
БТ / ZAPOLNITELI BETONA
.pdf
Технологический процесс производства складывается следующим образом. Подсушенные гранулы из подготовительно-формовочного отделения завода подают в бункер запаса сырья (примерно на 2 ч) для их последующего
.измельчения и подсушки в молотковой мельнице. Глиняная крошка размером менее 5 мм (влажность 8... 12%) отделяется в осадительном циклоне от теплоносителя и направляется в расходный бункер двухзонной печи кипящего слоя. Температура в зоне термоподготовки 200... 400°С, в зоне обжига — 1000... 1100°С. Из зоны обжига большая часть керамзитового песка (примерно 70%) поступает в холодильник кипящего слоя, температура в котором находится в пределах 120... 180°С. Другая часть, состоящая из пылевидных и мелких частиц (около 30%), выносится в футерованный циклон. Керамзитовый песок из холодильника и циклона поступает в систему пневмотранспорта и далее на склад готовой продукции.
1 – молотковая мельница; 2 — осадительный циклон; 3 — элеватор; 4 — бункер; 5 — печь кипящего слоя СМС-139; 6 — вентиляторы; 7 — батарея циклонов; 8 — электрофильтр; 9— холодильник; 10 — футерованный циклон; 11 — склад готовой продукции; 12 — рукавный фильтр
Рисунок 15 - Технологическая схема производства керамзитового песка
4.2 Аглопорит
Аглопоритом называют искусственный пористый материал, получаемый путем термической обработки силикатных материалов методом агломерации. Под агломерацией понимают спекание в конгломерат сыпучего топливо содержащего материала посредством его слоевого обжига с интенсивным просасыванием или продуванием воздуха через слой зажженного материала. Аглопорит используют в качестве заполнителя легких бетонов.
49
Свойства аглопорита
По ГОСТ 11991 различают два вида аглопоритовых материалов - аглопоритовый щебень и аглопоритовый песок. В зависимости от размера зерен различают три фракции щебня: 5…10, 10…20 и 20…40 мм. Зерна песка имеют размер менее 5 мм. Марки аглопоритовых материалов различают по их объемной насыпной массе (таблица 11).
Таблица 11 - Требования к аглопоритовому щебню по плотности и прочности
Марка |
Насыпная |
Прочность при сжатии в цилиндре |
|
плотность в кг/м3 |
в кгс/м2 (в МПа) |
400 |
До 400 |
4(0,4) |
500 |
401…500 |
6(0,6) |
600 |
501…600 |
8(0,8) |
700 |
601…700 |
10(1) |
800 |
701…800 |
12(1,2) |
Потери по массе не должны превышать (в %): при прокаливании - 3, при определении стойкости щебня против силикатного распада - 8, против железистого распада - 5, при испытании на стойкость в растворе сернистого натрия - 5, при испытании на морозостойкость после 15 теплосмен - 10. Отпускная влажность не должна превышать 5 %.
Требования к аглопоритовому песку ГОСТ 11991 не нормирует. Сырьевые материалы. Для изготовления аглопорита используют основ-
ные материалы и добавки. Различают три группы основных материалов:
-сухие плотные, или зернистые, материалы - к ним относят угленосные и глинистые сланцы и топливные шлаки;
-рыхлые горные породы, естественно влажные - это главным образом глинистые породы - глины, суглинки, супеси, лессы;
-сухие пылевидные материалы, представителями которых являются золы от сжигания углей.
Угленосные сланцы в большинстве случаев содержат достаточное количество горючих веществ, обеспечивающих процесс агломерации без добавки угля. Они являются попутными продуктами угледобычи, и потому их использование является наиболее экономичным.
Глинистые породы получили преимущественное применение для производства аглопорита [2,6].
Из тощих глинистых пород, содержащих 7…10% А12О3, можно получать только тяжелый аглопорит марок 500…700. Из глин, содержащих 10...14%
А12О3 с числом пластичности 14...17, можно получать легкий аглопорит с насыпной плотностью 350...500 кг/м3. Высоко вспучивающиеся глины для производства аглопорита не пригодны, так как при их вспучивании заплывают межзерновые пустоты, прекращается поступление через них воздуха в зону горения и, вследствие этого, процесс горения начинает затухать.
50
Добавки. В качестве добавок используют антрацит, каменный и бурый уголь, древесные опилки, лигнин, костру, топливосодержащие промышленные отходы: золу ТЭЦ, возврат, известь и с.с.б.
Наилучшим сортом антрацита для производства аглопорита является антрацитовый штыб, используемый для агломерации руд.
Гранулометрический состав угля подбирают экспериментально. Но во всех случаях количество пылевидной фракции должно быть минимальным, а максимальный размер зерен должен быть не более 3 мм. Крупные зерна угля не успевают выгорать в зоне спекания. Они догорают при охлаждении аглопорита, затрудняя и удлиняя этот процесс. Пылевидные частицы не выгорают из-за трудности доступа к ним воздуха.
Использование бурых углей вместо тощих увеличивает производительность агломерационных машин в 1,5 раза. Оптимальный гранулометрический состав бурого угля: фракция 2...5 мм - 80%, менее 2 мм -20%. Уголь добавляют в количестве 10...15% от массы сухой глины.
Древесные опилки добавляют до 10% по объему для увеличения пористости аглопорита и более раннего развития процесса горения. Размер зерен опилок не должен превышать 10 мм. Однако данные об их влиянии противоречивы. Имеются указания на то, что введение опилок в спекаемую шихту понижает ее газопроницаемость.
Лигнин, являющийся отходом гидролизной переработки древесины, добавляют в количестве до 25%. При этом достигают существенного увеличения скорости спекания.
Аналогичным образом действует костра-отход от переработки льна, имеющая теплоту сгорания около 17 000 кДж/кг. Добавка 5% костры повышает газопроницаемость шихты и на 100° снижает температуру ее зажигания, повышает равномерность структуры аглопорита, снижает на 10% его плотность и количество недожога в нем, интенсифицирует процесс охлаждения спекшегося коржа, понижая его температуру при сходе с машины с 600...800 до 120...200° С.
Золу ТЭЦ с малым содержанием СаО и МgО можно вводить в количестве 30…50%. Ее добавка устраняет трудности обработки переувлажненных глин и снижает расход топлива за счет содержащегося в ней несгоревшего углерода.
4.2.1 Технологический процесс изготовления аглопорита
Основными операциями технологического процесса изготовления аглопорита являются: подготовка добавок и шихты (дробление основного сырья, дозирование компонентов и их перемешивание), грануляция шихты и ее спекание, охлаждение спекшегося конгломерата (коржа), дробление коржа, сортировка и складирование аглопорита.
Подготовка шихты. Уголь дробят и отсеивают до предельной величины зерен 3 мм. Оптимальный состав угля: фракция 2...3 мм - 80%, менее 2 мм - 20%. Топливосодержащие породы также дробят и отсеивают для получения зерен с предельной величиной 5 мм. Величина зерен возврата и опилок не должна превышать 10 мм. Известь вводят в виде известкового молока при приготовлении из глины пластичного теста. Способы приготовления гранул зависят от структур-
51
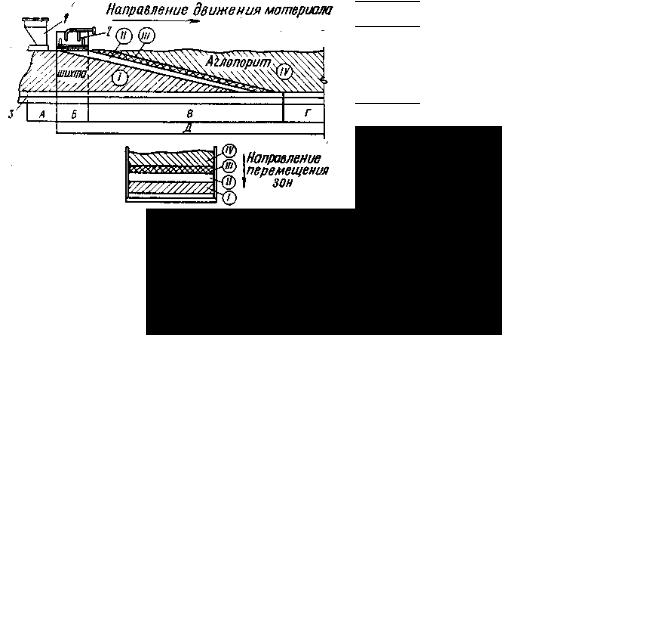
ных особенностей исходных материалов. Основными требованиями при подготовке гранул является обеспечение необходимой газопроницаемости и достаточно равномерного распределения всех компонентов шихты. Газопроницаемость регулируют подбором гранулометрического состава шихты в зависимости от пластичности глины. Оптимальные составы приведены в таблице 12.
Влажность шихты должна быть достаточной для образования слитных гранул и в то же время не должна быть чрезмерной с тем, чтобы гранулы не слипались в сплошную газонепроницаемую массу. Диапазон влажности, соответствующий экстремальным точкам кривых этой диаграммы, является оптимальным. Определяют его экспериментально. Примерные диапазоны влажности составляют для сырья: первой группы - 8...14%, второй группы - 16...23% [2,4].
Таблица 12 - Оптимальные зерновые составы в % и насыпная плотность глинистых шихт для производства аглопорита
Пластичность глинистых |
Размеры зерен,вмм |
Насыпная плотность шихты, |
|||
пород |
|
|
|
в кг/м3 |
|
7...10 |
3…7 |
0…3 |
|||
|
|
||||
|
|
|
|
|
|
Малопластичные |
20 |
40 |
40 |
980…1070 |
|
Умереннопластичные |
20 |
60 |
20 |
970…1050 |
|
Среднепластичные |
- |
70 |
30 |
940…1030 |
|
|
|
|
|
|
1 - загрузочный бункер; 2 - зажигательный горн; 3 - рабочая ветвь агломерационной машины.
Технологические зоны: I - испарения влаги; II - подогрева шихты;
III - спекания шихты; IV - охлаждения аглопорита.
Участки агломерационной ленты: А- загрузка; Б- зажигание; В -спекание; Г- охлаждение; Д-просос воздуха.
Рисунок 16 - Схема рабочего процесса ленточной агломерационной машины
Крупное сырье измельчают в молотковых или валковых дробилках. Иногда применяют двухступенчатое дробление. В этом случае сырье сначала подвергают дроблению, а затем грохочению и повторному дроблению. Углесодержащие породы, являющиеся отходами от добычи или обогащения угля, часто содержат топливо в количестве, значительно превышающем необходимый расход
52
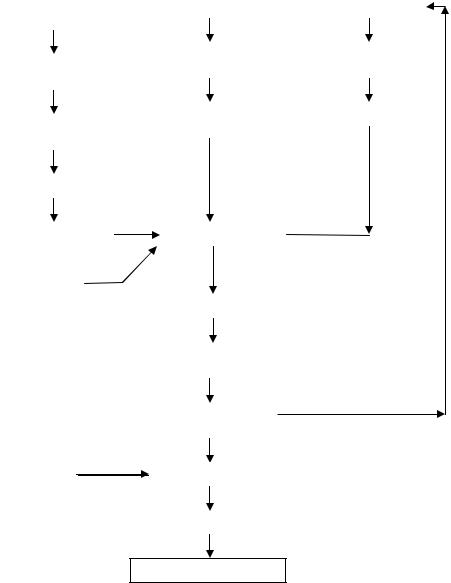
его на спекание аглопорита. В этих случаях возникает необходимость повысить «зольность» такого сырья добавкой в него глины.
Спекание шихты осуществляют в установках периодического и непрерывного действия.
Схема технологического процесса для получения аглопорита из углесодержащих пород имеет вид:
Отвалы отходов |
|
|
|
Глина |
|
|
|
Недожог |
|
углеобогащения |
|
|
|
|
|
|
|
|
|
|
|
|
|
|
|
|
|
|
|
|
|
|
|
|
|
|
|
|
|
|
|
|
|
|
|
|
|
|
|
|
|
|
Ящичный подаватель с |
|
|
Расходный бункер |
|
||
Склад для усредне- |
|
|
|
рыхлителем |
|
|
недожога |
|
|
ния породы |
|
|
|
|
|
|
|
|
|
|
|
|
|
|
|
|
|
|
|
|
|
|
|
|
|
||||
|
|
|
|
|
|
||||
|
|
Дезинтеграторные вальцы |
|
|
Дозатор |
||||
Щековая дробилка |
|
|
|
||||||
|
|
|
|
|
|
|
|
|
|
|
|
|
|
|
|
|
|
|
|
первичного дробле- |
|
|
|
|
|
|
|
|
|
|
|
|
|
|
|
|
|
|
|
|
|
|
|
|
|
|
|
|
|
|
|
|
|
|
|
|
|
|
|
Бункер запаса |
|
|
|
|
|
|
|
|
|
|
|
|
|
|
|
|
|||
|
|
|
|
|
|
|
|||
Дозатор |
|
|
|
Шихтосмеситель |
|
|
|
||
|
|
|
|
|
|
|
|
|
|
Вода
|
|
|
Питатель |
|
|
|
|
|
|
|
|
|
|
|
|
|
|
Агломерационная |
|
|
|
|
машина |
|
|
|
|
|
|
|
|
|
|
|
|
|
|
Грохот для отделения |
|
|
|
|
недожога |
|
|
|
|
|
|
|
|
|
||
Вода для |
|
|
Роторная дробилка |
|
охлаждения |
|
|
|
|
|
|
|
||
|
|
|
|
|
|
|
|
Грохот |
|
|
|
|
|
|
Силоса готовой продукции
Рисунок 17 - Получение аглопорита из углесодержащих пород
К установкам периодического действия относят чаши, которые могут быть поворотными и переносными, а к установкам непрерывного действияленточные и карусельные агломерационные машины. Чаши периодического действия малопроизводительны и трудоемки в обслуживании. На новых предприятиях их не устанавливают. Наиболее совершенным и высокопроизводительным агрегатом для обжига аглопорита является ленточная агломерационная машина. Она представляет собой вертикально замкнутый конвейер, со-
53
стоящий из отдельных тележек-чаш, называемых палетами. Схема рабочего процесса ленточной агломерационной машины приведена на рисунке 16. Питатель загружает в палеты гранулированную шихту в начале их движения по верхней (рабочей) ветви. Здесь они попадают в зону действия зажигательной камеры, и в верхнем слое шихты загорается топливо. Перемещаясь вперед, палета все время находится над вакуум-камерами и под влиянием господствующего в них разрежения, создаваемого дымососами. Через слой шихты просасывается воздух, а в вакуум-камеры поступают отработанные газы. При подходе палеты к концу рабочей ветви во всем слое шихты завершаются процессы спекания, а частично и охлаждения. Спекшийся корж при повороте палеты автоматически поступает на решетку с раскалывающим устройством, а палета по нижней ветви возвращается к загрузочному концу машины.
В зависимости от вида сырья температура зажигания шихты составляет 800...1200° С, а продолжительность зажигания 0,5...3 и даже 7 мин. Разрежение в период зажигания шихты 0,01...0,025 кПа, а в период спекания 0,02...0,05 кПа. Расход воздуха на 1 м2 площади спекания 0,5...1,1 м3/(м2·ч). Удельная (условная) производительность 0,15...0,85 м3/(м2·ч) [1].
Производительность (м3/ч) агломерационных ленточных машин может быть определена по формуле:
Пан Fам Q , |
(20) |
где Пан - производительность в м3/ч (по насыпной плотности); Q - условная (удельная) производительность в м3/( м2·ч); Fам - рабочая площадь агломерационной машины в м2.
Величину Q определяют по результатам испытаний данного вида сырья, а для ориентировочных подсчетов принимают по справочным данным.
Охлаждение аглопорита в настоящее время осуществляют тремя способами: на самой агломерационной ленте; недробленого спекшегося коржа на промежуточных складах и дробленого аглопорита в холодильниках
Охлаждение на агломерационной ленте удобно тем, что в одном агрегате совмещаются процессы спекания шихты и охлаждения аглопорита. Однако этому способу присущи и серьезные недостатки. В этом случае корж остывает неравномерно: в то время как периферийная часть его приобретает достаточно низкую температуру, сердцевина продолжает оставаться раскаленной, не утратив еще полностью пиропластического состояния. Последующее дробление горячего и частично вязкого коржа затрудняет работу дробильных машин и способствует их быстрому износу, а иногда и аварийным поломкам. Для интенсификации процесса охлаждения некоторые заводы подают распыленную воду в зону охлаждения агломерационной машины. Однако последующая конденсация водяных паров в газоочистительных устройствах быстро выводит их из строя
[1,2].
54
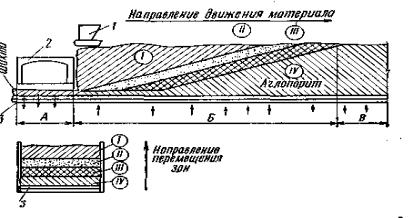
1-питатель; 2 - зажигательная камера; 3 - колосниковая решетка; участки агломерационной ленты; А - зажигания; Б - спекания; В - доводки и охлаждения.
Технологические зоны: I -загрузки шихты; II -подсушки; III -горения топ-
лива; IV-спекания шихты.
Рисунок 18 -Схема рабочего процесса агломерационной машины, работающей по дутьевому способу
В холодильниках охлаждение предварительно дробленного аглопорита происходит более равномерно. Однако тяжелые условия работы дробильных машин на горячем аглопорите в этом случае еще больше усугубляются. К тому же не имеется пока отработанных конструкций холодильников, оправдавших себя для аглопорита.
Охлаждение недробленых коржей на промежуточных складах требует большой их емкости в связи с длительными сроками этого процесса (несколько суток). Но в то же время этот способ удобен тем, что при нем работа дробиль- но-сортировочного оборудования становится независимой от работы агломерационных машин и его можно эксплуатировать в 1…2 смены при круглосуточной работе агломерационных машин. Имея достаточно емкие склады, можно при этом способе обеспечить работу дробильных машин на полностью охлажденном аглопорите. Этот способ получил предпочтительное распространение за рубежом, причем там промежуточные склады делают иногда открытыми, что улучшает санитарные условия труда по сравнению с закрытыми складами.
Дробление, сортировка и складирование аглопорита. На выходном конце агломерационных машин устанавливают неподвижный (иногда вибрирующий) колосниковый грохот с прикомпонованным к нему раскалывающим механизмом, который разрушает отколовшийся от агломерационной ленты (при повороте палеты) корж на сравнительно крупные куски. На колосниковом грохоте от коржа также отделяются неспекшиеся зерна, используемые в дальнейшем в качестве добавки в шихту (возврат). На второй стадии дробления иногда применяют щековые дробилки. Ступенчатое дробление обеспечивает наиболее высокий выход фракций 5...10 и 10...20 мм, а сортировка аглопорита по фракциям увеличивает выход готовой продукции на 20...30%. Для сортировки аглопорита используют барабанные и виброгрохоты.
55
4.2.2 Пример составления технологической схемы производства аглопоритового щебня и песка
Принципиальная технологическая схема производства аглопоритового щебня и песка приведена на рисунке 19. Помимо показанного на схеме шахтного холодильника для охлаждения аглопорита применяют ленточные (металлический транспортер с перфорированным дном), чашевые (кольцевой бункер с двумя жалюзийными цилиндрическими стенками) и барабанные холодильники.
При использовании в качестве основного сырья отходов углеобогащения в технологическую схему вносятся изменения, касающиеся подготовки исходных материалов. Отходы углеобогащения измельчают дроблением в две стадии с промежуточным грохочением, получая зерна размером не более 2,5 мм. Глину добавляют в виде сухого компонента (крупность до 3 мм) или глиняного шликера. Последующие технологические операции аналогичны приведенным на схеме.
Для производства аглопорита выпускается комплект основного технологического оборудования с агломерационными машинами СМС-117 и СМ-961 (длина 40 м, ширина 1,5 м).
Производительность агломерационной машины (т/ч):
П 0,06vLa B H kПkВ, |
(21) |
где v — вертикальная скорость спекания, мм/мин: La - активная длина агломерационной машины, м, равная общей длине машины L за вычетом длины зон сушки Lc (обычно Lc = 0,05…0,1L) и охлаждения Lo (при наличии холодильника Lo=0,2L, при отсутствии холодильника и производстве аглопоритового гравия Lo = 0,4L); В — активная ширина агломерационной машины, м; рн — насыпная плотность сырцовых гранул, рн=1 ... 1,1 т/м3; kn — коэффициент выхода аглопорита, kn — 0,75 ...0,90; kB — коэффициент, учитывающий возврат в шихту недожога; при отсутствии подачи возврата в шихту, kB =1.
Годовая мощность агломерационной машины (м3/г):
Мaг ТПkи / н , |
(22) |
где Т — годовой фонд рабочего времени, ч; П — расчетная производительность агломерационной машины, т/ч; kи — коэффициент использования годового фонда рабочего времени, kи = 0,82 ...0,9; рн — насыпная плотность аглопоритового щебня (гравия), т/м3.
Вспучивающееся глинистое сырье, пригодное для производства керамзита, не часто встречается. Более распространены малопластичные, тощие, запесоченные глинистые породы, суглинки, которые при обжиге не вспучиваются. Эти породы можно использовать для получения другого искусственного пористого заполнителя — аглопорита.
56
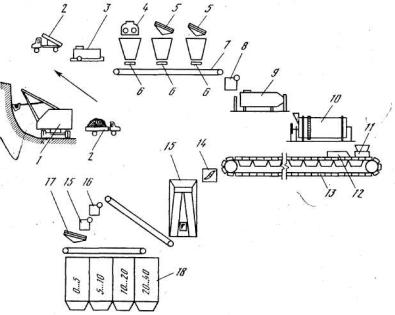
Таблица 13 – Требования к прочности аглопоритового щебня
|
Прочность при сдавли- |
|
Прочность при сдав- |
|||
|
|
ливании в цилиндре, |
||||
Марка по |
вании в цилиндре, МПа, |
Марка по на- |
||||
насыпной |
не менее, |
сыпной плот- |
МПа, не менее, |
|||
по категориям каче- |
||||||
плотности |
по категориям качества |
ности |
ства |
|
||
|
|
|
|
|
||
|
|
|
|
|
|
|
|
высшая |
первая |
|
высшая |
|
первая |
400 |
0,4 |
0,3 |
700 |
1,0 |
|
0,9 |
500 |
0,6 |
0,5 |
800 |
1,4 |
|
1,2 |
600 |
0,8 |
0,7 |
900 |
1,6 |
|
1,4 |
|
|
|
|
|
|
|
1 — экскаватор; 2 — автотранспорт; 3 — ящичный подаватель; 4 - валковая дробилка; 5 — вибросито; 6 — ленточный питатель; 7 — сборный ленточный транспортер;
8 — камневыделительные вальцы; 9 — двухвальная глиномешалка; 10 - барабанный гранулятор; 11 — укладчик шихты;
12 — зажигательный горн; 13 — агломерационная машина; 14 — коржеломатель; 15 — шахтный холодильник; 16 — валково-зубчатая
дробилка; 17 — гравиесортировочная машина; 18 — склад готовой продукции. Рисунок 19 - Технологическая схема производства аглопоритового
щебня и песка
Применение. Если керамзит, который, как правило, получается более пористым и легким, чем аглопорит, используется преимущественно для стеновых панелей, то для аглопорита главной областью применения являются конструкционные легкие бетоны. Аглопоритобетон с пределом прочности 20...30, а в отдельных случаях и до 50 МПа, идет на изготовление предварительно напряженных железобетонных конструкций перекрытий и покрытий, большепролетных балок и ферм, мостовых пролетных строений и т. д. Замена в этих кон-
57
струкциях тяжелого бетона легким аглопоритобетоном значительно повышает их эффективность. Кроме того, аглопоритобетон применяют как конструкцион- но-теплоизоляционный материал.
4.3 Шлаковая пемза Шлаковую пемзу получают главным образом из доменных шлаков,
причем не из отвальных (такие шлаки еще нужно было бы расплавить), а непосредственно из шлаковых расплавов, сливаемых из доменных печей в ог- ненно-жидком состоянии. По себестоимости шлаковая пемза — самый дешевый искусственный пористый заполнитель. Естественно, что шлаковая пемза производится и применяется в районах металлургической промышленности.
4.3.1 Основы технологии
Имеется несколько способов производства шлаковой пемзы, но все они основаны на вспучивании шлакового расплава водой.
При контакте шлакового расплава (температура около 1300 °С) с водой происходит бурное вскипание с интенсивным образованием пара. Пузырьки пара, внедряясь в расплав, не могут выделиться свободно, поскольку при охлаждении вязкость расплава увеличивается. В результате он вздувается, вспучивается и застывает в виде поризованной массы ячеистой структуры. Основное значение при этом имеют химический состав шлаков и наличие в них растворенных газов, определяющие газотворную способность, вязкость и поверхностное натяжение шлаковых расплавов [1,4].
Бассейновый способ производства шлаковой пемзы состоит в следующем. Шлаковый расплав выливается шлаковозными ковшами в опрокидной бассейн для вспучивания, представляющий собой металлическую ванну с перфорированным дном. Вместимость бассейна позволяет принять сразу весь расплав из шлаковозного ковша (до 16,5 м3). Снизу через отверстия в бассейн подается вода, на ее фонтанирующие струйки выливают шлаковый расплав. Он вспучивается и отвердевает, после чего выгружается, остывает в виде глыб, затем подвергается дроблению и рассеву на фракции (рисунок 20).
Производственный цикл, включающий слив из ковша и наполнение бассейна расплавом, вспучивание (1,5...2 мин), охлаждение и кристаллизацию (без подачи воды), разгрузку бассейна и его подготовку к следующему циклу, составляет 15... 20 мин. Объем получаемой шлаковой пемзы — до 25 м3. Режим поризации шлакового расплава можно регулировать при изменении его состава.
58