
проектирование ТГ
.pdf119
Для расчета кривой КПД достаточно взять следующие точки нагрузки: 0,25РН; 0,5РН; 0,75РН; 1,0РН; 1,25РН. Результаты расчёта сводят в таблицу
(табл. 31) и строят кривую КПД
η=f(P/PН).
Таблица 31
Зависимость КПД от нагрузки
Мощности и |
|
|
Р/РН |
|
|
|
составляющие |
|
|
|
|
|
|
0,25 |
0,5 |
0,75 |
1 |
1,25 |
||
потерь |
||||||
|
|
|
|
|
||
|
|
|
|
|
|
|
Р, Вт |
|
|
|
|
|
|
|
|
|
|
|
|
|
Р0,Вт |
|
|
|
|
|
|
|
|
|
|
|
|
|
РК , Вт |
|
|
|
|
|
|
|
|
|
|
|
|
|
Р2 , Вт |
|
|
|
|
|
|
|
|
|
|
|
|
|
РΣ , Вт |
|
|
|
|
|
|
Р+ РΣ , Вт |
|
|
|
|
|
|
η, % |
|
|
|
|
|
|
|
|
|
|
|
|
120
3. Тепловой расчет
3.1. Общие замечания
Тепловой расчет турбогенератора производится с целью определения тем-
пературы обмоток, активной стали статора, бочки ротора. Тепловой расчет произ-
водится для установившегося режима, когда все тепло, выделяющееся в машине,
отводится охлаждающей средой.
При установившемся режиме температура обмоток не должна превосходить допустимых значений для данного класса изоляции. В турбогенераторах обычно применяется изоляция класса F или B. Предельной температурой изоляции этих классов является 155 и 130 °С соответственно.
Кроме того, для турбогенераторов большое значение имеет разность темпе-
ратур между различными частями машины. Это связано с тем, что при различных температурах различные части машины будут иметь неодинаковую деформацию,
тем более что и температурные коэффициенты линейного расширения материа-
лов, соприкасающихся между собой, могут значительно различаться. Это может привести к недопустимой неравномерной деформации отдельных элементов ма-
шины, соприкасающихся друг с другом.
Далее приведены упрощенные методы расчета, построенные на основе теп-
ловых схем.
3.2. Тепловой расчет статора
Для расчета нагрева турбогенератора используется метод тепловых схем.
Для расчета температуры статора в качестве расчетной зоны принимается одно зубцовое деление одного пакета сердечника (рис. 30).
Движение среды в расчетном участке следующее. Потери в меди обмотки проходят через основную изоляцию. Одна часть потерь направлена в радиальные каналы и отдается окружающей среде – тепловой поток qМ2; другая часть прохо-
дит через зубцы – тепловой поток qМ1.

121
Потери, выделившиеся в зубцах сердечника qZ, вместе с частью потерь в меди qМ1 движутся по трем направ-
лениям: вдоль листов стали к воздуш-
ному зазору машины (qdZ), поперек листов стали к радиальному каналу
(qqZ) и вдоль листов стали (qZa) к ярму сердечника.
Потери qа, выделившиеся в ярме,
вместе с потоком qZa, поступающим от зубцов, движутся в двух направлениях:
поперек листов к радиальному каналу
(qqa) и вдоль листов стали в направле-
нии к наружной поверхности сердеч-
ника статора (qda).
Тепловая схема замещения
статора с косвенным охлаждением |
Рис. 30. Расчетная область статора |
меди обмотки показана на рис. 31. меди обмотки показана на рис. 31.
Эта схема предполагает, что наиболее горячей точкой является медь обмот-
ки статора, затем зубцы и ярмо. Такая картина соответствует действительному распределению температуры в статоре с косвенным охлаждением. Основные до-
пущения в этой схеме – равенство температур охлаждающей среды во всех точ-
ках статора (каналах и зазоре турбогенератора) и отсутствие потоков теплоты в аксиальном направлении, что справедливо для современных многоструйных сис-
тем вентиляции.
.

122
Рис. 31. Тепловая схема замещения статора с косвенным охлаждением меди обмотки
Равенство температур ох-
лаждающей среды для всех точек статора отражено в схеме «за-
землением» узлов, соответству-
ющим этим точкам.
Расчет тепловой схемы про-
водится в следующей последова-
тельности.
Вычисляют потери в рас-
четном объеме для меди, Вт:
|
|
|
1 |
|
|
|
l1 |
|
|
qM |
= |
|
|
|
× |
|
|
|
.(296) |
|
|
|
|
||||||
Z1 |
|
× PЭО |
l1 |
+ lЛ1 |
+ РЭД |
||||
|
|
× nП |
|
|
|
Вычисляют потери в расчет-
ном объеме для стали зубцов: qZ=PZ/(Z1×nП), (297)
где PZ – суммарные потери в стали зубцов, включающие в себя
основные и добавочные потери в стали зубцов,
PZ=PZ1+PZνk× (1+ОКЗ2)+ PZZ0. |
|
Вычисляют потери в расчетном объеме для стали ярма: |
|
qa=Pa/(Z1× nП), |
(298) |
где Pa – суммарные потери в стали ярма
Pa=Pса+Paνk× (1+ОКЗ2).
Вычисляют сопротивления теплопроводности (тепловые сопротивления),
соответствующие схеме рис. 31. Тепловое сопротивление теплопроводности для участка теплопроводящего тела
Rλ=b/(l×S),
123
где b – толщина теплопроводящего тела в направлении движения теплового пото-
ка; l – удельная теплопроводность (коэффициент теплопроводности); S – сечение плоскости, перпендикулярной направлению движения теплового потока.
Тепловое сопротивление теплоотдачи для поверхности тела
Rα=1/(a×S),
где a – коэффициент теплоотдачи. |
|
Тепловое сопротивление изоляции в пазу, град/Вт, |
|
RИ=dИ/(2× lИЭ× hM× lПАК), |
(299) |
где lИЭ – эквивалентная теплопроводность пазовой изоляции с учетом прослойки газа между стержнем обмотки и стенкой паза:
λИЭ |
= |
(δ |
И |
+ δ Н )× λИ × λН |
, |
(300) |
|
|
|
||||
|
|
δ И × λН + δ Н × λИ |
|
dИ – односторонняя толщина корпусной изоляции, м, (п. 2.3); lИ – удельная теп-
лопроводность пазовой изоляции, Вт/(м×град), (табл. 32); dН – толщина газовой прослойки между стержнем обмотки и стенкой паза, dН = 0,2 мм (0,0002 м); lН –
удельная теплопроводность охлаждающего газа (табл. 33).
Тепловое сопротивление изоляции обмотки в радиальном канале
R¢И=dИ/(2× lИ× hM× lПАК). (301)
Тепловое сопротивление стали зубца вдоль листов стали
|
R¢ |
= |
|
|
hП1 |
|
|
, |
|
|
(302) |
|||
|
2 × bZ1 ×lПАК × λd |
|
|
|||||||||||
|
|
dZ |
|
|
|
|
|
|
||||||
|
|
|
|
|
|
|
|
|
|
|||||
где bZ1 – средняя толщина зубца (рис. 30) |
|
|
|
|
|
|
|
|||||||
b |
|
= |
|
π |
|
× (D + h |
|
) - b |
|
; |
(303) |
|||
Z1 |
|
|
|
|
П1 |
П1 |
||||||||
|
|
2 × Z1 |
1 |
|
|
|
|
|
||||||
|
|
|
|
|
|
|
|
|
|
|
||||
ld – теплопроводность стали вдоль листов (табл. 32). |
|
|
||||||||||||
Тепловое сопротивление стали зубца поперёк листов стали |
|
|||||||||||||
|
|
R¢ |
= |
|
lПАK |
|
|
|
, |
|
|
(304) |
||
|
|
qZ |
4 |
× bZ1 × hП1 × λq |
|
|
|
где lq – теплопроводность стали поперёк листов (табл. 32).
124
|
|
Таблица 32 |
Коэффициенты теплопроводности и теплоемкости материалов, |
||
используемых в турбогенераторостроении |
|
|
|
|
|
|
Коэффициент |
Удельная теп- |
Материал |
теплопроводности, |
лоемкость, |
|
Вт/(м×град) |
Дж/(кг×град) |
|
|
|
Медь электротехническая |
385 |
388 |
Алюминий |
233 |
920 |
Серебро |
420 |
250 |
Сталь листовая электротехническая: |
|
|
вдоль листов |
25 |
480 |
поперек листов |
3,75 |
480 |
Сталь роторная |
56 |
– |
Изоляция: |
|
|
обмотки ротора |
0,13–0,16 |
– |
компаудированная |
0,20 |
– |
миканитовая, "Монолит" |
0,24 |
– |
"Слюдотерм" |
0,26 |
– |
|
|
|
Тепловые сопротивления для стали ярма |
|
|
|
|
|
|
||||||||||
|
|
|
Rda! |
= |
|
|
|
ha1 |
|
|
, |
|
(305) |
|||
|
|
2 ×ba |
× lПАК × |
|
|
|
||||||||||
|
|
|
|
|
|
|
λd |
|
|
|
||||||
|
|
|
Rqa! |
= |
|
|
|
lПАК |
|
, |
|
|
|
(306) |
||
|
|
|
|
|
|
|
|
|
|
|||||||
|
|
|
|
|
|
|
|
4 × ba × ha × λq |
|
|
|
|||||
где ba – ширина расчетного элемента на уровне ярма |
|
|||||||||||||||
b |
|
= |
|
π |
|
× (D |
|
+ D + 2 × h |
|
). |
(307) |
|||||
a |
|
|
|
a |
П1 |
|||||||||||
|
2 |
× Z1 |
1 |
|
|
|
|
|
||||||||
|
|
|
|
|
|
|
|
|
|
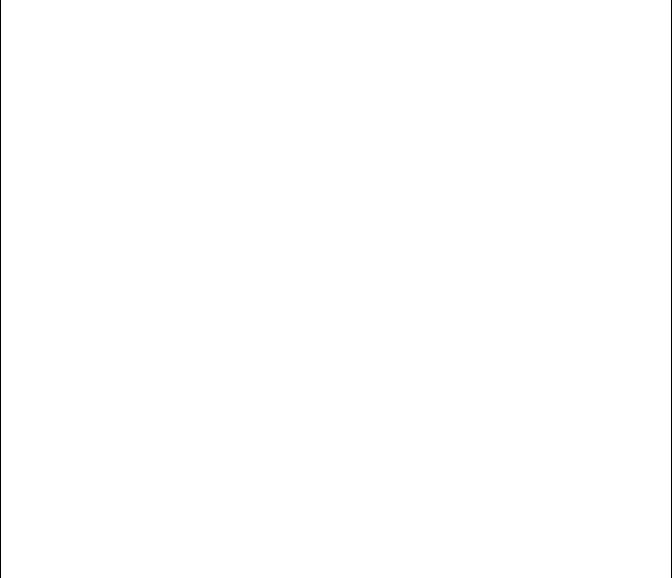
125
|
|
|
|
|
Таблица 33 |
|
Теплофизические свойства охлаждающих сред |
|
|||
|
|
|
|
|
|
Темпера- |
Плотность, |
|
Вязкость ки- |
Коэффициент теп- |
Удельная теп- |
|
нематиче- |
лопроводности, |
лоёмкость, |
||
тура, °С |
кг/м3 |
|
|||
|
ская, м2/с |
Вт/(м×град) |
Дж/(кг×град) |
||
|
|
|
|||
|
|
|
|
|
|
|
|
Воздух при давлении 0,1 МПа |
|
||
|
|
|
|
|
|
20 |
1,205 |
|
14×10-6 |
0,0258 |
1004 |
40 |
1,128 |
|
14,7×10-6 |
0,0272 |
1006 |
60 |
1,060 |
|
15,4×10-6 |
0,0288 |
1007 |
80 |
0,999 |
|
16,0×10-6 |
0,0304 |
1008 |
|
|
|
|
|
|
Газовая смесь (водород 98%, кислород 0,2%, азот 1,8%) при давлении 0,4 МПа
40 |
0,319 |
|
25,6×10-6 |
0,190 |
14040 |
60 |
0,299 |
|
26,8×10-6 |
0,199 |
14140 |
80 |
0,283 |
|
27,8×10-6 |
0,207 |
14140 |
|
|
|
|
|
|
|
|
Вода при давлении 0,1 МПа |
|
||
|
|
|
|
|
|
20 |
993 |
|
1,0×10-6 |
0,580 |
4195 |
40 |
985 |
|
0,7×10-6 |
0,609 |
4181 |
60 |
977 |
|
0,5×10-6 |
0,657 |
4192 |
80 |
969 |
|
0,4×10-6 |
0,666 |
4204 |
|
|
|
|
|
|
Сопротивление между ярмом и зубцом
RZa=R¢dZ+R¢da. (308)
Вычисляют сопротивления теплоотдачи. Коэффициенты теплоотдачи зави-
сят от скорости охлаждающей среды в каналах, которая может быть получена в результате вентиляционного расчета.
Полный расход газа определяется из условия равенства выделяемых в тур-
богенераторе потерь полному количеству теплоты, уносимому газом. Если пред-

126
положить, что весь охлаждающий газ проходит по каналам статора, то полный
расход его равен, м3/с, |
|
V=PΣ /( cV×qo)=PΣ /( c×r×qo), |
(309) |
где PΣ – полные потери в турбогенераторе, уносимые газом; |
cV – объемная тепло- |
ёмкость газа, Дж/(м3×град); qo – средний подогрев газа, принимается qo=25 °С; c –
удельная теплоёмкость газа, Дж/(кг×град), (табл. 33); r – плотность газа, кг/м3.
В случае непосредственного охлаждения обмотки статора водой из полных потерь необходимо вычесть потери в меди, так как приближенно можно считать,
что они полностью уносятся водой. |
|
Расход газа на один вентиляционный канал |
|
VK=V/(пП –1). |
(310) |
Зная расход газа на один канал, находят скорость охлаждающего газа в зоне
зубцового слоя с учетом того, что часть сечения канала занята стержнями обмот-
ки статора. Скорость охлаждающего газа в зоне зубцового слоя, м/с,
υ КП = |
[π × (D + h |
VK |
|
|
|
]× b |
|
. |
(311) |
||
П1 |
) |
- Z |
1 |
× b |
П1 |
|
|||||
1 |
|
|
|
|
К |
|
В зоне ярма охлаждающий газ течет в кольцевом канале без препятствий
(толщиной распорок можно пренебречь), поэтому скорость газа в зоне ярма
υ Kа |
= |
|
VK |
. |
(312) |
||
π × (D1 |
+ hП1 + ha1 )× bK |
||||||
|
|
|
|
||||
Скорость течения газа в зоне внешней поверхности ярма обычно принима- |
|||||||
ют u1=5–7 м/с. |
|
|
|
|
|
|
|
Скорость газа в зазоре |
|
|
|
|
|
|
|
|
|
υδ = |
|
, |
|
|
|
|
|
υ R2 +υa2 |
|
(313) |
|||
где uа=40 м/с – средняя аксиальная скорость газа в зазоре; uR – |
окружная скорость |
||||||
поверхности ротора |
|
|
|
|
|
|
uR=p×D2×f1.
После вычисления скоростей находят коэффициенты теплоотдачи.
|
|
|
|
|
127 |
|
|
|
|
|
|
|
||||
Коэффициент теплоотдачи в зазоре, Вт/(м2×град), |
|
|||||||||||||||
aδ=22,2×(1+0,125×uδ). |
(314) |
|||||||||||||||
Коэффициент теплоотдачи в радиальных каналах в районе зубцовой зоны |
||||||||||||||||
aКП=22,2× (1+0,24× uКП). |
(315) |
|||||||||||||||
Коэффициент теплоотдачи в радиальных каналах в районе ярма |
|
|||||||||||||||
aКа=22,2× (1+0,24× uКа). |
(316) |
|||||||||||||||
Коэффициент теплоотдачи внешней поверхности сердечника статора |
|
|||||||||||||||
a1=22,2× (1+0,24× u1). |
(317) |
|||||||||||||||
При водородном охлаждении коэффициент необходимо пересчитать с уче- |
||||||||||||||||
том давления водорода: |
|
|
|
|
|
|
|
|
|
|
|
|
|
|
|
|
|
|
aH=6,31×p0,8×a , |
(318) |
|||||||||||||
где р – давление, МПа. |
|
|
|
|
|
|
|
|
|
|
|
|
|
|
|
|
Далее рассчитывают тепловые сопротивления. |
|
|||||||||||||||
Сопротивление теплоотдачи для зазора, град/Вт, |
|
|||||||||||||||
|
R¢ |
= |
|
|
|
1 |
|
|
. |
|
|
(319) |
||||
|
|
|
|
|
|
|
|
|
||||||||
|
|
|
|
|
|
|||||||||||
|
|
δα |
|
|
|
|
bZ1 × lПАК |
×αδ |
|
|||||||
|
|
|
|
|
|
|
|
|||||||||
Сопротивление теплоотдачи с поверхности изоляции в канале |
|
|||||||||||||||
R¢ |
|
= |
|
|
|
|
|
1 |
|
|
|
|
|
. |
(320) |
|
|
|
|
|
|
|
|
|
|
|
|
||||||
|
|
|
|
|
|
|
|
|
|
|
||||||
Иα |
|
|
2 × hМ × bК × hП1 ×α KП |
|
||||||||||||
|
|
|
|
|
||||||||||||
Сопротивление теплоотдачи зубца в канале |
|
|||||||||||||||
R¢ |
|
= |
|
|
|
|
1 |
|
|
|
|
. |
|
(321) |
||
|
|
|
|
|
|
|
|
|
|
|||||||
|
|
|
|
|
|
|
|
|
|
|||||||
|
Zα |
|
|
2 × bZ1 × hП1 |
×αKП |
|
||||||||||
|
|
|
|
|
|
|||||||||||
Сопротивление теплоотдачи ярма в канале |
|
|||||||||||||||
|
R¢pα |
= |
|
|
|
|
1 |
|
|
|
. |
|
(322) |
|||
|
|
|
|
|
|
|
|
|
||||||||
|
|
2 × ba1 × ha1 |
|
|
|
|||||||||||
|
|
|
|
|
|
×αкa |
|
|||||||||
Сопротивление теплоотдачи сердечника статора с внешней поверхности |
||||||||||||||||
|
|
R0¢α |
= |
|
1 |
|
. |
|
|
(323) |
||||||
|
|
|
|
|
|
|
||||||||||
|
|
ba |
× lПАК |
|
|
|
||||||||||
|
|
|
|
|
|
|
|
×α1 |
|
Далее находят сопротивления ветвей тепловой схемы:
RИα RdZ= R′dZ+ R′δα;
128
RqZ= R′qZ+ R′Zα; Rdа= R′dа+ R′0α; |
|
|||||
|
Rqа= R′qа+ R′рα. |
(324) |
||||
Затем находят сопротивления, получающиеся в результате параллельного |
||||||
соединения RdZ и RqZ, а также Rdа и Rqа |
|
|
|
|
||
RZ = |
RdZ × RqZ |
; |
Rа = |
Rdа × Rqа |
. |
(325) |
|
|
|||||
|
RdZ + RqZ |
|
Rdа + Rqа |
|
Свертывая дальше схему, находят вспомогательные сопротивления:
R1 |
= |
|
|
RZ × RZа |
|
RZ |
+ Rа + RZa |
|
|||
|
|
|
|||
R2 |
= |
|
|
Rа × RZа |
|
RZ |
+ Rа + RZa |
|
|||
|
|
|
|||
R3 |
= |
|
|
RZ × Rа |
|
|
RZ |
+ Rа + RZa |
|
||
|
|
|
|
;
;
, |
(326) |
где RZa – тепловое сопротивление вдоль листов стали между зубцом и ярмом.
И, наконец, рассчитывают превышение температур частей статора над тем-
пературой окружающей среды.
Перегрев меди обмотки, °С,
θ М |
= RИα × |
qМ × (RИ + R1 + R3 ) + qZ × (R1 + R3 ) + qa × R3 |
+ |
1 |
×θ 0 , |
(327) |
||
|
RИα + RИ + R1 + R3 |
|
||||||
|
|
|
2 |
|
|
|||
Перегрев стали зубцов |
|
|
|
|
||||
|
qZ= qа×R3+qZ × (R1+R3)+qM1× (R1+R3)+0,5×q0, |
|
(328) |
|||||
где |
|
|
|
|
|
|
|
|
|
qМ1 = |
qМ × RИα - qZ × (R1 + R3 ) - qa × R3 |
. |
|
|
|
(329) |
|
|
|
|
|
|
||||
|
|
|
RИα + RИ + R1 + R3 |
|
|
|
|
|
Перегрев стали ярма |
|
|
|
|
||||
|
qа=(qа+ qZ+qM1)×R3+qа×R2+0,5×q0. |
|
|
|
(330) |
Превышение температуры горячего газа в машине над температурой холод-
ного принимают для турбогенераторов 25 °С.
Для машин с косвенным охлаждением наибольшее превышение температу-
ры обмотки статора 65 °С. При этом температура холодного газа в машине прини-