
- •Abstract
- •Acknowledgements
- •Table of contents
- •List of figures
- •List of tables
- •List of boxes
- •Executive summary
- •Absent a change in course, ammonia production would continue to take an environmental toll
- •Towards more sustainable ammonia production
- •Near-zero-emission ammonia production requires new infrastructure, innovation and investment
- •Enabling more sustainable ammonia production
- •Chapter 1. Ammonia production today
- •Ammonia and society
- •Nitrogen fertilisers: An indispensable input to our modern agricultural systems
- •Demand, supply and trade
- •Ammonia production fundamentals
- •Current and emerging production pathways
- •A brief history of ammonia production
- •Natural gas reforming
- •Coal gasification
- •Near-zero-emission production routes currently being pursued
- •Economic considerations
- •Ammonia and the environment
- •Non-CO2 environmental impacts
- •Non-CO2 greenhouse gas emissions from fertiliser production and use
- •Impacts on water, soil, air and ecosystems
- •What will happen tomorrow to today’s CO2 emissions from ammonia production?
- •Chapter 2. The future of ammonia production
- •Three contrasting futures for the ammonia industry
- •The outlook for demand and production
- •The outlook for nitrogen demand, nutrient use efficiency and material efficiency
- •Nitrogen demand drivers
- •Measures to improve nitrogen use efficiency
- •The outlook for production
- •Technology pathways towards net zero emissions
- •Energy consumption and CO2 emissions
- •A portfolio of mitigation options
- •Innovative technology pathways
- •Overview of global and regional technology trends
- •China
- •India
- •North America
- •Europe
- •Other key regions
- •Considerations for the main innovative technologies
- •Dedicated VRE electrolysis
- •CCUS-equipped pathways
- •Readiness, competitiveness and investment
- •An array of technology options at differing levels of maturity
- •Exploring key uncertainties
- •Future production costs
- •Uncertainty in technology innovation
- •Investment
- •Chapter 3. Enabling more sustainable ammonia production
- •The current policy, innovation and financing landscape
- •Ongoing efforts by governments
- •Carbon pricing and energy efficiency measures
- •Support for near-zero-emission technology RD&D and early commercial deployment
- •Policies for improving efficiency of use
- •International collaboration
- •Encouraging progress in the private sector
- •Initiatives involving financial institutions and investors
- •Recommendations for accelerating progress
- •Framework fundamentals
- •Establishing plans and policy for long-term CO2 emission reductions
- •Mobilising finance and investment
- •Targeted actions for specific technologies and strategies
- •Managing existing assets and near-term investment
- •Creating a market for near-zero-emission nitrogen products
- •Developing earlier-stage near-zero-emission technologies
- •Improving use efficiency for ammonia-base products
- •Necessary enabling conditions
- •Enhancing international co-operation and creating a level playing field
- •Planning and developing infrastructure
- •Tracking progress and improving data
- •Key milestones and decision points
- •Annexes
- •Abbreviations
- •Units of measure

Ammonia Technology Roadmap |
Chapter 2. The future of ammonia production |
Towards more sustainable nitrogen fertiliser production |
|
Readiness, competitiveness and investment
Near-zero-emission technologies for the ammonia industry are currently at different stages of development. They include technologies that are ready to be deployed by industry today, and those that still have innovation hurdles to overcome before being fully placed on the market. Which technologies are ultimately deployed will be context-specific, depending on factors such as energy costs, availability of supporting infrastructure and the policy environment. The future is uncertain, and factors such as the pace of innovation and extent of technology cost reductions may affect technology deployment. Regardless, achieving deep emission reductions in the ammonia industry will require a massive shift in investment towards near-zero-emission technologies and the infrastructure to support them.
Box 2.6 The TRL scale
One way to assess where a technology is on its journey from initial idea to market is to use the TRL scale. Originally developed by the National Aeronautics and Space Administration (NASA) in the United States in the 1970s and used in many US government agencies since the 1990s, the TRL provides a snapshot in time of the level of maturity of a given technology within a defined scale. The US Department of Defense has been using the TRL scale since the early 2000s for procurement, while the European Space Agency adopted it in 2008. In 2014 the TRL was applied for the first time outside the aerospace industry to assess EUfunded projects as part of the Horizon 2020 framework programme. It is now widely used by research institutions and technology developers around the world to set research priorities and design innovation support programmes.
The scale provides a common framework that can be applied consistently to any technology, to assess and compare the maturity of technologies across sectors. The technology journey begins from the point at which its basic principles are defined (TRL 1). As the concept and area of application develop, the technology moves into TRL 2, reaching TRL 3 when an experiment has been carried out that proves the concept. The technology now enters the phase where the concept itself needs to be validated, starting from a prototype developed in a laboratory environment (TRL 4), followed by testing of components in the conditions it will be deployed (TRL 5), through to testing the full prototype in the conditions in which it will be deployed (TRL 6). The technology then moves to the demonstration phase, where it is tested in real-world environments (TRL 7), eventually reaching a first-
PAGE | 107
IEA. All rights reserved.

Ammonia Technology Roadmap |
Chapter 2. The future of ammonia production |
|
Towards more sustainable nitrogen fertiliser production |
|
|
|
|
|
|
|
|
of-a-kind commercial demonstration (TRL 8) on its way towards full commercial operation in the relevant environment (TRL 9).
Arriving at a stage where a technology can be considered commercially available (TRL 9) is not sufficient to describe its readiness to meet energy policy objectives, for which scale is often crucial. Beyond the TRL 9 stage, technologies need to be further developed to be integrated within existing systems or otherwise evolve to be able to reach scale; other supporting technologies may need to be developed, or supply chains set up, which in turn might require further development of the technology itself. For this reason, the IEA has extended the TRL scale it uses in its reports to incorporate two additional readiness levels: one where the technology is commercial and competitive, but needs further innovation for its integration into energy systems and value chains when deployed at scale (TRL 10), and a final one where the technology has achieved predictable growth (TRL 11).
Maturity categories and technology readiness levels along innovation cycles
|
|
Category |
|
Sub-category |
|
|
Level |
||||
|
|
|
|
|
|
|
|
|
|
|
INITIAL IDEA |
|
|
|
|
|
|
|
|
|
1 |
|
|
|
|
|
|
|
|
|
|
|
|
Basic principles have been defined |
|
|
|
|
|
CONCEPT |
|
|
|
|
2 |
|
APPLICATION FORMULATED |
|
|
SMALL |
|
|
|
|
|
Concept and application of solution have been formulated |
|||
|
|
|
|
|
|
|
|
|
|
CONCEPT NEEDS VALIDATION |
|
|
|
PROTOTYPE or lab |
|
|
|
|
|
|
3 |
|
|
|
|
|
|
|
|
|
|
|
Solution needs to be prototyped and applied |
||
|
|
|
|
|
|
|
|
|
|
|
EARLY PROTOTYPE |
|
|
|
|
SMALL PROTOTYPE |
|
|
4 |
|
|||
TECHNOLOGY |
|
|
|
|
|
|
Prototype proven in test conditions |
||||
|
|
|
|
|
|
|
|
|
|
|
|
DEVELOPMENT |
|
|
|
|
|
|
|
|
5 |
|
LARGE PROTOTYPE |
|
LARGE |
|
LARGE |
|
|
|
|||||
|
|
|
|
|
|
Components proven in conditions to be deployed |
|||||
|
|
PROTOTYPE |
|
PROTOTYPE |
|
|
6 |
|
FULL PROTOTYPE AT SCALE |
||
|
|
|
|
|
|
|
|
|
|
Prototype proven at scale in conditions to be deployed |
|
|
|
|
|
|
|
|
|
|
|
|
PRE-COMMERCIAL DEMONSTRATION |
|
|
|
|
|
|
|
|
|
7 |
|
|
|
|
|
|
|
|
|
|
|
|
Solution working in expected conditions |
|
|
|
DEMONSTRATION |
|
DEMONSTRATION |
|
|
|
|
|||
|
|
|
|
8 |
|
FIRST OF A KIND COMMERCIAL |
|||||
|
|
|
|
|
|
|
|
|
|
||
|
|
|
|
|
|
|
|
|
|
|
Commercial demonstration, full scale deployment in final form |
|
|
|
|
EARLY ADOPTION |
|
9 |
|
COMMERCIAL OPERATION IN RELEVANT ENVIRONMENT |
|||
MARKET |
|
MARKET UPTAKE |
|
|
|
Solution is commercially available, needs evolutionary improvement to stay competitive |
|||||
|
|
|
|
|
|
|
10 |
|
INTEGRATION NEEDED AT SCALE |
||
|
|
|
STEADY SCALE UP |
|
|
|
|||||
DEVELOPMENT |
|
|
|
|
|
|
Solution is commercial and competitive but needs further integration efforts |
||||
|
|
|
|
|
|
||||||
|
|
MATURE |
|
MATURE |
|
|
|
11 |
|
PROOF OF STABILITY REACHED |
|
|
|
|
|
|
Predictable growth |
||||||
|
|
|
|
|
|
|
|
|
|
|
|
IEA, 2021.
As technologies pass through each stage, the level of risk associated with their performance is reduced, but the level of overall risk rises as capital expenditure requirements grow. However, innovation is rarely a linear progression. Not all technology designs make it to market or are deployed at scale. Stages of development can accelerate or slow down depending on technical or cost factors, and a given technology can be at different stages in different markets and applications. As the development of a technology generates new ideas for improvement, alternative configurations and potentially better components can appear even once a given technology configuration has become competitive. Stages overlap and run concurrently, feeding off one another.
In this report we refer to several broader readiness categories, each of which comprises a different range of specific readiness levels from the full TRL scale:
PAGE | 108
IEA. All rights reserved.
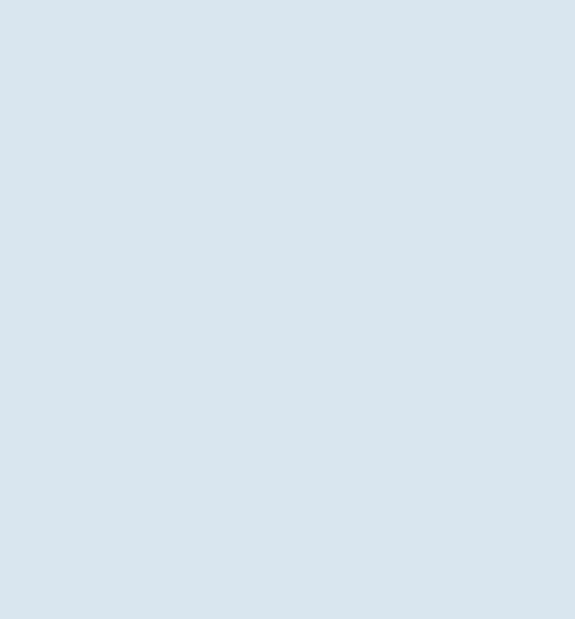
Ammonia Technology Roadmap |
Chapter 2. The future of ammonia production |
Towards more sustainable nitrogen fertiliser production |
|
mature, market uptake, demonstration, large prototype and small prototype
(technologies at the small prototype stage of TRL 4 or lower are not included in the Sustainable Development Scenario). Each technology type is assigned to one of these higher-level categories based on the granular levels of maturity of individual technology designs or components currently associated with that technology:
“Mature” for technologies that have reached market stability, and the number of new purchases or installations are constant or even declining in some environments as newer technologies start to compete with the stock of existing assets, for example ammonia production via SMR.
“Market uptake” for technologies that are being deployed in a number of markets. This category includes the sub-categories “early adoption” for technologies that have a cost and performance gap with established technologies and “steady scaleup” for technologies that are competitive but barriers to reaching their full market potential remain, such as integration with existing infrastructure or consumer preference. Policy attention is needed in both cases to stimulate wider diffusion to reduce costs and to overcome existing barriers, with more of the costs and risks being borne gradually by the private sector. An example is ammonia production via SMR with CCS.
“Demonstration” for technologies where the first examples of a new technology are being introduced at the size of a full scale commercial unit, for example ammonia production via methane pyrolysis.
“Large prototype” for technology types for which prototypes are being developed at a considerable size, as in pilot plants.
“Small prototype or lab” for technology types for which designs are being developed into lab-scale prototypes. This category includes the sub-categories “small prototype” for technologies that have been proven in test conditions and “concept” for technologies still needing to be prototyped.
An array of technology options at differing levels of maturity
Technologies that are not yet mature in the marketplace will be critical to achieving deep emission reductions in the ammonia industry. Most of these technologies either capture CO2 from fossil fuels for permanent storage or rely on electricity as an important input. Within both categories there are several different technology options with varying levels of readiness.
With regard to CCS, the ammonia industry has an advantage over many other industrial sectors in that CO2 separation is already an integral part of conventional
PAGE | 109
IEA. All rights reserved.
Ammonia Technology Roadmap |
Chapter 2. The future of ammonia production |
Towards more sustainable nitrogen fertiliser production |
|
ammonia production processes. In conventional reforming to produce hydrogen from natural gas, process CO2 from the feedstock is removed using either chemical or physical absorption technologies. Thus the CO2 capture technologies are mature (TRL 11) for application to the concentrated CO2 stream from feedstock energy. Many ammonia plants are already utilising the captured CO2, often for urea production.
It is not a huge leap from a technology standpoint to take the extra steps to permanently store the already-captured CO2. It simply needs to be compressed and transported to the storage site. For several decades a number of fertiliser plants in the United States have been providing their CO2 for EOR (through which virtually all of the CO2 injected is ultimately retained in the reservoir over the life of the project, although monitoring and verification is needed to confirm permanent storage). A similar project came online in 2020 in Canada, with additional projects in the construction or planning stages in the United States, the United Kingdom and China. At least two of these projects are specifically intended to reduce emissions, with the CO2 stored in dedicated geological storage sites rather than being used for EOR. Given that the technology is ready, but deployment is not yet widespread, the full chain of CCS for ammonia production – including CO2 transport and storage infrastructure – is considered to be at the market uptake stage (TRL 9) and would still benefit considerably from policy support for further deployment.
Unlike the process emissions, CO2 emissions from fuel combustion to provide process heat are not already captured as part of conventional production processes. Thus a second capture unit would be needed, or the existing unit would need to be expanded with some reconfiguration. Given the lower concentration of CO2 in the combustion flue gas, chemical absorption is a probable technology choice. This technology is being used to capture fuel combustion CO2 in two known ammonia plant in Bahrain and Pakistan (the CO2 being used for urea and methanol production) and for CO2 streams with comparable concentrations in the power sector (TRL 9-10 for the capture technology and CO2 use). There are no known ammonia plants capturing the dilute stream for permanent storage, although transport and storage requirements would not present a technology challenge given experience in other applications (TRL 8 for the full CCS chain). The potential for applying CCS to ammonia fuel combustion emissions is less a question of technology readiness than a question of cost – using current technologies, capturing CO2 from fuel combustion is about two to four times costlier than from the process stream, and the CO2 capture from the process stream is already part of the costs of the ammonia plant’s costs anyway.
PAGE | 110
IEA. All rights reserved.

Ammonia Technology Roadmap |
Chapter 2. The future of ammonia production |
Towards more sustainable nitrogen fertiliser production |
|
Various options exist to reduce fuel stream emissions to less than 10% of total emissions, such as using ATR technology or diverting a proportion of the hydrogen produced in the reforming process for use in the furnace. Thus, some operations may opt out of capturing the small amount of remaining dilute fuel combustion CO2. However, at least one known company is working towards full CO2 capture ammonia production. The setup would use a cryogenic CO2 capture system
together with a process that displaces steam requirements by making use of highpressure CO2. The company is working towards a first commercial plant in New Zealand that is expected to come online in 2024 (TRL 7).
Status of main near-zero-emission technologies in ammonia production
TRL, year available,
Technology importance Deployment status (selected projects) for net zero
emissions
Carbon capture, utilisation and storage
PAGE | 111
IEA. All rights reserved.

Ammonia Technology Roadmap |
Chapter 2. The future of ammonia production |
Towards more sustainable nitrogen fertiliser production |
|
TRL, year available,
Technology importance Deployment status (selected projects) for net zero
emissions
Chemical |
|
absorption – |
8 |
full capture |
Today |
(dilute CO2 |
Medium |
stream) |
|
Full capture involves additional capacity to capture the dilute CO2 stream from fuel combustion for heat provision. Chemical absorption would be a likely candidate for this CO2 stream. It is already being applied commercially to the concentrated process emissions stream in ammonia plants, as well as to dilute CO2 streams in a more limited number of cases in the power sector (TRL 9-10 for capture technology). However, it is likely currently being applied to the dilute stream in only a very limited number of ammonia plants.
Two known ammonia plants are capturing dilute emissions for use (TRL 9 for CCU):
•GCIP; Sitra, Bahrain; operational 2010; 0.16 Mt CO2/yr
•Engro; Daharki, Pakistan; operational 2010; 0.12 Mt CO2/yr
No known ammonia plants are capturing dilute emissions for permanent storage, although based on other related experience there would be no major technology hurdles to overcome (TRL 8 for full CCS chain).
Physical |
|
absorption – |
9 |
partial capture |
Today |
(concentrated |
Very high |
CO2 stream) |
|
Capture technology widely used commercially as part of the SMR hydrogen production process (TRL 11 for capture technology)
Several commercial plants in operation, using captured CO2 for EOR (TRL 9 for full CCS chain). Known projects are:
•Coffeyville Resources Nitrogen Fertilizers; Coffeyville, KS, United States; operational 2013; 1 Mt CO2/yr
•Nutrien; Redwater, AB, Canada; operational 2020; 0.3 Mt CO2/yr; part of the Alberta Carbon Trunk Line project.
|
|
Pouakai NZ (subsidiary of eight Rivers Capital) is developing a zero-emission |
|
Cryogenic – |
|
hydrogen project in Taranaki, New Zealand, set to come online in 2024 |
|
7 |
capturing 1 Mt CO2/yr. It will produce fertilisers, hydrogen and power. |
||
full capture |
2025 |
Through use of a cryogenic CO2 capture system and a process called the |
|
(dilute CO2 |
|||
Medium |
Allam-Fetvedt Cycle, which uses high-pressure CO2 instead of steam, the |
||
stream) |
|||
|
project is aiming to store 100% of CO2 generated. |
||
|
|
PAGE | 112
IEA. All rights reserved.

Ammonia Technology Roadmap |
Chapter 2. The future of ammonia production |
Towards more sustainable nitrogen fertiliser production |
|
|
|
|
TRL, year |
|
|
|
|
|
available, |
|
|
|
Technology |
|
importance |
|
Deployment status (selected projects) |
|
|
|
for net zero |
|
|
|
|
|
emissions |
|
|
|
|
|
|
|
|
|
Electricity |
|
|
|
|
|
|
|
|
|
|
|
|
|
|
Electrolysers have been used commercially over the past century, including |
|
|
|
|
|
for ammonia production using hydropower. However, their use is not |
|
|
|
|
|
widespread today, putting the electrolyser itself at TRL 9-10. Only one known |
|
|
|
|
|
ammonia plant using electrolytic hydrogen from hydropower remains, |
|
|
|
|
|
operated by Industrias Cachimayo in Cusco, Peru, since the 1970s. |
|
|
|
|
|
|
The full chain of VRE-powered electrolysis to produce ammonia is being |
|
|
|
|
|
developed, with several large-scale demonstration or first commercial plants |
|
|
|
|
|
in the development stages (TRL 8 for full chain). Some of the projects that |
|
|
|
|
|
are most advanced and/or most relevant to fertilisers and other current uses |
|
|
|
|
|
of ammonia include: |
|
|
|
|
|
• Fertiberia and Iberdrola; Puertollano, Spain; under construction, due to |
|
|
|
|
|
be online by end of 2021; 20 MW electrolyser, solar-powered; for use in |
|
|
|
|
|
fertiliser plant to enable 10% reduction in natural gas requirements; |
|
|
|
|
|
three additional projects planned between 2023 and 2027 in Puertollano |
|
|
|
|
|
and Palos de la Frontera for a total of 800 MW electrolysis |
|
|
|
|
|
• Yara, NEL Porsgrunn, Norway, 25 MW electrolyser expected online in |
|
|
|
|
|
2023; expanded electrolyser capacity to fully shift 0.5 Mt/yr of ammonia |
|
|
|
|
|
production away from natural gas in 2026-2028 (in partnership with |
|
|
|
|
|
Statkraft and Aker Clean Hydrogen); grid-connected hydropower |
|
Electrolytic |
8 |
|
• Yara and Ørsted; Sluiskil, Netherlands; at feasibility stage, expected |
|
|
hydrogen |
|
|||
|
2025 |
|
online 2025; 100 MW electrolyser, 70 kt/yr ammonia; powered by |
||
|
supplied by |
|
|||
|
|
Very high |
|
offshore wind |
|
|
VRE |
|
|
||
|
|
|
|
• Yara and Engie; Pilbara, Australia; 10 MW electrolyser by 2023; solarpowered
• CF Industries; Donaldsonville, LA, United States; construction to begin in 2021, completion by 2023; 20 MW electrolyser, 20 kt/yr ammonia; gridconnected
• Enaex and Engie (Hyex project); Mejillones district, Chile; pilot with 26 MW electrolyser and 18 kt/yr ammonia expected online by 2024; fullscale operation with 1.6 GW electrolyser and 700 kt/yr ammonia by 2030; solar-powered
• Balance Agri-Nutrients and Hiringa Energy; Kapuni, New Zealand; expected online mid-2020s; 7 kt urea/yr; wind-powered
Other pilot to commercial-scale projects are also at various stages of planning and development, including some that would use ammonia for fuel. They are located around the world, including in Australia (Queensland Nitrates; Dyno Nobel; H2U; BP; Fortescue Metals Group; Origin Energy), Denmark (Skovgaard Invest; Copenhagen Infrastructure Partners), Trinidad and Tobago (Kenesjay Green Ltd), Germany (RWE), Chile (AES Gener; CORFO; Austria Energy), Oman (ACME) and Morocco (OCP Group).
PAGE | 113
IEA. All rights reserved.

Ammonia Technology Roadmap |
Chapter 2. The future of ammonia production |
Towards more sustainable nitrogen fertiliser production |
|
|
|
TRL, year |
|
|
|
|
available, |
|
|
|
Technology |
importance |
|
Deployment status (selected projects) |
|
|
for net zero |
|
|
|
|
emissions |
|
|
|
|
|
|
|
|
|
|
|
Several projects are working towards using methane pyrolysis to produce |
|
|
|
|
hydrogen. While some are already planning to use the hydrogen to produce |
|
|
|
|
ammonia, for others the intended use of hydrogen is not yet determined. |
|
|
|
|
Projects include: |
|
|
|
|
• Monolith completed pilot testing in Redwood City, CA, United States |
|
|
|
|
during 2013-15. First commercial unit - Olive Creek 1, 14 kt/yr carbon |
|
|
|
|
black capacity; Hallam, NE; construction completed in 2020 with |
|
|
|
|
production expected to start in 2021. Second phase to begin |
|
|
|
|
construction in 2021 on same site, Olive Creek 2; production expected to |
|
|
|
|
begin 2023/24; will produce 275 kt/yr ammonia and 180 kt/yr carbon |
|
Methane |
7 |
|
black |
|
|
|
||
|
2025 |
|
• BASF is pilot testing in Ludwigshafen, Germany; first industrial-scale |
|
|
pyrolysis |
|
High |
plant expected around 2030; technology expected to be used for |
|
|
|
producing chemicals such as ammonia and methanol |
|
• Hazer Group is preparing for construction of a commercial |
|
demonstration project in Munster, Australia |
|
• C-Zero is working on commercialising a methane pyrolysis technology |
|
developed at the University of California, Santa Barbara in the |
|
United States; in early 2021 funds were raised for a first pilot plant |
|
• A number of other companies and research institutions have done lab- |
|
scale testing, with a few – including HiiROC in the United Kingdom, TNO |
|
in the Netherlands and KIT in Germany – working towards pilot plants. |
|
|
Bioenergy |
|
|
|
Biomass/ |
5 |
waste |
- |
gasification |
Low |
Techno-economic evaluation of producing ammonia via biomass
gasification completed, but suggests it is not yet economically viable. Higher TRLs for other applications (for example biomethane, ethanol and methanol production), but not yet applied to ammonia.
*For CO2 capture projects, if information on the type of capture technology was unavailable, the project was listed under chemical absorption.
Notes: TRL = technology readiness level; SMR = steam methane reforming; CCU = carbon capture and utilisation; CCS = carbon capture and storage.
Electrolytic hydrogen has already been used commercially for ammonia production, powered by large-scale hydropower. In fact, ammonia production from electrolytic hydrogen was quite common until around the 1970s when cheap natural gas led to the technology’s replacement by SMR plants. Only one electrolytic ammonia plant remains in the world, a plant built in the 1960s in Peru. While electrolytic ammonia production in itself is a commercially proven
PAGE | 114
IEA. All rights reserved.
Ammonia Technology Roadmap |
Chapter 2. The future of ammonia production |
Towards more sustainable nitrogen fertiliser production |
|
technology, producing ammonia from electrolysis powered by VRE has the added challenge of adapting the production chain to the variability of electricity infeed.
Producing ammonia from electrolytic hydrogen has regained interest in recent years due to the need to reduce CO2 emissions. Numerous projects around the world are at various stages of integrating electrolytic hydrogen into ammonia production, including in Europe, the United States, Chile, Australia and New Zealand. Several will use the ammonia for fertiliser production, some for explosives and some for energy. Many are beginning with smaller electrolysers (10-25 MW) to meet a proportion of the plant’s hydrogen input requirements, and have plans to scale up in the subsequent years to gigawatt-scale electrolysers providing 80-100% of hydrogen requirements. The first small-scale electrolyser for ammonia production is scheduled to come online by the end of 2021, with larger electrolysers coming online in the mid to late 2020s. While some will use grid electricity, many will be powered directly by dedicated VRE. Given that several projects to produce ammonia with electrolytic hydrogen from VRE are at advanced stages, but the VRE integration challenge remains, the full chain of ammonia from VRE is assessed at TRL 8.
Innovation of the electrolysers themselves also continues, which will bring down capital costs and improve efficiency. Alkaline electrolysers have already been used commercially (TRL 9). Polymer electrolyte membrane (PEM) electrolysers are less commercially developed, but have been scaled up to industrial size with commercial projects in operation (TRL 9) and have several advantages, such as the potential to respond rapidly to required changes in capacity factor even more rapidly than alkaline modules. Solid oxide electrolysers that could considerably reduce electricity input requirements – although provide less flexibility than PEM and alkaline electrolysers – are at the pilot stage (TRL 6). Of course, nitrogen fertiliser production can benefit from technology learnings in the many other sectors where electrolysers are being advanced to produce hydrogen.
Methane pyrolysis is also approaching market readiness. What is expected be the first methane pyrolysis unit to produce ammonia at commercial scale is due to come online in the United States in 2023 or 2024, putting the technology at TRL 7. Other companies and research institutions – primarily in Europe, the United States and Australia – are also developing technologies to produce hydrogen from methane pyrolysis, some of which are likely to be used for ammonia production. Within the broader category of methane pyrolysis, there are three main technologies, plasma, thermal and catalytic, and different variations of these technologies are at different stages of readiness.
PAGE | 115
IEA. All rights reserved.
Ammonia Technology Roadmap |
Chapter 2. The future of ammonia production |
Towards more sustainable nitrogen fertiliser production |
|
Gasification of biomass or waste is also a possible technology option for near- zero-emission ammonia production. While techno-economic evaluations have been completed and biomass gasification is used for other applications, no known projects are pursuing scale-up specifically for ammonia production. This puts biomass gasification for ammonia still at the prototype stage (TRL 5). High costs and competition for sustainable biomass resources from other sectors make this technology route unlikely to play a large role.
R&D is also underway on a variety of other technologies for low-emission ammonia production. Some involve modifications to producing ammonia with Haber-Bosch, while others are based on processes other than Haber-Bosch. These technologies are at the small prototype or lab phase (TRL 4 or lower) and would require considerable further development to reach market readiness. As such, they are not included in the scenarios discussed in this technology roadmap. However, the innovation process involves many uncertainties and advances could occur more rapidly than anticipated. Thus, it is a possible that they could play a role in sustainable ammonia production in the future. Major categories of earlierstage technologies being researched include:
Electrified SMR: hydrogen could be produced using a combination of natural gas for feedstock – for which process emissions are more easily captured – and using electricity to provide process heat. This is challenging given the high-temperature heat required. Other renewable direct heat sources, such as concentrated solar power or geothermal, could also be an option. The Haber-Bosch process would be maintained for ammonia synthesis.
Biological enzymes: such processes would replace Haber-Bosch with biological enzyme catalysts – produced by genetically modified bacteria – that synthesise ammonia directly from water and nitrogen in the air. As such, they would mimic natural biological nitrogen fixation.
Electrochemical production: such processes would replace Haber-Bosch by electrolysis using specific electrolytes and electrocatalysts to synthesise ammonia directly from water and atmospheric nitrogen in the air.
Chemical looping: such processes would produce ammonia as a by-product of chemical and electrochemical reactions, while recycling the core reaction chemicals. Some of these processes would avoid hydrogen production and thus replace Haber-Bosch, while others would produce hydrogen for ammonia synthesis via Haber-Bosch.
Low-temperature catalytic synthesis: such processes would use innovative catalysts at low temperatures (around 50°C) to drive ammonia synthesis, increasing yield and reducing process energy requirements relative to conventional high-temperature Haber-Bosch using an iron catalyst.
PAGE | 116
IEA. All rights reserved.