
БТ / ZAPOLNITELI BETONA
.pdf
Установка для |
|
Установка для |
|
Приёмный бункер |
|
Открытый склад |
|
|
Глинозапасник |
|||||||||||
приготовления |
|
приготовления |
|
твёрдых добавок |
|
|
|
глины |
|
|
|
|
|
|
|
|||||
|
|
|
|
|
|
|
|
|
|
|
|
|||||||||
опудривающего |
|
эмульсии |
|
|
|
|
|
|
|
|
|
|
|
|
|
|
|
|
|
|
|
|
|
|
|
|
|
|
|
|
|
|
|
|
|
|
|
|
|||
порошка |
|
|
|
|
|
|
|
|
|
|
|
|
|
|
|
|
|
|
|
|
|
|
|
|
|
|
|
|
|
|
|
|
|
|
|
|
|
|
|
|
|
|
|
|
|
|
|
|
|
|
|
|
|
|
Экскаватор |
|
|
|
|
|
|
|
Бункера опудри- |
|
Насос шестерен- |
|
Ленточный пита- |
|
|
|
|
|
|||||||||||
|
|
|
|
|
|
|
|
|
|
|
|
|
||||||||
|
|
|
|
|
|
|
|
|
|
|
|
|
||||||||
вающего порошка |
|
чатый |
|
|
тель ПЛ-6 |
|
|
|
|
|
|
|
|
|
|
|
||||
|
|
|
|
|
|
|
Мостовой грей- |
|||||||||||||
|
|
|
|
|
|
|
|
|
|
|
|
|
|
|
||||||
|
|
|
|
|
|
|
|
|
|
|
|
Автосамосвал |
|
|
ферный кран |
|||||
|
|
|
|
|
|
|
|
|
|
|
||||||||||
|
|
|
|
|
|
|
|
|
|
|
|
|
|
|
|
|
|
|
|
|
Ленточный пита- |
|
|
|
|
|
|
|
|
|
|
|
|
|
|
|
|
|
|
|
|
тель ПЛ-4 |
|
|
|
|
|
|
|
|
|
|
|
|
|
|
|
|
|
|
|
|
|
|
|
|
|
|
|
|
|
|
|
|
Глинорыхлительная машина 1031-А |
|
|
||||||
|
|
|
|
|
|
|
|
|
|
|
|
|
|
|||||||
|
|
|
|
|
|
|
|
|
|
|
|
|
|
|
||||||
|
|
|
|
|
|
|
|
|
|
|
|
|
|
|
|
|
|
|
|
|
|
|
|
|
|
|
|
|
|
|
|
|
|
|
|
|
|
|
|
|
|
|
|
|
|
|
|
|
|
|
|
|
|
|
Ящичный подаватель 1090 |
|
|
|
|
|
||
|
|
|
|
|
|
|
|
|
|
|
|
|
|
|
|
|
|
|||
|
|
|
|
|
|
|
|
|
|
|
|
|
|
|
||||||
|
|
|
|
|
|
|
|
|
|
|
|
|
Дезинтеграторные вальцы 150-А |
|
|
|
||||
|
|
|
|
|
|
|
|
|
|
|
|
|
|
|
|
|||||
|
|
|
|
|
|
|
|
|
|
|
|
|
|
|
|
|
|
|
||
|
|
|
|
|
|
|
|
|
|
|
|
|
|
|
|
|
|
|
||
|
|
|
|
|
|
|
|
|
|
|
|
|
Глиномешалка СМ-447А |
|
|
|
|
|
||
|
|
|
|
|
|
|
|
|
|
|
|
|
|
|
|
|
Вода |
|||
|
|
|
|
|
|
|
|
|
|
|
|
|
|
|
|
|
|
|
|
|
|
|
|
|
|
|
|
|
|
|
|
|
|
|
|
|
|
|
|
|
|
|
|
|
|
|
|
|
|
|
|
|
|
|
|
|
|
|
|
|
|
|
|
|
|
|
|
|
|
|
|
|
|
|
|
Глиномешалка СМ-246 |
|
|
|
|
|
||
|
|
|
|
|
|
|
|
|
|
|
|
|
|
|
|
|
|
|
|
|
|
|
|
|
|
|
|
|
|
|
|
|
|
|
|
|
|
|
|
|
Пар |
|
|
|
|
|
|
|
|
|
|
|
|
|
|
|
|
|||||
|
|
|
|
|
|
|
|
|
|
|
|
|
|
|
||||||
|
|
|
|
|
|
|
|
|
|
|
|
|
Вальцы дырчатые перерабатываю- |
|
|
|
||||
|
|
|
|
|
|
|
|
|
|
|
|
|
щие СМ-369А |
|
|
|
|
|
||
|
|
|
|
|
|
|
|
|
|
|
|
|
|
|
|
|
|
|
|
|
|
|
|
|
|
|
Ленточный |
|
|
|
|
|
|
|
|
|
|
|
|
||
|
|
|
|
|
|
пресс |
|
|
|
|
Вальцы дырчатые формующие |
|
||||||||
|
|
|
|
|
|
|
|
|
|
|
|
|
СМ-927 |
|
|
|
|
|
||
|
|
|
|
|
|
|
|
|
|
|
|
|
|
|
|
|
|
|||
|
|
|
|
|
|
|
|
|
|
|
|
|
|
|
|
|
|
|
|
|
|
|
|
|
|
|
|
|
|
|
|
|
|
|
|
|
|
|
|
|
|
|
|
|
|
|
|
|
|
|
|
|
|
|
Барабан для окатки гранул |
|
|
|
|
|
||
|
|
|
|
|
|
|
|
|
|
|
|
|
|
|
|
|
|
|
|
|
|
|
|
|
|
|
|
|
|
|
|
|
|
|
|
|
|
|
|
||
|
|
|
|
|
|
|
|
|
|
|
|
|
Сушильный барабан |
|
|
|
|
|
||
|
|
|
|
|
|
|
|
|
|
|
|
|
|
|
|
|
|
|
||
|
|
|
|
|
|
|
|
|
|
|
|
|
|
|
|
|
|
|
||
|
|
|
|
|
|
|
|
|
|
|
|
|
Бункер сухих гранул |
|
|
|
|
|
||
|
|
|
|
|
|
|
|
|
|
|
|
|
|
|
||||||
|
|
|
|
|
|
|
|
|
|
|
|
|
|
|||||||
|
|
|
|
|
|
|
|
|
|
|
|
|
Маятниковый питатель С-633 |
|
|
|
|
|||
|
|
|
|
|
|
|
|
|
|
|
|
|
|
|
|
|
|
|
||
|
|
|
|
|
|
|
|
|
|
|
|
|
|
|
|
|
|
|
||
|
|
|
|
|
|
|
|
|
|
|
|
|
Вращающаяся печь |
|
|
|
|
|
Рисунок 9 - Технологическая схема подготовки гранул пластическим способом
Наличие двух глиномялок встречается довольно редко, хотя двойная переработка глины в глиномешалках заметно улучшает качество керамзита.
При назначении диаметра формуемых гранул следует учитывать, что кривая зависимости плотности вспученной гранулы от ее диаметра в сырце имеет экстремальный характер и, следовательно, каждой глине соответствует некоторый диаметр сырцовых гранул, дающий керамзит с минимальной плотностью.
Перед обжигом гранулы сушат не всегда. В некоторых случаях отмечается повышенная вспучиваемость гранул при их поступлении в печь непосредственно с формовочной машины без предварительной сушки. Однако такая схема применима только при высокой трещиностойкости глин в сушке и высокой их вспучиваемости. В последнем случае, если гранулы в печи даже разрушаются, то их осколки все равно будут вспучиваться, давая легкий керамзит. Осколки же гранул
39
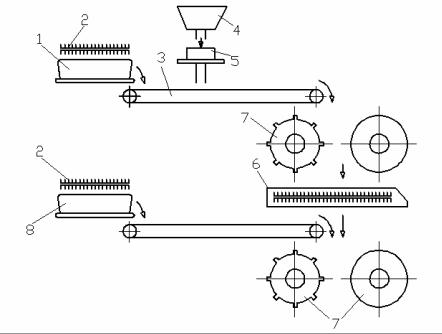
из средне- и слабовспучивающихся глин в обжиге почти не вспучиваются и заметно утяжеляют керамзит. Работа без предварительной сушки гранул неудобна еще и тем, что в этом случае формовочное отделение должно работать в три смены, а перебои в работе формовочного оборудования немедленно вызывают нарушения в работе печи. Но даже при отсутствии видимых перебоев в работе глиноперерабатывающего оборудования колебания в питании печи полуфабрикатом в условиях отсутствия буферного запаса сухих гранул довольно велики из-за неравномерной работы ящичного подавателя.
Влажность выходящих из сушильного барабана гранул составляет 12…14%. Бункеры запаса высушенных гранул надежно работают лишь при наличии приточно-вытяжной вентиляции для эвакуации водяных паров, выделяющихся из горячих гранул. При отсутствии такой вентиляции происходит зависание гранул в бункерах. Добавки подготовляют и вводят следующим образом: опилки и уголь просевают для отделения крупных фракций и дозируют ленточным или тарельчатым питателем на конвейер или глиномешалку (прямой ввод). Более эффективен ступенчатый ввод по схеме (рисунок 10). Низковязкие жидкие добавки специальной подготовки не требуют; их вводят в глиномешалку, распыливая механическими, предварительно тарированными форсунками. Высоковязкие добавки подогревают в специальных паровых теплообменниках до 80—100° С и затем также вводят распылением.
1 - ящичный подаватель, подающий 15% общего расхода глины; 2 - рыхлитель глины; 3 - ленточный конвейер; 4 - бункер твердой добавки; 5 - тарельчатый питатель; 6 - одновальная глиномешалка; 7 - дезинтеграторные вальцы;
8 - ящичный подаватель, подающий 85% глины. Рисунок 10 - Схема ступенчатого ввода твердых добавок
Эмульсионные добавки приготовляют тщательным перемешиванием в турбулентном диспергаторе предварительно разогретого мазута и глинистой сус-
40
пензии (стабилизатора) до получения устойчивой тонкой дисперсии мазута в воде.
Равномерность распределения добавок в глине резко возрастает при обработке ее в вибрационной глиномялке.
Опудривание сырых гранул огнеупорной глиной или каолином дает возможность обжигать гранулы при более высокой температуре и за счет этого понизить плотность керамзита и повысить производительность печи. Примерный расход опудривающего порошка составляет 3…5% массы сырцовых гранул.
Пластический способ является более сложным и дорогим, чем сухой, но зато он допускает использование глин более распространенных разновидностей
идает возможность вводить в глину добавки, повышающие ее вспучиваемость. В силу этого он получил в нашей стране преимущественное распространение.
Шликерный способ является бесформовочным. Во вращающуюся печь подают глиняный шликер, и гранулы образуются самопроизвольно в самой печи. Этот способ целесообразно применять, когда карьерная влажность глин выше формовочной, а также для глин, природную структуру которых трудно разрушить способами пластической переработки, при добавках высоковязких глин и при значительном содержании каменистых включений в глине (более 10%).
Для первичного дробления глины можно применять дезинтеграторные вальцы, валковозубчатые дробилки и дисковые глинорезки. Глиняный шликер приготовляют в глиноболтушках грабельного типа. Диаметр их достигает 12 м, а производительность 60 т по массе. Достоинством их является безаварийная работа с глинами, засоренными каменистыми включениями, в том числе и крупными кремневыми. Крупные каменистые включения задерживаются выпускной решеткой глиноболтушки, остаются в ней и периодически удаляются. Мелкие включения размером 0,5…10 мм необходимо отделять на дуговом сите, на которое шликер подается под давлением 0,2…0,3 МПа. Приготовленный шликер должен иметь текучесть 10 с и растекаемость 65…..75 мм.
Для понижения влажности шликера в него вводят электролиты. Запас шли-
кера хранят в специальных емкостях – шлам-бассейнах. Они бывают вертикальные диаметром 8 м, вместимостью 1000 м3 с пневматическим перемешиванием, а также горизонтальные круглые диаметром 35 м, вместимостью 6000 м3 с крановыми мешалками и пневматическим перемешиванием. Шликерный способ обладает серьезными достоинствами: он является наиболее универсальным и позволяет использовать глины с более широким диапазоном свойств. Значительно упрощается при этом способе решение задачи очистки глины от каменистых и карбонатных включений. Глину можно размораживать в глиноболтушках. Поэтому отпадает необходимость утеплять запас глины для работы в зимнее время. Керамзит получается более легким и более мелким, чем при пластическом способе. К недостаткам этого способа следует отнести повышенный расход топлива
иснижение производительности печи примерно на 25…30% в связи с необходимостью испарять большое количество влаги.
Обжиг керамзитового гравия осуществляют во вращающихся однобарабанных и двухбарабанных печах.
41
Наибольшее распространение для обжига керамзитового гравия получили однобарабанные печи двух типа размеров: 40Ч2,5 и 22Ч2,3 м. В единичных экземплярах работают печи других типоразмеров, максимальная длина которых достигает 60 м. С увеличением длины печи расход топлива снижается. Однако плотность керамзита при этом возрастает.
Можно выделить четыре технологические зоны: сушки, подогрева, вспучивания и отвердевания. Основное количество свободной влаги удаляется на длине 11 м при температуре материала до 100 °С. Потерь при прокаливании в этой зоне не происходит, а плотность материала уменьшается медленно, исключительно за счет подсушки гранул. Температура газов этой зоны довольно высока – 700…850 °С, однако из-за того, что гранулы поступают в печь сырыми, их температура повышается довольно медленно. Коэффициент теплообмена в этой зоне составляет 145…232 Вт/(м2·град). Зона подогрева занимает в данном случае 15 м. В ней удаляются остатки гигроскопической (связанной) влаги, полностью удаляются летучие вещества (заканчиваются потери при прокаливании), материал подогревается со 100 до 875 °С при температуре в печи 850…1100 °С. Плотность гранул продолжает монотонно уменьшаться за счет удаления остатков гигроскопической и гидратной влаги и некоторого количества летучих веществ. Коэффициент теплообмена в этой зоне равен 105…128 Вт/(м2·град).
Взоне вспучивания на коротком участке длиной 8 м почти скачкообразно понижается плотность гранул с повышением температуры материала до 1125 °С. Затем в этой же зоне на последнем ее участке длиной 4 м температура газов и материала продолжает оставаться стабильной, а плотность гранул продолжает несколько уменьшаться, поскольку материал их в этой зоне находится в пирокластическом состоянии.
Зона отвердевания очень короткая - всего 2 м. В ней температура материала понижается от конечной 1125 до 1025 °С и соответственно уменьшается температура газов. Иногда в этой зоне температура газов снижается более интенсивно, чем температура материала.
Режим термоподготовки оказывает существенное влияние на качество керамзита. Он должен исключить взрывание гранул и потерю ими вспучиваемости вследствие преждевременного удаления органических веществ [2,6].
Результаты вспучивания обжигаемых гранул в производственной печи сильно зависят еще от химического характера газовой печной среды. Восстановительная среда обеспечивает наиболее высокий коэффициент вспучивания, но чревата опасностью сваривания гранул в конгломерат. Сильно окислительная среда снижает вспучиваемость и повышает расход топлива. Наиболее целесообразна слабо восстановительная среда с содержанием кислорода в печных газах не выше 9%.
Для многих глин представляется необходимым замедлить повышение температуры в зоне подогрева и поднимать ее в этой зоне лишь до 400…600 °С с тем, чтобы сохранить в материале полностью его газотворную способность для зоны вспучивания.
Вэтом случае кривая температуры материала примет четко выраженный ступенчатый характер. Поэтому обжиг с медленным повышением температуры в
42
зоне подогрева и быстрым в зоне вспучивания - называют иногда ступенчатым (или двухстадийным) обжигом. Для осуществления такого режима нужно располагать возможностью регулирования параметров процесса по длине печи. В известных пределах в однобарабанных печах режим можно регулировать изменением длины факела за счет конструкций горелок, изменением интенсивности загрузки материала в печь, устройством в футеровке подпорных колец, оборудованием «холодного» конца печи теплообменными устройствами, применением ребристой футеровки в «холодном» конце печи и установкой У-образного теплообменника на загрузочном конце печи. При установке теплообменника совместно с перевальным порогом производительность печи возрастает почти на 70%, а расход топлива снижается на 20%.
Рассмотренные мероприятия дают возможность регулировать режим обжига в весьма ограниченных пределах и эффективны преимущественно в коротких печах. Гораздо большими возможностями технологического маневрирования обладают двухбарабанные печи. В них длинный барабан малого диаметра предназначен для сушки и подогрева гранул до температуры 200…600 °С, а короткий барабан большого диаметра - для их вспучивания. Каждый барабан имеет самостоятельный привод, благодаря чему создается возможность регулировать скорость продвижения материала в каждом барабане. Увеличенный диаметр барабана вспучивания дает также возможность повысить в нем тепловую мощность и тем самым придать кривой нагрева более четкий ступенчатый характер.
Охлаждение керамзита. Наибольшее распространение для охлаждения керамзита получили барабанные холодильники, основным достоинством которых является надежность в работе. Они представляют собой полые цилиндры диаметром 1,5…2,5 м и длиной 8…22 м, устанавливают их с уклоном 3…4% и частотой вращения 1,5…2,5 мин. Для замедления темпа охлаждения керамзита в области температур его кристаллизации рекомендуют этот участок футеровать огнеупорным легковесом, а остальную часть барабана оборудуют пересыпными устройствами. Общую длительность охлаждения в барабанном холодильнике можно регулировать изменением числа оборотов, угла наклона и расхода воздуха, а также установкой подпорных колец. Возможность осуществления ступенчатой кривой охлаждения в нем крайне ограничена.
Присущие барабанным холодильникам низкие интенсивности теплообмена и, как следствие, высокая температура выгружаемого керамзита (150…250° С) и громоздкость установки вызывают необходимость заменить их более компактными холодильниками, к числу которых относится самотечный слоевой колосниковый холодильник керамзита (рисунок 11). Он состоит из двух ступеней наклонных решеток, заключенных в футерованный изнутри металлический корпус. Холодный воздух поступает под нижние решетки, затем пронизывает слой керамзита, находящегося на верхних решетках, и удаляется через специальные патрубки. Охлаждение в слое и принцип противотока обусловливают мягкий режим охлаждения, исключающий значительную потерю прочности керамзита. Производительность холодильника достигает 20 м3/ч, температура выгружаемого керамзита 60° С, отработанного воздуха 250…350° С, его расход 1…2 м3/кг, аэродинамическое сопротивление 5…15 МПа, масса 13 т. Длительность охлаждения
43
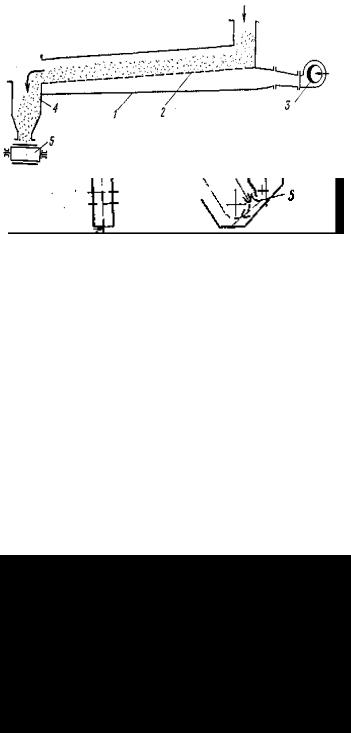
зависит от производительности и почти вдвое больше, чем в барабанном холодильнике.
1 - корпус теплообменника; 2 - наклонные решетки; 3 - поворотные шиберы; 4- ковшовый элеватор; 5- секторный затвор; 6-загрузочное отверстие;
7-патрубок отбора горячего воздуха;
8- патрубок подачи холодного воздуха Рисунок 11 - Самотечный колосниковый холодильник
На некоторых заводах для охлаждения керамзита установлены аэрожелоба (рисунок 12). Аэрожелоб представляет собой установленный с уклоном к горизонту длинный полутрубчатый корпус 1, внутри которого помещено решетчатое днище 2. Вентилятор 3 нагнетает холодный воздух под решетку, создавая на ней воздушную подушку, по которой движется керамзит, в приемный бункер 4 и далее на конвейер 5. Достоинством аэрожелобов является простота устройства и надежность работы. Однако первые опыты их применения выявили, что прочность охлажденного в них керамзита ниже, чем керамзита, получаемого в холодильниках других типов [1].
Рисунок 12 - Аэрожелоб для охлаждения керамзита
Сортировка и складирование керамзита. Охлажденный керамзит сорти-
руют по размерам гранул на четыре фракции. Для этой цели применяют гравиесортировки С-215Б, устанавливаемые на перекрытии склада готовой продукции. На некоторых заводах сортировочное устройство агрегируется с барабанным холодильником, составляя его выходную часть. Такое решение повышает компактность схемы.
44
4.1.4 Производство керамзитового песка
Для изготовления керамзитобетонных изделий нужен не только керамзитовый гравий, но и мелкий пористый заполнитель — керамзитовый песок.
Производство керамзитового песка по обычной технологии во вращающейся печи неэффективно. Некоторая примесь песчаной фракции получается при производстве керамзитового гравия за счет разрушения частиц в процессе термообработки, однако он сравнительно тяжелый, так как мелкие частицы глинистого сырья практически не вспучиваются (резервы газообразования исчерпываются раньше, чем глина переходит в пиропластическое состояние). Кроме того, в зоне высоких температур мелкие гранулы разогреваются сильнее крупных, при этом возможно их оплавление и налипание на зерна гравия.
На многих предприятиях керамзитовый песок получают дроблением керамзитового гравия, преимущественно в валковых дробилках. Себестимость дробленого керамзитового песка высока не только в связи с дополнительными затратами на дробление, но главным образом потому, что выход песка всегда меньше объема дробимого гравия. Коэффициент выхода песка составляет 0,4...0,7, т.е. в среднем из 1 м3 гравия получают только около 0,5 м3 дробленого керамзитового песка. При этом почти вдвое возрастает его насыпная плотность [5].
В настоящее время при получении керамзитового песка лучшей считают технологию его обжига в кипящем слое. В вертикальную печь загружают глиняную крошку крупностью до 3 или 5 мм, получаемую дроблением подсушенной глины или специально приготовленных по пластическому способу и затем высушенных гранул. Печь (рисунок 13) имеет две зоны: обжига и подогрева, разделенные между собой сплошной перегородкой. Через решетчатый (пористый) под печи снизу под давлением подают воздух и газообразное топливо. При определенной скорости подачи газов слой глиняной крошки разрыхляется, приходит в псевдоожиженное состояние, а при ее увеличении как бы кипит. Газообразное топливо сгорает непосредственно в кипящем слое. Благодаря интенсификации теплообмена в кипящем слое происходит быстрый и равномерный нагрев материала. Частицы глины обжигаются и вспучиваются примерно за 1,5 мин. Перед подачей в зону обжига глиняная крошка подогревается в кипящем слое зоны термоподготовки примерно до 300°С, а готовый песок после обжига охлаждается в кипящем слое холодильного устройства. Часть мелких фракций песка с отходящими газами из зоны обжига поступает в футерованный циклон и осаждается, а очищенные газы направляются в зону предварительного нагрева печи.
Принимаемая для расчетов паспортная производительность печи кипящего слоя CMC-139—6,7 м3/ч (коэффициент использования kи=0,85). Насыпная плотность получаемого керамзитового песка — 500...700 кг/м3. К зерновому составу керамзитового песка предъявляются требования, аналогичные
45

требованиям к природному песку, но крупных фракций в нем должно быть больше.
Проблему получения керамзитового песка, достаточно эффективного по свойствам и себестоимости, нельзя считать полностью решенной. Часто при получении керамзитобетона в качестве мелкого заполнителя применяют вспученный перлит, а также природный песок.
1 — зона предварительного подогрева; 2 — зона обжига; 3 — холодильник кипящего слоя; 4 — футерованный циклон;
5 — нагнетатель воздуха; 6 — выгрузочные клапанные затворы; 7 — подача газа; 8 — секторные затворы на наружных перетоках; 9 — циклон зоны термоподготовки
Рисунок 13 - Схема двухзонной печи кипящего слоя
4.1.5 Примеры составления технологических схем производства керамзита и керамзитового песка
Оптимальные мощности заводов и цехов по производству керамзита, согласно нормам технологического проектирования ОНТП 11—86, составляют соответственно 200 ...400 и 100 ...200 тыс. м3 в год. При этом обычно предусматривают выпуск продукции со следующим соотношением по фракциям: 0
... 5 мм— 10%; 5... 10 мм — 40%; 10...20 мм —40%; 20 ...40 мм—10%.
Предварительными испытаниями сырья устанавливают способ производства, состав шихты, технологическую схему производства и ожидаемое качество керамзита [5].
Подавляющее большинство предприятий производят керамзит по пластическому способу с применением технологических схем, отличающихся вариантами переработки глинистого сырья и типом обжиговых печей (агрегатов). Сухой способ производства применяют, главным образом, для получения разновидности керамзита — шунгизита.
В качестве примера на рисунке 14 показана принципиальная технологи-
ческая схема типового цеха по производству керамзитового гравия мощностью 200 тыс. м3 в год.
Цех состоит из трех отделений: подготовительно-формовочного, печного и склада готовой продукции. Сырье автосамосвалами из карьера или конуса,
46
расположенного вблизи производства, доставляют на склад вместимостью 3500 м3 (восьмисуточный запас). Мостовым грейферным краном глину равномерно распределяют по площади склада и подают в производство [7,8].
Вподготовительно-формовочном отделении установлены две линии переработки сырья и формования сырцовых гранул, одна из которых показана на рисунке 14, и линия подсушки глины с повышенной карьерной влажностью. В теплое время года глину можно подавать автосамосвалами непосредственно в приемный бункер глинорыхлителя линии подсушки сырья. Разрыхленную глину повышенной влажности направляют сначала в камневыделительные вальцы, затем — в сушильный барабан. Подсушенную глину транспортируют ленточным конвейером в приемный бункер линии переработки сырья, где ее измельчают в вальцах грубого помола, перемешивают в глиномешалке, в которую при необходимости подают добавку, например водный раствор ЛСТ, затем дополнительно измельчают в вальцах тонкого помола с зазором между валками 1...1,5 мм. Подготовленную массу транспортируют в ящичный питатель, установленный над формующим агрегатом, для его бесперебойного питания.
Формование сырцовых гранул осуществляют на ленточном шнековом прессе с гранулирующей приставкой. В качестве формующего агрегата могут быть использованы дырчатые формующие вальцы, если перерабатывают суглинки с числом пластичности менее 15 или сырье, сильно засоренное крупными включениями.
Сформованные гранулы окатываются и подсушиваются в сушильном барабане до влажности не более 19%, а затем их транспортируют в печное отделение для обжига в агрегате CMC-197.
Вслоевом подготовителе (CMC-198) гранулы полностью высушиваются
ипоступают во вращающуюся печь (CMC-199) подогретыми до 200°С, где происходит их дальнейший нагрев и вспучивание при температуре 1150...
1250°С. Вспученные гранулы сначала несколько охлаждаются, в печи (примерно до 900... 1000°С), а затем в слоевом холодильнике (СМ-1250) до 80°С. Предельная скорость охлаждения гравия крупностью до 20 мм не должна превышать 100°С/мин.
Охлажденный керамзит транспортируют ленточными конвейерами на склад готовой продукции, где элеватором его подают на рассев в гравиесортировку. Полученные фракции распределяют по силосным банкам ленточным конвейером. Для фракций 5... 10 и 10... 20 мм предусмотрено по три силоса, для фракций 0...5 и 20... 40 мм — по одному силосу. Вместимость силосных банок рассчитана на четырехсуточный запас готовой продукции.
47
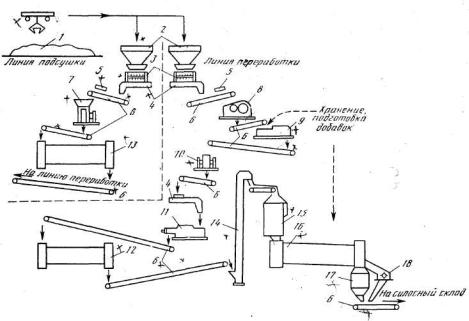
1 - склад глины, оборудованный мостовым электрическим краном с грейфером; 2 - бункер приемный; 3 - глинорыхлитель; 4 - питатель ящичный; 5 - железоотделитель подвесной;
6 - конвейер ленточный;
7 - вальцы дырчатые (или камневыделительные);
8- вальцы грубого помола (камневыделительные); 9 - пресс ленточный шнекбвый с камневыделительной приставкой (или
смеситель с фильтрующей решеткой); 10вальцы тонкого помола; 11 - пресс ленточный шнековый с гранулирующей приставкой;
12 - барабан сушильный для под сушки гранул; 13 - барабан сушильный для подсушки глины; 14 - элеватор;
15 - подготовитель слоевой; 16 - печь вращающаяся 2,8х20; 17 - холодильник слоевой; 18 - дробящее устройство (для спеков) Рисунок 14 - Технологическая схема производства керамзита
с подготовкой сырцовых гранул по пластическому способу и обжигом в агрегате CMC-197
На складе предусмотрен узел дробления крупных фракций (свыше 20 мм) с последующим рассевом в гравиесортировке и распределением по силосным банкам.
Отгрузка готовой продукции предусмотрена на автомобильный и железнодорожный транспорт.
Производство керамзитового песка в печах кипящего слоя целесообразно организовывать при заводах и цехах керамзитового гравия, используя в качестве сырья гранулы-полуфабрикаты от сушильного барабана.
Технологическая схема производства керамзитового песка цеха мощностью 50 тыс. м3 в год приведена на рисунке 15. Цех предусмотрен для размещения на территории завода керамзитового гравия. Режим работы — круглогодовой, в три смены.
48