
Свидунович_Материаловедение_для ХТОМ
.pdfСтупенчатая закалка. При ступенчатой закалке деталь, нагретую до температуры закалки, переносят в жидкую среду, имеющую температуру на 50—100 ° С выше мартенситной точки Мн закаливаемой стали, и выдерживают небольшое время, необходимое для выравнивания температуры по сечению, а затем окончательно охлаждают на спокойном воздухе
(см. рис. 6.29).
Получение мартенсита при таком способе охлаждения возможно только в легированных сталях с достаточно высокой устойчивостью переохлажденного аустенита в интервале температур перлитного превращения.
К ступенчатой закалке прибегают обычно при термической обработке инструментов небольшого сечения из низко- и среднелегированных сталей. Достоинство указанного способа охлаждения состоит также в возможности правки инструментов в специальных приспособлениях при охлаждении после изотермической выдержки.
Изотермическая закалка. В некоторых случаях после закалки на мартенсит и последующего отпуска не удается получить достаточной прочности и вязкости, тогда применяют изотермическую закалку на нижний бейнит, обладающий высокой вязкостью и прочностью.
При изотермической закалке нагретую деталь переносят в ванну с расплавленными солями, имеющую температуру на 50 — 100 ° С выше мартенситной точки Мн, выдерживают при этой температуре до завершения превращения аустенита в бейнит и затем охлаждают на воздухе (см. рис.
6.29).
Изотермическая закалка, так же как и ступенчатая, применима только к сталям с достаточной устойчивостью переохлажденного аустенита.
Для предотвращения коробления изделий, таких, как ножовки, пилы, бритвы, их охлаждают заневоленными, например, в массивных медных или стальных плитах; скорость охлаждения в этих условиях оказывается меньшей, чем в маслах.
Обработка холодом1. Охлаждение закаленных деталей до температуры, меньшей 20 - 25 ° С, называют обработкой холодом.
Обработке холодом подвергают закаленные легированные стали, для которых температура конца мартенситного превращения Мк значительно ниже 20-25 ° С. Вследствие этого, после охлаждения до этой температуры, наряду с мартенситом в структуре оказывается значительное количество остаточного аустенита. Остаточный аустенит понижает твердость закаленной стали и может вызвать нестабильность размеров готовых деталей,
так как, будучи нестабильной фазой, способен к распаду при низкой температуре с малой скоростью. Для стабилизации размеров закаленных изделий и повышения их твердости проводится охлаждение до температуры Мк, в процессе которого аустенит превращается в мартенсит. Температура Мк легированных сталей изменяется в широких пределах, поэтому при обработке холодом их охлаждают до температур от -40 до -196° С (температуры жидкого азота).
Остаточный аустенит в процессе выдержки при 20 - 25 ° С несколько
стабилизируется, поэтому обработку холодом следует проводить сразу после закалки.
Обработке холодом подвергают измерительные инструменты, детали подшипников качения, цементированные детали из легированных сталей и ряд других изделий.
ЗАКАЛИВАЕМОСТЬ И ПРОКАЛИВАЕМОСТЬ СТАЛЕЙ
Закаливаемость и прокаливаемость — важнейшие характеристики сталей. Закаливаемость определяется твердостью поверхности закаленной детали и зависит главным образом от содержания углерода в стали. При закалке различных деталей поверхность их, как правило, охлаждается со скоростью, большей υкр, следовательно, на поверхности образуется мартенсит, обладающий высокой твердостью.
При закалке любых деталей даже в самых сильных охладителях невозможно добиться одинаковой скорости охлаждения поверхности и сердцевины детали. Следовательно, если скорость охлаждения сердцевины при закалке будет меньше υкр, то деталь не прокалится насквозь, т.е. там не образуется мартенсит.
Прокаливаемостъю называют способность стали закаливаться на определенную глубину. С помощью термокинетических диаграмм можно не только анализировать эту способность стали, но и определять ее, если известны кривые охлаждения закаливаемой детали в различных точках. Этот прием показан на рис. 6.18, где на термокинетическую диаграмму стали 45 нанесены кривые охлаждения в воде детали типа вала в точках, расположенных на поверхности (1) на расстоянии 0,5R от поверхности (2) и в центре (3) вала. Эти кривые получают экспериментальным или расчетным путем. В данном случае кривые расположились так, что при указанных условиях охлаждения на поверхности и на расстоянии 0,5R от нее будет образовываться только мартенситная структура, а в центре вала — смесь перлита с бейнитом.
Иногда на термокинетических диаграммах указывают значения твердости стали после охлаждения с той или иной скоростью. В этом случае
можно построить график изменения твердости по сечению цилиндрического образца данной стали. Такие графики, но полученные экспериментальным путем, приведены в справочниках и характеризуют прокаливаемость сталей.
Условились при оценке прокаливаемоcти закаленными считать слои, в которых содержится не менее 50 % мартенсита (полумартенситная зона). Установлено, что легирование стали любыми элементами, кроме кобальта, увеличивает прокаливаемость, так как при этом повышается устойчивость переохлажденного аустенита. Для экспериментального определения прокаливаемости менее трудоемким оказался способ торцовой закалки (ГОСТ 5657-69). Цилиндрический образец, диаметром 0,025 м и длиной 0,1 м, нагретый до температуры закалки, охлаждают струей воды только с торца на специальной установке. После охлаждения измеряют твердость по

образующей цилиндра и строят график изменения твердости по длине образца (рис. 6.30). Оригинальным в этом способе является то, что каждая точка поверхности стандартного образца охлаждается с различной и вполне определенной скоростью. Сопоставление двух кривых на рис. 6.30 наглядно показывает, что сталь, характеризуемая кривой 2, имеет более высокую прокаливаемость, чем сталь, у которой твердость изменяется в соответствии с кривой 1. Прокаливаемость стали одной и той же марки в зависимости от изменений химического состава, размера зерна аустенита (температуры нагрева), размера и формы детали и т.д. колеблется в значительных пределах. В связи с этим в справочниках прокаливаемость стали каждой марки характеризуется не кривой, а полосой прокаливаемости.
ОТПУСК ЗАКАЛЕННЫХ СТАЛЕЙ
Нагрев закаленных сталей до температур, не превышающих А1, называют отпуском.
В результате закалки чаще всего получают структуру мартенсита с некоторым количеством остаточного аустенита, иногда — структуру сорбита, троостита или бейнита.
Изменение структуры мартенситно-аустенитной стали при отпуске При отпуске происходит несколько процессов. Основной — распад
мартенсита, состоящий в выделении углерода в виде карбидов. Кроме того, распадается остаточный аустенит, совершаются карбидное превращение и коагуляция карбидов, уменьшаются несовершенства кристаллического строения а-твердого раствора и остаточные напряжения.
Фазовые превращения при отпуске принято разделять на три превращения в зависимости от изменения удельного объема стали. Распад мартенсита и карбидное превращение вызывают уменьшение объема, а распад аустенита — его увеличение.
На рис. 6.31 схематично показано изменение длины закаленного образца углеродистой стали при отпуске, в которой было значительное количество остаточного аустенита. В сталях, не содержащих легирующих элементов,

первое превращение происходит в интервале температур 80-200° С, второе при 200-260° С, третье при 260-380° С (см. рис. 6.31, I - III).
I. Из мартенсита выделяется часть углерода в виде метастабильного е- карбида, имеющего гексагональную решетку и химический состав, близкий к FезС. Дисперсные кристаллы ε-карбида когерентны с решеткой мартенсита. Обеднение твердого раствора углеродом происходит неравномерно: наряду с участками мартенсита, обедненного углеродом (вблизи карбидов), сохраняются участки с исходным содержанием углерода. Первое превращение идет с очень малой скоростью и без нагрева. Уменьшение количества растворенного углерода снижает тетрагональность мартенсита — длина образца уменьшается.
Содержание углерода в мартенсите в интервале температур первого превращения зависит от исходного количества углерода (рис. 6.32), тогда как при более высоком нагреве оно определяется лишь температурой.
П. Одновременно происходит несколько процессов: продолжается распад мартенсита, распадается остаточный аустенит и начинается карбидное превращение. Распад мартенсита распространяется на весь объем, концентрационная неоднородность твердого раствора исчезает; в мартенсите остается около 0,2 % растворенного углерода. Распад остаточного аустенита происходит по механизму бейнитной реакции: образуется смесь кристаллов низкоуглеродистого мартенсита и дисперсных карбидов. При температурах около 250 ° С начинается превращение ε-карбида в цементит; при этом когерентность решеток твердого раствора и карбида нарушается.
Если в закаленной стали было много остаточного аустенита, то уменьшение плотности при распаде будет большим, чем ее увеличение, вследствие выделения углерода из мартенсита. В этом случае (см. рис. 6.31) длина закаленного образца возрастает.
III. Завершаются распад мартенсита и карбидное превращение. Из мартенсита выделяется весь пересыщающий углерод в виде карбидов, тетрагональность решетки α-твердого раствора устраняется — мартенсит переходит в феррит. После отпуска при 380 —400° С в структуре стали обнаруживается только карбид цементитного типа. Оба указанные процесса вызывают увеличение плотности стали — длина образца уменьшается (см.
рис. 6.31).
Ферритно-карбидная смесь, образовавшаяся в конце третьего превра-
щения, весьма дисперсна и имеет примерно такую же твердость, как троостит (ее называют трооститом отпуска). Структуру стали, образовавшуюся при температурах первого и второго превращений, называют отпущенным мартенситом.
При более высоких нагревах в углеродистых сталях происходят изменения структуры, не связанные с фазовыми превращениями: изменяются форма, размер карбидов и структура феррита.
Винтервале температур третьего превращения цементит имеет форму тонких пластин. С повышением температуры происходит коагуляция: кристаллы цементита укрупняются (более мелкие кристаллы распадаются, а более крупные растут); при этом форма кристаллов постепенно приближается к сфероидальной. Коагуляция и сфероидизация карбидов происходят с заметной скоростью начиная с температур 350-400 ° С. Скорость этих процессов увеличивается при повышении температуры.
Изменения структуры феррита обнаруживаются начиная с температуры около 400 ° С: уменьшается плотность дислокаций, которая очень велика в мартенсите до отпуска; постепенно устраняются границы между пластинчатыми кристаллами феррита, в результате чего зерна феррита
укрупняются и их форма приближается к равноосной. Таким образом, с повышением температуры отпуска постепенно снимается фазовый наклеп, возникший при мартенситном превращении.
Ферритно-карбидную смесь, которая образуется после отпуска при 450
—650 ° С, называют сорбитом отпуска. После отпуска при температуре, близкой к температуре А1, образуется грубая ферритно-карбидная смесь — зернистый перлит.
Влияние легирующих элементов на процесс отпуска
Многие легирующие элементы повышают температуры II и III превращений, уменьшают скорость коагуляции карбидов и влияют на карбидные превращения при отпуске.
При легировании сталей Сг, Мо, W, V, Со и Si затрудняется распад мартенсита: он завершается при нагреве до 450 - 500 ° С; карбидообразующие элементы (Сг, Мо, W, V) уменьшают скорость диффузии углерода вследствие химического сродства с ним; Со и Si, не образующие карбидов в сталях, а также большинство карбидообразующих элементов увеличивают силы межатомной связи в твердом растворе. Вследствие этого стали приобретают повышенную сопротивляемость отпуску (теплостойкость).
Всталях с большим количеством карбидообразующих элементов температурой отпуска определяется тип выделяющихся карбидов. При температурах до ~ 400 ° С подвижность атомов легирующих элементов весьма мала, поэтому вместо специальных карбидов из мартенсита, так же как и в углеродистых сталях, выделяется карбид железа, для образования которого требуется лишь перемещение атомов углерода. При более высоких температурах становится возможным образование специальных карбидов: кристаллы цементита постепенно исчезают, а вместо них появляются более дисперсные специальные карбиды.
Многие легирующие элементы повышают температурный интервал распада остаточного аустенита до 400 - 580 ° С. В сталях с большим количеством карбидообразующих элементов изменяется и механизм распада: при температуре отпуска из аустенита выделяются специальные карбиды, легированность аустенита уменьшается, и он приобретает способность к превращению при охлаждении — по достижении температуры Мн начинается превращение аустенита в мартенсит.
Все карбидообразующие элементы замедляют коагуляцию карбидов; наиболее медленно коагулируют специальные карбиды типа Ме6С и
МеС, их заметное укрупнение происходит при температуре, большей
550600° С.
В зависимости от температурного интервала принято различать три вида отпуска: низкий при 120-250 ° С, средний при 350-450 ° С и высокий при 500 — 680° С. Продолжительность выдержки при отпуске устанавливают с таким расчетом, чтобы обеспечить стабильность свойств стали. При низком отпуске инструментов продолжительность его чаще всего составляет 0,5 - 2 ч в зависимости от сечения инструмента. Продолжительность отпуска увеличивается до 10 - 15 ч, если температура низкого отпуска не превышает 100 —120 ° С. В этом случае, например, при отпуске измерительного инструмента, когда падение твердости нежелательно, такой продолжительный отпуск позволяет исключить объемные изменения в процессе эксплуатации инструмента.
Продолжительность среднего и высокого отпуска обычно составляет 1 - 2 ч для деталей небольшого сечения и 3 - 8 ч для деталей массой от 200 до 1000 кг (диски газовых и паровых турбин, валы и цельнокованые роторы турбин и другие детали большой массы).
Так как структура отпущенной стали формируется в период выдержки при температуре отпуска, интенсивность последующего охлаждения не оказывает влияния на структурное состояние стали. Обычно от температуры отпуска детали охлаждают на спокойном воздухе.
Отпуск стали с дисперсной структурой перлита или беинита Сорбит, троостит или бейнит образуются при охлаждении стали из
аустенитной области со скоростью, меньшей υкр. Эти структуры часто образуются в отливках, а также в поковках, штамповых заготовках и сортовом прокате из легированных сталей при охлаждении их на воздухе от температуры деформации. При нагреве до температур, меньших температуры А1, будут происходить структурные изменения, т.е. указанные структуры тоже «отпускаются».
При нагреве углеродистых сталей с дисперсными перлитными структурами происходят коагуляция и сфероидизация карбидов. В легированных сталях возможны и карбидные превращения: если перлитная структура появилась при значительном переохлаждении аустенита (например, структура троостита), когда образование специальных карбидов затруднено, отпуск при 600 - 700 ° С вызовет превращение цементита в специальный карбид.
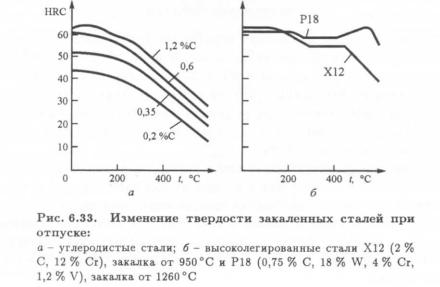
При отпуске бейнитных структур, помимо указанных процессов, происходит выделение карбидов из α-твердого раствора и изменение структуры феррита, как и при отпуске мартенсита.
Свойства отпущенной стали Твердость отпущенной стали определяется несколькими факторами:
уменьшение тетрагональности решетки, степени фазового наклепа и укрупнение карбидных частиц вызывают снижение твердости; выделение когерентных кристаллов е-карбида и дисперсных кристаллов специальных карбидов, а также распад остаточного аустенита способствуют ее повышению.
В конструкционных сталях, в которых количество углерода обычно не превышает 0,7%, твердость уменьшается непрерывно, однако ее снижение невелико до 100 — 120 ° С. В инструментальных сталях с более высоким содержанием углерода эффект твердения вследствие выделения е-карбида преобладает, поэтому твердость при отпуске до 100 — 120 ° С несколько увеличивается. Изменение твердости углеродистых сталей в интервале температур II превращения в большой степени зависит от количества остаточного аустенита; например, в стали с содержанием 1,2 % С в интервале 200 — 300 ° С интенсивность снижения твердости уменьшается (рис. 6.33, а).
Аналогично изменяется твердость при отпуске низколегированных и среднелегированных сталей, не содержащих карбидообразующих легирующих элементов. Сильные карбидообразователи задерживают выделение карбидов железа, поэтому при температуре отпуска до 400 - 500 ° С твердость снижается незначительно (рис. 6.33, б). При температурах выделения дисперсных специальных карбидов в сложнолегированных сталях (Сг, W, V; Сг, Мо, V и др.) происходит повышение твердости несмотря на уменьшение содержания углерода в мартенсите. Увеличение твердости у сталей с хромом, вольфрамом (молибденом) и ванадием наблюдается при температуре 500 -
560 ° С.
Для закаленной и неотпущенной сталей характерны довольно низкие значения временного сопротивления, предела упругости и предела текучести;

при отпуске до 300 ° С эти характеристики прочности возрастают, а при дальнейшем ее повышении монотонно снижаются. Наиболее высокое отношение σ0,2/ σв в конструкционных сталях достигается после отпуска при
300 - 350'°С (рис. 6.34).
Характеристики пластичности δ и ψ возрастают по мере повышения температуры отпуска (см. рис. 6.34). Ударная вязкость непосредственно после закалки низкая. С повышением температуры отпуска ударная вязкость увеличивается, однако есть два температурных интервала, при которых у конструкционных сталей она заметно снижается: 250 - 350 и 500 - 600 ° С. Понижение вязкости соответственно называют отпускной хрупкостью I и II рода (рис. 6.35). Природа охрупчивания сталей после отпуска при указанных температурах недостаточно ясна.
Понижение ударной вязкости после отпуска при 250 — 350° С наблюдается у всех конструкционных сталей независимо от степени легирования.
Заметное падение ударной вязкости после отпуска при 500 |
— 600° С |
наблюдается только у легированных конструкционных сталей — |
хромистых, |
марганцевых, хромоникелевых, хромомарганцевых и т.д. Снижения вязкости почти не происходит в случае быстрого охлаждения от температуры отпуска (в воде или масле). Отпускная хрупкость II рода заметно подавляется даже при медленном охлаждении от температуры отпуска дополнительным легированием сталей молибденом или вольфрамом в количестве 0,3 и 1 % соответственно.
Комплексную термическую обработку, состоящую из полной закалки и высокого отпуска конструкционных сталей, называют улучшением.
ОБОРУДОВАНИЕ ДЛЯ ТЕРМИЧЕСКОЙ ОБРАБОТКИ
К основному оборудованию для термической обработки относятся печи, нагревательные установки и охлаждающие устройства. По источнику теплоты печи подразделяют на электрические и топливные (газовые и редко

— мазутные).
Для того чтобы избежать окисления и обезуглероживания стальных деталей при нагреве, рабочее пространство современных термических печей заполняют специальными защитными газовыми средами или нагревательную камеру вакуумируют. Для повышения производительности при термической обработке мелких деталей машин и приборов применяют скоростной нагрев, т.е. детали загружают в окончательно нагретую печь. Возникающие при нагреве временные тепловые напряжения не вызывают образования трещин и короблений. Однако скоростной нагрев опасен для крупных деталей (прокатных валков, валов и корпусных деталей), поэтому такие детали нагревают медленно (вместе с печью) или ступенчато. Иногда быстрый нагрев проводят в печах-ваннах с расплавленной солью (сверла, метчики и другие мелкие инструменты). На машиностроительных заводах для термической обработки применяют механизированные печи (рис. 6.36) и автоматизированные агрегаты.
Механизированная электропечь предназначена для закалки штампов или мелких деталей, укладываемых на поддон. Нагревательную и закалочную камеру можно заполнять защитной атмосферой, предохраняющей закаливаемые детали от окисления и обезуглероживания. С помощью цепного механизма 5 поддон с деталями по направляющим роликам перемещается в нагревательную камеру 4.
После нагревания и выдержки тем же цепным механизмом поддон перемещается в закалочную камеру 2 и вместе со столиком 1 погружается в закалочную жидкость (масло или воду). После охлаждения столик поднимается пневмомеханизмом, и поддон выгружается из печи. Детали нагре-

ваются в результате излучения электронагревателей 6 и конвективного теплообмена. Вентиляторы 3, установленные в нагревательной камере и в закалочном баке, предназначены для интенсификации теплообмена, а также равномерного нагрева и охлаждения деталей.
В механизированных и автоматизированных агрегатах проводят весь цикл термической обработки деталей, например закалку и отпуск. Такие агрегаты состоят из механизированных нагревательных печей и закалочных баков, моечных машин и транспортных устройств конвейерного типа.
Поверхностный нагрев деталей проводят тогда, когда в результате поверхностной закалки требуется получить высокую твердость наружных слоев при сохранении мягкой сердцевины. Чаще всего закаливают наружный слой трущихся деталей машин.
Наиболее совершенным способом поверхностной закалки является закалка в специальных установках с нагревом токами высокой частоты. Этот способ нагрева очень производителен; может быть полностью автоматизирован и позволяет получать при крупносерийном производстве стабильное высокое качество закаливаемых изделий при минимальном их
короблении и окислении поверхности. Известно, что с увеличением частоты тока
возрастает скин-эффект; плотность тока в наружных слоях проводника оказывается во много раз большей, чем в сердцевине. В результате почти вся тепловая энергия выделяется в поверхностном слое и вызывает его разогрев.
Нагрев деталей токами высокой частоты осуществляется индуктором. Если деталь имеет небольшую длину (высоту), то вся ее поверхность может быть одновременно нагрета до температуры закалки. Если же деталь длинная (рис. 6.37), нагрев происходит последовательно путем перемещения изделия относительно индуктора с рассчитанной скоростью.
Охлаждение при закалке с нагревом токами обычно осуществляется водой, подающейся через спрейер — трубку с отверстиями для разбрызгивания воды, изогнутую в кольцо и расположенную относительно детали аналогично индуктору. Нагретый в индукторе участок детали или все изделие, перемещаясь, попадает в спрейер, где и охлаждается.
Преимущество поверхностной закалки деталей, так же как и большинства способов упрочнения поверхности (химико-термическая обработка, поверхностный наклеп, обкатка), состоит в том, что в поверхностных слоях деталей возникают значительные сжимающие напряжения.
В последнее время для термической обработки некоторых деталей применяют источники высококонцентрированной энергии (электронные и лазерные лучи).