
Свидунович_Материаловедение_для ХТОМ
.pdf
состоит из стального основания, слоя (250 мкм) свинцовистой бронзы (БрСЗО), тонкого (~ 10 мкм) слоя никеля или латуни и слоя свинцовооловянного сплава толщиной 25 мкм.' Стальная основа обеспечивает прочность и жесткость подшипника; верхний мягкий слой улучшает прирабатываемость. Когда он износится, рабочим слоем становится свинцовистая бронза. Слой бронзы, имеющий невысокую твердость, также обеспечивает хорошее прилегание шейки вала, высокую теплопроводность и сопротивление усталости. Слой никеля служит барьером, не допускающим диффузию олова из верхнего слоя в свинец бронзы.
Рис. 11.7. Схема строения четырехслойного металлического подшипника скольжения: 1 - сплав свинца и олова; 2 - никель; 3 - свинцовистая бронза; 4 – сталь
Из неметаллических материалов для изтотовления подшипников скольжения применяют термореактивные и термопластичные пластмассы (более десять видов). Среди термореактивных пластмасс используют текстолит. Из него изготовляют подшипники прокатных станов, гидравлических машин, гребных винтов. Такие подшипники могут работать в тяжелых условиях, смазываются водой, которая хорошо их охлаждает.
Из полимеров наиболее широко применяют полиамиды: ПС 10, анид, капрон и особенно фторопласт (Ф4, Ф40). Достоинства полимеров: низкий коэффициент трения, высокая износостойкость и коррозионная стойкость.
Исключительно высокими антифрикционными свойствами обладает фторопласт, коэффициент трения которого без смазочного материала по стали составляет 0,04 - 0,06. Однако фторопласт «течет» под нагрузкой и, как все полимеры, плохо отводит теплоту. Его можно применять лишь при ограниченных нагрузках и скоростях. Высокие антифрикционные свойства фторопласта реализуют в комбинации с другими материалами, используя его в виде тонких пленок либо как наполнитель.
Комбинированные материалы состоят из нескольких металлов и неметаллов, имеющих благоприятные для работы подшипника свойства. Рассмотрим подшипники двух типов.
1. Самосмазывающиеся подшипники получают методом порошковой металлургии из материалов различной комбинации: железо — графит, железо — медь (2 - 3 %) - графит или бронза - графит. Графит вводят в
количестве 1 - 4 %. После спекания в материале сохраняют 15 - 35 % пор, которые затем заполняют маслом. Масло и графит смазывают трущиеся поверхности. При увеличении трения под влиянием нагрева поры

раскрываются полнее, и смазочный материал поступает обильнее. Тем самым осуществляется автоматическое регулирование подачи смазочного материала (его запас находится в специальной камере). Такие подшипники работают при небольших скоростях скольжения (до 3 м/с), отсутствии ударных нагрузок и устанавливаются в труднодоступных для смазки местах.
2. Металлофторопластовые подшипники изготовляют из металлофторопластовой ленты (МФПл) в виде свертных втулок методом точной штамповки. Лента состоит из четырех слоев (рис. 11.8). Первый слой (приработочный) выполнен из фторопласта, наполненного дисульфидом молибдена (25 %). Толщина слоя 0,01 - 0,05 мм. В тех случаях, когда допустимый линейный износ достаточно велик, первый слой утолщают до 0,1 - 0,2 мм. Второй слой (~ 0,3 мм) — бронзофторопластовый. Он представляет собой слой пористой бронзы БрО10Ц2, полученный спеканием частиц порошка сферической формы. Поры в этом слое заполнены смесью фторопласта с 20 % РЬ (или фторопласта и дисульфида молибдена). Третий слой (0,1 мм) образован медью. Его назначение — обеспечить прочное сцепление бронзового пористого слоя с четвертым слоем — стальной основой. Толщина основы, которую изготовляют из стали 08кп, составляет 1- 4 мм.
Рис. 11.8. Схема строения металлофторопластовой ленты:
1 - фторопласт с дисульфидом молибдена; 2 - бронза в слое фторопласта; 3 - медь; 4 - сталь
При работе такого подшипника пористый каркас второго слоя отводит теплоту и воспринимает нагрузку, а поверхностный слой и питающий его фторопласт выполняют роль смазочного материала, уменьшая трение. Если первый слой в отдельных местах по какой-либо причине изнашивается, то начинается трение стали по бронзе, что сопровождается повышением коэффициента трения и температуры. При этом фторопласт, имеющий более высокий температурный коэффициент линейного расширения, чем бронза, выдавливается из пор, вновь создавая смазочную пленку.
При тяжелых режимах трения, когда температура нагрева превышает 327 ° С, происходит плавление свинца. Образующаяся жидкая фаза снижает коэффициент трения и тепловыделение.
Металлофторопластовые подшипники имеют высокие антифрикцион-
ные свойства (в диапазоне 200 .. .280° С / = 0,03 .. .0,1; pv - 1500 • 10 5 Па • м/с).
Их используют в узлах трения, работающих без смазочного материала, хотя его введение оказывает благоприятное действие. Они могут работать в вакууме, жидких средах, не обладающих смазочным действием, а также при
наличии абразивных частиц, которые легко «утапливаются» в мягкой составляющей материала. Такие подшипники применяют в машиностроительной, авиационной и других отраслях промышленности.
Минералы — естественные (агат) и искусственные (рубин, корунд) — или их заменители — ситаллы (стеклокристаллические материалы) применяют для миниатюрных подшипников скольжения — камневых опор. Камневые опоры используют в прецизионных приборах — часах, гироскопах, тахометрах и т.д. Главное достоинство таких опор — низкий и стабильный момент трения. Низкое трение достигается малыми размерами опор, что уменьшает плечо действия силы трения, а также небольшим коэффициентом трения вследствие слабой адгезии минералов к металлу цапфы. Постоянство момента трения обусловлено высокой износостойкостью минералов, способных из-за высокой твердости выдерживать громадные контактные давления.
ФРИКЦИОННЫЕ МАТЕРИАЛЫ
Фрикционные материалы применяют в тормозных устройствах и механизмах, передающих крутящий момент; они работают в тяжелых условиях изнашивания — при высоких давлениях (до 6 МПа), скоростях скольжения (до 40 м/с) и температуре, мгновенно возрастающей до 1000 ° С. Для выполнения своих функций фрикционные материалы должны иметь высокий и стабильный в широком интервале температур коэффициент трения, минимальный износ, высокие теплопроводность и теплостойкость, хорошую прирабатываемость и достаточную прочность. Этим требованиям удовлетворяют многокомпонентные неметаллические и металлические спеченные материалы. Их производят в виде пластин или накладок, которые прикрепляют к стальным деталям, например дискам трения. Материал выбирают по предельной поверхностной температуре нагрева и максимальному давлению, которые он выдерживает. Неметаллические
материалы применяют при легких (tпред < 200 ° С, рmax < 0,8 МПа) и средних (tпред = 400 ° С, рмах = 1,5 МПа) режимах трения. Из них преимущественно используют асбофрикционные материалы] состоящие из связующего
(полимеры каучука), наполнителя и специальных добавок. Основным наполнителем является асбест, который придает материалу теплостойкость, повышает коэффициент трения и сопротивление схватыванию. К нему добавляют медь, алюминий, свинец, латунь в виде стружки или проволоки для повышения теплопроводности; графит для затруднения схватывания (этому же способствует свинец, который, расплавляясь, служит как бы жидким смазочным материалом); оксиды или соли металлов (ZnO, BaS04 и др.) для увеличения коэффициента трения.
Из асбофрикционных материалов наибольшей работоспособностью обладает ретинакс (ФК-24А и ФК-16Л), который содержит 25% фенолформальдегидной смолы, 40 % асбеста, 35 % барита, кусочки латуни и пластификатор. В паре со сталью ретинакс обеспечивает коэффициент
трения 0,37-0,40. Его используют в тормозных механизмах самолетов, автомобилей и других машин.
Недостатком неметаллических материалов является невысокая теплопроводность, из-за чего возможны перегрев и разрушение материала.
Металлические спеченные материалы применяют при тяжелых ре-
жимах трения (tпред < 1200 ° С, рmax < 6 МПа). Их производят на основе железа (ФМК-8 и ФМК-11) и меди (МК-5). Кроме основы и металлических
компонентов (Sn, Pb, Ni и др.), обеспечивающих прочность, хорошую теплопроводность и износостойкость, эти материалы содержат неметаллические добавки — асбест, графит, оксид кремния, барит. Они выполняют те же функции, что и в асбофрикционных материалах.
Материалы на основе железа из-за высокой теплостойкости используют в узлах трения без смазочного материала, а материалы на основе меди — при смазывании маслом.
В многодисковой тормозной системе самолетов применяют бериллий из-за его высокой теплоемкости, теплопроводности и малой плотности.
МАТЕРИАЛЫ С ВЫСОКИМИ УПРУГИМИ СВОЙСТВАМИ
ОСНОВНЫЕ ТРЕБОВАНИЯ К ПРУЖИННЫМ МАТЕРИАЛАМ
Стали и сплавы с высокими упругими свойствами находят широкое применение в машино- и приборостроении. В машиностроении их используют для изготовления рессор, амортизаторов, силовых пружин различного назначения; в приборостроении — для многочисленных упругих элементов: мембран, пружин, пластин реле, сильфонов, растяжек, подвесок и т.п.
Пружины, рессоры машин и упругие элементы приборов характеризуются многообразием форм, размеров, различными условиями работы. Особенность их работы состоит в том, что при больших статических, циклических или ударных нагрузках в них не допускается остаточная деформация. В связи с этим пружинные сплавы кроме механических свойств, характерных для конструкционных материалов (прочности, пластичности, вязкости разрушения, выносливости), должны обладать высоким сопротивлением малым пластическим деформациям. В условиях кратковременного статического нагружения сопротивление малым пластическим деформациям характеризуется пределом упругости, при длительном статическом или циклическом нагружении — релаксационной стойкостью.
Релаксационная стойкость оценивается сопротивлением релаксации напряжений. Релаксация напряжений характеризуется снижением рабочих напряжений в изделии от σ1 до σ2 при заданной упругой деформации ε1 (рис. 12.1). Релаксация напряжений опасна тем, что при переходе части упругой деформации в пластическую (εост) упругие элементы после разгрузки изменяют размеры и форму. Например, долгое время сжатая пружина или изогнутая пластина реле при снятии нагрузки полностью не распрямляются и теряют упругие и эксплуатационные свойства.

Рис. 12.1. Диаграмма деформации, объясняющая релаксацию и упругое последействие
Релаксация напряжений происходит путем микропластической деформации, которая совершается в отдельных зернах и накапливается во времени. При напряжении ниже предела упругости микропластическая деформация может быть вызвана изгибом дислокаций или срывом отдельных из них с мест закрепления при малых напряжениях и перемещением заторможенных дислокаций при повышенных напряжениях.
В связи с этим для достижения в сплаве высокого предела упругости и релаксационной стойкости необходимо создать стабильную дислокационную структуру, в которой прочно заблокированы не большинство, а
практически все дислокации. Кроме того, такая структура должна иметь невысокий уровень микронапряжений, которые, суммируясь с рабочими напряжениями, облегчают перемещение дислокаций.
Для закрепления дислокаций используют все средства создания эффективных барьеров: легирование, повышение плотности дислокаций, выделение дисперсных частиц вторичных фаз. Наиболее благоприятную субструктуру, обеспечивающую высокие упругие свойства, формирует термомеханическая обработка. Ее успешно применяют для всех пружинных сплавов.
РЕССОРНО-ПРУЖИННЫЕ СТАЛИ
Рессорно-пружинные углеродистые и легированные стали имеют высокий модуль упругости, ограничивающий упругую деформацию, равную
σ0,002/Е1 .В связи с этим их применяют для изготовления жестких (силовых) упругих элементов. Недорогие и достаточно технологичные рессорно-
пружинные стали широко используют в авто- и тракторостроении, железнодорожном транспорте, станкостроении. Кроме того, они находят применение и для силовых упругих элементов приборов. Часто эти материалы называют пружинными сталями общего назначения.
Для обеспечения работоспособности силовых упругих элементов рес- сорно-пружинные стали должны иметь высокие пределы упругости, выносливости и релаксационную стойкость. Этим требованиям удовлетворяют стали с повышенным содержанием углерода (0,5 - 0,7%), которые
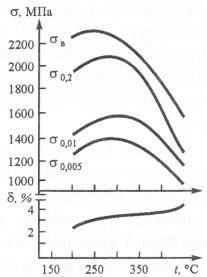
подвергают закалке и отпуску при 420 - 520 ° С.
Закаленная на мартенсит сталь имеет невысокий предел упругости. Он заметно повышается при отпуске, когда образуется структура троостита (рис. 12.2). В этой структуре феррит из-за сильного фазового наклепа имеет высокую плотность малоподвижных дислокаций, которые, кроме того, эффективно блокируются дисперсными карбидными частицами. Поэтому троостит отличается стабильной дислокационной структурой.
Рис. 12.2. Зависимость механических свойств пружинной стали (0,6 % С, 2 % Si) от температуры отпуска
Кроме высоких упругих свойств отпуск на троостит обеспечивает некоторое повышение пластичности и вязкости разрушения (особенно в сталях, не склонных к отпускной хрупкости), что важно для снижения чувствительности к концентраторам напряжений и увеличения предела выносливости.
Хорошие результаты дает также изотермическая закалка на структуру нижнего бейнита. Она обеспечивает высокие механические свойства при малой деформации изделий.
Небольшие пружины простой формы изготовляют из стали, поставляемой в термически обработанном состоянии. Для крупных пружин, требующих больших усилий при навивке, сталь используют в отожженном состоянии. Термической обработке подвергают готовые изделия, полученные горячей навивкой или штамповкой.
Сталь для рессор поставляют в виде полосы. Нарезанные из нее заготовки закаливают в специальных штампах с определенной стрелой прогиба, затем отпускают и собирают в виде пакета. Рессорно-пружинные стали
65, 70, 75, 80, 85, 60Г, 65Г, 70Г (ГОСТ 14959-79) характеризуются невысокой релаксационной стойкостью, особенно при нагреве. Они не пригодны для работы при температурах выше 100 ° С. Из-за низкой прокаливаемое™ из них изготовляют пружины небольшого сечения.
Легированные рессорно-пружинные стали (ГОСТ 14959-79) относятся
к перлитному классу. Основными легирующими элементами в них являются Si (1 - 3 %), Mn (~ 1 %), а в сталях более ответственного назначения — Сг (~ 1%), V (~ 0,15%) и Ni (< 1,7%). Легирование (за исключением Si и Мп) мало влияет на предел упругости — главную характеристику этих сталей. Более существенно оно проявляется в повышении прокаливаемости, релаксационной стойкости, предела выносливости. В связи с этим легированные стали предназначены для больших по размеру упругих элементов и обеспечивают их более длительную и надежную работу.
Дешевые кремнистые стали 55С2, 60С2, 70СЗА применяют для пружин и рессор толщиной до 18 мм. Стали стойки к росту зерна при нагреве под закалку, но склонны к обезуглероживанию — опасному поверхностному дефекту, снижающему предел выносливости. В кремнемарганцевой стали 60СГА этот недостаток выражен менее сильно. Ее преимущественно применяют для рессор толщиной до 14 мм.
Стали 50ХФА, 50ХГФА, которые по сравнению с кремнистыми и кремнемарганцевой сталями подвергают более высокому нагреву при отпуске (520° С), обладают теплостойкостью, меньшей чувствительностью к надрезу. Они предназначены для рессор легковых автомобилей, клапанных и других пружин ответственного назначения, которые могут работать при температурах до 300° С.
Стали 60С2ХА и 60С2Н2А прокаливаются в сечениях соответственно до 50 и 80 мм и применяются для крупных тяжелонагруженных и особо ответственных пружин и рессор. Механические свойства сталей определяются содержанием углерода и температурой отпуска. Отпуск проводят при температуре несколько более высокой, чем та, которая отвечает максимальному пределу упругости, что необходимо для повышения пластичности и вязкости.
Наиболее высокие механические свойства имеют стали 70СЗА,
60С2ХА и 60С2Н2А: σв > 1800 МПа; σ0,2 > 1600 МПа; δ > 5 %; ψ > 20 %. Их предел упругости составляет σ1 = 880 ... 1150 МПа, а твердость — 38 - 48
HRC. При такой прочности и твердости стали чувствительны к концентраторам напряжений, поэтому на сопротивление усталости большое влияние оказывает состояние поверхности. При отсутствии поверхностных дефектов (обезуглероживания, окалины, грубых рисок и др.) предел выносливости сталей при изгибе не ниже 500 МПа, а при кручении — 300 МПа. Для уменьшения чувствительности к концентраторам напряжений готовые пружины и листы рессор подвергают поверхностному наклепу обдувкой дробью. После упрочнения дробью предел выносливости увеличивается в 1,5-2 раза.
МАТЕРИАЛЫ С МАЛОЙ ПЛОТНОСТЬЮ
ОСОБЕННОСТИ МАТЕРИАЛОВ С МАЛОЙ ПЛОТНОСТЬЮ
Материалы с малой плотностью (легкие материалы) широко исполь-

зуются в авиации, ракетной и космической технике, а также в автомобилестроении, судостроении, строительстве и других отраслях промышленности. Применение легких материалов дает возможность снизить массу, увеличить грузоподъемность летательных аппаратов без снижения скорости и дальности полета, повысить скорость движения автомобилей, судов, железнодорожного транспорта.
Основными конструкционными легкими материалами являются пластмассы, цветные металлы Mg, Be, Al, Ti и сплавы на их основе, а также композиционные материалы. Особенно перспективны материалы, которые дают возможность снизить массу конструкций при одновременном повышении их прочности и жесткости. Основными критериями при выборе конструкционных материалов в этом случае являются удельные прочность σв/(ρɡ) и жесткость Е/(ρɡ). По этим характеристикам легкие материалы неравноценны (табл. 13.1)
Таблица 13.1. Прочность, удельная прочность и удельная жесткость легких материалов
Примечание. В скобках указана основа сплава.
АЛЮМИНИЙ И ЕГО СПЛАВЫ
СВОЙСТВА АЛЮМИНИЯ
Алюминий — металл серебристо-белого цвета. Он не имеет полиморфных превращений и кристаллизуется в решетке ГЦК с периодом а = 0,4041 нм.
Алюминий обладает малой плотностью, хорошими теплопроводностью и электрической проводимостью (см. § 1.2), высокой пластичностью и коррозионной стойкостью. Примеси ухудшают все эти свойства алюминия.
Постоянные примеси алюминия — Fe, Si, Си, Zn, Ti. В зависимости от содержания примесей первичный алюминий подразделяют на три класса: особой чистоты А999 (< 0,001 % примесей), высокой чистоты А995, А99, А97, А95 (0,005 - 0,05 % примесей) и технической чистоты А85, А8 и др. (0,15 — 1 % примесей). Технический алюминий, выпускаемый в виде деформируемого полуфабриката (листы, профили, прутки и др.), маркируют А ДО и АД1. Механические свойства алюминия зависят от его чистоты и состояния. Увеличение содержания примесей и пластическая деформация
повышают прочность и твердость алюминия.
Ввиду низкой прочности алюминий применяют для ненагруженных деталей и элементов конструкций, когда от материала требуется легкость, свариваемость, пластичность. Так, из него изготовляют рамы, двери, трубопроводы, фольгу, цистерны для перевозки нефти и нефтепродуктов, посуду и др. Благодаря высокой теплопроводности его используют для различных теплообменников, в промышленных и бытовых холодильниках. Высокая электрическая проводимость алюминия способствует его широкому применению для конденсаторов, проводов, кабелей, шин и т.п.
Следует также отметить высокую отражательную способность алюминия, в связи с чем его используют в прожекторах, рефлекторах, экранах телевизоров. Алюминий имеет малое эффективное поперечное сечение захвата нейтронов, он хорошо обрабатывается давлением, сваривается газовой и контактной сваркой, но плохо обрабатывается резанием. Алюминий имеет большую усадку при затвердевании (6 %). Высокие теплота плавления и теплоемкость способствуют медленному остыванию алюминия из жидкого состояния, что дает возможность улучшать отливки из алюминия и его сплавов путем модифицирования, рафинирования и других технологических операций.
ОБЩАЯ ХАРАКТЕРИСТИКА АЛЮМИНИЕВЫХ СПЛАВОВ
Алюминиевые сплавы характеризуются высокой удельной прочностью, способностью сопротивляться инерционным и динамическим нагрузкам, хорошей технологичностью. Временное сопротивление алюминиевых сплавов достигает 500-700 МПа при плотности не более 2,850 г/см3. По удельной прочности некоторые алюминиевые сплавы σв/(ρɡ) = 23 км) приближаются или соответствуют высокопрочным сталям σв/(ρɡ) = 27 км). Большинство алюминиевых сплавов имеют хорошую коррозионную стойкость (за исключением сплавов с медью), высокие теплопроводность и электрическую проводимость, хорошие технологические свойства (обрабатываются давлением, свариваются точечной сваркой, а специальные
— сваркой плавлением, в основном хорошо обрабатываются резанием). Основными легирующими элементами алюминиевых сплавов являются
Си, Mg, Si, Mn, Zn; реже — Li, Ni, Ti. Многие легирующие элементы образуют с алюминием твердые растворы ограниченной переменной растворимости и промежуточные фазы CuAl2, Mg2Si и др. (рис. 13.1). Это дает возможность подвергать сплавы упрочняющей термической обработке, состоящей из закалки на пересыщенный твердый раствор и естественного или искусственного старения.
Легирующие элементы, особенно переходные, повышают температуру рекристаллизации алюминия (рис. 13.2.). При кристаллизации они образуют с алюминием пересыщенные твердые растворы. В процессе гомогенизации и горячей обработки давлением происходит распад твердых растворов с образованием тонкодисперсных частиц интерметаллидных фаз, препятствующих прохождению процессов рекристаллизации и упрочняющих

сплавы. Это явление получило название структурного упрочнения, а применительно к прессованным полуфабрикатам — пресс-эффекта. По этой причине некоторые алюминиевые сплавы имеют температуру рекристаллизации выше температуры закалки. Для снятия остаточных напряжений в нагартованных полуфабрикатах (деталях), полученных холодной обработкой давлением, а также в фасонных отливках проводят низкий отжиг. Температура отжига находится в пределах 150 — 300 ° С.
Конструкционная прочность алюминиевых сплавов зависит от примесей Fe и Si. Они образуют в сплавах нерастворимые в твердом растворе фазы: FeA13, α(Аl, Fe, Si), β (Аl, Fe, Si) и др. Независимо от формы (пластинчатой, игольчатой и т.д.) кристаллы этих фаз снижают пластичность, вязкость разрушения, сопротивление развитию трещин. Легирование сплавов марганцем уменьшает вредное влияние примесей, так как он связывает их в четверную α-фазу (Al, Fe, Si, Мп), кристаллизующуюся в компактной форме. Однако более эффективным способом повышения конструкционной прочности является снижение содержания примесей с 0,5 - 0,7 % (ГОСТ 4784-74) до 0,1 - 0,3 % (чистый сплав), а иногда и до сотых долей процента (сплав повышенной чистоты). В первом случае к марке сплава добавляют букву "ч", например Д16ч, во втором — буквы "пч", например В95пч. Особенно значительно повышаются характеристики пластичности и вязкости разрушения в направлении, перпендикулярном пластическому деформированию. Например, ударная вязкость сплава Д16ч после естественного старения более чем в два раза, а относительное удлинение в 1,5 раза выше, чем у сплава Д16 после той же обработки. Так, К1с = 43 ... 46 МПа • м1/2 для сплава Д16ч и 35 - 36 МПа • м1/2 для сплава Д16. Сплавы повышенной чистоты используют для ответственных нагруженных деталей, например, для силовых элементов конструкции пассажирских и