
БТ / ZAPOLNITELI BETONA
.pdf
1 — машина для вдувания порошковых добавок; 2 — шлаковозный ковш; 3 — опрокидной бассейн; 4 — приямок;
5 — промежуточный склад;
6 — мостовой кран с грейферным захватом;
7 — приемное устройство дробильно-сортировочного отделения; 8 — первая ступень дробления; 9 — вторая ступень дробления; 10 — грохот; 11 — сепаратор для разделения щебня на две марки Рисунок 20 - Технологическая схема производства шлаковой пемзы в опрокидном бассейне
Брызгально-траншейный способ наиболее прост. Шлаковый расплав при сливе в траншею орошается водой из перфорированных труб, вспучивается и застывает в ней, а после охлаждения разрабатывается экскаватором и подается на дробление и рассев. Этот способ не является перспективным для производства шлаковой пемзы из-за ее невысокого качества и неоднородности по структуре.
Вододутьевой способ состоит в разбивке массы расплава на отдельные гранулы сильной струей водовоздушной смеси с последующим интенсивным смешением еще жидких гранул расплава с водовоздушной смесью и. вспучиванием. Поризация расплава производится в струйных аппаратах (рисунок 21). Гранулы, вспученные в камере смешения, выбрасываются на экран, с которого они попадают на приемные устройства и агрегируются в глыбы. Полученная шлаковая пемза имеет однородную мелкопористую структуру с размером пор до 1 мм [1,4].
59

1 — стенка приемной камеры; 2 — направляющий лоток; 3 — водяная рубашка; 4—камера смешения;
5 — рабочее сегментное сопло Рисунок 21 - Схема струйного вододутьевого аппарата
Гидроэкранный способ предусматривает последовательную обработку шлака на двух гидрожелобах (рисунок 22). С первого желоба вспучивающийся шлаковый расплав струями воды бросается на вертикальный экран, отразившись от которого попадает на второй желоб, где снова подхватывается струями воды и направляется на пластинчатый перегружатель для последующего охлаждения и дробления. Технологическая схема производства представлена на рисунке 23.
Все описанные выше способы позволяют получать дробленую шлаковую пемзу в виде пористого щебня и песка.
Шлакопемзовый щебень, как и аглопоритовый, имеет зерна остроугольной формы с открытыми порами, отличается большой межзерновой пустотностью.
1 — приемная воронка; 2 — гидромониторная насадка; 3 — экран; 4 — желоб; 5 — пластинчатый перегружатель
Рисунок 22 - Схема установки для гидроэкранного способа получения шлаковой пемзы
60
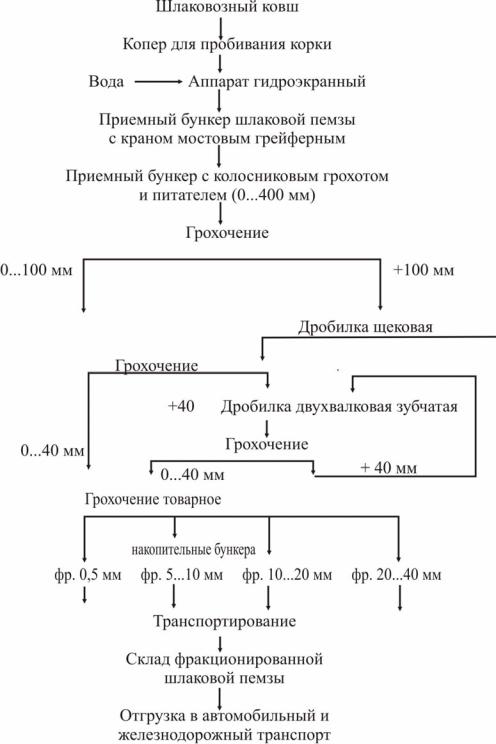
Рисунок 23 - Технологическая схема производства шлаковой пемзы гидроэкранным способом
Шлакопемзовый гравий получают на установке (рисунок 21), в которой применен усовершенствованный струйный вододутьевой аппарат (водовоздушный гранулятор). Диспергированные и вспученные частицы шлакового расплава соединяются на встречном экране в .крупные куски. Полученную массу, еще не потерявшую пластические свойства, обрабатывают в барабанном холодильнике. Во вращающемся барабане с продольными лопастями про-
61
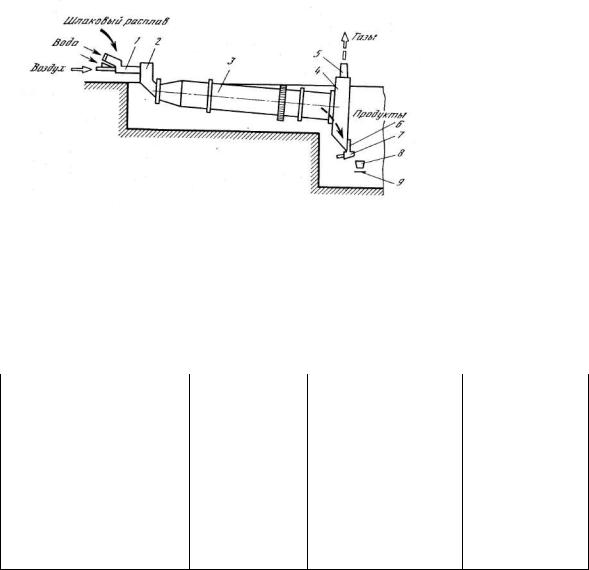
исходит дополнительное вспучивание, разделение крупных кусков на отдельные зерна и их окатывание.
Пустотность фракционированного щебня не должна быть боле 52%, среднее значение коэффициента формы зерен не должно превышать 2,5.
Стандарт предусматривает испытание шлакопемзового щебня и стой-
кость против силикатного распада.
Требования к прочности шлакопемзового щебня при сдавливании в цилиндре (таблица 14) близки к соответствующим требованиям для аглопоритового щебня (таблица 12).
1 — водовоздушный гранулятор; 2 — приемная камера; 3 — барабанный холодильник; 4 — разгрузочная камера;
5— паровоздухопровод; 6 — затвор «мигалка»; 7 — вибропитатель; 8
—короб; 9—конвейер ленточный
Рисунок 24 - Схема установки для производства гравиеподобной шлаковой пемзы
Таблица 14 - Требования к прочности шлакопемзового щебня
|
Прочность при |
|
Прочность при |
|
Марка по насыпной плот- |
сдавливании в Марка по насыпной |
сдавливании в |
||
ности |
цилиндре, МПа, |
плотности |
цилиндре, МПа, |
|
|
не менее |
|
не менее |
|
400 |
0,30 |
700 |
0,70 |
|
450 |
0,35 |
|||
750 |
0,90 |
|||
500 |
0,40 |
|||
800 |
1,10 |
|||
550 |
0,45 |
|||
850 |
1,30 |
|||
600 |
0,55 |
|||
900 |
1,50 |
|||
650 |
0,65 |
|||
|
|
Зерна шлаковой пемзы имеют явно выраженную ячеистую структуру. Средний диаметр пор-ячеек — 1...2 мм. Иногда получают шлаковую пемзу с диаметром пор 5... 6 мм. Такая пемза напоминает затвердевшую пену. В качестве заполнителя для бетона лучше использовать мелкопористую шлаковую пемзу. Шлаковая пемза получается весьма неоднородной по степени вспучивания. Поэтому после дробления и сортировки по крупности целесообразна сепарация по плотности зерен, что может значительно повысить эффективность ее применения.
62

Применение. Шлаковую пемзу используют главным образом в конструк- ционно-теплоизоляционных бетонах ограждающих конструкций. В силу меньшей ее теплопроводности возможно применение шлакопемзобетона повышенной плотности без ухудшения его теплозащитных свойств по сравнению, например, с керамзитобетоном: шлакопемзобетон с плотностью 1400 кг/м3 имеет
примерно такую же теплопроводность, как керамзитобетон с плотностью 1200 кг/м3.
Шлаковая пемза М 750...900 может использоваться при получении высокопрочных бетонов для различных несущих конструкций. Однако необходимо иметь в виду возможность коррозии стальной арматуры в шлакопемзобетоне изза содержания в шлаке серы. При производстве предварительно напряженных конструкций, особенно с проволочной арматурой, стойкость арматуры в шлакопемзобетоне должна быть установлена специальным исследованием.
4.4 Обжиговый зольный гравий
Сырьем для производства обжигового зольного гравия служат золы теплоэлектростанций, в том числе и из отвалов после их гидроудаления.
Технология предусматривает сушку и помол золы, затем ее окатывание в шаровидные гранулы диаметром около 15 мм. Для облегчения грануляции и обеспечения достаточной прочности гранул золу смачивают водным раствором ЛСТ (лигносульфонатов технических) или же добавляют глину. Далее гранулы подсушивают и обжигают в коротких вращающихся печах прямоточного действия, причем их подают сразу в высокотемпературную (около 1200°С) зону печи. Для повышения пористости гравия в золу можно добавлять древесные опилки.
1 — ящичный подаватель с глинорыхлителем; 2 — сушильный барабан контактного нагрева; 3 — дымосос; 4 — шаровая мельница;
5 — тарельчатый гранулятор; 6 — сушильный барабан; 7 — узел приготовления жидкой добавки;
8 — прямоточная вращающаяся печь; 9 — холодильник; 10 — гравиесортировка; 11 — бункера готовой продукции
Рисунок 25 - Технологическая схема изготовления зольного гравия
63
Насыпная плотность зольного гравия — 300... 800 кг/м3. Насыпная плотность гравия фракций 5... 10 и 10...20 мм близка. Предел прочности при сдавливании в цилиндре приблизительно соответствует требованиям к керамзитовому гравию той же насыпной плотности[1,4].
Основное назначение — конструкционно-теплоизоляционные бетоны. Заполнитель на основе золы теплоэлектростанций в смеси с глинами
получают также и в противоточных вращающихся печах по технологии, принятой в производстве керамзита. Его называют глинозольным керамзитом.
4.5 Безобжиговый зольный гравий
Основами получения безобжигового зольного гравия (БЗГ) являются: 1) грануляция увлажненной смеси золы и вяжущего; 2) гидратационное твердение вяжущего и его взаимодействие с активными составляющими золы.
Для изготовления БЗГ можно применять портландцемент, известь, гипсовые, гипсоцементно-пуццолановые вяжущие (ГЦПВ) и использовать золы ТЭС сухого отбора (из-под фильтров и циклонов), а также высушенные золы из отвалов их гидроудаления (золошлаковые смеси).
Содержание частиц несгоревшего топлива в золах и золошлаковых смесях допускается до 25%, что существенно выше, чем для производства обжиговых заполнителей. Таким образом, возможность использования зол расширяется.
Удельная поверхность зол должна быть не менее 2500 см2/г. Это обусловлено тем, что гранулируемость порошков зависит от их гранулометрического состава, в частности от содержания мелких частиц с размерами до 20 мкм: дисперсность частиц золы имеет значение и для гидратационного твердения гранул [1,9].
Разработаны различные варианты технологии получения БЗГ, один из которых показан на рисунке 30. На основе молотой золы или золошлаковой смеси с добавкой 10...15% портландцемента получают гранулы, которые подвергают кратковременному пропариванию в камере (4 ч при температуре
90...95°С).
Насыпная плотность такого гравия 700...950 кг/м3. Прочность при сдав-
ливании в цилиндре 0,6...0,8 МПа обеспечивает возможность транспортирования и складирования.
Прочность продолжает расти при естественном твердении (до 5...6 МПа в 28-суточном возрасте), а также в составе бетона при тепловой обработке изделий. Повышения прочности гранул и сокращения сроков их тепловой обработки можно достигнуть применением добавок-ускорителей твердения типа сернокислого натрия, нитрит-нитратхлорида кальция и других солей неорганических кислот, вводимых с водой затворения в количестве 1...3% от массы вяжущего.
64

При использовании вместо портландцемента быстротвердеющего ГЦПВ заполнитель сразу после грануляции приобретает достаточную прочность и не нуждается в тепловой обработке. Через сутки прочность при сдавливании в цилиндре составляет 0,7...1,5 МПа, через трое суток - 2,3...3,0 МПа.
Насыпная плотность гравия может быть снижена введением в состав сырьевой смеси различных облегчающих добавок: вспученного перлитового песка, древесных опилок, стеклопора, отходов пеностекла или газосиликата и др.
1 — бункер цемента; 2 — бункер золы; 3 — дозатор весовой; 4 — мельница шаровая; 5 — система пневмотранспорта; 6 — циклоны; 7
— бункер золоцементной смеси; 8 — питатель ленточный; 9 — конвейер винтовой; 10 — бак воды с дозатором; 11 — емкость для жидких добавок с дозатором; 12 — смесители двухвальный; 13 — гранулятор тарельчатый;
14 — конвейер ленточный; 15 — камера пропарочная; 16 — бункер приемный; 17 — элеватор; 18 — грохот; 19 — силосы
Рисунок 26 - Технологическая схема изготовления безобжигового зольного гравия (БЗГ)
Добавки вводят в смеситель при подготовке массы к грануляции. Расход цемента составляет 60...100 кг/м3. Облегченный безобжиговый гравий (ОБЗГ) имеет насыпную плотность 400...600 кг/м3, а прочность при сдавливании в цилиндре в сухом состоянии — 1,0...1,6 МПа.
Производство безобжигового зольного гравия характеризуется экономией топливно-энергетических ресурсов. Например, расход условного топлива в 2...3 раза ниже, чем при производстве обжиговых искусственных пористых заполнителей.
Применяется БЗГ как крупный заполнитель для конструкционных и конструкционно-теплоизоляционных легких бетонов.
65
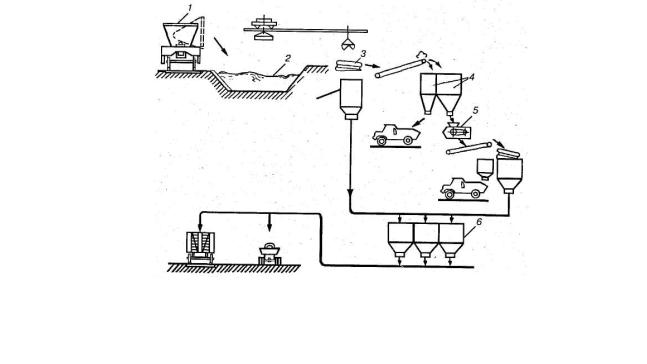
4.6 Заполнители из металлургических шлаков
Металлургические шлаки являются значительным резервом обеспечения строительной индустрии заполнителями для бетонов. Шлаковые заполнители по величине насыпной плотности могут быть тяжелыми (ρ0 > 1000 кг/м3) и легкими (ρ0 ≤1000 кг/м3), апокрупностизерен — мелкими (< 5 мм) и крупными (> 5 мм).
Шлаковый щебень. Шлаковый щебень получают дроблением отвальных металлургических шлаков или специальной обработкой огненно-жидких шлаковых расплавов (литой шлаковый щебень). Для производства щебня в основном применяют отвальные шлаки, сталеплавильные (приемлемые для переработки в щебень), а также медеплавильные, никелевые и другие шлаки цветной металлургии.
К эффективным видам тяжелых заполнителей бетона, не уступающих по физико-механическим свойствам продуктам дробления плотных природных каменных материалов, относится литой шлаковый щебень. При производстве этого материала огненно-жидкий шлак из шлаковозных ковшей сливается слоями толщиной 250…500 мм на специальные литейные площадки или в трапециевидные ямы-траншеи (рисунок 27). При выдерживании в течение 2…3 ч на открытом воздухе температура расплава в слое снижается до 800 °С и шлак кристаллизуется. Затем его охлаждают водой, что приводит к развитию многочисленных трещин. Шлаковые массивы на линейных площадках или в траншеях разрабатываются экскаваторами с последующим дроблением и грохочением.
Физико-механическиесвойствалитогошлаковогощебня:
Средняяплотностькусков, кг/м3........................................................2200…2800 Истиннаяплотность, кг/м3…………………………………….2900…3000
Пределпрочностинасжатие, МПа……………………………….60…100
Водопоглощение, % масс…………………………………………....…1…5
Насыпнаяплотностьщебня, кг/м3…………………………….1200…1500
1 — шлаковозныйковш; 2 — траншеядляшлаковыхрасплавов; 3 — грохот; 4 — бункеры; 5 — дробилка;
6 — бункерыдляготовойпродукции(шлаковогощебня) Рисунок 27 - Схема производства литого щебня траншейным способом:
66
Литой шлаковый щебень характеризуется высокими морозо- и жаростойкостью, а также сопротивлением истиранию. Стоимость его почти в 2 раза меньше, чем щебня из природного камня. Для изготовления бетонных и железобетонных изделий применяют фракционированный литой шлаковый щебень крупностью 5…70 мм. Несортированный материал используется в дорожном строительстве и в производстве минеральной ваты, а отсев может служить
.заполнителем жароупорных бетонов и частично заменять гранулированный шлак в производстве шлакопортландцемента. Для получения литого плотного шлакового щебня кристаллической структуры применяются «малогазистые» ог- ненно-жидкие шлаки, в которых при охлаждении образуется минимальное число пор, асредняяплотностькусков— не менее 2200 кг/м3.
Необходимым условием получения заполнителей из металлургических шлаков является устойчивость их к различным видам распада. Особенно опасен силикатный распад, характерный для высококальциевых, маломарганцевых и малоглиноземистых шлаков.
Полиморфное превращение ортосиликата кальция — основная причина, вызывающая эту форму распада, может возникнуть при медленном остывании шлаков. Поэтому основным способом стабилизации шлаков, склонных к силикатному распаду является быстрое их охлаждение (термическая стабилизация); например, слив шлаковых расплавов тонким слоем с откоса щлаковой горы или грануляция.
Кроме термической, разработаны также способы химической и кристаллохимической стабилизации, основанные на введении в расплав добавок, способствущихобразованиюустойчивыхсоединений. При химическом способе в расплав вводятся обычно добавки (глина, песок), связывающие оксид кальция и способствующие кристаллизации устойчивых минералов (геленита, окерманита и др.). Сущность кристаллохимического способа заключается в стабилизации β-C2S введением некоторых добавок в шлаковый расплав. К эффективным стабилизаторам, при введении которых образуется устойчивая решетка ортосиликата кальция, относятся щелочи, оксиды фосфора, бора и др. Опасен также железистый распад, вызываемый увеличением объема (почти на 38%) при воздействии воды на сульфид железа и образованием гидроксида железа. Распад шлаков начинается в процессе их охлаждения и завершается в отвалах в течение 2…3 месяцев. Шлаки, пролежавшие в отвалах длительное время и не имеющие признаков распада, считаются устойчивыми.
Для ускоренной оценки стойкости шлаков к силикатному распаду пробу подвергают пропариванию над кипящей водой или в автоклаве при давлении 0,2 МПа. Шлаковый щебень считается стойким к силикатному распаду, если потеря массы для испытываемой фракции не превышает 5%. Склонность к силикатному распаду можно определить, облучая шлаки ультрафиолетовыми лучами (люминесцентный метод). Шлаки, склонные к силикатному распаду, отличаются желтым или золотистым свечением, а устойчивые — фиолетовым различных оттенков.
Стойкость против железистого распада устанавливается выдерживанием шлакового щебня в дистиллированной воде в течение 30 сут. Потеря массы при
67

этом так же, как и при испытании на силикатный распад, не должна превышать
5%.
Для предотвращения известкового и магнезиального распада в шлаках, перерабатываемых на заполнители, не допускаются свободные оксиды кальция
имагния.
Взависимости от крупности зерен щебень делится на фракции: 5…10, 10…20, 20…40, 40…70, 70…120 мм. Зерновой состав шлакового щебня, как и других видов заполнителя, подбирается для обеспечения минимальной пустотно-
сти. Минимальная насыпная плотность щебня каждой из фракций составляет 1000 кг/м3. Содержание зерен пластинчатой (лещадной) и игловатой формы, должно быть для щебня: кубовидного — не более 15%; улучшенного — 25; обычного — 35%. Длина таких зерен в три и более раза превышает их толщину или ширину.
Прочность шлакового щебня характеризуется его маркой. Для щебня из доменного шлака, применяемого в качестве заполнителя тяжелого бетона, установлено пять марок по прочности:
Таблица 15 - Марки щебня по прочности
Марка щебня по прочности |
1200 |
1000 |
800 |
600 |
300 |
Потеря в массе после испытаний, % |
До 15 |
15…25 |
25…35 |
35…45 |
45…55 |
Щебень марки M1200 может быть использован при изготовлении бетона марки М400 и выше, М1000 — марки М300, М800— марки М200 и М600 — ниже М200. Щебень низких марок применяется также при изготовлении бетонов более высокой прочности, но после соответствующей проверки и техникоэкономического обоснования.
В зависимости от числа циклов, которые выдерживает щебень при испытании, устанавливают его марки по морозостойкости(таблица16).
Таблица16 - Маркишлаковогощебняпоморозостойкости
Испытания |
|
Марка щебня по морозостойкости |
|
|||||
|
|
|
|
|
|
|
|
|
F15 |
F25 |
F50 |
F100 |
F150 |
F200 |
|
F300 |
|
|
|
|||||||
|
|
|
|
|
|
|
|
|
непосредственное замора- |
|
|
|
|
|
|
|
|
живание: |
15 |
25 |
50 |
100 |
150 |
200 |
|
300 |
число циклов |
|
|
|
|
|
|
|
|
|
|
|
|
|
|
|
|
|
потеря массы после испы- |
10 |
10 |
5 |
5 |
5 |
5 |
|
5 |
тания, %, не более |
|
|
|
|
|
|
|
|
Содержание в шлаковом щебне отмучиваемых пылевидных и глинистых частиц должно быть не более 3% для слабоактивного и неактивного шлаков. Для активных и высокоактивных шлаков содержание отмучиваемых примесей не нормируется. Недопустимо содержание в щебне примесей топливных шлаков, золы, колошниковой пыли.
Содержание глины в комках в щебне из шлаков всех видов не должно быть более 0,25% по массе.
68