
Пинч / Смит Р.,Клемеш Й.,Товажнянский Л.Л.,Капустенко П.А.,Ульев Л.М.-- Основы интеграции тепловых процессов (2000)
.pdf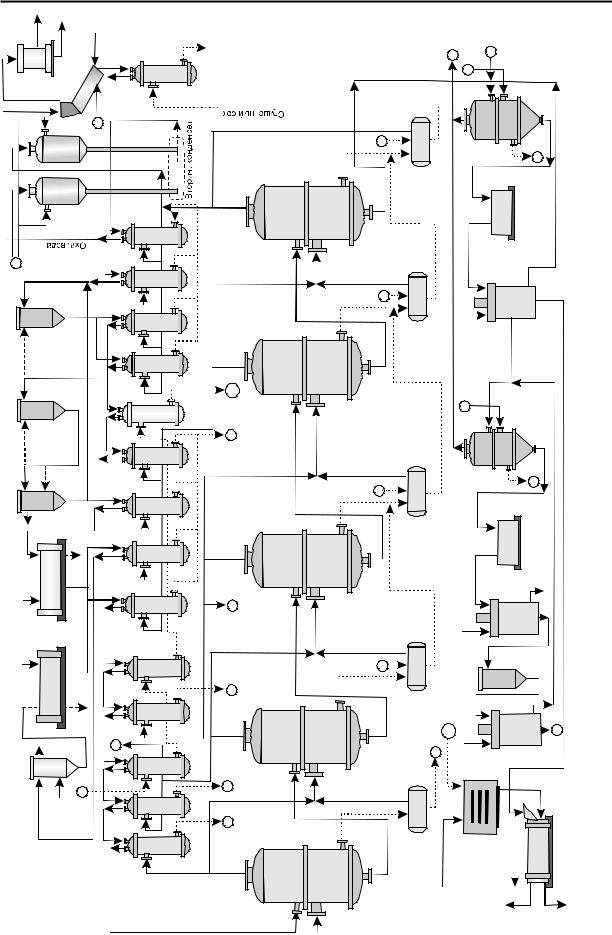
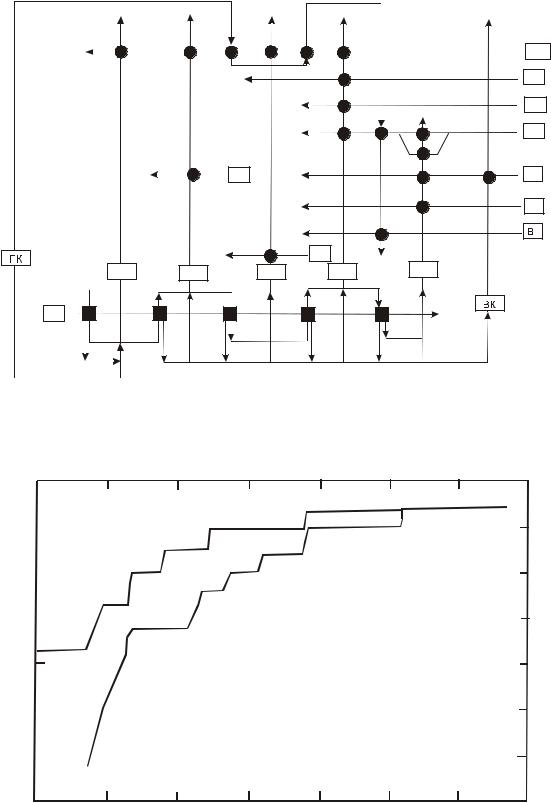
432 |
Приложение Д |
|
|
123 C |
|
|
|
|
|
|
|
640C |
0 |
|
|
0 |
0 |
0 |
0 |
0 |
|
|
|
75 C |
|
|
|
0 |
|
|
|
|
СПВ 83,1 кВт/0С |
||||||
|
114 C |
111 C |
105 C |
99 C |
96 C |
|
|
|
|
||
|
|
|
|
|
940C |
|
|
|
880C СС |
83,8 кВт/0С |
|
|
|
|
|
|
880C |
|
|
|
860C ОС |
86,4 кВт/0С |
|
|
|
|
|
|
860C |
830C |
800C |
|
700C ДС 153,1 кВт/0С |
||
|
0 |
0 |
|
|
0 |
|
|
0 |
0 |
|
|
|
70 C |
70 C |
УП |
|
62 C |
|
|
54 C |
30 C С 74,9 кВт/0С |
||
|
|
|
|
|
|
||||||
|
|
|
|
|
650C |
|
|
|
400C |
|
0 |
|
|
|
|
|
|
|
|
|
|
СВ 58,2 кВт/ С |
|
1260C |
|
|
|
|
600C |
|
|
|
150C |
|
0 |
27,3 кВт/0С |
|
|
300C |
150C |
|
|
|
|
|
|
9,0 кВт/ С |
|
|
|
ДФ |
|
|
|
|
|
|
||
|
|
|
|
|
|
|
|
|
|
|
|
ГП |
ВП1 |
ВП2 |
ВП3 |
ВП4 |
1000C |
ВП5 |
|
900C |
|
|
|
1260C |
1180C |
|
0 |
|
850C |
|
87,8 кВт/0С |
|
|||
1350C |
|
|
|
109 C |
|
|
|
|
|
|
|
СТ |
|
|
|
|
|
|
|
|
|
|
|
Рис. Д7. Модифицированная схема потоков через систему теплообменников в
производстве сахара
T,0C
120
100
80
60
40
20
0 |
1 |
2 |
3 |
4 |
5 |
6 H 104 кВт |
Рис. Д8. Составные кривые для модифицированной схемы производства сахара
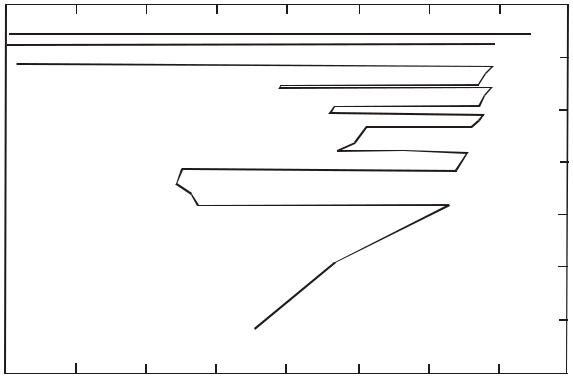

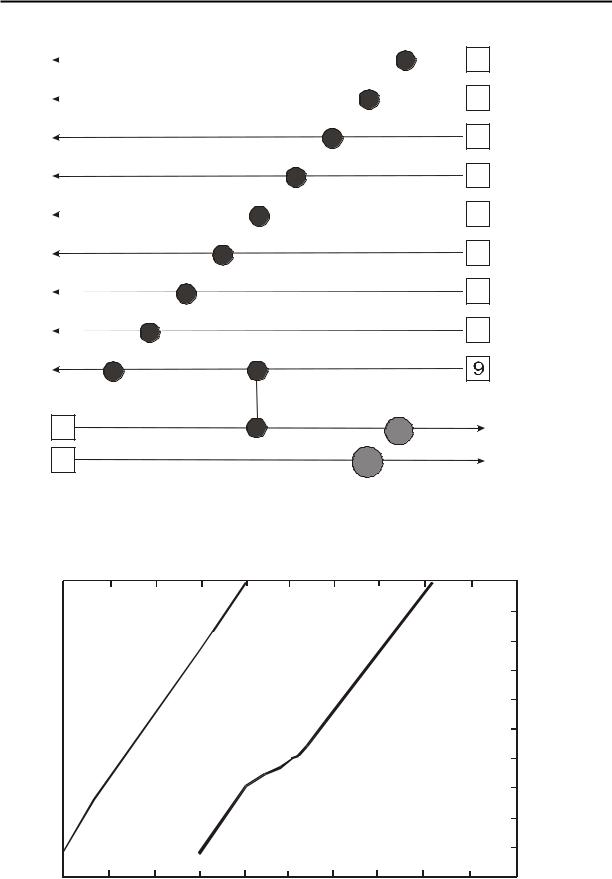

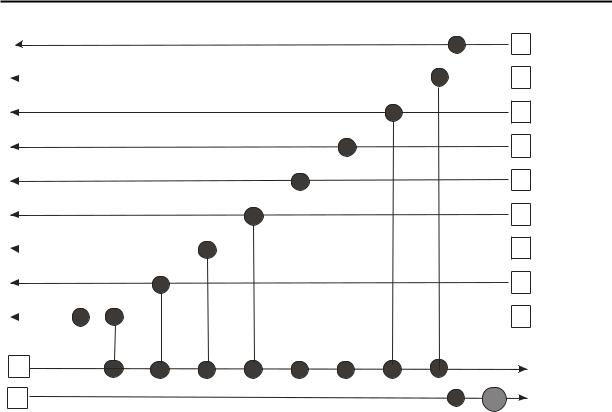
438 Приложение Д
|
500C |
|
|
|
112 кВт |
200C |
1 |
|
0 |
|||||||||
|
|
|
|
|
|
|
|
|
|
|
|
|
|
|
3,7 кВт/ С |
|||
|
700C |
|
|
|
78 кВт |
500C |
|
2 |
|
3,9 кВт/0С |
||||||||
70 |
0 |
C |
|
|
4 кВт |
|
|
|
||||||||||
|
|
|
0 |
|
|
|
|
|
||||||||||
|
|
|
20 C |
3 |
|
0,1 кВт/0С |
||||||||||||
100 |
0 |
C |
|
112 кВт |
|
|||||||||||||
|
|
0 |
|
|
|
|
|
|||||||||||
|
|
|
|
|
|
70 C |
4 |
|
4,0 кВт/0С |
|||||||||
90 |
0 |
C |
|
59 кВт |
|
20 C |
5 |
|
0,8 кВт/0С |
|||||||||
|
|
|
|
|
|
|
|
|
|
|
|
0 |
|
|
|
|
|
|
90 |
|
C |
|
|
|
|
|
|
|
|
|
|
|
|||||
0 |
|
61 кВт |
|
|
|
0 |
|
|
|
|
|
|||||||
100 |
0 |
C |
24 кВт |
|
|
75 C |
6 |
|
3,7 кВт/0С |
|||||||||
|
|
100 |
0 |
C |
|
|
|
|
|
|||||||||
|
|
|
|
|
|
|
|
|
|
|
|
|
|
|
||||
|
|
|
|
|
|
|
|
|
|
|
|
7 |
|
не опр. |
||||
|
|
|
|
|
|
|
|
|
|
|
|
|
|
|||||
90 |
0 |
C |
20 кВт |
|
|
|
0 |
|
|
|||||||||
|
|
|
|
|
|
|
|
|||||||||||
|
|
|
|
85 C |
|
|
|
|
|
|||||||||
|
1900C |
|
|
|
8 |
|
4,0 кВт/0С |
|||||||||||
|
2500C |
|
|
|
|
0 |
|
|
|
|
|
|||||||
|
|
|
|
|
|
|
|
|
|
|
85 C |
|
9 |
|
5,0 кВт/0С |
|||
|
|
|
|
|
|
|
534 кВт |
|
|
|
|
|
||||||
|
|
|
|
|
|
|
|
|
|
|
|
|
|
|
|
|
||
10 2500C |
1400C 1350C 1300C 1250C |
1120C |
820C 810C |
|
|
|
600C |
0 |
||||||||||
|
|
|
|
310C |
|
|
|
|
||||||||||
|
|
|
|
|
|
0 |
|
|
|
|
|
|
0 |
|
4,5 кВт/ С |
|||
11 60 C |
|
|
|
|
|
С120 |
|
C 3,6 кВт/0С |
||||||||||
|
|
|
|
|
|
|||||||||||||
|
|
|
|
|
|
|
|
|
|
|
|
|
|
36 кВт |
Рис. Д14. Модифицированная схема сети теплообменников для процесса рафинации
Д3.4. Результаты и выводы
Существующая система потребляет 437 кВт тепла от паров Даутерм и 489 кВт от водяного пара, что в сумме составляет 926 кВт тепла. В охла- ждающую воду сбрасывается 613 кВт, а в захоложенную воду – 146 кВт. Стоимость энергозатрат для существующей системы для 5200 часов рабо- ты в год и стоимости тепла 22,5 EURO/Гкал, охлаждающей воды 0,25 EURO/м3 и электроэнергии 0,05 EURO/кВт×ч (для холодильной машины) составляет 134000 EURO в год. Общая величина поверхности теплопере- дачи двенадцати теплообменников составляет 64 м2.
Для моделирования реконструкции существующей схемы и сниже-
ния энергопотребления было применено математическое обеспечение
SPRINTTM .
Путем улучшения интеграции тепла и снижения DТmin сформирована новая оптимизированная система. Оптимальная величина минимальной разности температур для неё находится в диапазоне от 8 до 14оС, при этом общая стоимость зависит от этой величины.
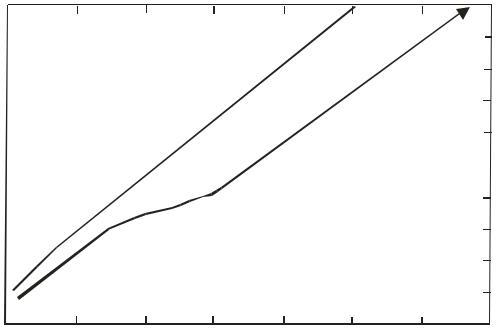
Приложение Д |
439 |
|
|
Это позволяет нам предложить изменение существующей схемы на основе базовых принципов Пинч-методики. Составные кривые горячих и
T,0C
225
200
175
150
125
100
75
50
25
0 |
2 |
4 |
6 |
8 |
10 |
12 |
H×102, кВт |
Рис. Д15. составные кривые для модифицированной схемы процесса рафинации
холодных потоков для оптимизированной системы приведены на рис. 15,
большая составная кривая – на рис. Д16, при этом Тmin=10оС. Модифици- рованная схема потоков через теплообменники приведена на рис.Д14.
Составные кривые ясно показывают потребность процесса в утили- тах. Оптимизированной системе требуются горячие утилиты на тех же температурных уровнях паров Даутерм и водяного пара, но в существенно меньших количествах – 101кВт от паров Даутерма и 190 кВт от водяного пара, всего 291 кВт. Для холодных утилитов ситуация такова, что потреб- ность в охлаждающей воде первого уровня отпала вообще, а потребность в холоде для захоложенной воды составила 36 кВт. В общей сложности мы можем отметить 77% снижения расхода паров Даутерм, 61% снижения расхода водяного пара, полное отсутствие потребности охлаждающей во- ды и 72% снижения расхода захоложенной воды. Такая экономия может
быть получена при реконструкции существующей теплообменной системы добавлением пластин в существующие теплообменные аппараты. Таким образом, срок окупаемости составляет менее одного года. Стоимость энер- гозатрат для оптимизированной схемы составляет 31900 EURO/год, соот-