычках между карманами.
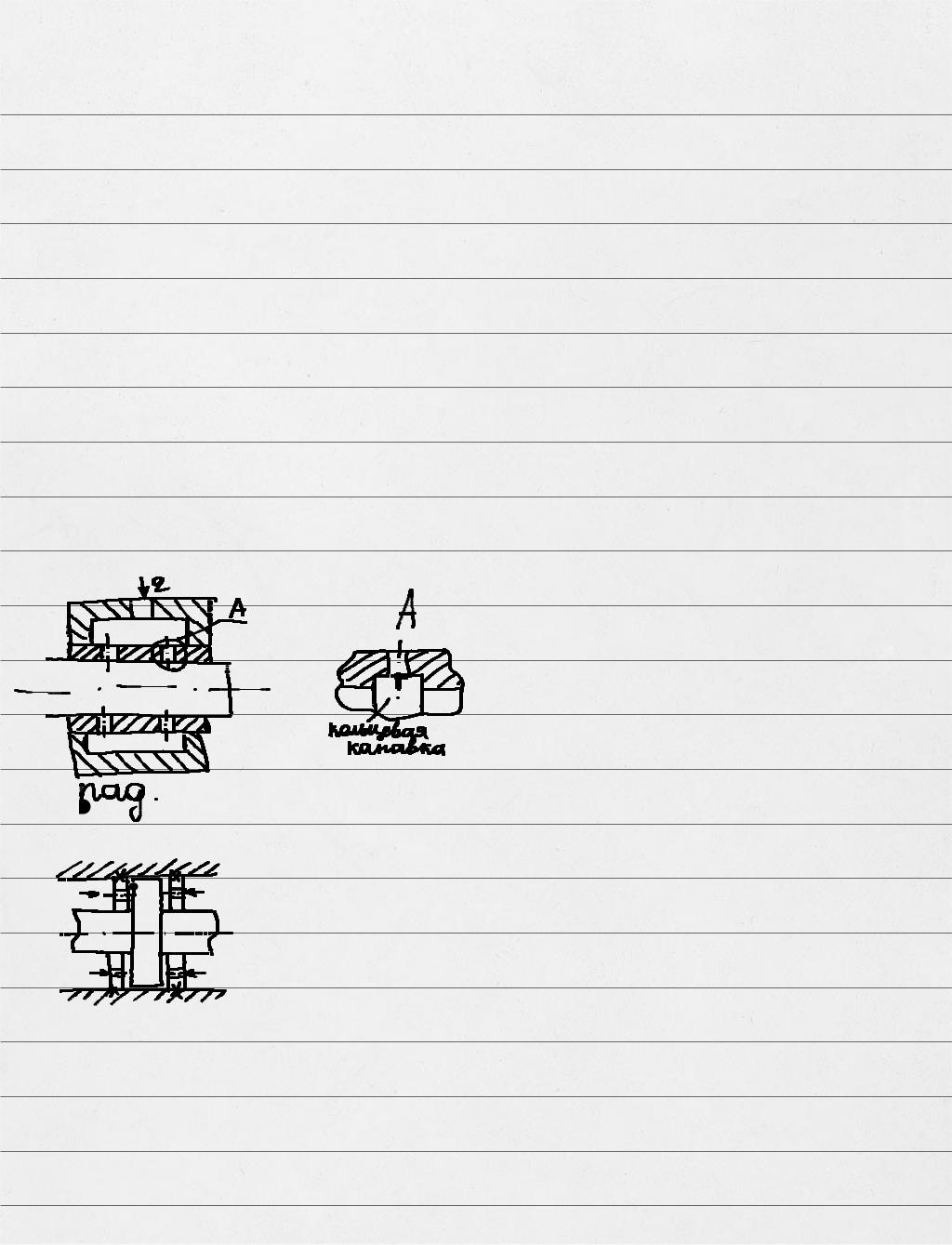
Критерий расчета:
1.На нагрузочную способность
2.На жесткость слоя смазки.
3.На расход масла.
4.По потерям на трение и прокачку масла.
Основное применение гидростатических опор - тяжелые станки, обеспечивающие достаточно высокую точность обработки.
Аэростатические опоры или опоры с воздушной смазкой.
В этом случае шпиндель и опора разделяются слоем воздуха, что обеспечивает следующие преимущества:
1)малое тепловыделение ввиду малой вязкости воздуха.
2)низкие потери на трение.
3)высокая долговечность при соблюдении соответствующих требований эксплуатации.
4)экологическая чистота.
Недостаток
-низкая нагрузочная способность Область применения: небольшие прецезионные станки с частотами вращения до
300-500 тыс об/мин. Могут быть как радиальными так и упорными.
Электромагнитные опоры шпинделей. Работа основана на работе сил
отталкивания. Также могут быть радиальными и упорными.
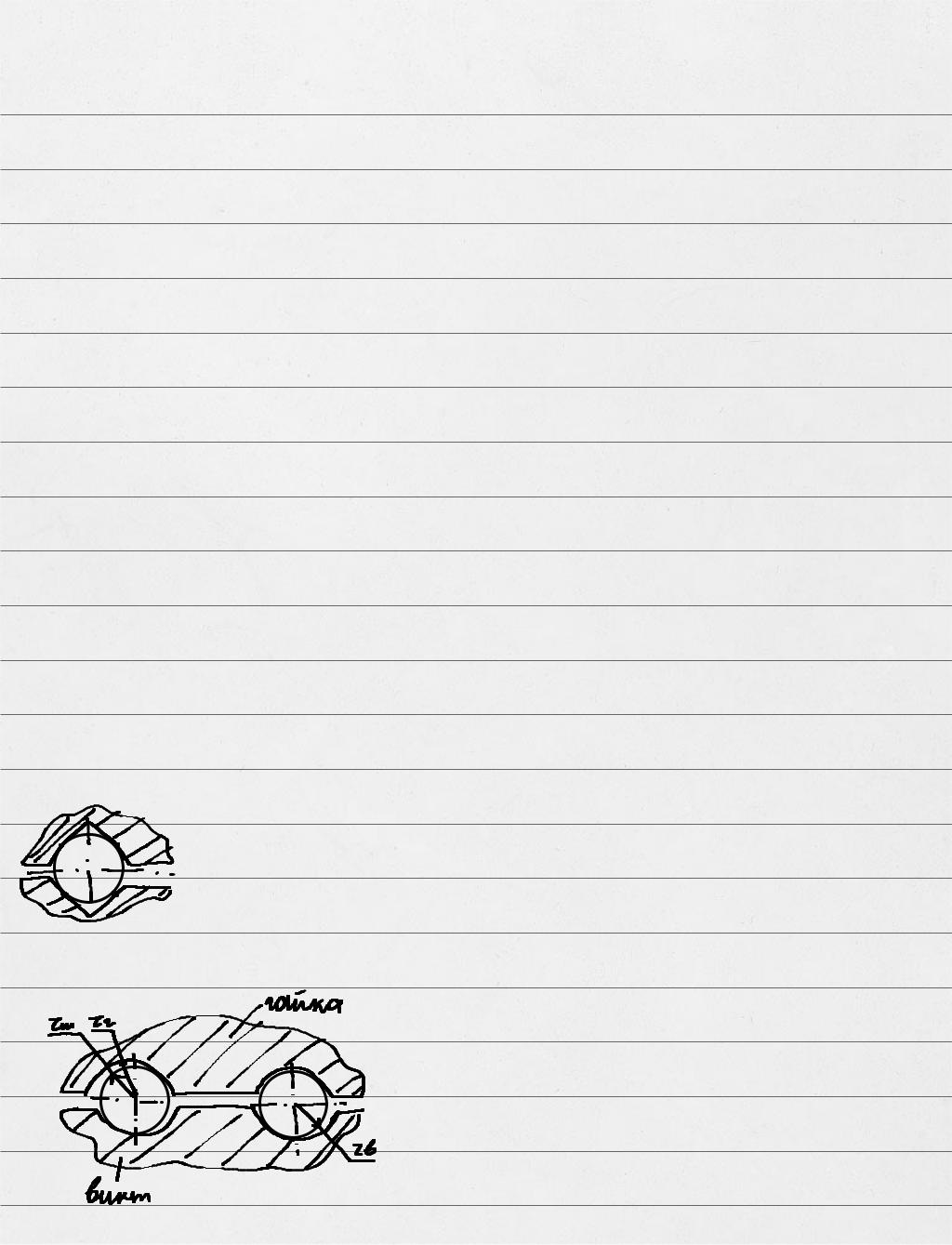
Передача винт-гайка качения применяется в точных станках. Широко применяется в станках с ЧПУ.
Преимущества: 1)Высокий КПД
2)относительно небольшой крутящий момент на ходовом винте в связи с высоким КПД при той же тяговой силе.
3)высокая осевая жесткость в связи с возможностью полного выбора зазора между телами качения и рабочими поверхностями винта и гайки.
4)примерное равенство коэфициентов трения покоя и движения и незначительная зависимость коэффициента трения от скорости. Недостатки:
1)сложность конструкции
2)относительно низкая нагрузочная способность ввиду высоких контактных напряжений
3)трудоемкость изготовления, высокая стоимость
4) отсутствие самоторможения
Передача состоит из винта, гайки, комплекта шариков и устройства для возврата шариков. В наиболее распространенных конструкциях шарики возвращаются по
каналу, выполенному во вкладыше. Канал замыкает конец витка с его началом. В результате образуется контур, по которому циркулируют шарики. Обычно
выполняется 2-3 независимых замкнутых контура. Для создания предварительного натяга гайка выполняется из 2х частей и одна часть смещается
относительно другой различными способами. Размерный ряд передачи в соответствии с нормалью станкостроения
1)Т ходового винта 2.5
2)номинальный диаметр винта 16-100 мм.
3)профиль прямоугольный, тропециидальный, стрельчатый
Обеспечивает четырехточечный контакт, что позволяет воспринимать осевую нагрузку в 2-х направлениях при одной гайке.
Недостаток: значительная сложность изготовления.
Наиболее технологичным, а по этому распространенным является полукруглый
профиль.
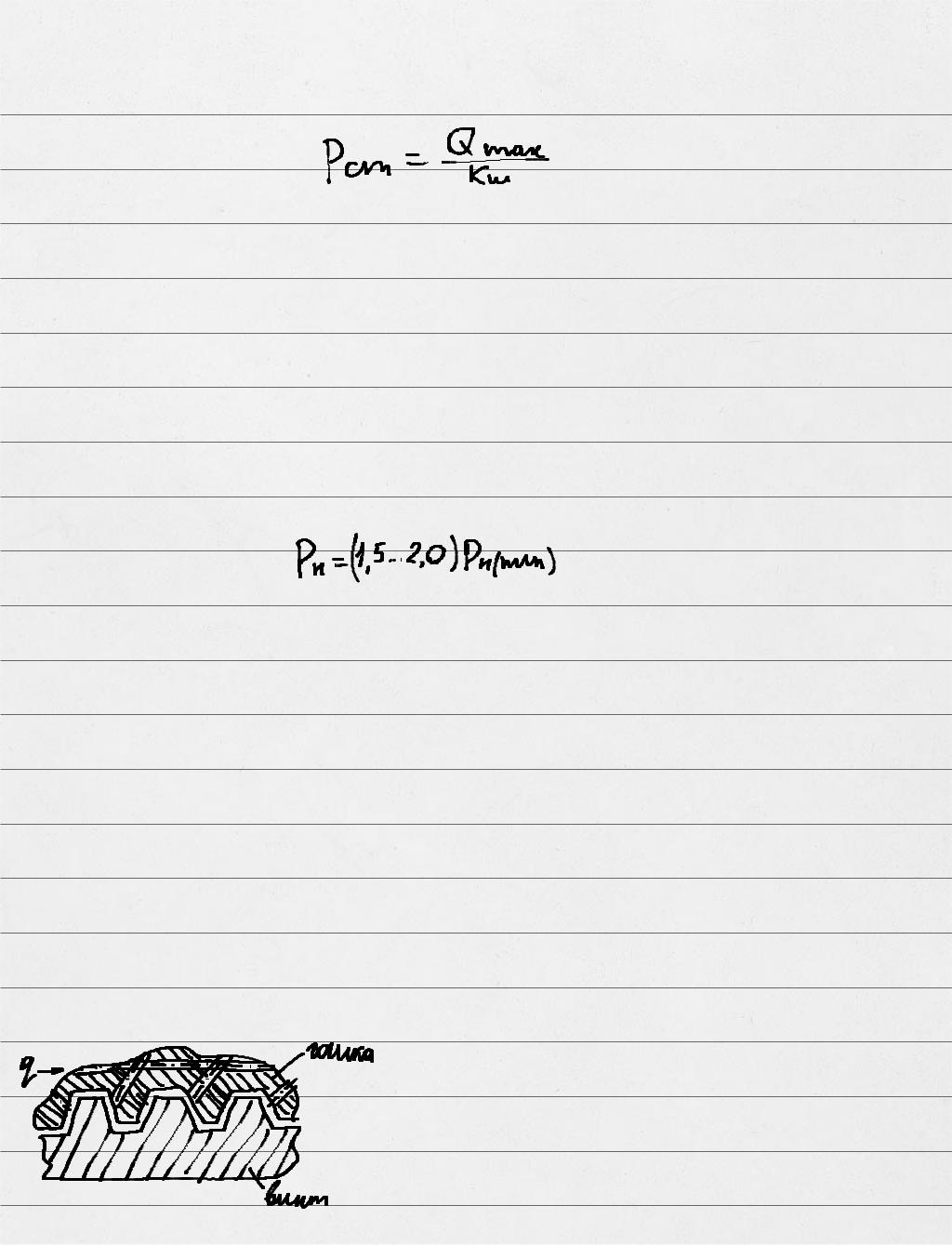
Критерий расчета передачи винт-гайка качения.
1. На статическую нагрузку, приходящуюся на 1 шарик. Определяется по максимальной тяговой силе и количеству шариков, одновременно работающих в
одном направлении.
Полученые значения сравниваются с допусимым.
2.На жесткость. Аналогично передаче винт-гайка скольжения.
3.На устойчивость. Аналогично.
4.На статическую грузоподъемность, под которой понимается пределно допустимая осевая нагрузка на винт в результате действия которой общая деформация тел качения гайки и винта составляет 10^-5 диаметра шарика.
5.На динамическую грузоподъемность, под которой понимается постоянная осевая нагрузка, которую должна выдержать передача в течение 10^6 оборотов.
6.На усилие предворительного натяга. Минимальная величина натяга должна обеспечивать сохранение натяга при действии максимальной тяговой силы. Максимальная величина натяга должна обеспечивать статическую прочность передачи. Обычно принимается
Гидростатическая передача винт-гайка.
Масло постоянно под давлением подается в зазоры между витками винта и гайки. Это обеспечивает следующие преимущества:
1)высокий КПД (0,98...0,99)
2)значительное уменьшение крутящего момента на ходовом винте всвязи с высоким КПД.
3)высокая точность и плавность перемещений
4)низкий коэфициент трения и практически независимость коэффициента трения от скорости Недостатки:
1)сложная система подачи масла с обязательной его тонкой очисткой
2)существенное повышение температуры масла при значительных частотах и больших нагрузках, что может вызвать деформацию ходового винта.
Данная передача применяется в основном в тяжелых станках.

Основные способы установки ходовых винтов на опорах. 1.
Применяется для коотких ходовых винтов при относительно небольших частотах вращения и нагрузках.
2.
Применяется для более длинных ходовых винтов при возможно больших
частотах вращения и нагрузках. Недостаток:
-при движении гайки вправо винт испытывает осевой изгиб
3.
При движении гайки в обоих направлениях винт работает на растяжение.
Реечные преобразующие механизмы. 1. Передача зк-рейка
1)Простота конструкции
2)высокий КПД
3)возможность использования в различных сочетаниях перемещения ЗК или рейки Недостатки:
1)низкая степень редукции
2)отсутствие самоторможения, что не позволяет использовать данную передачу для вертикальных перемещений Расчет обычный, по максимальному тяговому усилию.
2. Передача червякзубчатая рейка

Данную передачу можно сравнить с передачей винт-гайка. Червяк - это укороченный ходовой винт, червячная рейка - длинная гайка.
Обеспечивается более полный поверхностный контакт, а значит значительно большеи тяговые усилия.
Г) гидростатическая передача червяк-червячная рейка
Кулачковые тяговые устройства Широко используются в станках автоматах и полуавтоматах
Обеспечивают точность перемещений до 0,01 мм, величина хода ограниченна до
200-300 мм.
Передача движения от кулочка к рабочему органу осуществляется через систему рычагов с последним звеном зубчатый сектор - рейка.
1- рабочий орган 2- зубчатая рейка 3- зубчатый сектор 4- система рычагов 5- закаленный ролик 6- кулачок
7- пружина, работающая на растяжение Рабочая подача П3 осуществляется с помощью кулачка через систему рычагов и
передачу зубчатый сектор - рейка. Пружина при этом растягивается возвращение рабочего органа в исходное положение осуществляется при спаде рабочего профиля кулочка с помощью пружины.