
Пинч / Смит Р.,Клемеш Й.,Товажнянский Л.Л.,Капустенко П.А.,Ульев Л.М.-- Основы интеграции тепловых процессов (2000)
.pdf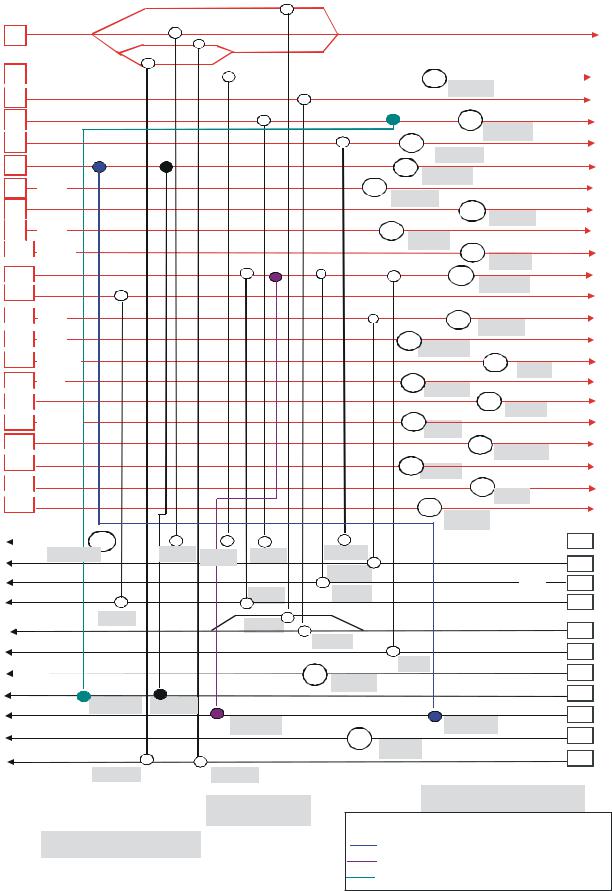
Приложение Г |
421 |
|
|
Целевой срок окупаемости 15 месяцев соответствует следующим показателям:
–требуемые капитальными вложения 3,9 млн. долл. США;
–требуемая Tmin = 10o C ;
–снижение энергопотребления (горячие утилиты) – около 23,5 МВт, т.е. приблизительно 62%.
Применение метода сетевого пинча [9] для проекта реконструкции, результаты диагностики и оптимизации показали, что возможно снижение тепла, подводимого горячими утилитами, на 49% и тепла, отводимого холодными утилитами, на 20% при установке дополнительных четырех теплообменников.
Большая часть экономии горячих утилитов происходит за счет снижения потребления пара низкого давления приблизительно на 67% по сравнению с существующим потреблением. Выработка пара среднего давления осталась неизменной. Наконец, это требует умеренных капитальных вложений в размере 1,25 млн. долл. США, в то время как экономия энергии составляет 2,492 млн. долл. США в год, при этом срок окупаемости составляет всего 6 месяцев.
Г.9. Рекомендации по реконструкции
1.Добавить четыре новых теплообменника для технологических потоков вместо использующих пар низкого давления как горячий утилит. В этом случае экономия тепла составит 49% по горячему и 20% по холодному утилиту соответственно, принимая во внимание неизменное количество потребляемого пара среднего давления.
2.Некоторые модификации (увеличение поверхности теплообмена) требуют приспособления некоторых теплообменников и охладителей на новые параметры.
3.Существующие теплообменники, использовавшие пар низкого давления, могут быть сохранены для работы во время нестабильных режимов.

422 |
Приложение Д |
|
|
ПРИЛОЖЕНИЕ Д
ИНТЕГРАЦИЯ ТЕПЛА В ПИЩЕВОЙ ПРОМЫШЛЕННОСТИ
Д1. АННОТАЦИЯ
Основные проблемы, которые необходимо решать человечеству в настоящее время и в будущем – удовлетворение потребностей в пище и энергии, а также создание удовлетворительных условий обитания со сто- роны окружающей среды. Производство пищи, которая поддерживает энергетический обмен в человеческом организме, требует ощутимого по- требления энергии от природных ресурсов – главным образом угля, нефти и природного газа. Статистические данные, полученные в настоящее вре- мя, указывают на весьма ощутимое энергопотребление в пищевой про- мышленности: на производство 1 Дж энергии в виде пищи приходятся за- траты 10 Дж энергии природных ресурсов. Постоянный рост народонасе-
ления Земли и обеспечение его питанием обуславливают ежегодный рост энергопотребления на 24-40%. С другой стороны, это приводит к резкому
ухудшению состояния окружающей среды ввиду увеличения выбросов СО2, NOx, SOx, пыли, сажи и различных промышленных выбросов. Таким образом, проблема энергосбережения в пищевой промышленности являет- ся жизненно важной. Представленная работа расширяет основные принци- пы интеграции процессов – пинч технологии. Методика интеграции про-
цессов успешно показала себя для многих энергосистем производственных процессов и обеспечила пути существенного энергосбережения.
Интеграция процессов заложила эффективную основу для определе- ния минимального потребления топлива; кроме того, были усовершенст- вованы подходы к проектированию и синтезу процессов. Разработки были успешно внедрены в различных секторах пищевой промышленности – в производствах сахара, этилового спирта, глюкозы, сухого молока, томат- ной пасты, растительного масла, консервов.
Цель большинства подобных исследований состояла в том, чтобы обеспечить снижение более, чем на 30% расхода топлива и соответственно снизить выбросы СО2, NOx, SOx, а также механических частиц (например, пыли и сажи). Главная задача – создание новой методологии проектирова-
ния наряду с применением соответствующего программного обеспечения для рационального использования энергии с целью минимизации потреб- ления топлива с экономичным и экологичным использованием выбросов, главным образом газообразных, а также накапливаемых жидких и твердых отходов.
Приложение Д |
423 |
|
|
Д2. Улучшение интеграции тепла в производстве сахара из сахарной свеклы
Д2.1. Введение
Производство сахара из сахарной свеклы является сложным процес- сом, который состоит из тесно взаимосвязанных тепловых процессов, та- ких как нагревание, многокорпусная выпарка, варка, кристаллизация и сушка, а также таких процессов, как отбелка, дефекация, сатурация, фильтрация, центрифугирование и т.д. Тепловая система сахарного завода представляет собой очень сложный комплекс, состоящий из многокорпус- ной выпарной установки, а также системы теплообменников, греющим агентом в которых является выпар из корпусов выпарной установки. По- пытки усовершенствования теплообменной системы привели к ряду реше- ний, целью которых являлось, главным образом, повышение эффективно- сти энергоиспользования и снижение энергопотребления.
Имеется ряд успешных применений методологии интеграции про- цессов для различных производств, в том числе и для сахарных заводов Западной и Центральной Европы. В данной работе анализируется эффект, который возможно получить для типичного восточноевропейского сахар- ного завода.
Основные принципы подобного анализа представлены в других ра- ботах, данная же работа является результатом расширения и углубления исследований.
Д2.2 Типичное производство сахара из сахарной свеклы в Болгарии
Объектом исследования, проведенного в данной работе, является те- пловая схема одного из сахарных заводов в Болгарии, расположенном на юге страны. Завод производит белый сахар-рафинад и кондитерские изде- лия. Сырьё для производства представляет собой сахарную свеклу, а также сахар-сырец, поступающий извне. Производительность завода составляет 1500 тонн сахарной свеклы в сутки. Основные характеристики производ- ственного процесса, представленные на рис.Д1, следующие:
−применение наклонных двухшнековых экстракторов типа DC;
−горячая очистка сока с применением преддефекации, дефека- ции и двойной сатурации;
−выпарная четырехкорпусная установка;
−схема кристаллизации для двух типов продуктов.


|
|
|
Приложение Д |
|
|
427 |
|
|
|
|
|
|
|
|
|
|
|
|
|
|
|
|
|
|
5. |
Сок сатурации |
83,8 |
88 |
91 |
251 |
НХ9 |
|
|
|
|
|
|
|
|
|
5. |
Сок сатурации |
83,8 |
91 |
94 |
251 |
H10 |
|
|
|
|
|
|
|
|
|
6. |
Сок перед выпаркой |
83,1 |
93 |
100 |
582 |
H11 |
|
|
|
|
|
|
|
|
|
6. |
Сок перед выпаркой |
83,1 |
100 |
108 |
665 |
H12 |
|
|
|
|
|
|
|
|
|
6. |
Сок перед выпаркой |
83,1 |
108 |
123 |
1247 |
НХ13, |
|
НХ14 |
||||||
|
|
|
|
|
|
|
|
|
7. |
Диффузия |
- |
- |
- |
1362 |
ДФ |
|
|
|
|
|
|
|
|
|
8. |
Упаривание |
не определялась |
75 |
75 |
7716 |
УП |
|
|
|
|
|
|
|
|
|
9. |
Воздух |
9,0 |
15 |
60 |
405 |
НХ15 |
|
|
|
|
|
|
|
|
|
10. Кипение 1й корпус |
не определялась |
128 |
128 |
16747 |
EV1 |
|
|
11. Кипение 2й корпус |
не определялась |
119 |
119 |
15024 |
EV2 |
|
|
12. Кипение 3й корпус |
не определялась |
107 |
107 |
7047 |
EV3 |
|
|
13. Кипение 4й корпус |
не определялась |
95 |
95 |
4734 |
EV4 |
Д2.3. Анализ интеграции процесса
Был выполнен энергетический и Пинч-анализ существующей тепло- вой схемы с применением математического обеспечения SPRINTTM. По- требители и источники тепла (исключая вакуум-аппараты и кристаллиза- торы, непригодные для интеграции тепла), результаты расчета энергетиче- ских балансов и существующие отборы выпар приведены в таблице Д1. Результаты расчетов для использования поверхности теплопередачи теп- лообменной системы приведены в таблице Д2. Используя SPRINTTM для существующих данных, получаем схему потоков, приведенную на рис. Д3. Составные кривые приведены на рис. Д4, а большая составная кривая – на рис. Д5.
Таблица Д2
|
Потребление |
Потребление |
Общая поверхность |
Энергоза- |
|||
Схема |
охлаждающей |
||||||
|
пара |
теплопередачи, м2 |
траты |
||||
|
|
|
воды |
|
|
|
|
|
т/ч |
кг/100 кг |
м3/ч |
Име- |
Исполь- |
/ кампанию |
|
|
|
свеклы |
|
ющаяся |
зуемая |
|
|
Существующая |
26,4 |
42,2 |
250 |
5601 |
4317 |
647670 |
|
Модифициро- |
24,0 |
38,3 |
250 |
5601 |
5091 |
591540 |
|
ванная |
|||||||
|
|
|
|
|
|
||
Изменение по |
-2,4 |
-3,9 |
0 |
0 |
774 |
56129 |
|
абс. величине |
|||||||
|
|
|
|
|
|
||
Измельчение, |
-9,0 |
-9,0 |
0 |
0 |
+18 |
-9 |
|
% |
|||||||
|
|
|
|
|
|
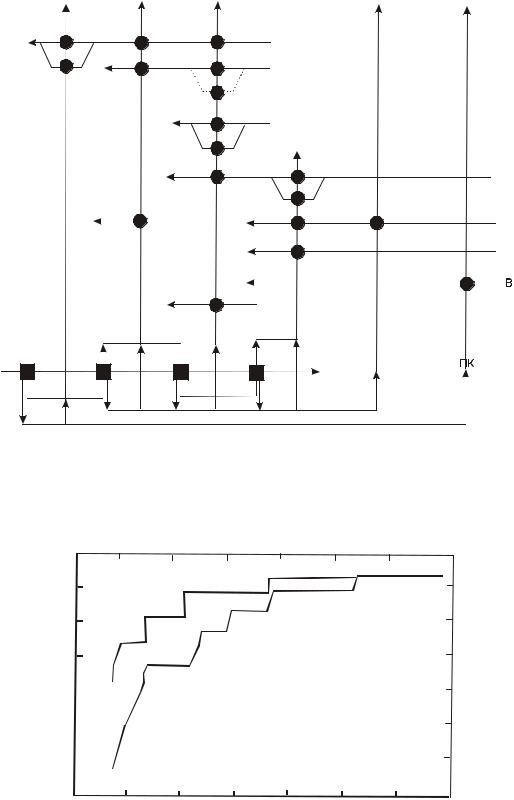

Приложение Д |
429 |
|
|
T,0C
120
100
80
60
40
20
0 |
2 |
4 |
6 |
8 10 |
12 |
14 16 18 H 103 кВт |
Рис. Д5. Большая составная кривая для существующей схемы производства са-
хара
Горизонтальные линии на составной кривой для горячих потоков и на большой составной кривой соответствуют выпару в каждом корпусе выпарной установки, а расстояние между концами отрезков на кривых оп- ределяет требуемую величину охлаждения или нагрева. Всё это показыва- ет, что проектное потребление пара составляет 26,4 тонн в час, в то время, как фактическое составляет 30-33 тонн пара в час.
Количество потребляемой холодной воды (холодного утилита) со- ставляет 250м3/ч при температуре воды 15-40оС.
Таким образом, стоимость ежегодного потребления пара в течение кампании, которая составляет 95 дней, и при стоимости тепла 22,5 EURO/Гкал составляет около 909 000 EURO.
Д2.4. Результаты и выводы
Предварительные посылки на основании результатов и полученных кривых показывают нам следующие недостатки существующей тепловой системы:
-существенное избыточное потребление горячего утилита (почти 35% выше проектной), обуславливаемое пониженной, по сравне- нию с проектной, нагрузкой, нестабильным режимом работы и