
БТ / ZAPOLNITELI BETONA
.pdf
В металлургических шлаках содержится сера, вызывающая коррозию арматурной стали. В щебне из доменного шлака ее содержание не должно превышать 2,5% по массе. Наличие серы необходимо учитывать в производстве преднапряженных железобетонных конструкций, где возможность использования шлакового щебня должна быть обоснована специальными исследованиями.
Наряду с плотными отвальными шлаками для производства щебня используют пористые шлаки, образуемые из расплавов с большим газонасыщением, вспучиванием пузырьками выделяющихся газов. Прочность пористых отвальных шлаков 2,5…40 МПа; средняя плотность в куске составляет 400…1600 кг/м3, что позволяет обеспечить насыпную плотность щебня 800 кг/м3 и менее и применять их для производства легких бетонов.
Физико-механические свойства шлакового щебня изменяются в более широком интервале, чем щебня из горных пород (таблица 17), что обусловлено колебаниями качества сырьевых материалов и технологических параметров.
Таблица 17 - Физико-механическиесвойствашлаковогощебнянаразличных шлаках
|
Истинная |
Средняя |
Водо- |
Предел |
Показатель |
|
Вид шлака или |
поглоще- |
прочности |
||||
плотность, |
плотность, |
дроби- |
||||
породы |
кг/м3 |
кг/м3 |
ние по |
при сжатии, |
мости, % |
|
|
|
|
массе, % |
МПа |
|
|
Гранит |
2650 |
2650 |
0,2 |
120 |
11 |
|
Шлак: |
|
|
|
|
|
|
доменный плотный |
2950 |
2820 |
1,5 |
104 |
19 |
|
пористый |
2940 |
2300 |
7,3 |
62 |
44 |
|
|
|
|
|
|
|
|
мартеновский |
3200 |
3030 |
2,3 |
110 |
17 |
|
конвертерный |
3100 |
2800 |
4,0 |
76 |
39 |
|
медеплавильный |
3500 |
3430 |
0,4 |
140 |
6 |
|
фосфорный |
2950 |
2850 |
0,9 |
135 |
12 |
Шлаковый щебень применяется не только как заполнитель цементных бетонов, но также в дорожном строительстве для укрепления оснований и устройства асфальтобетонных покрытий. В зависимости от структурных особенностей, сопротивления истиранию и дробимости шлаковый щебень делится на марки:
Таблица 18 – Марки шлакового щебня по истираемости
Марка щебня по истираемости |
ИI |
ИII |
ИIII |
ИIV |
Потеря массы при испытании, % |
<25 |
25…35 |
35…45 |
45…60 |
Марка щебня из металлургического шлака как заполнителя асфальтовых бетонов зависит от вида смесей. Она должна быть, например, для смесей марки:
—для горячих и теплых асфальтобетонов типов А, Б и В соответственно 1200, 1000 и 800;
—холодных— типовБх иВх — 800 и600;
—пористых— 800.
Шлакоминеральные смеси. К шлакоминеральным смесям относятся каменные материалы, укрепленные гранулированным доменным шлаком и предназна-
69
ченные для устройства оснований автомобильных дорог. Для активизации шлаков и твердения смесей в их состав вводят добавки гашеной извести (1…3%) или портландцемента (3…5%). Шлакоминеральные смеси, активированные гашеной известью, медленно схватываются и твердеют, что позволяет делать разрывы в несколько суток между приготовлением смеси и ее укладкой в основания. Шлакоминеральные смеси, активированные цементом, схватываются быстрее и позволяют вести строительные работы в течение 6…8 ч.
Шлакоминеральные смеси, уложенные в слое основания, практически не требуют специального ухода и позволяют открыть движение сразу после уплотнения. Они допускают укладку асфальтобетонных покрытий сразу после уплотнения основания. При устройстве оснований из шлакоминеральных смесей на дорогах высших категорий можно использовать не только местные малопрочные каменные материалы, но и песчано-гравийные смеси.
Шлакоминеральное основание более жестко по сравнению с битумоминеральным, однако оно гораздо гибче и деформативнее оснований, устроенных из цементированныхматериалов, втомчислеизбетона.
По трещиностойкости шлакоминеральное основание уступает битумоминеральному, и поперечные трещины в нем возникают при перепадах температур. В южных районах и при достаточно толстых слоях асфальтобетонного покрытия трещинообразования в шлакоминеральном основании можно избежать.
В дорожно-строительной практике хорошо зарекомендовали себя составы шлакоминеральных смесей, в которых расход гранулированного шлака изменяется от 10 до 20%.
Минеральная часть смесей подбирается по кривым плотных смесей, рекомендованным для битумоминеральных смесей. Физико-механические свойства шлакоминеральныхсмесейприведенывтаблице19.
Шлакоминеральные смеси, затворенные 8…9% воды, хорошо перемешиваются и легко уплотняются. Асфальтобетонное покрытие, уложенное на шлакоминеральное основание, хорошо объединяется с ним.
Дорожное строительство является наиболее материалоемкой областью применения шлакового щебня. Требования, предъявляемые к шлаковому щебню, зависят от слоя дорожной одежды, где он используется. Так, материал, укладываемый в подстилающий слой, должен обладать водоустойчивостью и морозостойкостью, щебень для оснований - шероховатой поверхностью. В утрамбованном состоянии материал для строительства дорог должен обладать высокой прочностью на сдвиг. Для обеспечения движения с установленной скоростью покрытия должны иметь высокую износостойкость и сохранять ровность. Одним из основных требований к щебню для дорожного строительства является его способность не дробиться при укладке и уплотнении.
В дорожных насыпях и подстилающих слоях применяют щебень из несортированных отвальных шлаков. Нефракционированный шлаковый щебень пригоден также для устройства упорных призм плотин и дамб, укрепления их откосов, подверженных волновым воздействиям. Щебень из доменных и сталеплавильных шлаков легко укатывается в основаниях дорог, цементируется и образует моно-
70

литный слой, особенно в смеси со щебнем из слабых известняковых пород. Щебень из мартеновских шлаков успешно применяется для расклинивания оснований из гранитного щебня, плохо поддающегося укатке.
Таблица 19 - Физико-механическиесвойствашлакоминеральныхсмесей
|
Пределпрочности |
Пределпрочности |
Пределпрочности |
|||
|
присжатииводонасы- |
присжатиипосле |
||||
Смеси |
щенныхобразцов, |
прираскалывании, |
25 цикловзамо- |
|||
МПаввозрасте |
МПаввозрасте |
раживания— от- |
||||
|
|
|
|
|
|
таиванияввозрас- |
|
|
|
|
|
|
|
|
7 сут |
28 сут |
60 сут |
28 сут |
60 сут |
те28сут, МПа |
|
|
|
|
|
|
|
Щебеночные и гравийно- |
|
|
|
|
|
|
песчаные, шлак гранули- |
- |
0,2…0,3 |
0,5…0,6 |
- |
0,1 |
Ненормируется |
рованный 10-20% и 1— |
|
|
|
|
|
|
2% извести |
|
|
|
|
|
|
|
|
|
|
|
|
|
Щебеночные и гравийно- |
|
|
|
|
|
|
песчаные, шлак гранули- |
|
|
|
|
|
|
рованный 5-10% и це- |
0,5 |
1,0 |
|
0,2…0,3 |
|
0,8 |
мент: |
|
|
|
|
|
|
3% |
|
|
|
|
|
|
5% |
0,8 |
2,0 |
- |
0,5 |
- |
1,5 |
Песчаные, шлак гранули- |
|
|
- |
|
- |
|
рованный 10-20% и це- |
0,4 |
1,0-1,5 |
0,1-0,2 |
0,8-1,0 |
||
мент 3% |
|
|
|
|
|
|
Шлак гранулированный |
0,5 |
2,0 |
- |
0,2 |
- |
1,5 |
10% и цемент 5% |
|
|
|
|
|
|
Наиболее экономичны конструкции с использованием сталеплавильных шлаков крупностью до 40 мм. При эксплуатации модуль упругости слоев в основании медленно возрастает вследствие наращивания прочности. Применение шлаков с активизатором (хлористым кальцием) дает возможность вести дорожные работы в зимнее время. Отвальные шлаки и минеральный порошок из сталеплавильных шлаков успешно используют при приготовлении асфальтобетона для верхних слоев дорожных одежд. Асфальтобетонные покрытия со шлаковым заполнителем характеризуются высокой прочностью, устойчивостью к истиранию, большим коэффициентом сцепления, отсутствием сдвиговых деформаций. Также эти покрытия отличаются повышенным сопротивлением ударным нагрузкам при положительных и отрицательных температурах, большей теплостойкостью, чем асфальтобетоны на природных минеральных заполнителях. При длительном контакте с водой поры шлакового материала прорастают кристаллогидратными новообразованиями, что предотвращает в последующем доступ в них водыиприводиткповышениюморозостойкостиасфальтобетона.
Недостатком шлаковых асфальтобетонных смесей является их высокая средняя плотность, на 15…25% превышающая плотность смесей из природных материалов.
71

Шлаковый наполнитель. Из сталеплавильных шлаков получают высококачественный минеральный порошок, являющийся важным структурообразующим компонентом (наполнителем) асфальтобетона. На долю минерального порошка приходится 90…95% суммарной поверхности минеральных зерен, входящих в состав асфальтобетона. Основное его назначение — это перевод битума в пленочное состояние, а также заполнение пор между крупными частицами, в результате чего повышаются плотность и прочность асфальтобетона. Минеральному порошку из сталеплавильных шлаков свойственна более развитая поверхность, чем у порошка из карбонатных материалов и, как следствие, более высокое набухание его в смеси е битумом.
Требования к минеральному порошку из измельченных основных металлургических шлаков приведены в таблице 20.
Таблица 20 - Требованиякминеральномупорошкудляасфальтовыхбетонов наосновеметаллургических шлаков
|
Показатель |
Нормы |
|
|
|
Зерновой состав, % по массе, не менее: |
|
|
|
|
|
мельче 1,25 мм |
100 |
|
|
|
|
» |
0,315 мм |
90 |
» |
0,071мм |
70 |
|
|
|
Показатель битумоемкости, г, не более |
100 |
|
|
|
|
Содержание водорастворимых соединений, % по массе, не |
Не нормируются |
|
|
|
|
Пористость, % по объему, не более |
40 |
|
|
|
|
Влажность, % по массе, не более |
1 |
|
|
|
|
Набухание образцов из смеси минерального порошка с би- |
2,5 |
|
тумом, % по объему, не более |
|
|
|
|
|
Содержание оксидов щелочных материалов (Na20+ К20), % по |
Не нормируются |
|
массе, не более |
|
|
Потери при прокаливании, % по массе, не более |
-«- |
|
|
|
|
Коэффициент водостойкости образцов из смеси порошка с |
0,7 |
|
битумом, не более |
|
|
|
|
|
Содержание свободного оксида кальция СаО, % по массе |
0 |
Минеральный порошок повышает прочность асфальтобетона, но вместе с тем увеличивает его хрупкость, поэтому его содержание в смеси должно быть предельно минимальным, достаточным лишь для придания асфальтобетону нормативной плотности и прочности. Повышение массовой доли минерального порошка в смеси сверх необходимого минимума понижает трещиностойкость покрытий и резко снижает их сдвигоустойчивость.
Тонкоизмельченные шлаки, обладающие гидравлической активностью, т. е. способностью химически связывать Са(ОН)2 уже при нормальной температуре, являются эффективными наполнителями (микронаполнителями) в цементных бетонах.
Цементный камень, по определению В.Н. Юнга, можно считать «микробетоном». Значительная часть цементных зерен гидратируется не полностью и вы-
72
полняет роль своеобразных наполнителей цементного камня. Глубина гидратации отдельных клинкерных минералов не одинакова и, как следует из данных Ю.М. Бутта (таблица 21), даже в 6 мес. не превышает для наиболее активного минерала C3S 15 мкм, а наименее активного C2S — 2,7 мкм.
Многочисленными исследованиями показано, что кроме «естественных» наполнителей, которыми служат ядра большей части клинкерных частиц, в цементы и бетонные смеси могут быть с успехом введены «искусственные» наполнители — тонкомолотые, практически не растворимые в воде неорганические вещества, состоящие из частиц размером менее 150 мкм.
Таблица 21 - Глубинагидратацииклинкерныхматериалов, мкм
Минерал |
|
|
Гидратация в течение |
|
|
||
|
|
|
|
|
|
|
|
|
3 сут |
7 сут |
|
28 сут |
|
3 мес |
6 мес |
C3S |
3,5 |
4,7 |
|
7,9 |
|
14,5 |
15,0 |
|
|
|
|
|
|
|
|
C2S |
0,6 |
0,9 |
|
1,0 |
|
2,6 |
2,7 |
С3А |
10,7 |
10,4 |
|
11,2 |
|
13,8 |
14,5 |
C4AF |
7,7 |
8,0 |
|
8,4 |
|
12,2 |
13,2 |
Обладая высокой удельной поверхностью, наполнители, наряду с прямым химическим воздействием, влияют на физико-химические процессы у поверхности раздела фаз. В соответствии с учением Гиббса—Фольмера энергия образования зародышей кристаллов значительно уменьшается при наличии центров кристаллизации, которыми могут служить частицы наполнителя.
Уменьшая радиус зерен наполнителя и поверхностное натяжение на границе «кристалл — жидкая фаза», можно значительно повысить вероятность зарождения новой фазы. При оптимальной концентрации и дисперсности наполнителя образуется мелкозернистая структура связующего, что благоприятно отражается на технических свойствах искусственного камня. При введении наполнителя в систему «цемент — вода» скорость твердения и прочность возрастают до тех пор, пока все зерна наполнителя остаются окруженными продуктами гидратации. Для кремнеземистых частиц степень наполнения можно определить по количеству СаО, которое может связать 1 г наполнителя. Степень наполнения, рассчитанная таким образом, колеблется от 5 до 10% массы цемента.
При избытке наполнителя с высокой дисперсностью зерен возникают участки самонапряжения, что по мере роста кристаллов может привести к образованию трещин и другим нарушениям однородности микроструктуры.
Наполнитель должен обеспечить максимальную адгезионную прочность между связующими и заполнителем и когезионную прочность связующего, минимальную пустотность за счет вытеснения цементного теста в контактную зону и общую пустотность бетона в целом. При этом степень наполнения должна быть такой, чтобы на начальной стадии формирования структуры были обеспечены заданные реологические параметры смеси.
73
Легкие шлаковые заполнители. Гранулированный шлак применяют в бето-
нах как мелкий заполнитель. По зерновому составу он соответствует крупному песку. Примерно 50% его массы составляют зерна крупностью более 2,5 мм. Насыпная плотность гранулированного шлака зависит от свойств шлакового расплава и технологии грануляции и составляет 600…1200 кг/м3. Гранулы, образующиеся при быстром охлаждении шлакового расплава водой или паровоздушной смесью, характеризуются высоким содержанием стекловидной фазы и пористостью.
Гранулированный шлак является эффективным заполнителем обычных и мелкозернистых бетонов, может служить укрупняющей добавкой для обогащения природных мелких песков. Пористые разновидности гранулированного шлака применяют как заполнители легких бетонов.
4.7 Заполнители из топливных зол и шлаков
Золошлаковое сырье может применяться для изготовления заполнителей как тяжелых, так и легких бетонов. Пористыми заполнителями для легких бетонов служат: шлаки от сжигания антрацита, каменного и бурого углей, торфа и сланцев; золы, щебень и песок из топливных шлаков, аглопорит на основе золы ТЭС, зольный обжиговый и безобжиговый гравий, глинозольный керамзит.
Золошлаковыезаполнители. Свойствазолишлаковзависят отспособа сжигания и вида топлива. Оптимальную пористую структуру антрацитовых и каменноугольных шлаков получают при кусковом сжигании, а у шлаков бурого угля
— при пылевидном. Недостатком пылевидного сжигания или переработки в газогенераторах антрацита и каменных углей является то, что эти процессы приводят к чрезмерному спеканию и получению в результате этого плотных и тяжелых заполнителей.
По зерновому составу шлак представляет собой механическую смесь зерен крупностью 0,14…30 мм с отдельными включениями более крупных частиц, поэтому ее можно рассматривать как естественную смесь мелкого и крупного заполнителей. В связи с этим шлаки ТЭС целесообразно применять в легких и тяжелых бетонах в качестве основного заполнителя, для частичной замены щебня (20…50%), а также для улучшения гранулометрического состава песков.
Все топливные шлаки можно классифицировать на основные, кислые и нейтральные. Шлаки каменных углей в основном кислые. Шлаки некоторых бурых углей и сланцев, содержащие до 40% СаО и повышенное количество оксидов железа, относятся к основным. Наименее кислыми являются антрацитовые шлаки.
Вредными компонентами шлаков, вызывающими при повышенном количестве разрушение бетона, являются сульфаты и сульфиды. Общее содержание сернокислых и сернистых соединений в пересчете на SО3 в топливных шлаках не должно превышать 3% массы, в том числе не более 1 % водорастворимых сульфатов и 1 % сульфидов. Недопустимо также присутствие в шлаках ТЭС свободного оксида кальция, гашение которого в затвердевшем бетоне может послужить причиной его разрушения.
74
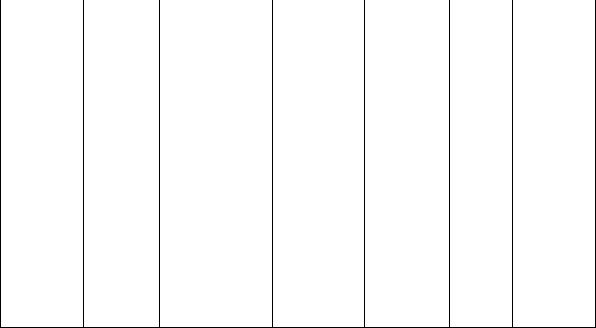
Так же, как и металлургические, шлаки ТЭС должны быть устойчивы против силикатного и железистого распада. Стойкость против силикатного распада определяют пропариванием и автоклавной обработкой пористого щебня, а железистого — 30-дневным выдерживанием в дистиллированной воде. Потеря массы испытываемых проб не должна превышать 5%. Для предотвращения распада топливные шлаки рекомендуется применять после длительного (3…6 месяцев) вылеживания в отвалах, в результате чего в них гасится свободный оксид кальция, частично выщелачиваются растворимые соли и окисляются топливные остатки. При применении шлаков в бетонах целесообразно их обогащать, отсеивая мелкие фракции, содержащие наибольшее количество несгоревшего угля и других вредных примесей.
Насыпная плотность топливных шлаков составляет 600…1000 кг/м3, средняя плотность зерен — 1500…2000 кг/м3. Пористость шлаков обычно колеблется от 40 до 60%, морозостойкость достигает до 50 циклов и более. Оптимальные структуру и физико-механические свойства имеют антрацитовые шлаки, буроугольные — менее применимы.
В отличие от щебня из природного камня шлаковый щебень практически не содержит лещадных и игловатых зерен, глинистых и других вредных примесей, и при использовании в качестве заполнителя в бетонах такой щебень, как свидетельствуют результаты исследований, обеспечивает прочностные характеристики до 30 МПа(таблица22).
Таблица 22 - Физико-механические свойства бетонов на топливных шлаках
|
|
Отношение |
Предел |
Модуль |
Сцеп- |
Морозо- |
|
Вид бето- |
Класс бе- |
призменной |
прочности |
ление с |
стой-кость |
||
на |
тона |
прочности к |
при изгибе, |
упругости |
армату- |
(число |
|
|
|
кубиковой |
МПа |
МПа |
рой, |
циклов) |
|
|
|
|
МПа |
||||
Тяжелые |
|
|
|
|
|
|
|
бетоны В7,5…В2 |
0,8…0,9 |
4,5…7,5 |
18000 |
4,6…5,5 |
100…150 |
||
ρ0=2400… |
5 |
||||||
|
|
|
|
|
|||
2500 кг/м3 |
|
|
|
|
|
|
|
Мелкозер- |
|
|
|
|
|
|
|
нистые бе- |
В12,5…В |
|
|
18000…21 |
|
|
|
тоны |
0,8…0,9 |
4,0…6,0 |
2,5…3,7 |
75…100 |
|||
ρ0=2000… |
15 |
|
|
000 |
|
|
|
2200 кг/м3 |
|
|
|
|
|
|
|
Легкие бе- |
В3,5- |
|
|
|
|
|
|
тоны ρ0 = |
В12,5 |
0,85-0,88 |
3,5-3,8 |
5000-8000 |
1,5-1,7 |
25-50 |
|
1000-1800 |
|
|
|
|
|
|
Мелкий заполнитель в тяжелых и легких бетонах частично или полностью может быть заменен золой. При изготовлении конструктивнотеплоизоляционных легких бетонов классов В2,5…В7,5 зола, используемая в качестве песка, должна иметь насыпную плотность до 1100 кг/м3 и включать зерна размером менее 0,14 мм в количестве не более 90% массы. Содержание коксовых остатков в золе, полученной при сжигании каменного угля и антрацита, должно бытьнеболее12%, бурых углей — не более 5%.
75
Установлено, что на долговечность бетона при использовании зол оказывает влияние, главным образом, состав топливных остатков, стойкость которых к окислению и воздействию влаги зависит в свою очередь от минералогического состава исходного угля.
Несгоревшие частицы угля представлены, в основном, в виде остатков кокса и полукокса. Отрицательные свойства этих топливных остатков сказываются в незначительной степени, так как кокс и полукокс стойки к окислению на воздухе и поглощают мало влаги, а поэтому мало подвержены объемным изменениям при попеременном увлажнении и замораживании. Определение качественного состава остатков несгоревшего топлива дает возможность оценить целесообразность применения золы как мелкого заполнителя бетона.
В немалой степени свойства бетона зависят от влажности зол и содержания в них сернистых и сернокислых соединений. Количество последних в перерасчете на SО3 не должно превышать 3% по массе (в том числе сульфидной серы в перерасчете на SО3 не более 1%). Влажность не должна превышать 35% по массе. Для получения долговечного золобетона для армированных легкобетонных конструкций золы ТЭС должны также содержать пониженное количество глинистых частиц при повышенномсодержании стеклофазы (неменее 50…60%).
Свойства бетона в значительной степени зависят от гранулометрического состава заполнителей. Оптимальным для легких бетонов является соотношение 1:1 между крупной (более 0,3 мм) и мелкой (менее 0,08 мм) фракциями золы. Хорошие прочностные показатели бетона достигаются при использовании зол, у которых соотношение между крупной и мелкой фракциями не превышает 1:2,5, а содержание частиц средней фракции составляет 50%.
Применение в бетонах золы-уноса позволяет заменять как часть песка, так и часть цемента. Количество вводимой в состав бетона золы может достигать 150…250 кг/м3 и более. При выборе возможного содержания золы в бетоне следует учитывать воздействие золы на свойства бетонной смеси. В зависимости от содержания золы влияние ее на водопотребность может быть несущественным или значительным. Так, если введение в состав бетона до 70…90 кг золы дисперсностью 3000…4500 см2/г практически не сказывается на водопотребности бетонной смеси, то дальнейшее увеличение содержания золы вплоть до 300 кг на 1 м3 бетона приводит к увеличению водопотребности бетонной смеси на 5…6% на каждые 50 кг дополнительно вводимой золы.
Золобетоны можно получать с широким диапазоном свойств: по прочности на сжатие — 0,5…40 МПа, средней плотности — от особо легких (ρ0 < 1000 кг/м3) до тяжелых (ρ0 = 1800…2000 кг/м3). Их получают как на портландцементе, так и на бесклинкерных вяжущих в условиях обычного и автоклавного твердения. Плотный золобетон характеризуется высокими значениями прочности на изгиб и деформативных характеристик (предельной сжимаемости и ползучести).
76
Таблица23 - Средняяплотностьимодульупругостизолобетонаразличныхклассов
Класс по прочности |
Средняя плотность, кг/м3 |
Модуль упругости, МПа |
на сжатие, МПа |
|
|
1,5 |
1150...1500 |
— |
2,5 |
1200...1550 |
3,0·103 |
3,5 |
1250...1600 |
3,5·103 |
5 |
1350...1700 |
5,5·103 |
7,5 |
1450...1800 |
7·103 |
12,5 |
1650...1900 |
9·103 |
15 |
1850...2000 |
1·104 |
Значения средней плотности и модуля упругости для характерных классов плотного золобетона даны в таблице 23.
Недостатками плотных золобетонов являются значительное водопоглощение, а также усадка, которая при твердении образцов на воздухе составляет до 2...3 мм/м. Для уменьшения водопоглощения рекомендуется вводить в смесь тонкомолотые добавки, снижающие пористость золобетона, например гранулированный шлак. Усадка снижается при автоклавной обработке и введении в
массу до 30% крупных пористых заполнителей или песка, а также применением жестких смесей.
На приготовление золобетона классов В2,5…В12,5 со средней плотностью 1000…1600 кг/м3 при безавтоклавном твердении расходуется 200…400 кг/м3 цемента, в зависимости от свойств исходных компонентов и технологии изготовления изделий. Запаривание золобетонных изделий в автоклавах позволяет в 1,5…2 раза снизить расход вяжущего и частично (или полностью) заменить цемент известью.
Более широкое применение находит зола как мелкий заполнитель в производстве керамзитобетонов. Для обеспечения плотной структуры этих материалов в песчаной фракции должно содержаться 40–50% по массе частиц размером менее 0,15 мм. В связи с дефицитом керамзитового песка многие заводы при изготовлении конструктивно-теплоизоляционных легких бетонов применяют обычный кварцевый песок, что приводит к утяжелению керамзитобетонов до 1400…1600 кг/м3 и соответственно к снижению термического сопротивления стен. Применение золы в керамзитобетонах в количестве 180…200 кг/м3, а для однофракционного керамзита и в больших количествах, улучшает технологические свойства легкобетонныхсмесейиспособствуетполучению плотной структуры бетона.
Полная замена мелкого заполнителя золой наиболее целесообразна в конст- руктивно-теплоизоляционных легких бетонах. Оптимальное содержание золы в конструктивно-теплоизоляционном керамзитобетоне составляет 300…450 кг/м3. Дальнейшее увеличение ее содержания повышает среднюю плотность легкого бетона. При изготовлении легких конструктивных бетонов добавка золы в количестве до 100 кг на 1 м3 бетона может служить микронаполнителем.
Возможно применение в бетонах рядовых классов наряду с золой и шлаками и золошлаковой смеси отвалов ТЭС. Золошлаковую смесь целесообразно использовать в качестве основного заполнителя бетонов, для частичной замены
77
щебня (20…50%) и песка (40…100%), а также для улучшения гранулометрии мелких песков.
Производственный опыт показал, что применение золошлаковых смесей в качестве основного заполнителя бетона более экономично, поскольку шлаковые фракции, заменяя часть мелкого песка и щебня, улучшают зерновой состав, а пылевидная зола, играя роль активного микронаполнителя, улучшает пластичность бетонной смеси, повышает коэффициент эффективности использования цемента. Это позволяет применить значительную часть золошлакового сырья, сосредоточенного в отвалах.
При введении золошлаковых смесей в бетоны применяются смеси с довольно широкими границами изменения гранулометрии. Однако оптимальными являются смеси, в состав которых входит 16…30% пылевидной золы–уноса. Общее содержание золошлаковой смеси должно быть в пределах 230…330 кг на 1 м3 бетона.
При прочих равных условиях средняя плотность бетона на золошлаковой смеси на 130…150 кг/м3 меньше, чем на гранитном щебне. Для бетона, например, на золошлаковой смеси, полученной при сжигании донецких углей, характерны следующие физико-механические свойства: прочность при сжатии – до 35 МПа; растяжении – 2,3 МПа; модуль упругости – 24,1 МПа; морозостойкость – 150 циклов; усадка – 0,6…0,7 мм/м.
Гранулированныйтопливныйшлак. Химическийсостав гранулированных шлаков, полученных из одного и того же топлива, но с применением различных способов удаления, несколько различается. В топках топливо сжигают в условиях избытка воздуха, т. е. в слабо окислительной среде, в результате чего в кусковых шлаках образуются соединения трехвалентного железа. При жидком шлакоудалении ион Fe3+ восстанавливается до Fe2+ вследствие непосредственного взаимодействия Fe2О3 с углеродом.
Гранулированные шлаки от сжигания каменного угля характеризуются практически полным выгоранием органической части и переходом соединений железа в двухвалентное состояние. Буроугольные шлаки содержат повышенное количество глинозема или оксидов кальция при значительно меньшем количестве оксидов железа. Сланцевые шлаки являются высококальциевыми, в них больше сульфатов, чем в шлаках от сжигания каменных или бурых углей.
Для большинства ТЭС характерны сверхкислые гранулированные шлаки с модулем основности:
М0 = |
CaO MgO |
≈ 0,05 – 0,07 |
(23) |
||
|
SiO |
Al O |
|
|
|
|
2 |
2 |
3 |
|
|
Содержание кислых стеклообразующих оксидов (SiО2 + A12О3) в гранули- рованныхшлакахнаходитсяобычновпределах70–85%. Только шлаки из угля Кан- ско-Ачинского бассейна являются слабокислыми (М0 = 0,6—0,9), а шлаки из сланцев – основными (М0 > 1).
Гранулированные шлаки устойчивы к силикатному и железистому распаду, не вступают в реакцию с оксидами щелочных металлов в цементе, несмотря на наличие в них значительного количества аморфного SiО2.
78