
- •ОГЛАВЛЕНИЕ
- •1. МЕТОДИЧЕСКИЕ УКАЗАНИЯ ПО ВЫПОЛНЕНИЮ ЛАБОРАТОРНЫХ РАБОТ
- •Введение
- •Техника безопасности
- •ОБЩИЕ СВЕДЕНИЯ
- •2.1. ЦЕЛЬ И ЗАДАЧИ КУРСОВОГО ПРОЕКТА
- •2.2. ТЕМАТИКА КУРСОВОГО ПРОЕКТА
- •2.3. СОДЕРЖАНИЕ И ОБЪЕМ КУРСОВОГО ПРОЕКТА
- •Раздел 1. ОБОСНОВАНИЕ ВЫБОРА ТИПА СОЕДИНЕНИЙ, СХЕМЫ СВАРКИ
- •Раздел 2. ОПИСАНИЕ ОСНОВНОГО МАТЕРИАЛА И ЕГО СВАРИВАЕМОСТИ
- •Раздел 3. ОБОСНОВАНИЕ ВЫБОРА ЦИКЛА СВАРКИ И РАСЧЕТ ПАРАМЕТРОВ РЕЖИМА СВАРКИ
- •Раздел 4. ВЫБОР СВАРОЧНОГО ОБОРУДОВАНИЯ
- •Раздел 8. КОНТРОЛЬ КАЧЕСТВА СВАРНЫХ СОЕДИЕНИЙ
- •Раздел 9. ТЕХНИКО-ЭКОНОМИЧЕСКАЯ ОЦЕНКА ПРОЕКТА
- •ЗАКЛЮЧЕНИЕ И ВЫВОДЫ
- •2.5. ВЫПОЛНЕНИЕ И ЗАЩИТА ПРОЕКТА
- •2.6. ВАРИАНТЫ ЗАДАНИЙ НА КУРСОВОЙ ПРОЕКТ
- •БИБЛИОГРАФИЧЕСКИЙ СПИСОК
ется избегать сложных типов соединений, связанных с предварительной обработкой кромок. При изготовлении изделий сложной формы в условиях массового производства можно использовать многоточечную, рельефную сварку.
При этом должны учитываться конкретные условия протекания процессов формирования физического контакта, удаление окисных пленок и образование металлическихсвязей втвердойилижидкойфазеприконтактнойсварке.
Раздел 2. ОПИСАНИЕ ОСНОВНОГО МАТЕРИАЛА И ЕГО СВАРИВАЕМОСТИ
Важнейшим обстоятельством при разработке курсового проекта является описание и определение свариваемости металла, из которого изготавливается изделие.
Вописании металла следует привести назначение материала. Также необходимо указать химический состав, механические, технологические и физические свойства данного материала.
Вобщем случае под свариваемостью понимают способность металлов образовывать прочное соединение без существенного ухудшения их технологических свойств в литом ядре и околошовной зоне. Прежде чем подойти к оценке свариваемости металла, целесообразно установить критерии, которыми обладает свариваемость.
Удельное сопротивление и теплопроводность в значительной степени определяют относительную жесткость режима сварки.
теплопроводность и температуропроводность в сочетании с продолжительностью сварки влияют на размер зоны термического влияния, температуру в переходном контакте, плотность сварочного тока и др.
Коэффициент линейного расширения и температуропроводность влияют на остаточные напряжения.
Технология сварки характеризуется качеством подготовки поверхности свариваемых деталей и рабочих контактов электродов, циклом сварки. Благодаря зачистке поверхностей деталей и электродов снижается температура в переходном контакте, возрастает работоспособность электродов.
Различают хорошую, удовлетворительную, ограниченную и плохую свариваемость. хорошей свариваемостью обладают металлы, которые свариваются на простейшем цикле сварки, в широком диапазоне основных параметров режима, образуя прочное соединение. При этом обеспечивается устойчивость процесса сварки с несущественными изменениями металла в зоны сварки и сохраняется высокая работоспособность электродов.
Удовлетворительную свариваемость имеют металлы, которые свариваются
вузком диапазоне основных параметров режима, образуя достаточно прочное соединение на простейшем цикле сварки. При этом получается удовлетворительное проплавление деталей, но процесс сварки теряет устойчивость, возникают выплески, в литом ядре точки и околошовной зоне наблюдаются существенные металлоструктурныеизменения. стойкостьэлектродовснижается.
109
Плохую свариваемость имеют металлы, которые при сварке на простейшем цикле не могут обеспечить удовлетворительного качества соединения. Процесс сварки сопровождается выплесками, подгорают электроды, нарушается стабильность размеров точки. Претерпевает существенное изменение металлоструктура литого ядра точки и околошовной зоны.
Как было показано, на свариваемость оказывают влияние свойства металлов, технология и оборудование. Что же касается свойств металлов, то чаще всего они задаются техническими условиями работы сварного узла и заменить их не удается. В распоряжении технолога имеются неисчерпаемые возможности программного обеспечения термомеханического процесса. Используя соответствующие программы сварочного тока и усилия на электродах в сочетании с рациональными технологическими приемами, можно добиться удовлетворительной и даже хорошей свариваемости у большинства сварных соединений, имеющих плохую свариваемость на простейшем цикле.
Следовательно, свариваемость сама по себе является относительным понятием. Например, жаропрочные сплавы на простейшем цикле имеют плохую свариваемость, а на сложном программированном цикле хорошую.
Автору проекта следует по литературным источникам определить свариваемость металла, данного в проекте сварного узла. Свои заключения отобразить в пояснительной записке.
Раздел 3. ОБОСНОВАНИЕ ВЫБОРА ЦИКЛА СВАРКИ И РАСЧЕТ ПАРАМЕТРОВ РЕЖИМА СВАРКИ
Среди циклов традиционных способов КТС (рис. 1), по-видимому, наиболее распространенным является цикл изменения параметров режима (рис. 2.1, а), предложенный еще Н. Н. Бенардосом. При сварке по этому циклу детали сжимают токопроводящими электродами неизменным усилием FСВ и через определенное время сжатия tСЖ пропускают импульс сварочного тока заданной силы IСВ и длительности tСВ, а затем через определенное время проковки tПР, достаточное для кристаллизации и охлаждения зоны сварки, усилие сжатия электродов снимают. Его технологические возможности до настоящего времени удовлетворяют требованиям практики КТС не только сварки деталей из малоуглеродистых сталей в автомобиле- и сельхозмашиностроении, но и сварки некоторых специальных сталей и сплавов.
Сцельюпредотвращенияобразованиявядредефектовусадочногохарактера (трещин, пор) при сварке деталей из материалов, склонных к их образованию, например, относительно толстых деталей или деталей, склонных к закалке, а также деталей из высокопрочных материалов, применяют цикл (рис. 2.1, б), в котором при кристаллизации расплавленного металла в ядре и охлаждения зоны сварки (в период tПР проковки) усилие сжатия электродов увеличивают (прикладывают ковочноеусилиеFК). Этимувеличиваютвнейстепеньпластическойдеформации металла, компенсирующейегоусадкуприкристаллизациииохлаждении.
110
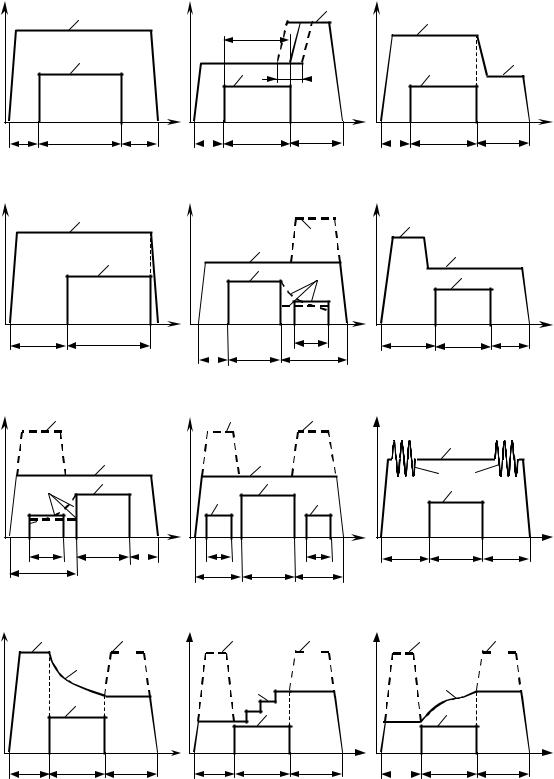
I, F |
FСВ |
|
|
|
|
|
|
|
|
IСВ |
|
|
|
|
t |
tСЖ |
|
tСВ |
tПР |
|
|
а |
|
I, F |
|
FСВ |
|
|
|
|
|
|
|
IСВ |
|
|
|
|
t |
tСЖ |
tСВ |
|
|
|
|
г |
|
I, F |
|
FК |
|
|
|
FСВ |
|
|
IП |
IСВ |
|
|
|
|
|
|
|
|
t |
|
tП |
tСВ |
tПР |
|
tСЖ |
|
|
|
|
ж |
|
I, F |
F0 |
|
FК |
|
|
FЭ |
|
|
|
IСВ |
|
|
|
|
t |
tСЖ |
tСВ |
tПР |
|
|
|
к |
|
I, F |
tК |
FК |
|
|
|
|
IСВ |
tК |
|
|
|
|
|
t |
tСЖ |
tСВ |
tПР |
|
б |
|
I, F |
|
|
|
|
FК |
|
FСВ |
|
|
IСВ |
IД |
|
|
|
|
|
t |
tСЖ |
tСВ |
tД |
tПР |
||
|
д |
|
I, F |
FК |
FК |
|
FСВ |
|
|
IСВ |
|
IП |
|
IД |
|
|
t |
tП |
tСВ |
tП |
tСЖ |
tПР |
|
|
з |
|
I, F |
F0 |
FК |
|
FЭ |
|
|
IСВ |
|
|
|
t |
tСЖ |
tСВ |
tПР |
|
л |
|
I, F |
FСВ |
|
|
|
|
|
IСВ |
FК |
|
|
|
|
|
t |
tСЖ |
tСВ |
tПР |
|
в |
|
I, F |
|
|
FО |
|
|
|
FСВ |
|
|
IСВ |
|
|
|
t |
tСЖ |
tСВ |
tПР |
|
е |
|
I, F |
|
|
|
Fсв |
|
|
УЗК |
|
|
IСВ |
|
|
|
t |
tСЖ |
tСВ |
tПР |
|
и |
|
I, F |
F0 |
FК |
|
FЭ |
|
|
IСВ |
|
|
|
t |
tСЖ |
tСВ |
tПР |
|
м |
|
Рис. 2.1. Наиболее распространенные циклограммы усилия сжатия электродов и тока при традиционных способах контактной точечной сварки
111
В технологии КТС известны и циклы (рис. 2.1, в), при осуществлении которых в период проковки соединения tПР усилие сжатия электродов не только не увеличивают, но даже и уменьшают. Например, при сварке свинцовых деталей со стальными.
При сварке деталей из углеродистых и низколегированных сталей с целью предотвращения образования в соединении закалочных структур и трещин путем уменьшения скорости его охлаждения применяют цикл (рис. 1, г), в котором сжатие деталей электродами вообще прекращают одновременно с окончанием импульса сварочного тока. Для решения этой же задачи, а также с целью улучшения условий проковки соединений и уменьшения требуемой величины ковочного усилия, а иногда для термообработки соединения в сварочных электродах применяют цикл, в котором после окончания импульса сварочного тока IСВ в период проковки соединения tПР пропускают дополнительный подогревающий импульс тока IД (рис. 2.1, д). Дополнительный подогревающий импульс тока IД, уменьшающий сопротивление деформации металла в зоне сварки, может применяться в сочетании с любой циклограммой изменения усилия сжатия электродов. Подогревающий ток пропускают обычно в виде отдельного дополнительного импульса IД, но иногда и как модулированное продолжение импульса сварочного.
Для получения оптимальных значений начальных электрических сопротивлений в контактах, в особенности при сварке деталей из высокопрочных материалов или деталей с относительно невысоким качеством подготовки поверхностей, в практике точечной сварки применяют цикл (рис 2.1, е), в котором перед импульсом сварочного тока в период сжатия деталей tСЖ производят их обжатие повышенным усилием сжатия электродов F0 (усилием обжатия). Этот технологический прием используют и для предупреждения наружных и внутренних начальных выплесков, а также для вытеснения пластичных прослоек грунта, клея.
Однако в ряде случаев только предварительным обжатием деталей не удаётся получить оптимальные значения начальных электрических сопротивлений в контактах. В этом случае применяют цикл (рис 2.1, ж), в котором металл в зоне сварки предварительно, перед сварочным импульсом IСВ, подогревают отдельным либо совмещенным со сварочным дополнительным подогревающим IП импульсом тока.
Во многих случаях точечной сварки стабилизировать процесс формирования соединения можно интенсификацией микро- и макропластических деформаций металла в зоне сварки путем уменьшения его сопротивления пластической деформации на стадиях сжатия и проковки соединения. В таких случаях одном цикле рационально использовать и предварительный, и дополнительный подогревающие импульсы тока, в частности, даже при сварке деталей из легких сплавов. Подогревающие импульсы тока IП и IД можно использовать в сочетании с любой циклограммой изменения усилия сжатия электродов (рис 2.1, з). Для достижения указанных выше целей иногда ис-
112
пользуют цикл (рис. 2.1, и), в котором до импульса сварочного тока и после его окончания, осуществляют колебания электродов с инфразвуковой, звуковой, или ультразвуковой частотой.
В ряде случаев, например, при сварке деталей из жаропрочных материалом, рационально применять даже цикл (рис 2.1, к), в котором усилие сжатия электродов FЭ во время tСВ действия импульса сварочного тока уменьшают по определенной программе.
Кроме того, программированное изменение усилия сжатия электродов во время импульса сварочного тока позволяет повысить и энергетическую эффективность процесса КТС, а также его устойчивость против образования непроваров. Для достижения этих целей применяют циклы, в которых усилие сжатия электродов в процессе сварки изменяют. Причем, в процессе КТС усилие сжатия электродов чаще всего увеличивают от начального до конечного его значения. И осуществляют это ступенчато (рис. 2.1, л).
Из представленных циклов студенту следует выбрать цикл, который наиболее подходит в соответствии с конструкцией и материалом изделия.
Обеспечение высокого качества сварки и максимальной производительности процесса для данной толщины, формы и материала изделия определяется правильностью выбранного режима сварки.
Режимом сварки называется совокупность электрических, механических и временных параметров, обеспечиваемых сварочным оборудованием и необходимых для получения качественного сварного соединения.
Режим контактной сварки зависит от многих факторов: электро- и теплопроводности, температуропроводности, прочности свариваемых материалов, температуры плавления, плотности, конструкции сварного узла, условия токоподвода, схемы сварки и др.
Параметры режима выбирают по таблицам, номограммам, рассчитывают или устанавливают опытным путем. Выбранные или расчетные режимы проверяют и уточняют для конкретных условий.
К основным параметрам режима сварки относят:
при точечной сварке: сила сварочного тока — IСВ, время сварки — tСВ, сварочное усилие — FСВ, ковочное усилие — FK, время проковки — tK, а также размеры рабочей поверхности электродов (RЭ и dЭ).
шовной сварке: IСВ, tСВ, FСВ, время паузы — tП, скорость вращения роликов – псв, а также размеры рабочей поверхности роликов (fp, Rp, Dp), а при шаговой шовной сварке с проковкой — дополнительно FK, tK, и кроме того длительность перемещения и остановки роликов;
рельефной сварке: IСВ, tСВ, FСВ, а также диаметр и высота рельефа (dр
иhp).
При этих способах сварки режим должен обеспечить заданные по ГОСТ 15878-79 размеры литого ядра (d, h) в зависимости от толщины свариваемых деталей.
113
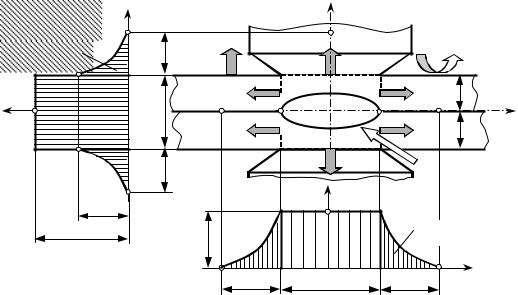
Расчетным путем определяется действующее значение сварочного тока с использованием формул теплового баланса и формул для оценки сопротивления деталей к концу сварки.
При расчете режимов шовной сварки величина тока рассчитывается аналогичным способом. При этом оптимальный диаметр ядра соответствует ширине шва для данной толщины. Расчетное значение тока увеличивается на 10-15% с учетом явления шунтирования.
Тепловой баланс в зоне сварки и расчет сварочного тока
Теплоту QЭЭ, которая должна выделиться в зоне формирования соединения для получения ядра заданных размеров, можно рассчитать через теплосодержание металла в ней к концу процесса сварки и количество теплоты, отведенное из зоны сварки в процессе формирования соединения.
/8 |
z |
|
z |
|
|
|
|
|
|
||
ПЛ |
|
|
|
|
|
Т |
3 |
|
|
|
|
|
х |
Q4 |
Q3 |
|
Q5 |
|
|
|
|||
|
|
Q2 |
|
s |
r |
|
s |
|
|
||
T |
2 |
Q2 |
|
s |
|
|
|
|
|
||
|
|
|
|
|
|
|
3 |
|
Q3 |
Q1 |
|
|
х |
|
|
|
|
0,5ТПЛ |
|
Т |
|
|
|
|
|
|
|
||
ТПЛ |
|
ПЛ |
|
ТПЛ /4 |
|
|
|
|
|
|
|
|
|
T |
|
r |
|
|
|
|
|
|
|
|
|
х2 |
dЭ |
х2 |
|
Рис. 2.2. Схемы теплопередачи в зоне сварки и распределения в ней температуры для расчета теплового баланса
Для этого используют условные схемы теплопередачи в зоне сварки и распределения в ней температуры (рис. 2.2).
Вданной методике расчета допускают, что вся теплота QЭЭ выделяется
вцилиндре, диаметр которого равен диаметру dЭ контакта электрод-деталь. Выделившуюся теплоту QЭЭ условно разделяют на теплоту Q1, которая расходуется на нагрев и плавление металла в выделенном цилиндре (Q1 ≈ 20...30 % от QЭЭ, а также на теплоту Q2, которая отводится в окружающий его металл деталей (Q2 ≈ 20 % от QЭЭ) и теплоту Q3, которая отводится в электроды (Q3 > 50 % от QЭЭ). Относительно очень небольшая часть теплоты QЭЭ отводится с
114
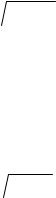
поверхностей деталей радиационной Q4 и конвективной Q5 теплоотдачей. Такое распределение теплоты QЭЭ описывается так называемым «уравнением теплового баланса», которое было предложено еще в 30-х годах прошлого века и используется до настоящего времени в инженерных методиках расчетного определения силы сварочного тока:
QЭЭ Q1 Q2 Q3 Q4 Q5 . |
(2.1) |
При расчетах по уравнению теплового баланса (2.1) общего количества теплоты QЭЭ, требуемой для формирования соединения заданных размеров, радиационной Q4 и конвективной Q5 теплоотдачей с поверхностей деталей обычно пренебрегают из-за их относительно малых величин.
Для расчета теплоты в зоне сварки делают ряд допущений. Так, принимают, что средняя температура в цилиндре, диаметром dЭ, который приближенно равен диаметру ядра, и высотой, равной суммарной толщине двух деталей 2s, принимается равной температуре плавления ТПЛ. Считается, что заметное повышение температуры металла в деталях из-за отвода в них теплоты Q2 наблюдается на расстоянии х2 от границы цилиндра, которое определяется временем сварки tСВ и коэффициентом температуропроводности металла
аМ:
х2 4 аМtСВ .
При этом принимается, что средняя температура кольца шириной х2 вокруг цилиндра диаметром dЭ, равна ТПЛ / 4.
Определение потерь тепла в электроды производится аналогичным образом. При этом принимается, что за счет тепла Q3 нагревается до средней температуры, равной ТПЛ / 8, участок электрода длиной
х3 4 аЭtСВ ,
где аЭ — коэффициент температуропроводности металла электродов. С учетом сказанного сокращенное уравнение теплового баланса
QЭЭ Q1 Q2 Q3
в развернутом виде описывают обычно следующим выражением:
Q |
|
|
dЭ2 |
2s |
|
c |
|
|
Т |
|
|
k |
d |
|
x |
|
x |
|
2s |
|
c |
|
ТПЛ |
|
|||||
ЭЭ |
М |
М |
ПЛ |
Э |
2 |
2 |
М |
М 4 |
|||||||||||||||||||||
|
|
4 |
|
|
|
|
|
1 |
|
|
|
|
|
, (2.2) |
|||||||||||||||
|
|
|
|
|
dЭ2 |
|
|
|
|
|
|
|
|
ТПЛ |
|
|
|
|
|
|
|
|
|
|
|
|
|||
|
|
2 k |
|
x |
|
Э |
c |
Э |
|
|
|
|
|
|
|
|
|
|
|
|
|
||||||||
|
|
|
|
|
|
|
|
|
|
|
|
|
|
|
|
||||||||||||||
|
|
|
|
2 |
4 |
|
3 |
|
|
|
|
8 |
|
|
|
|
|
|
|
|
|
|
|
|
|
где γМ и γЭ — плотность металла свариваемых деталей и электродов; сМ и сЭ
— теплоемкость металла свариваемых деталей и электродов; k1 — коэффици-
115

ент, который учитывает неравномерность распределения температуры в кольце; k2 — коэффициент, учитывающий влияние на теплоотвод формы рабочей части электродов.
С увеличением времени точечной сварки доля теплоты, отводимой в окружающий металл и электроды, всегда увеличивается, т. е. с увеличением времени сварки всегда уменьшается КПД процесса нагрева.
Количество теплоты QЭЭ, которое требуется для образования точечного сварного соединения заданных размеров, используют в основном для приближенного определения силы сварочного тока IСВ по зависимости, обеспечивающего выделение этой теплоты.
Расчет сварочного тока
Сварочный ток рассчитывают по закону Джоуля – Ленца.
IСВ |
QЭЭ |
, |
(2.3) |
|
mr 2rДК tСВ |
||||
|
|
|
где QЭЭ — общее количество теплоты, затрачиваемой на образование соединения; mr — коэффициент, учитывающий изменение rЭЭ в процессе сварки.
Для низкоуглеродистых сталей mr ≈ 1, для алюминиевых и магниевых сплавовmr ≈1,15, коррозионно-стойкихсталейmr ≈1,2, сплавовтитанаmr ≈1,4.
Продолжительность сварки
Продолжительность сварки tсв может являться критерием жесткости режима сварки. Относительно большое время характеризует мягкий режим, а малое время – жесткий. нетрудно представить себе, что с увеличением продолжительности сварки при прочих равных условиях размер литой зоны, а следовательно, и прочность точки будет увеличиваться. Следует иметь в виду, что развитие литой зоны происходи до определенного возрастания продолжительности сварки. Когда диаметр литого ядра достигает критических размеров, дальнейший рост его приостанавливается независимо от действия сварочного тока. В этом случае ядро будет распространяться в толщину деталей, в сторону электродов. Температура в контакте электрод-деталь резко увеличивается. Вместе с тем возрастает и пластичность перегретой зоны вплоть до потери устойчивости изложницы литого ядра. Под действием внутреннего давления металл литого ядра выбрасывается наружу. Обычно выплеск происходит в околошовной зоне рядом с электродом.
Ориентировочно для сварки сталей:
Низкоуглеродистых tсв= (0,1-0,2) δ;
Аустинитных сталей tсв= (0,1-0,3) δ;
Цветных металлов tсв= (0,01-0,10) δ; где δ – толщина одной свариваемой детали, мм.
116

Расчет параметров режима шовной сварки
Диаметр электрода-ролика Dэр = 100-250 мм выбирается в зависимости от толщины свариваемой стали и геометрической формы изделия
Ширина контактной поверхности hр выбирается по эмпирической фор-
муле
hp 4,5 |
|
(2.4) |
где δ – толщина одной свариваемой детали, мм.
Скорость сварки должна быть такой, чтобы каждая последующая точка перекрывала предыдущую на 20-50% . Обычно скорость прерывистой роликовой сварки для углеродистых и нержавеющих сталей средних толщин колеблется в пределах 0,5-3 м/мин.
Величину сварочного тока определяются по методике расчета тока при точечной сварке, увеличивая его на 20-50% в зависимости от диаметра электродов. Так, при Dэр=100 мм ток увеличивается на 20%, а при Dэр=250 мм ток увеличивается на 50%.
Расчет параметров режима шовной сварки
При сварке сопротивлением для образования качественного соединения основное внимание уделяют получению равномерного нагрева торцов и деталей и деформации металла, в наибольшей степени обеспечивающей разрушение и удаление оксидов. Основными параметрами режима являются сварочный ток Iсв или плотность тока j время протекания тока tсв, начальное усилие сжатия Fн и усилие осадки, Fос (соответственно начальное давление рн и давление осадки рос), укорочение деталей при сварке св, установочная длина l0.
Для определения j и tсв используют эмпирическую формулу
j tсв 103 |
(2.5) |
где k — коэффициент, равный 8 – 10 для сталей, 20 для алюминия, 27 для меди.
Как tсв так и j колеблются в широких пределах. При чрезмерной j возможен выплеск. Уменьшение tCB приводит к неравномерности нагрева деталей по сечению, а увеличение усиливает окислительные процессы. Малое рн облегчает нагрев деталей, однако может привести к образованию выплесков и усилению окисления торцов. Повышение рос увеличивает пластическую деформацию деталей, активизирует процессы разрушения оксидов и обновления поверхности. Минимальная установочная длина при сварке компактных сечений обычно равна диаметру или трем-четырем толщинам свариваемых деталей. Увеличение 10 может привести к искривлению деталей, потере их
117
устойчивости. При малом значении 10, на зону сварки сильное влияние оказывает отвод теплоты в электроды.
При сварке оплавлением электрические параметры режима зависят от теплопроводности и температуры плавления металла и определяются в основном скоростью оплавления, которая задается также с учетом активности металла к взаимодействию с газами и к процессам испарения легирующих элементов, а также от сечения свариваемых деталей. Усилие осадки и скорость осадки соответственно определяются теплопроводностью металла и его активностью к окислению.
При сварке оплавлением стремятся обеспечить: 1) нагрев деталей для оплавления торцов и проведения деформации целью удаления оксидов, а также для предупреждения образования неблагоприятных структур в околошовной зоне; 2) локальную интенсивность оплавления перед осадкой для формирования равномерно оплавленного слоя металла, предупреждения окисления и получения, благоприятного рельефа поверхности торцов; 3) деформацию деталей с достаточно большой скоростью, предупреждающей преждевременное остывание металла торцов и застревание оксидов в стыке. Величина деформации должна обеспечивать определенное растекание металла в плоскости стыка и выравнивание рельефа поверхности, необходимое для выдавливания расплавленного металла и оксидов.
Основные параметры режима: скорость оплавления vопл, плотность тока
при оплавлении jопл, |
припуск на оплавление опл, время оплавления tопл, вели- |
чина осадки ос и ее скорость vос длительность осадки под током toc.т, величи- |
|
на осадки под током |
ос. т, усилие осадки Foc или давление осадки рос, устано- |
вочная длина детали l0. Задают также напряжение холостого хода машины U20 и программу его изменения. При сварке импульсным оплавлением указывают также частоту fк и амплитуду Ак колебаний подвижной плиты машины.
При сварке оплавлением с подогревши задают температуру подогрева Tпод, длительность подогрева tпод, число импульсов подогрева и их длительность tимп, припуск на подогрев под.
Скорость оплавления vопл выбирают из условий получения определенного распределения температуры в деталях. Для равномерного нагрева торцов перед осадкой конечную скорость оплавления vопл.к значительно увеличивают. От припуска на оплавление опл зависит получение равномерного нагрева но сечению, оптимального распределения температуры вдоль деталей я образование слоя расплавленного металла на торцах. Обычно опл составляет 0,7— 0,8 общего припуска на сварку. При сварке с подогревом и импульсным оплавлением опл сокращается в 2-3 раза.
Плотность тока jопл должна обеспечить процесс устойчивого оплавления. Она увеличивается с увеличением λ металла и vопл снижается при сварке с подогревом, а также при сварке деталей большого сечения. Вначале оплавления jопл наибольшая, по мере нагрева деталей она снижается, однако увеличение скорости оплавения к концу процесса вызывает увеличение jопл .
118
Припуск на осадку ос выбирают из условия удаления нагретого металла и оксидов из стыка. Припуск на осадку под током ос.т составляет обычно 0,5-0,8 ос . Давление осадки рос выбирают в зависимости от природы свариваемого металла и степени нагрева деталей. Скорость осадки vос выбирают с учетом ее влияния на окисление металла во время осадки и удаление оксидов и перегретого металла из стыка; она увеличивается при сварке активных металлов. Напряжении холостого хода U20 выбирают минимальным, обеспечивающим устойчивое оплавление.
Установочная длина деталей 2l0 = опл + ос + к., где к конечное расстояние между зажимами. Обычно при сварке круглых стержней и толстостенных труб l0 = (0,7÷1) d, где d – диаметр свариваемых деталей. При малой l0 наблюдается большой отвод теплоты в электроды, а зона интенсивного нагрева сужается, что требует увеличения рос. С увеличением l0 увеличивается требуемая электрическая мощность и уменьшается жесткость деталей.
При сварке оплавлением с подогревом температуру подогрева Тпод выбирают в зависимости от сечения свариваемых деталей и их металла. При сварке конструкционных сталей температура подогрева обычно составляет 800 – 1000 °С и возрастает до 1000 – 1200 °С при сварке деталей сечением 10000 – 20000 мм2. Температура подогрева деталей из труднодеформируемых аустенитных сталей на 100 – 150 °С выше. Время подогрева tпод возрастает с увеличением площади сечения деталей от нескольких секунд при сварке деталей сечением 500 – 1000 мм2 до нескольких минут при сварке деталей сечением 15000 – 20000 мм2. Длительность импульсов подогрева tимп обычно составляет 1 – 8 с, а припуск на подогрев под изменяется в пределах 1 – 12 мм в зависимости от сечения деталей и свойств свариваемого металла.
Усилие зажатия деталей Fзаж выбирают из условия предупреждения роскальзывания деталей в губках при осадке: Fзаж = k0Foc, коэффициент k0 обычно колеблется от 1,5 до 4 и зависит от свойств свариваемого металла, конструкции зажимов, наличия упоров, конфигурации деталей.
После анализа образования соединений, особенностей стыковой сварки свариваемого материала и формы деталей, а также возможностей сварочного оборудования выбирают ориентировочные значения параметров режима, которые затем корректируются при сварке образцов-свидетелей с учетом конкретных технологических условий сварки до получения требуемого качества соединения. Уточненный (оптимальный) режим, обеспечивающий положительные результаты сварки, фиксируется в соответствующей технологической документации; при этом выдается разрешение на сварку изделий.
Ориентировочные режимы сварки можно также определить расчетом с использованием критериев подобия, если известны режимы сварки деталей из того же металла, близких по геометрической форме, но различных по размерам. Согласно теории подобия температурных полей и деформаций, при геометрическом подобии параметры режима соединений определяются четырьмя критериями
119