
[SHipinsky_V.G.]_Oborudovanie_i_osnastka_upakovoch(z-lib.org)
.pdf
Процесс формирования бандероли и скрепления термоусадочной пленкой включает следующие операции:
группирование в определенном порядке изделий или потребительских упаковочных единиц в транспортную единицу (блок);
обертывание сгруппированной транспортной единицы термоусадочной пленкой в виде полотна, полурукава или рукава;
сварку между собой краев отрезков обворачивающей пленки и формирование скрепляющей оболочки;
нагревание, усадку и охлаждение скрепляющей оболочки.
Из приведенных исполнений бандеролей (рис.19.1) наиболее широкое распространение получили с отверстиями на торцовых сторонах, которые выполняются из отрезков пленки, поступающей с двух горизонтальных рулонов (рис.19.1а). Автоматизированные линии, применяемые для такого обандероливания, обычно состоят из группирующее-обандероливающей 1 и термоусадочной 2 машин (рис.19.2). При работе на столе 3 такой линии толкателем 4 группируется блок 5 из штучной продукции, поступающей по конвейеру из технологического автомата. В это же время смыкающимися сварочными линейками 6 и 7 соединяются между собой поперечным швом концы полотен термоусадочных пленок, поступающих с верхнего 8 и нижнего 9 рулонов и перед формируемым блоком создается перегородка 10 из пленочного полотна. Затем сформированный блок 5 толкателем 4 перемещается за сварочные линейки, обтягиваясь при этом разматывающейся с рулонов пленкой по передней, нижней и верхней сторонам. На столе 11 этот блок фиксируется прижимом 12, который опускается на штоке срабатывающего пневмоцилиндра 13, а толкатель 4 возвращается после этого в исходное положение.
Рис.19.2. Схема группирующее-обандероливающей линии
Далее смыкающиеся сварочные линейки 6 и 7 обтягивают поданный блок пленкой по задней стороне и сваривают концы полотен между собой двойным поперечным швом с одновременной разрезкой материала между швами. При этом один из этих шов соединяет между собой края полотен двух рулонов, образующих новую перегородку 10 из пленочного полотна, а второй – края сформированной оболочки. После этого сварочные линейки и прижим 12 возвращаются соответствующими пневмоцилиндрами в исходные положения, а толкатель 4 перемещает на перегородку 10 следующий сформированный за это время блок 5, который сталкивает предыдущую бандероль со стола 11 на сетчатую ленту транспортера 14 термоусадочной машины 2, приводимую в
71

движение пневмоприводом 15. Здесь поступающие бандероли вначале перемещаются транспортером 14 через туннельную камеру 16, обеспечивающую нагрев оболочек потоками горячего воздуха и их термоусадку, а затем через устройство 17, блок вентиляторов которого направленными потоками холодного воздуха охлаждает усаженную оболочку. В результате усадки сгруппированные изделия скрепляются этой оболочкой в плотную транспортную единицу 18 с усилием до 1,8 МПа как по периметру, так и в результате затягивания ее выступающих концов на торцовые стенки блока с образованием на них отверстий, а затем готовые транспортные единицы транспортером 14 выводятся на позицию выгрузки из машины 2. Производительность этих линий составляет от 10 до 30 бандеролей в минуту.
Линия такого же типа применяется, например, и в составе
автоматизированного комплекса модели ЛПУ-МВ, обеспечивающего на ОАО «Гомельстройматериалы» (Беларусь) обандероливание и транспортное пакетирование на поддонах производимых теплоизоляционных минераловатных плит. Состоит этот комплекс из стапилирующего устройства 1 (рис.19.3), транспортера-перекладчика 2, обандероливающего автомата 3, термоусадочной машины 4, шагового транспортера 5, накопителя 6, портального робота 7 и микропроцессорной системы управления 8, обеспечивающей автоматическую работу всех устройств и механизмов комплекса в едином ритме с технологической линией 9, изготовляющей эту продукцию.
Рис.19.3. Схема автоматизированного комплекса модели ЛПУ-МВ
В процессе работы комплекса изготовляемые минераловатные плиты четырехрядным непрерывным потоком поступают в стапелирующее устройство 1 линии, где укладываются друг на друга в четыре стопы по шесть
72
штук в каждой, а затем торцевой подвижной стенкой 10 этого устройства за период изготовления следующего ряда плит перемещаются на транспортерперекладчик 2. Он же стопы плит перемещает в шаговом режиме и поочередно укладывает на приемный стол автомата 3, который производит их обандероливание термоусадочной полиэтиленовой пленкой, поступающей с двух горизонтальных рулонов.
Далее полученные бандероли перемещаются конвейером через туннельную термоусадочную камеру машины 4, где их оболочки нагреваются горячим воздухом и усаживаются, плотно обтягивая стопу плит по всему периметру. Из машины 4 готовые бандероли 11 передаются на шаговый транспортер 5 и перемещаются им до ограничительной стенки 12. При образовании у стенки 12 ряда из двух последовательно расположенных бандеролей 11, по команде соответствующих датчиков срабатывает толкатель 13 и перемещает этот сформированный ряд на стол накопителя 6, одновременно продвигая через него по столу ранее поданные в накопитель бандероли.
При заполнении стола бандеролями, портальный робот 7, по сигналу соответствующего датчика, опускает свой механический захват и забирает им с накопителя 6 блок из восьми крайних бандеролей (4 ряда по 2 бандероли), а затем переносит и укладывает его на один из двух расположенных в зоне загрузки поддонов 14, заполняя первым ярусом сразу всю грузовую площадку поддона. Для повышения устойчивости формируемого транспортного пакета, четные ярусы укладываемых на поддон бандеролей робот поворачивает в плане на 90о, обеспечивая тем самым их взаимоувязку. После укладки на поддон всех ярусов робот 7 автоматически переключается на загрузку второго поддона 14, а в это время сформированный транспортный пакет вилочным погрузчиком доставляется на слад готовой продукции.
На освободившееся место устанавливается пустой поддон размерами 2000 2000 мм, и непрерывная работа комплекса продолжается с производительностью 150 бандеролей в час. Данный комплекс обеспечил предприятию дешевое и эффективное транспортное упаковывание производимой продукции в экспортном исполнении и, как следствие, расширение рынка сбыта, автоматизацию процесса с высвобождением от вредных и тяжелых условий труда значительного количества рабочих, а также снижение потерь готовой продукции и затрат на расходные упаковочные материалы.
При выполнении бандеролей с оболочками из термоусадочной пленки, полностью покрывающими упаковываемую продукцию (без отверстий) в группирующее-обандероливающих линиях применяются устройства с Г-образными или П-образными сварочными линейками (рис.19.4).
Устройства с Г-образными сварочными линейками применяются при формировании обандероливающих оболочек из рулонной полурукавной пленки. При этом разматываемая с рулона полурукавная пленка 1 (рис.19.4а) раскрывается специальным клином 2 с подачей струи сжатого воздуха между слоями. Затем внутрь полотна укладываются изделия 3 и, опускающейся сварочной линейкой 4, производится соединение краев пленки одинарным швом в продольном направлении и двойным швом поперек полурукава с
73

одновременной разрезкой материала между швами. При этом продольным и одним из поперечных швов полностью закрывается оболочка 5 на обандероливаемых изделиях, а второй поперечный шов остается на краю полурукава для оболочки следующей бандероли.
Рис.19.4. Исполнения Г-образных и П-образных сварочных линеек
Устройства же с П-образными сварочными линейками применяются при формировании обандероливающих оболочек из пленочного полотна, поступающего с двух рулонов. При этом изделие 1 (рис.19.4б) или блок из сгруппированных изделий укладываются между двумя слоями термоусадочной пленки 2, разматывающейся с верхнего и нижнего горизонтально расположенных рулонов. Затем опускающаяся П-образная сварочная линейка 3 сразу выполняет четыре шва – два по продольным сторонам формируемой бандероли и двойной шов поперек соединяемых полотен с одновременной разрезкой материала между швами. При этом двумя продольными и одним поперечным швом полностью закрывается оболочка 4 на обандероливаемых изделиях, а второй поперечный шов соединяет передние края полотен для оболочки следующей бандероли. Имеются также линии, в которых для данного способа обертывания применяются отдельные механизмы для поперечной и параллельной продольной сварки пленок, располагающиеся на двух соседних позициях машины.
Для скрепления транспортных пакетов оболочки из термоусадочной пленки применяются как самостоятельно, так и в комплексе с другими средствами пакетирования, в том числе с плоскими поддонами, подкладными листами и рамками. По конструктивному исполнению они подразделяются на оболочки с отверстием сверху и оболочки зачехляющего типа, полностью покрывающие скрепляемый пакет.
Пакетирующие оболочки с верхним отверстием формируются из пленочного полотна, поступающего с двух вертикальных рулонов с соединением краев отрезков двумя (спереди и сзади пакета) вертикальными сварными швами (рис.19.5а) или из надеваемого сверху на пакет отрезка рукавной пленки поступающего с одного рулона (рис.19.5б). При этом пленочное полотно по высоте значительно превышает высоту пакета, и его выступающие края при термоусадке затягиваются на верх пакета, закрывая тем самым 50 – 70% этой поверхности.
В оболочках же зачехляющего типа верхние края отрезка рукавной пленки обычно соединяют сварным швом. Затем такой чехол расправляют по периметру в прямоугольник и надевают сверху на транспортный пакет, уложенный на плоском поддоне, так, чтобы нижний край чехла находился несколько ниже поддона и после этого его термоусаживают. Пленка при этом сокращается, а свивающий край чехла затягивается под низ поддона и в
74

результате такая оболочка прочно скрепляет транспортный пакет со всех сторон (рис.19.5в).
Рис.19.5. Схемы скрепления транспортных пакетов оболочками из термоусадочной пленки: 1 – пленочное полотно; 2 – рукавная пленка; 3 – плоский поддон.
При формировании бесподдонных транспортных пакетов (рис.19.5г) из грузов в мешках или в другой преимущественно мягкой таре, верхний ярус пакета укладывается не полным, а таким образом, чтобы на краях по его длине оставались выемки на ширину вилочных захватов погрузчика. Затем из отрезка рукавной пленки аналогичным образом изготовляют и сверху надевают на него чехол, с последующей термоусадкой пленки. Далее этот пакет в ротационном устройстве переворачивают на 180о так, что его верхний ярус с выемками по краям оказывается внизу, а затем сверху на пакет надевают такой же контрчехол и производят его термоусадку с одновременным термопрофилированием пленки оболочки по поверхности нижних выемок для вилочных захватов. Для повышения прочности дна пакета на верхний слой груза перед надеванием чехла может укладываться дополнительный лист пленки. Такие транспортные пакеты характеризуются малым затратами на расходные материалы (термоусадочную пленку), отсутствием возвратных средств пакетирования (поддонов), а также достаточной прочностью и герметичностью, допускающей их транспортирование и хранение на открытых транспортных средствах и площадках.
Размеры отрезка пленки (длиной l и шириной b), необходимого для скрепления транспортного пакета термоусадочной оболочкой, рассчитываются в зависимости от схемы скрепления грузов (рис.19.5) по формулам, приведенным в таблице 19.4.
Прочность пакетирующей оболочки определяется толщиной термоусадочной пленки и прочностными характеристиками полимера, из которого она изготовлена. При скреплении пакетов, сформированных на жестком основании (плоском поддоне, подкладной рамке), требуемая толщина пленки выбирается в зависимости от массы и габаритных размеров скрепляемого пакета, а также коэффициента трения между поверхностями пакетируемых грузов по одному из следующих графиков (рис.19.6 и рис.19.7), полученных опытным путем.
Для определения толщины полиэтиленовой термоусадочной пленки по методике, учитывающей массу и габаритные размеры скрепляемого пакета, вначале вычисляют среднюю плотность (Рср) пакета по формуле:
75

Р |
|
М |
|
L B H , кг/м3 |
|
||
ср |
|
(19.2) |
где М – масса сформированного пакета, кг;
L, B, H – соответственно длина, ширина и высота пакета, м.
Таблица 19.4 – Формулы для расчета размеров развертки термоусадочной пакетирующей оболочки
Размеры развертки, мм.
Схема скрепления пакета (рис.19.5): |
длина, l |
ширина, b |
|
|
|
|
|
на поддоне полотном |
с двух |
|
|
вертикальных рулонов…………………… |
2,1(L+B+c) |
H+z+1/3В |
|
на поддоне рукавной пленкой………… |
2,1(L+B) |
H+z+1/3В |
|
на поддоне чехлом из |
рукавной |
|
|
пленки…………………………………….. 2,1(L+B) |
H+L/2+c+z+150 |
||
чехлом (контрчехлом) из |
рукавной |
|
|
пленки……………………………………. |
2,1(L+B) |
H+L/2+c+150 |
|
|
|
|
|
Примечание: L – длина пакета; B – ширина пакета; H – высота пакета; с – припуск на сварной шов (с = 20 – 40 мм); z – высота поддона ( z = 150 –
200 мм).
Затем по графику, приведенному на рис.19.6, в зависимости от значения Рср определяют толщину пленки, которая является оптимальной при перевозке данного пакета одним видом транспорта. При перевозке этих пакетов с перевалками или смешанным транспортом (например, железнодорожным и водным) определенную по графику толщину пленки следует увеличить на 0,02
– 0,03 мм.
Рис. 19.6. График для определения толщины термоусадочной пленки в зависимости от средней плотности Рср транспортного пакета.
Требуемую толщину полиэтиленовой термоусадочной пленки можно определить также по графику, приведенному на рис.19.7, исходя из массы скрепляемого пакета (М) и коэффициента трения (fтр) между сопрягающимися поверхностями пакетируемых штучных изделий (плит, листов, кирпичей, черепицы и других) или тарно-штучных грузов (в мешках, ящиках, бандеролях и т. д.).
76
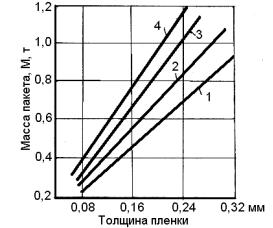
Оболочками из термоусадочной пленки скрепляют транспортные пакеты с продукцией (в упаковке или без нее), обладающей механической прочностью, достаточной для транспортирования и штабелирования пакетов. Исходные размеры оболочки должны быть такими, чтобы в процессе усадки пленки не реализовывалась максимальная степень ее усадки, так как при этом резко уменьшается остаточное напряжение усадки.
Рис.19.7. График для определения толщины термоусадочной пленки в зависимости от массы М транспортного пакета и коэффициента трения
fтр груза: 1 – fтр = 0,3; 2 – fтр = 0,4; 3 – fтр = 0,5; 4 – fтр = 0,6.
Оболочка после усадки должна плотно обтягивать транспортный пакет и не иметь механических повреждений. Содержащиеся на ней сварные соединения должны обладать прочностью при растяжении не менее 11 МПа (110 кгс/см2). Не допускается применять термоусадочные оболочки для продукции, поверхность которой покрыта смазкой, а также для продукции в упаковке из полимерных материалов, температура плавления которых ниже или равна температуре плавления термоусадочной пленки. Не допускается также приваривание оболочки к пакетируемой продукции или ее упаковке.
Процесс формирования транспортных пакетов и их скрепления оболочками из термоусадочной пленки включает следующие операции:
укладку многоярусного транспортного пакета, по возможности с перевязкой между ярусами, на поддоне или без него;
обертывание пакета термоусадочной пленкой;
сварку краев пленки и формирование пакетирующей оболочки или изготовление и одевание на пакет чехла;
нагревание, усадку и охлаждение скрепляющей пакетирующей оболочки.
Вчастности, скрепление транспортных пакетов сформированных на поддоне оболочками, изготовляемыми из пленочного полотна, поступающего с двух вертикальных рулонов (рис.19.5а), обеспечивается на
автоматизированной линии модели ЛПУ-К. Эта линия устанавливается обычно над конвейером 1 (рис.19.8) технологического комплекса по производству самой продукции (например, кирпичей) и состоит из обандероливающего автомата 2 и термоусадочного устройства 3. В процессе ее работы транспортные пакеты 4, сформированные из уложенных на поддоны кирпичей, перемещаются с заданным шагом конвейером 1 и в процессе
77

движения набегают на перегораживающее конвейер пленочное полотно, разматывающееся с двух вертикальных рулонов 5 через двухвалковые механизмы 6 его амортизации и натяжения, и обтягиваются при этом пленкой по передней и боковым сторонам. Затем за остановившимся пакетом смыкаются расположенные с двух сторон конвейера термосварочные линейки 7 и 8 обандероливающего автомата 2, которые обтягивают пленкой пакет по задней стороне и сваривают сопрягающиеся полотна между собой двойным вертикальным швом с одновременной разрезкой материала между швами. После этого сварочные линейки возвращаются в исходное положение, а пакет оказывается обтянутым пленкой по всему периметру и отделенным от полотна, натянутого поперек конвейера перед следующим пакетом.
Рис.19.8. Схема автоматизированной линии модели ЛПУ-К
Далее перемещением конвейера на следующий шаг обтянутый пакет подается к термоусадочному устройству 3 линии, содержащему вертикально перемещающуюся по колоне 9 раму 10, несущую по внутреннему периметру лучевые нагреватели 11. Здесь в процессе перемещения рамы 10 вниз ее включенными нагревателями 11 оболочка нагревается по всей поверхности и усаживается, плотно обтягивая транспортный пакет. При этом выступающие края пленочной оболочки в процессе термоусадки затягиваются на верх пакета, закрывая 50 – 70% этой поверхности. Затем рама ускоренно возвращается в верхнее исходное положение, конвейер совершает следующий шаг и цикл повторяется одновременно на всех позициях линии, а скрепленные транспортные пакеты 12 доставляются на склад. Например, такая линия, внедренная на Родошковичском керамическом заводе (Беларусь) в составе комплекса по производству кирпичей, обеспечивает скрепление транспортных пакетов габаритными размерами 1400 х 1400 х 1075 мм с производительностью 45 штук в час.
Автоматизированный пакетирующий комплекс модели FSA
известной фирмы «Mollers» (Германия) обеспечивает, например, формирование транспортных пакетов на стандартных поддонах размерами в плане 800 х 1200 мм и их скрепление термоусадочными оболочками зачехляющего типа (рис.19.5в). Он состоит из подающего конвейера 1 (рис.19.9), ориентирующего устройства 2, модульного автомата-укладчика 3, расположенного за ним магазина 4 поддонов с устройством их поштучной выдачи на позицию загрузки, зачехляющего автомата 5, соединяющих транспортеров 6 и станции 7 приема готовых транспортных пакетов 8.
78

В процессе работы комплекса из магазина 4 на стол автомата-укладчика 3 подается очередной поддон 9, а конвейером 1 в это время на ориентирующее устройство 2 поштучно доставляются пакетируемые упаковочные единицы (изделия) 10. После ориентирования в заданное положение эти упаковочные единицы захватываются манипулятором 11 и укладываются на поддоне 9 в транспортный пакет с их междуярусной перевязкой по заданной схеме.
Рис.19.9. Схема автоматизированного пакетирующего комплекса модели FSA фирмы «Mollers» (Германия)
Далее сформированный пакет транспортером 6 перемещается в зачехляющий автомат 5. Здесь сведенные захваты, находящейся в верхнем положении рамы 12 автомата, вводятся в нижний торец заправленной рукавной пленки 13, разматывающейся с рулона 14, а затем расходятся и расправляют его в прямоугольник по размерам пакета. После этого подачей через пальцы захватов внутрь сжатого воздуха рукав раздувается и перемещением рамы 12 вниз надевается на весь пакет, включая и высоту поддона. При этом автоматически контролируются габаритные размеры пакета. Далее соответствующим механизмом надетая часть рукава отрезается от рулона по высоте пакета и на ней герметичным поперечным швом сваривается верх чехла. Затем захваты отпускают нижний край рукава, и рама 12 движется обратно вверх, осуществляя нагрев и усадку надетого пленочного чехла с помощью включающихся газовых или электролучевых нагревателей, расположенных по ее внутреннему периметру. При этом пленка сокращается, нижний край чехла затягивается под низ поддона, и оболочка прочно скрепляет транспортный пакет со всех сторон. При подходе же рамы к верхнему конечному положению нагреватели выключаются, ее захваты сходятся и вводятся в нижний торец рукавной пленки 13 для формирования и надевания следующего чехла, а скрепленный пакет 8 транспортером 6 перемещается на станцию 7 приема готовых грузовых единиц. На освободившееся место из автомата-укладчика 3 подается следующий пакет, сформированный за это время на поддоне 9 из упаковочных единиц 10, и цикл повторяется с производительностью от 14 до 120 транспортных пакетов в час.
Этой же фирмой «Mollers» (Германия) создана технология и автоматизированные комплексы серии PKS, обеспечивающие бесподдонное формирование транспортных пакетов (рис.19.5г) из грузов в мешках или в другой преимущественно мягкой упаковке и их скрепление термоусадочными оболочками зачехляющего типа. В частности, такой автоматизированный пакетирующий комплекс модели PKS-2, работающий с производительностью
79

50 – 70 транспортных пакетов в час, состоит из конвейера 1 (рис.19.10), подающего ориентирующего устройства 2, автомата-укладчика 3, автомата 4, скрепляющего пакеты чехлом, ротационной станции 5 кантования пакетов, автомата 6, скрепляющего пакеты контрчехлом, соединяющих транспортеров 7 и станции 8 приема готовых грузовых единиц.
Рис.19.10. Схема автоматизированного пакетирующего комплекса модели PKS-2 фирмы «Mollers» (Германия)
В процессе работы комплекса конвейером 1 на ориентирующее устройство 2 поштучно доставляются пакетируемые упаковочные единицы (изделия) 9. После ориентирования в заданное положение эти упаковочные единицы захватываются манипулятором 10 и укладываются на столе автоматаукладчика 3 в транспортный пакет с их междуярусной перевязкой по заданной схеме. При этом последний верхний ярус укладывается не полным таким образом, чтобы на краях по его длине оставались выемки на ширину вилочных захватов погрузчика.
Затем сформированный пакет 11 транспортером 7 перемещается в автомат 4. Здесь сведенные захваты, находящейся в верхнем положении рамы 12 автомата, вводятся в нижний торец заправленной рукавной пленки 13, разматывающейся с рулона 14, а затем расходятся и расправляют его в прямоугольник по размерам пакета. После этого подачей через пальцы захватов внутрь сжатого воздуха рукав раздувается и перемещением рамы 12 вниз надевается на весь пакет, высота которого при этом автоматически измеряется. Далее соответствующим механизмом надетая часть рукава отрезается от рулона по высоте пакета и на ней герметичным поперечным швом сваривается верх чехла. Затем захваты отпускают нижний край чехла, и рама 12 движется обратно вверх, осуществляя нагрев и усадку надетого пленочного полотна с помощью включающихся газовых нагревателей, расположенных по ее внутреннему периметру. При этом пленка сокращается, свисающий край чехла затягивается под низ пакета, и оболочка прочно скрепляет его со всех сторон. При подходе рамы к верхнему конечному положению нагреватели выключаются, ее захваты сходятся и вводятся в
нижний торец рукавной пленки 13 для формирования и надевания следующего чехла, а скрепленный пакет 11 следующим транспортером 7 перемещается в ротационную станцию 5, которая кантует его на 180о так, что верхний ярус с выемками по краям оказывается внизу пакета.
С ротационной станции 5 перевернутый транспортный пакет 11 следующим транспортером 7 перемещается в автомат 6, где на него также как
80