
Свидунович_Материаловедение_для ХТОМ
.pdfпрочностью, достаточной для изготовления металлоконструкций различного назначения.
Стали обыкновенного качества поставляют горячекатаными в виде проката (прутки, листы, уголки, швейлеры, трубы и т.п.). Для этих сталей марки, химический состав и степень раскисления при выплавке регламентирует ГОСТ 380-94.
Стали маркируют сочетанием букв «Ст» и цифрой (от 0 до 6), показывающей номер марки. Степень раскисления обозначают добавлением в спокойных сталях букв «сп», в полу спокойных — « пс», в кипящих — « кп». Например, СтЗсп, СтЗпс, СтЗкп. Спокойными и полуспокойными производят стали Ст1 - Стб, кипящими — Ст1 - Ст4. Сталь СтО по степени раскисления не разделяют, в этой стали указывают только содержание углерода (С< 0,23 %), серы (S'< 0,06 %) и фосфора (Р < 0,07 %). В остальных марках регламентировано содержание С, Mn, Si, S, Р, а также As и Р (табл. 9.1).
Для всех сталей, кроме СтО, справедлива следующая формула: С (%)« 0,07х номер марки. Так, в стали СтЗ содержание С« 0,07 X 3 и ~ 0,21 % (фактически 0,14 - 0,22 96).
Концентрация марганца возрастает от 0,25 - 0,50 % в стали Ст1 до 0,50 - 0,80 % в стали Ст6. Три марки стали производят с повышенным (0,80 - 1,1 %) содержанием марганца, на что указывает буква «Г» в марке: Ст ЗГпс, СтЗГсп, Ст6Гпс.
Содержание кремния зависит от способа раскисления стали: у кипящих
— не более 0,05 %, у полуспокойных — не более 0,15 %, у спокойных — не более 0,30 %.
Степень раскисления определяет также различное содержание газообразных примесей, а следовательно, порог хладноломкости и возможную температуру эксплуатации. Более надежны спокойные стали, имеющие более низкий порог хладноломкости t50. Так, для сталей СтЗсп, СтЗпс и СтЗкп он составляет -20; -10 и 0° С соответственно.
Механические свойства горячекатаных сталей обыкновенного качества регламентирует ГОСТ 535-88.
Углеродистые качественные стали
Эти стали характеризуются более низким, чем у сталей обыкновенного качества, содержанием вредных примесей и неметаллических включений. Их поставляют в виде проката, поковок и других полуфабрикатов с гарантированным химическим составом и механическими свойствами Маркируют их двухзначными числами: 08, 10, 15, 20, ..., 60, обозначающими среднее содержание углерода в сотых долях процента (ГОСТ 1050-88). Например, сталь 10 содержит в среднем 0,10 % С, сталь 45 - 0,45 % С и т.д.
Спокойные стали маркируют без индекса, полуспокойные и кипящие с индексами соответственно «пс» и «кп». Химический состав спокойных сталей приведен в табл. 9.3. Кипящими производят стали 08кп, 10кп, 15кп, 18кп, 20кп; полу спокойными — 08 пс, 10пс, 15пс, 20пс. В отличие от спокойных кипящие стали практически не содержат кремния (не более 0,03 %); в полуспокойных его количество ограничено 0,05 - 0,17 %.

Содержание марганца повышается по мере увеличения концентрации углерода от 0,25 до 0,80 %. Содержание азота для сталей, перерабатываемых в тонкий лист, ограничено 0,006 %; для остальных сталей — 0,008 %.
Механические свойства зависят от толщины проката: при толщине проката более 80 мм показатели прочности и пластичности несколько ниже . ГОСТ 1050-88 гарантирует механические свойства углеродистых качественных сталей после закалки и отпуска, нагартовки или термической обработки, устраняющей нагартовку — отжига или высокого отпуска.
Качественные стали находят многостороннее применение в технике, так как в зависимости от содержания углерода и термической обработки обладают разнообразными механическими и технологическими свойствами.
Низкоуглеродистые стали по назначению подразделяют на две подгруппы.
1.Малопрочные и высокопластичные стали 08, 10. Из-за способности к глубокой вытяжке их применяют для холодной штамповки различных изделий. Без термической обработки в горячекатаном состоянии эти стали используют для шайб, прокладок, кожухов и других деталей, изготавливаемых холодной деформацией и сваркой.
2.Цементуемые — стали 15, 20, 25. Предназначены они для деталей небольшого размера (кулачки, толкатели, малонагруженные шестерни и т.п.), от которых требуется твердая, износостойкая поверхность и вязкая сердцевина. Поверхностный слой после цементации упрочняют закалкой в воде в сочетании с низким отпуском. Сердцевина из-за низкой прокаливаемости упрочняется слабо. Эти стали применяют также горячекатаными и после нормализации. Они пластичны, хорошо штампуются и свариваются; используются для изготовления деталей машин и приборов невысокой прочности (крепежные детали, втулки, штуцеры и т.п.), а также деталей котлотурбостроения (трубы перегревателей, змеевики), работающих под
давлением при температуре от — 40 до 425 ° С.
Рис. 9.5. Зависимость механических свойств стали 40 от температуры отпуска (а) и диаметра заготовок после отпуска при 580 ° С (б)
Среднеуглеродистые стали 30, 35, 40, 45, 50, 55 отличаются большей прочностью, но меньшей пластичностью, чем низкоуглеродистые (см. табл. 9.3). Их применяют после улучшения, нормализации и поверхностной закалки. В улучшенном состоянии — после закалки и высокого отпуска на

структуру сорбита — достигаются высокая ударная вязкость, пластичность (рис. 9.5, а) и, как следствие, малая чувствительность к концентраторам напряжений. При увеличении сечения деталей из-за несквозной прокаливаемости механические свойства таких сталей снижаются (рис. 9.5,
б).
После улучшения стали применяют для изготовления деталей небольшого размера, работоспособность которых определяется сопротивлением усталости (шатуны, коленчатые валы малооборотных двигателей, зубчатые колеса, маховики, оси и т.п.). При этом возможный размер деталей зависит от условий их работы и требований к прокаливаемости. Для деталей, работающих на растяжение — сжатие (например, шатуны), необходима однородность свойств металла по всему сечению и, как следствие, сквозная прокаливаемость. Размер поперечного сечения таких нагруженных деталей ограничивается 12 мм. Для деталей (валы, оси и т.п.), испытывающих главным образом напряжения изгиба и кручения, которые максимальны на поверхности, толщина упрочненного при закалке слоя должна быть не менее половины радиуса детали. Возможный размер поперечного сечения таких деталей — 30 мм.
Для изготовления более крупных деталей, работающих при невысоких циклических и контактных нагрузках, используют стали 40, 45, 50.
Рис. 9.6. Схема сечения ходового винта после поверхностной индукционной закалки: 1 - закаленный слой; 2 - сердцевина
Их применяют после нормализации и поверхностной индукционной закалки с нагревом ТВЧ тех мест, которые должны иметь высокую твердость поверхности (40 – 58 HRC) и сопротивление износу (шейки коленчатых валов, кулачки распределительных валиков, зубья шестерен И Т П )
Индукционной закалкой с нагревом ТВЧ упрочняют также поверхность длинных валов, ходовых винтов станков (рис. 9.6) и других деталей, для которых важно ограничить деформации при термической обработке.
Легированные стали
Легированные стали производят и поставляют качественными, высококачественными и особовысококачественными. Эта группа сталей многочисленна по числу марок.
Маркировка легированных сталей Марка легированных сталей состоит из сочетания букв и цифр, обо-
значающих ее химический состав. По ГОСТ 4543-71 принято обозначать хром — X, никель — Н, марганец — Г, кремний — С, молибден — М, вольфрам — В, титан — Т, ванадий — Ф, алюминий — Ю, медь — Д, ниобий — Б, бор — Р, кобальт — К. Число, стоящее после буквы, указывает
на примерное содержание легирующего элемента в процентах. Если число отсутствует, то легирующего элемента меньше или около 1 %.
Число в начале марки конструкционной легированной стали показывает содержание углерода в сотых долях процента. Например, сталь 20ХНЗА в среднем содержит 0,20 % С, 1 % Сr и 3 % Ni. Буква А в конце марки означает, что сталь высококачественная. Особовысококачественные стали (например, после электрошлакового переплава) имеют в конце марки букву Ш, например ЗОХГС-Ш.
Некоторые группы сталей содержат дополнительные обозначения: марки подшипниковых сталей начинаются с буквы Ш, автоматных — с буквы А.
Нестандартные легированные стали, выплавляемые заводом «Электросталь», маркируют сочетанием букв ЭИ (электросталь исследовательская) или ЭП (П — пробная) и порядковым номером (например, ЭИ415, ЭП716 и т.д.). После промышленного освоения условное обозначение заменяют на марку, отражающую примерный состав стали.
Низколегированные строительные стали
Общая характеристика Эту группу сталей используют для изготовления металлических кон-
струкций и сооружений из профилей, листов и труб. Из них производят рамы машин и вагонов, металлоконструкции промышленных зданий, пролеты мостов и эстакад, магистральные нефте- и газопроводы. Стали должны обладать достаточной прочностью и пластичностью, малой склонностью к хрупким разрушениям, хорошей технологичностью (свариваемостью, способностью к гибке, правке и т.п.) и хладостойкостью.
Основными расчетными характеристиками металлоконструкций являются временное сопротивление и предел текучести. В соответствии с ГОСТ 27772-88 строительные стали подразделяют на несколько классов прочности. Маркируют их буквой «С» и числом, выражающим значение предела текучести в мегапаскалях: С235, С285, ... , С590, В конце могут стоять буквы К, Т или Д, обозначающие:
К — отличие химического состава стали от состава стали того же класса прочности, например С345К, отличается от С345 наличием
0,08...0,15% А1;
Т — упрочнение проката термической обработкой (для листов из сталей С390, С390К, С440 используют нормализацию или улучшение, для листов из сталей С590 и С590К — только улучшение).
Д — введение в сталь 0,15 - 0,30 % Си для повышения сопротивления атмосферной коррозии.
Механические свойства строительных сталей зависят от толщины проката: чем больше толщина проката (начиная с 4 мм), тем меньше значение σв, σтт и KCU. Тем самым учитываются различия механических свойств из-за разных условий превращения переохлажденного аустенита. Основным требованием для всех видов проката и любых толщин является обеспечение хладостойкости: KCU должна быть не менее 29 Дж/см2 при температурах -
20... - 70 ° С и при 20 ° С после механического старения.
Низколегированные строительные стали разделяют на стали повышенной прочности (σт > 285 МПа) и высокопрочные стали (σт > > 440 МПа). Использование этих сталей вместо углеродистой СтЗ (сталь нормальной прочности σт > 234 МПа) обеспечивает повышение предела текучести в 1,3 - 1,8 раза. Благодаря этому достигается снижение массы
металлоконструкции и сокращение расхода металла на 30 - 50 %. Низкий порог хладноломкости (от -70 до -40 ° С) этих сталей дает возможность использовать их в районах с низкими климатическими температурами
Строительные стали повышенной прочности
Производят и поставляют в соответствии с ГОСТ 19281-89 и ГОСТ 27772-88.) Основными легирующими элементами в них являются недефицитные марганец и кремний (табл. 9.4). Некоторые стали дополнительно содержат небольшое количество ванадия или ниобия, а также медь. Медь вводят в количестве 0,15-0,30 % для повышения стойкости к атмосферной коррозии.1
В сталях этого класса прочности преобладает твердорастворный механизм упрочнения. Определенный вклад вносит повышение устойчивости аустенита при легировании и получение более дисперсных продуктов его распада. Структура сталей состоит из феррита и 10 - 15 % перлита. Для проката толщиной 10 - 40 мм диаметр зерна феррита равен 2050 мкм. Это обеспечивает низколегированным сталям хладостойкость, несмотря на высокую прочность.
Таблица 9.4- Химический состав и механические свойства низколегированных строительных сталей повышенной прочности
Марка |
Содержание элементов, % |
|
σв |
σт |
δ, |
KCU, МДж/м2, |
|||||||||
стали |
|
|
|
|
|
|
|
|
|
|
% |
|
при t, ºС |
||
|
С |
|
Si |
|
Мп |
|
V |
|
МПа |
|
+20 |
|
-40 |
-70 |
|
09Г2 |
< 0,12 |
|
0,17 |
- |
1,4 |
- |
_ |
|
45 |
310 |
21 |
- |
|
0,30 |
- |
|
|
|
0,37 |
|
1,8 |
|
|
|
0 |
|
|
|
|
|
|
09Г2С |
< 0,12 |
|
0,5-0,8 |
|
1,3-1,7 |
- |
|
48 |
330 |
21 |
0,6 |
|
0,35 |
0,3 |
|
|
|
|
|
|
|
|
|
|
0 |
|
|
|
|
|
|
10Г2С |
< 0,12 |
|
0,8 - 1,1 |
|
1,3 |
- |
- |
|
49 |
340 |
21 |
0,6 |
|
0,30 |
0,25 |
1 |
|
|
|
|
1,6 |
|
|
|
0 |
|
|
|
|
|
|
14Г2 |
0,12 |
- |
0,17- |
|
1,2-1,6 |
- |
|
46 |
330 |
21 |
- |
|
0,30 |
- |
|
|
0,18 |
|
0,37 |
|
|
|
|
|
0 |
|
|
|
|
|
|
17ГС |
0,14 |
- |
0,4 - 0,6 |
|
1,0 |
- |
- |
|
50 |
340 |
23 |
- |
|
0,35 |
- |
|
0,20 |
|
|
|
1,5 |
|
|
|
0 |
|
|
|
|
|
|
15ГФ |
0,12 |
- |
0,17- |
|
0,9 |
- |
0,05 |
- |
52 |
360 |
21 |
- |
|
0,30 |
- |
|
0,18 |
|
0,37 |
|
1,2 |
|
0,12 |
|
0 |
|
|
|
|
|
|
15Г2С |
0,12 |
- |
0,4-0,7 |
|
1*3 |
- |
0,05- |
|
56 |
400 |
18 |
- |
|
0,35 |
- |
Ф |
0,18 |
|
|
|
1,7 |
|
0,10 |
|
0 |
|
|
|
|
|
|
Особую группу низколегированных сталей образуют атмосферостойкие стали. Использование их в металлоконструкциях

позволяет обойтись без применения антикоррозионных покрытий. Атмосферостойкость обеспечивают малые количества Сu, Р, Ni, Сг, Si и других элементов, модифицирующие слой ржавчины на поверхности металла. Образующиеся продукты коррозии имеют более высокую плотность и прочность, лучшее сцепление с поверхностью, чем антикоррозионные покрытия. Защитный слой образуется постепенно (через 1,5-3 года), после чего коррозия практически прекращается.
Атмосферостойкие стали производят во многих странах. Химический состав отечественных сталей 10ХНДП и 12ХГДАФ (табл. 9.5) близок к американским сталям Сог Теп А (~ 0,5 Сu, 1,0 Сг, 0,5 Si, 0,5 Ni, О1Р) и Сог Теп В (1,0 Мп, 0,3 Си, 0,6 Сг, 0,02 - 0,1 V, < 0,04 Р). Первую сталь используют для проката толщиной < 12 мм, вторую - < 50 мм. Атмосферостойкие стали имеют σт > 325 МПа.
Высокопрочные стали
Строительные стали высокой прочности (табл. 9.6) производят и поставляют в соответствии с ГОСТ 19281-89 и ГОСТ 27772-88.
Высокая прочность этих сталей достигается карбонитридным упрочнением (в сталях, содержащих ванадий и алюминий и повышенное количество азота (до 0,03%)), термическим упрочнением и контролируемой прокаткой.
Для карбонитридного упрочнения применяют охлаждение с температуры прокатки или нормализацию при 890950 ° С. При охлаждении образуются частицы V (С, N) диаметром 10 - 100 нм и формируется мелкозернистая структура с размером зерен феррита 5-12 мкм. Эта структура мало зависит от толщины проката (при условии, что она не превышает 40 - 50 мм), обеспечивает (σ0.2 — 400 ... 500 МПа и низкие значения t50.
Термическое упрочнение этих сталей заключается в закалке от 850 -920 ° С и высоком отпуске при 600680 ° С. Этому упрочнению подвергают прокат толщиной до 40 - 50 мм из сталей 12Г2СМФ, 14Г2МФ, 12ГН2МФАЮ и 12ХГН2МФБАЮ. После высокого отпуска получается высокодисперсная смесь продуктов распада мартенсита и нижнего бейнита. Однако наибольшая
прочность достигается у сталей с карбонитридным упрочнением благодаря дисперсионному твердению при отпуске (σт = 600... 730 МПа).
Присутствие частиц карбонитридов и нитридов способствует заметному измельчению зерна и обусловливает дополнительное зернограничное упрочнение
Уровень свойств сталей зависит от сочетания легирующих элементов и микродобавок. Наиболее широкое распространение получила сталь 16Г2АФ. После нормализации она имеет мелкое зерно (10-20 мкм), высокую прочность в сочетании с низким порогом хладноломкости.
Особую группу среди высокопрочных строительных сталей образуют малоперлитные (5-10% перлита) стали с карбонитридным упрочнением при низком содержании углерода. Наибольшее применение получили 09Г2ФЮ и
09Г2ФБ. Сталь 09Г2ФБ содержит, %: до 0,12 С; 0,05 Nb; 0,08 V и до 0,015 N.
Следствием снижения концентрации углерода является повышенная ударная вязкость и пластичность, низкий порог хладноломкости этих сталей. Основное их назначение — магистральные нефте- и газопроводные трубы большого диаметра (до 1420 мм) северного исполнения.
ЛЕГИРОВАННЫЕ МАШИНОСТРОИТЕЛЬНЫЕ СТАЛИ
Назначение легирования Легирующие элементы вводлят с целью повышения конструкционной
прочности сталей, что достигается при их использовании в термически упрочненном состоянии — после закалки и отпуска. В отожженном состоянии легированные стали по механическим свойствам практически не отличаются от углеродистых. В связи с этим обеспечение необходимой прокаливаемости — первостепенное назначение легирования. Прокаливаемость стали определяется ее химическим составом. Все легирующие элементы, кроме кобальта, повышают устойчивость переохлажденного аустенита, снижают критическую скорость закалки и увеличивают прокаливаемость.При комплексном легировании высокие механические свойства можно получить практически в сечении любого размера, поэтому комплексно-легированные стали применяют для крупных деталей сложной формы. Возможность менее резкого охлаждения при закалке таких деталей уменьшает в них напряжения и опасность образования трещин.
ВЛИЯНИЕ ЛЕГИРУЮЩИХ ЭЛЕМЕНТОВ НА МЕХАНИЧЕСКИЕ СВОЙСТВА СТАЛЕЙ
Влияние легирующих элементов на механические свойства стали зависит от ее структурного состояния, которое определяется термической обработкой. Рассмотрим это влияние для двух структурных состояний стали.
1. После закалки на мартенсит и низкого отпуска свойства легированной стали определяются концентрацией углерода в мартенсите. Чем она выше, тем больше прочность и твердость, ниже ударная вязкость, выше
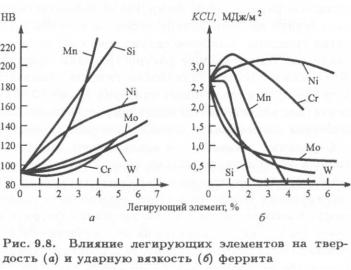
склонность к хрупкому разрушению стали. Максимальное упрочнение достигается уже при 0,4 % С (рис. 9.7). При большей концентрации углерода показатели прочности становятся нестабильными из-за хрупкого разрушения стали, о чем свидетельствуют низкие значения ударной вязкости.
Карбидообразующие элементы (Сг, Мо, W, V) увеличивают прочность связи атомов углерода с атомами твердого раствора, снижают термодинамическую активность (подвижность) атомов углерода, способствуют увеличению его концентрации в мартенсите, т.е. упрочнению. Некарбидообразующие элементы (Ni, Si, Сu, Со), наоборот, увеличивают термодинамическую активность атомов углерода, снижая тем самым концентрацию углерода в твердом растворе. Особенно активно действует никель, предупреждая излишнюю хрупкость мартенсита.
2. После закалки и высокого отпуска (улучшения) структура стали представляет собой сорбит — ферритно-карбидную смесь с зернистой формой карбидной фазы. Высокие механические свойства сорбита обусловлены влиянием легирующих элементов на прочность феррита, а также дисперсность и количество карбидной фазы.
Наиболее сильно повышают твердость медленно охлажденного (нормализованного) феррита (рис. 9.8, a) Si, Mn, Ni, т.е. элементы, имеющие отличную от Fea кристаллическую решетку. Слабее влияют Mo, V и Сг, решетки которых изоморфны Fea.
Упрочняя феррит и мало влияя на пластичность, большинство легирующих элементов снижают его ударную вязкость, особенно если их концентрация выше 1 % (рис. 9.8, б). Исключение составляет никель.
Большинство легирующих элементов измельчает зерно, что способствует повышению работы развития трещины и снижению порога хладноломкости.
Таким образом, для обеспечения высокой конструкционной прочности количество легирующих элементов в стали должно быть рациональным.
Хром вводят в количестве до 2 %. Растворяясь в феррите и цементите, он оказывает благоприятное влияние на механические свойства стали, что
предопределило его широкое применение в конструкционных сталях. Никель — наиболее ценный и в то же время наиболее дефицитный
легирующий элемент. Его добавляют в количестве от 1 до 5 %.
Марганец вводят в количестве до 1,5% и используют нередко как заменитель никеля. Он заметно повышает предел текучести стали, однако делает ее чувствительной к перегреву, поэтому для измельчения зерна вместе с марганцем вводят карбидообразующие элементы.
Кремний — некарбидообразующий элемент, количество которого ограничивают 2 %. Кремний сильно повышает предел текучести, несколько затрудняет разупрочнение стали при отпуске; снижает вязкость и повышает порог хладноломкости при содержании Si свыше 1 %.
Молибден и вольфрам — дорогие и остродефицитные карбидообразующие элементы, которые большей частью находятся в карбидах. Основная цель введения 0,2 - 0,4 % Мо и 0,8 - 1,2 % W — уменьшение склонности к отпускной хрупкости второго рода, улучшение свойств комплекснолегированных сталей в результате измельчения зерна, повышения стойкости к отпуску, увеличения прокаливаемости.
Ванадий и титан — сильные карбидообразователи. Их добавляют в небольшом количестве (до 0,3 % V и 0,1 % Ti) в стали, содержащие хром, марганец, никель, для измельчения зерна. Повышенное содержание этих элементов (так же, как Мо и W) недопустимо, из-за образования специальных труднорастворимых при нагреве карбидов. Избыточные карбиды снижают прокаливаемость и, располагаясь по границам зерен, способствуют хрупкому разрушению.
Бор добавляют в микродозах (0,002-0,005%) для увеличения прокаливаемости. Микролегирование бором эквивалентно введению 1 % Ni; 0,5 % Сr или 0,2 % Мо.
Легированные стали нормальной и повышенной статической прочности
Из сталей нормальной и повышенной прочности наибольшее применение в машино- и приборостроении имеют низкоуглеродистые (цементуемые) и среднеуглеродистые (улучшаемые) стали, содержащие, как правило, в сумме не более 5 % легирующих элементов.
Функциональное назначение низкоуглеродистых сталей — цементуемые (нитроцементуемые) детали (зубчатые колеса, кулачки и т.п.), работающие в условиях трения. После насыщения поверхности углеродом, закалки и низкого отпуска низкоуглеродистые стали наряду с твердой поверхностью (58-63 HRC) имеют достаточно прочную и вязкую сердцевину, устойчивую к воздействию циклических и ударных нагрузок. Работоспособность цементованных деталей зависит от свойств поверхностного слоя и сердцевины. При одних и тех же свойствах цементованного слоя работоспособность деталей повышается по мере увеличения предела текучести и твердости сердцевины. При недостаточном уровне этих свойств под цементованным слоем происходит пластическая деформация, которая вызывает его преждевременное разрушение.

Благоприятное сочетание прочности, пластичности и вязкости, а также высокая хладостойкость (порог хладноломкости лежит в области отрицательных температур) обусловливают применение низкоуглеродистых сталей и без поверхностного упрочнения.
Хромистые стали 15Х, 20Х, а также содержащие дополнительно ванадий (15ХФ) или бор (20ХР), образуют группу дешевых сталей нормальной прочности. Для уменьшения коробления их закаливают не в воде, а в масле. В результате они приобретают структуру троостита или бейнита и упрочняются несколько меньше (см. табл. 9.8). Стали этой группы применяют для небольших деталей (сечением не более 25 мм), работающих при средних нагрузках.
К группе сталей повышенной прочности относятся комплексно-леги- рованные, а также экономно-легированные стали с повышенным содержа-
нием углерода (0,25-0,30%).
Хромоникелевые стали 12ХНЗА, 20ХНЗА, 12Х2Н4А, 20Х2Н4А применяют для крупных деталей ответственного назначения. После закалки в масле эти стали в сечениях до 100 мм имеют структуру низкоуглеродистого мартенсита в смеси с нижним бейнитом, которая обеспечивает сочетание высокой прочности и вязкости.
Хромоникельмолибденовая (хромоникельвольфрамовая) сталь 18Х2Н4МА (18Х2Н4ВА) наиболее высоколегирована и имеет высокие механические свойства.
В этой стали отсутствует перлитное превращение, а температурный интервал бейнитного превращения практически сливается с мартенситным, поэтому при любом, даже очень медленном охлаждении получается структура мартенсита (или смеси мартенсита и бейнита). Отжиг для нее