
техн трансп обсл и рем уч метод компл
.pdfмойку одного автомобиля – 1200…1300 л. Автомобиль передвигается конвейером.
Значительное уменьшение расхода воды обеспечивают системы оборотного водоснабжения. В соответствии с принятым законодательством все водопользователи обязаны принимать меры по сокращению расхода воды и прекращению сброса неочищенных сточных вод. Поэтому все АТП должны иметь очистные сооружения и систему оборотного использования воды.
Сушка кузова производится после окончательного ополаскивания его чистой водой. При механизации процесса внешнего ухода за автомобилями для сушки кузова применяют обдув холодным или подогретым воздухом.
Главной целью полирования кузова является создание стойкого защитного слоя на его поверхности, предохраняющего металлическую основу кузова от агрессивного влияния окружающей среды. Поэтому как новые, так и старые кузова автомобилей подвергаются периодической обработке полиролями. Новые кузова обрабатывают 1 раз в 1,5 – 2 мес. При этом используются полироли, созданные на основе водоотталкивающих средств, эмульгаторов, растворителей и воды. Для старых, потерявших блеск лакокрасочных покрытий используют автополироль, составной частью которой является композиция абразивных материалов.
Контрольно-диагностические работы предназначены для определения и обеспечения соответствия автомобиля требованиям безопасности движения и воздействия автомобиля на окружающую среду, для оценки технического состояния агрегатов, узлов без их разборки. Эти работы являются составной частью процесса технического обслуживания и ремонта. Диагностирование какого либо агрегата (системы) проводится на специальных стендах приспособлениями, приборами. Принцип их действия зависит от характера диагностических признаков, которые присущи объекту контроля.
Регулировочные работы, как правило, являются заключительным этапом процесса диагностирования. Они предназначены для восстановления работоспособности систем и узлов и автомобиля без замены составных частей. Специальными регулировочными узлами в конструкции автомобиля (эксцентрики в тормозных барабанах, натяжные устройства приводных ремней, поворотные устройства прерывателей-распределителей и т.д.) устанавливают нормативные параметры. Многие наиболее важные характеристики автомобиля (расход топлива, мощность, износ шин, тормозной путь) в большинстве случаев зависит от своевременности и качества выполнения диагностических и регулировочных работ.
Крепежные работы предназначены для обеспечения нормального состояния (затяжки) резьбовых соединений. В объеме ТО в зависимости от вида ТО и типа подвижного состава эти работы составляют примерно 30%. При ТО-1 необходимо проверить и, если требуется, подтянуть несколько десятков соединений. При ТО-2 это число возрастает еще больше. При текущем ремонте с крепежными работами связано большинство монтажнодемонтажных, сборочно-разборочных операций. Поэтому применение
191
правильных приемов по обслуживанию резьбовых соединений позволяет повысить эксплуатационную надежность автомобиля в целом, облегчить труд рабочих и резко снизить трудоемкость работ. Резьбовые соединения обеспечивают сборку узлов как посредством резьбы, находящейся непосредственно на детали (свеча зажигания, шаровые пальцы шарниров рулевого привода, регулировочные винты в механизме газораспределения), так и при помощи крепежных деталей – винтов, болтов, шпилек, гаек специального назначения.
Подъемно-транспортные работы составляют значительную часть производящихся на АТП при ТО и ТР работ, связанных с перемещением автомобилей с поста на пост, а также с подъемом и перемещением агрегатов и узлов большой массы: двигателя, коробки передач, мостов, редукторов заднего моста и др. В зонах ТО-2 и ТР и на поточных линиях автомобили могут перемещаться собственным ходом, перекатыванием или с помощью специальных конвейеров. На постах ТР агрегаты поднимают и транспортируют с помощью различных подъемно-транспортных механизмов, оборудованных захватами, гарантирующими безопасность работы. Делается это с помощью электротельфера, перемещающегося по монорельсу, или кранбалки, а в случае их отсутствия с помощью передвижных гидравлических кранов и грузовых тележек.
Для подъема автомобиля над уровнем пола при обслуживании и ремонте используют стационарные подъемники различных конструкций. Для вывешивания переднего и заднего мостов при работах на осмотровых канавах широко используют канавные подъемники. Для подъема передних и задних частей автомобиля при работе на напольных постах используют гаражные домкраты различной грузоподъемности. Наличие указанных средств на постах ТО и ТР обеспечивает необходимый уровень механизации подъемноосмотровых работ, повышает производительность труда и культуру производства.
Разборочно-сборочные работы являются начальной и конечной операциями текущего ремонта автомобилей. Эти работы включают замену неисправных агрегатов, механизмов и узлов автомобиля на исправные, замену в них неисправных деталей на новые или отремонтированные, а также разборочно-сборочные работы, связанные с ремонтом отдельных деталей и подгонкой их по месту установки. Наиболее характерными являются работы по замене двигателей, мостов, коробки передач, радиаторов, сцеплений, рессор, износившихся деталей в агрегатах и узлах. Выполняют их на постах ТР, где производят снятие с автомобилей неисправных и установку новых или отремонтированных агрегатов, узлов и деталей. Здесь же выполняют работы по частичной разборке и устранению неисправностей агрегатов, не снимаемых с автомобиля.
Трудоемкость разборочно-сборочных работ, выполняемых на постах, значительна. В зависимости от модели автомобиля она составляет 28 – 37% общей трудоемкости собственно постовых работ.
192
Кроме постов ТР, разборочно-сборочные работы проводятся практически во всех других производственных отделениях, куда поступают для ремонта различные агрегаты и узлы, снятые с автомобиля. Качество разборочно-сборочных работ в значительной мере определяет эксплуатационную надежность подвижного состава. Даже небольшие улучшения в организации разборочно-сборочных работ дают значительный технико-экономический эффект. Так, проведенная согласно технологии разборка обеспечивает сохранность деталей, уменьшает трудоемкость последующего ремонта. При правильной организации разборочного процесса на АТП повторно используют 70 -80% деталей. С целью повышения уровня механизации при разборке-сборке необходимо использовать различные гайковерты, приспособления, наборы ключей и т.д.
Разборочно-сборочные работы на агрегатном участке, как правило, проводят на специализированных стендах, обеспечивающих свободный доступ к ремонтируемому агрегату, а также поворот и наклон агрегата для удобства работы. Разборка-сборка различных узлов, например электрооборудования, топливной аппаратуры, проводится в основном на верстаках с применением универсального инструмента и специальных приспособлений.
Слесарно-механические работы включают изготовление крепежных деталей (болтов, гаек, шпилек, шайб), механическую обработку после наплавки или сварки, растачивание втулок для тормозных барабанов, изготовление и растачивание втулок для восстановления гнезд подшипников, протачивание рабочей поверхности нажимных дисков сцепления и т.д. Проводятся перечисленные работы на слесарно-механическом участке АТП с помощью токарно-винторезных станков, сверлильных, фрезерных, шлифовальных и других универсальных металлообрабатывающих станков, а также вручную на слесарных верстаках. В общей трудоемкости ТР слесарномеханические работы составляют 4…12%.
Кузнечные работы представляют пластическую обработку металлических деталей и составляют примерно 2…3% объема работ по текущему ремонту. Основная доля связана с ремонтом рессор – заменой сломанных листов, рихтовкой (восстановление первоначальной формы) просевших. Кроме того, изготавливают различного вида стремянки, скобы, хомуты, кронштейны.
Жестяницкие работы в основном представляют ремонт повреждений кузовов автобусов и легковых автомобилей (7…9% объема ТР) и кабин грузовых (примерно 2,5% объема ТР). В указанные объемы входят сопутствующие сварочные работы.
Сварочные работы предназначены для ликвидации трещин, разрывов, поломок, а также прикрепления различных кронштейнов, уголков и т.д. На АТП применяют как электродуговую, так и газовую сварку. Электросваркой ремонтируют массивные детали (раму, кузов самосвала), газовой, как правило, - тонкостенные детали. Сварочные работы без учета работ по
193
ремонту кузовов легковых автомобилей, кабин грузовых составляют 1,0-1,5% объема текущего ремонта.
Медницкие работы составляют примерно 2% объема работ по текущему ремонту и предназначены для восстановления герметичности деталей, изготовленных в основном из цветных металлов. Это пайка радиаторов, поплавков карбюраторов, латунных трубопроводов и др.
Смазочно-заправочные, очистительно-промывочные работы предназначены для уменьшения интенсивности изнашивания и сил сопротивления в узлах трения, а также для обеспечения нормального функционирования систем, содержащих технические жидкости, смазки. Эти работы составляют значительный объем ТО-1 (16 – 26%) и ТО-2 (9 – 18%).
Смазочно-заправочные работы состоят в замене или пополнении агрегатов (узлов) автомобиля маслом, топливом, техническими жидкостями. Качество этих работ относится к числу наиболее весомых факторов, влияющих на ресурс узлов. Так, если смазку шкворня грузового автомобиля проводить не каждое ТО-1, как это требуется, а через раз, то ресурс шкворня сократится более чем на 40%. Эксплуатация двигателя с уровнем масла ниже допустимого приводит к полному падению давления в системе смазки и почти мгновенному выплавлению вкладышей коленчатого вала. Снижение уровня тормозной жидкости приводит к попаданию воздуха в тормозную систему и ее отказу. Основным технологическим документом, определяющим содержание смазочных работ, является химмотологическая карта, в которой указывают места и число точек смазки, периодичность смазки, марку масел, их расход. Косвенно к заправочным работам относятся работы по подкачке шин.
Очистительно-промывочные работы являются обязательной частью заправочных работ при замене полных объемов масла или технических жидкостей. Периодическая промывка (1 раз в год) тормозной системы увеличивает долговечность резиновых уплотнительных манжет в 1,5 – 2,5 раза. При промывке вымываются продукты износа, что обеспечивает лучшие условия работы деталей. Промывка каждого узла или системы регламентирована и выполняется по индивидуальной технологии.
Аккумуляторные работы включают в себя контроль за внешним состоянием аккумуляторной батареи, ее заряженностью, проверку уровня и плотности электролита, замену сепараторов, моноблока. Замена пластин относится к капитальному ремонту, и проведение его в условиях АТП допустимо только в критических ситуациях, так как трудоемкость капитального ремонта аккумулятора почти в 10 раз выше трудоемкости изготовления нового.
Вулканизационные работы предназначены для восстановления работоспособности (вулканизации) поврежденных автомобильных камер, устранения мелких повреждений шин – проведение так называемого ремонта.
Окрасочные работы предназначены для создания на автомобиле защитно-декоративных лакокрасочных покрытий. Эти работы относятся к
194
текущему ремонту и составляют примерно 5% его объема для грузовых автомобилей и 8% для автобусов и легковых автомобилей. Защитнодекоративные покрытия состоят из нескольких слоев: шпатлевки для выравнивания неровностей металла, грунтовки для создания высокой адгезии (иногда грунт наносят также перед шпатлевкой) и окрасочного слоя, как правило, - эмали (суспензии пигмента в лаке). Декоративные свойства покрытий должны сохраняться до 3 лет в умеренном и тропическом климате, защитные – до 3 лет в тропиках и 5 в умеренном климате.
Рабочие посты и места. Операционно-технологическая карта
Рабочий пост организуют в АТП для проведения ТО и ремонта. Рабочий пост представляет собой участок производственной площади, предназначенной для размещения автомобиля и включающий одно или несколько рабочих мест для проведения ТО и ремонта.
Рабочее место – зона трудовой деятельности исполнителя, оснащенная предметами и орудиями труда, а также средствами, необходимыми для выполнения конкретного производственного задания. По конструкции и технологической оснащенности рабочие посты подразделяют на группы. Целесообразность применения рабочих постов различного типа зависит от характера работ, производственной программы, технологических особенностей оборудования и от других факторов.
По технологическому назначению рабочие посты подразделяют на универсальные и специализированные. Различие между ними заключается в том, что на универсальном посту выполняют все или большинство операций данного воздействия, тога как на специализированном – только одну или несколько.
По способу установки подвижного состава посты могут быть тупиковыми и проездными. На проездной пост въезд и выезд производится только передним ходом. В зависимости от организации производства тупиковые и проездные посты можно использовать в качестве универсальных или специализированных.
По взаимному расположению посты бывают параллельными и последовательными. При этом тупиковые посты – только параллельные, а проездные – параллельные и последовательные. Расположение постов в помещении может быть различным:
тупиковых постов – параллельное без проезда, параллельное с проездом, параллельное двустороннее (прямоугольное) с проездом, косоугольное, комбинированное;
проездных постов – параллельное и последовательное.
Параллельные посты могут быть универсальными или специализированными, а последовательные - только специализированными. Содержание работ и их последовательность, инструмент и приспособление, способ выполнения и необходимое для этого время, а также специальность и квалификацию исполнителей устанавливают для каждого поста и его рабочих мест соответствующими операционно - технологическими картами.
195
Операционно-технологические карты во многом универсальны. Они используются как на стадии планирования и организации процесса (необходимы номенклатура операций и норма времени), так и непосредственно на рабочих местах (в этом случае необходимы оборудование, инструмент, технические условия и др.).
Стремление конструктора к снижению собственного веса автомобиля, несогласованное с показателями его надежности и эксплуатационной технологичности, приводит к увеличению материальных и трудовых затрат на поддержание автомобиля в работоспособном состоянии, увеличению расхода запасных частей, сокращению межремонтных пробегов, увеличению объема ремонтов за заданный срок службы.
Средняя фактическая трудоемкость работ по техническому обслуживанию и текущему ремонту современных автомобилей весьма велика.
Улучшение эксплуатационной надежности и технологичности подвижного состава, сокращение затрат на его техническое обслуживание и ремонт являются важнейшими задачами как сферы производства, так и сферы
эксплуатации |
автомобилей. |
Эксплуатационную |
технологичность |
конструкции автомобиля наиболее полно можно оценить в три этапа. |
|||
П е р в ы й |
э т а п состоит |
в предварительной по |
агрегатной оценке |
тенденций изменения эксплуатационной технологичности нового автомобиля по сравнению с прототипом. Первый этап проводится в период проектирования, доводки и государственных испытаний автомобилей. К моменту проведения государственных испытаний должен быть разработан проект заводской инструкции по уходу и эксплуатации автомобилей, который содержит: рекомендуемые виды, периодичности и перечень операций технического обслуживания, рекомендуемые виды топлива, смазочных материалов и жидкостей, а также гарантированные заводом минимальные межремонтные пробеги агрегатов. Указанные сведения используются для предварительной оценки эксплуатационной технологичности. Оценка на первом этапе является предварительной, но она имеет важнейшее значение для последующего улучшения (доработки) конструкции автомобилей.
В т о р о й |
э т а п состоит в уточнении предварительной оценки путем |
|
определения |
трудоемкости характерных операций |
техобслуживания и |
ремонта. В течение второго этапа оценку проводят главным образом в период опытной эксплуатации автомобилей в экспериментально-производственных или опытных хозяйствах.
Т р е т и й э т а п - в процессе опытной эксплуатации устанавливают или уточняют перечни или периодичности операций технического обслуживания, наработки на отказ и неисправности, что с учетом материалов по трудоемкости, полученных на втором этапе, позволяет определить удельную трудоемкость ТО и ТР и сравнить полученные данные с прототипом или данными, гарантированными заводом.
196
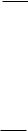
В типовой перечень операций технического обслуживания включаются большинство операций ЕО и ТО-1, которые определяют удельную трудоемкость технического обслуживания, а также часть операций ТО-2.
Для объективной оценки эксплуатационной технологичности при выполнении текущего ремонта выбраны разборочно-сборочные работы при снятии узлов, агрегатов и механизмов, т.к. эти работы являются подготовительными для последующего ремонта: полной или частичной разборки агрегатов, сварки, правки и т.д. Для оценки технологичности принят ряд показателей, разработанных НИИАТом.
Коэффициент коррекции – учитывает конструкцию и геометрические размеры объектов обслуживания, влияющих на трудоемкость выполнения соответствующих операций.
Коэффициент доступа и удобства – при оценке эксплуатационной технологичности вопросы удобства и доступа, как правило, являются наиболее сложными. Это объясняется отсутствием в технической литературе четкого определения данных понятий.
Показатели стандартизации и унификации конструкции определяются агрегатно – узловой и подетальной унификацией, структурной характеристикой крепежных деталей, унификацией инструментов и эксплуатационных материалов. Под унификацией понимается мероприятие, направленное на максимально возможное единообразие конструкции и применяемых материалов путем их взаимозаменяемости, сокращения видов, сортов и типоразмеров. Под взаимозаменяемостью понимается свойство конструкции (детали, узла, механизма, агрегата), обеспечивающие возможность их использования при обслуживании и ремонте автомобилей без дополнительной пригонки, обработки и соблюдения установленных технических условий и требований.
Агрегатно-узловая унификация характеризует степень взаимозаменяемости основных агрегатов и узлов оцениваемого образца автомобиля с одноименными агрегатами и узлами, установленными на прототипе или других выпускаемых автомобилях.
Коэффициент агрегатно-узловой унификации Кау определяется отношением унифицированных узлов и агрегатов, в том числе и заимствованных Nау, к общему их количеству, применяемому на автомобиле
N
Кау = NNау 100%.
Подетальная унификация более полно характеризует взаимозаменяемость деталей, важную при организации ремонта автомобилей и снабжения запасными частями.
Коэффициент подетальной унификации Кду определяется
Кду = N ду 100%,
N д
197

где Nду – суммарное количество унифицированных деталей, применяемых на выпускаемых автомобилях, без учета крепежных деталей;
Nд – общее количество деталей на оцениваемом автомобиле, в том числе и оригинальных деталей.
Унификация крепежных деталей и общее их количество на автомобиле оказывают непосредственное влияние на трудоемкость замены узлов и агрегатов, а также снабжение АТП крепежными деталями. Степень унификации оценивается двумя коэффициентами: коэффициентом применяемости Кпр и коэффициентом нормализации Кн.
Коэффициент применяемости выражает отношение количества крепежных деталей, применяемых на оцениваемом автомобиле Nкд11 ,к количеству одноименных деталей, применяемых на сопоставляемых автомобилях Nкд1
Кпр=
N N
11 кд 1 кд
.
Коэффициент нормализации учитывает долю нормализованных крепежных деталей (пяти групп) и определяется
Кн =
N |
с |
N |
н |
|
|
||
|
|
N |
|
100%,
где N – общее количество крепежных деталей пяти групп;
N=Nс+Nн+Nор;
Nс – количество стандартных крепежных деталей;
Nн – количество нормализованных крепежных деталей; Nор – количество оригинальных крепежных деталей.
Коэффициент типизации Кт крепежных деталей есть отношение общего количества крепежных деталей N, применяемых на автомобиле, к количеству их типоразмеров nт
Кт=
N |
|
n |
т |
|
.
Коэффициент применяемости эксплуатационных материалов Кпм.
Унификация видов и сортов масла, рекомендуемых для применения на новой модели автомобиля, определяется соотношением количества видов м сортов, рекомендуемых для оцениваемого автомобиля и прототипа,
Кпм=
М М
11 1
,
где М11 - суммарное количество рекомендуемых эксплуатационных материалов для новой модели автомобиля; М1 - суммарное количество материалов для автомбиля-прототипа.
Ремонтные работы выполняют по потребности, т.е. после появления соответствующего отказа, или неисправности, или по плану через определенный пробег, или во время работы автомобиля – предупредительный ремонт.
198
В соответствии с назначением и характером выполняемых работ ремонт подразделяют:
Текущий ремонт – ТР – проводимый на автотранспортных предприятиях (АТП) и СТО;
Капитальный ремонт – КР – проводимый на специализированных ремонтных предприятиях.
Ремонт включает в себя: контрольно-диагностические, разборочные, сборочные, регулировочные, слесарные, механические, медницкие, кузнечные, сварочные, жестяницкие, электротехнические, шиноремонтные, обойные и малярные работы. Ремонт может выполняться по отдельным агрегатам и узлам, а также по автомобилям в целом.
Текущий ремонт предназначен для устранения возникших неисправностей, а также для обеспечения установленных нормативов пробегов автомобилей и агрегатов до капитального ремонта. Характерными работами ТР являются: разборочные, сборочные, слесарные, сварочные, дефектовочные, окрасочные, замена деталей и агрегатов. При ТР агрегата допускается замена деталей, достигших предельного состояния, кроме базовых. У автомобиля при ТР могут заменяться отдельные детали, механизмы, агрегаты, требующие текущего или капитального ремонта. ТР должен обеспечивать безотказную работу отремонтированных агрегатов и узлов на пробеге, не меньшем, чем до очередного ТО – 2. В действующей системе для ТР регламентируется удельная трудоемкость, т.е. трудоемкость, отнесенная к пробегу автомобиля (чел-ч/1000 км). Кроме того, специальными нормативами регламентируются затраты на ТО (руб/1000км) с поэлементной разбивкой на рабочую силу, запасные части и материалы. Положение по ТО и ремонту и соответствующая практика свидетельствуют о целесообразности регламентации ряда работ ТР (предупредительный ремонт), например по предупреждению отказов, влияющих на безопасность движения или дающих большие убытки при их возникновении. Часть таких операций ТР малой трудоемкости может совмещаться с ТО (сопутствующий ТР). Другие выполняются в виде самостоятельных комплексов, например, по поддержанию исправного состояния кузовов, кабин, рам. Они производятся 2
– 3 раза за срок службы автомобиля и включают:
-углубленный контроль технического состояния элементов; -восстановление или замену деталей, достигших предельного состояния; -обеспечение герметичности и прочности сварных швов; -удаление продуктов коррозии и нанесение противокоррозионного
покрытия; -устранение вмятин и трещин; проведение мер, обеспечивающих
комфортные условия для водителей и пассажиров; -полную или частичную окраску кузова, кабины и рамы.
Капитальный ремонт предназначен для регламентированного восстановления потерявших работоспособность автомобилей и его агрегатов,
199
обеспечения их ресурса до следующего капитального ремонта или списания не менее 80% от норм для новых автомобилей и агрегатов.
Капитальный ремонт агрегата предусматривает его полную разборку, дефектацию, восстановление или замену деталей с последующей сборкой, регулировкой и испытанием. Агрегат направляется в капитальный ремонт в случаях, когда базовая и основные детали нуждаются в ремонте, требующем полной разборки агрегата, а также, когда работоспособность агрегата не может быть восстановлена путем проведения ТР. Основные детали обеспечивают выполнение функциональных свойств агрегатов и определяют их эксплуатационную надежность. Поэтому восстановление основных деталей при капитальном ремонте должно обеспечивать уровень качества, близкий или равный качеству новых изделий.
К базовым или корпусным деталям относят детали, составляющие основу агрегата и обеспечивающие правильное размещение, взаимное расположение и функционирование всех остальных деталей и агрегата в целом (блок цилиндров, картер коробки передач, картер моста и т.д.). Работоспособность и ремонтопригодность базовых деталей, как правило, определяют полный срок службы агрегата и условия списания.
При капитальном ремонте обеспечивается также восстановление до уровня новых изделий или близкого к нему: зазоров и натягов, взаимного расположения деталей (осей, плоскостей и т.д.), микро – и макрогеометрии рабочих поверхностей, структуры и твердости металла, форм и внешнего вида составных частей изделия. Капитальный ремонт производится преимущественно на специализированных авторемонтных предприятиях. Направление подвижного состава и агрегатов в капитальный ремонт производится на основании результатов анализа их технического состояния с применением средств диагностики и учетом пробега, а также затрат на ТО и ремонт.
Легковые автомобили и автобусы направляются в капитальный ремонт при необходимости капитального ремонта кузова. Грузовые автомобили – при необходимости капитального ремонта рамы, кабины, а также не менее трех основных агрегатов автомобиля в любом их сочетании. К основным агрегатам относятся: двигатель, коробка передач, раздаточная коробка, ведущий мост (передний, задний, средний), передняя ось и рулевой механизм.
Одной из основных тенденций в области капитального ремонта является замена ремонта полнокомплектных грузовых автомобилей на агрегатный метод ремонта, при котором агрегаты, требующие капитального (в ряде случаев и текущего) ремонта, меняются на АТП на исправные. Для капитального ремонта регламентируются ресурс агрегата и автомобиля до первого и последующих капитальных ремонтов и продолжительность ремонта (в днях).
Автомобили ремонтируют индивидуальным или агрегатным методом. При индивидуальном методе, снятые с автомобиля агрегаты после
ремонта устанавливают на тот же автомобиль, при этом, время простоя
200