
- •Учебник подготовлен в рамках Инновационной образовательной программы
- •ISBN 978-5-7262-0821-3
- •5.1. Однокомпонентные диаграммы фазового равновесия,
- •5.2.1. Диаграмма с полной взаимной растворимостью
- •5.2.4. Диаграммы с наличием трехфазного равновесия
- •5.2.5. Диаграммы с эвтектическим и эвтектоидным
- •5.2.6. Диаграммы с монотектическим и монотектоидным
- •5.2.8. Диаграммы с перитектическим и перитектоидным
- •7.1. Физико-химические основы взаимодействия
- •7.1.4. Роль термодинамики и химической кинетики
- •7.2.3. Пленки на металлах как продукты химической
- •7.2.9. Формирование защитных жаростойких пленок
- •7.2.10. Влияние внешних и внутренних факторов
- •7.3.3. Механизм электрохимической коррозии. Работа
- •7.3.4. Гетерогенность поверхности и микрогальванические
- •7.3.7. Термодинамика процессов электрохимической
- •7.4.3. Влияние примесей в жидких металлах
- •7.4.4. Основные пути снижения взаимодействия
- •конструкционных материалов с жидкометаллическими
- •7.5. Защита от коррозии на стадии проектирования и разработки
- •Предисловие к тому 2
- •Глава 4. ТЕРМОДИНАМИКА В МАТЕРИАЛОВЕДЕНИИ
- •Введение.
- •4.1. Основные понятия термодинамики
- •4.2. Метод термодинамических потенциалов
- •4.3. Прикладная термохимия
- •4.4. Фазовые равновесия
- •4.5. Термодинамика растворов
- •4.6. Физическая химия неидеальных растворов
- •4.7. Термодинамическая теория диаграмм состояния
- •Список использованной литературы
- •Глава 5. ДИАГРАММЫ ФАЗОВОГО РАВНОВЕСИЯ
- •Введение
- •5.2.2. Диаграмма с расслоением твердого раствора
- •5.2.3. Диаграмма с наличием упорядочения
- •5.2.4. Диаграммы с наличием трехфазного равновесия
- •5.2.7. Диаграмма с метатектическим равновесием
- •5.2.9. Диаграмма с синтектическим равновесием
- •5.2.10. Диаграммы с промежуточными фазами
- •5.3. Диаграмма железо – углерод
- •5.4. Анализ сложных диаграмм фазового равновесия
- •Контрольные вопросы
- •Список использованной литературы
- •6.4. Закономерности сегрегации примесей
- •Контрольные вопросы
- •Список использованной литературы
- •Глава 7. СОВМЕСТИМОСТЬ И КОРРОЗИЯ МАТЕРИАЛОВ
- •7.1.1. Совместимость материалов со средой
- •7.1.2. Коррозия. Основные понятия и определения
- •7.1.3. Коррозионные проблемы
- •7.1.5. Классификация процессов коррозии
- •7.2. Химическая коррозия металлов
- •7.2.1. Химическая газовая коррозия
- •7.2.4. Состав и структура оксидов. Эпитаксия
- •7.2.5. Толщина и защитные свойства пленок
- •7.2.7. Механизм химической газовой коррозии
- •7.2.8. Оксидные пленки на поверхности железа
- •7.2.11. Химическая коррозия в газовых теплоносителях
- •7.3. Электрохимическая коррозия
- •7.3.1. Основные признаки и причины
- •7.3.2. Электролиты
- •7.3.6. Электродные потенциалы
- •7.3.8. Диаграммы Пурбе
- •7.3.9. Кинетика электрохимических процессов коррозии
- •7.3.10. Электрохимическая защита
- •7.4. Коррозия в жидкометаллических средах
- •7.4.1. Типы процессов
- •7.4.2. Растворение твердого металла в жидком
- •7.5. Защита от коррозии на стадии проектирования
- •7.5.1. Коррозия и вопросы конструирования
- •7.5.2. Выбор материалов и их совместимость
- •7.5.3. Выбор рациональной формы элементов
- •7.5.4. Учет влияния механических нагрузок
- •7.5.5. Рациональные способы сборки конструкций
- •Контрольные вопросы
- •Список использованной литературы
вследствие туннельного эффекта или в результате термоионной эмиссии и на внешней поверхности пленки реагировать с адсорбированным кислородом. В таком случае очень быстро возникает слой хемосорбированного кислорода, и в то же время в оксиде формируется значительное электрическое поле. На поверхности раздела Ме/МеО образуются катионы, а на поверхности раздела МеО/О2 – анионы кислорода (или другого окислителя). Электрическое поле способствует миграции положительных ионов (катионов) к поверхности раздела МеО/О2. В противоположность тому, что происходит при наличии толстых слоев, где градиент концентрации играет основную роль, для тонкой пленки важен градиент потенциала, т.е. причиной переноса вещества через пленку является электрическое поле. Образовавшаяся пленка является не электрически нейтральной, а заряженной.
Теория Кабреры и Мотта позволяет определить критическую толщину оксидной пленки ho, выше которой применима теория образования толстой оксидной пленки (теория Вагнера), а ниже которой необходимо использовать теорию для тонких пленок.
В соответствии с рассмотренной теорией
dho / dt = niviE/(hoV), (7.14)
где ho – толщина оксидной пленки; vi – подвижность ионов; V – объем оксида, приходящийся на 1 ион металла; ni – концентрация межузельных ионов (для оксида – полупроводника n-типа); Е – разность потенциалов на внутренней и внешней границах пленки.
Эта теория позволяет получить для тонких оксидных пленок из полупроводника n-типа параболический закон роста пленки, из полупроводника p-типа – кубический закон, а для очень тонких пленок (т.е. при высоком градиенте потенциала, когда движение ионов преобладает в одном направлении) из полупроводника n-типа – обратнологарифмический закон роста пленки.
7.2.8.Оксидные пленки на поверхности железа
Всоответствии с диаграммой состояний Fe–O (рис. 7.18) на поверхности железа при высоких температурах (> 570 °C) может сформироваться окалина, содержащая три основных устойчивых
489
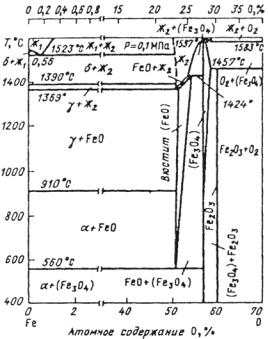
оксида: непосредственно примыкающая к поверхности закись железа FeO (вюстит), далее закись–окись Fe3O4 (магнетит) и затем внешняя часть окалины Fe2O3 (гематит). Соотношение толщин ок-
сидов FeO:Fe3O4:Fe2O3 близко к 100:10:1.
Рис. 7.18. Диаграмма состояний системы Fe–O
Вюстит FeO имеет ГЦК-решетку типа NaCl, содержащую четыре иона Fe2+ и четыре иона О2–. При высокой температуре кислород, проникая в слой оксида, растворяется в нем в количествах, превышающих стехиометрический состав, и ионизируется, отбирая электроны у части двухвалентных ионов железа Fe2+, которые, окисляясь, переходят в трехвалентные ионы Fe3+. При таком процессе в кристаллической решетке оксида образуется большое количество катионных вакансий, через которые со сравнительно высокой скоростью диффундируют катионы Fe2+ и через электронные дырки и межузельное пространство перемещаются электроны по-
490
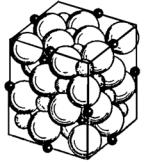
средством перехода Fe2+ = Fe3+ + e–. Все это не способствует формированию защитных свойств вюстита, значительные количества которого в окалине снижают ее защитные свойства. Из-за недостатка электронов проводимость вюстита – дырочная и относится к полупроводникам р-типа.
При температурах ниже 570 °С вюстит неустойчив и распадается на магнетит (Fe3O4) и железо по реакции
4FeO → Fe3O4 + Fe (7.15)
Магнетит Fe3O4 также имеет избыток кислорода, но меньший, чем у вюстита, поэтому в нем ниже и концентрация дефектов. В магнетите возможна диффузия как катионов, так и анионов. Fe3O4 имеет кристаллическую кубическую решетку типа шпинели (рис. 7.19).
Рис. 7.19. Структура кристаллической решетки шпинели. Большие белые шары – ионы О2-; шары меньших размеров – ионы металла
в октаэдрических узлах; маленькие черные шарики – ионы металла в тетраэдрических узлах
Элементарная ячейка содержит восемь молекул Fe3O4. В решетке на каждый ион Fe2+ приходится два иона Fe3+ при правильном кристаллографическом чередовании. В отличие от других оксидов магнетит ферромагнитен и обладает электронной проводимостью, что объясняется строгим чередованием ионов Fe3+ – Fe2+ – Fe3+ в структуре оксида, обеспечивающим легкость перехода электрона от одного катионного узла к другому. Магнетит представляет собой плотное вещество с хорошей адгезией к металлу, негигроскопичен, практически не растворим в воде и в слабощелочных растворах при комнатной температуре, но при рН = 0,3–1,3 растворяется полностью. При нагревании в окислительной среде до 220 °С Fe3O4 переходит в γ-Fe2O3 (маггемит). При этом изменяется состав
491
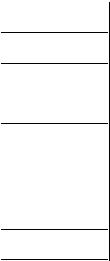
оксида без изменения кристаллографической структуры (шпинели). При нагревании до 400–500 °С образуется α-Fe2O3.
Гематит Fe2O3 является проводником n-типа. В нем диффундируют преимущественно анионы по анионным дефектам. Оксид Fe2O3 обладает ромбоэдрической структурой с минимальной концентрацией дефектов и поэтому препятствует дальнейшему окислению железа. В элементарной ячейке содержится две молекулы Fe2O3, т.е. четыре иона Fe3+ и шесть ионов О2–. Гематит существует в широком интервале температур, но выше 1100 °С происходит его частичная диссоциация.
В табл. 7.7 приводится схема процесса образования окалины при окислении стали.
Таблица 7.7
Схема процесса образования окалины
Интервал |
Стадии процесса и превращения в окали- |
температуры, °С |
не и металле |
От комнатной |
Образование пленки, состоящей |
до 200 |
из γ-Fe2O3 |
От 200 до 400 |
Возникновение наружного слоя α-Fe2O3 |
|
на внешней стороне окалины |
400–575 |
Возникновение подслоя Fe3O4 на внут- |
|
ренней стороне окалины |
575–730 |
Возникновение подслоя FeO на внутрен- |
|
ней стороне окалины |
730–780 |
Магнитное (α-Fe → β-Fe) и эвтектоидное |
|
(перлит → аустенит эвтектоидной кон- |
|
центрации) превращение в стали |
730–1150 |
Аллотропическое превращение в стали |
|
(β-Fe → γ-Fe) |
Выше 1100 |
Частичная диссоциация Fe2O3 |
|
|
Закон роста окалины Логарифмический
Логарифмический
Степенной с n > 2
То же
Параболический
То же
Сложнопараболический
Во влажном воздухе в результате электрохимической коррозии поверхность железа и стали покрывается слоем окалины, состоящей из гидроксидов Fe(OH)2, Fe(OH)3.
492
7.2.9. Формирование защитных жаростойких пленок на металлах
Применительно к условиям газовой коррозии одним из эффективных способов защиты металлов является легирование с целью получения сплавов жаростойких сплавов. В зависимости от предполагаемого действия легирующей добавки можно указать на три наиболее обоснованные теории такого легирования, которые не противоречат, а скорее дополняют друг друга.
Теории легирования для повышения жаростойкости.
1. Теория уменьшения дефектности образующегося оксида.
Согласно теории, разработанной Вагнером и Хауффе, небольшая добавка легирующего элемента окисляется с образованием ионов определенной валентности и, растворяясь в оксиде основного металла, уменьшает в его кристаллической решетке концентрацию дефектов (межузельных катионов в оксидах с избытком металла или катионных вакансий в оксидах с недостатком металла). Это приводит к упорядочению структуры и снижению скорости диффузии ионов в защитной пленке, уменьшая тем самым скорость окисления.
В соответствии с этой теорией к легирующему элементу Лэ предъявляются следующие требования:
1) иметь большее сродство к кислороду, чем у основного метал-
ла, т.е. ( Gт)ЛэО < ( Gт)МеО;
2)оксид легирующего элемента ЛэО должен растворяться в оксиде основного металла;
3)при легировании металлов, образующих оксиды с избытком
металла, валентность ионов легирующего элемента zЛэ должна удовлетворять неравенству zЛэ > z, где z – валентность ионов основного металла;
4)при легировании металлов, образующих оксиды с недостатком
металла, необходимо соблюдение неравенства zЛэ < z, а при zЛэ = z желательно соблюдение неравенства радиусов ионов, т.е. rи.Лэ < rи.
Данная теория позволяет предсказать влияние низкого легирования различными элементами на жаростойкость основного металла.
493
Если скорость окисления металла определяется не диффузией ионов, а другими процессами, или при легировании в оксидной пленке образуется новая фаза, то изложенные выше принципы жаростойкого легирования неприменимы.
2. Теория образования защитного оксида легирующего элемен-
та. Согласно теории, разработанной А.А. Смирновым, И.Д. Тома-
шовым и др., на поверхности металла (сплава) образуется защитный оксид легирующего элемента, затрудняющий диффузию реагентов и окисление основного металла. Для этого легирующий элемент должен удовлетворять следующим требованиям:
1)его оксид удовлетворяет условию сплошности: Voк/V Лэ ≥ 1;
2)он имеет большее сродство к кислороду, чем основной ме-
талл: ( Gт)ЛэО < ( Gт)МеО;
3)размер ионов легирующего элемента должен быть меньше
размера иона основного металла, т.е. rи.Лэ < rи. Это облегчает диффузию легирующего элемента к поверхности сплава, на которой образуется защитный оксид;
4)образуется оксид с высоким электросопротивлением, затрудняющим движение в нем ионов и электронов;
5)оксиды легирующих элементов имеют высокие температуры плавления и возгонки и не образуют низкоплавких эвтектик. Этообеспечивает при высоких температурах сохранение оксида в твердой фазе. Переход оксида в жидкое состояние облегчает протекание диффузионных процессов, а частичная возгонка оксида увеличивает пористость пленки, что снижает ее защитные свойства;
6)легирующий элемент и основной металл образуют твердый раствор, что обеспечивает образование сплошной пленки оксида легирующего элемента по всей поверхности сплава.
Рассмотренная теория легирования для повышения жаростойкости находится в хорошем соответствии с целым рядом практических данных по окислению сплавов и позволяет на основании некоторых свойств элементов и их оксидов качественно оценить пригодность различных элементов для среднего и высокого легирования металлов с целью повышения жаростойкости.
3. Теория образования высокозащитных двойных оксидов. Эта теория разработана В.И. Архаровым, П.Д. Данковым, И.И. Корни-
494
ловым и др. наиболее полно для сплавов на основе железа. По этой теории оптимальными являются такие легирующие элементы, которые уменьшают возможность образования малозащитной вюститной фазы и благоприятствуют образованию двойных оксидов шпинельной структуры с малым параметром решетки:
FeCr2O4, FeAl2O4, NiFe2O4, NiCr2O4 и др.
Даже при низком легировании хромом, кобальтом, кремнием и алюминием повышается температура появления в окалине вюстита, что указывает на возрастание жаростойкости стали. В табл. 7.8 указана температура, при которой замечены первые следы FeO в окалине.
Таблица 7.8
Первые следы FeO в окалине |
||
|
|
|
Состав |
Температура Т |
|
появления FeO, °С |
||
|
||
Чистое железо |
575 |
|
Fe + 1,03 %Cr |
600 |
|
Fe + 1,5 %Cr |
650 |
|
Fe + 1,0 %Co |
650 |
|
Fe + 10 %Co |
700 |
|
Fe + 1,14 %Si |
750 |
|
Fe + 0,4 %Si + 1,1 %Al |
800 |
|
Fe + 0,5 %Si + 2,2 %Al |
850 |
Установлено, что железо в пассивном состоянии, а также легированные стали имеют поверхностные слои с кристаллографической решеткой шпинельного типа, обладающие защитными свойствами. При окислении железа образуется магнетит FeO·Fe2O3, а в хромоникелевых сплавах пленка состоит из NiO·Cr2O3. Двухвалентными ионами могут быть ионы Mg, Fe, Ni, Mn, трехвалентны-
ми – ионы Al, Fe, Cr.
Малое количество дефектов у пленок со структурой типа шпинелей делает их защитными. Еще более высокими защитными свойствами обладают сложные оксиды типа FeO·Me2O3 или MeO Fe2O3. Установлено, что при длительном окислении слой оксидной пленки, примыкающий к поверхности высокохромистой стали, имеет состав FeO·Cr2O3, а внешний слой, обогащенный железом, сформирован из твердых растворов хрома в оксидах железа
495
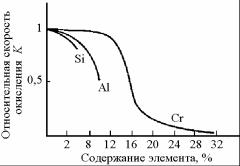
типа (Fe,Cr)2O3. При повышении температуры окисления поверхностный слой пленки значительно обогащается оксидами железа.
Легирование сталей на жаростойкость. Легирование стали элементами с меньшим, чем у железа ионным радиусом (например, Cr, Al, Si, и др.; см. табл. 7.7) уменьшает параметр решетки образовавшегося сложного оксида, замедляя диффузионную подвижность ионов кислорода и основного металла (железа), что и способствует повышению жаростойкости стали.
Основными легирующими элементами стали, повышающими ее жаростойкость, являются хром, алюминий и кремний, образующие прочные защитные оксидные пленки. На рис. 7.20 показано влияние этих элементов на относительную скорость газовой коррозии стали.
Рис. 7.20. Влияние легирующих элементов на относительную скорость газовой коррозии стали
Наиболее важным легирующим элементом, повышающим жаростойкость сталей, является хром. Хромистые стали благодаря образованию плотной и прочной защитной пленки относятся к лучшим техническим сплавам с повышенным сопротивлением окислению в газовой и пароводяной средах. Поскольку плотности оксидов Fe2O3 и Cr2O3 близки (5100–5200 и 5210 кг/м3 соответственно), обогащение защитных пленок оксидом хрома не вызывает в них дополнительных объемных изменений и напряжений, что могло бы привести к их разрушению. Достаточная жаростойкость при рабочей температуре 700 °С обеспечивается содержанием в стали 5 % Cr. Для работы при более высоких температурах (до 1100 °С) содержание хрома в стали необходимо увеличить до 15–25 %.
496
Легирование алюминием и кремнием, снижающим диффузионную подвижность ионов Fe в образовавшихся сложных оксидах FeO·SiO2 и FeO·Al2O3, значительно повышает жаростойкость сталей. Но низкая плотность оксидов Al2O3 и SiO2 (2200 и 3960 кг/м3 соответственно) по сравнению с оксидом железа может привести к значительным объемным изменениям, возникновению напряжений и разрушению защитных пленок. Кроме того, повышенная концентрация в стали Si (> 4 %) и Al (> 1,5 %) приводит к снижению ее технологических свойств – уменьшению пластичности и большей склонности к хрупкому разрушению.
Наибольшее повышение жаростойкости дает одновременное легирование стали несколькими элементами: Cr и Si, Cr и Al или Cr, Si и Al. При этом легирование хромом повышает жаростойкость в наибольшей степени, а Si и Al только усиливают действие Cr, но самостоятельного значения практически не имеют.
При высоких температурах (выше 800 °С) в воздушной атмосфере окисление и обезуглероживание стали замедляется с повышением содержания в ней углерода, что связано с интенсификацией процесса образования оксида углерода СО, образующего в окалине газовые пузыри.
Сера, фосфор, никель и марганец, присутствующие в стали, практически не влияют на высокотемпературное окисление железа, а титан, медь, кобальт и бериллий, хотя и незначительно, но повышают сопротивление окислению в газовой среде. Введение в сталь в небольших количествах Мо (до 0,7 %) и V (0,1–0,35 %) замедляет окисление из-за торможения диффузионного переноса атомов железа в стали. Но превышение указанных количеств Мо и V сильно ускоряет окисление вследствие образования их легкоплавких и ле-
тучих оксидов МоО3 (Тпл = 795 °С) и V2O5 (Тпл = 660 °С) на поверхности стали.
Повышение жаростойкости тугоплавких металлов может быть достигнуто:
1)легированием для получения сложных нелетучих оксидов
(например, Nb + Ti → TiO2·3Nb2O5);
2)легированием для приближения отношения Vок/VМе к единице
(Nb + V или Мо);
497
3)легированием элементами, оксиды которых термодинамически устойчивее основного металла (Nb + Ti или Zr);
4)легированием оксидами для получения дисперсно-упрочнен-
ных материалов типа Ме + оксид (W + ThO2; Mo + Al2O3, Cr2O3, ZrO2, TiO2 и др.).
Практическая реализация жаростойкого легирования ограничивается следующими причинами:
•концентрация легирующей добавки должна быть невысокой из-за ограниченной растворимости компонентов квазибинарных систем оксид-оксид;
•различие в сродстве компонентов сплава к кислороду и их различная диффузионная подвижность в сплаве и окалине затрудняет равномерное распределение легирующих катионов в пленке, а, следовательно, и типа проводимости оксида по глубине слоя.
7.2.10.Влияние внешних и внутренних факторов на химическую коррозию металлов
Характер и скорость процесса химической газовой коррозии металлов зависят от ряда факторов.
Внешними называют факторы, связанные с составом коррозионной среды и условиями коррозии (температура, давление, скорость движения среды и др.).
Внутренними являются факторы, связанные со структурнофазовым состоянием сплава, внутренними напряжениями в металле, характером обработки поверхности и др.
Влияние температуры. Ранее было показано, что термодинамическая возможность осуществления большинства реакций, в результате которых образуются защитные пленки, с повышением температуры падает. В то же время с ростом температуры увеличивается скорость химической реакции. Поэтому в пределах термодинамической возможности ( Gо < 0) с увеличением температуры скорость коррозии возрастает.
Характер влияния температуры на скорость окисления металлов определяется температурной зависимостью константы скорости химической реакции (при кинетическом контроле процесса окис-
498
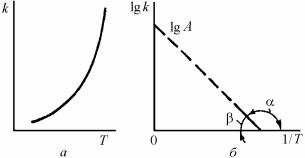
ления) или коэффициента диффузии (при диффузионном контроле процесса) и выражается одним и тем же экспоненциальным законом (уравнением Аррениуса)
k = A·exp(–Q/(RT)), (7.16)
где k – константа скорости химической реакции (или коэффициент диффузии); А – постоянная, численно равная k при экстраполяции на 1/Т = 0 (рис. 7.21); Q – энергия активации химической реакции (или диффузии); R – газовая постоянная, равная 8,32 кДж/моль; Т – абсолютная температура.
Рис. 7.21. Температурная зависимость константы скорости химической реакции (а) и коэффициента диффузии (б)
Прологарифмировав уравнение (16), получим: |
|
lg k = lg A – Q/(2,303RT). |
(7.17) |
График в координатах 1/Т – lg k выражается прямой линией, для которой Q/(2,303R) равно тангенсу угла наклона.
Если при изменении температуры изменяется контролирующий фактор (лимитирующая стадия) процесса окисления (например, кинетический контроль заменяется на диффузионный) или происходят какие-либо превращения в металле или окалине, то эти эффекты отмечаются изломом наклона прямой линии (рис. 7.22).
На рисунке каждый излом соответствует изменениям, происходящим в металле (эвтектоидное, магнитное и аллотропическое превращения) и в прилегающем к нему слое окалины (появление подслоя FeO). Верхний участок, при температуре > 800 °С, может быть связан с изменением лимитирующей стадии процесса.
499
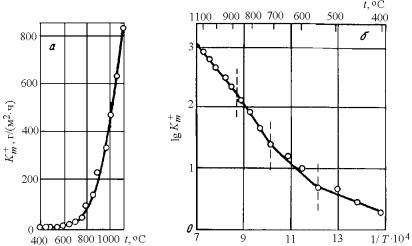
Рис. 7.22. Температурная зависимость окисления стали на воздухе:
а – скорость окисления Km близка к экспоненциальной зависимости; б – скорость окисления в координатах 1/Т – lgKm ; вертикальными штриховыми линиями отмечены изменения наклона
С изменением температуры изменяются состав и строение окалины, а также кинетический закон ее роста (см. табл. 7.7). Колебания температуры при нагреве металла, попеременные нагрев и охлаждение увеличивают скорость окисления металлов, т.к. возникающие в оксидной пленке термические напряжения инициируют образование трещин и отслоение от металла.
Влияние давления и состава газа. На скорость окисления ме-
таллов большое влияние оказывает парциальное давление окислителя в газовой среде. Если парциальное давление окислителя ниже давления диссоциации образующегося соединения, то, как уже было показано ранее, металл становится термодинамически устойчивым, и его окисление прекращается.
Если окисление металла лимитируется химической реакцией, то скорость коррозии увеличивается пропорционально корню квадратному от величины давления окислителя (кислорода).
Если скорость реакции определяется процессом диффузии в защитной пленке, то четкой зависимости от давления газа не наблюдается.
500
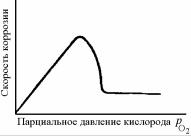
При высокотемпературном окислении меди, титана, циркония, хромистых сталей с повышением парциального давления кислорода скорость окисления вначале увеличивается, а затем, при достижении некоторого критического значения рО2, рез-
ко уменьшается, и в широком интервале давлений остается низкой (рис. 7.23).
Такое уменьшение скорости газовой коррозии при возрастании парциального давления кислорода в газовой смеси называют высокотемпературной пассивацией. Возникновение пассивного состояния металла объясняют образованием на его поверхности более совершенной пленки. Дальнейшее увеличение парциального давления кислорода приводит к нарушению пассивного состояния, и скорость коррозии возрастает, что отмечено у целого ряда легиро-
ванных сталей (08Х13, 30Х13, 12Х17).
Агрессивность других окислителей (F, Cl, SO2, H2S, CO, H2O и др.) по отношению к различным металлам при повышенных температурах неодинакова. Так, алюминий и его сплавы, хром и стали с высоким содержанием хрома устойчивы в атмосфере, содержащей кислород, но неустойчивы в атмосфере, содержащей хлор. Никель неустойчив в атмосфере диоксида серы, а медь устойчива. Коррозия углеродистых и низколегированных сталей в выхлопных газах двигателей внутреннего сгорания, в топочных и печных газах сильно зависит от соотношения СО и О2. Повышение содержания О2 увеличивает скорость газовой коррозии и, наоборот, повышение содержания СО замедляет коррозию.
Сера, как составная часть продуктов сгорания топлива в виде сероводорода (в восстановительной среде), или диоксида серы (в окислительной среде), оказывает сильное разрушающее действие на ряд сталей и сплавов, особенно содержащих никель, кобальт, хром. Образующиеся при этом легкоплавкие эвтектики сульфатов и сульфидов вызывают у стали межкристаллитную коррозию. Даже
501
небольшие концентрации диоксида серы значительно увеличивают скорость коррозии стали в воздухе. Это связано с тем, что SO2 окисляется до SO3 и при наличии в воздухе влаги образуется серная кислота, вступающая в реакцию с железом. В табл. 7.9 приведены значения скорости коррозии стали с 0,17 %С при разных составах газовой среды.
Таблица 7.9
Относительная скорость коррозии стали в зависимости от состава газовой среды при 900 °С
Состав среды |
Скорость коррозии, % |
Чистый воздух |
100 |
Чистый воздух + 2 %SO2 |
118 |
Чистый воздух + 5 %H2O |
134 |
Кислород |
200 |
Воздух + 5 %SO2 + 5 %H2O |
276 |
Впромышленных центрах атмосфера в несколько раз более коррозионно-активна, чем городская, сельская или даже морская.
Всостав агрессивных промышленных сред помимо основных составляющих часто входят жидкие и твердые вещества в виде взвесей в потоке газов, например частицы пыли. Адсорбируясь на металлической поверхности, они действуют как зародыши коррозионного разрушения, а так как многие частицы гигроскопичны (например, частицы древесного угля), то их присутствие способствует увеличению периодов увлажнения поверхности стали.
Пленки ржавчины, образующиеся на поверхности стали на открытом воздухе и в закрытых помещениях, заметно отличаются химическим составом, структурой и защитными свойствами.
Влияние состава и структуры сплава. Влияние легирования
сталей и сплавов на жаростойкость, рассмотренное ранее (см. п. 7.2.9), проявляется на формировании защитной оксидной пленки. В зависимости от состава, наличия аллотропического превращения и вида термической обработки сплав может иметь различное структурно-фазовое состояние, которое обладает различной стойкостью против окисления. В сталях наиболее жаростойкой является аустенитная фаза. Хромоникелевые стали с однофазной аустенит-
502
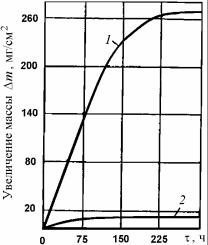
ной структурой более устойчивы против окисления на воздухе, чем стали с двухфазной аустенитно-ферритной структурой. С увеличением содержания феррита жаростойкость двухфазных сталей на воздухе ухудшается. Меньшая жаростойкость двухфазных сталей связана с большей неоднородностью образующейся защитной оксидной пленки по составу и распределению в ней внутренних напряжений, возникающих в процессе ее роста, что приводит к значительной неоднородности защитных свойств и частичному саморазрушению этой пленки.
Жаростойкость чугунов тоже определяется химическим составом и структурой, которая может быть ферритной, карбидоферритной, перлитной или аустенитной. Существенное влияние на жаростойкость чугунов оказывает форма и размеры графитовых включений. Шаровидная форма графита, а также измельчение графитовых включений присадками Si, Ni, Cu способствуют повышению жаростойкости серых чугунов (рис. 7.24).
Рис. 7.24. Интенсивность окисления хромистых чугунов при 9000С на воздухе: 1 – чугун с пластинчатым графитом; 2 – чугун с шаровидным графитом
Влияние деформации металла. Предварительная деформация металла ускоряет окисление в его начальной стадии (при температурах, не превышающих температуру возврата или рекристаллиза-
503