
БТ / ZAPOLNITELI BETONA
.pdfРастворимый кремнезем предопределяет пуццолановый характер взаимодействия шлаковых зерен с цементным камнем. Реакционная способность повышается с увеличением количества СаО в стеклофазе и снижается при увеличении количества Fe2О3.
Гидравлическая активность топливных гранулированных шлаков, выраженная количеством поглощенной извести, составляет 20…30 мг/г. Непосредственное влияние на гидравлическую активность шлаков имеет их фазовый состав. Структура зерен шлака зависит от условий охлаждения. Так, шлаковые зерна, полученные при непосредственном попадании расплава в воду, т. е. при отсутствии условий кристаллизации, состоят из однородного алюможелезистосиликатного стекла. В воздушных условиях шлаковый расплав характеризуется более медленным режимом охлаждения, что способствует образованию зародышей кристаллов, вследствие чего структура шлака отличается закристаллизованностью.
Гранулированные шлаки от сжигания углей с низкокальциевой минеральной частью относятся к труднокристаллизующимся даже при относительно медленном охлаждении, содержат не более 10…15% кристаллических компонентов.
Физико-механические характеристики шлака, его структура зависят от вида сжигаемого топлива и способа его удаления. Среди общей массы шлака можно выделить плотные и пористые зерна с различным количеством открытых и закрытых пор. Средняя плотность таких зерен может колебаться от 2,6 до 1,5 г/см3, в редких случаях встречаются зерна со средней плотностью до 1 г/см3. Истинная плотность шлака в основном 2,3…2,7 г/см3, насыпная находится в пределах
1100…1700 кг/м3.
Гранулированный топливный шлак характеризуется широким разнообразием формы и рельефа поверхности отдельных гранул. Преобладающей является кубообразная, призматическая и остроугольная форма его зерен. Важной положительной особенностью гранулированных шлаков по сравнению с заполнителями из горных пород является значительное содержание зерен с высокоразвитым микрорельефом. Анализ зерен шлаков под микроскопом показывает, что в крупных зернах шлака часто встречаются поры диаметром 1…3 мм и более, а также поверхностные раковины. Это наряду с гидравлической активностью шлака служит фактором, несомненно способствующим увеличению его сцепления с цементным камнем.
Важнейшими особенностями гранулированных топливных шлаков как заполнителей бетона являются сравнительно большая прочность шлаковых зерен (образцы–кубики с размером ребра 2 см имеют прочность 120…140 МПа; повышенная макро- и микропористость (до 13%)); развитая поверхность зерен и, вследствие этого, повышенная водопотребность (9…11%); отсутствие глинистых, илистых и других вредных примесей, а также игловатых и лещадных зерен.
Механические характеристики топливных гранулированных шлаков позволяют получить бетон классов до В40.
Морозостойкость стекловидных шлаков довольно высока и допускает изготовление разнообразных бетонов для высокодолговечных строительных конструкций. Шлаки практически не содержат компонентов, которые могут снижать
79
защитные свойства бетона или придавать ему агрессивность по отношению к арматуре.
Всоответствии с ГОСТ содержание зерен, проходящих через сито с сеткой
№0315, должно быть для фракционированного щебня не более 5% по массе, для шлакового песка – не более 20% и для рядового несортированного шлака – не более 10%.
Вряде исследований установлено, что гранулированный топливный шлак оказывает существенное влияние на реологические и технологические свойства бетонных смесей. Отмечается, что бетонные смеси с шлаковым заполнителем имеют лучшую удобоукладываемость по сравнению с бетонами на природных заполнителях. Предлагается применять топливный гранулированный шлак для литых бетонных смесей, транспортируемых бетононасосами, производительность которых увеличивается благодаря тому, что пробки в них возникают в 4 раза реже. Однако, стекловидная поверхность шлака, обладающая малой водоудерживающей способностью (3…4%), способствует водоотделению бетонной смеси в бетонах высокой подвижности даже при повышенных расходах цемента.
Установлено, что бетоны на топливных гранулированных шлаках отличаются по структуре и свойствам от бетонов на природных заполнителях. Плотная структура шлакобетона, большая площадь поверхности гранулированного шлака, хорошее сцепление заполнителя с цементным камнем придают бетону хорошие прочностные и деформативные свойства. Разрушение бетона на граншлаке ТЭС проходит частично по растворной части и частично по шлаку, в отличие от бетона на гранитном щебне. Такой характер разрушения свидетельствует об однородности бетона, прочном сцеплении заполнителя с растворной частью. Физикохимическими исследованиями установлено, что прочность сцепления шлака с цементным камнем обусловлена не только адгезией за счет рельефа поверхности зерен, но и в значительной степени химическим взаимодействием цементного камня и заполнителя. Образуемая в зоне контакта пленка новоообразований (низкоосновные гидросиликаты кальция) является оболочкой, которая обволакивает зерназаполнителя, улучшает сопротивление бетона внешним воздействиям.
Более интенсивно взаимодействие гранулированного шлака с цементом протекает при тепловлажностной обработке бетона. В связи с этим сразу после пропаривания прочность шлакосодержащего бетона составляет около 80% от марочной, а спустя 28 суток она на 10…15% превышает прочность бетона, твердевшеговнормальныхусловиях.
При проведении сравнительных испытаний бетона со шлаковым и гранитным заполнителями на прочность при растяжении методом раскалывания были получены практически одинаковые результаты. Исследования призменной прочности, начального модуля упругости, предельных относительных деформаций, а также деформаций усадки и ползучести позволили сделать вывод о том, что деформативные свойства шлакобетона также можно приравнять к свойствам тяжелого бетона на щебне из природных материалов.
Замена природных заполнителей топливным гранулированным шлаком снижает расход цемента за счет улучшения гранулометрии смеси заполнителей, а также упрочнения контактной зоны между шлаком и цементным камнем, обес-
80
печивая снижение общих энергетических и трудовых затрат на единицу продукции. Расход цемента снижается на 4…6% на 1 м3 бетона. Экономический эффект зависит от стоимости шлака и природных заполнителей в конкретных условиях производства.
К настоящему времени накоплен определенный опыт применения гранулированных топливных шлаков в качестве заполнителей бетона, Большинство из них пригодно для приготовления бетонов различных классов и назначения.
4.8 Вспученный перлит Вспученный перлит — материал, получаемый вспучиванием при обжиге
подготовленных зерен из вулканических водосодержащих пород (перлит, обсидиан, витрофир и др.).
Вперлите содержится около 1...2% (иногда больше) связанной воды. При обжиге (1000...1250 °С) перлит размягчается и под давлением паров высвобождаемой воды сильно вспучивается. Коэффициент вспучивания — до 10...12. Чем он больше, тем меньше расход сырья на единицу объема продукции. Поэтому многие предприятия, производящие легкий вспученный перлит, работают на привозном сырье с умеренной себестоимостью продукции. Однако если коэффициент вспучивания меньше, удельные затраты на перевозку сырья увеличиваются и себестоимость продукции возрастает.
Всоответствии с ГОСТ 10832—83 «Песок и щебень перлитовые вспученные» предусматриваются марки по насыпной плотности для песка 75...500, для щебня — 200...500. Прочность щебня при сдавливании в цилиндре для указанных марок должна быть не менее 0,15... 0,9 МПа.
Вспученный перлит отличается от других пористых заполнителей высоким водопоглощением, которое тем больше, чем больше степень вспучивания.
Встандарте водопоглощение щебня ограничивается: для марки 500 — не бо-
лее 30%, для марки 400…50%, для марки 300…75%, для марки 250…100%,
для марки 200…125% по массе.
Вотличие от других пористых заполнителей мелкие фракции вспученного перлита легче крупных. Это объясняется особенностями вспучивания стекловидных пород по сравнению, например, с глинистыми. Так; при производстве керамзита мелкие глиняные гранулы (до 5 мм) часто совсем не вспучиваются, так как еще до размягчения теряют все образующиеся при обжиге газы. Перлитовая же стекловидная порода удерживает газы, и чем лучше она прогревается в мелких гранулах, тем интенсивнее вспучивается.
4.8.1 Технология производства перлитового песка и щебня
Технология производства вспученного перлита включает дробление исходной породы (до 1...2 мм при производстве песка и до 5...10 мм при производстве щебня) и сортировку. Перед обжигом сырье в ряде случаев рекомендуется подвергать предварительной термической обработке в сушильном барабане или малой вращающейся печи при температуре 250...450°С в течение нескольких минут. При этом удаляется свободная и слабосвязанная вода, в дальнейшем зерна породы могут при обжиге выдержать более высокую темпе-
81
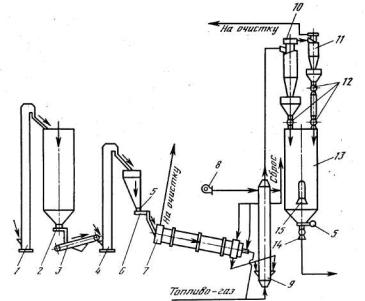
ратуру, не растрескиваясь. Остаточной, трудноудаляемой воды в зернах вполне достаточно для бурного вспучивания при температуре до 1250°С.
Для получения вспученного перлита используют вертикальные (шахтные) и вращающиеся печи, а также печи кипящего слоя. Выбор конструкции печи определяется размером обжигаемых зерен, требуемыми свойствами заполнителя и запланированной производительностью.
При производстве вспученного перлитового песка (рисунок 28) применяют шахтные печи. Печь представляет собой вертикальный футерованный изнутри цилиндр с конической нижней частью. Поток горячих газов от сжигания топлива направляется снизу вверх. Поскольку площадь сечения конической части печи с подъемом увеличивается, скорость газового потока соответственно уменьшается. Через загрузочные отверстия в верхнюю цилиндрическую часть печи подается дробленая перлитовая порода и свободно падает вниз, пока в конической части не подхватывается восходящим потоком горячих газов. Зерна породы, витая в горячей газовой струе, вспучиваются. При этом парусность их резко увеличивается, и они увлекаются газовым потоком вверх, выносятся из печи и затем осаждаются в циклонах.
1 — элеватор ленточный для сырья; 2 — питатель тарельчатый; 3 — конвейер ленточный передвижной; 4 — элеватор ленточный; 5 — затвор шиберный реечный; 6 — питатель дисковый;
7— печь термоподготовки СМТ-178; 8 — вентилятор дутьевой, 9 — печь вспучивания вертикальная (шахтная) СМТ-177; 10, 11 — циклоны; 12 — затвор-питатель;
13 — бункер готового продукта; 14 — питатель ячейковый; 15 — затвор челюстной
Рисунок 28 - Технологическая схема производства перлитового песка обжигом в вертикальной печи
Технология производства вспученного перлитового щебня и песка (рису-
нок 29) предусматривает термическую обработку сырья во вращающихся пе-
82

чах. Легкие мелкие фракции песка вспучиваются в основном во взвешенном состоянии и уносятся из печи потоком отходящих газов (с последующим осаждением в циклонах).
Более крупные фракции, не увлекаемые газовым потоком, вспучиваются на футеровке печи и выгружаются. Для ускорения нагрева материала используют принцип прямотока, т. е. факел горящего топлива и поток газов направляют не навстречу потоку обжигаемого материала (как при получении керамзита), а в том же направлении — по наклону печи.
Для получения вспученного перлита с зернами размером до 10 мм, в основном крупного песка, обжиг целесообразно производить в двухзонных печах кипящего слоя.
Применяют вспученный перлит в качестве теплоизоляционного материала и заполнителя для особо легких теплоизоляционных и конструкционнотеплоизоляционных, а также жаростойких бетонов.
1 — загрузочное устройство для сырья; 2 — элеватор ленточный; 3 — силос сырья; 4 — питатель тарельчатый; 5 — конвейер ленточный пе-
редвижной; 6 — элеватор ленточный; 7 — затвор реечный шиберный; 8 — питатель дисковый; 9 — печь термоподготовки СМТ-178;
10 — печь вспучивания вращающаяся СМТ-179; 11 — дутьевой вентилятор; 12 — циклон; 13 — осадитель;
14 — сито-бурат; 15 - затвор-питатель; 16 — силосы готовой продукции; 17
— затвор челюстной; 18 — питатель дисковый (производство щебня); 19 — питатель ячейковый (производство песка)
Рисунок 29 - Технологическая схема производства перлитовых щебня и песка обжигом во вращающейся печи
83
Вряде случаев перлитовый песок используют как мелкий заполнитель в других видах легкого бетона: керамзитоперлитобетоне, шлакопемзоперлитобетоне и других, в которых крупный заполнитель — керамзит, шлаковая пемза, а мелкий — вспученный перлит.
Опыт показал, что при этом насыпная плотность перлитового песка должна соответствовать М 200 или более, а содержание в нем фракции мельче 0,16 мм не должно превышать 10% по объему.
Всвязи с большим водопоглощением вспученного перлита и замедленной влагоотдачей представляет интерес его гидрофобизация растворами ГКЖ10 и ГКЖ-11, при которой значительно уменьшается водопоглощение и создаются условия для более эффективного использования вспученного перлита.
84

5 НОВЫЕ ТЕХНОЛОГИИ В ПРОИЗВОДСТВЕ ЗАПОЛНИТЕЛЕЙ
5.1 Безобжиговый искусственный заполнитель для бетонов на основе зол гидроудаления ТЭС
Высокая себестоимость изготовления керамзитового гравия диктует необходимость получения более дешевых легких заполнителей для бетонов. Перспективным представляется изготовление безобжигового искусственного заполнителя (БИЗ), получаемого путем грануляции сырьевой смеси на основе зол ТЭС. БИЗ — экологически чистый материал, отвечающий требованиям нормативных документов. Плотность БИЗ составляет 600…1100 кг/м и зависит от плотности используемой для его приготовления золы (рисунок 30).
Насыпная плотность золы, кг/м3
Рисунок 30 - Зависимость плотности БИЗ от насыпной плотности золы
Марка по прочности БИЗ составляет П15...ПЗОО. БИЗ применяется для изготовления бетонов пониженной средней плотности (1700…1900 кг/м3), классов по прочности при сжатии до В22,5, а также в качестве теплоизоляционных засыпок. Производство БИЗ требует незначительных энергетических затрат, отличается простотой технологии и наличием широкой сырьевой базы. Сырьевая смесь приготовляется путем совместного перемешивания золы гидроудаления, вяжущего, воды затворения и, при необходимости, химических добавок.
Большинство тепловых электростанций осуществляют совместное гидроудаление золы и шлака, в этом случае в отвалах образуется смесь нестабильного состава. Учитывая это обстоятельство, следует обратить внимание на требования по качеству золы, используемой для изготовления БИЗ. Отвальная зола гидроудаления ТЭС должна соответствовать требованиям ГОСТ 25592, предъявляемым к золошлаковым смесям класса "Б" вида "II" (Смесь золошлаковая для легкого неармированного бетона) и следующим дополнительным требованиям:
—содержание зерен размером свыше 5 мм — не более 5 масс.%.
—максимальный размер зерен — не более 10 мм;
—содержание зерен, проходящих через сито с сеткой № 014, — не менее
40 масс.%;
85
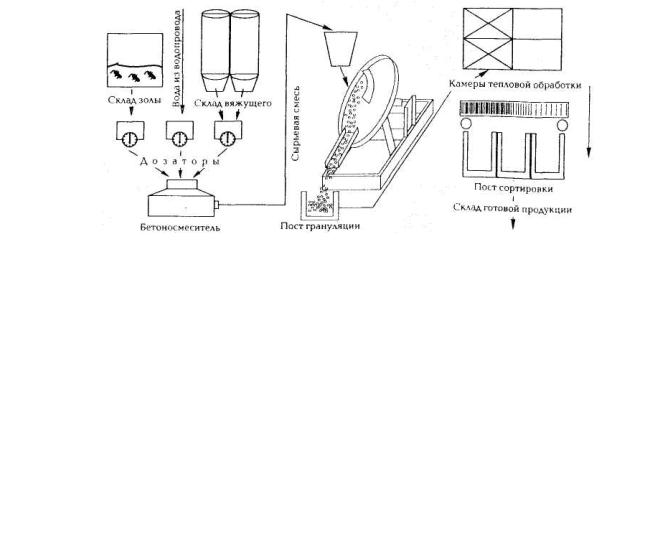
— влажность не более 15 масс. %.
В качестве вяжущего материала для изготовления БИЗ можно применять портландцемент, шлакопортландцемент и их разновидности, а также вяжущее низкой водопотребности (ВНВ). Для ускорения процессов твердения, снижения продолжительности и температуры ТВО могут применяться химические добавки, удовлетворяющие требованиям действующих стандартов или технических условий.
Изготовление БИЗ осуществляется с применением типового оборудования бетоносмесительных узлов и гранулятора тарельчатого типа. Технология изготовления БИЗ включает в себя следующие операции:
—приготовление сырьевой смеси;
—изготовление сырцовых гранул;
—тепловая обработка сырцовых гранул или твердение их в нормальных условиях;
—фракционирование БИЗ.
Принципиальная технологическая схема изготовления БИЗ приведена на рисунке 31.
Рисунок 31 - Принципиальная технологическая схема изготовления БИЗ
Используемую для производства БИЗ сырьевую смесь следует приготовлять в бетоносмесителях с горизонтальным валом, обеспечивающих качественное перемешивание и высокую однородность смеси, а также предотвращающих ее комкование в процессе перемешивания. Приготовленная сырьевая смесь подается на гранулятор, где происходит ее грануляция (закатка) в сырцовые гранулы с последующим их твердением.
Промышленный гранулятор тарельчатого типа при непрерывной технологии производства позволяет изготовлять до 3 м3/ч БИЗ.
Применение зол гидроудаления для производства БИЗ дает возможность эффективно использовать отходы производства ТЭС, а также существенно сократить затраты на создание, расширение и эксплуатацию золоотвалов и улучшить экологическую обстановку в районе расположения ТЭС. Использование
86
БИЗ в качестве крупного заполнителя для различных видов бетонов при изготовлении бетонных и железобетонных конструкций позволит:
—уменьшить в 2…2,5 раза раcход топлива и электроэнергии производство 1 м3 БИЗ по сравнению с керамзитовым гравием;
—расширить сырьевую базу для получения легких заполнителей, что даст возможность организовать производство БИЗ в любом районе, где имеется зола гидроудаления ТЭС, но отсутствует местное сырье для получения традиционных заполнителей;
—снизить себестоимость 1 м3 заполнителя на 26…40% по сравнению с керамзитовым гравием.
5.2 Совместное производство керамзитового гравия и песка во вращающихся печах
При традиционном обжиге гранул полуфабриката керамзита во вращающихся печах попутно получается 2…3, редко 5% обжигового песка. При этом обжиг ведется при максимально возможной температуре, устанавливаемой для гранул полуфабриката основного размера (10…15 мм). Уменьшение размера гранул или увеличение содержания крошки в полуфабрикате неизбежно требует снижения температуры обжига, что приводит к существенному утяжелению керамзитового гравия.
Совместный обжиг разнофракционного полуфабриката (гранулы, крошка) во вращающихся печах становится возможным только при использовании метода селективной интенсификации теплопереноса.
Основная часть теплоты (85…95%), получаемой при сгорании топлива в процессе обжига во вращающейся печи, передается лучистым теплопереносом, а остальная конвекцией и теплопроводностью. Непосредственно материальному слою через футеровку передается 65…75 % теплоты лучистого теплопереноса и теплопроводности. Поэтому в процессе нагрева ведущее место занимает излучение, далее следует конвекция и теплопроводность.
При температуре обжига, устанавливаемой при сгорании топлива и лимитируемой конвективной составляющей теплопереноса (слипание гранул, крошки, спекообразование) для интенсификации нагрева разнофракционного полуфабриката, целесообразно использовать теплопроводность.
В процессе производства теплопроводность глинистого сырья и соответственно, гранул полуфабриката изменяется в весьма широких пределах и зависит от множества факторов как природного, так и технологического характера. Наиболее распространенной оценкой коэффициента теплопроводности (λ) сухого глинистого сырья (W=0%) является 0,155...0,163 Вт/(м·єС). Это же сырье при нормальной формовочной влажности (WH = 24…25% ) имеет λ = 0, 423...0,465 Вт/мград. При водонасыщении его этот показатель может возрасти в 6...8 раз. При увеличении кажущейся плотности (1,05→2,0 г/см3) λ возрастает (0,239→1,131 Вт/(м·єС). Совместное влияние влажности и давления (ленточный пресс, дырчатые вальцы) на теплопроводность глинистого сырья незначительно и не превышает 10%.
87
При нагревании в глинистом сырье происходят сложные физикохимические процессы. Продукты этих процессов имеют теплопроводность, существенно отличающуюся от одноименного показателя исходного сырья. Так, при сушке, термоподготовке во вращающейся печи его теплопроводность уменьшается. В следующей зоне она возрастает, достигая максимального значения 2,208 Вт/(м·єС). При вспучивании λ резко снижается из-за быстрого роста пористости и большого содержания стекловидной фазы в гранулах керамзита.
Для получения мелкого полуфабриката из пластичного глинистого сырья или по порошковой технологии имеются отработанные в заводских условиях технологические приемы его подготовки.
Основные технико-экономические показатели туннельно-шнековой печи приведены в таблице 24, в которой для сравнения даны одноименные показатели, как наиболее распространенной среди коротких вращающихся печей - 2,3x22 м. В отличие от традиционной вращающейся печи (2,3x22 м) равной производительности, туннельно-шнековая печь имеет в 2,0 раза меньшую потребность в огнеупорных материалах, т.е. обеспечивается экономия 35...40 т огнеупоров. Футеровка печи не подвергается абразивному износу и механическому воздействию при работе, что имеет место во вращающихся печах. Соответственно улучшаются условия эксплуатации футеровки, что обеспечивает экономию 34 т огнеупоров за счет сокращения объемов текущего и капитального ремонтов. Снижается потребность в стали (бандаж, обечайки, венец) на 25...27 т на одну печь.
Вконструкции печи используются новые конструкционные материалы - жаростойкие стали и жаростойкие огнеупорные материалы. Отечественный и зарубежный опыт показывает, что применение этих материалов в печах строительной керамики дает высокую экономическую эффективность. Например, переоборудование туннельных печей на роликовые на 50% снижает расход энергии.
Втуннельно-шнековой печи жаростойкие стали используются для изготовления транспортирующих шнеков. Действие известных недостатков шнековых транспортеров - дробление, измельчение транспортируемого материала и абразивный износ существенно снижено за счет изменения характера транспортирования и соответственно времени контакта материала со шнеком. В частности, шаг винта предусматривает предельно возможную величину, а скорость его вращения – минимально возможную.
Отечественный производственный опыт эксплуатации роликовых печей, как технического аналога туннельно-шнековой, показывает, что расход жаростойкой стали не превышает 6% от массы роликов, установленных на печи. На 1 м роликовой печи устанавливаются ролики массой 240...250 кг из жаростойкой стали, в туннельно-шнековой — 190...200 кг.
Иными словами, потребность в жаростойкой стали для туннельношнековой печи составит 28% от потребности для роликовой, а расход стали не превысит 6%.
Предварительная оценка технико-экономической эффективности применения туннельно-шнековой печи в сравнении с вращающейся печью (таблица
88