
02 BOPs / Woods D.R 2008 rules-of-thumb-in-Engineering-practice (epdf.tips)
.pdf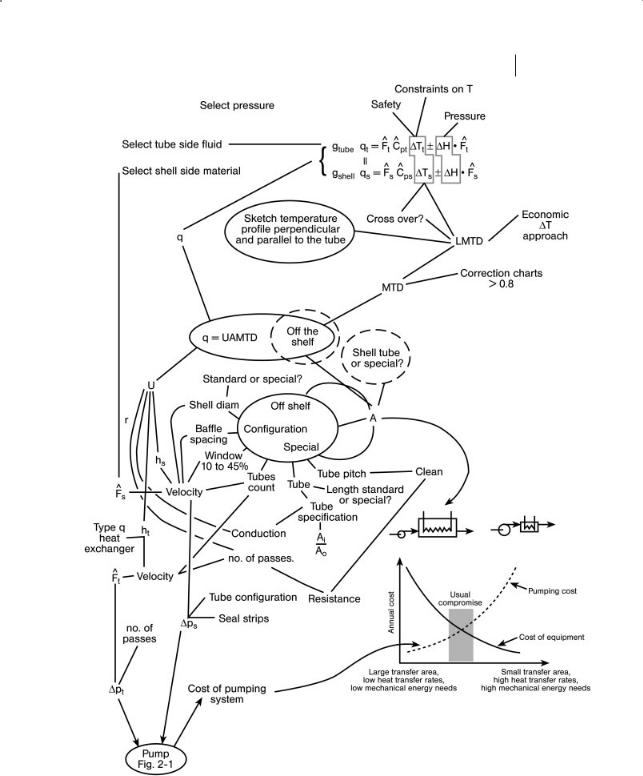
3.3 Thermal Energy: Fluid Heat Exchangers, Condensers and Boilers 71
Figure 3.1 Sizing map for shell and tube heat exchangers.

72 3 Energy Exchange
Tube velocity i 1 m/s; for crude preheat exchangers tube velocity 1–2 m/s; overhead water condensers, tube velocity 1–3.5 m/s. To minimize fouling keep tubeside velocities 3–4.5 m/s, reduce the wall temperature and use single flow channels.
Nozzle velocity I 2 m/s and p, kPa = 0.75–0.9 (nozzle velocity, m/s)2
Baffle cut I 30 %; baffle pitch: minimum should be the maximum of 5 cm or 1/5 of ID shell diameter. the maximum should be the smaller of 0.75 m or shell ID diameter.
Resistance allowances: clean water I 50 hC, 0.0002 m2 K/W; silty water, 0.0006 m2 K/W; steam, 0.0001 m2 K/W; fuel oil, 0.0008 m2 K/W; refrigerants, 0.0002 m2 K/W; vegetable oils, 0.0005 m2 K/W; amines, 0.00 035 m2 K/W; usual hydrocarbons, 0.0003 m2 K/W.
For shell and tube heat exchange: Numerous related topics including evaporation Section 4.1, distillation, Section 4.2, crystallization Section 4.6, freeze concentration Section 4.3, melt crystallization, Section 4.4, PFTR reactors Sections 6.5–6.12. Approach temperature 5 to 8 hC; use 0.4 THTU/pass; design so that the total pressure drop on the liquid side is about 70 kPa. Allow 4 velocity heads pressure drop for each pass in a multipass system. Put inside the tubes the more corrosive, higher pressure, dirtier, hotter and more viscous fluids. Recommended liquid velocities 1 to 1.5 m/s with maximum velocity increasing as more exotic alloys used. Use triangular pitch for all fixed tube sheet and for steam condensing on the shell side. Try U = 0.5 kW/m2 hC for water/liquid; U = 0.3 kW/m2 hC for hydrocarbon/hydrocarbon; U = 0.03 kW/m2 hC for gas/ liquid and 0.03 kW/m2 hC for gas/gas.
Finned tubes: see Air cooled.
For shell and tube condensation: Related topics evaporation Section 4.1, distillation Section 4.2. Prefer condensation outside horizontal tubes; use vertical tubes when condensing immiscible liquids to subcool the condensate. Assume pressure drop of 0.5 of the pressure drop calculated for the vapor at the inlet conditions. Baffle spacing is 0.2 to 1 times the shell diameter with the baffle window about 25 %. Limit pressure drop for steam to 7 kPa on the shell side. U = 0.5–0.85 kW/m2 hC. For shell and tube boiling: approach temperature I 25 hC to ensure nucleate boiling. Related topics evaporation Section 4.1, distillation, Section 4.2, solution crystallization Section 4.6 and reactors PFTR non-adiabatic, Sections 6.8 and 6.12.
– kettle: use for clean, relatively low pressure, nucleate pool boiling; not for foams. 75 to 100 % vaporized. U = 1.1 kW/m2 hC.
–vertical/horizontal thermo syphon: use for clean, relatively low pressure, nucleate pool boiling; 5 to 25 % vaporized; Use 45 to 56 kW/m2 heat flux for hydrocarbon and petrochemicals; 62 to 75 for aqueous and 37 to 44 for vacuum. Rarely use for vacuum or very high pressure service. U = 1 kW/m2 K.
–forced circulation: use for vacuum or viscous/fouling fluids. sensible heat only.
Tube velocity 3–4.5 m/s.
For various configurations of evaporators, see Evaporation, Section 4.1. For steam usage see steam traps, Section 5.1.

3.3 Thermal Energy: Fluid Heat Exchangers, Condensers and Boilers 73
For shell and tube gas reactor with fixed catalyst inside tubes: Related to reactor, Section 6.12.
endothermic reaction in catalytic fired tube. U = 0.045 kW/m2 hC.
exothermic reaction in catalytic multitube non-adiabatic with boiling water or molten heat transfer salt or liquid: 0.05–0.12 kW/m2 hC.
Spiral plate: for large flows and alloy construction select spiral over shell and tube. Heat transfer coefficients about double that of shell and tube; approach temperature 2.8 hC. liquid–liquid U = 2.8–4 kW/m2 hC.
Surface compactness: up to 185 m2/m3.
Lamella/plate (Raman): approach temperature 2 hC; for liquid–liquid U = 1.7–2.5 kW/m2 hC.
Surface compactness: 150–5900 m2/m3.
Gasket/plate: approach temperature 1–2.8 hC; heat transfer coefficients about 3–5 times higher than shell and tube. For liquid–liquid U = 4–4.5 kW/m2 hC. h = 2 kW/m2 hC for hydrocarbons; = 10 kW/m2 hC for water. Surface compactness: 120–1000 m2/m3.
Double pipe: for heat exchange: use for I 20 m2; attractive for the condensation of reacting gases because it provides least area per unit volume.
Air cooled: 2 fins/cm of tube length; use finned tubes on gas side to give less weight, less pressure drop but not for dirty gases on the fin side because of difficulty in cleaning: Use when the potential finned side coefficient is small (0.05–0.1 kW/m2 hC) and when the ratio of tube side to gas side coefficient is 75–300 but not when 1–25. Use hoAo not area only for optimization (because heat transfer coefficient decreases as the fin area increases). Finned tubes with 15–20 m2 total area/m2 bare tube area. 0.4–0.6 kW/m2 hC of bare tube; approach temperature i 26 hC; fan power is 5 to 13 kW/kW thermal energy transferred or 0.15 kW/m2 of bare tube.
Cubic/monolithic: corrosive acids and bases: liquid–liquid U = 0.5 to 1.1 kW/m2 hC. For gas–catalyst heat exchange U = 3.5–7.5 kW/m2 hC. Heat transfer areas up to 2200 m2.
Monolithic catalyst for gas–solid catalytic reactions: U = 3.5–7.5 kW/m2 hC and areas up to 2200 m2.
Agitated falling film: see Evaporation, Section 4.1.
Scraped surface (often horizontal): Votator: thin liquids U = 2.2–4 kW/m2 hC ; viscous films U = 0.8–2.3 kW/m2 hC; crystallization U = 0.15–3.7 kW/m2 hC; sulfonation U = 0.8–2.2 kW/m2 hC; polymerization, U = 1–2.8 kW/m2 hC. See also Evaporation Section 4.1, crystallization, Section 4.6 and reactors, Section 6.20.
Coil in tank: heating U = 0.6–2.5 kW/m2 hC; cooling U = 0.2–1.2 kW/m2 hC. Jacketed: heating U = 0.2–1.7 kW/m2 hC; cooling U = 0.1–0.6 kW/m2 hC;
Half-round pipe on wall: cooling U = 0.3–0.9 kW/m2 hC;
Cooling finger: cooling U = 0.5–1.2 kW/m2 hC.
Thermal screw conveyor: see Section 2.6 but provide heat transfer fluid to the inside of hollow screws. Related to drying, Section 5.6.

74 3 Energy Exchange
x Good Practice
For not truly countercurrent, if the correction factor for the LMTD drops below 0.75 we run the risk of temperature crossover. Provide pressure relief to allow for systems where block valves could isolate trapped fluids. Include impingement baffles at shell inlet nozzles to prevent erosion of tubes and flow induced vibration. For air cooled systems include a trim cooler with water as coolant. Account for the larger heat exchange that occurs for clean tubes/surfaces; the design was based on reduced heat transfer coefficients that account for ultimate dirty film resistance. Ensure the air is vented. Liquids being heated should leave at the top of the exchanger to prevent the buildup of gases coming out of solution and vice versa for liquids with suspended solids or viscous fluids. Orient baffle windows to facilitate drainage. Slope condensers to remove the condensed phase. Maximum cooling water temperature is 45 hC (J). Prefer water or other nonflammable heat transfer media (H). For flammable heat transfer fluids, select operating temperature below its atmospheric boiling temperature (H). If refrigeration is required, prefer less hazardous refrigerant even if this means operating at higher pressures (H). Use pinch analysis, identify inefficient exchanges and retrofit heat exchanger networks to maximize heat recovery. Optimize cleaning schedule. Consider “on-line” mechanical cleaning where fouling is a problem. Use turbulence promoters in laminar flow and gas services and where turndown has significantly reduced the heat transfer coefficient.
Shell and tube heat exchangers: To provide lower inventory and intensify, prefer plate to shell and tube exchangers with the highest surface compactness (H). Shell and tube reboilers: To provide lower inventory and intensify, prefer thermosyphon reboilers to kettle reboilers.
– thermosyphon: Vertical thermosyphon usually not used for vacuum or extremely high pressure service.
Plate exchanger: put regulating and control valves on the inlet lines, never on the outlet lines, to minimize pressure in the exchanger. Never allow the exchanger to be under a vacuum. Keep temperature I 120 hC; pressure I 2.5 MPa.
Air cooled: induced draft preferred to forced draft to minimize hot gas recirculation. Include a water-cooled “trim cooler”. Ensure the exit tubes are “flooded” so that the vapor does not bypass condenser. If extreme cold conditions are expected, allow for fan to operate in reverse to counteract the overcooling by the natural circulation of cold air.
x Trouble Shooting
When trouble shooting heat exchangers, usually the fault is fluid dynamical: liquids do not drain; baffles are placed so that liquid cannot go where we expect; vents are missing that prevent us from bleeding off trapped gases. Thermal expansion will occur when exchangers are brought up to temperature. This may cause a leak at the head-to-tubesheet joint if the difference between the temperature on the tubeside less the temperature of the bolts i 50 hC. For systems involving steam, scrutinize the steam trapping system: ensure that traps are not flooded, that the appropriate trap has been installed, that the bypass is not left

3.3 Thermal Energy: Fluid Heat Exchangers, Condensers and Boilers 75
open, and that thermodynamic traps are not fed to a common header. Steam should come from a nozzle on the top of the steam main; condensate should be discharged into the top of the condensate header.
Shell and tube heat exchangers: “Thermal underperformance on both streams (coolant exit temperature I design; hot exit i design temperature)”: instrument fault/not enough area/thermal load reduced via flowrate or change in thermal properties (e.g., less hydrogen than design)/inerts blinding tubes/[ fouling]* more than expected/tube flooded with condensate (see faulty steam trap, Section 5.1) or trap in backwards or insulated inverted bucket steam trap. “Equipment suddenly begins to underperform”: fouling/bypass open. Temperature control problems”: missing or damaged insulation/poor tuning of controller/not designed for transient state/unexpected heat of reaction effects/contaminated feeds/design error/unexpected heat of solution effects/changes in properties of the fluids. “Heat transfer to shell side fluid I design and Dp I design”: instrument/increase in viscosity/fluid bypasses baffles (baffle cut i 20 %, no sealing strips, excessive baffle clearance, shell side nozzles too far from tube bundle)/stratification/faulty location of exit nozzles/faulty baffling/inlet maldistribution.
“Heat transfer to tubeside I design and uneven (and uneven tube-end erosion at inlet)”: maldistribution to the tubes (axial nozzle entry velocity i tube velocity, for radial nozzle entry velocity i 1.9 tube velocity).
“Heat transfer to one fluid I design and Dp = design”: instrument fault/oil contamination of water.
“Thermal overperformance both fluids, and usually Dp i design on hot fluid side, perhaps charring of cold stream and freezing of hot stream”: instrument fault/cocurrent piped incorrectly as countercurrent/area too large/hydrogen concentration in gas stream i design/clean tubes but design area selected on dirty service.
“Thermal overperformance one stream: cold exit temperature i expected”: instrument/ plugged tubes/inlet velocity I design, fouled screen on pump suction/pump problems, see Section 2.3/increased heat load.
“Poor control of outlet temperatures (e5 hC)”: poor tuning of control/instrument fault/oversized area combined with multipass with local changes in effective MTD with fluid velocity.
“Rapid tube failure or glass or karbate tubes break”: inlet gas velocity too high and directed onto tubes/gas velocity i 5 m/s causing tube vibration/surges in cooling water/surges cause by syphon without vent break.
“Higher Dp when operating at design flows and temperatures”: underdesign/design for two-phase stratified flow but slug flow occurs/gas service but the operating pressure I design.
“Leaks”: erosion/corrosion/vibration/improper tube finishing/cavitation/lack of support for tube bundle/tube end fatigue.
“Noise/vibration”: excessive clearance between baffles and tubes/inlet gas velocity too high and directed onto tubes/gas velocity i 5 m/s causing tube vibration/ surges in cooling water/surges cause by syphon without vent break.
“Gradual reduction in heat transfer and increase in Dp”: small tube leaks.
[Fouling]*: see Section 1.12.

76 3 Energy Exchange
Shell and tube condensers:“Condensation duty I design; exit vapor temperature i design, high flowrate of vapor out vent”: instrument fault/undersized condensers/change in process gas pressure/inward leakage of noncondensibles/change in feed composition/[ fouling]* on the process side/vapor binding/vapor pockets/inert blanketing (usually near the condensate outlet for condensers operated flooded for pressure control)/condensate flooding, see steam traps, Section 5.1/ baffle orientation horizontal not vertical/excessive entrainment in vapor feed/ baffle window i 45 %/drain line too small/leakage between the tubesheet and baffles/bowed tubesheet/condenser designed for horizontal service installed vertically.
“Condensation duty i design:” excess condenser area/clean tubes/condenser designed for vertical service installed horizontally/liquid entrainment in feed.
“Condensation duty I design Dp process i design and excessive flow out vapor vent”: undersized condenser.
“Coolant water temperature i design”: instrument fault/low coolant flowrate/high coolant inlet temperature/cooling tower fault/excess condenser area.
“Cooling water exit temperature i design and higher steam usage in distillation column reboiler and uneven column operation”: excess condenser area via overdesign or clean surfaces.
“Heat transfer drops off i rate than expected and Dp increases faster than expected”: fouling because of oversized kettle reboiler on distillation column or change in pH or flow regime laminar when design was turbulent or higher level of contamination in fluids or crud carry over from upstream equipment (e.g. silica from catalyst in upstream reactor) or compensation for oversize by reduced coolant flowrate.
“Loss of volatile vapor out vent , high vent gas temperature, degree of subcooling I design and unusual temperature profile between vapor inlet and condensate outlet:” instrument error/underdesign.
“Loss of volatile vapor out vent, apparent undersized area for condensation of immiscible liquids”: lack of subcooling of condensate/condenser installed horizontally instead of vertically.
“Fog formation”: high DT with noncondensibles present/high DT with wide range of molar mass of the vapor.
“Equipment suddenly begins to underperform”: fouling/bypass open. “Temperature control problems”: missing or damaged insulation/poor tuning of controller/not designed for transient state/unexpected heat of reaction effects/contaminated feeds/design error/unexpected heat of solution effects/changes in properties of the fluids.
[Fouling]*: see Section 1.12.
Shell and tube reboilers: general:“Low boilup”: [ fouling on process side]*/condensate flooding, see steam trap malfunction, Section 5.1 including higher pressure in the condensate header/inadequate heat supply, steam valve closed, superheated steam/boiling point elevation of the bottoms/inert blanketing/film boiling/increase in pressure for the process side/feed richer in the higher boiling components/undersized reboiler/control system fault/for distillation, overdesigned con-

3.3 Thermal Energy: Fluid Heat Exchangers, Condensers and Boilers 77
denser. “Equipment suddenly begins to underperform”: fouling/bypass open. “Temperature control problems”: missing or damaged insulation/poor tuning of controller/not designed for transient state/unexpected heat of reaction effects/contaminated feeds/design error/unexpected heat of solution effects/changes in properties of the fluids.
“Low boilup and gradual increase in steam pressure to maintain boilup:” [ fouling]*/ inerts in steam.
“Low boilup and gradual decrease in steam pressure to maintain boilup:” steam blowing, see steam trap malfunction, Section 5.1.
“Water contamination”: leak.
“Cycling (30 s – several minutes duration) steam flow, cycling pressure on the process side and, for columns, cycling Dp and cycling level in bottoms”: instrument fault/condensate in instrument sensing lines/surging/foaming in kettle & thermosyphon/ liquid maldistribution/steam trap problems, see Section 5.1, with orifice Dp across trap I design/temperature sensor at the feed zone in a distillation column/ collapsed tray in a distillation column.
“Level high in reboiler”: instrument/inlet or exit pipe nozzle too small/wrong nozzle orientation/steam trap fault, see Section 5.1/steam trap is above the reboiler.
“Breathing: puffs of vapor and entrained liquid leave reboiler:” overdesign/clean tubes when designed for fouled conditions.
[Inadequate heat supply]*: wet steam/too great a Dp across steam valve gives wiredrawing and superheat/steam valve closed/control system fault.
– kettle: rarely underdesigned and not for foams. Trouble shooting: general plus the following symptoms and causes unique to this type of reboiler:
“Surging”: poor liquid distribution/[ fouling]*.
“Low boilup rate and gradual increase in steam”: film instead of nucleate boiling/too high a DT/clean tubes/conservative overdesign/[ fouling]*/flooding with condensate because of steam trap problems, see Section 5.1/bottom temperature elevation/increase in column pressure/feed concentration of light components I design/not enough heating medium.
“Low boilup rate and decrease in steam pressure”: steam trap blowing, see Section 5.1. “Low boilup rate, pressure increase in reboiler and surges”: [ foaming]*/inerts/leaks/ undersized reboiler/diameter of vent line too small/top tubes not covered with liquid/high liquid level that floods the vapor disengagement space/inlet feed maldistribution/inadequate vapor disengagement.
[Fouling on the process side]*: low liquid level causing vapor-induced fouling/solids in feed that are trapped by the overflow baffle.
[Foaming]*: see Section 1.12.
– thermosyphon: general plus the following symptoms and causes unique to this type of reboiler:
“Low boilup”: [ fouling on the process side]*/insufficient steam flow/condensate flooding/low liquid level in distillation column gives low liquid circulation and increased fouling/high liquid level in distillation column (static head i design) or higher density of feed liquid gives higher boiling temperature and circulation and

78 3 Energy Exchange
insufficient vaporization for vertical thermosyphon/pipe lengths I design/pipe diameter i design/process fluid in vertical thermosyphon drops below 30– 40 % of the tube length. For horizontal thermosyphon, appears to be undersized but the cause is liquid feed maldistribution.
“Surges in boilup”: process fluid circulation rate too low/[ fouling on the process side]*/wide boiling range/overdesign.
“Cycling (30 s – several minutes duration) steam flow, cycling pressure on the process side and, for columns, cycling Dp and cycling level in bottoms”: in addition to general, all natural circulation systems are prone to surging/feed contains high w/w % of high boilers/vaporization-induced fouling/contriction in the vapor line to the distillation column. For horizontal thermosyphon: maldistribution of fluid temperature and liquid.
[Fouling]*: insufficient static head/excess friction in the pipes/on the tubeside the outlet nozzle area I total tube area/on tubeside the inlet nozzle area I 0.5 total tube area/rate of vaporization i 25 % of circulation rate/mass rate of vaporization i mass rate of circulation/natural circulation rate I 3 q vaporization rate/vaporization induced solids, and see Section 1.12 for generic fouling.
– forced circulation: operates with sensible heat mode in the tubes. General plus the following symptoms and causes unique to this type of reboiler: “Unstable”: insufficient NPSH in pump, see Section 2.3. “Low boilup and rapid fouling”: insufficient circulation/pump fault, see Section 2.3/plugged circulation lines.
“Low boilup”: [ fouling]*/circulation rate low/pump problems, see Section 2.3/no vortex breaker/excessive circulation and a wide spread in boiling temperatures in bottoms. “Excessive vapor in flash chamber, unstable distillation column operation and apparent underdesign of overhead condenser”: overdesign.
Spiral plate exchanger: “Heat transfer I design”: stratification caused by faulty inlet and exit nozzle location/baffling/maldistribution.
Gasket plate exchanger: “Leaking gaskets”: temperature too high/temperature spike/pressure too high/cold fluid stopped but hot fluid continues/superheated steam/under vacuum.
Air cooled: “Insufficient condensation”: instrument fault/maldistribution along either feed or exit headers/buildup of noncondensibles in bottom tube rows/ insufficient area/ambient temperature too hot/fan not working/blades wrong pitch/baffles stuck/[ fouled tubes]*/hot gas recirculation/tubes not sealed.
“Cycling”: control system/vent for syphon-break is missing on exit manifold.
“Outlet temperature on tube-side is high”: undersized/[tube fouling on inside or outside]*/flow maldistribution on process or air side/hot air recirculation/air flowrate too low. “Dp on process side high”: [ fouled tube side]*/increased liquid viscosity/overcooling/vapor not condensed. “Exit air temperature i expected”: low air flowrate/flow maldistribution on tube side/ambient air temperature i expected/ unexpected hot air recirculation. “Exit air temperature I expected”: high air flowrate/flow maldistribution on tube side/ambient air temperature I expected. “Sluggish control”: the use of fan pitch variation as the control variable. [Fouling]*: see Section 1.12.

3.6 Thermal Energy: Direct Contact L–L Immiscible Liquids 79
3.4
Thermal Energy: Fluidized Bed (Coils in Bed)
Fluidized beds are also used as reactors, Section 6.30; dryers, Section 5.6, and for size enlargement, Section 9.4.
x Area of Application
Use for heating/cooling solids. Mixing provides uniform temperature in the bed and solids increase the heat transfer coefficients 5 to 25 times that of the gas alone.
x Guidelines
Coils in fluidized bed: U = 0.2–0.4 kW/m2 hC; bed to wall U = 0.45–1.1 kW/m2 hC; solids to gas U = 0.017–0.055 kW/m2 hC; thermal conductivity gas–solid thermal conductivity 0.17–42.5 kW/m K.
3.5
Thermal Energy: Static Mixers
Related topics reactors, Section 6.6; mixing, Section 7.1 and Section liquid–liquid, Section 7.2, and size reduction for liquid–liquid, Section 8.3.
x Area of Application
Use for viscosity liquids I 50 mPa s and liquid reactions Section 6.6. Used to cool polymer melts.
x Guidelines:
Cooling melts U = 0.15–0.25 kW/m2 hC. Polymerization: 10 kW/m2 hC. Internal
heat transfer coefficient hinside = 3 q value for fluid flowing in empty pipe of same diameter and length.
3.6
Thermal Energy: Direct Contact L–L Immiscible Liquids
Related topic: size reduction, Section 8.3.
x Area of Application
Exchange heat across liquid–liquid interface. Droplet diameter and area per unit volume estimated from Section 1.6.2 and Fig. 1.2.

80 3 Energy Exchange
x Guidelines
Volumetric overall heat transfer coefficients:
Tray, sieve: Uv = 160 kW/m3 hC; Wetted wall: Uv = 20 kW/m3 hC.
Baffles: Uv = 20 kW/m3 hC;
Spray tower: Uv = 2 to 100 kW/m3 hC; RDC: Uv = 260 kW/m3 hC;
Pipeline: Uv = 200 to 1000 kW/m3 hC.
3.7
Thermal Energy: Direct Contact G–L Cooling Towers
x Area of Application
Use of the latent heat of evaporation of 9 % of hot water to cool the water by removing sensible heat from hot water; size range: 60–1500 L/s.
x Guidelines
Volumetric heat transfer coefficients Uv = 0.5–15 kW/m3 hC; gas superficial velocity 1 m/s; liquid loading 1 L/s m2 cross sectional area.
3.8
Thermal Energy: Direct Contact G–L Quenchers
See Section 1.6.1 for area predictions.
x Area of Application
The quenching media can be any liquid. Gas flowrate 4–100 m3/s.
x Guidelines
Tray: heat transfer coefficient, U = 7–20 kW/m2 hC. of tray area; volumetric heat transfer coefficient, Uv = 3 kW/m3 hC; superficial gas velocity = 1–1.6 m/s; mass loading liquid/gas = 10–20/1.
Packing: volumetric heat transfer coefficient, Uv = 3 kW/m3 hC; superficial gas velocity = 1 m/s; mass loading liquid/gas = 1.5–3/1.
Spray tower: volumetric heat transfer coefficient, Uv = 1.8–5 kW/m3 hC; superficial gas velocity = 1 m/s; mass loading liquid to gas = 1–50/1.
Baffles: volumetric heat transfer coefficient, Uv = 0.5 kW/m3 hC; superficial gas velocity = 0.7–1 m/s; mass loading liquid to gas = 15–60/1.