
Лабораторный практикум ЭМ июнь 2012 КРАСНОЯРСК
.pdf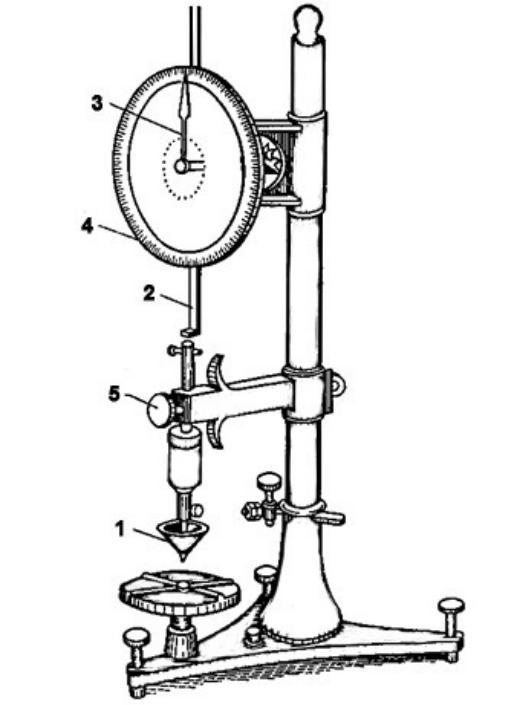
от 0 до 100 ºС и ценой деления шкалы в 1º; секундомер; шпатель; образцы пластичных смазок.
Рис. 41. Пенетрометр. 1– конус; 2 – кремальера; 3 – стрелка; 4 – циферблат; 5 – пусковая кнопка.
161
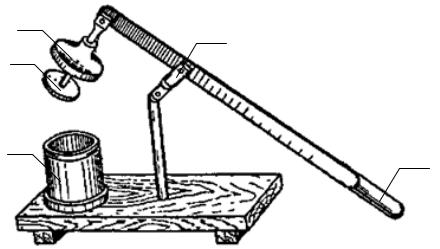
3 |
4 |
|
2
1 |
5 |
|
Рис. 42. Смеситель. 1 – стакан смесителя; 2 – рабочий орган смесителя; 3 – крышка; 4 – рычаг; 5– рукоятка
Краткие теоретические сведения
Одним из основных показателей при выборе пластичной смазки для узла трения является ее консистенция, которая условно определяет прочность смазки, возможность еѐ удерживаться в узлах трения и обеспечивать смазывание поверхностей трения деталей. В соответствии с российским и зарубежными стандартами этот показатель принято оценивать по числу пенетрации. Пенетрация (лат. Penetration – проникать) мера проникновения конусного тела в смазку, таким образом оценивают консистенцию или густоту смазки.
Число пенетрации пластичной смазки определяют при температуре плюс 25 ºС, оно выражается в десятых долях миллиметра погружения конуса в смазку. Согласно значения числа пенетрации по действующим стандартам смазке присваиваются номера консистенции. По данному показателю область возможного применения смазки в зависимости от конструктивных особенностей узлов трения, начиная от централизованной подачи до полностью открытых передач.
Порядок выполнения работы
В стакан смесителя (рис. 42) загружают вмазыванием испытуемую смазку таким образом, чтобы она выступала в виде полусферы на высоту 15 мм, это обеспечит общий объем смазки на 15 % больше объема стакана. При вмазывании смазки необходимо следить, чтобы в ней не оставалось карманов воздуха.
После заполнения стакана завинчивают плотно крышку смесителя и погружают его в ванну, там его выдерживают в течение 1 часа при температуре + 25ºС.
162
После выдержки стакан крепят к основанию смесителя, рукоятку к рычагу и приступают к перемешиванию смазки. Перешивание производят с интенсивностью 60 погружений мешалки в течение 1 мин.
После перемешивания смазку снова выдерживают в ванне в течение 15 минут при температуре испытания.
Затем стакан со смазкой помещают на столик пенетрометра (рис. 41), тщательно выравнивают поверхность смазки (излишек смазки убирают).
Конус пенетрометра устанавливают так, чтобы он касался острием поверхности смазки не в центре стакана, но при этом при погружении конус не должен касаться стенки стакана.
После установки конуса опускают кремальеру (франц. – привод преобразующий поступательное движение рейки в круговое движение стрелки). До соприкосновения с плунжером конуса и устанавливают стрелку циферблата на нуль.
При замере погружения конуса в смазку одновременно пускают в ход секундомер и нажимают пусковую кнопку пенетрометра. В течение 5 секунд конус свободно погружается в смазку, после чего отпускают кнопку, прекращая погружение конуса.
Затем снова опускают кремальеру до соприкосновения с плунжером. При этом вместе с кремальерой передвигается и стрелка циферблата, отсчитывая число пенетрации смазки по циферблату.
После снятия показателей конус приподнимают, тщательно очищают, выравнивают смазку в стакане, проводят повторные испытания не менее 4-х раз.
Расхождения между результатами отдельных испытаний не должны превышать ± 3% от среднего арифметического по результатам 4-х испытаний.
Полученный результат заносится в таблицу для определения показателей качества смазки по всем показателям, определяемым в данной работе.
Определение температуры каплепадения смазки
Применяемая аппаратура и материалы
Прибор для определения температуры каплепадения – 1 шт, баня глицериновая – 1 шт, испытуемая смазка – 10 г.
Краткие теоретические сведения
О переходе смазки из пластичного в текучее состояние судят по температуре каплепадения. Температурой каплепадения пластических смазок называют температуру, при которой происходит падение первой капли
163
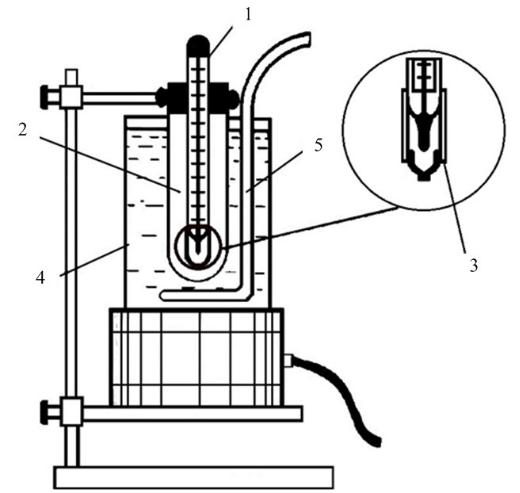
смазки из капсюля прибора, нагреваемого в строго определенных условиях.
По температуре каплепадения судят о верхней температурной границе применения смазки. Смазка не будет вытекать из узла трения, если его температура на 15–20 °С ниже температуры каплепадения применяемой смазки. Смазка с низкой температурой каплепадения не будет удерживаться в узле трения, и ее придется часто пополнять. Смазка с чрезмерно высокой температурой каплепадения не обеспечивает надежный режим смазки узла трения.
Основной частью прибора для определения температуры каплепадения смазки является специальный термометр 1, оборудованный в нижней части гильзой, в которой помещают капсюль 3 (рис. 43). Диаметр отверстия капсюля равен 3мм. Термометр с капсюлем при помощи пробки вставляют в пробирку 2 с таким расчетом, чтобы до ее дна от нижней кромки капсюля оставалось свободное пространство 25 мм.
Рис. 43. Прибор для определения температуры каплепадения пластичных смазок: 1 – термометр с капсюлем; 2 – пробирка; 3 – капсуль; 4 – водяная баня; 5 – мешалка
164
Пробирку на зажиме штатива укрепляют в глицериновой или водяной бане 4, нагревают электроплиткой.
Порядок выполнения работы
Капсюль при помощи шпателя наполняют испытуемой смазкой. Излишек смазки срезают с верхней части капсюля шпателем, вкла-
дывают капсюль в гильзу термометра до упора во внутренний буртик. Излишек смазки, выдавленный концом термометра, срезают шпателем.
Термометр с капсюлем вставляют в пробирку, которую помещают в баню и подогревают ее таким образом, чтобы скорость нагрева, начиная с температуры на 20 °С ниже ожидаемой температуры каплепадения, была равна 1°С в минуту. При определении температуры каплепадения низко- и среднеплавких смазок в баню заливают воду, а тугоплавких – глицерин. На дно пробирки рекомендуется помещать кусочек бумаги для удобства наблюдения и защиты капли от дополнительного нагрева лучеиспусканием от электроплитки.
Температура, при которой из нижнего отверстия капсюля упадет первая капля, принимается за температуру каплепадения. По полученным результатам определяют соответствие температуры каплепадения требованиям стандарта, а если марка смазки не известна, определяют еѐ по таблице (прил. П 12).
Определение предела прочности пластичных смазок
Приборы и оборудование
Пластомер К-2 (рис. 44) – 1шт., мешалка – 1шт., электроплитка – 1шт., термостат – 1шт., минеральное масло с кинематической вязкостью при 50 °С в пределах 19–53 сСт – 200 мл, образец смазки – 250 г.
Краткие теоретические сведения
За предел прочности пластичных смазок принимают минимальное напряжение в кг/см2, при котором происходит сдвиг одного слоя смазки относительно другого. Метод основан на определении давления, при котором происходит сдвиг смазки в капилляре пластомера К-2. От предела прочности зависит надежность смазки негерметизированных узлов трения.
165
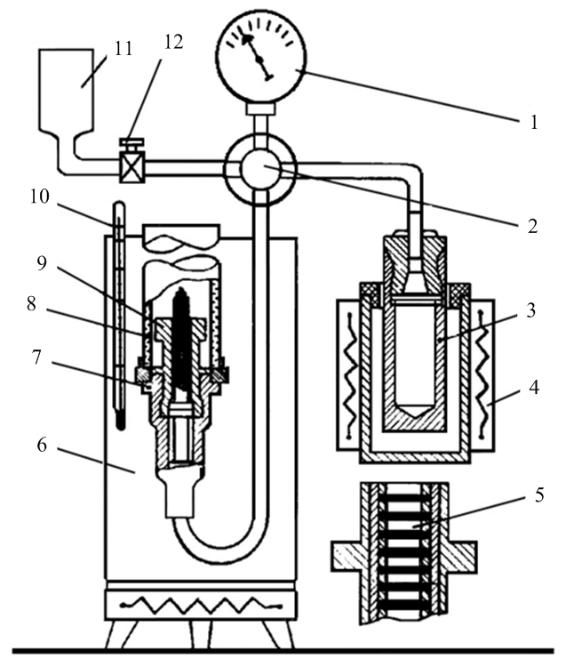
Рис. 44. Пластомер К. И. Климова (К-2):
1 – манометр, 2 – блок каналов; 3 – резервуар для нагрева масла; 4 – электронагреватель; 5 – капилляр; 6 – водяная баня; 7 – корпус пластомера; 8 – защитное стекло; 9 – оправка капилляра; 10 – термометр; 11 – воронка; 12 – кран
Порядок выполнения работы
Заполнить мешалку смазкой и выдержать в термостате при температуре 20 + 1 °С в течение 30 минут, после чего перемешать смазку, сообщив поршню 100 двойных ходов.
166
После этого обе половинки желоба капилляра заполнить испытуемой смазкой, соединить обе половинки и надеть на капилляр кольцо.
Смазать наружную поверхность капилляра и внутреннюю поверхность оправки. Медленно вращая и продвигая вдоль оси, вставить капилляр в оправку. На нижний конец оправки надеть резиновую прокладку и установить оправку в корпусе пластомера. Заполнить пластомер маслом, для чего открыть кран воронки, залить масло в воронку и держать кран открытым да тех пор, пока уровень масла в корпусе пластомера не достигнет верхнего обреза буртика оправки капилляра. После этого закрепить оправку капилляра в корпусе гайкой и установить защитное стекло.
Корпус пластомера поместить в водяную баню и выдержать в ней при температуре 50 + 1 °С в течение 20 минут. Уровень жидкости в бане должен быть на 30 мм выше верхнего кольца капилляра. Во время термостатирования кран воронки для залива масла держать открытым.
Закрыть кран воронки 12, включить электронагреватель 4, обогревающий резервуар с маслом 3, и наблюдать за манометром. Скорость повышения давления в системе должна быть не более 0,05 кг/см2 в минуту при использовании капилляра длиной 100 мм и 0,05 кг/см2 в две минуты при использовании капилляра длиной 50 мм и регулироваться реостатом электронагревателя.
После того как давление в системе, достигнув некоторого максимума, начнет снижаться, включают электронагреватель, открывают кран воронки и медленно вынимают оправку с капилляром, после чего кран закрывают.
Максимальное давление фиксируют с точностью до 0,01 кг/см2.
Предел прочности испытуемой смазки вычисляют по формуле: |
|
||
|
p r |
1000, |
(23) |
|
|||
|
2l |
|
где p – максимальное давление, кг/см2; r – радиус капилляра, 0,2 см; l – длина капилляра, мм
За результат испытаний принимают среднее арифметическое двух параллельных определений, допускаемые расхождения между которыми не должны превышать 10 %.
По результатам лабораторных исследований определяют марку сказки, и соответствие показателей качества требованиям стандарта, указывают область применения данной смазки (прил. П 12).
Дать рекомендации по возможному применению данной смазки.
167
Показатели испытуемой смазки и еѐ близкий прототип
|
Температура |
Пенетрация |
Предел |
Основа |
Смазка |
каплепадения, |
×10-1 мм при |
прочности, |
|
|
ºС |
25 ºС |
Па при 20 ºС |
смазки |
|
|
|||
|
|
|
|
|
Испытуемая |
|
|
|
|
|
|
|
|
|
Прототип |
|
|
|
|
|
|
|
|
|
Контрольные вопросы к лабораторной работе № 7
1.Состав и назначение пластичных смазок.
2.Основные показатели качества пластичных смазок и методы их определения.
3.Требования, предъявляемые к пластичным смазкам для шарниров рулевых тяг.
4.Требования, предъявляемые к пластичным смазкам для подшипников генератора и стартера.
5.Требования, предъявляемые к консервационным смазкам.
168
Лабораторная работа № 8
Определение показателей качества низкозамерзающих охлаждающих жидкостей
Цель работы: определить показатели качества низкозамерзающей жидкости, дать рекомендации по их исправлению, выполнить операцию по исправлению.
Инструкция по технике безопасности при выполнении лабораторной работы № 8
К лабораторной работе допускаются только прошедшие инструктаж по безопасным методам работы с агрессивными материалами. Приступать к работе можно с разрешения преподавателя.
При проведении работы:
–убедитесь в исправности приборов и оборудования;
–на рабочем месте не должно быть посторонних предметов и жид-
костей;
–по окончании работы слить отработанные жидкости в специальную емкость и сдать рабочее место преподавателю.
Краткие теоретические сведения
Показателями качества низкозамерзающих охлаждающих жидкостей являются: внешний вид (прозрачность, цвет); коррозионные свойства (бурый цвет указывает на наличие продуктов коррозии); вспениваемость; температура застывания (определяют по составу ОЖ); содержание механических примесей. Эти жидкости принято называть антифризами.
Маркировка антифризов связана с температурой их застывания. Для климатических зон с умеренным климатом до минус 35°С рекомендуется применять антифриз, маркируемый цифрой 40. Это значит, что его температура застывания не ниже минус 40 ºС.
Для северных и восточных районов, а также для Арктики и Антарктики приготавливают антифриз 65, имеющий температуру застывания не ниже минус 65 °С.
Производители также выпускают полуфабрикат антифриза, который представляет собой технический этиленгликоль с антикоррозийной присадкой. Его маркируют цифрой 40 с индексом К (40К). Он пригоден для приготовления антифриза 40 при разбавлении дистиллированной водой. На 1 литр 40К – 0,73 литра воды (прил. П 14).
Для автомобилей марок ВАЗ, КамАЗ выпускаются жидкости, рассчитанные на длительное всесезонное применение: тосол А40 и тосол А65, а
169
также концентрированный тосол 40К. Для эксплуатации его разводят дистиллированной водой в соотношении 54 % тосол и 40–46 % воды.
Следует помнить, что температура застывания этиленгликоля минус 12°С – минус 13ºС, и только при разбавлении его водой она достигает значений, которые обеспечивают низкотемпературную эксплуатацию.
В прил. в табл. П 14 приведены плотность, и температура застывания смеси технического этиленгликоля и воды.
При нормальном давлении этиленгликоль кипит при температуре 198 °С, а вода – при 100 °С. Поэтому в процессе эксплуатации выкипание воды всегда больше, чем выкипание этиленгликоля. В результате оптимальное их соотношение в охлаждающей жидкости нарушается в сторону увеличения концентрации этиленгликоля, а это приводит к ухудшению низкотемпературных свойств. Следовательно, при испарении из системы охлаждающей жидкости в нее следует доливать только дистиллированную воду.
Порядок выполнения работы
Ареометром определить плотность антифриза. Значение плотности антифриза при температуре опыта привести к стандартной температуре 20 °С по формуле:
|
|
20 |
= + – 20 , |
(24) |
|
|
4 |
4 |
|
где 20 |
– |
плотность антифриза при стандартных условиях, |
г/см3; – |
|
4 |
|
антифриза при температуре определения, г/см3; |
4 |
|
плотность |
– среднее |
значение температурного коэффициента этиленгликолевого антифриза, которое равно 0,000525; t – температура испытания, ºС.
Состав и температуру застывания антифриза по приведенной плотности определить по диаграмме (рис. 45).
Для этого провести горизонтальную линию от оси ординат, где нанесены значения плотности, до пересечения ее с кривой плотности, опустить перпендикуляр на ось абсцисс и получить значение состава антифриза. Продолжая перпендикуляр вниз, до пересечения с кривой температур застывания и проводя горизонтальную линию влево до оси ординат, получить значение температуры застывания данной смеси.
На основании проведенных испытаний сделать заключение о соответствии качества испытуемого образца антифриза требованиям температуры застывания одного из стандартных значений.
Если показатели качества образца антифриза отличаются от норм стандарта, рассчитать состав антифриза в соответствии с необходимым значением и приготовить смесь требуемого качества.
170