
Пожарная безопасность технологических процессов / Artemiev -Pozharnaya bezopasnost tekhnologicheskikh processov. Chast-2 2008
.pdf−искры и электрические дуги при механическом повреждении изоляции электрических кабелей, подключенных к электродвигателям станков;
−тепловое проявление неисправного электрооборудования, осветительных и силовых сетей (короткие замыкания, перегрузки, большие переходные сопротивления), перегрузка электродвигателей станков;
−искровые разряды статического электричества при работе пневмотранспорта;
−удары молнии и ее вторичные проявления;
−теплота самовозгорания древесных отходов, пропитанных маслом (при их скоплении под станками или длительном хранении), а также промасленных обтирочных материалов;
−применение открытого огня (курение, огневые ремонтные работы). Распространению пожара в цехах механической обработки древесины
способствуют: горючие конструкции зданий; древесина и отходы ее обработки; воздуховоды систем вентиляции; системы удаления отходов производства, конвейерные линии и технологические проемы.
1.2.1 Требования по обеспечению пожарной безопасности при проведении процессов механической обработки древесины
Специфические требования по обеспечению пожарной безопасности при проведении процессов механической обработки древесины
(регламентируют [24]):
−помещения и оборудование должны регулярно очищаться от пыли, стружек, опилок и промасленных обтирочных материалов. Периодичность очистки от пыли высоко расположенных строительных конструкций, инженерных коммуникаций и светильников в помещениях должна определяться в зависимости от времени накопления пыли в опасном количестве и согласно цеховой инструкции о мерах пожарной безопасности;
−уборка пыли в производственных помещениях со строительных конструкций, оборудования, инженерных коммуникаций и светильников должна производиться с помощью промышленных пылесосов во взрывозащищенном
исполнении или специальной системой пневмоуборки, а при их отсутствии − влажным способом, не допускающим пыления. Сжатый воздух для уборки использовать не допускается;
−для удаления отходов деревообрабатывающие станки должны быть оборудованы исправными местными отсосами. Работа станков при выключенных системах вентиляции и пневмотранспорта не допускается;
−для предотвращения осаждения отходов в воздуховодах местных отсосов и пневмотранспорта скорость движения воздуха при отсосе принимают не менее 15 м/с;
−в пневмотранспортных и аспирационных системах, в бункерах должны исключаться застойные зоны, ведущие к отложению пыли;
−системы транспортирования стружки и пыли должны исключать
21
просыпание материалов;
−должен осуществляться контроль исправности электрооборудования и электропроводки, не допускается перегрузка электрооборудования станков;
−необходим периодически осуществлять контроль температуры подшипников;
−для работы должен применяться острый и правильно заточенный режущий инструмент;
−в системах пневмотранспорта должны применяться вентиляторы во взрывобезопасном исполнении;
−для предотвращения попадания металлических предметов в аспирационные и вентиляционные установки, удаляющие пожароопасные вещества, воздуховоды за местными отсосами должны быть оборудованы сетками с
размером ячейки 10×10 мм или магнитными уловителями; − передача движения от электродвигателя к механизмам должна осущест-
вляться при помощи клиновидных ремней.
1.3 Пожарная безопасность процессов механической обработки пластмасс
Механическую обработку деталей при производстве изделий из пластмасс применяют с целью: изготовления более точных, чем при прессовании или литье деталей; изготовления деталей из листовых пластиков; удаления литников, облоя, грата, пленки в отверстиях; более экономичного изготовления деталей сложной конфигурации; изготовления деталей в условиях единичного и мелкосерийного производства.
При механической обработке пластмасс различают следующие способы: разделительную штамповку, обработку пластмасс резанием. Разделительную штамповку применяют для изготовления деталей из листовых материалов. При этом выполняют следующие операции: вырубку, пробивку, отрезку, разрезку, обрезку, зачистку. Обработку пластмасс резанием применяют для отделки (удаления литников, облоя, пленки и др.) после горячего формообразования деталей и как самостоятельный способ изготовления деталей из поделочных пластмасс. При этом выполняют следующие операции: разрезку, точение, фрезерование, сверление, нарезание резьб, шлифование, полирование.
Термопласты обрабатывают ленточными и дисковыми пилами, вырубают на штампах, а также фрезеруют и сверлят соответствующими инструментами.
Для механической обработки изделий из реактопластов применяют шлифовальные круги, фрезы, резцы, сверла из твердых сплавов или инструментальной и быстрорежущей стали.
Горючую среду в цехах механической обработки пластмасс составляют: обрабатываемые материалы, отходы производства, в том числе и взрывопожароопасная пыль.
22
Для процессов механической обработки пластмасс характерны источники зажигания с природой происхождения свойственной процессам механической обработки древесины.
Распространению пожара в цехах механической обработки пластмасс способствуют горючие конструкции зданий; пластмассы и их отходы; расплавы пластмасс; технологические проемы и коммуникации.
1.3.1 Требования по обеспечению пожарной безопасности при проведении процессов механической обработки пластмасс
Специфические требования по обеспечению пожарной безопасности при проведении процессов механической обработки пластмасс
(регламентируют [36]):
−установки высокочастотного нагрева прессматериалов должны размещаться в металлических, хорошо экранированных шкафах. Установки должны быть снабжены блокировками, обеспечивающими при открывании дверей полное снятие напряжения со всех элементов, находящихся в открываемом отсеке;
−сушильные камеры, пропиточные установки, автоклавы и другие нагревательные устройства должны иметь измерительные и регулирующие устройства, а также средства аварийной сигнализации;
−бункеры и другие емкости, используемые для хранения сыпучих мелкодисперсных пожароопасных веществ и материалов, должны периодически осматриваться и при необходимости очищаться от остатков продукта и отложений пыли;
−оборудование и аппараты, при работе которых происходит образование пыли (роторные машины, таблетировочные машины и др.) должны быть герметичными;
−переработка полиформальдегида должна производиться при температуре, не превышающей температуру его плавления более чем на 10 ºС;
−электропитание нагревателей стационарных прессформ и нагревательных плит должно иметь напряжение не более 36 В;
−станины технологического оборудования, корпуса электродвигателей, конструктивные части электронагревательных приборов, а также металлические части, которые могут оказаться под напряжением, должны быть заземлены;
−для отвода статического электричества, накапливающегося на работнике, должны быть устроены полы с повышенной электропроводностью (заземленные рабочие площадки); необходимо применять токопроводящую специальную обувь с подошвой из кожи, токопроводящей резины или с токопроводящими заклепками;
−не допускается во время работы носить одежду из синтетических тканей, способных к электризации, не разрешается также носить кольца и браслеты, во избежание аккумуляции зарядов электричества;
−работающим на электризующемся оборудовании, с электризующимися
23
материалами, а также на электризующихся полах следует периодически прикасаться к заземленным частям, находящимся в руке металлическим предметом.
1.4 Пожарная безопасность процессов измельчения твердых горючих материалов
В химических, мукомольных, деревообрабатывающих, краскоприготовительных и других производствах находят применение процессы измельчения твердых материалов. Измельчение – это разрушение твердых тел до требуемых размеров. По размеру (крупности) измельченного продукта различают: грубое (300 − 100 мм), среднее (100 − 25 мм) и мелкое (25 − 1 мм) дробление; грубый (1000 − 500 мкм), средний (500 − 100 мкм), тонкий (100 − 40 мкм) и сверхтонкий (< 40 мкм) помол. Цель измельчения − получение продукта необходимой крупности и гранулометрического, или фракционного состава. Измельчение может быть сухим (как правило, при грубом и среднем дроблении) и мокрым (часто при мелком дроблении и помоле). Сухое измельчение проводят в воздушной среде или в инертных газах (при переработке окисляющихся, пожаро- и взрывоопасных, а также токсичных материалов). Мокрое измельчение (исходный материал смешивают с жидкостью, преимущественно с водой) применяют при обогащении руд методом флотации, при последующей обработке измельченного материала в виде суспензии (например, в производстве ТiO2), при повышенной влажности материала и наличии в нем комкующихся примесей, при необходимости исключить пылеобразование. В процессах измельчения используются способы раздавливания, раскалывания, удара и истирания. Для измельчения применяются измельчающие машины, которые делятся на дробилки и мельницы. Дробилками называются машины для крупного и среднего измельчения. Дробилки бывают четырех типов: щековые, конусные, валковые и роторные. На рисунке 1.15 показана схема щековой дробилки. В щековой дробилке материалы разрушаются в рабочей камере, состоящей из подвижной щеки, неподвижной щеки (дробящие плиты) и стенок корпуса. Подвижная щека совершает колебательные движения, надавливает на измельчаемый материал, подаваемый через загрузочное отверстие в рабочую камеру. При сближении подвижной дробящей плиты с неподвижной плитой происходит разрушение дробимого материала. Поверхность дробящих плит обычно выполняют рифлеными, а на стенки рабочей камеры устанавливают защитные пластины из чугуна либо износостойкой стали. Щековые дробилки относятся к агрегатам цикличного действия.
Мельницы − это машины для мелкого и тонкого измельчения, а также для коллоидного размола. Они бывают со свободными и закрепленными мелющими телами и без них. К машинам со свободными мелющими телами (металлические, керамические и другие шары, стержни, скатанная кремневая галька и др.) относятся: тихоходные вращающиеся барабанные мельницы − шаровые, стержневые, галечные (для грубого, среднего и тонкого помола); быстроходные мель-
24

ницы – центробежно-шаровые, вибрационные, планетарные, магнитные, бисерные и др. (для тонкого и сверхтонкого помола).
Рис. 1.15 − Схема щековой дробилки:
1 – стенка корпуса; 2 – боковая щека; 3 – подвижная щека; 4 – ось; 5 – вал; 6 – шатун; 7 – ременная передача; 8 – электродвигатель; 9 – пружина; 10 – тяга; 11 – упор; 12,13 – распорная плита; 14,15 – дробящие плиты.
На рисунке 1.16 показана схема устройства барабанной шаровой мельницы. Такие мельницы загружены мелющими телами обычно на 35-40% объема, в межшаровом пространстве находится материал, который измельчается в результате совместного действия шаров и крупных кусков, а также взаимного истирания.
Сухое тонкое измельчение и сухой размол горючих материалов является взрывопожароопасными процессами, т.к. готовый мелкодисперсный продукт способен легко взвихряться с образованием взрывоопасного аэрозоля, отложения пыли часто склонны к самовозгоранию.
Рисунок 1.16 − Схема барабанной шаровой мельницы:
1– корпус, 2 – мелющие тела, 3 – футеровочные плиты, 4 – привод.
Впроцессе размола появляются такие источники зажигания, как фрикционные искры и разряды статического электричества.
25
1.4.1 Требования пожарной безопасности процессов измельчения твердых горючих материалов
Специфические требования по обеспечению пожарной безопасности при проведении процессов измельчения твердых горючих материалов
(регламентируют [22, 23]):
−оборудование должно быть герметичным;
−перед вальцевыми станками, дробилками и др. машинами ударного типа должны быть установлены магнитные заграждения;
−подшипники оборудования и приводов должны регулярно смазываться
иочищаться от пыли и излишков масла;
−эксплуатируемое технологическое оборудование должно ежедневно очищаться от осевшей на них горючей пыли.
Вопросы для самопроверки
1.Какие вещества образовывают горючую среду в цехах холодной обработки металлов?
2.Какие факторы влияют на степень разогрева металлов при их механической обработке?
3.Назовите требования пожарной безопасности в процессах механической обработки металлов.
4.Охарактеризуйте особенности пожарной опасности процессов механической обработки магния, титана, циркония и их сплавов.
5.Назовите специфические требования пожарной безопасности при механической обработке магния, титана, циркония и их сплавов.
6.Назовите причины образования пылевоздушных горючих концентраций в машинах измельчения твердых горючих материалов.
7.Дайте характеристику источников зажигания в процессах измельчения твердых горючих материалов (в машинах, системах аспирации и т.п.).
8.Назовите требования пожарной безопасности, исключающие возникновение пожаров и взрывов в процессах измельчения твердых горючих материалов.
9.Что составляет горючую среду при механической обработке древесины.
10.Перечислите источники зажигания в деревообрабатывающих производствах.
11.Назовите требования пожарной безопасности для процессов механической обработки древесины.
12.Охарактеризуйте пожарную опасность процессов механической обработки пластмасс.
13.Назовите требования пожарной безопасности для процессов механической обработки пластмасс.
26

ГЛАВА 2
ПОЖАРНАЯ БЕЗОПАСНОСТЬ ПРОЦЕССОВ ТРАНСПОРТИРОВАНИЯ И ХРАНЕНИЯ ВЕЩЕСТВ И МАТЕРИАЛОВ
Многие производства промышленности и сельского хозяйства требуют бесперебойной подачи сырья, топлива, заготовок, удаления отходов производства и перемещения готовой продукции. Для этих целей применяются специальные транспортные системы, которые в зависимости от транспортируемых веществ, транспортные системы включают технологические трубопроводы, промежуточные емкости, насосы и насосные станции, компрессоры и компрессорные станции, транспортеры, элеваторы, бункеры, циклоны и другие технологические устройства.
Транспортные системы с горючими веществами являются пожароопасными, т.к. они могут являться местом возникновения пожара и путями его распространения.
2.1 Пожарная безопасность процессов транспортирования твердых материалов
В зависимости от вида транспортируемого материала различают устройства для перемещения сыпучих материалов и штучных грузов. К таким устройствам относятся транспортеры, элеваторы, самотечные и пневматические трубы. По режиму работы устройства для транспортировки могут быть непрерывными и периодическими, а по направлению транспортировки – горизонтальными, вертикальными и смешанными.
Транспортеры и элеваторы по конструкции бывают: ленточные; пластинчатые; скребковые и винтовые. Наиболее широкое применение нашли ленточные горизонтальные или наклонные транспортеры. Общее устройство таких транспортеров показано на рисунке 2.1. Лента приводится в движение ведущим
Рисунок 2.1 – Схема устройства ленточного транспортера:
1 – ведущий барабан; 2 – ведомый барабан; 3 – загрузочное устройство; 4 – опорные ролики; 5 – лента; 6 – разгрузочное устройство;
7 – транспортируемый материал
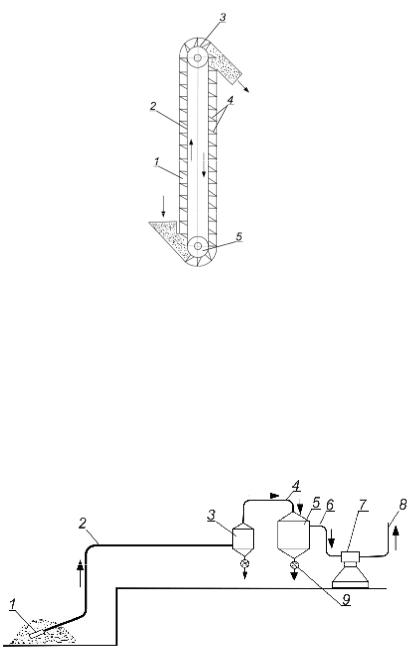
барабаном с электроприводом через редуктор. Ведомый вал служит для натяжения ленты. Чтобы предотвратить провисание ленты, под ней устанавливают ряд опорных роликов. Разновидностью ленточных транспортеров являются вертикальные транспортеры, которые называют нориями или элеваторами. Нории (элеваторы) применяют для подъема материала на высоту до 40 м. Они представляет собой бесконечную цепь (ленту), на которой закреплены металлические ковши. Скорость движения (цепи) ленты до 1,5 м/с. Все устройство заключают в металлический кожух. Схема устройства нории (элеватора) приводится на рисунке 2.2.
Рисунок 2.2 – Схема устройства элеватора:
1 – кожух; 2 – цепь или лента; 3,5 – барабаны или цепные блоки; 4 – ковши.
Транспортеры размещают в помещениях, галереях, шахтах, под навесами или на открытых площадях.
Пневматический транспорт применяют для транспортировки сыпучих материалов в потоке газа по трубам. Системы пневмотранспорта могут работать под разрежением (рисунок 2.3) или избыточным давлением (рисунок 2.4).
Рисунок 2.3 – Схема устройства пневматического транспорта, работающего под разрежением:
1 – приемное устройство; 2 – всасывающий трубопровод; 3 – циклон; 4, 6 – трубопровод; 5 – пылеулавливатель; 7 – вентилятор (вакуум – насос);
8 – выброс воздуха; 9 – шлюзовый затвор
28

Рабочим газом в системах пневмотранспорта в основном является воздух. Для транспортирования взрывопожароопасных материалов при необходимости может применяться инертный газ. Движение рабочего газа обеспечивается вентилятором, вакуум-насосом или компрессором. Скорость газа в системах пневмотранспорта находится в пределах от 8 до 35 м/с и выбирается так, чтобы скорость газа была выше скорости осаждения частиц, т.к. частицы материала должны перейти во взвешенное состояние и унестись потоком газа.
Рисунок 2.4 – Схема устройства пневматического транспорта, работающего под давлением:
1 – вентилятор; 2 – ресивер воздуха; 3 – бункер с материалом; 4 – нагнетательный воздуховод; 5 – циклон; 6 – пылеулавливатель;
7 – выброс воздуха; 8 – шлюзовый затвор.
Горючую среду в устройствах для транспортирования твердых материалов образуют: горючий транспортируемый материал; пыль, выделяемая в результате транспортировки материала; горючие отложения, образуемые перемещаемыми материалами; транспортерные ленты. На транспортерах и элеваторах находится значительное количество равномерно распределенного материала, но при нарушении режима работы, количество материала в каком-либо месте может резко увеличиться, например, в месте разгрузки при отказе разгрузочного устройства. Часть транспортируемого материала переходит в помещение в виде взвешенной пыли, а затем оседает на различных поверхностях. Часть же материала просыпается на пол. Выделение пыли наиболее интенсивно происходит в местах загрузки, пересыпания, разгрузки, при прохождении ленты через направляющие ролики.
Для процессов транспортирования твердых материалов свойственны следующие источники зажигания: тепло трения и удара; тепловое проявление электрической, химической энергий (самовозгорание транспортируемых материалов); неосторожное обращение с огнем. Но все же основной причиной пожаров в устройствах для транспортирования является тепло, выделившееся в результате трения или удара (при перегрузке или заклинивании ленты происходит ее интенсивное нагревание, что может привести к ее воспламенению).
Повышенную пожарную опасность представляют системы пневмотранспорта, в виду того, что транспортировка горючих материалов производится в особо опасном измельченном состоянии и есть возможность образования горючих концентраций пыли как в системах, так и объеме производственного поме-
29
щения. Системам пневмотранспорта свойственны источники зажигания от теплового проявления механической энергии, вызванного трением и ударом, а также от искровых разрядов статического электричества (особенно при транспортировке по трубам из неметаллических материалов).
Системы пневмотранспорта способствуют распространению пожара, т.к. имеет значительную протяженность транспортных коммуникаций, переходят из помещения в помещение, в том числе через противопожарные преграды зданий и сооружений. При пожаре в длинных наклонных галереях или вертикальных шахтах возникает сильная тяга, способствующая интенсивному распространению пожара.
2.1.1Требования пожарной безопасности процессов транспортирования твердых материалов
Специфические требования по обеспечению пожарной безопасности процессов транспортирования твердых материалов (регламентируют [22]):
−конвейеры должны иметь предохраняющие устройства, отключающие приводы при перегрузке;
−конвейеры, транспортирующие порошкообразные пылящие материалы, а также материалы, выделяющие пары и газы, или материалы с высокой температурой, должны оборудоваться системами пылеподавления, вентиляции или аспирации и тепловой защитой в зависимости от физико-химических свойств материалов и конструкции конвейера;
−при обосновании необходимо применять закрытые транспортеры;
−при необходимости ленточные конвейеры должны быть оснащены магнитными металлоулавливателями (электромагнитными сепараторами) для удаления металлических включений в пунктах перегрузки. Конвейеры, оборудованные магнитными металлоулавливателями, должны иметь блокировку, исключающую пуск конвейера при отключенном металлоулавливателе;
−необходимо осуществлять контроль натяжения цепей и транспортерных лент. Пробуксовка ленты конвейера должна устраняться соответствующей натяжкой ленты натяжными устройствами после очистки барабанов и ленты. Подсыпать канифоль и другие материалы в целях устранения пробуксовки ленты запрещается;
−приводы наклонных пластинчатых конвейеров должны быть оборудованы автоматическими тормозными устройствами, исключающими обратный ход механизма при обрыве цепи;
−недопустимы перегрузка, перекосы и завалы транспортерных лент как основные причины заклинивания транспортеров;
−для предупреждения воспламенения транспортерной ленты приводные станции конвейеров должны быть оборудованы тепловыми датчиками, сблокированными с приводом конвейера;
−для исключения перегрева подшипников необходимо своевременно контролировать их температуру и своевременно смазывать;
30