
техн трансп обсл и рем уч метод компл
.pdfВосстановление деталей ремонтными размерами. Суть этого способа заключается в следующем. Если номинальный размер изнашивающейся части детали, например шейки вала, больше минимального размера по прочности детали, определенного конструктором расчетным или экспериментальным путем, то такая изношенная часть может быть отремонтирована снятием с нее некоторого минимально необходимого слоя металла в целях устранения нарушений (вследствие износа) правильной геометрической формы. После такой операции изношенная часть детали будет иметь правильную геометрическую форму и она пригодна для дальнейшей работы.
Следовательно, ремонтным размером называется такой размер, который будет иметь износившаяся часть детали после снятия с нее механической обработкой слоя металла, необходимого для придания этой части детали правильной геометрической формы с учетом припуска на обработку.
Под ремонтный размер восстанавливают более сложную и дорогую деталь, а сопрягаемую заменяют новой или восстановленной деталью, имеющей такой же ремонтный размер.
Способ основан на применении механической обработки (точение, шлифование и др.) и имеет ряд преимуществ: обеспечивает взаимозаменяемость сопрягаемых деталей в пределах данного ремонтного размера, позволяет организовать массовый выпуск заменяемой детали на заводах, упрощает технологию восстановления сопрягаемой более сложной детали, снижает стоимость и сокращает время восстановления.
Величину нормализованного ремонтного размера устанавливают в зависимости от величины и характера износа поверхности, а также от припуска на механическую обработку, который должен быть минимальным.
Для повышения качества, а также упрощения и удешевления ремонта автомобилей ремонтные размеры многих базовых и основных деталей стандартизированы.
В соответствии с принятыми стандартными ремонтными размерами деталей автомобильной промышленностью крупными сериями выпускаются в качестве запасных частей к автомобилям такие детали, как поршни, поршневые кольца, поршневые пальцы, вкладыши подшипников коленчатых валов со стандартными ремонтными размерами.
Следовательно, система ремонтных размеров в целом способствует ускорению и удешевлению ремонта автомобилей. Вместе с тем этот способ не всегда может быть применен или качественно выполнен из-за неприспособленности деталей к их ремонту под ремонтные размеры. После ремонта деталь может потерять свои рабочие функции, если при ее конструировании не была учтена возможность ремонта под ее ремонтный размер.
Восстановление деталей постановкой дополнительных ремонтных деталей.
211
Сложную деталь, изношенную в местах сопряжения с другими деталями, в ряде случаев восстанавливают постановкой втулок, ввертышей, гильз, шайб или накладок на изношенные плоскости пластин. Например, при ремонте шеек распределительного вала под ремонтный размер их диаметр уменьшается по сравнению с номинальным размером. Следовательно, отверстия в блоке также должны быть уменьшены. Наиболее удобно для этого запрессовать в блок втулки и довести их отверстия до нужного размера.
Если деталь имеет большое количество поверхностей, а надо восстановить одну или две поверхности, то восстановление ведут путем удаления части детали с изношенными поверхностями и заменяют эту часть детали новой частью. Обе части соединяют сваркой, прессовкой или резьбовым соединением.
Распространенным способом является постановка ввертышей. Частым дефектом головок цилиндров является износ и смятие резьбы в отверстиях под свечи из-за того что головка изготовлена из алюминиевых сплавов.
Дополнительный материал детали подбирают в связи с условиями работы, размеры определяют расчетным путем, обеспечивая необходимую прочность.
Дополнительные детали устанавливают на основную восстанавливаемую деталь напрессовкой или запрессовкой с натягом, при помощи заклепок и др. Ремонтные интервалы для восстановления деталей под ремонтные размеры, конструктор должен назначать минимальными, исходя из статистических данных эксплуатации и авторемонтного производства по износам в зависимости от пробега агрегата.
Завышение ремонтного интервала по сравнению с минимально необходимым ведет или к сокращению общего срока службы деталей или к ненужному увеличению запаса прочности металла.
При конструировании сложных и дорогостоящих деталей следует в изнашивающихся местах предусматривать легкосъемные сменные простые по конструкции детали.
Необходимо, чтобы детали, подлежащие ремонту с применением механической обработки, имели технологические установочные базовые поверхности, неподвергающиеся изменению в процессе эксплуатации, а также повреждению при монтаже, демонтаже и транспортировании. Кроме того, эти базовые поверхности должны быть точными по отношению к поверхностям, не изнашивающимися и являющимися посадочными для других сопряженных деталей.
При восстановлении под ремонтные размеры или постановке дополнительных деталей у основной детали не должны нарушаться ее рабочие функции.
Детали агрегатов и узлов следует изготавливать из минимального количества марок сталей и других материалов. Многообразие металлов влечет за собой многообразие режимов обработки на станках, видов инструмента, охлаждающих жидкостей, увеличение номенклатуры и запасов
212
материала на складах АРЗ, что ведет к снижению производительности и увеличению себестоимости ремонта автомобилей.
Восстановление деталей обработкой давлением.
В зависимости от характера дефекта при этом способе применяются осадка, вдавливание, вытягивание, раздача, обжатие, правка и накатка.
Осадкой восстанавливают толкатели клапанов при износе цилиндрической рабочей поверхности, полуоси при износе шлицев по толщине и др. детали.
Вдавливанием восстанавливают головки клапанов при значительном износе рабочей фаски, зубчатые колеса при износе зуба по толщине. Операции производятся в штампах соответствующих форм и размера. После операции вдавливанием размеры головки клапана или зубьев шестерен доводят до минимального значения механической обработкой.
Вытяжкой восстанавливают детали, нуждающиеся в удлинении: шатуны, стержни клапанов, тяги и т.п. Удлиняют деталь в результате местного сужения.
Раздачей восстанавливают поршневые пальцы, крестовины шарниров карданной передачи, кожухи и трубы полуосей, шейки под подшипники чашек дифференциала и т.д.
Обжатием восстанавливают втулки из цветных металлов, рычаги при износе отверстий в проушинах, шлицевое отверстие рулевой сошки и др.
Накаткой восстанавливают изношенные посадочные места под подшипники качения путем местного подъема металла созданием рифленой поверхности, т.е. вытеснение металла зубцами накаточного ролика или вытеснение металла шариками.
Восстановление деталей правкой.
Существует два способа правки: статическим нагружением и наклепом. Правкой статическим нагружением в холодном состоянии восстанавливают погнутые коленчатые и распределительные валы, валы коробки передач, полуоси, шатуны, балки передней оси и др.
Правкой наклепом восстанавливают валы и стержни. При такой правке легкими ударами молотка по нерабочей поверхности верхний слой как бы вытягивается и стремится занять большую поверхность, происходит выпрямление изогнутой детали.
Восстановление деталей обработкой давлением возможно при условии, если их конструкция удовлетворяет двум основным требованиям: перемещение металла в зону с изношенной поверхностью из близкорасположенных зон не сопровождается снижением прочности или других свойств детали; необходимо, чтобы деталь была технологична с точки зрения проведения операции. Это означает, что ее внешние формы должны допускать удобную установку в штамп или другое приспособление несложной конструкции.
Особенности комплектования деталей, сборки узлов и агрегатов.
213
Особенностью комплектования в авторемонтном производстве является наличие различных по точности групп деталей, поступающих на сборку. На сборку поступают детали, признанные при дефектовке годными, однако имеющие допустимый износ; восстановленные детали; новые детали, поступающие на авторемонтный завод в качестве запасных частей.
Такое многообразие деталей при сборке по методу полной взаимозаменяемости часто приводит к появлению увеличенных зазоров и натягов в сопряжениях, не соответствующих требованиям технических условий на сборку. Объясняется это тем, что восстановленные детали и детали, признанные годными, не укладываются в допуски на геометрические параметры. Поэтому в авторемонтном производстве при сборке наряду с полной взаимозаменяемостью применяют метод регулировки с использованием неподвижных компенсаторов - регулировочных прокладок и шайб, а также метод селективного подбора деталей.
Сборка агрегатов на авторемонтном заводе аналогична сборке на автомобильном заводе, за некоторым исключением. Приработка и испытание агрегатов на авторемонтном заводе аналогична этим операциям на автомобильном заводе.
Обкатка автомобиля.
Новые и поступающие из капитального ремонта автомобили проходят обкатку, согласно инструкции заводов-изготовителей и авторемонтных предприятий. Продолжительность обкатки регламентируется инструкциями заводов-изготовителей.
В течение периода обкатки необходимо:
-не превышать величины полезной нагрузки, установленной заводомизготовителем;
-избегать движения по тяжелым дорогам;
-не начинать движения с непрогретым двигателем и не давать работать холодному двигателю с большим числом оборотов;
-не заменять в двигателе и агрегатах автомобиля масло и смазки, залитые на заводе;
-следить за температурой тормозных барабанов;
-следить за температурой ступиц колес. При значительном их нагреве ослабить их затяжку подшипников ступиц;
-следить за креплениями автомобиля и соединениями трубопроводов. Ослабленные болты – подтягивать. При обнаружении течи масла, топлива, воды и тормозной жидкости – устранить течь.
По окончании обкатки следует: подтянуть гайки головки цилиндров, выполнить ТО-2, сменить масло в картере двигателя после его промывки, снять ограничительную шайбу или ограничительный винт, установленный на рычаге дроссельной заслонки.
Контроль качества выполнения технического обслуживания.
Контроль осуществляют водитель автомобиля и ОТК АПТ. Качество технического обслуживания и технического ремонта оценивают по
214
результатам проверки автомобиля на КПП, а также непосредственно наблюдением работников ОТК за выполнением работ в зонах ТО или ремонта.
При этом работники ОТК обязаны следить за соблюдением установленных периодичностей и объемов ТО.
Водитель обязательно должен проверить автомобиль перед выездом на линию и следить за его состоянием при работе.
На каждый автомобиль, проходящий КПП заполняют Листок учета технического обслуживания и ремонта автомобиля. В листе записывают вид ТО, дату и время выполнения работ, а при текущем ремонте – содержание заявки водителя, наименование агрегата и неисправности, причину последней. Выполнение работ подтверждается подписью и штампом представителя ответственного за работу.
На каждый автомобиль на АТП заводят “Лицевую карточку автомобиля”. В нее из путевых листов нарастающим итогом записывают ежедневный пробег автомобиля, а условными знаками на основании листов учета ТО отмечают выполнения технического обслуживания (по видам, датам и пробегу), ремонта и замену агрегата.
4.3. Диагностика технического состояния автомобилей
Техническая диагностика – область знаний, охватывающая теорию, методы и средства определения состояния технического объекта.
Назначение технической диагностики заключается как в установлении отклонений от пределов параметров рабочих характеристик агрегатов и узлов, так и в анализе характера и причин возникновения этих отклонений с целью прогнозирования дальнейшей безотказной работы автомобиля.
Диагностикараздел науки по эксплуатации автомобилей, изучающий и систематизирующий неисправности их агрегатов и узлов и симптомы этих неисправностей, разрабатывающий методы и аппаратуру для их выявления, а также прогнозирования ресурса безотказной работы автомобиля. Диагностике подлежат наиболее важные функции автомобилей, к которым можно отнести развиваемую или потребляемую мощность, потребление энергии, скорость, ускорение, движение по инерции, колебания, вибрации, расход топлива и другие. Поэтому при выполнении ТО нельзя относить к диагностике такие операции, как контроль уровня масла и других жидкостей в агрегатах и системах, свободный ход педалей тормоза и сцепления, затяжка резьбовых соединений, натяжение ремня вентилятора и др. Диагностика – это более глубокое изучение и оценка состояния агрегата и узла, чем их осмотр и контроль. Основывается этот метод на использовании средств новейшей измерительной техники. Различают диагностику двух видов: совмещенную и целевую.
Совмещенная диагностика проводится на постах технического обслуживания и включается в технологический процесс. Основное
215
назначение – выявить дефекты, которые устраняются при техническом обслуживании регулировочными или ремонтными операциями.
Целевая диагностика проводится вне технического обслуживания на специальных постах и станциях диагностики и имеет целью определить состояние и ресурс безотказной работы по пробегу отдельных агрегатов, узлов и автомобиля в целом.
Техническое состояние – состояние, которое характеризуется в определенный момент времени при определенных условиях внешней среды значениями параметров, установленных технической документацией на объект.
Процесс определения состояния технического объекта называется диагностированием. Различают рабочее диагностирование, при котором на объект подаются рабочие воздействия и тестовое, при котором на объект подаются тестовые воздействия, вызывающие его реакцию. Результат диагностирования, т.е. заключение о техническом состоянии объекта,
называют диагнозом.
Диагностирование может осуществляться различными методами. Метод диагностирования – совокупность операций, действий, позволяющих дать объективное заключение о состоянии объекта. Определение состояния объекта предусматривает наличие обоснованных алгоритмов диагностирования. Алгоритмы диагностирования – совокупность предписаний, определяющих упорядоченную последовательность действий при проведении диагностирования. Алгоритм диагностирования реализуется с помощью средств технического диагностирования, под которыми понимается аппаратура, программы и ремонтно-эксплуатационная документация, позволяющие определять состояние технического объекта.
Узлы, механизмы, оборудование, системы, подлежащие (подвергаемые) диагностированию, называются объектами диагностирования (ОД). Часть ОД, которую при диагностировании нельзя разделить на более мелкие, называют элементом (структурной единицей – СЕ). Любой объект диагностирования состоит из элементов.
Состояние ОД оценивается по диагностическим признакам. Диагностическим признаком (ДП) называют параметр или характеристику, используемые при диагностировании. Параметры – физические величины: давление, диаметр, зазор, сила тока, напряжение, мощность и др. Характеристики – зависимость одной физической величины от другой, а именно: статическая характеристика, если величина не зависит от времени, частоты; динамическая характеристика. Каждому состоянию соответствует определенное значение диагностического признака.
Диагностические параметры выбираются в результате анализа диагностической модели, под которой понимается формальное описание ОД (в аналитической, табличной, графической и других формах), учитывающее изменение его состояния.
216

Состояние, при котором значения всех диагностических признаков, характеризующих способность ОД выполнять заданные функции, соответствуют установленным требованиям, называется работоспособным.
При диагностировании решаются следующие задачи:
-контроль работоспособности;
-поиск дефекта;
-прогнозирование состояния объекта.
Первая задача обязательно решается при диагностировании объектов любого назначения. Контроль работоспособности предполагает проверку соответствия значений диагностических признаков ОД требованиям технической документации.
Вторая задача может решаться в том случае, когда ОД утратил работоспособность или запас работоспособности значительно снизился. В этом случае целесообразность решения задачи определяется возможностью восстановления ОД, т.е. устранением возникшего дефекта. Устранить возникший дефект можно только, если ОД ремонтопригоден, а обслуживающий персонал имеет средства и время для его восстановления.
При решении третьей задачи изучается характер изменения диагностических параметров и на основе сформировавшихся тенденций предсказывается значение параметров в будущий момент времени.
Одним из основных элементов системы диагностирования является объект. В зависимости от характера описания процессов, протекающих во времени объекте, ОД подразделяются на непрерывные, дискретные и гибридные. Непрерывные - ОД, изменение состояния которых может быть описано непрерывно во времени. Дискретные – ОД, изменение состояния которых описываются дискретно во времени с использованием аппарата булевой алгебры. Гибридные – ОД, представляющие собой комбинацию непрерывных и дискретных устройств.
ОД можно диагностировать непрерывно или периодически. Периодическое диагностирование может выполняться с постоянным (регулярно-периодическим) или случайным (случайно-периодическим) периодом. Для диагностирования объект может переводиться в специальный режим диагностирования или диагностироваться в рабочем и дежурном режимах.
По приспособленности ОД к замене отказавших узлов и блоков для восстановления работоспособности они разделяются на восстанавливаемые и невосстанавливаемые (электрические приборы, тормозная система, рулевое управление и т.д. – восстанавливаемые; интегральные схемы, сальники, подшипники – невосстанавливаемые).
Приспособленность объекта к диагностированию оценивают показателями:
- коэффициент полноты проверок, рассчитываемый по формуле:
Кпп= nk ,
n0
217

где nk - число измеряемых диагностических параметров; n0 - общее число диагностических параметров.
- коэффициент глубины поиска дефектов
Кгп =
F R
,
где F- число однозначно различимых составных частей ОД на принятом уровне деления;
R – общее число составных частей ОД на принятом уровне деления. - среднее время подготовки к диагностированию
Тпд= Тус +Тмд, где Тус – среднее время установки и снятия устройств сопряжения (измерителя, преобразователя и др.);
Тмд – среднее время монтажно-демонтажных работ для ОД (вскрытие лючков, разъемов, снятие блоков и др.).
В зависимости от особенностей эксплуатации ОД может иметь различный уровень приспособленности к диагностированию.
Приспособленность автомобилей и их агрегатов к диагностированию обеспечивается на стадии их разработки и изготовления соблюдением требований к техническому диагностированию в части конструктивного исполнения изделий, параметров и методов диагностирования, показателей приспособленности объекта. Приспособленность может быть повышена за счет удобного и простого подключения датчиков к автомобилю, выбором наиболее эффективных методов диагностирования и контроля, обеспечением автомобиля универсальными специально предусмотренными присоединительными разъемами, штуцерами, заглушками и т.д.; введением в
конструкцию автомобиля встроенных датчиков, к выводам которых на период диагностирования можно подключать вне бортовые (внешние) средства диагностирования; комплектованием автомобилей бортовыми системами контроля (БСК), выдающими водителю в любой момент времени информацию о техническом состоянии соответствующего узла, системы или агрегата. На практике наиболее целесообразно комплексное использование всех трех способов повышения приспособленности автомобилей к диагностированию.
Для рационального взаимодействия ОД с другими элементами системы диагностирования необходимо оценить закономерности тех или иных неисправностей, установить целесообразность их выявления и устранения на стадии производства, эксплуатации или ремонта изделия. Полученные законы распределения этих вероятностей позволяют определить, какие части изделия должны быть обеспечены диагностированием в первую очередь, и какова его периодичность по наработке. Анализ физических процессов , происходящих в объекте диагностирования, позволяет выявить физическую сущность явлений, происходящих в объекте, представить себе механизм возникновения повреждений и дефектов, выявить и оценить признаки их проявления. На основе данных анализа разрабатывают блок-схемы структурно-следственных
218
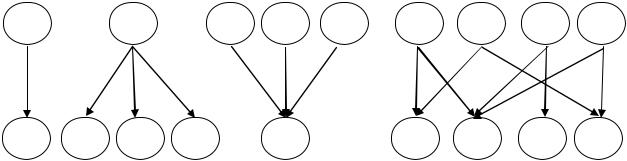
связей по цепи: диагностируемый объект (автомобиль) – агрегат – система, механизм, узел – элемент – структурный параметр – неисправность – внешний признак (симптом) – диагностический параметр. Число звеньев в цепи в каждом конкретном случае (применительно к различным системам и агрегатам) может меняться. Каждое звено определяет задаваемый уровень поиска или технологического шага, направленного на установление неисправности.
В процессе эксплуатации трущиеся сопряжения автомобилей изнашиваются, происходит разрегулировка его систем, узлов и агрегатов, т.е. изменяются значения его структурных параметров, непосредственно характеризующих исправность объекта диагностирования. К ним относя зазоры в сопряжении, величину износа поверхностей детали и другие параметры, измерение которых связано с необходимостью проведения разборочных работ. Это повышает трудоемкость контроля и существенно снижает (иногда на 5 – 10%) ресурс контролируемого агрегата. Последнее объясняется появлением дополнительного цикла приработки поверхностей контролируемого сопряжения.
Изменение структурных параметров сопровождается изменениями параметров рабочих и сопутствующих выходных процессов автомобиля, которые могут наблюдаться и измеряться извне без разборки (или с частичной разборкой) контролируемого агрегата. Например, из-за износа сопряжений цилиндропоршневой группы двигателя внутреннего сгорания снижается компрессия в цилиндрах и как результат – эффективная мощность на коленчатом валу двигателя падает или в результате износа сопряжений коренных и шатунных подшипников коленчатого вала увеличиваются утечки масла из системы смазки двигателя и тем самым снижается давление масла в системе. Если эти функциональные параметры несут достаточную и однозначную информацию о состоянии контролируемого объекта, то они могут быть отнесены к числу диагностических параметров, косвенно характеризующих исправность объекта диагностирования. Связи между структурными и диагностическими параметрами представлены на рис. 21.
А |
Б |
|
В |
|
|
|
Г |
|
S |
S |
S1 |
S2 |
S3 |
S1 |
S2 |
S3 |
S4 |
D |
D1 D2 D3 |
D |
D1 |
D2 |
D3 D4 |
Рис. 21. Связи между структурными S и диагностическими D параметрами: А - единичная, Б - множественная, В - неопределенная, Г - комбинированная.
219
Единичная связь (А) характеризуется с изменением структурного параметра (S) изменением только одного диагностического параметра (D). Такая связь позволяет почти безошибочно оценивать техническое состояние объекта диагностирования по проверяемому структурному параметру (зазору, натягу, герметичности и др.).
Множественные связи (Б) проявляются наличием нескольких диагностических признаков при изменении какого-либо структурного параметра. Например, увеличение зазоров в подшипниках коленчатого вала двигателя внутреннего сгорания сопровождается снижением давления в системе смазки, появлением характерных стуков при его работе и повышением концентрации компонентов веществ, входящих во вкладыши подшипников, в моторном масле. Каждая из этих связей может составить самостоятельный метод диагностирования или дополнить друг друга, повышая точность и достоверность диагноза.
Неопределенные связи (В) выражаются в изменении одного диагностического параметра (признака) с изменением ряда структурных параметров. Так, уменьшение амплитуды звукового импульса выхлопа из одного цилиндра ДВС может быть вызвано, например, разгерметизацией выпускного или впускного клапанов газораспределения, или увеличенными зазорами в цилиндро-поршневой группе, или нарушением момента впрыска топлива в цилиндр дизеля, или другими отклонениями структурных параметров ДВС, обеспечивающих протекание рабочего процесса в цилиндре двигателя.
Комбинированные связи (Г) характеризуются наличием любого сочетания вышеуказанных связей.
По объему и характеру передаваемой информации диагностические параметры классифицируют на частные, общие и взаимозависимые. Частные диагностические параметры независимо от других указывают на вполне определенную конкретную неисправность. Например, угол замкнутого состояния контактов определяет зазор в контактах прерывателя. Общие диагностические параметры характеризуют техническое состояние диагностируемого объекта в целом. Например, люфт на выходном валу коробки передач характеризует ее общее техническое состояние, но не состояние конкретной зубчатой пары. Взаимозависимые диагностические параметры оценивают неисправность только по совокупности нескольких измеренных параметров. Например, износ поршневых колец определяется давлением в цилиндре в такте сжатия, относительными утечками отработавших газов в картер двигателя, наличием «хлопков» в карбюраторе при пуске двигателя.
Естественно, что чем больше измеряемых диагностических параметров, тем шире информация о состоянии объекта, но при этом повышаются трудоемкость и стоимость диагностирования.
По содержанию передаваемой информации диагностические параметры разделяют на три группы: параметры, дающие информацию о техническом
220