
- •К 70-летию Фирмы ОРГРЭС
- •70 лет на передовых рубежах энергетики
- •Разработка и осуществление мероприятий по повышению надежности энергосистем
- •Опыт организации пусконаладочных работ при внедрении АСУ ТП энергоблока ПГУ-450Т Северо-Западной ТЭЦ
- •Опыт внедрения технологических функций АСУ ТП на энергоблоке ПГУ-450Т Северо-Западной ТЭЦ
- •Разработка и эксплуатационная проверка алгоритма аварийной разгрузки энергоблоков 200 МВт Псковской ГРЭС
- •Cовершенствование управления топочным процессом и режимных карт энергетических котельных агрегатов
- •Влияние изменений основных показателей непроектных углей на работу узлов и агрегатов пылеугольных тепловых электростанций
- •Анализ причин повреждения экранных труб поверхностей нагрева котла ТПЕ-208
- •Причины повреждений и статистика по отказам трубопроводов ТЭС
- •Вакуумные выключатели в сетях 6, 10 кВ
- •Пути повышения надежности работы арматуры высоких параметров ТЭС
- •Использование отечественных и зарубежных приборов инфракрасной техники в энергетике
- •О нормировании потерь электроэнергии в электрических сетях
- •Об учете электроэнергии в электрических сетях ПЭС
- •О проведении энергетического обследования ПЭС
- •ЭНЕРГОХОЗЯЙСТВО ЗА РУБЕЖОМ
- •Парогазовые электростанции США (статистика за 2001 г.)

Cовершенствование управления топочным процессом и режимных карт энергетических котельных агрегатов
Левит Г. Т., êàíä. òåõí. íàóê
ОАО “Фирма ОРГРЭС”
В работах [1, 2] обращалось внимание на то, |
Èç òàáë. 1 видно, что изменение в организации |
||
что режимные карты часто не содержат необходи- |
топочного режима при изменении нагрузки не |
||
мой информации по ведению режима работы топ- |
конкретизируется – для диапазона нагрузок |
||
ки и пылесистем. В порядке иллюстрации этого |
100 – 70% номинальной выбор степени открытия |
||
шиберов на разные ветви воздушного тракта пре- |
|||
рассмотрим режимную карту котла ПК-14 одной |
|||
доставляется машинисту котла. Причем, не ясно, |
|||
из электростанций, приведенную в òàáë. 1. Котел |
|||
чем он должен руководствоваться. Не ясно также, |
|||
оснащен четырьмя молотковыми мельницами |
ñ |
||
с какой целью на всех параллельных ветвях шибе- |
|||
шахтным сепаратором. Пылевоздушная смесь |
â |
||
ры рекомендуется поддерживать в частично при- |
|||
топку вводится через открытые амбразуры |
ñî |
||
крытом положении. Если не обсуждать целесооб- |
|||
|
|
||
шлицами вторичного воздуха. Кроме того, воздух |
разность того или иного подвода воздуха в топку, |
||
подается в топку через задние шлицы и шлицы хо- |
правильней было бы полностью открыть шиберы |
||
лодной воронки. |
|
на холодную воронку, где степень открытия наибо- |
Ò à á ë è ö à 1
' ! 1 ' , " / , , !
|
|
|
Молотковая мельница |
|
|
|||
Параметр |
|
|
|
|
|
|
|
|
1 |
|
2 |
|
|
3 |
|
4 |
|
|
|
|
|
|
||||
|
|
|
|
|
|
|
|
|
Нагрузка котла при Ð = 100 êãñ ñì2, ò ÷ |
150 |
|
170 |
|
|
190 |
|
210 |
Давление пара, кгс см2: |
|
|
|
|
|
|
|
|
в барабане |
|
|
|
100 |
– 110 |
|
|
|
перегретого |
|
|
|
90 – 100 |
|
|
||
|
|
|
|
|
|
|
|
|
Температура перегретого пара, °С |
|
|
|
520 |
– 540 |
|
|
|
|
|
|
|
|
|
|
|
|
Давление питательной воды, кгс см2 |
|
|
|
140 |
|
|
||
Температура питательной воды, °С |
|
|
|
210 |
– 215 |
|
|
|
|
|
|
|
|
|
|
|
|
Загрузка электродвигателей питателей, А |
3 – 4 |
|
|
|
|
4 – 5 |
||
|
|
|
|
|
|
|
|
|
Давление воздуха за ДВ, кгс м2 |
370 |
|
420 |
|
|
470 |
|
520 |
Перепад воздуха на мельницы, мм вод. ст. |
|
|
|
10 |
– 20 |
|
|
|
|
|
|
|
|
|
|
|
|
Содержание O2 за пароперегревателем, % |
|
|
|
5,0 |
– 6,0 |
|
|
|
|
|
|
|
|
|
|
|
|
Температура воздуха, °С: |
|
|
|
|
|
|
|
|
холодного |
30 |
|
30 |
|
|
30 |
|
30 |
горячего за ВЗП |
240 |
|
245 |
|
|
250 |
|
255 |
|
|
|
|
|
|
|
|
|
Температура дымовых газов, °С: |
|
|
|
|
|
|
|
|
за пароперегревателем |
420 |
|
430 |
|
|
440 |
|
450 |
за первой ступенью ВЗП (уходящих газов) |
140 |
|
145 |
|
|
150 |
|
155 |
|
|
|
|
|
|
|
|
|
Разрежение, кгс м2: |
|
|
|
|
|
|
|
|
в топке |
5 – 6 |
|
5 – 6 |
|
|
5 – 6 |
|
5 – 6 |
перед дымососом |
120 |
|
130 |
|
|
140 |
|
150 |
|
|
|
|
|
|
|
|
|
П р и м е ч а н и я : 1. Число работающих мельниц не менее трех. 2. Шиберы под холодную воронку открывать на 40 – 50%. 3. Шиберы на верхние шлицы открывать на 20 – 30%. 4. Шиберы на задние шлицы открывать на 10 – 20%. 5. Слой топлива устанавливать минимально возможным.
2003, ¹ 4 33

льшая, и увеличить степень открытия шиберов на других параллельных ветвях.
Соответственно можно было бы снизить давление воздуха за вентилятором, т.е. снизить затраты электроэнергии и переток воздуха через неплотности воздухоподогревателя в газовый тракт. Однако все это можно было бы осуществить при неполном открытии шиберов первичного воздуха на мельницы. Во всяком случае, указания по поводу обеспечения достаточного диапазона управления подачей первичного воздуха в мельницы должны были бы присутствовать в режимной карте.
Режимная карта, приведенная в табл. 1, относится к котлу, плохо подготовленному к работе на непроектном кузнецком угле. Из отчета об испытаниях этого котла следует, что потери тепла с механическим недожогом на кузнецком длиннопламенном угле находятся на уровне 4%. Одной из причин является, на наш взгляд, недостаточно тонкое измельчение топлива (указание о перепаде на измерительном устройстве первичного воздуха весьма расплывчато). Другая причина – неоправданно затянутая организация процесса горения (подвод значительной доли воздуха вдали от места ввода в топку пыли через задние шлицы и в холодную воронку). О последнем, в частности, свидетельствует низкое значение NOx – около 350 мг м3, несмотря на сравнительно большой избыток воздуха. Отчасти затяжка процесса горения – это стремление повысить за счет ухудшения организации топочного режима температуру перегретого пара (в опытах она составляла лишь около 500°С). Повышение температуры пара путем наращивания поверхности пароперегревателя, по-видимому, малопродуктивно – низка температура газов за перегревателем. Повысить температуру газов на выходе из топки и соответственно температуру пара можно было бы путем увеличения числа работающих мельниц. Подъем температуры на выходе из топки при этом обусловлен более полным заполнением поперечного сечения топки факелом отдельных горелок и, в результате, перемещением вверх ядра горения.
Увеличение числа работающих мельниц способствовало бы уменьшению потерь тепла с механическим недожогом благодаря утонению пыли (возможности работать с меньшими скоростями в шахтах мельниц). Этому способствовал бы и отказ от непроизводительной подачи воздуха в холодную воронку в условиях маловероятной сепарации пыли. Однако здесь опять-таки видна неподготовленность котла к сжиганию высококалорийного каменного угля, а именно, излишняя производительность питателей топлива Не ясно, правда, каков коэффициент готовности Êã пылесистем к работе – при грамотной организации ремонта вполне возможно достижения Êã = 0,95, т.е. при четырех пылесистемах все они могут находиться в работе 80% времени [3].
В режимной карте, приведенной в табл. 1, недостаточно указаний не только по распределению воздуха по параллельным потокам, но и по изменению общего расхода воздуха в функции нагрузки – ничем не подкрепляется указание о поддержании во всем диапазоне нагрузок О2 = 5 6% (ïï = 1,3 1,4) против обычного, учитывающего сокращение доли присосов в топку, уменьшения избытка воздуха по мере роста нагрузки.
Даже при исправно работающих кислородомерах следовало бы рекомендовать контроль за расходом воздуха по перепаду на воздухоподогревателе, а вместо давления за дутьевым вентилятором контролировать давление за воздухоподогревателем и одновременно давление за регулирующими шиберами по каждому потоку вторичного воздуха. Приведенные значения давления за вентилятором плохо корреспондируются с нагрузкой котла: при изменении нагрузки в 1,4 раза давление меняется также в 1,4 раза, а должно было бы при неизменном положении шиберов измениться в 2 раза, т.е. по мере роста нагрузки шиберы открывались. Вопрос: почему это не показано? Точно так же разрежение перед дымососом должно было измениться пропорционально квадрату изменения нагрузки, т.е. в 2 раза, а изменяется в 1,25 раза.
Отвлекаясь от рассмотрения режимной карты для конкретного котла, следует отметить общие трудности управления подачей воздуха в топку при наличии нескольких параллельных потоков, управляемых в функции нагрузки по разным законам. Дело в том, что изменение подачи воздуха на одну из ветвей (открытие или прикрытие шиберов на эту ветвь) приводит к изменению давления за воздухоподогревателем и изменению расхода на другие ветви. В этих условиях попытка организовать желаемое распределение воздуха занимает даже при наличии соответствующих измерений расхода или давления воздуха примерно 1 ч. Машинист котла таким временем обычно не располагает, поэтому организуется приблизительное распределение воздуха. В зарубежной практике при многих параллельных потоках воздуха применяется авторегулирование со стабилизацией давления за воздухоподогревателем. В этом случае изменение подачи воздуха на один из потоков не привносит изменений расхода по другим.
В принципе, наличие нескольких, разных по назначению и по закону изменения в функции нагрузки, потоков воздуха – свидетельство слабости в организации топочного режима. Оптимально, когда для котла с пылесистемами прямого вдувания имеются потоки первичного и вторичного воздуха и схема организации топочного режима позволяет получить приемлемые значения эмиссии NOx без организации ступенчатого сжигания. В этом случае для организации воздушного режима достаточно в помощь дутьевым вентиляторам
34 |
2003, ¹ 4 |

иметь общие шиберы вторичного воздуха, которые управляются по положению регулировочных шиберов первичного воздуха на мельницы [2].
Пример режимной карты котла ТП-170, оснащенного тремя молотковыми мельницами с шахтным сепаратором и пылегазовыми горелками, рассмотренный в [4], приведен в òàáë. 2. Особенность этой режимной карты в том, что в ней показаны условия обеспечения работы котла при разной доле сжигаемого газа. Причем, доля эта определена не процентом газа, как это часто делается, а паровой нагрузкой, обеспечиваемой за счет сжигания угля: 100%, 120 т ч, 60 т ч, 0. Это для случая, когда предпочтительно регулирование нагрузки
Ò à á ë è ö à 2
газом. Может быть и другая схема, когда базовой является нагрузка на газе, а регулирование ведется углем. Очевидно, что управлять котлом в последнем случае сложнее.
Принятые значения нагрузки, обеспечиваемые при работе на смеси за счет сжигания угля, могут быть и другими, но удобство принятых значений в том, что сохраняется неизменным режим работы пылесистем. Меняется лишь их число – две или одна пылесистема. Как и в предыдущем примере, работа котла на всех установленных пылесистемах не рассматривается в связи с чрезмерной производительностью питателей топлива на непроектном кузнецком угле. Доля нагрузки за счет сжигания
' ! 9 6 " / |
, ) , " |
|
|
|
|
|
|
|
||||||||||||
|
|
|
|
|
|
|
|
|
|
|
|
|
|
|
|
|
|
|
||
|
|
|
|
|
|
|
|
Режим работы котла |
|
|
|
|
|
|
|
|||||
Параметр |
|
|
|
|
|
|
|
|
|
|
|
|
|
|
|
|
|
|
|
|
|
|
|
|
|
120 ò ÷ ïàðà çà |
|
|
60 ò ÷ ïàðà |
|
|
|
|
|
|
||||||
|
100%-ная нагрузка на угле |
|
|
|
100%-ная нагрузка на газе |
|||||||||||||||
|
счет сжигания угля |
|
за счет сжигания угля |
|||||||||||||||||
|
|
|
|
|
|
|
|
|
|
|
|
|||||||||
|
|
|
|
|
|
|
|
|
|
|
|
|
|
|
|
|
|
|
|
|
Нагрузка котла Äê, |
100 |
120 |
140 |
160 |
180 |
140 |
160 |
180 |
100 |
|
120 |
|
140 |
160 |
180 |
100 |
120 |
140 |
160 |
180 |
ò ÷ |
|
|
||||||||||||||||||
|
|
|
|
|
|
|
|
|
|
|
|
|
|
|
|
|
|
|
|
|
|
|
|
|
|
|
|
|
|
|
|
|
|
|
|
|
|
|
|
|
|
Расход газа Qãàç, ì3 ÷ |
|
|
0 |
|
|
1750 |
3500 |
5250 |
3500 |
|
5250 |
|
7000 |
8700 |
10300 |
8700 |
10 300 |
11 900 |
13 500 |
15 100 |
Число работающих |
|
|
|
|
|
|
|
|
|
|
|
|
|
|
|
|
|
|
|
|
газовых горелок nã.ã, |
- |
- |
- |
- |
- |
1 |
1 |
2 |
2 |
|
2 |
|
3 |
3 |
3 |
3 |
3 |
3 |
3 |
3 |
øò. |
|
|
|
|
|
|
|
|
|
|
|
|
|
|
|
|
|
|
|
|
|
|
|
|
|
|
|
|
|
|
|
|
|
|
|
|
|
|
|
|
|
Давление газа перед |
- |
- |
- |
- |
- |
|
|
|
|
|
|
0,8 |
|
|
|
|
|
|
||
котлом Ðãàç, êãñ ñì2 |
|
|
|
|
|
|
|
|
|
|
|
|
||||||||
Давление газа перед |
|
|
|
|
|
|
|
|
|
|
|
|
|
|
|
|
|
|
|
|
горелками Ð ãîð, |
- |
- |
- |
- |
- |
340 |
1350 |
770 |
340 |
|
770 |
|
780 |
960 |
1320 |
960 |
1320 |
1720 |
2250 |
2900 |
êãñ ì2 |
|
|
|
|
|
|
|
|
|
|
|
|
|
|
|
|
|
|
|
|
Давление воздуха пе- |
|
|
|
|
|
|
|
|
|
|
|
|
|
|
|
|
|
|
|
|
ред газовыми горел- |
- |
- |
- |
- |
- |
33 |
47 |
40 |
33 |
|
40 |
|
40 |
42 |
46 |
42 |
46 |
52 |
93 |
150 |
êàìè (Ðâ) ãîð, êãñ ì2 |
|
|
|
|
|
|
|
|
|
|
|
|
|
|
|
|
|
|
|
|
Число работающих |
2 |
2 |
2 |
2 |
2 |
2 |
2 |
2 |
1 |
|
1 |
|
1 |
1 |
1 |
- |
- |
- |
- |
- |
мельниц nì, øò. |
|
|
||||||||||||||||||
|
|
|
|
|
|
|
|
|
|
|
|
|
|
|
|
|
|
|
|
|
Перепад на шайбах |
|
|
|
|
|
|
|
|
|
|
|
|
|
|
|
|
|
|
|
|
первичного воздуха |
30 |
36 |
42 |
50 |
64 |
|
|
|
36 |
|
|
|
|
- |
- |
- |
- |
- |
||
hì, êãñ ì2 |
|
|
|
|
|
|
|
|
|
|
|
|
|
|
|
|
|
|
|
|
Содержание О2 â ãà- |
|
|
|
|
|
|
|
|
|
|
|
|
|
|
|
|
|
|
|
|
зах во второй ступе- |
5,4 |
5,2 |
5,0 |
4,8 |
4,8 |
4,4 |
4,2 |
4,2 |
4,6 |
|
4,4 |
|
4,2 |
4 |
4 |
4 |
3,7 |
3,6 |
3,5 |
3,5 |
ни экономайзера, % |
|
|
|
|
|
|
|
|
|
|
|
|
|
|
|
|
|
|
|
|
|
|
|
|
|
|
|
|
|
|
|
|
|
|
|
|
|
|
|
|
|
Перепад давления |
|
|
|
|
|
|
|
|
|
|
|
|
|
|
|
|
|
|
|
|
воздуха на воздухо- |
25 |
38 |
56 |
80 |
88 |
48 |
70 |
78 |
20 |
|
29 |
|
44 |
64 |
76 |
16 |
24 |
38 |
55 |
71 |
подогревателе Pâ.ï, |
|
|
||||||||||||||||||
|
|
|
|
|
|
|
|
|
|
|
|
|
|
|
|
|
|
|
|
|
êãñ ì2 |
|
|
|
|
|
|
|
|
|
|
|
|
|
|
|
|
|
|
|
|
П р и м е ч а н и я : 1. Для всех режимов работы котла: давление перегретого пара Pïå= 100 êãñ ñì2; температура перегретого пара tïå = 510 + 10 °С; температура питательной воды tïâ = 215 °С; температура в шахтах мельниц tì = 70 90°С; разрежение в
верху топки Sâ. ò = 3,0 4,0 êãñ ì2; температура воздуха на входе в воздухоподогреватель tâ = 30 °С. 2. Оптимальное сочетание работающих угольных и газовых горелок – симметричное (при двух – А и В, при одной – Б). 3. Давление вторичного воздуха на работающие угольные горелки и соответственно общий расход воздуха устанавливаются по содержанию О2 или на основе косвенного показателя – перепада давления воздуха на воздухоподогревателе. На неработающие горелки (угольные и газовые) давление воздуха устанавливается на уровне минус 5 мм вод.ст. На мазутные форсунки воздух должен быть закрыт. 4. Во всем диапазоне нагрузок пароохладители, как правило, обеспечивают достаточный диапазон регулирования температуры перегретого пара. При необходимости для снижения перегрева следует увеличить скорости на выходе из работающих горелок, прикрыв подачу воздуха на неработающие, а также несколько увеличить общий расход воздуха. Для повышения КПД котла (снижения температуры уходящих газов) стремиться в меньшей степени использовать поверхностный пароохладитель, чем впрыскивающий. 5. Для повышения КПД котла при сжигании угля (уменьшения горючих в уносе) стремиться к максимальному сокращению расхода первичного воздуха. 6. Для сокращения расхода электроэнергии на собственные нужды при сжигании газа степень открытия направляющих аппаратов вентиляторов поддерживать в соответствии со степенью открытия шиберов перед горелками, сохраняя последнюю в диапазоне 50 – 80%. 7. Нагрузка котла указана при проектной температуре питательной воды (tïâ) 215°С и проектных параметрах пара. При пониженной tïå показания паромера уменьшить (разделить) на коэффициент Ê: 1,11 (tïâ = 160°Ñ); 1,09 (170°Ñ); 1,07 (180°Ñ); 1,05 (190°Ñ); 1,03 (200°Ñ); 1 (215°Ñ).
2003, ¹ 4 |
35 |

угля определяется по расходу газа. Общий расход воздуха на котел определяется помимо кислородомера по перепаду давления воздуха на воздухоподогревателе. Из индивидуальных потоков воздуха определен расход на мельницы и на газовые горелки. На угольные горелки количество (давление) воздуха не указывается и определяется как замыкающий член воздушного баланса. Малое сопротивление тракта первичного воздуха благодаря эжектирующему действию горелок позволяет при всех режимах обходиться без использования (прикрытия) имеющихся общих дроссельных шиберов вторичного воздуха.
Конструкция горелок в сочетании с четкой организацией топочного режима позволила получить при работе на угле и смеси угля с газом (при доле газа около 50%) потери тепла с механическим недожогом на уровне 1%, т.е. на 2% ниже, чем на других котлах ТЭЦ с горелками в виде амбразур.
Дополнительно на 1% ниже потери тепла с уходящими газами благодаря возможности работы с меньшими избытками воздуха без химического недожога. Ниже и значения Nox: 350 – 400 против 500 мг м3 при работе на угле и смеси и 120 против 300 мг м3 при работе на газе.
Список литературы
1.ÐÄ 34.25.514-96. Методические указания по составлению режимных карт котельных установок и оптимизации управления ими. М.: СПО ОРГРЭС, 1998.
2.Левит Г. Т. Режимные карты и оптимизация управления котельными установками. – Электрические станции, 1998, ¹ 5.
3.Работы Союзтехэнерго по усовершенствованию пылеприготовительного оборудования электростанций. – Теплоэнергетика, 1979, ¹ 3.
4.Оптимизация горелочных устройств для сжигания твердого топлива и природного газа применительно к котлам с шахтными мельницами Левит Г. Т., Ицкович В. Я., Соловьев А. К. и др. – Электрические станции, 2003, ¹ 1.
Влияние изменений основных показателей непроектных углей на работу узлов и агрегатов пылеугольных тепловых электростанций
Векслер Ф. М., èíæ., Говсиевич Е. Р., Алешинский Р. Е., кандидаты эконом. наук
ОАО “Фирма ОРГРЭС” – ОАО “НИИ экономики энергетики” – ЗАО “Стин Холдинг”
В складывающихся условиях рыночной экономики большинство российских тепловых электростанций (ТЭС) вынуждены искать возможность использования не только проектных, но и других марок углей с близкими качественными характеристиками. При этом сохраняется и даже возрастает необходимость обеспечить эффективность производства электроэнергии без нанесения ущерба оборудованию электростанции при постоянно возрастающих требованиях по сокращению вредных выбросов. Угли, на которых удается приблизиться к соблюдению указанного комплекса требований, называют взаимозаменяемыми, так как их теплотехнические характеристики незначительно отли- чаются от проектных. При использовании на ТЭС взаимозаменяемых углей для поддержания проектного уровня эффективности производства энергии не требуется дорогостоящей реконструкции основного и вспомогательного котельного оборудования.
При длительной эксплуатации отечественных электростанций часто наблюдаются отклонения теплотехнических характеристик угля от проектных.
Влияние отдельных теплотехнических характеристик углей (или их небольших наборов, на-
пример, Vdaf, Wr, Ar, Qír ) на работу котла и его уз-
лов можно оценить известными расчетными методами, например [1]. Однако оценить влияние всего известного набора теплотехнических характеристик углей и тем более их неопределенных и нестабильных смесей на показатели пылеугольных электростанций очень трудно не только рас- четами, но и экспертными оценками, полученными на основании накопленного эксплуатационного опыта.
В настоящей статье делается попытка хотя бы качественно учесть влияние изменения основных теплотехнических характеристик углей по сравнению с проектными характеристиками на работу как электростанции в целом, так и отдельных узлов и систем оборудования.
Далее последовательно рассматривается влияние изменения основных характеристик угля на условия работы ТЭС. Влияние качественных показателей угля на конкретные узлы и агрегаты ТЭС схематично показано на рисунке.
Выход летучих веществ Vdaf является одним из важнейших показателей теплотехнических характеристик углей, определяющим его вид (марку) и реакционную способность угля. Данный показа-
36 |
2003, ¹ 4 |
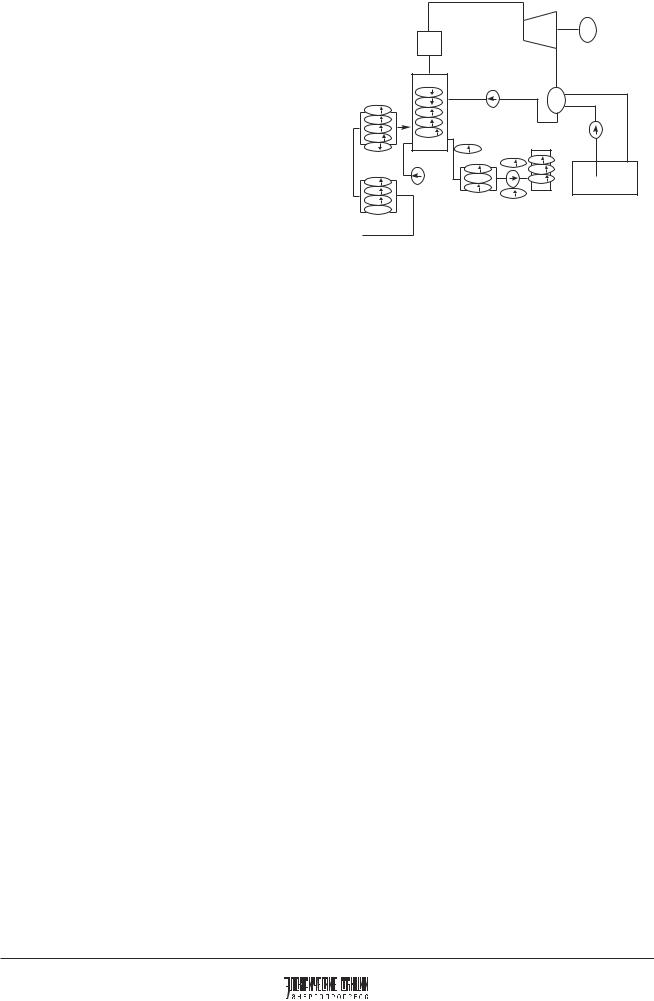
тель показывает способность воспламенения угля и устойчивость его горения в топочной камере котлоагрегата. При определенных значениях V daf появляется необходимость использовать для подсветки факела мазут или газ.
От выхода летучих веществ зависит скорость взаимодействия угля с кислородом воздуха, возрастающая с увеличением температуры реагирующих компонентов, т.е. реакционная способность угля, и этот показатель определяет конструктивные особенности топок и горелок котлов [1], требуемую тонкость размола углей (R90, R200) при факельном сжигании [2], а также склонность углей к окислению и самовозгоранию при хранении на складах и в бункерах [3].
Одна из важнейших проблем сушки и размола углей – обеспечение взрывобезопасности этих процессов [4], которая во многом зависит от объема выхода летучих веществ и от теплоты сгорания. В объем летучих веществ, по методике их определения, входят не только горючие летучие газы (в основном, углеводороды), но и негорючие газы, например, азот и водяные пары.
По [4] большинство марок углей Канско-Ачин- ского бассейна относится к третьей группе взрываемости. Поэтому эти угли рекомендуется использовать в системах пылеприготовления с газовой сушкой, в которых содержание кислорода в сушильном агенте не превышает 16%. А угли Кузнецкого или Воркутинского бассейнов марок Г и Д относятся ко второй и третьей группам взрываемости, поэтому они могут использоваться в системах пылеприготовления как с газовой сушкой (в которых содержание кислорода в сушильном агенте не превышает 16%), так и с воздушной сушкой (О2 = 21%) и с разными типами мельниц.
Рабочая влажность угля W r является одной из его важнейших качественных характеристик и состоит из двух составляющих: аналитической постоянной, и внешней, зависящей от влажности и температуры внешней среды.
Процесс сушки топлива в системах пылеприготовления определяется, в основном, приведенной влажностью W ï. Допустимый диапазон отклонения от проектных значений составляет (5 10)%. Значительное уменьшение приведенной влажности по сравнению с проектной (более чем на 15 20%) повышает температуру угольной пыли на выходе из мельницы, что в соответствии с ограничениями по [4] требует принятия специальных обязательных мер для обеспечения взрывобезопасной работы систем пылеприготовления.
Увеличение внешней влаги приводит прежде всего к изменению (ухудшению) сыпучих свойств углей, затруднениям при разгрузке топлива и прохождении его по тракту топливоподачи. Это может потребовать значительного увеличения обслужи-
|
|
5 |
|
|
|
|
|
|
|
|
|
6 |
8 |
|
4 |
|
|
|
|
|
|
3 |
|
15 |
|
|
9 |
|
Q |
|
|
|
|
|
|
|
|
|
|
7 |
|
2 |
V |
|
|
|
|
|
V – |
W |
|
|
|
|
|
W – |
A |
|
|
|
|
11 |
A – |
|
|
|
|
||
CaO |
|
|
|
|
||
HGI + |
|
|
|
|
|
|
|
|
|
|
|
|
|
R + |
|
S – |
|
|
|
12 |
|
|
14 |
|
|
||
|
17 |
W – |
A – |
|||
|
|
|
||||
|
W + |
|
SOx |
– |
||
|
|
|
|
|||
V – |
|
S+ |
|
|
NOx – |
|
|
A – |
|
|
|
10 |
|
W – |
|
|
A – |
13 |
||
|
16 |
|
|
|||
A – |
|
|
|
|
||
|
|
|
|
|
R+
1
/$! + , # ! + 3:) &
% . .- . ;
1 – топливоподача; 2 – пылеприготовление; 3 – топка котлоагрегата; 4 – пароперегреватель; 5 – паропровод; 6 – паровая турбина; 7 – конденсатор; 8 – генератор; 9 – отводящий водовод; 10 – водоем; 11 – циркулярный насос; 12 – подводящий водовод; 13 – дымовая труба; 14 – дымосос; 15 – насос; 16 – золоулавливатели; 17 – вентилятор
вающего персонала даже при использовании специальных систем виброили пневмообрушения.
В зимнее время, особенно при длительной транспортировке и повышенной влажности, может повышаться смерзаемость углей, что требует значительного увеличения производительности имеющихся размораживающих устройств, установки дополнительных размораживающих мощностей и еще более значительного увеличения обслуживающего и ремонтного персонала.
При повышенной, по сравнению с проектной, приведенной влажностью угля может быть ограничена сушильная производительность систем пылеприготовления, что, в свою очередь, приводит к увеличению влажности готовой пыли и к снижению надежности и экономичности ее сжигания в котлоагрегате.
Повышение влажности пыли особенно опасно для систем пылеприготовления с промежуточным бункером пыли, так как может приводить к ухудшению сыпучести пыли и к нарушению работы бункеров и питателей пыли.
Увеличение рабочей влажности углей при постоянной тепловой нагрузке котлов приводит к увеличению объемов водяных паров и скоростей дымовых газов в конвективных поверхностях нагрева. Такое повышение скоростей, с одной стороны, улучшает теплообмен в конвективных поверхностях нагрева, а, с другой стороны, усиливает их абразивный износ. Отрицательный эффект от абразивного износа конвективных поверхностей нагрева оценивается значительнее, чем положительный от улучшения теплообмена. Кроме того, увеличение объемов водяных паров может приводить
2003, ¹ 4 |
37 |
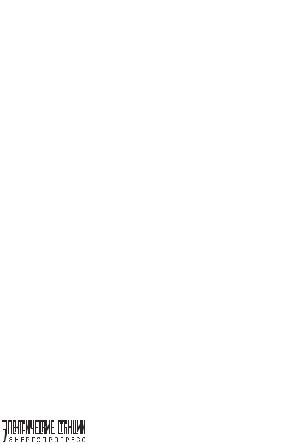
к ограничению производительности дымососов и |
золы. Поэтому обычно электростанции пользуют- |
|||||||
из-за этого – производительности котлов. |
ся фактическими данными о сжигании углей раз- |
|||||||
Одновременно |
увеличение |
относительной |
ной зольности и их влиянии на эксплуатацию обо- |
|||||
влажности дымовых газов может способствовать |
рудования. |
|
|
|
||||
улучшению работы электрофильтров (за счет из- |
При изменении топлива могут изменяться не |
|||||||
менения электрического сопротивления золы, что |
только свойства самой золы, но и связанные с ней |
|||||||
часто используется на электростанциях, сжигаю- |
составляющие как вредные (радиоактивность, со- |
|||||||
щих сухой многозольный экибастузский уголь), а |
держания фтора, хлора и абсорбированного золой |
|||||||
также и других золо- и сероулавливающих устано- |
бензапирена), обусловливающие усиление пробле- |
|||||||
вок. В конечном счете, это явление за счет лучше- |
мы выбросов вредных веществ, так и относитель- |
|||||||
го улавливания может способствовать снижению |
но полезные, делающие золу товарным продуктом |
|||||||
вредных выбросов в атмосферу и соответственно- |
для получения, например, редкоземельных эле- |
|||||||
му уменьшению экологических платежей. |
ментов (типа германия), или соединений СаО, по- |
|||||||
Рабочая зольность угля Ar также является важ- |
зволяющих использовать золу в сельском хозяйст- |
|||||||
ной качественной характеристикой, состоящей из |
ве или строительстве. |
|
|
|
||||
двух составляющих: “материнской”, прочно свя- |
По экспертным оценкам, основанным на име- |
|||||||
занной с горючей частью (прежде всего с углеро- |
ющемся опыте эксплуатации мощных котлоагре- |
|||||||
дом) и внешней, изменяющейся от внешних усло- |
гатов, каждый процент увеличения зольности или |
|||||||
вий, – организации и механизмов добычи, распо- |
влажности углей ориентировочно приводит: |
|||||||
ложения мест добычи и других условий. |
к снижению КПД на 0,05 – 0,15%; |
|||||||
Кроме рассмотренного влияния на теплоту сго- |
к увеличению дополнительного расхода топли- |
|||||||
рания и через нее на показатели котлов, изменение |
ва для поддержания заданной мощности на 0,2 – |
|||||||
рабочей зольности может привести к изменениям |
0,5 г на выработанный 1 кВт ч; |
|
|
|||||
и работы общестанционного оборудования ТЭС. |
к увеличению расхода электроэнергии на соб- |
|||||||
Повышение общей зольности обычно приво- |
||||||||
ственные нужды на 0,07 – 0,13%; |
||||||||
дит к пропорциональному или (при повышении |
||||||||
к увеличению расхода мазута на 0,15 – 0,4% на |
||||||||
доли абразивных составляющих SiO2, Al2O3 è äð.) |
||||||||
каждую тонну сжигаемого топлива; |
||||||||
даже более сильному износу оборудования ТЭС: |
к дополнительному останову энергоблока на |
|||||||
системы транспортировки угля, дробильного угле- |
||||||||
ремонт до 60 ч в год. |
|
|
|
|
||||
размольного оборудования, прежде всего быстро- |
|
|
|
|
||||
Теплота сгорания сухой беззольной массы уг- |
||||||||
изнашивающихся |
элементов мельниц (шаров у |
|||||||
r |
|
|
|
|||||
шаровых, бил у молотковых, валков у среднеход- |
ëåé Qí в пределах одного месторождения, особен- |
|||||||
но при малом содержании карбонатов (СО2)êàðá è |
||||||||
ных мельниц и рабочих лопаток у мельниц-венти- |
||||||||
серы обычно остается постоянной, т.е. |
||||||||
ляторов), а также брони у всех типов мельниц с се- |
||||||||
|
|
|
|
|
||||
параторами и пылепроводов, особенно их гибов. |
Q daf Q r |
|
100 |
|
. |
|||
Кроме этого, увеличение количества золы приво- |
|
|||||||
i |
|
W r |
A r |
|||||
|
|
|
100 |
|||||
дит к увеличению износа конвективных поверхно- |
|
|
t |
|
|
|||
|
|
|
|
|
||||
стей нагрева котлов и лопаток дымососов. |
Изменение теплоты сгорания прежде всего свя- |
|||||||
Увеличение зольности затрудняет работу золо- |
||||||||
зано с изменением влажности или зольности углей |
||||||||
улавливающих установок и ухудшает экологиче- |
||||||||
или обоих этих показателей вместе. При снижении |
||||||||
ские показатели ТЭС. При сжигании углей наибо- |
||||||||
теплоты сгорания Qir, как было показано при ана- |
||||||||
льшая часть экологических платежей обычно при- |
||||||||
ходится на выбросы золы, превышающие норми- |
лизе изменения влажности угля, увеличивается |
|||||||
рованные показатели (предельно допустимые вы- |
влажность готовой пыли, ухудшаются характери- |
|||||||
бросы – ПДВ), и на хранение золошлакоотходов. |
стики ее воспламенения, повышается минималь- |
|||||||
Оценить такие затраты можно по изменению со- |
ная паропроизводительность котлов, при которых |
|||||||
держания золы с учетом эффективности золоулав- |
они могут устойчиво работать без дополнительной |
|||||||
ливающих установок [объем выбросов равен рабо- |
подсветки факела мазутом или газом. Значитель- |
|||||||
чей зольности, умноженной на (1 – )]. |
ное (более 10 – 15%) снижение теплоты сгорания |
|||||||
Кроме увеличения зольности, особенно силь- |
и соответственно паропроизводительности котло- |
|||||||
ный износ оборудования может вызвать повыше- |
агрегатов не всегда может быть компенсировано |
|||||||
ние абразивности золы за счет увеличения абра- |
подсветкой мазутом/газом или увеличением расхо- |
|||||||
зивных составляющих: SiO2, Fe2O3, Al2O3 è |
да угля. Следствием этого является уменьшение |
|||||||
СаО + MqO – в виде кварцевого песка, пиритных, |
располагаемой мощности ТЭС. |
|
|
|||||
колчеданных и гранитных включений. Принятые в |
В то же время из-за снижения максимальной |
|||||||
[1] характеристики абразивности золы углей (со- |
производительности систем пылеприготовления |
|||||||
отношения твердых и мягких составляющих) не |
по сушке и размолу падает максимально возмож- |
|||||||
всегда позволяют достаточно точно расчетным пу- |
ная паропроизводительность котлов. Обычно при |
|||||||
тем оценить влияние изменения |
абразивности |
этом снижаются температуры газов в топке и газо- |
||||||
|
|
|
|
|
|
|
||
38 |
|
|
|
|
|
2003, ¹ 4 |

ходах котлов, не выдерживаются расчетные параметры пара, снижается средняя эксплуатационная нагрузка котлов и, в конечном счете, ухудшаются все экономические показатели котлов и электростанций (увеличиваются потери тепла с механиче- ским недожогом и уходящими газами, уменьшается коэффициент полезного действия котлов, увеличивается удельный расход топлива на отпущенный 1 кВт ч, удельный расход электроэнергии на собственные нужды, возникает перерасход топлива).
При улучшении качества сжигаемого угля происходит в целом обратная картина и экономич- ность котла может в некоторых случаях даже улуч- шаться, но из-за повышения температуры газов в топке и газоходах повышается опасность шлакования топок и конвективных поверхностей нагрева котлов. На основании накопленного эксплуатационного опыта следует отметить, что ухудшение тех- нико-экономических показателей электростанций в целом и котлов, в частности, при ухудшении и нарушении стабильности качества углей происходит очень быстро и резко, а улучшение тех же показателей, даже при стабильном восстановлении качества углей, происходит значительно медленнее.
Процессы шлакования особенно опасны для котлов, у которых отсутствуют средства очистки поверхностей нагрева от возможных шлаковых отложений (например, отсутствуют системы водяной очистки или пушечной обдувки зашлакованных поверхностей). В результате шлакования вынужденно может снижаться нагрузка котлов и могут даже потребоваться дополнительные длительные остановы котлов для ручной очистки.
Для отдельных видов углей вероятность шлакования можно оценить по температурным характеристикам и химическому составу золы. Однако для попеременного сжигания углей с различными качественными характеристиками или их смесей не всегда можно оценить вероятность возникновения или усиления шлакования по характеристикам отдельных углей. Наиболее точно это можно оценить только по результатам опытных сжиганий, проводимых не менее одного-двух месяцев или при опытной эксплуатации котлов в течение нескольких месяцев или даже лет.
Опыт эксплуатации многих электростанций Дальнего Востока и европейской части России показывает: попеременное и обычно неорганизованное сжигание углей разного качества приводит к дополнительному снижению надежности и экономичности работы котлов по сравнению с показателями работы на самом худшем из сжигаемых углей за счет нарушений стабильности и оптимальности работы отдельных узлов и котлов в целом. Проблемы переменных и нестабильных режимов особенно остры при использовании для сжигания новых (малоизвестных) марок и месторождений углей.
Содержание серы S r определяет допустимую температуру уходящих газов за воздухоподогревателями котлов и тем самым конструкцию котлов, поскольку с увеличением содержания серы возрастает температура начала сернокислотной коррозии (точка росы H2SO4) металлических элементов воздухоподогревателей. В целях снижения сернокислотной коррозии приходится повышать температуру уходящих газов, а поскольку потери тепла с уходящими газами являются основной составляющей потерь в котлоагрегатах, данное обстоятельство оказывает отрицательное воздействие на КПД котлов и экономичность их работы в целом. Также требуется особый подход к конструктивным особенностям воздухоподогревателей и экономайзеров.
Содержание серы для котлов с пылевым сжиганием определяет количество выбросов вредных оксидов серы в атмосферу, размер экологических платежей, тип и производительность сероулавливающих установок. При отсутствии сероулавливающих установок небольшое связывание оксидов серы возможно за счет содержащихся в топливе или специально добавляемых оксидов СаО или ча- стичного растворения оксидов серы в установках мокрого золоулавливания.
Кроме отрицательного, содержание серы в топливе в небольших количествах может оказывать и положительное влияние, поскольку способствует улучшению улавливания золы в электрофильтрах и уменьшению ее выбросов в атмосферу.
Содержание азота Nr частично определяет количество вредных выбросов оксидов азота в атмосферу с дымовыми газами, уходящими из котла. Общее количество образовавшихся оксидов азота в котле можно разделить на две части: образующиеся из азота топлива и образующиеся из азота воздуха, которые по-разному зависят от максимальных температур газов, достигаемых в топках котлов, избытков воздуха в разных зонах топки, т.е. от технологии сжигания.
Если технологические резервы снижения оксидов азота в котлах исчерпаны, повышение содержания азота в топливе может потребовать значительных затрат на оплату штрафов за сверхнормативные выбросы или сооружение весьма дорогих азотоулавливающих установок.
Элементный состав золы обычно используют для экспертных оценок свойств золы: прежде всего, склонности к шлакованию и образованию твердых отложений на конвективных поверхностях нагрева, а также абразивных свойств золы, которые уже были рассмотрены ранее. Для отдельных видов углей, например, канско-ачинских, вероятность шлакования можно оценить по химическому составу золы, для чего обычно используют соотношение K/O (числитель – кислые; знаменатель – щелочные/основные составляющие) т.е.
2003, ¹ 4 |
39 |

K/O = (SiO2 + Al2O3 + TiO2) (ÑàÎ + + MqO + K2O + Na2O + Fe2O3).
Для углей других марок и месторождений разработка методов подобной оценки является вопросом дополнительного изучения.
Склонность к образованию твердых отложений на топочных и конвективных поверхностях нагрева оценивают по аналогичным соотношениям и по суммам содержания СаО + MqO и K2O + Na2О. Влияние СаО подробно описано далее. Влияние MqO близко, но менее ярко выражено, обычно изза его меньшей концентрации. Влияние K2O + Na2O еще менее выражено и обычно сказывается при редко встречающихся содержаниях более 5 – 7% (так называемые, “соленые” угли).
Содержание оксида кальция в золе, как уже отмечалось ранее, во многом определяет шлакующие свойства топлива и, главное, способность к образованию твердых трудноудаляемых отложений на конвективных поверхностях нагрева. Такие отложения начинают обычно образовываться при содержании СаО в золе более 13 – 15%.
Соединения оксида кальция с оксидами серы, углерода, железа при их взаимодействии с водой образуют гипсо- и цементноподобные трудноудаляемые отложения. Поэтому при содержании СаО
âзоле более 13 – 15% не рекомендуется применение мокрых систем золоулавливания, а для надежной работы гидро-, золо- и шлакоудаления с оборотной системой водоснабжения необходимо увеличение резервирования оборудования этих систем и увеличение плановых затрат на ремонт и замену этих элементов. При этом не рекомендуется допускать увеличение рН осветленной воды в таких гидросистемах более 9 – 10.
При повышенной щелочности золы и наличии
âней “вяжущих” элементов, т.е. при значительном содержании соединений СаО (25 – 40%), возникает возможность использования такой золы в сельском хозяйстве для раскисления почв и в строительстве в качестве наполнителей бетонов, особенно при дорожном строительстве.
Температурные характеристики золы (Òà, Òb,
Òñ ) (à – начало деформации; b – плавления полусферы; ñ – жидкоплавкого состояния растекания) связаны со способом определения этих характеристик и в последнее время мало используются. Более объективными показателями шлакующих и жидкоплавких состояний золы являются температура начала шлакования и температура начала нормального жидкого шлакоудаления, которые во многом определяют выбор способа и устройств шлакоудаления, а также конструкцию топок котлов [1], в первую очередь, температуру газов на выходе из топки перед тесными пучками труб, а также типы и конструкции средств очистки топоч- ных и конвективных поверхностей от шлаковых отложений.
Температура начала нормального жидкого шлакоудаления имеет особенно важное значение для котлоагрегатов с жидким шлакоудалением.
Коэффициент размолоспособности определяет способность углей к измельчению и соответственно размольную производительность систем пылеприготовления. В настоящее время данный коэффициент определяется по двум шкалам: по шкале ВТИ (Всероссийский теплотехнический ин-
ститут) – Êëî ÂÒÈ, и по шкале Хардгроува – ÊлоХАР. Взаимосвязь между коэффициентами размолоспо-
собности устанавливается в соответствии с [2]. Увеличение коэффициента размолоспособно-
сти приводит к более легкому измельчению топлива и сокращению удельных расходов электроэнергии на размол и пылеподготовку.
Коэффициент размолоспособности определяет способность топлива к измельчению и определяет тип, конструкцию и производительность необходимых мельниц, сепараторов, питателей топлива и другого оборудования систем пылеприготовления.
Гранулометрический состав исходного топлива и готовой пыли (R5, R10, R90, R200) характеризует соответственно исходное топливо и готовую пыль по остаткам на ситах с размерами ячеек 5 и 10 мм для углей, а также 90 и 200 мкм для готовой пыли.
Гранулометрический состав добытого и доставленного на электростанцию угля определяет необходимость использования специальных “додрабливающих” механизмов на решетках приемных бункеров, а также число ступеней, тип и производительность дробилок в тракте топливопода- чи. Чем крупнее куски топлива, поступающего на электростанцию, тем больше затрат требуется для его дробления.
Гранулометрический состав топлива, подаваемого в приемные бункера систем пылеприготовления, и необходимый гранулометрический состав готовой пыли определяют необходимые типы и производительность мельниц и сепараторов пыли. Чем крупнее куски топлива, поступающего в бункера систем пылеприготовления и чем более тонкий помол пыли необходим, тем больше затрат требуется для измельчения угля.
Оптимальный гранулометрический состав пыли для конкретных условий определяется по минимуму затрат для измельчения угля и потерь топлива с механическим недожогом.
В заключение необходимо отметить следующее: предельно допустимые значения качественных показателей определенного топлива на отдельных этапах технологического цикла ТЭС для конкретного оборудования в значительной мере определяются резервами производительности и гибкостью используемого основного и вспомогательного оборудования, которые предусматриваются на этапе проектирования ТЭС и сложились в процессе экс-
плуатации;
40 |
2003, ¹ 4 |