
- •К 70-летию Фирмы ОРГРЭС
- •70 лет на передовых рубежах энергетики
- •Разработка и осуществление мероприятий по повышению надежности энергосистем
- •Опыт организации пусконаладочных работ при внедрении АСУ ТП энергоблока ПГУ-450Т Северо-Западной ТЭЦ
- •Опыт внедрения технологических функций АСУ ТП на энергоблоке ПГУ-450Т Северо-Западной ТЭЦ
- •Разработка и эксплуатационная проверка алгоритма аварийной разгрузки энергоблоков 200 МВт Псковской ГРЭС
- •Cовершенствование управления топочным процессом и режимных карт энергетических котельных агрегатов
- •Влияние изменений основных показателей непроектных углей на работу узлов и агрегатов пылеугольных тепловых электростанций
- •Анализ причин повреждения экранных труб поверхностей нагрева котла ТПЕ-208
- •Причины повреждений и статистика по отказам трубопроводов ТЭС
- •Вакуумные выключатели в сетях 6, 10 кВ
- •Пути повышения надежности работы арматуры высоких параметров ТЭС
- •Использование отечественных и зарубежных приборов инфракрасной техники в энергетике
- •О нормировании потерь электроэнергии в электрических сетях
- •Об учете электроэнергии в электрических сетях ПЭС
- •О проведении энергетического обследования ПЭС
- •ЭНЕРГОХОЗЯЙСТВО ЗА РУБЕЖОМ
- •Парогазовые электростанции США (статистика за 2001 г.)

Причины повреждений и статистика по отказам трубопроводов ТЭС
Дитяшев Б. Д., êàíä. òåõí. íàóê, Терентьев И. А., èíæ.
ОАО “Фирма ОРГРЭС”
Более 5% отказов энергоблоков происходит изза повреждения деталей и элементов паропроводов и питательных трубопроводов, а для электростанций с поперечными связями в зависимости от года они составляют от 2 до 10% общего числа отказов. Анализ повреждаемости паропроводов показывает, что четверть всех повреждений наиболее опасна и связана с разрывами их элементов (гибов, сварных соединений и реже – прямых труб).
Основные причины повреждений деталей и элементов паропроводов следующие:
повышенные (непроектные) напряжения – 24%; дефекты сварки – 22%; металлургические дефекты и применение не-
проектных материалов – 19%; исчерпание ресурса металла – 19%;
прочие (коррозия, воздействие сторонних механизмов и др.) – 16%.
Если систематизировать повреждения трубопроводов по размерам труб и видам повреждений с учетом времени восстановления, то 50% всех повреждений относится к трубам с наружным диаметром 100 мм и более. Среди поврежденных труб меньшего диаметра подавляющее большинство составляют дренажи и байпасы. Время восстановления трубопроводов колеблется от 1 сут. (среднее давление) до 4 сут. (высокое и сверхкритическое давление).
Минимальное значение средней наработки трубопроводов, при которой происходят повреждения, характерно для дефектов сварки – 22 тыс. ч, а максимальное – свыше 150 тыс. ч – для исчерпания ресурса металла (как основного, так и наплавленного).
Проанализируем причины повреждаемости паропроводов. Их условно можно разделить на четыре группы.
К первой группе причин следует отнести “объективные”:
при переходе на нормы расчета на прочность 1965/1971 гг. был снижен коэффициент запаса прочности, кроме того, были внесены повышенные допускаемые напряжения для стали 12Х1МФ. Это привело к уменьшению толщины стенки труб. В результате были получены трубы диаметром: 194/170 мм, 273/239 мм, 325/285 мм и т.д., что явилось причиной разрывов трубопроводов, в первую очередь, гибов при наработке от 40 до 100 тыс. ч
эксплуатации. Далее последовали массовая замена паропроводов на электростанциях и соответственно огромные непланируемые затраты;
âправилах устройства и безопасной эксплуатации трубопроводов пара и горячей воды вплоть до 1994 г. был регламентирован уклон горизонтальных участков паропроводов 4 мм на 1 м в сторону движения рабочей среды. Этот уклон был достато- чен для паропроводов энергоустановок, вводимых
â50-õ годах, имеющих относительно небольшие вертикальные участки паропроводов и большое число промежуточных неподвижных опор. В дальнейшем при росте единичной мощности энергоустановок произошло увеличение вертикальных участков паропроводов, кроме того, была доказана нецелесообразность установки промежуточных неподвижных опор. Все это послужило причиной образования контруклонов горизонтальных участков паропроводов в периоды пусков и остановов оборудования и, следовательно, к короблению паропроводов. Экспериментальные данные показывают, что уровень напряжений, возникающих при короблении паропроводов, в ряде случаев достигает предела текучести металла. По этой причине до настоящего времени происходят повреждения паропроводов;
âныне действующих нормах, по нашему мнению, завышено значение коэффициента релаксации напряжений, что также приводит к возникновению неучтенных напряжений в металле паропроводов.
Кроме того, нет достаточной ясности в учете манометрического эффекта при проведении расче- тов трасс трубопроводов, что, в первую очередь, относится к паропроводам горячего и холодного промперегрева и др.
Ко второй группе причин следует отнести типовые недостатки, заложенные на стадии проектирования. Наиболее характерные из них следующие:
применение нерегулируемых катково-пружин- ных опор;
применение скользящих опор на участках, подверженных короблению, особенно это относится к паропроводам на РОУ и БРОУ, что приводит к подгибке паропроводов и в дальнейшем к повреждениям;
ввод холодной растяжки (30, 50 и 100%) для снижения напряжений;
2003, ¹ 4 |
47 |

отсутствие учета при расчете нагрузок на опоры полных перемещений паропроводов, что приводит к появлению дополнительных напряжений в металле паропроводов в рабочем состоянии от весовой составляющей и к повреждениям сварных соединений;
отсутствие учета собственных смещений энергооборудования в местах присоединения паропроводов при проведении расчетов приводит к появлению дополнительных неучтенных напряжений; выполнение проектов трасс паропроводов без учета их тепловых перемещений приводит к защемлениям паропроводов другими трубопровода-
ми или строительными конструкциями; при проведении проектных расчетов учитывал-
ся только один базовый режим работы оборудования. Остальные режимы работы и возможные переключения не учитывались, что, в свою очередь, приводит также к появлению дополнительных напряжений в металле паропроводов;
при проведении реконструкции не учитывался опыт эксплуатации, трассы паропроводов оставляли неизменными, несмотря на определенную повторяемость повреждений.
Этот перечень можно продолжить. Например, при проведении расчетов на прочность и самокомпенсацию эквивалентные напряжения от действия всех нагружающих факторов на расчетный срок службы сравниваются с допускаемыми с коэффициентом 1,5. В то же время коэффициенты концентрации напряжений в сварных соединениях сложного профиля по нашим данным и данным ВТИ в ряде случаев более 1,5.
К третьей группе причин можно отнести наиболее часто встречающиеся недостатки при проведении монтажа паропроводов, которые также оказывают существенное влияние на их дальнейшую надежную эксплуатацию, а именно:
детали и элементы трубопроводов, поставляемые заводами-изготовителями, имеют, как правило, положительный допуск по длине изделия, который в большинстве случаев не учитывается при укрупнении блоков и последующем монтаже паропроводов. В итоге возникает изменение в пространственном расположении трасс паропроводов, что в конечном итоге приводит к возникновению защемлений при эксплуатации;
скользящие и катковые опоры монтируются без учета тепловых перемещений паропроводов;
не производится смещение тяг опор и подвесок трубопроводов на половину их теплового перемещения в сторону, противоположную перемещениям;
неправильно производится затяжка пружин в подвесках (малый зазор между центральной шпилькой и коромыслами), в результате чего при растопке пружина выключается из работы и пружинная подвеска работает как жесткая тяга, что увеличивает напряжения на ряде участков трубопроводов;
не устраняются в полном объеме монтажные стяжки, времянки, вспомогательные конструкции
èдр., что также изменяет напряженное состояние паропроводов;
не выдерживаются необходимые зазоры при проходе через перекрытия, что вызывает защемление паропроводов;
запорная арматура на дренажных и байпасных линиях монтируется на расстоянии, превышающем 250 мм от паропровода, что приводит к образованию трещин на внутренней поверхности в месте приварки штуцера за счет попадания конденсата.
Êчетвертой группе причин следует отнести недостатки эксплуатации:
не выдерживаются заданные скорости прогрева и охлаждения паропроводов;
имеют место выбеги температуры пара, что оказывает существенное влияние на длительность эксплуатации паропроводов;
при пуске оборудования не в полном объеме открываются дренажи, что приводит к короблению паропроводов и гидроударам;
после окончания ремонтов не в полном объеме демонтируются ремонтные стяжки и другие вспомогательные конструкции, что приводит к защемлениям паропроводов;
не уделяется должного внимания опорно-под- весной системе креплений. Как правило, ряд опор
èподвесок находится в неудовлетворительном состоянии (пружины потеряли устойчивость, сломаны, “находит” виток пружины на виток, не несут расчетную нагрузку). Тумбы скользящих и неподвижных опор частично разрушены. Скользящие поверхности имеют задиры. На неподвижных опорах отсутствуют сухари, хомуты ослаблены и опоры не выполняют своих функций;
часть индикаторов тепловых перемещений находится в неработоспособном состоянии. Контроль за тепловыми перемещениями нередко проводится формально;
при ремонтах часто замуровываются дренажные линии, скользящие опоры и зазоры в перекрытиях для свободного перемещения паропроводов; отсутствует должный контроль за свободными перемещениями байпасных и дренажных линий, что приводит к их защемлениям и, как следствие,
êповреждениям.
 òàáë. 1 представлены статистические данные повреждаемости трубопроводов ТЭС за 1997 – 2000 гг. В òàáë. 2 указаны повреждения главных паропроводов ТЭС с параметрами пара 10 МПа и более за 1997 – 2000 гг.
Данные, представленные в òàáë. 1 è 2, можно проиллюстрировать следующими конкретными примерами.
Так, на паропроводе горячего промперегрева диаметром 720/678 мм (сталь 15Х1М1Ф, наработка 119 тыс. ч) энергоблока 500 МВт Рефтинской
48 |
2003, ¹ 4 |

ГРЭС образовалась сквозная трещина протяжен- |
Вследствие несвоевременной замены при на- |
||||||||||||
ностью 375 мм по зоне термовлияния сварного со- |
работке 160 тыс. ч на Волгоградской ТЭЦ-3 прои- |
||||||||||||
единения трубы со штампосварным коленом. Ана- |
зошло разрушение гиба паропровода диаметром |
||||||||||||
логичное повреждение на этом же паропроводе |
219/169 мм (сталь 12Х1МФ) из-за ползучести ме- |
||||||||||||
произошло |
при наработке 125 тыс. ч, |
т.е. через |
талла. |
|
|
|
|
||||||
6 тыс.ч после первого повреждения. Причина воз- |
Из-за дефектов монтажной сварки при нара- |
||||||||||||
никновения трещин – воздействие неучтенных до- |
ботке 47 тыс. ч образовался свищ в узле приварки |
||||||||||||
полнительных компенсационных напряжений. |
дренажной линии к паропроводу холодного пром- |
||||||||||||
На паропроводе свежего пара диаметром |
перегрева энергоблока 800 МВт Нижневартовской |
||||||||||||
465/315 (сталь 15Х1М1Ф) энергоблока |
|
800 ÌÂò |
ГРЭС. По этой же причине зарегистрированы по- |
||||||||||
Сургутской ГРЭС-2 образовалась кольцевая тре- |
вреждения трубопроводов на Смоленской ГРЭС, |
||||||||||||
щина в зоне термовлияния монтажного сварного |
Ириклинской ГРЭС, Ростовской ТЭЦ-2. |
||||||||||||
соединения при наработке 92 тыс. ч. Предполагае- |
Дефекты ремонтной сварки явились причиной |
||||||||||||
мой причиной повреждения сварного соединения |
повреждения углового шва приварки дренажной |
||||||||||||
явилось |
воздействие |
повышенных |
напряжений, |
линии к паропроводу свежего пара на Читинской |
|||||||||
возникающих в результате коробления паропрово- |
ТЭЦ-1. Кроме того, дефекты ремонтной сварки |
||||||||||||
дов при пусках и остановах оборудования. |
привели к разрушению угловых швов приварки |
||||||||||||
На паропроводе свежего пара диаметром |
байпасной линии и растопочного трубопровода к |
||||||||||||
325/195 ìì |
(сталь |
15Õ1Ì1Ô) |
энергоблока |
главным паропроводам Ярославской ТЭЦ-3 и Че- |
|||||||||
300 МВт Каширской ГРЭС обнаружена сквозная |
лябинской ТЭЦ-2 соответственно. По этой же при- |
||||||||||||
трещина |
протяженностью 245 мм |
â |
заводском |
чине отмечены повреждения сварных соединений |
|||||||||
сварном |
соединении. Возникновению |
|
трещины |
на питательных трубопроводах Северодвинской |
|||||||||
способствовало неудовлетворительное состояние |
ТЭЦ-1, Северодвинской ТЭЦ-2, Пермской ТЭЦ-3, |
||||||||||||
опорно-подвесной системы креплений. |
|
|
|
Тюменской ТЭЦ-1. |
|
|
|
||||||
Кроме того, из-за воздействия повышенных на- |
Невыполнение в полном объеме требований |
||||||||||||
пряжений имелись повреждения сварных соедине- |
нормативных документов в части установки ли- |
||||||||||||
ний паропроводов на Троицкой ГРЭС, Заинской |
нии прогрева достаточного диаметра дважды при- |
||||||||||||
ГРЭС, Райчихинской ГРЭС, Кировской ТЭЦ-4, |
водило к отказам энергоблоков 300 МВт Ириклин- |
||||||||||||
Пермской ТЭЦ-9, Уфимской ТЭЦ-1, Новосибир- |
ской ГРЭС. В первом случае на паропроводе горя- |
||||||||||||
ской ТЭЦ-4, Тобольской ТЭЦ, Кумертауской ТЭЦ, |
чего промперегрева диаметром 426/390 мм (сталь |
||||||||||||
Нижнетуринской ГРЭС, а также повреждения бай- |
12Х1МФ) энергоблока ¹ 1 обнаружили попереч- |
||||||||||||
пасных и дренажных линий в местах их приварки |
ную трещину длиной 28 мм на участке врезки ли- |
||||||||||||
к главным паропроводам Заинской ГРЭС, Сара- |
нии прогрева предохранительных клапанов. Тре- |
||||||||||||
товской ТЭЦ-2, Ярославской ТЭЦ-3, Казанской |
щина термоусталостного характера образовалась |
||||||||||||
ÒÝÖ-2. |
|
|
|
|
|
|
|
из-за попадания конденсата из линии прогрева на |
|||||
При работе котла ПК-10 (10,0 МПа, 510°С) Ир- |
внутреннюю поверхность паропровода. Во втором |
||||||||||||
кутской ТЭЦ-1 разорвался прямой участок главно- |
случае по аналогичной причине на паропроводе |
||||||||||||
го паропровода. При расследовании выявлена |
горячего промперегрева |
диаметром |
630/574 ìì |
||||||||||
ошибочная установка ремонтным персоналом тру- |
(сталь 15Х1МФ) энергоблока ¹ 5 образовалась |
||||||||||||
бы, изготовленной из стали 20 вместо 12Х1МФ по |
трещина протяженностью 80 мм. Начало развития |
||||||||||||
проекту, при замене главного паропровода в |
трещины – отверстие в месте врезки постоянно |
||||||||||||
1992 г. Наработка поврежденного участка паро- |
действующего дренажа диаметром 32/20 мм бай- |
||||||||||||
провода составила 24,7 тыс. ч. |
|
|
|
|
паса промперегрева. |
|
|
|
|||||
Ò à á ë è ö à |
1 |
|
|
|
|
|
|
|
|
|
|
|
|
|
|
|
|
|
|
|
|
|
|
|
|
|
|
|
|
|
|
|
|
|
|
Число отказов по годам |
|
|
|||
|
Наименование трубопровода |
|
|
|
|
|
|
|
|
|
|
||
|
|
|
|
1997 |
|
1998 |
|
1999 |
|
2000 |
|||
|
|
|
|
|
|
|
|
|
|
||||
|
|
|
|
|
|
|
|
|
|
|
|||
Трубопроводы ТЭС с поперечными связями: |
|
|
|
|
|
|
|
|
|
|
|||
паропроводы свежего пара: |
|
|
|
|
|
|
|
|
|
|
|||
14 ÌÏà, 560°Ñ |
|
|
|
|
2 |
|
8 |
|
10 |
|
4 |
||
10 ÌÏà, 510 – 540°Ñ |
|
|
|
|
– |
|
9 |
|
4 |
|
1 |
||
питательные трубопроводы высокого давления |
|
3 |
|
5 |
|
4 |
|
3 |
|||||
прочие трубопроводы |
|
|
|
|
15 |
|
4 |
|
13 |
|
27 |
||
Трубопроводы энергоблоков |
|
|
|
10 |
|
14 |
|
18 |
|
16 |
|||
|
|
|
|
|
|
|
|
|
|
|
|
|
|
Всего |
|
|
|
|
|
|
30 |
|
40 |
|
49 |
|
51 |
|
|
|
|
|
|
|
|
|
|
|
|
|
|
|
|
|
|
|
|
|
|
|
|
|
|
|
|
2003, ¹ 4 |
|
|
|
|
|
|
|
|
|
|
|
49 |

Невыполнение указаний требований норматив273/233 мм (сталь 12Х1МФ, наработка 26,7 тыс. ч)
íûõ |
документов также |
привело к образованию |
Камчатской ТЭЦ-1 в месте присоединения бай- |
||||||||
трещины |
íà |
главном |
|
паропроводе |
диаметром |
пасной линии. Вентиль байпаса был установлен на |
|||||
Ò à á ë è ö à |
2 |
|
|
|
|
|
|
|
|
||
|
|
|
|
|
|
|
|
|
|
|
|
|
|
Диаметр |
|
|
Расчетные |
|
|
|
|
||
|
|
Марка |
|
параметры пара |
Наработ- |
|
|
|
|||
Ãîä |
|
паропро- |
|
|
Место повреждения |
Причина повреждения |
|||||
|
стали |
|
|
|
êà, òûñ. ÷ |
|
|||||
|
|
âîäà, ìì |
|
Ð, ÌÏà |
t, °Ñ |
|
|
|
|||
|
|
|
|
|
|
|
|
||||
|
|
|
|
|
|
|
|
|
|
||
|
|
|
|
|
|
|
|
|
|
||
1997 |
|
273/201 |
12Õ1ÌÔ |
|
14,0 |
560 |
214 |
Узел приварки дренажа к паропроводу |
Дефект сварки |
||
|
|
325/249 |
Òî æå |
|
14,0 |
545 |
174 |
Узел приварки штуцера к паропроводу |
Òî æå |
||
|
|
273/209 |
Òî æå |
|
13,0 |
550 |
194 |
|
Прямой участок |
Исчерпание ресурса |
|
|
|
377/287 |
Òî æå |
|
13,0 |
550 |
112 |
Узел приварки дренажа к паропроводу |
Дефект сварки |
||
|
|
273/233 |
Òî æå |
|
10,0 |
540 |
201 |
|
Òî æå |
Òî æå |
|
|
|
273/209 |
Òî æå |
|
13,0 |
550 |
338 |
|
Сварной шов |
Исчерпание ресурса |
|
|
|
|
|
|
|
|
|
|
|
|
|
1998 |
|
465/315 |
15Õ1Ì1Ô |
|
25,5 |
545 |
93 |
|
Сварной шов |
Повышенные напряжения |
|
|
|
325/195 |
Òî æå |
|
25,5 |
545 |
157 |
|
Òî æå |
Òî æå |
|
|
|
720/676 |
Òî æå |
|
4,0 |
545 |
130 |
|
Òî æå |
Причина не установлена |
|
|
|
720/676 |
Òî æå |
|
4,0 |
545 |
119 |
|
Òî æå |
Повышенные напряжения |
|
|
|
245/165 |
12Õ1ÌÔ |
|
13,0 |
550 |
104 |
Узел приварки байпаса к паропроводу |
Òî æå |
||
|
|
273/209 |
Òî æå |
|
14,0 |
560 |
111 |
|
Ãèá |
Исчерпание ресурса |
|
|
|
325/249 |
15Õ1Ì1Ô |
|
13,0 |
550 |
238 |
Узел приварки байпаса к паропроводу |
Дефект сварки |
||
|
|
273/233 |
12Õ1ÌÔ |
|
10,0 |
540 |
216 |
|
Сварной шов |
Повышенные напряжения |
|
|
|
273/243 |
Òî æå |
|
10,0 |
510 |
25 |
|
Прямой участок |
Несоответствие марки ста- |
|
|
|
|
|
ли проекту |
|||||||
|
|
|
|
|
|
|
|
|
|
|
|
|
|
273/233 |
Òî æå |
|
10,0 |
540 |
27 |
Узел приварки байпаса к паропроводу |
Термическая усталость |
||
|
|
273/243 |
Òî æå |
|
10,0 |
510 |
288 |
Узел приварки штуцера к паропроводу |
Дефект сварки |
||
|
|
377/277 |
15Õ1Ì1Ô |
|
13,0 |
550 |
13 |
Узел приварки дренажа к паропроводу |
Дефект монтажа |
||
|
|
273/233 |
12Õ1ÌÔ |
|
10,0 |
540 |
210 |
|
Сварной шов |
Дефект сварки |
|
|
|
273/209 |
Òî æå |
|
14,0 |
560 |
15 |
Узел приварки байпаса к паропроводу |
Òî æå |
||
|
|
|
|
|
|
|
|
|
|
|
|
1999 |
|
325/249 |
12Õ1ÌÔ |
|
13,0 |
550 |
147 |
|
Сварной шов |
Дефект монтажа |
|
|
|
720/676 |
15Õ1Ì1Ô |
|
4,0 |
545 |
125 |
|
Òî æå |
Повышенные напряжения |
|
|
|
325/239 |
12Õ1ÌÔ |
|
14,0 |
545 |
240 |
|
Òî æå |
Дефект сварки |
|
|
|
219/165 |
Òî æå |
|
13,0 |
550 |
161 |
|
Ãèá |
Исчерпание ресурса |
|
|
|
219/165 |
Òî æå |
|
13,0 |
550 |
69 |
|
Òî æå |
Дефект изготовления |
|
|
|
273/209 |
Òî æå |
|
14,0 |
560 |
99 |
|
Òî æå |
Исчерпание ресурса |
|
|
|
273/243 |
Òî æå |
|
10,0 |
510 |
322 |
|
Сварной шов |
Прочие причины |
|
|
|
273/243 |
Òî æå |
|
10,0 |
510 |
35 |
Узел приварки байпаса к паропроводу |
Дефект сварки |
||
|
|
273/201 |
Òî æå |
|
13,0 |
550 |
186 |
|
Òî æå |
Исчерпание ресурса |
|
|
|
273/233 |
Òî æå |
|
10,0 |
540 |
122 |
Узел приварки дренажа к паропроводу |
Дефект сварки |
||
|
|
325/239 |
Òî æå |
|
13,0 |
550 |
304 |
|
Òî æå |
Повышенные напряжения |
|
|
|
273/201 |
Òî æå |
|
13,0 |
550 |
236 |
|
Òî æå |
Òî æå |
|
|
|
273/233 |
Òî æå |
|
10,0 |
540 |
115 |
Узел приварки штуцера к паропроводу |
Дефект сварки |
||
|
|
|
|
|
|
|
|
|
|
||
2000 |
|
426/390 |
12Õ1ÌÔ |
|
4,0 |
545 |
207 |
Узел приварки штуцера к паропроводу |
Повышенные напряжения |
||
|
|
630/574 |
15Õ1Ì1Ô |
|
4,0 |
545 |
295 |
Узел приварки дренажа к паропроводу |
Òî æå |
||
|
|
325/205 |
Òî æå |
|
25,5 |
545 |
170 |
Узел приварки штуцера к паропроводу |
Òî æå |
||
|
|
273/201 |
12Õ1ÌÔ |
|
13,0 |
550 |
222 |
Узел приварки паропровода к тройнику |
Òî æå |
||
|
|
159/135 |
Òî æå |
|
10,0 |
540 |
85 |
|
Прямой участок |
Òî æå |
|
|
|
273/201 |
Òî æå |
|
14,0 |
560 |
101 |
Узел приварки паропровода к тройнику |
Òî æå |
||
|
|
235/159 |
Òî æå |
|
14,0 |
560 |
140 |
Узел приварки дренажа к паропроводу |
Дефект монтажа |
||
|
|
273/201 |
Òî æå |
|
14,0 |
560 |
157 |
|
Òî æå |
Òî æå |
|
|
|
|
|
|
|
|
|
|
|
|
|
50 |
|
|
|
|
|
|
|
|
|
|
2003, ¹ 4 |
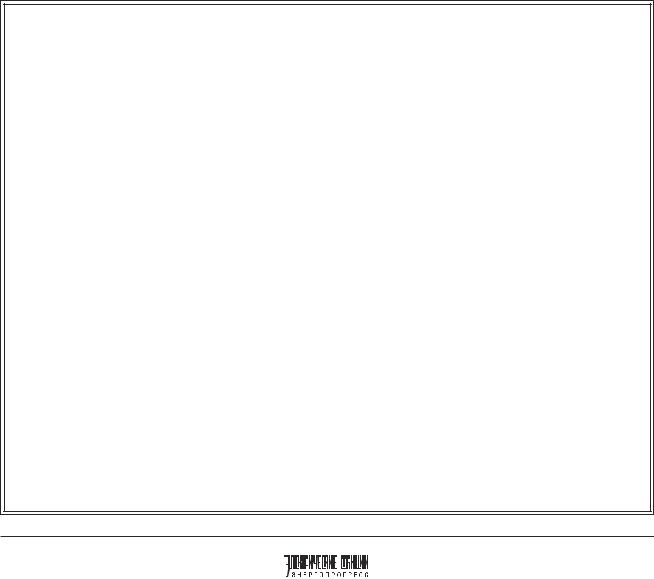
значительном расстоянии от узла врезки в паропровод.
Также из-за попадания конденсата из дренажной линии произошло повреждение гиба растопочного трубопровода котла ТГМ-84 Архангельской ТЭЦ. Наработка растопочного трубопровода на момент повреждения составила 55,6 тыс. ч.
На питательном трубопроводе котла ТГМ-84Б Волгоградской ТЭЦ-3 произошел разрыв прямого участка трубы диаметром 133/113 мм (сталь 20, наработка 12,0 тыс. ч) за регулирующим питательным клапаном (РПК). Параметры рабочей среды 23,0 МПа, 230°С. При расследовании установлено, что разрыв произошел по нижней образующей трубы вследствие эрозионного износа. На момент разрушения толщина стенки трубы составляла 1,3 – 1,7 мм вместо 10 мм по номиналу. Разрушение участка питательной линии было связано с работой котла при низких нагрузках, когда его питание велось, в основном, через линию диаметром 133/113 мм вместо основной линии диаметром 273/233 мм, с перепадом давления на клапане 5,0 МПа. Таким образом, было нарушено требование нормативного документа о необходимости
снижения избыточного перепада давления за РПК до значения, не превышающего 2,0 МПа.
На Иркутской ТЭЦ-1 при включении в работу редукционной установки подачи пара с очереди 9,0 МПа на паропроводы очереди 6,0 МПа произошел заброс образовавшегося конденсата в паропровод острого пара 6,0 МПа с отключением турбины ПТ-19-66 технологической защитой из-за низкой температуры пара. При расследовании установлено, что включаемый участок паропровода не был дренирован. При включении в работу редукционной установки имели место несогласованные действия оперативного персонала котельного и турбинного цехов. В эксплуатационной инструкции отсутствовали четкие указания по разграничению обязанностей персонала цехов при обслуживании редукционной установки.
Итак, на основании проведенного анализа повреждаемости трубопроводов большинство пере- численных причин повреждений трубопроводов является прогнозируемым, а следовательно, устраняемым, поэтому можно сделать вывод, что существует реальный резерв повышения надежной и безопасной эксплуатации трубопроводов тепловых электростанций.
Уважаемые читатели журнала «Электрические станции»!
Редакция журнала приступила к выпуску
годовых сборников журнала на CD!
На экране своего компьютера Вы увидите электронную версию журнала, в точности соответствующую печатному оригиналу. Удобная система закладок, тематический указатель и рубрикатор позволят Вам быстро находить нужную информацию.
Годовой сборник журнала на CD –
это самый удобный способ хранения информации!
Требования к оперативной системе: IBM-совместимый компьютер на базе процессора Pentium; Microsoft Windows 95 и выше; 16 Мб RAM (рекомендуется 32 Мб); 20 Мб свободного места на жестком диске.
Заплатив 350 ðóá. (в том числе НДС и почтовые расходы), Вы уже сейчас можете приобрести CD «Электрические станции. 2001» è CD «Электрические станции. 2002».
Направьте в редакцию (по почте, факсу или E-mail) гарантийное письмо-заявку с указанием платежных реквизитов и точного почтового адреса. Вам будет выставлен счет, после оплаты которого мы вышлем в Ваш адрес СD.
Адрес редакции: 115280, Москва, ул. Ленинская слобода, 23 Тел/факс: (095) 234-74-17
E-mail: tis@mail.magelan.ru
2003, ¹ 4 |
51 |