
Конспект лекций Бордусов
.pdf
30
тивного элемента. При этом уменьшается производительность. RLCгенераторы используются для чистовых операций, где необходимо сохранить без изменения форму электрода – инструмента. В таких схемах применяется обратная полярность (инструментом является анод).
В LC-генераторах используются электромагнитный вибратор, управляющий перемещением электрода-инструмента. Из-за отсутствия ограничивающего резистора КПД этой схемы высок, но отличается сложность настройки. Поэтому LC схема используется, для какого либо одного режима в основном на черновых стадиях.
Общим недостатком релаксационных генераторов является сравнительно низкая производительность процесса, т.к. С ростом энергии импульса возрастает время накопления заряда и падает частота импульсов.
Ламповые генераторы позволяют повысит частоту следования импульсов до f ≥ 20 кГц, получить импульсы малой длительности.
Рис. 2.7. Схемы построения лампового генератора
К недостаткам ламповых генераторов относятся низкий КПД, необходимость применения источников питания с напряжением до несколько тысяч вольт, необходимость принудительной прокачки рабочей жидкости через разрядный промежуток, ограничение энергии импульса.
Наиболее широкое применение находят полупроводниковые генераторы импульсов. Они обладают широким диапазоном режимов обработки и частота следовании импульсов не зависит от свойств межэлектродного промежутка.
Генераторы этого типа могут быть двух видов:
1.На основе инверторов, в которых управляемые тиристоры регулируют период зарядки и разрядки конденсатора в релаксационных генераторах.
2.Широкодиапазонные генераторы импульсов.
Наиболее часто в современном оборудовании используются широкодиапазонные генератор. Они вырабатывают импульсы с частотой 1..880 кГц и выходным током 16..180 А, т. е. дают возможность работать на любых режимах электроэрозионной обработки. Кроме того, они вырабатывают импульсы такой формы, при которой износ электрода-инструмента становиться минимальным.
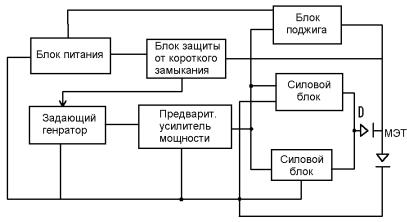
31
Структурная схема широкодиапазонного генератора импульсов представлена на рис. 2.8.
Рис. 2.8. Структурная схема широкодиапазонного генератора импульсов Тип широкодиапозонного генератора обозначается следующим образом:
ШГИ-20_440.3.
Первая цифра обозначает верхний предел средней силы тока в импульсе (в А), вторая - максимальную частоту следования импульсов (в кГц). Цифра после наклонной черты -количество выходов генератора.
2.4.2. Регуляторы подачи электрода – инструмента
Регулятора необходимы для поддержания размера межэлектродного заряда
втечении времени обработки. Этот размер составляет десятые и сотые доли миллиметра, поэтому регуляторы должны удовлетворять следующим требованиям:
1)высокое быстродействие;
2)эрогная чувствительность;
3)отсутствие люфтов в узлах с подвижными элементами;
4)малая инерционность;
5)высокая устойчивость к случайным возмещениям, вызванным наличием
вмежэлектродном промежутке электропроводных частиц, колебанием напряжением в сети;
6)малогабаритность и т.д.
Функциональная схема для электроэрозионных станков в общем случае представляет собой автоматическую систему с обратной связью по выходному сигналу.
С датчика 7 выходной величины Хвых сигнал с объекта управления 6 (МЭП) поступает на блок сравнения (БС). С БС разность выходного и заданного Хзд сигналов усиливается схемой 2, через преобразователь 3 и усилитель мощности 4 поступает на исполнительный орган 5. При ЭЭО конфигурация МЭП постоянно изменяется, что всегда дает отличную от нуля разность между заданным Хзд и выходным Хвых значениями. Под ее воздействием привод пода-

32
чи перемещает электрод-инструмент, поддерживая заданный зазор в определенной части МЭП.
Рис. 2.9. Функциональная схема регулятора межэлектродного зазора
Из-за затруднительности непосредственного измерения, зазора межэлектродного промежутка в качестве параметра регулирования используется ток разряда, падение напряжения на нем или их комбинация.
Регуляторы могут быть взвешенного типа, жесткого типа или с дифференциальным приводом.
Врегуляторах взвешенного типа сила тяжести подвесной системы, несущий электрод-инструмент, частично или полностью уравновешивается усилием электромагнита, являющимся функцией падения напряжения на разрядном промежутке.
Врегуляторах жесткого типа электродвигатель в зависимости от полученного сигнала перемещает подвижную систему вверх или вниз. Электродвигатель с электродержателем соединяться жесткой механической передачей (рейка, винтовая, эксцентриковая или роликовая передача).
Впрецизионных станках используется дифференциальный привод с двумя электродвигателями, вращение которых в нормальном режиме компенсирует друг-друга, а перемещение электрода происходит при неравенстве их частот вращения.
2.4.3. Системы рабочих перемещений электрода-инструмента
Известны три основных способа задания рабочих перемещений электродаинструмента:
1)обеспечение различных перемещений в пространстве жесткого электро- да–инструмента;
2)изменение формы гибкого электрода инструмента;
3)вибрация электрода-инструмента в направлении обработки.
Первый способ реализуется с помощью различных механизмов и систем перемещения электрода-инструмента в горизонтальной и вертикальной плоскостях. Существующие универсальные головки позволяют получать до 11 раз-

33
личных движений электрода-инструмента (поступательное, орбитальное с вращением вокруг своей оси, осциллирующие, криволинейное движение и т.д.).
Второй способ позволяет изготавливать детали имеющие отверстие с криволинейной осью. Примером устройства для его реализации может служить следующее:
Рис. 2.10. Принцип работы и устройство гибкого электрода-инструмента
Обработка отверстий 2 в детали 1 ведется нежестким электродоминструментом 4, рабочая часть 3 которого связана с гибкими поводками 5 и 6. На поводки 5 и 6 действуют усилия, соотношение которых задается из условия обеспечения заданной кривизны отверстия на определенном участке. Для изменения усилий на поводки 5 и 6 применяются программные механизмы 7 и 8 с электрогидравлическим или электромеханическим приводом.
Для сообщения электроду-инструменту возвратно-поступательных колебаний используется электромагнитный вибратор, который крепиться к исполнительному элементу регулятора межэлектродного зазора. Электромагнит с элек- тродом-инструментом представляют одно целое и вместе перемещаются в следящем режиме.
Система задания рабочих перемещений может быть отнесенная и к обрабатываемой детали. В этом случае используют вибрационные и вращающиеся столы, на которых деталь закреплена неподвижно.
2.4.4. Система очистки и подачи рабочей жидкости
Система очистки и подачи рабочей жидкости (гидравлическая система станка) предназначена для прокачки рабочей жидкости через межэлектродный промежуток.
Типовая схема гидравлической системы электроэрозионного станка представлена на рис. 2.11.
Основными элементами гидравлической системы станка являются:

34
—бак (1) для хранения и отстаивания рабочей среды;
—рабочая ванна (3) в которой протекает процесс обработки;
—насос (2) центробежного типа для обеспечения циркуляций жидкостей; фильтры (4) – для стабилизации режима обработки и уменьшения простоя
станка во время очистки рабочей жидкости;
— устройства для регулирования расхода (5) рабочей среды для изменения гидравлического режима обработки по командам адаптивного устройства управления.
Рис. 2.11. Типовая схема гидравлической системы электроэрозионного станка
Гидравлическая система работает следующим образом.
Рабочая среда из бака 1 подается насосом 2 через фильтры 4 и устройство регулирования расхода в рабочую зону. При этом возможны два варианта подачи рабочей среды: либо при открытом кране 9 через кран 10, либо непосредственно в рабочую ванну 13.
На рисунке также указаны манометры (3) для измерения давления рабочей среды, сливное отверстие 14 из рабочей ванны 13 в бак 1, ротаметр 8.
2.5. Электроды-инструменты
Параметры рабочей части ЭИ существенно влияют на точность и производительность обработки.
Основные требования, предъявляемые к электродам-интструментам:
35
—высокая электропроводность;
—эрозионная стойкость;
—механическая прочность и жесткость;
—техничность в изготовлении;
—малая стоимость;
—недефицитность материала.
Различают профилированные и непрофилированнные электродыинструменты. Форма профилированного ЭИ частично или полностью отражается в обрабатываемой заготовке. Профилированный (фасонный) электродинструмент состоит из рабочей части, поверхности которой определяют собой форму профиля обработки, и вспомогательных частей, необходимых для крепления инструмента и его базирования. Рабочую часть ЭИ изготавливают из эро- зионно-стойкого материала. Вспомогательная часть может быть выполнена из любого токопроводящего материала.
Непрофилированный электрод – это проволока различного диаметра. Выбор марки материала ЭИ зависит от типа применяемого генератора им-
пульсов, чернового или чистового режима обработки, физико–химических свойств обрабатываемого материала, геометрических параметров обрабатываемых поверхностей (видам ЭЭО).
В качестве материалов для ЭИ используют:
1)металлы и сплавы – медь (М1, М2), латунь (ЛС59, Л65), алюминиевые сплавы (Д1, АК7, АЛ3), вольфрам (ВМР), молибден (МНР) и др.;
2)композиционные материалы – Эльконайт (W-90, Cu-10), КМК-Б20 (W- 70, Cu-30) и др.;
3)углеграфитовые материалы – графит мягкозернистый прочный (МПГ-6), углерофитовые материалы МПГ-7, АРВ-2 и др.
Профиль и геометрические размеры рабочей части ЭИ представляют собой зеркальное отображение профиля детали с учетом бокового и торцевого межэлектродного зазоров, износа инструмента, а также допуска на выполняемый размер детали.
Расчет электрических размеров рабочей части профилированного ЭИ может быть выполнен аналитическим и графоаналитическим методами.
При аналитическом расчете по специальным формулам производиться определение торцевого и бокового МЭЗ по заданным разрядным параметрам: J, Uxx, f, объемный расход РЭС Q, длины вертикальной трассы удаления шлама h
ит.д. А затем по формулам определяется горизонтальный диаметральный элек- трода-инструмента длина рабочей части ЭИ. При графоаналитическом методе вычерчивается в необходимых проекциях и масштабе профиль обрабатываемой детали. Затем на чертеже откладываются значения боковых и торцевых МЭВ, которые берутся из справочных таблиц. Затем по данным чертежа определяют необходимые размеры ЭИ.
При электроэрозионном вырезании непрофилированным (проволочным) ЭИ определяются материал, диаметр, а также усилия нажатия и скорость перемотки проволочного ЭИ. Выбор значений производится по справочным таблицам.

36
Метод изготовления электрода-инструмента зависит от материала рабочей части ЭИ, размеров обрабатываемых поверхностей деталей, сложности, получаемых форм, серийности, требований к точности их изготовления.
Рис. 2.12. Основные конструктивные элементы станка для электроэрозионной обработки
Для электродов достаточно простых форм (плоских или тел вращения) используют обычные методы механической обработки: точение, фрезерование, шлифование.
При изготовлении фасонных электродов-инструментов применяют:
—металлизацию напылением, метод гальваноочистки (для получения медных ИЭ);
—методы порошковой металлургии (для электродов из композиционных материалов);
—метод вихревого копирования (для углеграфитовых электродов).
В конструкции ЭИ должны быть предусмотрены базовые поверхности для закрепления инструмента в электрододержателе станка.
Оборудование для электроэрозионной обработки может быть универсальным и специальным. Наиболее часто применяться универсальные станки для копировально-прошивочных операций.
Универсальные станки и установки для копировально-прошивочных операций имеют вертикальную компоновку, при которой деталь закрепляется на рабочем столе, снабженном подъемной ванной для диэлектрической среды, а шпиндель станка обеспечивает вертикальное прямолинейное перемещение электрода-инструмента.

37
3. Оборудование для размерной электрохимической обработки
3.1. Особенности процессов размерной ЭХО
ЭХРО, как и электроэрозионная, предназначена для обработки токопроводящих материалов независимо от их твердости и других физико-химических свойств. Однако она имеет ряд существенных отличительных особенностей:
—сравнительно высокая чистота обрабатываемой поверхности (обычно составляет 0,63…0,32 мкм);
—высокая плотность тока и как следствие этого высокая производитель-
ность;
—отсутствие заусенцев на обрабатываемых поверхностях;
—отсутствие износа ЭИ;
—вследствие наличия эффекта повторной обработки (т. к. съем материала происходит недискретно, а повсеместно) точность электрохимического формообразования не очень высока, и не превышает 0,1…0,3 мм при электрической изоляции нерабочих частей ЭИ.
3.2.Области применения электрохимической размерной обработки
1. Электрохимическое глубокое сверление отверстий диаметром 5…6 мм на глубину 200 мм и более в жаропрочных нержавеющих и других труднообрабатываемых сплавах.
Выпускаемый Троицким станкостроительным заводом станок модели 4427 позволяет образовывать отверстия диаметром 5…20 мм с точностью 0,1…0,3 мм на глубину 400 мм, со скоростью 5..10 мм/мин. Особенно эффективен электрохимический метод в случае необходимости образования треугольных, прямоугольных и др. отверстий некруглой формы.
Рис. 3.1. Схема электрохимического глубокого сверления

38
Обрабатываемая деталь 1 подключена к положительному полюсу источника тока и является анодом, а трубчатый ЭИ 2 — к отрицательному. Для повышения точности формообразования и снижения эффекта повторной обработки на ЭИ 2 образован буртик, а боковые поверхности изолированы полиэтиленовой пленкой или лаком.
2. Обработка внутренних поверхностей отверстий в деталях с различным изгибом оси (внутренних поверхностей змеевиков, элементов вакуумных систем и др.), когда к ним предъявляются повышенные эксплуатационные требования. В этих случаях применяется ЭИ нежесткой конструкции.
Рис. 3.2. Схема электрохимической обработки внутренних поверхностей
Обрабатываемое изделие 1 представляет собой криволинейную трубу с радиусом изгиба оси R и подключено к положительному полюсу источника тока. ЭИ 2 собран из отдельных токопроводящих колец попеременно с изоляционными кольцами 3, подключен к отрицательному полюсу источника тока и перемещается посредством гибкого троса. Изоляционные кольца предназначаются для:
—предотвращения коротких замыканий в процессе обработки;
—обеспечения необходимого МЭЗ (обычно 0,2…0,5 мм);
—механического удаления пассивирующей пленки с обрабатываемой поверхности.
Скорость обработки достигает 0,3…1 мм/с при шероховатости поверхности 0,6…2,0 мкм и погрешности обработки 0,1…0,2 мм.
3. Снятие заусенцев на деталях после механической обработки.
4. Изготовление печатных плат для радиоэлектронной аппаратуры. Использование электрохимического растворения участков металлической фольги вместо традиционного фотохимического способа позволяет в 2 раза повысить производительность обработки, упростить технологический процесс обработки
иулучшить условия труда, т.к. в качестве электролита используются в основном водные растворы нейтральных солей, таких как хлористый натрий, азотнокислый натрий и др. Формирование рисунка печатных плат происходит в результате копирования формы ЭИ в процессе растворения фольги до диэлектрического основания.

39
3.3. Типовая структура оборудования для ЭХО
Типовая структура оборудования для ЭХО представляет собой технический комплекс, в который входят:
—собственно станок, на котором закрепляют заготовку и инструмент;
—источник технологического тока;
—система циркуляции электролита, позволяющая прокачивать электролит при большом давлении, стабилизировать его параметры, очищать от продуктов растворения;
—система управления процессом обработки, осуществляющая взаимосвязь работы всех систем станка, контроль за процессом обработки и выбор оптимального режима обработки;
—система подачи воздуха или газа в электролит;
—система вентиляции.
Типовая схема установки для электрохимического фрезерования имеет вид, представленный на рис. 3.3.
Рис. 3.3. Типовая схема установки для электрохимической размерной обработки: 1 – электрохимический станок; 2 – обрабатываемая деталь; 3 – ЭИ; 4 – индикатор положения ЭИ; 5 – привод подачи ЭИ; 6 – вентиляция; 7 – источник технологического тока; 8 – блок измерения электрических параметров; 9 – блок защиты от короткого замыкания; 10 – система регулирования и управления электрическими и технологическими параметрами; 11 – система регулирования и стабилизации параметров и свойств электролита; 12 – блок измерения параметров и свойств электролита; 13 – смеситель раствора электролита с воздухом; 14 – фильтр; 15 – регулятор давления; 16 – насос; 17 – блок коррек-
ции состава электролита; 18 – нагреватель; 19 – теплообменник; 20 – бак для электролита; 21 – устройство очистки электролита; 22 – устройство обработки шлама.