
БТ / ZAPOLNITELI BETONA
.pdf
током воздуха материал расслаивается, тяжелые зерна оказываются внизу более легкие вверху, откуда и отбираются. Одновременно материал очищается от пыли. Также предусматривается способ сепарации пористых заполнителей в пневмосуспензии.
1 - решето; 2 - фильтр; 3 - подача воздуха; 4 - песок; 5 – загрузка заполнителя; 6 - выдача легкого продукта; 7 - выдача сравнительно тяжелого продукта.
Рисунок 5 - Схема сепаратора для обогащения пористых заполнителей
Установка (рисунок 5) работает следующим образом. Воздух через фильтр непрерывно нагнетается в слой песка, отчего последний «кипит». Подбором песка соответствующей плотности и крупности получают требуемую плотность пневмосуспензии, в которой часть зерен крупного пористого заполнителя тонет, другая часть всплывает. Разделенный на два класса, крупный пористый заполнитель отбирается вместе с песком, от которого затем отделяется грохочением. Песок возвращается в установку.
Менее надежен, но проще способ разделения в воздушном потоке (рисунок 6). Если ссыпать материал поперек воздушного потока, создаваемого вентилятором, то поток в большей степени отклонит сравнительно мелкие или более легкие зерна. При предварительном фракционировании заполнителя по крупности таким образом можно произвести классификацию по плотности зерен.
29
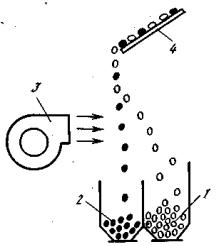
1 - легкий продукт; 2 - сравнительно тяжелый продукт; 3 - вентилятор; 4 - питатель
Рисунок 6 – Разделение пористого заполнителя в воздушном потоке Перечисленные способы сухой классификации можно применять при раз-
делении пористого заполнителя на два класса для повышения его однородности или для выделения из заполнителя тяжелых включений. В пемзе, например, часто содержится примесь тяжелых зерен вулканического стекла (обсидиана), при удалении которых повышаются качество заполнителя и эффективность его использования. Зерна пористых заполнителей при дроблении нередко получаются слишком остроугольными, далекими от подобия шару или кубу. Из-за этого пустотность щебня доходит до 60%, что вызывает повышенный расход цемента. Удобоукладываемость бетонных смесей при прочих равных условиях ухудшается. Для получения окатанного щебня А. А. Аракеляном разработан способ его обработки во вращающемся барабане с последующим отсевом мелочи. Форма зерен пористого щебня может быть улучшена также при использовании для дробления исходной породы специальных барабанных дробилок.
30
4 ИСКУССТВЕННЫЕПОРИСТЫЕЗАПОЛНИТЕЛИ
Применение легких пористых заполнителей позволяет получать эффективные легкие бетоны для теплоизоляции, стеновых панелей, монолитных стен и разнообразных несущих конструкций. Замена обычных тяжелых заполнителей пористыми позволяет улучшить теплоизоляционные свойства бетонов. В то же время достаточная прочность ряда пористых заполнителей обеспечивает возможность получения на их основе конструкционных легких бетонов высокой прочности.
Применение пористых заполнителей — отходов промышленности также носит локальный характер: вблизи предприятий, выдающих такие отходы.
Главный источник обеспечения потребности строительства и строительной индустрии пористыми заполнителями для легких бетонов — специально созданная промышленность искусственных пористых заполнителей.
Предприятия по производству искусственных пористых заполнителей создаются там, где в них есть потребность, и базируются они, как правило, на местных источниках сырья. Себестоимость искусственных пористых заполнителей выше себестоимости промышленных отходов или природных пористых заполнителей (если последние имеются в данном районе), но часто ниже себестоимости привозных заполнителей. Кроме того, искусственные пористые заполнители отличаются более высоким качеством и эффективностью использования в бетонах [4,5].
Из искусственных пористых заполнителей наиболее распространен в настоящее время (примерно 3/4 общего выпуска) керамзит.
4.1 Керамзит
Некоторые глины при обжиге вспучиваются. Это явление использовано для получения из глин пористого материала— керамзита.
Керамзит получают главным образом в виде керамзитового гравия. Зерна его имеют округлую форму. Структура пористая, ячеистая. На по-
31
верхности его часто имеется более плотная корочка. Цвет керамзитового гравия обычно темно-бурый, в изломе — почти черный.
Вспучивание глины при обжиге связано с двумя процессами: с газовыделением и переходом глины в пиропластическое состояние.
Источниками газовыделения являются реакции восстановления оксидов железа при их взаимодействии с органическими примесями, окисления этих примесей, дегидратации гидрослюд и других водосодержащих глинистых минералов, диссоциации карбонатов и т. д. В пиропластическое состояние глины переходят, когда при высокой температуре в них образуется жидкая фаза (расплав), в результате чего глина размягчается, приобретает способность к пластической деформации, в то же время становится газонепроницаемой и вспучивается выделяющимися газами.
Сырьевые материалы для производства керамзита. Сырьем для производства керамзита служат глинистые породы, относящиеся в основном к осадочным горным. Некоторые камнеподобные глинистые породы — глинистые сланцы, аргиллиты — относятся к метаморфическим.
Глинистые породы отличаются сложностью минералогического состава
икроме глинистых минералов (каолинита, монтмориллонита, гидрослюды и др.) содержат кварц, полевые шпаты, карбонаты, железистые, органические примеси.
Глинистые минералы слагают глинистое вещество — наиболее дисперсную часть глинистых пород (частицы мельче 0,005 мм). Собственно глинами называют глинистые породы, содержащие более 30% глинистого вещества
[4].
Для производства керамзита наиболее пригодны монтморилло-нитовые
игидрослюдистые глины, содержащие не более 30% кварца. Общее со-
держание SiO2 должно быть не более 70%, Al2O3 — не менее 12% (желательно около 20%), Fe2O3 + FeO - до 10%, органических примесей – 1…2%.
Добавки в глину при производстве керамзита. В производстве керамзи-
та добавки используют для повышения прочности керамзита и вспучиваемости глины и для расширения ее температурного интервала вспучивания.
По физическому состоянию добавки подразделяют на твердые и жидкие.
Вкачестве жидких добавок применяют соляровое масло, мазут, петролатум, антрацен, пиролизную смолу, сланцевое масло, сульфидно-спиртовую барду (с.с.б.), неорганических твердых — пирит и пиритные огарки, а органических
— молотый уголь, древесные опилки, гумбрин и др.
Последние вводят обычно при содержании в глине природных органических примесей менее 1,2%. Суммарное содержание органических примесей и добавок не должно превышать 2%.
Древесные опилки и торф должны иметь не менее 95% подрешетного продукта при просеве через сетку № 3,3, а уголь через сетку № 1. Содержание серы в пиритных огарках не должно превышать 5%.
Добавки целесообразно вводить в виде эмульсий и комплексных органических или органо-минеральных смесей, состоящих из смеси порошковых материалов с органическими жидкостями [5].
32
Органические материалы с широким температурным интервалом выгорания (мазут, комплексные добавки) применяют при содержании природных органических примесей в глине менее 0,5%, а при более высоком их содержании используют добавки с узким температурным интервалом выгорания (соляровое масло, керосин).
Железистые добавки вводят из расчета, чтобы суммарное их содержание с природными примесями составляло в пересчете на Fе2О3 - 7…8% от массы сухой шихты. Лучше всего их вводить в виде комплексных добавок — смесей порошковых материалов с водными эмульсиями и эмульсиями мазута, солярового масла или пиролизной смолы. В качестве стабилизаторов эмульсии используют глину и техническое мыло.
Применение добавок, особенно комплексных, дает возможность увеличить коэффициент вспучивания глины в 2…3 раза, соответственно уменьшить насыпную плотность керамзита, существенно снизить его себестоимость и увеличить производительность печей.
Применение. Наиболее широкое применение керамзитобетон находит в качестве стенового материала. Особенно эффективно применение для стеновых панелей хорошо вспученного легкого керамзитового гравия М300, 400, до 500 (по насыпной плотности).
Плотность конструкционно-теплоизоляционного керамзитобетона для однослойных стеновых панелей, как правило, составляет 900...1100 кг/м3, предел прочности при сжатии — 5...7,5 МПа. Такой бетон в конструкции выполняет одновременно несущую и теплоизоляционную функции. В двухили трехслойных стеновых панелях требуемую несущую способность может обеспечить слой (или два слоя) конструкционного керамзитобетона, а теплозащитную — слой крупнопористого теплоизоляционного керамзитобетона плотностью 500...600 кг/м3.
Теплоизоляционный крупнопористый керамзитобетон — самый легкий бетон, который можно получить на данном заполнителе. Его плотность при минимальном расходе цемента лишь немного больше насыпной плотности керамзитового гравия.
На керамзите М700, 800 получают конструкционные легкие бетоны с пределом прочности при сжатии 20, 30, 40 МПа, используемые для производства панелей перекрытий и покрытий, в мостостроении, где особенно важно снизить массу конструкций.
4.1.1 Основы теории вспучивания глины
Как уже отмечалось, керамзит получают вспучиванием глин при их обжиге. Для уяснения основных закономерностей процесса вспучивания глиняной гранулы рассмотрим его в самом схематическом приближении. Представим себе, что нагревается полый глиняный шарик (рисунок 7), который можно уподобить элементарной поре глиняной гранулы. Во время нагрева при достижении определенной температуры (индивидуальной для каждой глины) глиняная оболочка рассматриваемого шарика начнет размягчаться, спекаться и в конечном счете уплотнится и станет газонепроницаемой, находясь в пиропластическом состоя-
33

нии, т.е. будучи способной к пластическим деформациям без разрыва сплошно-
сти [6].
1
1 - невспученной; 2 – вспученной Рисунок 7 - Схема вспучивания элементарной ячейки глиняной гранулы.
Если в этот момент внутри шарика по каким-либо причинам начнут выделяться газы, то, не имея выхода через оболочку, они будут создавать во внутренней полости шарика избыточное давление, под воздействием которого оболочка, будучи размягченной, начнет расширяться. Это и будет представлять собой вспучивание элементарной ячейки глины. Таким образом, процесс вспучивания состоит из двух стадий: первая — спекание с образованием закрытой поры и вторая — собственно вспучивание под давлением газов, выделяющихся внутри закрытой поры. Сумма таких элементарных актов в каждой ячейке глиняной гранулы и обусловит общий процесс вспучивания всей гранулы. При этом, рассматривая процесс вспучивания всей гранулы, необходимо иметь в виду, что по своей толще она нагревается неравномерно: с поверхности нагревается быстрее, чем в центре. Поэтому поверхность гранулы еще до того, как вся ее масса приобретает пиропластическое состояние, покрывается плотной спекшейся газонепроницаемой оболочкой, предотвращающей утечку газов из гранулы даже в том случае, если под давлением газов отдельные перегородки пор окажутся прорванными.
Факторы, обусловливающие газовыделение в глинах. В глинах при их нагревании выделяется довольно значительное количество газообразных продуктов, причем экспериментально установлено, что вспучиваемость глин зависит от величины удельного газовыделения, которое у хорошо вспучивающихся глин превышает 100 мг/г. В настоящее время можно считать установленным, что источниками газовыделения в глинах являются реакции разложения и восстановления окислов железа при их взаимодействии с органическими примесями или добавками в глине, а также химически связанная вода глинистых минералов. Схема восстановительных реакций может быть представлена следующими уравнениями:
6Fe2O3 4Fe3O4 O2; |
2Fe3O4 6FeO O2; |
(17) |
Fe2O3 C 2FeO CO; |
Fe2O3 CO 2FeO CO2. |
Влияние этих реакций на вспучивание подкрепляется тем, что глины, которые в природном состоянии содержат значительное количество железистых и органических примесей, хорошо вспучиваются. Добавка в глину железистых
34
примесей (например, пиритных огарков), а также органических веществ (уголь, соляровое масло, мазут) увеличивает способность глины вспучиваться.
Так как температуру реакции обычно отождествляют с температурой газовой среды печи, при которой эта реакция наступает, то воздействие температурного перепада фиксируется обычно как сдвиг реакции в область более высоких температур. Экспериментально подтвержден сдвиг восстановительных реакций в область более высоких температур при возрастании интенсивности нагрева гранул, а также участие гидратной воды глинистых минералов в качестве источника газовыделения в глине при ее вспучивании.
Факторы, обусловливающие возникновение пиропластического со-
стояния. В глине оно наступает в результате накопления в ней достаточного количества жидкой фазы силикатного расплава. Интенсивность накопления жидкой фазы зависит, прежде всего, от химического состава глины. Она возрастает с увеличением содержания щелочей в глине и резко убывает по мере возрастания в ней количества свободного кварца.
Сильное влияние на процесс накопления жидкой фазы оказывает химический характер газовой среды. Восстановительная среда резко интенсифицирует процесс накопления жидкой фазы. Это связано главным образом с переводом Fе2О3 в FeO согласно приведенным ранее уравнениям химических реакций. Важно иметь в виду, что процесс восстановления окисного железа в закисное сопровождается повышением молекулярной концентрации реагирующих окислов, так как из одной молекулы Fе2О3 образуется 2FеО.
Атомы железа могут находиться в его гидроокиси, присутствующей в глинистой породе в качестве примеси, а могут входить в состав кристаллической решетки глинообразующих минералов, участвуя в образовании их замещенного комплекса. Влияние каждого из этих видов железа на вспучивание глины неодинаково. Наиболее благоприятное влияние оказывают так называемые «свободные» железистые окислы, входящие в состав гидроокисей.
Влияние химического характера газовой среды на вспучиваемость глин.
Восстановительная среда повышает вспучиваемость глин и понижает температуру их вспучивания. Однако это не обусловливает необходимость вести процесс обжига с недостатком воздуха для горения топлива. Важно, чтобы СО и Н2 содержались не в печных газах, а в газовых пузырьках, заполняющих поры гранул, что достигается наличием восстановительных реакций в обжигаемых гранулах.
4.1.2 Специфические свойства керамзитовых глин
Коэффициентом вспучивания называют отношение объема вспученной к объему сухой глиняной гранулы до ее вспучивания. Его можно подсчитать по формуле:
K |
всп |
|
0г (1 0.01Пп) |
, |
(18) |
|
|||||
|
|
к |
|
||
|
|
|
0 |
|
|
где ρг0—ρk0 - плотность соответственно сухой и вспученной гранулы; Пп — потери при прокаливании в %.
При Квсп>7…8 глины считают высоковспучивающимися, при Квсп=4…5 - средневспучивающимися и при Квсп = 2…2,5 — низковспучивающимися.
35

Вспучиваемость глин оценивают также по плотности вспученной гранулы, которую можно получить из данной глины. По этому признаку различают четыре группы глинистого сырья, представленные в таблице 10:
Таблица 10 – Группы глинистого сырья
Группа глинистого сырья по |
Плотность пористого черепка в |
куске в кг/м3, которую способно давать |
|
степени вспучиваемости |
при обжиге глинистое сырье |
|
|
|
|
Высоковспучивающееся |
Не более400 |
Средневспучивающееся |
400…750 |
Слабовспучивающееся |
750…1500 |
Невспучивающееся |
1500 и более |
На величину коэффициента вспучивания влияет гранулометрический состав глин. Отмечается достаточно устойчивая статистическая зависимость между содержанием в глине фракции размером зерен менее 10 мк (А<10мк) и ее коэффициентом вспучивания, выражаемая уравнением:
Квсп=0,66е0,02А<10мк |
, |
(19) |
|
Квсп - возрастает с увеличением содержания в породе глинистой фракции и резко понижается с увеличением содержания пылевидной и песчанистой фракций.
4.1.3 Способы производства керамзитового гравия
Технологический процесс производства керамзитового гравия складывается из следующих операций: карьерные работы — обработка глины — формование гранул — их сушка—обжиг — охлаждение и сортировка керамзита.
Карьерные работы в производстве керамзита не имеют какой-либо специфики. Можно лишь отметить, что для производства керамзита вопросы усреднения состава глины путем ее промежуточной экскавации имеют еще большее значение, чем в производстве стеновой керамики. Практика некоторых заводов показывает, что переход от непосредственной подачи в производство карьерной глины на работу с промежуточным ее вылеживанием в открытых штабелях позволяет снизить насыпную плотность керамзита на 100…150 кг/м3.В зависимости от методов обработки глины и приготовления гранул различают три способа производства керамзита: сухой, пластический и шликерный. Решающее значение на выбор способа производства оказывают свойства сырья.
Способ сухого изготовления гранул. При этом способе глиняные грану-
лы не формуются, а образуются дроблением и рассевом карьерной глины. Его можно и целесообразно применять при работе с камнеподобными хрупкими глинистыми породами (глинистые сланцы, аргиллиты), трудно размокающими в воде. При дроблении такие глины должны давать объемную крошку с относительно небольшим выходом мелочи — до 15%. Если глины обладают ярко выраженной спайностью и при дроблении дают большое количество «лещади» — тонких пластинок, то для производства керамзита они не пригодны, так как лещадь практически не вспучивается. Кроме того, при этом способе подготовки
36
гранул порода не должна содержать включений известняка, ибо при этом способе удалить их из глины невозможно [1,4].
Для такого способа подготовки гранул типична схема, приведенная на рисунке 8.
Гранулы подсушивают при карьерной влажности глины более 8%, в связи с чем сушильный барабан размещают с возможностью его обхода, что на схеме показано пунктирными линиями. При грохочении дробленой глины необходим ее рассев по фракциям с тем, чтобы в последующем каждую фракцию обжигать в отдельной печи, ибо режим обжига должен быть дифференцированным в зависимости от крупности фракции. Фракцию с размером зерен более 20 мм возвращают на додрабливание, а фракция менее 5 мм может быть использована для обжига на песок. Совместный обжиг мелкой фракции с крупной может привести к свариванию обжигаемых гранул в конгломерат.
Способ пластического формования гранул. При этом способе их фор-
муют из пластичной глиняной массы (рисунок 9). Его целесообразно применять для глин с рыхлой и плотной структурой, намокающих в воде, когда их карьерная влажность равна или ниже нормальной формовочной влажности. Содержание каменистых включений в глине не должно превышать 10%, а включения известняка должны иметь размер не более 1 мм.
37

Крытый склад
Автосамосвал
Приёмный бункер
Питатель
Валково-зубчатая дробилка
Сушильный барабан
Фракция > 20 мм Грохот
Фракция <5 мм
|
|
|
для обжига на песок |
|
|
|
Валково-зубчатая дробилка |
||
|
|
|
|
|
Крупная фракция |
|
Мелкая фракция |
||
|
||||
|
|
|
|
|
|
|
Сортировочный грохот |
|
|
|
|
|
|
|
|
|
|
|
|
|
|
Бункер |
|
|
|
|
Бункер |
|
|
|
|
|
|
|
|
|
|
|
|
|
|
|
|
|
|
|
|
|
|
|
|
|
|
|
Тарельчатый питатель |
|
|
|
|
Тарельчатый питатель |
|||
|
|
|
|
|
|
|
|
|
|
|
|
|
|
|
|
|
|
|
|
|
|
|
|
Вращающаяся печь |
|
|
|
|
|
Вращающаяся печь |
|
|
|
|
|
|
|
|
|
|
|
|
|
Рисунок 8 – Технологическая схема сухого способ подготовки гранул
Предпочтительно иметь крытый механизированный глинозапасник, который обеспечивает стабильную влажность глины, поступающей в производство, исключает перебои в работе оборудования из-за транспортных трудностей и погодных условий и дает возможность эксплуатировать карьер в одну смену при трехсменной работе остального оборудования. При его отсутствии открытый склад глины все же обеспечивает лучшие условия эксплуатации оборудования, чем при работе с непосредственной подачей в производство карьерной глины [7].
38