
Пожарная безопасность технологических процессов / Artemiev -Pozharnaya bezopasnost tekhnologicheskikh processov. Chast-2 2008
.pdf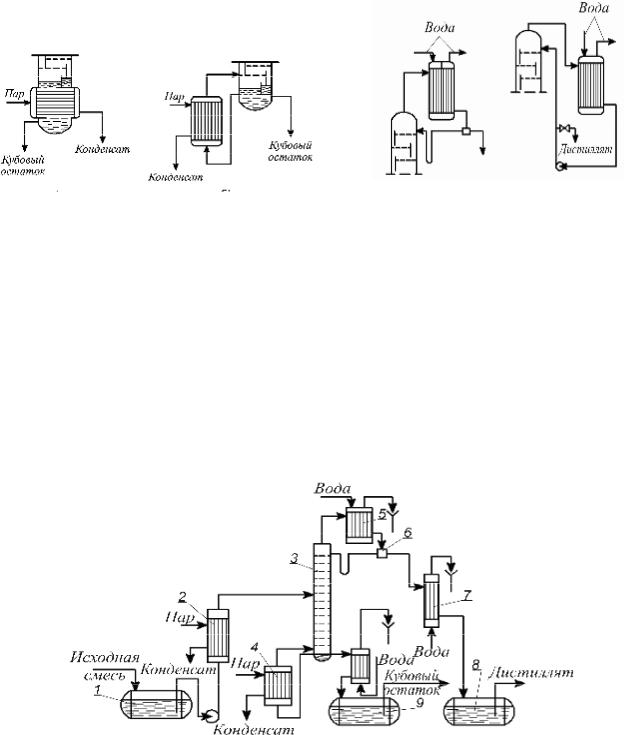
дефлегматоры – для получения флегмы за счет частичной конденсации выходящей паровой фазы. Варианты расположения дефлегматоров приводятся на рисунке 6.11.
а) |
б) |
а) |
б) |
Рисунок 6.10 − Варианты |
|
Рисунок 6.11 − Варианты располо- |
|
расположения кипятильников: |
жения дефлегматоров: |
|
|
а − встроенного; |
|
а − подачей флегмы самотеком; |
|
б − выносного. |
|
б − подачей флегмы насосом. |
Процессы ректификации проводят на установках непрерывного или периодического действия. В установке непрерывного действия (рисунок 6.19) необходимо, чтобы поступающая на разделение смесь соприкасалась со встречным потоком пара с несколько большей концентрацией ВК, чем в жидкой смеси. Поэтому исходную смесь подают в то место РК 3, которое соответствует этому условию. Место ввода исходной смеси, нагретой до температуры
Рисунок 6.12 − Схема ректификационной установки непрерывного действия:
1 − емкость для исходной смеси; 2 − подогреватель; 3 − колонна; 4 − кипятильник; 5 − дефлегматор; 6 − делитель флегмы; 7 − холодильник; 8 − сборник дистиллята; 9 − сборник кубового остатка.
кипения в подогревателе 2, называют тарелкой питания, или питательной тарелкой. Тарелка питания делит колонну на две части: верхнюю – укрепляющую
131

и нижнюю – исчерпывающую. В укрепляющей части происходит обогащение поднимающихся паров НК, а в исчерпывающей – удаление НК. Поток пара, поднимающегося по РК, поддерживается испарением части кубовой жидкости в кипятильнике 4, поток жидкости, текущей по колонне сверху вниз, возвратом части флегмы, образующейся при конденсации выходящих из колонны паров в дефлегматоре 5.
При непрерывной ректификации многокомпонентных смесей в установке должна быть не одна колонна, а больше, т.к. в одной колонне можно разделить смесь только на два продукта.
Периодически действующие ректификационные установки применяют, как правило, для разделения жидких смесей в тех случаях, когда использование непрерывно действующих установок нецелесообразно. Обычно это характерно для технологических процессов, в которых количества подлежащих разделению смесей невелики и требуется определенное время для накопления этих продуктов перед разделением или в условиях часто меняющегося состава исходной смеси. Периодическую ректификацию проводят на установках, схема которой показана на рисунке 6.13.
Рисунок 6.13 − Схема установки для проведения периодической ректификации.
Исходную смесь периодически загружают в куб-кипятильник 1, снабженный подогревателем 2, в который подается теплоноситель, например насыщенный водяной пар и доводят до кипения. Образующиеся пары поднимаются по колонне 3, в которой происходит противоточное взаимодействие этих паров с жидкостью (флегмой), поступающей из дефлегматора 4. Часть конденсата после делителя потока 5 возвращается в колонну в виде флегмы, другая часть – дистиллят Р – через холодильник 6 собирается в сборниках 7 в виде отдельных фракций. Процесс ректификации заканчивают обычно после того, как будет достигнут заданный средний состав дистиллята. Таким образом, колонна 3 является аналогом укрепляющей части колонны непрерывного действия, а куб выполняет роль исчерпывающей части.
132
Пожарная опасность процессов ректификации определяется пожароопасными свойствами веществ и режимом работы РК (температура, давление). Большинство колонн работает под небольшим давлением 0,12...0,7 МПа. При нормальных режимах работы, в РК работающих под избыточным давлением, образование горючей смеси невозможно. Горючие концентрации внутри РК могут образовываться в периоды остановки на ремонт и пуска колонн после ремонта. При авариях или неисправностях возможно: в колоннах, работающих под давлением – выход и воспламенение продукта, если продукт нагрет до температуры самовоспламенения и выше, а в колоннах, работающих под вакуумом
– подсос воздуха и образование взрывоопасных концентраций внутри колонны. Причины образования неплотностей и повреждений в РК: повышение давления, температурные и механические воздействия, химический износ оборудования. Повышение давления является следствием нарушений материального и энергетического балансов, процесса нормальной конденсации паровой фазы, попадания в высоконагретые РК жидкостей с низкой температурой
кипения.
Источниками зажигания в процессах ректификации могут быть: огневые работы; самовоспламенение нагретого продукта; самовозгорание пирофорных отложений; нагретые поверхности РК и другого оборудования.
Пожар на ректификационной колонне может быстро принять крупные масштабы, т.к. в результате аварии возможен выход наружу большого количества горючей жидкости и ее паров. Пары горючей жидкости выходящие наружу могут привести к образованию взрывоопасных концентраций в объеме помещений или на территории открытых площадок. Распространению пожара способствуют системы производственной вентиляции и канализации.
Специфические требования пожарной безопасности при проведении процессов ректификации (регламентируют [20, 25]):
−на открытых площадках ректификационное оборудование должно размещаться группами с учетом их пожарной опасности;
−перед пуском должны быть осмотрены, проверена исправность и готовность к работе всех связанных с РК аппаратов и трубопроводов, исправность контрольно-измерительных приборов, регуляторов температуры и давления в колонне, измерителей уровня жидкости в нижней части колонны, приемниках ректификата, рефлюксных емкостях и емкостях остатка;
−РК, установленные на открытых площадках, должны быть оборудованы стационарной или полустационарной системой пожаротушения (колонны для разделения СГГ, а также колонные аппараты высотой 40 м и более) должны быть обеспечены стационарными системами водяного или воздушно-пенного охлаждения и тушения;
−приборы автоматического контроля уровня жидкости в сепараторах должны быть в исправном состоянии. При отсутствии стационарных приборов, должен осуществляться лабораторный контроль с периодичностью, определенной в производственных инструкциях;
−колонны необходимо оборудовать предохранительными клапанами.
133
Выброшенная через клапан флегма должна отводиться в дренажные системы;
−поврежденные участки теплоизоляции РК и их опор должны своевременно исправляться. Теплоизоляция должна быть чистой, исправной и выполнена так, чтобы при утечках не могли образоваться скрытые течи жидкости по корпусу;
−при разгонке полимеризующихся жидкостей необходимо принимать меры против образования и отложения полимеров в колонне (подача ингибиторов) и периодически производить очистку от отложений;
−перед открытием нижнего люка РК в аппарат необходимо подать пар или иметь наготове подключенный к паровой гребенке шланг;
−при переключении линий должно исключаться попадание в колонну воды или других низкокипящих жидкостей;
−после промывки и продувки колонны должно производиться полное удаление воды и конденсата;
−при подаче острого пара в РК должно производиться его освобождение от конденсата, образующегося в паровой линии;
−во избежание проявления высоких температурных напряжений в стенках аппаратов ректификационной установки, которые могут возникнуть под воздействием атмосферных осадков либо при пожаре, трубопроводы на прямых участках необходимо оборудовать температурными компенсаторами; защищать теплоизоляцией опорные металлические конструкции (опоры, юбки, этажерки и др.);
−на открытых установках в зимнее время спускные и дренажные линии,
атакже участки трубопроводов подачи замерзающих жидкостей (воды, щелочи и других жидкостей) должны иметь исправное утепление;
−ремонтные работы в колонне могут производиться лишь после полного удаления продукта и продувки РК паром.
Вопросы для самопроверки
1.Объясните сущность процесса абсорбции.
2.Перечислите абсорбенты, наиболее часто используемые в технологических процессах производств, охарактеризуйте их свойства.
3.Нарисуйте схемы насадочного и тарельчатого абсорберов, объясните их работу.
4.Дайте оценку пожарной опасности абсорбционных установок и приведите требования пожарной безопасности к процессам абсорбции.
5.Объясните процессы адсорбции: распространенность, сущность, факторы, влияющие на протекание процесса адсорбции.
6.Перечислите широко используемые адсорбенты и охарактеризуйте их свойства.
7.Какие виды адсорберов вы знаете, нарисуйте схему одного из них, объясните фазы их работы.
8.Охарактеризуйте пожарную опасность адсорбционных установок.
134
9.Назовите способы осуществления процессов десорбции, охарактеризуйте их пожарную опасность.
10.Назовите требования пожарной безопасности, направленные на предотвращение образования горючих концентраций в адсорберах и линиях транспорта паровоздушной смеси.
11.Перечислите источники зажигания в процессах адсорбции и рекуперации и меры по предотвращению самовозгорания угля в адсорберах.
12.Назовите возможные пути распространения пожара на адсорбционных установках и меры по их предотвращению.
13.Назовите способы осуществления процессов десорбции, охарактеризуйте их пожарную опасность.
14.Объясните сущность процессов разделения горючих жидкостей простой перегонкой и ректификацией.
15.Объясните устройство и работу РК, приведите виды колонн.
16.Нарисуйте принципиальную схему непрерывно действующей ректификационной установки, объясните ее работу.
17.Охарактеризуйте особенности пожарной опасности процессов ректификации.
18.Перечислите источники зажигания на ректификационных установках.
19.Приведите основные требования пожарной безопасности при проведении процессов ректификации.
135
ГЛАВА 7
ПОЖАРНАЯ БЕЗОПАСНОСТЬ ХИМИЧЕСКИХ ПРОЦЕССОВ
Основными процессами большинства технологических схем производства химической промышленности являются процессы химического превращения веществ. Эти процессы сопровождаются выделением (экзотермические) или поглощением (эндотермические) тепла. Для обеспечения оптимальных условий и безопасных режимов работы технологического оборудования необходимо применение специальных систем охлаждения (процессы окисления, хлорирования, гидрохлорирования, гидрирования, полимеризации и поликонденсации) или нагрева (процессы дегидрирования, пиролиза) В большинстве случаев химические процессы протекают в присутствии катализаторов и инициаторов. Применяемые в реакторах катализаторы и инициаторы весьма разнообразны по составу. Это металлы, соли, кислоты, щелочи, металлоорганические соединения, перекиси, гидроперекиси, диазосоединения и др.
Основными аппаратами химических технологий являются химические реакторы.
7.1 Пожарная безопасность химических реакторов
Химический реактор – это аппарат для проведения химических реакций. Химические реакторы классифицируются по способу организации процесса; тепловому режиму; режиму движения реакционной среды; фазовому состоянию исходных реагентов; конструктивному оформлению теплообменных устройств.
По способу организации процесса различают реакторы периодического, полунепрерывного и непрерывного действия. В реакторах периодического действия исходное сырье (реагенты) загружают через определенные промежутки времени. После осуществления химических превращений продукты реакции выгружают из реактора. По окончании разгрузки реактора и его повторной загрузки процесс повторяется. Таким образом, в реакторах периодического действия все его стадии (загрузка, реакция, разгрузка), протекают в одном месте (в одном аппарате), но в разное время.
Вреакторах полунепрерывного (комбинированного) действия один из исходных реагентов загружается непрерывно, другой – периодически. Иногда реагенты поступают в реактор периодически, продукты реакции выгружаются непрерывно.
Вреакторах непрерывного действия, поступление исходных реагентов, сама химическая реакция и выгрузка продуктов реакции, производятся одновременно и непрерывно, но разобщены в пространстве, то есть осуществляются
вразличных частях одного аппарата.
По тепловому режиму реакторы бывают изотермические, адиабатические, реакторы с программированным тепловым режимом.
136

Реакторы, в которых процесс протекает при постоянной температуре во всех точках реакционного объема, называют изотермическими. Достичь постоянства температуры в реальных условиях весьма затруднительно, поэтому для большинства реакторов наиболее характерным является политропический режим, т.е. частичный отвод тепла реакции или подвод тепла извне. Для отвода и подвода тепла используют соответствующие тепло и хладагенты.
Реакторы, работающие без теплообмена с окружающей средой, называются адиабатическими. Все тепло, выделяемое (или поглощаемое) в реакторе, аккумулируется реакционной смесью. Эти реакторы просты по конструкции, у них нет теплообменных устройств. Для создания адиабатического режима используют теплоизоляцию.
В реакторах с программированным тепловым режимом теплообмен осуществляется в соответствии с заданной программой изменения температуры по высоте реактора или в определенных точках реакционного объема (в определенные промежутки времени).
По режиму движения реакционной среды различают реакторы вытеснения и реакторы с перемешиванием (при непрерывном действии реактора).
Реактор вытеснения (рисунок 7.1) характеризуется тем, что в нем все частицы заполняющего продукта движутся в заданном направлении, не перемешиваясь с движущимися впереди и сзади частицами и полностью вытесняя, подобно поршню, находящиеся впереди частицы потока. Время пребывания всех частиц реакционной среды в аппаратах идеального вытеснения одинаково. Состав реакционной смеси изменяется постепенно, по длине (высоте) реактора, вследствие протекания химической реакции.
Рисунок 7.1 − Реактор вытеснения трубчатого типа:
1 – корпус; 2 – катализатор; 3 – теплоноситель (хладагент); 4 – исходные продукты; 5 – продукты реакции.
Реакторы с перемешиванием (рисунки 7.2, 7.3), характеризуются тем, что поступающие в них реагенты интенсивно перемешиваются с помощью мешалки. Реагенты непрерывно подаются в реактор, а продукты реакции непрерывно
137

выводятся. Поступающие в такой реактор частицы вещества мгновенно смешиваются с уже находящимися в нем частицами. В результате во всех точках реакционного объема выравниваются параметры, характеризующие протекающий процесс.
Рисунок 7.2 − Схема реактора со |
Рисунок 7.3 − Схема реактора со |
||
скребковой мешалкой: |
|
спиралевидной мешалкой: |
|
1 |
– корпус; 2 – мешалка; |
1 |
– спираль большого диаметра; |
3 |
– рубашка для подогрева |
2 |
– спираль малого диаметра; |
и охлаждения. |
3 |
– рубашка охлаждения. |
По фазовому состоянию исходных реагентов реакторы бывают гомогенные и гетерогенные. Гомогенным называют реактор, если в нем реагирующие вещества находятся в одной фазе, например, только в жидкой или только в газообразной, а гетерогенным – если в реакторе реагирующие вещества находятся в различных агрегатных состояниях.
По конструктивному оформлению теплообменных устройств различают реакторы с рубашкой, с внутренними змеевиками, с наружным (внутренним) теплообменником и с двойными трубками.
Система теплообмена может быть непрерывной и ступенчатой. На рисунке 7.4 показаны наиболее распространенные теплообменные устройства, применяемые в реакторах смешения, а на рисунке 7.5 – в реакторах вытеснения.
а) |
б) |
в) |
г) |
Рисунок 7.4 Схемы теплообменных устройств в реакторах смешения:
а– аппарат с рубашкой; б – аппарат с внутренним змеевиком; в – аппарат
снаружным теплообменником; г – аппарат с внутренним теплообменником; 1 – исходное вещество; 2 – теплоноситель; 3 – продукты реакции.
138
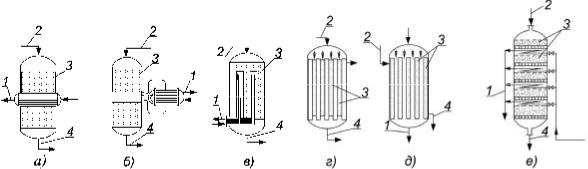
Непрерывный отвод (подвод) тепла осуществляется через теплообменную поверхность по всей высоте реактора. При ступенчатом отводе (подводе) тепла реактор делится на адиабатические секции с промежуточным охлаждением (подогревом).
Рисунок 7.5 − Схемы теплообменных устройств в реакторах вытеснения:
а – внутренний теплообменник; б – наружный теплообменник; в – двойные трубки; г, д – кожухотрубчатые теплообменники; е – внутренние змеевики; 1 – теплоноситель (хладагент); 2 – исходное вещество; 3 – катализатор; 4 – продукты реакции.
В реакторах помимо химических, идут и физические процессы, с помощью которых создаются оптимальные условия для осуществления химических реакций (поддерживаются определенная температура, давление, скорость перемешивания и др.). Поэтому химические реакторы соединяются с другими технологическими аппаратами (компрессорами, насосами, теплообменниками, сепараторами).
Машины и аппараты, соединенные между собой в определенной последовательности, образуют технологическую схему. При этом аппараты, расположенные до реактора, предназначены для подготовки и подачи исходных реагентов в реактор, а расположенные после реактора – для выделения целевого продукта, получаемого в результате химических превращений.
Пожарную опасность химических реакторов определяют физикохимические и пожароопасные свойства исходных реагентов и продуктов реакции; свойства реакционной среды и применяемых катализаторов (инициаторов); параметры проходящего в реакторе процесса, (давление, температура, объемная или массовая скорость); тип и конструктивные особенности реактора.
Горючая среда в период нормального ведения технологического процесса в реакторе не образуется, т.к. в исходных реагентах и продуктах реакции отсутствует окислитель. Горючая среда может образоваться в периоды загрузки или выгрузки, при замене отработанного катализатора, если нарушается безопасное соотношение между горючим и окислителем при подаче их в реактор.
Катализаторы могут быть взрывопожароопасными и стать источниками зажигания. Органические соединения обладают большой химической активностью, самовоспламеняются на воздухе, реагируют с взрывом с водой и другими веществами. Для увеличения поверхности контакта катализатора с веществом его наносят на пористую основу (активированный уголь, силикагель, керамику и др.), обладающую развитой поверхностью. Катализаторы, приготовленные на
139
основе активированного угля склонны к самовозгоранию.
Пути распространения пожара: при нормальном ходе технологического процесса выход ГГ, паров и жидкостей из реакторов исключен, т.к. они закрыты герметично. Выход горючих веществ в производственное помещение или на открытую площадку возможен только в случае повреждений либо возникновения аварий. Повреждения (аварии) реакторов могут произойти при нарушении материального баланса в реакторе, увеличении скорости химической реакции (приводит к значительному повышению давления и температуры в реакторе) и снижении механической прочности стенок реактора.
7.1.1Требования пожарной безопасности при устройстве
иэксплуатации химических реакторов
Основные требования пожарной безопасности при устройстве и эксплуатации химических реакторов (регламентируют [20, 25]):
−эксплуатация реакторов с отключенными или неисправными кон- трольно-измерительными и регулирующими приборами, средствами и системами противоаварийной защиты не допускается;
−в реакторном отделении не допускается приготовление растворов взрывопожароопасных компонентов. Эта операция должна производиться в специально оборудованном помещении;
−загрузку порошкообразных взрывопожароопасных веществ необходимо осуществлять при исправной системе местных отсосов или использовать эти вещества в виде предварительно подготовленных суспензий;
−не допускается эксплуатация реакторов и других аппаратов при заполнении гидравлических затворов ниже требуемого уровня;
−отбор проб из реакторов через неисправные пробоотборные устройства не допускается;
−при использовании металлоорганических катализаторов необходимо контролировать содержание кислорода и влаги в исходном сырье, инертном газе с периодичностью, установленной технологическим регламентом;
−для предотвращения повышения давления в контактных аппаратах, питающихся через испарители, не допускается попадание в них неиспарившейся жидкости;
−в реакторах, в которых происходит перемешивание взрывопожароопасных веществ, необходимо обеспечить надежную работу мешалок и контролировать герметичность сальниковых уплотнений вала мешалок. При остановке мешалки или нарушении герметичности вала мешалки реактор должен быть остановлен;
−в реакторах с использованием твердого катализатора (в виде зерен, стружки и т.п.) и необходимостью перемешивания массы, мешалку после остановки не допускается включать повторно без предварительной разгрузки аппарата от твердого катализатора;
−в жидкостных реакторах не допускается превышение регламентиро-
140