
Пинч / Смит Р.,Клемеш Й.,Товажнянский Л.Л.,Капустенко П.А.,Ульев Л.М.-- Основы интеграции тепловых процессов (2000)
.pdf
400 |
Приложение Г |
|
|
ПРИЛОЖЕНИЕ Г
АНАЛИЗ ИНТЕГРАЦИИ ПРОЦЕССОВ И ПРЕДЛОЖЕНИЯ ПО РЕКОНСТРУКЦИИ УСТАНОВКИ КАТАЛИТИЧЕСКОГО КРЕКИНГА
Г1. Аннотация
В свете решения проблем энергосбережения и снижения количества газообразных выбросов, использование интеграции процессов для повышения эффективности энергоиспользования при проектировании новых производств и реконструкции существующих становится весьма перспективным.
Одной из важных областей применения для улучшения энергоиспользования являются проекты реконструкции теплообменных систем (ТОС), в которых величина рекуперации тепла максимизируется при сохранении неизменного срока окупаемости, насколько это возможно. В данной публикации проиллюстрирована успешная реализация метода при постадийном подходе к реконструкции ТОС.
На стадии постановки задачи в качестве первого шага была использована концепция эффективности поверхности теплообмена. Второй шаг базировался на методе сетевого пинча, разработанном Зу и Асанте [9], который был применен для прогнозирования возможных структурных модификаций, требуемых для проектирования ТОС. Выбранный с помощью метода сетевого пинча вариант проекта переходит на стадию оптимизации, где устанавливается оптимальный вариант компромисса между затратами на дополнительную поверхность теплообмена (включая переобвязку и/или переустановку) и экономией энергии. Оптимизация ТОС производилась с помощью SPRINTã (одно из программных обеспечений, разработанных UMIST по интеграции процессов).
Вся необходимая информация по дополнительной поверхности теплообмена для существующих теплообменников и по новым теплообменникам, а также по стоимости сэкономленной энергии была использована для определения срока окупаемости при внедрении соответствующего варианта модернизации. С целью определения возможного энергосбережения и реализации соответствующих технических решений было проведено изучение работы установки каталитического крекинга одного из нефтеперерабатывающих комплексов в Румынии. Были получены удовлетворительные результаты по экономии энергии: подвод тепла с горячими утилитами снижена на 49%, а отвод
Приложение Г |
401 |
|
|
тепла с холодными утилитами – на 20%. Это соответствует снижению подводимого тепла с 37,6 МВт до 19,3 МВт (экономия 18,3 МВт) и снижению отводимого тепла с 91,2 МВт до 72,3 МВт. Для внедрения рекомендован вариант, предусматривающий умеренные затраты при удовлетворительной экономии энергии, что обуславливает довольно короткий срок окупаемости, составляющий около шести месяцев.
Г2. Введение
Проектирование теплообменной системы (ТОС) является одной из важнейших стадий проектирования технологического процесса. Несмотря на то, что основы проектирования широко известны, для реконструкции ТОС приемлемы лишь некоторые методы.
Большинство методов, применимых для промышленных производств, основаны на термодинамическом анализе задач проектирования, используя принципы, в основном относящиеся к Пинчметодике [1-5]. До последнего времени эти методы требовали подробных знаний принципов и правил интеграции процессов, которые предполагали использование различных процедур, частично выполняемых вручную, что делало процесс медленным и трудоемким [6-8].
Хотя предложен ряд методов, основанных на математическом программировании, эти методы либо чрезмерно специфицируют задачу постановкой её как чисто проектной задачи, либо требуют значительного компьютерного обеспечения. В большинстве случаев они сложны в использовании и неэффективны для решения задач реконструкции промышленных ТОС.
В то же время математическое программирование и пинч-методика более сильны для задачи проектирования ТОС, однако, до последнего времени не было такого метода, который был бы интерактивным и автоматизированным для проектирования.
Для решения задач применительно к промышленным системам Зу и Асанте [9] разработали новый метод – метод сетевого пинча (МСП). Он сочетает методы математической оптимизации с четким пониманием задачи реконструкции, базирующемся на термодинамическом анализе и практической технологии, в результате чего возможно эффективно решать задачи реконструкции в промышленных масштабах.
Данная работа проводилась с целью оценки возможностей усовершенствования ТОС установки каталитического крекинга (КК) с флюидизированным катализатором, включая отделение ректификации и газоулавливающую установку.

402 |
Приложение Г |
|
|
Г3. Описание типовой установки каталитического крекинга
Установка КК является одним из наиболее важных перерабатывающих производств в нефтепереработке. Установка КК производит переработку нефтепродуктов после первичной переработки нефти под атмосферным давлением и под вакуумом (газойлей и тяжелых фракций) в высокооктановый бензин, легкие дизельные топлива и газы с высоким содержанием олефинов.
Продукционный бензин имеет высокое октановое число головной фракции и хорошие осредненные октановые характеристики. Подобные установки создавались по типовым проектам с небольшими отличиями в части особенностей исходного сырья.
Установка КК состоит из трёх отделений: реакции, ректификации и газоулавливания, как показано на рис. Г1.
Реакции крекинга проходят в вертикальном реакторе, в котором поток нефтепродукта контактирует с горячим порошкообразным катализатором. Нефтепродукт испаряется и расщепляется на более легкие продукты по мере движения вверх по реактору, увлекая за собой порошкообразный катализатор. Реакции проходят быстро, во многих случаях за несколько секунд. Одновременно с нагаром в слое катализатора образуется углеродистое соединение с низким соотношением водорода и углерода, которое откладывается на катализаторе и снижает его активность.
Установка
газоулавливания Различные
продукты
Питание+
рециркуляция Отделение реактора
Рис.Г1. Схема процесса каталитического крекинга
Использованный катализатор отделяется от полученных продуктов и поступает в регенератор, где обновляется сжиганием нагара, а затем поступает в нижнюю часть реактора, и цикл повторяется. Газы из регенератора, содержащие СО/СО2 в определенном соотношении дожигаются до СО2 в СО-котле, который вырабатывает пар высокого
Приложение Г |
403 |
|
|
давления. Выходящий из реактора поток охлаждается (Рис. Г2) и разделяется на различные продукты в главной ректификационной колонне.
Головной продукт перегонки включает бензин и легкие фракции, направляющиеся на газоулавливающую установку. Более тяжелые жидкие продукты, нафта и циклические нефтепродукты отбираются с промежуточных тарелок ректификационной колонны, а суспензия (осветленная) отделяется из нижней части.
Легкие циклические нефтепродукты, которые обрабатываются как боковой погон, разгоняются для удаления легких головных продуктов и частично рециркулируются на газоулавливающую установку для нагрева других потоков и затем поступают во вторичный абсорбер для улавливания растворимых компонентов из газа, выходящего из первичного абсорбера.
Происходит максимальное использование тепла главной ректификационной колонны. Легкие и тяжелые циклические нефтепродукты используются как теплоносители в газоулавливающей установке, а циркуляция нижнего продукта колонны используется для выработки пара.
Газоулавливающая установка состоит из абсорберов и ректификационных колонн, которые разделяют головной продукт перегонки главной ректификационной колонны на бензин и легкие нефтепродукты. Иногда на газоулавливающую установку подают олефиносодержащие газы из других производств.
Типовая восьмиколонная газоулавливающая установка приведена на рис. Г2. Газ, выходящий из верхней части главной ректификационной колонны, сжимается и вместе с нижним продуктом первичного абсорбера и верхним продуктом стриппера, которые являются также газообразными, поступает через охладитель в ресивер высокого давления (ВД-ресивер). Газ из ВД-ресивера поступает в первичный абсорбер, где контактирует с нестабилизированным бензином из сборника продукта верха главной ректификационной колонны.
Полезный эффект этого контакта заключается в разделении С3+ и С2- фракций. Отходящий газ первичного абсорбера направляется во вторичный абсорбер, где циркуляция легких циклических нефтепродуктов из главной ректификационной колонны используется для поглощения большинства оставшихся в питании вторичного абсорбера С5+ углеводородов.
Обогащенные нефтепродукты из вторичного абсорбера возвращаются в главную ректификационную колонну КК. Верхний продукт вторичного абсорбера, большей частью свободный от основных С3+ углеводородов, но содержащий Н2S направляется либо на факел горючих газов, либо в другие процессы.
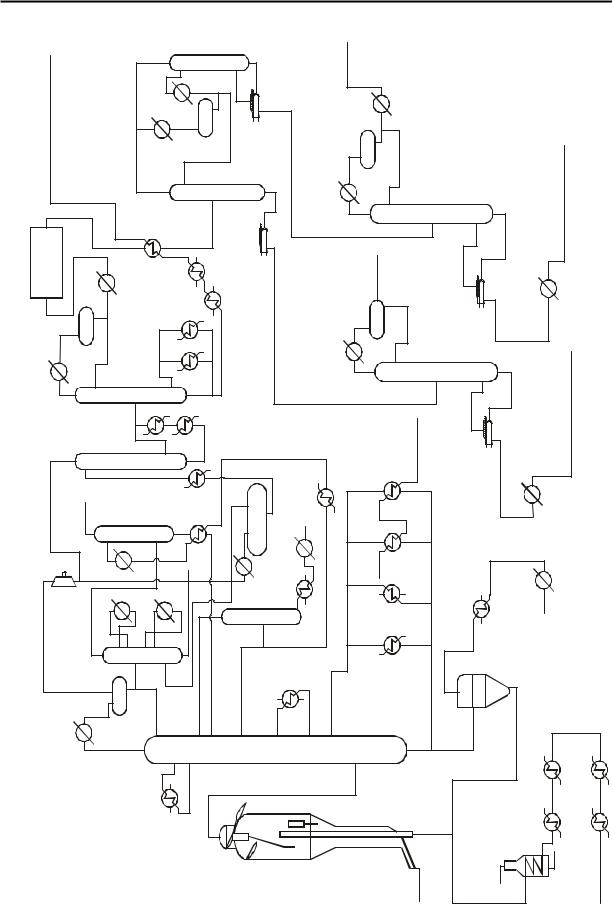
404 |
|
|
|
|
Приложение Г |
|
|
|
|
|
|
ДебутанизаторСтриппер Газолин |
Колонна |
осушки |
|
|
Пропилен насклад |
складна |
|
C4Тяжелые |
складна |
каталитичесогоустановкикрекинга |
|
Депропанизатор |
|
|
Отделитель C4фракции |
CЛегкие4 |
|
||||||
|
|
|
|
|
Отделитель пропилена |
|
|
|
Пропанскладна |
|
|
й Вторичный абсорбер |
Горючийгаз |
|
Реактор |
ВДресивер |
ЛЦН продукц. |
|
Вода Пар среднего давления |
ВреакторОтстойник |
Суспензия продукта |
Рис.2.Упрощеннаясхема |
|
Главная Первичын колонна абсорбре |
|
|
ТЦН |
|
Врегенератор |
ЦО суспензии |
втьНеф |
установку |
|||
|
|
|
|
|
|
|
|
|
Суспензия продукта |
|
|
|
|
|
|
|
|
|
|
|
|
ВЦО |
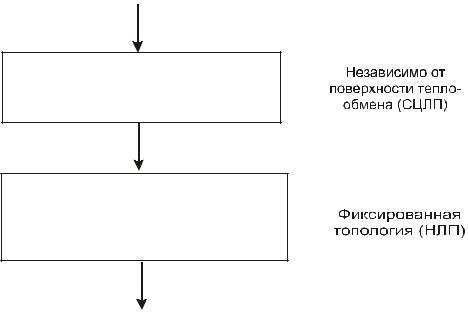
Приложение Г |
405 |
|
|
Жидкие продукты из ВД-ресивера направляются в колонну стриппера, где отгоняется большинство С2 - углеводородов, а затем возвращается в ВД-ресивер.
Нижний жидкий продукт направляется в дебутанизатор, где получается стабилизированный бензин также в качестве нижнего продукта. Верхний продукт – это олефиносодержащие С3-С4 углеводороды, которые отделяются как С4 фракция вниз. Верхний продукт содержит главным образом С3 углеводороды, а также некоторое количество воды, поэтому используется колонна осушки для разделения на азеотропную углеводородно-водяную смеси как верхний продукт и С3 фракцию как нижний продукт. Для этой колонны используется та же конденсационно-рефлюксная емкость, что и для колонны депропанизатора. Наконец, С3 фракция отделяется в отделителе пропилена, а С4 фракция – в отделителе С4.
Г4. Представление методологии
Г4.1. Реконструкция ТОС и метод сетевого пинча
Зу и Асанте [9] предложили новую методологию для проекта реконструкции существующей ТОС, которая может рассматриваться как один из основных методов реконструкции существующей ТОС. Если использовать этот метод последовательно с методом эффективности поверхности теплообмена, то возможно сформировать автоматизированное и интерактивное поколение проектирования реконструкции ТОС.
Существующий проект ТОС
СТАДИЯ ДИАГНОСТИКИ На этой стадии определяются новые модификации
СТАДИЯ ОПТИМИЗАЦИИ Компромисс между энерго-
сбережением и капитальными затратами
Проект реконструкции
Рис. Г3. Две стадии метода сетевого пинча
Приложение Г |
407 |
|
|
Г4.2. Ограничивающие сочетания теплоносителей и сетевой пинч
Ограничение рекуперации тепла зависит от минимальной разности температур между горячими и холодными потоками в ТОС. В случае реконструкции рекуперация тепла, достигаемая в существующей ТОС может быть повышена добавлением поверхности некоторых теплообменников и некоторым изменением топологии ТОС (на стадии диагностики).
Ограничивающими сочетаниями теплоносителей в ТОС можно считать сочетания горячих и холодных потоков при минимальной разности температур между ними, что приводит к максимуму рекуперации тепла (потенциал рекуперации) [9]. Сетевой пинч делит систему на сток тепла (недостаток тепла) и источник (избыток тепла), аналогично технологическому (процессному) пинчу. Разница между сетевым и технологическим пинчем заключается в том, что сетевой пинч является характеристикой как технологических потоков, так и расположения теплообменников, в то время, как технологический пинч является характеристикой только технологических потоков.
Г4.3. Стадия оптимизации
Цель этой стадии состоит в оптимизации выбранной топологии или иной структуры путем достижения компромисса между затратами на дополнительную поверхность теплообмена и эффектом от энергосбережения. С другой стороны, на стадии оптимизации выбранного проекта нет изменений в расположении и числе теплообменников ТОС. Целью оптимизации, использованной в данном случае реконструкции, является максимизация потенциала рекуперации. Кроме того, на этой стадии тепловые нагрузки теплообменников ТОС рассматриваются как переменные величины, соответственно общая величина рекуперируемого тепла также рассматривается как величина переменная.
Г5. Сбор данных
Данная работа иллюстрирует процедуру, выполненную для реконструкции ТОС типовой установки каталитического крекинга, части нефтеперерабатывающего комплекса (рис. Г2). Теплообменники используются в узле главной ректификационной колонны и в газоулавливающей установке. Установка КК была спроектирована несколько лет назад с использованием обычных принципов проектирования.
Полученные данные о работе установки были введены в
моделирующую процесс программу HYSIMTM [12], в результате чего были
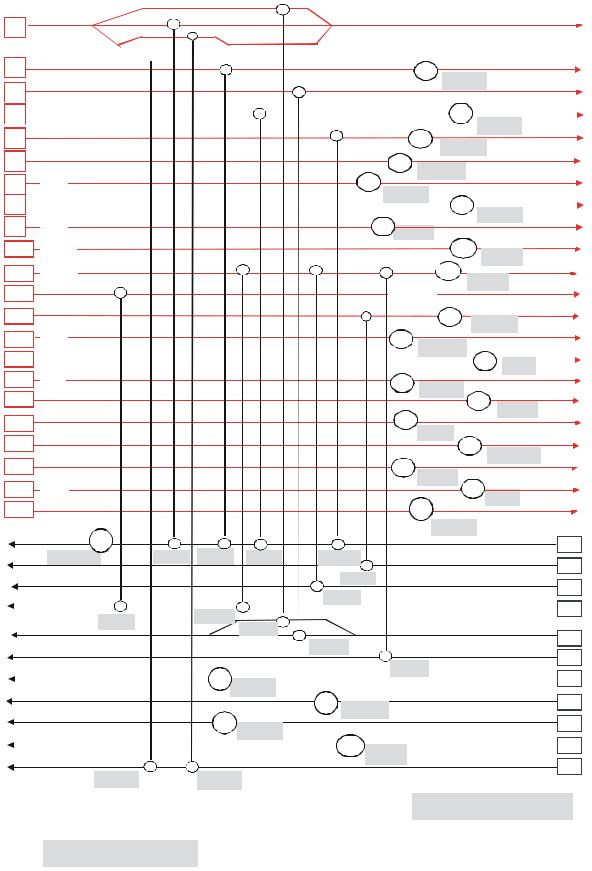