
Металловедение
.pdf
31
при измерении по шкалам С и А:
HR = 100-е.
Величина е определяется по следующей формуле:
е = (h-h0)/0,002,
где h0 - глубина внедрения наконечника в испытываемый материал под действием предварительной нагрузки Р0; h - глубина внедрения наконечника в испытываемый материал под действием общей нагрузки Р, измеренная после снятия основной нагрузки P1 с оставлением предварительной нагрузки P0 (см.
рис. 25).
Определение твердости по Роквеллу имеет широкое применение, так как дает возможность испытывать твердые и мягкие материалы; при этом отпечат-
ки от конуса или" шарика очень малы, поэтому можно испытывать готовые де-
тали без их порчи; испытание выполняется легко и быстро (30-60 с); не требу-
ется никаких измерений - число твердости читается прямо на шкале. Значения твердости по Роквеллу можно перевести в значения твердости по Бринеллю.
Испытание на твердость вдавливанием пирамиды (твердость по Виккер-
су). В поверхность металла вдавливают четырехгранную алмазную пирамиду
(рис. 26). По нагрузке, приходящейся на единицу поверхности отпечатка, опре-
деляют число твердости, обозначаемое HV:
HV |
2P |
sin |
|
1,8544 |
P |
, |
d2 |
|
d2 |
||||
|
2 |
|
|
где Р - нагрузка па пирамиду, Н (кгс); d - среднее арифметическое длины обеих диагоналей отпечатка после снятия нагрузки, мм; α - угол между проти-
воположными гранями пирамиды при вершине, равный 136°.

32
При испытании применяют нагрузки, равные 50, 100, 200, 300, 500, 1000
Н (соответственно 5, 10, 20, 30, 50, 100 кгс). Возможность применения
малых нагрузок - 50, 100 H (5, 10 кгс) позволяет испытывать материалы тонкого сечения и твердые поверхностные слои (например, цианированные,
азотированные).
Для определения числа твердости H"V по величине диагонали отпечатка пользуются специальной таблицей. Числа твердости до HV 400 единиц совпа-
дают с числами твердости НВ (по Бринеллю), а при твердости более HV 400
они превышают числа твердости НВ и тем больше, чем выше твердость.
Испытание на микротвердость. Это испытание применяют при определе-
нии твердости микроскопически малых объемов металла, например твердости отдельных структурных составляющих сплавов. Микротвердость определяют на специальном приборе, состоящем из механизма нагружения с алмазным на-
конечником и металлографического микроскопа. Поверхность образца подго-
тавливают так же, как и для микроисследования (шлифование, полирование,
травление). Четырехгранная алмазная пирамида (с углом при вершине 136°, та-
ким же как и у пирамиды при испытании по Виккерсу) вдавливается в испыты-
ваемый материал под очень небольшой нагрузкой 0,05-5 Н (5-50 гс). Число твердости определяется по формуле
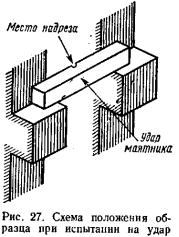
33
H=1,8544P/d2
где Р - нагрузка на пирамиду, Н (кгс); d - среднее арифметическое длины обеих диагоналей отпечатка по-
сле снятия нагрузки, мм.
Чтобы не вычислять твердость по приведенной выше формуле, пользуются специальными таблицами, в
которых для диагоналей отпечатков, определяемых в микронах, даны числа твердости (в Н/м2 или кгс/мм2).
Испытание на удар. Очень часто детали в процессе работы испытывают действие не только плавно возрастающих нагрузок,
но одновременно подвергаются и ударным (динамическим) нагрузкам.
Поэтому необходимо знать, насколько хорошо сопротивляется металл дейст-
вию на него этих нагрузок.
Испытание на удар проводится на специальном приборе, называемом ма-
ятниковым копром, изломом надрезанного образца, свободно установленного на две опоры копра (рис. 27), падающим с определенной высоты массивным маятником. Работа удара Л„ (в Дж или кгс-м), затраченная на излом образца,
определяется из разности энергии маятника в положении его до и после удара.
Ударная вязкость а„, т. е. работа, израсходованная на ударный излом образца,
отнесенная к площади поперечного сечения образца в месте надреза, определя-
ется по формуле aH = AH/F,
где F -площадь поперечного сечения образца в месте надреза, м2 (см2).
Определение ударной вязкости aH является наиболее простым и чувстви-
тельным способом оценки склонности некоторых металлов, имеющих объемноцентрированную кубическую решетку (например, железо (сталь), хром,
цинк и др.), к хрупкости при работе в условиях низких температур, называемой хладноломкостью.

34
Практически хладноломкость определяют при испытании на удар серии образцов при нескольких понижающихся температурах (от комнатной до - 100°
С). Результаты испытаний изображают в координатах «ударная вязкость - тем-
пература испытания» (рис. 28). Температура, при которой происходит переход металла
от вязкого разрушения к хрупкому, называется критической температурой хрупкости или порогом хладноломкости. Обычно на кривой испытания на-
блюдается переходная зона и поэтому различают верхнюю Тв и нижнюю ТН границы критического интервала (рис. 28). В этом интервале температур
ударная вязкость понижается и изменяется характер излома - от вязкого волок-
нистого до хрупкого кристаллического.
Обычно порогом хладноломкости считается средняя температура интер-
вала, но для деталей ответственного назначения берут верхнюю границу Тв, а
нередко принимают температуру, при которой в изломе появляются кристалли-
ческие участки, хотя ударная вязкость сохраняет еще высокое значение.
Испытание на усталость. Усталостью металла называют разрушение ме-
талла под действием повторных или знакопеременных напряжений. Свойство металла выдерживать большое число циклов переменных нагрузок, т. е. проти-
востоять усталости, называют выносливостью.
Цикл нагрузок может быть: а) симметричным, если напряжения противо-
положны по знаку и равны; б) асимметричным, если напряжения неодинаковы по величине (хотя и могут иметь одинаковый знак).
Повторно-переменным нагрузкам подвергаются в процессе работы раз-
личные детали: валы, шатуны, рессоры, пружины, рельсы, балки и т. п. Стати-
ческие испытания недостаточны для характеристики прочности материала,
подвергающегося в работе действию повторно-переменных усилий. Необходи-

35
мо определить предел выносливости, т. е. величину наибольшего напряжения,
которое металл способен выдержать без разрушения при заданном числе пере-
мен нагрузки (циклов). Для стали условно принято число перемен нагрузки = 5,
а для легких цветных сплавов = 20 миллионов циклов. Величина предела вы-
носливости зависит от ряда факторов - состояния поверхности, степени загряз-
ненности металла неметалическими включениями, структуры металла, формы и размеров образца, наклепа и др.
Разрушение при повторно-переменных нагрузках всегда происходит внезапно и при напряжениях значи-
тельно меньшей величины, чем разрушение при дейст-
вии однократной нагрузки.
Характерным является излом усталости (рис. 29), состоящий из двух разнородных по внешнему виду частей. Одна часть 1 с затертой поверхностью, получившейся вследствие тре-
ния поверхностей в области трещин, образовавшихся от действия повторно-
переменных нагрузок, и часть 2 с зернистым изломом, образовавшимся в мо-
мент разрушения детали.
Существующие ме-
тоды испытания металлов на усталость различают по характеру прилагаемой на-
грузки и по условиям про-
ведения испытания. Испы-
тания проводятся изгибом, растяжением - сжатием, кручением, при высоких и низких температурах, в условиях коррозии. Наиболее распространенным мето-
дом испытания является определение предела выносливости при изгибе вра-
щающегося образца по симметричному циклу (рис. 30). Результаты испытания фиксируются в виде диаграммы (рис. 31), на которой по оси абсцисс отклады-

36
ваются значения числа циклов N, а по оси ординат - напряжение (Н/м2 или кгс/мм2).

37
Г л а в а III
ТЕОРИЯ СПЛАВОВ
§ I. Основные сведения о сплавах
Чистые металлы в большинстве случаев не обеспечивают требуемого комплекса механических и технологических свойств и поэтому редко приме-
няются для изготовления изделий. Некоторое применение имеет, например,
медь, главным образом для изготовления проводников электричества. В боль-
шинстве случаев в технике применяют сплавы.
Металлическим сплавом называется вещество, состоящее из двух или бо-
лее элементов (металлов или металлов с металлоидами), обладающее металли-
ческими свойствами. Обычным способом приготовления сплавов является сплавление, но иногда применяют спекание, электролиз или возгонку.
В большинстве случаев входящие в сплав элементы в жидком состоянии полностью растворимы друг в друге, т. е. представляют собой жидкий раствор,
в котором атомы различных элементов более или менее равномерно перемеша-
ны друг с другом (рис. 32, а). В твердом виде сплавы способны образовывать твердые растворы, химические соединения, механические смеси (рис. 32, б, в,
г).
38
Твердый раствор. Во многих сплавах при переходе в твердое состояние
(при кристаллизации) сохраняется однородность распределения атомов различ-
ных элементов и, следовательно, сохраняется и растворимость. Образовавший-
ся в этом случае кристалл (зерно) называется твердым раствором.
Микроструктура твердого раствора в условиях равновесия представляет собой совершенно однородные и одинаковые по составу зерна и похожа на структуру чистого металла (рис. 32, б). Твердый раствор, как и чистый металл,
имеет одну кристаллическую решетку. Различие состоит только в том, что в кристаллической решетке чистого металла все узлы заняты атомами одного элемента, а в твердом растворе - атомами различных элементов, образующих этот твердый раствор.
Растворимость в твердом состоянии может быть неограниченной и огра-
ниченной. Растворимость твердого раствора, полученного при любом количе-
ственном соотношении элементов, называется неограниченной. Растворимость твердого раствора, полученного при определенном количественном соотноше-
нии элементов, называется ограниченной.
По расположению атомов в кристаллической решетке различают твердые растворы замещения и твердые растворы внедрения.
В твердом растворе замещения атомы растворенного элемента занимают узлы атомов элемента растворителя, т. е. расположены в узлах общей кристал-
лической решетки (рис. 33, a).
В твердом растворе внедрения атомы растворенного элемента располага-
ются внутри кристаллической решетки элемента растворителя между атомами металла-растворителя (рис. 33, б).
При образовании твердых растворов свойства сплавов изменяются плавно и отличаются от свойств элементов, из которых они состоят.
Химическое соединение. Особый характер металлической связи в сплавах приводит к образованию особого вида химических соединений. В отличие от

39
обычных химических соединений многие металлические соединения имеют пе-
менный состав, который может изменяться в широких пределах. Характерной особен-
ностью металлического химического со-
единения является образование кристалли-
ческой решетки (см. рис. 32, в), отличной от решеток образующих элементов, и су-
щественное изменение всех свойств. Иногда в металлических сплавах образу-
ются также химические соединения с нормальной валентностью, например ок-
сиды, сульфиды, а также соединения металлов с резко отличным электронным строением атомов (Mg2Sn, Mg2Pb и др.).
Механическая смесь. Если элементы, входящие в состав сплава не рас-
творяются друг в друге в твердом состоянии и не вступают в химическую реак-
цию с образованием соединения, то при этих условиях из атомов каждого эле-
мента образуется отдельная кристаллическая решетка, и кристаллы (зерна) эле-
ментов, входящие в сплав, образуют механическую смесь (см. рис. 32, г). При образовании механической смеси, когда каждый элемент кристаллизуется са-
мостоятельно, свойства сплава получаются средними между свойствами эле-
ментов, которые его образуют.
Механические смеси образуются также в случаях, когда элементы обла-
дают ограниченной растворимостью, а также когда образуют химическое со-
единение. Если в сплаве количество элементов превышает их предельную рас-
творимость, то возникает механическая смесь двух насыщенных твердых рас-
творов. При наличии в сплаве химического соединения образуется механиче-
ская смесь из зерен твердого раствора и химического соединения и т. д.
40
При изучении процессов, происходящих в металлах и сплавах пои их превращениях, и описании их строения в металловедении пользуются следую-
щими понятиями: система, фаза, компонент.
Системой называется совокупность фаз, находящихся в равновесии при определенных внешних условиях (температуре, давлении) Система может быть простой, если она состоит из одного элемента, и сложной, если она состоит из нескольких элементов.
Фазой называется однородная по химическому составу и кри-
сталлическому строению часть системы, отделенная от других частей системы поверхностью раздела. Фазами могут быть металлы и неметаллы, жидкие и твердые растворы, химические соединения. Однофазной системой является,
например, однородная жидкость, двухфазной - механическая смесь кристаллов двух металлов.
Компонентами называют вещества, образующие систему. Компонентами могут быть элементы (металлы и неметаллы) или устойчивые химические со-
единения.
§ 2. Диаграммы состояния двойных сплавов
Диаграмма состояния представляет собой графическое изображение фа-
зового состояния сплавов в зависимости от температуры и концентрации в ус-
ловиях равновесия.
Диаграмма состояния позволяет для конкретных сплавов проследить за превращениями, происходящими при их нагревании и охлаждении, определить температуру начала и конца плавления (затвердевания) сплава, выяснить будет ли сплав однородным, каковы его жидкотекучесть, пористость. Эти сведения необходимы при разработке литейной технологии. Сведения о структурных превращениях, их характере, структуре, получаемой в результате этих превра-
щений, температурах, при которых начинаются и заканчиваются эти превраще-
ния и т. п., необходимы при разработке технологии термической обработки де-