
- •Учебник подготовлен в рамках Инновационной образовательной программы
- •ISBN 978-5-7262-0821-3
- •5.1. Однокомпонентные диаграммы фазового равновесия,
- •5.2.1. Диаграмма с полной взаимной растворимостью
- •5.2.4. Диаграммы с наличием трехфазного равновесия
- •5.2.5. Диаграммы с эвтектическим и эвтектоидным
- •5.2.6. Диаграммы с монотектическим и монотектоидным
- •5.2.8. Диаграммы с перитектическим и перитектоидным
- •7.1. Физико-химические основы взаимодействия
- •7.1.4. Роль термодинамики и химической кинетики
- •7.2.3. Пленки на металлах как продукты химической
- •7.2.9. Формирование защитных жаростойких пленок
- •7.2.10. Влияние внешних и внутренних факторов
- •7.3.3. Механизм электрохимической коррозии. Работа
- •7.3.4. Гетерогенность поверхности и микрогальванические
- •7.3.7. Термодинамика процессов электрохимической
- •7.4.3. Влияние примесей в жидких металлах
- •7.4.4. Основные пути снижения взаимодействия
- •конструкционных материалов с жидкометаллическими
- •7.5. Защита от коррозии на стадии проектирования и разработки
- •Предисловие к тому 2
- •Глава 4. ТЕРМОДИНАМИКА В МАТЕРИАЛОВЕДЕНИИ
- •Введение.
- •4.1. Основные понятия термодинамики
- •4.2. Метод термодинамических потенциалов
- •4.3. Прикладная термохимия
- •4.4. Фазовые равновесия
- •4.5. Термодинамика растворов
- •4.6. Физическая химия неидеальных растворов
- •4.7. Термодинамическая теория диаграмм состояния
- •Список использованной литературы
- •Глава 5. ДИАГРАММЫ ФАЗОВОГО РАВНОВЕСИЯ
- •Введение
- •5.2.2. Диаграмма с расслоением твердого раствора
- •5.2.3. Диаграмма с наличием упорядочения
- •5.2.4. Диаграммы с наличием трехфазного равновесия
- •5.2.7. Диаграмма с метатектическим равновесием
- •5.2.9. Диаграмма с синтектическим равновесием
- •5.2.10. Диаграммы с промежуточными фазами
- •5.3. Диаграмма железо – углерод
- •5.4. Анализ сложных диаграмм фазового равновесия
- •Контрольные вопросы
- •Список использованной литературы
- •6.4. Закономерности сегрегации примесей
- •Контрольные вопросы
- •Список использованной литературы
- •Глава 7. СОВМЕСТИМОСТЬ И КОРРОЗИЯ МАТЕРИАЛОВ
- •7.1.1. Совместимость материалов со средой
- •7.1.2. Коррозия. Основные понятия и определения
- •7.1.3. Коррозионные проблемы
- •7.1.5. Классификация процессов коррозии
- •7.2. Химическая коррозия металлов
- •7.2.1. Химическая газовая коррозия
- •7.2.4. Состав и структура оксидов. Эпитаксия
- •7.2.5. Толщина и защитные свойства пленок
- •7.2.7. Механизм химической газовой коррозии
- •7.2.8. Оксидные пленки на поверхности железа
- •7.2.11. Химическая коррозия в газовых теплоносителях
- •7.3. Электрохимическая коррозия
- •7.3.1. Основные признаки и причины
- •7.3.2. Электролиты
- •7.3.6. Электродные потенциалы
- •7.3.8. Диаграммы Пурбе
- •7.3.9. Кинетика электрохимических процессов коррозии
- •7.3.10. Электрохимическая защита
- •7.4. Коррозия в жидкометаллических средах
- •7.4.1. Типы процессов
- •7.4.2. Растворение твердого металла в жидком
- •7.5. Защита от коррозии на стадии проектирования
- •7.5.1. Коррозия и вопросы конструирования
- •7.5.2. Выбор материалов и их совместимость
- •7.5.3. Выбор рациональной формы элементов
- •7.5.4. Учет влияния механических нагрузок
- •7.5.5. Рациональные способы сборки конструкций
- •Контрольные вопросы
- •Список использованной литературы
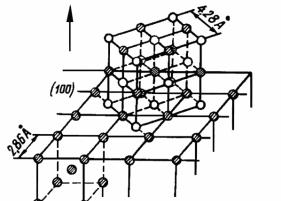
стного слоя оксида число дефектных мест в нем постепенно уменьшается, перемещение частиц замедляется, что приводит к торможению скорости окисления.
7.2.4. Состав и структура оксидов. Эпитаксия
Состав и структура образующихся оксидов определяются термодинамикой системы металл–окислитель, а также структурой подложки (поверхности). П.Д. Данков разработал принцип ориен-
тационного и размерного соответствия структур сопрягающихся фаз. В соответствии с этим принципом кристаллическая решетка оксидной фазы во избежание возникновения напряжений, приводящих к упругой деформации решеток, сопрягается с решеткой подложки такой кристаллографической плоскостью, в которой геометрическое расположение атомов наиболее подобно расположению атомов подложки (рис. 7.12). По этой же причине при окислении могут образовываться фазы, неустойчивые в обычных условиях.
Рис. 7.12. Схема взаимной ориентации α-Fe и FeO для случая, когда исходной поверхностью металла является плоскость (100). Ионы железа обозначены заштрихованными кружочками одного размера. Стрелкой указано направление роста кристаллов FeO
Ориентированное формирование слоя одного вещества на поверхности другого (подложки) носит название эпитаксия (с греч. «близкий по структуре», «продолжающий структуру»).
471
Эпитаксия наблюдается при формировании на поверхности твердого тела оксидных пленок или других осадков, полученных в результате химической реакции, кристаллизацией из растворов или газовой фазы. Новая фаза вырастает на подслое, во многих случаях наследуя его кристаллографическую структуру. Для реализации эпитаксии необходимо:
1)существование в обеих решетках одной или нескольких плоских ячеек, близких по форме и размерам;
2)достаточно малая скорость реакции, чтобы образующееся соединение имело возможность ориентироваться в соответствии с подложкой.
Интерес к эпитаксиальному росту пленок возникает вследствие того, что такие пленки наиболее прочно связаны с подложкой и являются хорошими барьерами на пути диффузии окислителя к металлу, т.е. лучшими защитниками от коррозии.
Структурно-геометрическое соответствие, сопряжение данной пары веществ при эпитаксии зависит от температуры процесса, степени пересыщения (переохлаждения) кристаллизующегося (осаждаемого) вещества в среде, совершенства подложки, чистоты
ееповерхности и других условий кристаллизации. Для разных веществ и условий существует так называемая эпитаксиальная температура, ниже которой нарастает только неориентированный слой (пленка).
Виды эпитаксии. Различают гетероэпитаксию, когда вещества подложки и нарастающего слоя различны, и гомоэпитаксию (автоэпитаксию), когда они одинаковы. Подложку обычно подвергают механической, химической или радиационной обработке для создания на ее поверхности определенного рельефа. В результате при гомоэпитаксии получают кристаллы с направленно-изменен- ным рельефом поверхности. Гомоэпитаксия в присутствии примесей позволяет получать кристаллы с легированным поверхностным слоем. При гетероэпитаксии центры кристаллизации формируются вблизи поверхностных дефектов подложки (ступеней, выходов дислокаций и др.) и ориентируются так, чтобы решетки нарастающего кристалла и подложки находились в максимальном соответ-
472
ствии с принципом П.Д. Данкова. В результате центры кристаллизации преимущественно растут либо в тангенциальном направлении, образуя сплошную пленку, либо в направлении нормали к поверхности подложки. Гетероэпитаксия осуществима для элементов, не склонных к химическому взаимодействию.
Процесс образования и ориентированного наращивания слоя за счет химического взаимодействия вещества подложки с наносимым веществом называется хемоэпитаксией. Ориентированный рост кристалла внутри объема другого называется эндоэпитаксией.
Ориентация кристалла образующегося соединения или осадка другого металла может сопровождаться изменением характера решетки, т.е. образуется псевдоморфный слой, являющийся кристаллографическим продолжением решетки кристалла подложки. С ростом толщины упругонапряженного псевдоаморфного слоя запасенная в нем энергия растет, и при толщинах более критической (для Au на Ag это 60 нм) нарастает слой с собственной структурой. Эпитаксия на аморфной подложке, на которой создан кристаллографически симметричный микрорельеф, носит название графо-
эпитаксия.
Скорость роста и толщина оксидных пленок, образованных на разных зернах подложки, сильно зависят от ориентации этих зерен, т.е. имеет место анизотропия процесса эпитаксии. Быстрее растут пленки на плоскостях с большей поверхностной энергией. Например, небольшая величина поверхностной энергии грани (111) (большая часть энергии приходится на внутреннюю связь с соседними атомами и небольшая часть – на внешнюю связь) затрудняет зародышеобразование и снижает скорость роста толщины пленки по сравнению с гранями (100) и (110), где скорость роста намного выше. Подчеркнем еще раз, что эпитаксия играет значительную роль при формировании прочных защитных оксидных пленок на металлических поверхностях.
Образующиеся оксиды металлов, так же как и сульфиды, фосфиды и другие подобные соединения, имеют преимущественно ионную связь. Оксид металла состоит из положительно заряженных ионов металла Me+ и имеющих значительно большие размеры отрицательно заряженных ионов кислорода О2–. Общая сумма всех
473
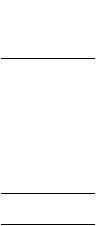
отрицательных зарядов равна общей сумме всех положительных зарядов, что обеспечивает электрическую нейтральность оксиду. Каждый оксид имеет свою кристаллографическую структуру, в которой ионы металла и кислорода принимаются существующими в двух отдельных, но взаимно проникающих одна в другую решетках, называемых подрешетками (см. п. 1.4.2).
Обычно оксиды состоят из зерен способных к рекристаллизации и росту; оксид может подвергаться пластической деформации, особенно при высоких температурах. Вдоль границ зерен в оксидах скорость диффузии выше, чем внутри зерен.
7.2.5. Толщина и защитные свойства пленок
По толщине образующиеся на поверхности металла пленки классифицируют на:
•тонкие (невидимые) толщиной от мономолекулярного слоя до
40 нм;
•средние (видимые благодаря интерференционному окрашиванию как цвета побежалости), имеющие толщину от 40 до 500 нм;
•толстые (видимые) толщиной более 500 нм.
|
|
|
Таблица 7.3 |
|
|
Толщина пленок на железе |
|
||
|
|
|
|
|
Условия получения |
Толщина пленки, нм |
Классификация |
||
|
|
|
|
|
Выдержка несколько дней в сухом |
1,5–2,0 |
Тонкие пленки |
||
воздухе при комнатной температуре |
||||
|
|
|||
Нагревание на воздухе при 400 °С |
|
|
||
|
|
|
|
|
Время нагрева, |
Цвет пленки |
|
|
|
мин |
|
|
Пленки средней |
|
1,0 |
Желтый |
46 |
||
толщины |
||||
1,5 |
Оранжевый |
52 |
||
|
||||
2,0 |
Красный |
58 |
|
|
2,5 |
Фиолетовый |
68 |
|
|
3,0 |
Синий |
72 |
Толстые |
|
Нагревание на воздухе в течение |
600 |
|||
7 сут при 900 °С |
|
пленки |
||
|
|
|||
|
|
474 |
|
Толщина образуемых пленок во многом определяется условиями окисления. В табл. 7.3 представлены данные значений толщины пленок и оксидных слоев на железе в зависимости от условий их образования. В табл. 7.4 приведены сравнительные данные по толщине оксидных пленок, полученных на некоторых металлах в сухом воздухе.
Защитные свойства оксидных пленок существенно зависят от их толщины. С ростом толщины пленок вследствие различия свойств металла и пленки снижаются ее релаксационные способности и происходит отслоение пленок.
|
Таблица 7.4 |
|
Толщина оксидных пленок на металлах |
||
|
|
|
Металл, атмосфера |
Толщина пленки, нм |
|
|
|
|
Цинк в сухом воздухе |
0,5–0,6 |
|
Медь в сухом воздухе |
1 |
|
Ртуть в сухом воздухе |
1,5–2 |
|
Нержавеющая сталь в сухом воздухе |
1–2 |
|
Нержавеющая сталь в воздухе с озоном |
2–3 |
|
Железо в сухом воздухе |
1,5–2,5 |
|
Железо во влажном воздухе с озоном |
3,5–4 |
|
Алюминий в сухом воздухе |
10–15 |
|
Жаростойкость металлов и сплавов в значительной степени зависит от свойств образующихся пленок. Чтобы оксидная пленка обладала защитными свойствами, она должна удовлетворять следующим требованиям: быть сплошной, беспористой; иметь хорошее сцепление с поверхностью металла; иметь достаточную прочность и эластичность; иметь близкий с металлом коэффициент термического расширения; быть химически инертной по отношению к окружающей среде.
Критерием сплошности такой пленки является условие Пиллинга и Бедворса, в соответствии с которым молекулярный объем хи-
мического соединения металла и окислителя (оксида), возникающего на металлической поверхности, Vок должен быть больше объема металла VМе, израсходованного на образование молекулы соединения. В противном случае образующегося соединения будет
475
недостаточно, чтобы покрыть сплошным слоем всю поверхность металла, и пленка продукта коррозии будет рыхлой, пористой.
Итак, если Vок/VMe < 1, то пленка будет рыхлой, если Vок/VMe 1, то пленка может быть сплошной. При окислении 1 грамм-атома
металла его объем VMe = AMe/ Me, где AMe – атомная масса металла;Me – плотность металла. Объем полученного оксида будет равен Vок = Mок/(n ок), где Мок – молекулярная масса оксида; n – число атомов металла в молекуле оксида; ок – плотность оксида. Отношение объемов можно рассчитать по формуле
Vок/VMe = Mок Me/(nAMe ок). (7.6)
В табл. 7.5 приведены значения отношения Vок/VMe для некоторых металлов. К металлам, не удовлетворяющим условию сплошности при окислении их кислородом, относятся Mg и все щелочные и щелочно-земельные металлы (за исключением Ве), но тонкая оксидная пленка на них может быть защитной.
|
|
|
|
|
|
Таблица 7.5 |
|
|
Отношение объемов оксида и исходного металла |
|
|
||||
|
|
|
|
|
|
|
|
Металл |
Оксид |
Vок/VMe |
Металл |
Оксид |
|
Vок/VMe |
|
Li |
Li2O |
0,57 |
Sn |
SnO2 |
|
1,33 |
|
Na |
Na2O |
0,59 |
Pb |
PbO |
|
1,15 |
|
K |
K2O |
0,48 |
Nb |
NbO |
|
1,57 |
|
Mg |
MgO |
0,79 |
Nb |
Nb2O5 |
|
2,81 |
|
Ca |
CaO |
0,63 |
Ta |
Ta2O5 |
|
2,32 |
|
Sr |
SrO |
0,66 |
Cr |
Cr2O3 |
|
2,02 |
|
Ba |
BaO |
0,73 |
Mo |
MoO2 |
|
2,18 |
|
Cu |
Cu2O |
1,67 |
Mo |
MoO3 |
|
3,45 |
|
Cu |
CuO |
1,74 |
W |
WO2 |
|
1,86 |
|
Ag |
Ag2O |
1,58 |
W |
WO3 |
|
3,36 |
|
Be |
BeO |
1,67 |
Fe |
FeO |
|
1,77 |
|
Zn |
ZnO |
1,58 |
Fe |
Fe3O4 |
|
2,09 |
|
Cd |
CdO |
1,27 |
Fe |
Fe2O3 |
|
2,14 |
|
U |
UO2 |
1,96 |
Co |
CoO |
|
1,75 |
|
U |
U3O8 |
3,12 |
Co |
Co3O4 |
|
2,00 |
|
Al |
Al2O3 |
1,31 |
Co |
Co2O3 |
|
2,42 |
|
Ti |
TiO2 |
1,76 |
Ni |
NiO |
|
1,52 |
|
Zr |
ZrO2 |
1,60 |
Pt |
PtO |
|
1,56 |
|
|
|
|
476 |
|
|
|
|
Сплошность пленки является необходимым, но недостаточным условием для проявления защитных свойств. Поскольку оксидные пленки обычно хрупки и малопластичны и имеют низкие релаксационные способности, то в реальных условиях в них могут возникнуть внутренние растягивающие или сжимающие напряжения. Растягивающие напряжения (при Vок/VMe < 1) способствуют образованию трещин, приводящих к разрушению пленки. Внутренние сжимающие напряжения (при Vок/VMe >> 1) приводят к вспучиванию, растрескиванию и отслаиванию пленки, частично или полностью нарушая ее сплошность, что значительно снижает ее защитные свойства (например, у пленок U3O8, WO3, MоO3). Считают, что достаточно хорошими защитными свойствами могут обладать лишь пленки, удовлетворяющие условию
2,5 > Vок/VMe > 1. |
(7.7) |
Могут быть и другие причины разрушения образовавшейся пленки, включая летучесть образовавшегося оксида и изменение его кристаллической структуры. Немаловажным условием формирования защитных оксидных пленок является и необходимость ориентационного соответствия образующейся пленки металлу, сущность которого сводится к требованию максимального сходства кристаллической решетки металла и образующегося оксида при минимальном смещении атомов. Защитная пленка должна иметь некоторую оптимальную толщину, чтобы в достаточной степени тормозить встречную диффузию атомов окислителя и ионов металла.
На рис. 7.13 показаны типичные разрушения оксидных пленок в процессе их роста. Пузыри под пленкой (рис. 7.13,а) образуются в тех случаях, когда прочность пленки на разрыв велика, а адгезия к поверхности металла мала. При недостаточной прочности пленки появляются пузыри с разрывом (рис. 7.13,б), что делает пленку газопроницаемой, незащитной, а под пузырем образуется новая оксидная пленка. В некоторых случаях в пленке возникают газонепроницаемые микропузыри (рис. 7.13,в), которые препятствуют диффузии ионов металла и тормозят процесс окисления, контролируемый этой диффузией.
477
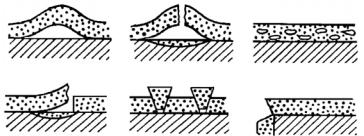
а |
б |
в |
г д е
Рис. 7.13. Типы разрушения оксидных плёнок при росте:
а – пузырь без разрыва плёнки; б – пузырь с разрывом; в – газонепроницаемые микропузыри; г – отслаивание; д – растрескивание при сдвиге;
е – растрескивание на углах
Разрушение пленки отслаиванием (рис. 7.13,г) на неровностях поверхности металла приводит к ускорению окисления металла. Растрескивание при сдвиге (рис. 7.13,д) характерно для пленок, обладающих большой адгезией к металлу и сравнительно малой прочностью.
Растрескивание на углах (рис. 7.13,е) и крутых изгибах поверхности приводит к более быстрому окислению острых выступов и часто служит началом разрушения оксидной пленки с отслаиванием.
7.2.6. Кинетика химической газовой коррозии металлов
Скорость процесса газовой коррозии обычно выражают через скорость роста толщины оксидной пленки
v = dh/dt, (7.8)
где v – скорость процесса, выражаемая в мм/год (глубинный показатель), или в г/(м2 ч) (массовый показатель); h – толщина оксидной пленки; t – время процесса. Скорость процесса зависит от ряда факторов: природы металла (состав сплава), характера и состава газовой среды и ее температуры, от защитных свойств образующихся продуктов коррозии, времени контакта металла с газовой средой и др.
Очень часто при газовой коррозии на поверхности металла возникает пористая оксидная пленка. Ее формирование проходит че-
478
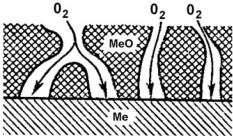
рез ряд последовательно протекающих стадий, основными из которых являются:
•транспортировка окислителя к поверхности раздела фаз;
•адсорбция окислителя на поверхности металла;
•химическое взаимодействие окислителя с металлом;
•отвод (десорбция, возгонка) продуктов коррозии.
Так как окисляющий компонент газа свободно проникает через поры в пленке к поверхности металла, то наиболее медленной (лимитирующей) стадией процесса является химическое взаимодействие кислорода с металлом (рис. 7.14). Скорость роста в этом случае будет величиной постоянной – толщина пленки пропорциональна времени окисления:
dh/dt = k, |
(7.9) |
где h – толщина пленки; t – время окисления металла; k – константа скорости химической реакции для данной концентрации окислителя.
Рис. 7.14. Схема процесса проникновения О2 через пористую оксидную плёнку на поверхности металла
Из уравнения (7.9) видно, что толщина пленки прямо пропорциональна времени окисления:
h = kt + Ah, |
(7.10) |
где Ah – постоянная интегрирования, численно равная начальной толщине пленки. При значении Ah близком к нулю (на начальной стадии окисления) уравнение (7.10) примет вид
h = kt. |
(7.11) |
Таким образом, рост пористой (незащитной) пленки, контролируемый скоростью химической реакции окисления, протекает по линейному закону. Линейный закон наблюдается при высокотемпературном окислении на воздухе щелочных и щелочно-земельных
479

металлов, а также металлов, оксиды которых возгоняются при высоких температурах (например, оксиды вольфрама, молибдена, магния).
Если на поверхности металла образуется сплошная защитная пленка, то процесс коррозии со временем будет замедляться. В этом случае на скорость коррозии будет влиять диффузия компонентов (окислителя и металла) через слой пленки. Диффузионный характер процесса проявляется тем резче, чем толще пленка и чем она качественнее. Чем выше защитные свойства пленки, тем меньше скорость ее роста, которая будет обратно пропорциональна ее толщине, т.е. dh/dt = k/h. Интегрируя данное уравнение, получим
параболическую зависимость для толщины пленки |
|
h2 = kt + const. |
(7.12) |
Из уравнения (7.12) следует, что скорость роста пленки пропорциональна t , что является признаком вклада диффузии в процесс коррозии и что скорость коррозии уменьшается во времени. Параболический закон роста оксидной пленки наблюдается при окислении вольфрама, меди, железа, никеля, кобальта, марганца, титана и других металлов.
Если рост толщины пленки происходит медленнее, чем это должно следовать из диффузионного механизма процесса окисления, то в таких случаях скорость коррозии описывается логариф-
мическим законом по уравнению |
|
h = lg(kt), |
(7.13) |
где k – некоторая константа.
Затухание процесса коррозии объясняют уплотнением пленки или появлением дефектов (например, формированием полостей в результате слияния вакансий), которые тормозят диффузию. По логарифмическому закону окисляются Si, Al, Cr, а также медь при температурах ниже 100 °С, тантал до 150 °С, цинк до 300 °С.
Рост толщины оксидных пленок многих металлов (Fe, Al, Ti, Cu, Mg, Zn, Ta, Mo, W и др.) в зависимости от внешних условий (температуры, состава газа, времени контакта) проходит по разным законам. Для описания роста толщины пленки при низких температурах и для тонких пленок применяются зависимости: логарифми-
480