
Металловедение
.pdf231
уделяется стабилизации напряженного состояния, стабилизации мартенсита и остаточного аустенита. Это достигается соответствующим режимом низкого отпуска - при температуре 120-130° С в течение 12-50 ч и обработкой при тем-
пературах ниже нуля (до-60° С).
§ 3. Штамповые стали
Штамповые стали делят на стали для инструментов холодного и горячего деформирования.
Стали для инструментов холодного деформирования. Штампы неболь-
ших размеров (диаметром 25-30 мм), простой формы, работающие в легких ус-
ловиях, изготовляют из углеродистых сталей У10, УН, У12. Штампы диамет-
ром 75-100 мм более сложной формы и для более тяжелых условий работы из-
готовляют из сталей повышенной прокаливаемости X, ХВГ.
Для изготовления инструмента, который должен иметь высокую твер-
дость и повышенную износостойкость, а также малую деформируемость при закалке, применяют стали с высокой прокаливаемостью и износостойкостью,
например сталь Х12Ф1 (1,25- 1,45%С; 11-12,5% Сr; 0,7-0,9% V).
Сталь Х12Ф1 содержит большое количество хрома (12%) и относится к сталям карбидного класса. Характерным режимом термической обработки ста-
ли Х12Ф1 является обработка на минимальную деформацию (тепловая довод-
ка). При обработке на минимальную деформацию закалку проводят с темпера-
туры 1080-1100° С с охлаждением в масле или в соляной ванне с температурой
400-475° С, а затем на воздухе с получением минусовых размеров (за счет по-
вышенного количества остаточного аустенита). Для доводки до требуемых раз-
меров проводят одноили многократный отпуск при температуре 475-500° С, в
результате которого размеры увеличиваются и достигают заданных.
Для инструмента, подвергающегося в работе большим ударным нагруз-
кам (пневматические зубила, обжимки, ножницы при холодной резке металла),
применяют стали с меньшим содержанием углерода, повышенной вязкости
232
4ХС, 6ХС, 4ХВ2С и др. Эти стали закаливают в масле с температуры 840-900°
С (в зависимости от стали) и отпускают при температуре 240-270° С с получе-
нием твердости HRC50-55. Стали для инструментов горячего деформирования.
Химический состав некоторых сталей для штампов горячего деформирования приведен в табл. 14.
Таблица 14
Химический состав (%) некоторых штамповых сталей для горячего де-
формирования
Марка ста- |
Элементы |
|
|
Прочие |
|
|
ли |
С |
Сr |
W |
Мо |
элементы |
|
|
|
|
|
|
|
|
5ХНМ |
0,5-0,6 |
0,5-0,8 |
- |
0,15-0,3 |
1,4-1,8 |
Ni |
5ХГМ |
0,5-0,6 |
0,6-0,9 |
- |
0,15-0,3 |
1,2-1,6 |
Мп |
5ХНВ |
0,5-0,6 |
0,5-0,8 |
0,4-0,7 |
- |
1,4-1,8 |
Ni |
ЗХ2В8Ф |
0,3-0,4 |
2,2-2,7 |
7,5-8,5 |
- |
0,2-0,5 |
V |
5ХЗВЗМФС |
0,12- |
2,5-3,2 |
3-3,6 |
0,8-1,1 |
1,5-1,8 |
V |
|
0,52 |
|
|
|
0,5-0,8 Si |
Стали 5ХНМ, 5ХГМ, 5ХНВ, применяемые для изготовления молотовых штампов, содержат одинаковое количество (0,5-0,6%) углерода и легированы хромом. Такое содержание углерода позволяет получить достаточно высокую ударную вязкость, а хром повышает прочность и увеличивает прокаливаемость.
Никель вводят в эти стали с целью повышения вязкости и улучшения прокали-
ваемости. Вольфрам и молибден повышают твердость и теплостойкость,
уменьшают отпускную хрупкость, измельчают зерно и уменьшают склонность стали к перегреву. Марганец, как более дешевый легирующий элемент, являет-
ся заменителем никеля.
Для сталей молотовых штампов характерна глубокая прокаливаемость,
например стали 5ХНМ и 5ХГМ прокаливаются в сечениях до 200-300 мм.
Температура закалки 820-860° С. Температура отпуска 500580° С и твердость после отпуска HRC35-45 зависят от стали и размера штампа.
Стали ЗХ2В8Ф, 5ХЗВЗМФС и другие применяют для вытяжных и выса-
дочных штампов, а также пресс-форм для литья под давлением. К этим сталям
233
предъявляют повышенные требования по теплостойкости и разгаростойкости и меньшие требования по прокаливаемости.
Для растворения сложных карбидов эти стали при закалке нагревают до высоких температур (1050-1100° С) и охлаждают в масле. Затем проводят от-
пуск при температуре 560-650° С. Твердость после термической обработки
HRC45-50.
§ 4. Инструментальные спеченные твердые сплавы
Эти сплавы состоят в основном из карбида вольфрама WC. Твердость карбида вольфрама очень высокая, но в то же время он очень хрупкий. Для применения карбида вольфрама в качестве материала для режущих инструмен-
тов порошок карбида вольфрама прессуют и спекают при высокой температуре
(1400° С) с порошком кобальта; при этом кобальт является пластичной связкой для карбида вольфрама.
Вольфрамокобальтовые твердые сплавы усовершенствованы введением в
них карбида титана TiC и карбида тантала ТаС.
Вольфрамотитанокобальтовые твердые сплавы получают прессованием и спеканием порошков карбида вольфрама, карбида титана и кобальта. Высокие твердость [HRA85-90 (HRC66-76)] и теплостойкость (до 900-1000° С) этих сплавов позволили значительно увеличить скорости резания.
Так как спеченные твердые сплавы содержат дорогостоящие элементы -
вольфрам, титан, кобальт, - они очень дороги. В целях экономии спеченные твердые сплавы изготовляют в виде пластин. Пластины в качестве режущей части инструмента напаивают (обычно медью) на державку из углеродистой стали.
Спеченные твердые сплавы делят на три группы: вольфрамокобальтовые группы ВК [например, ВК2 (98 % WC и 2% Со), ВК8 (92% WC и 8% Со)] для обработки чугуна, цветных металлов и сплавов, неметаллических материалов;
вольфрамотитанокобальтовые группы ТК [например, Т5К10 (85% WC, 5% TiC,
234
10% Со), Т30К.4 (66% WC, 30% TiC, 4% Со)] и вольфрамотитанотанталоко-
бальтовые группы ТТК [сплав ТТ7К12 (81% WC, 4% TiC, 3% ТаС, 12% Со] для обработки стали.
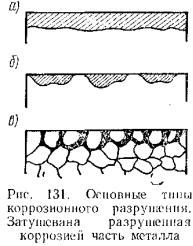
235
Глава XIV
СТАЛИ И СПЛАВЫ С ОСОБЫМИ СВОЙСТВАМИ
Как указано в классификации сталей по применению, к этой группе отно-
сят стали с особыми химическими свойствами (нержавеющие стали) и с особы-
ми физическими свойствами (магнитные, с малым и заданным коэффициентом расширения и др.).
Рассмотрим стали с особыми химическими свойствами.
§ 1. Нержавеющие (коррозионностойкие) стали
Нержавеющими сталями называют стали, обладающие стойкостью против электрохимической коррозии. Рассмотрим процесс коррозии и методы защиты деталей от коррозии.
Коррозия металлов. Коррозией называют разрушение металла вследст-
вие химического или электрохимического взаимодействия его с внешней сре-
дой. Коррозия приводит к невозвратимой потере металла и приносит огромные убытки. Поэтому изучение коррозии и ее предотвращение является очень важ-
ной задачей для промышленности.
В зависимости от воздействующей среды коррозию подразделяют на ат-
мосферную, жидкостную и газовую.
По характеру и месту распределения коррозия может быть равномерная
(рис. 131, а), местная (рис. 131, б) и межкристаллитная (рис. 131, в).
Теория коррозии. Коррозия начинается с по-
верхности на границе двух фаз металл - внешняя среда и с течением времени распространяется вглубь металла. По характеру физико-химических процессов, происходящих между металлом и сре-
дой, различают два вида коррозии - химическую и электрохимическую.
Химическая коррозия возникает в результате
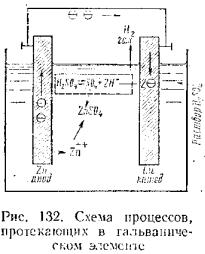
236
химического воздействия на поверхность металла внешней среды. Химическая коррозия возникает при образовании, например, на металле слоя окислов в пе-
чах при высоких температурах.
Электрохимическая коррозия возникает при действии на металл электро-
литов. Этот вид коррозии является наиболее распространенным. Большинство металлических конструкций в процессе эксплуатации находится в соприкосно-
вении с воздухом - каркасы зданий, фермы мостов, крыши зданий, различные механизмы и т. п.
Так как в воздухе находятся водяные пары, то поверхность конструкций покрывается влагой. Кроме того, воздух часто загрязнен углекислотой, серни-
стым газом и другими примесями, которые растворяются в капельках влаги, по-
этому поверхность конструкций покрывается влагой, насыщенной солями, ще-
лочами и кислотами, т. е. тонким слоем электролита, в связи с чем и возникает электрохимическая коррозия.
Электрохимической коррозии подвергаются также изделия, находящиеся в почве, - различные трубопроводы, кабели и т. п.
Процесс электрохимической коррозии протекает более сложно по срав-
нению с химической коррозией. Если два различных металла (например, цинк и медь) помещены в электролит (например, рас-
твор серной кислоты) и соединены проводни-
ком, т. е. создан гальванический элемент (рис. 132), то разрушается за счет перехода положи-
тельно заряженных ионов металла в электролит тот металл, который имеет более низкий (отри-
цательный) электродный потенциал, в данном случае цинк. Освободившиеся в цинке электро-
ны текут по внешнему проводнику к меди.
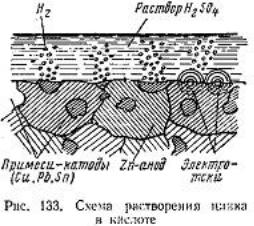
237
Металл с более высоким (положительным) электродным потенциалом
(медь) притягивает к себе положительно заряженные ионы водорода электро-
лита. Электроны меди соединяются с ионами водорода и нейтрализует их.
Таким образом, в гальваническом элементе металл, являющийся анодом
(цинк), разрушается, а металл, являющийся катодом (медь), остается нетрону-
тым и служит только местом разряда (нейтрализации) положительно заряжен-
ных ионов электролита.
Коррозия металлов и сплавов в электролите протекает так же, как работа-
ет гальванический элемент. Это объясняется тем, что металлы и сплавы неодно-
родны по химическому составу и представляют собой совокупность различных структурных составляющих: твердого раствора, эвтектики, химических соеди-
нений. Эти различные структурные составляющие имеют различные электрод-
ные потенциалы. Поэтому при погружении сплава в электролит одни участки сплава, имеющие более низкий потенциал, являются анодами и разрушаются, а
другие участки с высоким потенциалом являются катодами и сохраняются не-
изменными (рис. 133). Так как анодных и катодных участков в сплаве очень много, то сплав можно рассматривать состоящим из большого числа электро-
дов, т. е. как многоэлектродный микроэлемент.
Если сплав представляет собой микроэлемент, то при погружении в элек-
тролит двух различных находящихся в контакте между собой металлов или сплавов
образуется так называемый ма-
кроэлемент. Такие случаи часто наблюда-
ются в конструкциях, например в склепан-
ных листах, частях деталей, скрепленных болтами и т. д.
Методы защиты от коррозии. От коррозии металл может быть защищен: ле-
238
гированием; неметаллическими пленками; металлическими покрытиями; неме-
таллическими покрытиями; протекторами; обработкой коррозионной среды.
Защита легированием. Коррозионную стойкость металла можно повысить сплавлением его с другими металлами, т. е. получением сталей, стойких против коррозии.
Защита неметаллическими пленками. Неметаллические пленки получают оксидированием (окисные пленки) и фосфатированием (фосфатные пленки).
При оксидировании окисные пленки получают кипячением деталей в водном растворе, содержащем сильный окислитель, например в растворе с ед-
ким натром. В результате оксидирования детали приобретают красивый внеш-
ний вид (синий или черный цвет), в связи с чем этот процесс иначе называют воронением.
Сущность процесса фосфатирования заключается в обработке деталей в ваннах, содержащих различные, довольно сложные по составу смеси фосфор-
ной кислоты и ее солей, главным образом железных и марганцевых, в результа-
те которой на поверхности металла образуется пленка нерастворимых в воде фосфорнокислых соединений марганца и железа.
Защита металлическими покрытиями. Для покрытия деталей применяют металлы: цинк (цинкование), кадмий (кадмирование), алюминий (алитирова-
ние), олово (лужение), свинец (свинцевание), никель (никелирование), хром
(хромирование), медь (меднение), а также сплавы: латунь и бронзу.
Нанесение металла на поверхность детали может осуществляться различ-
ными методами: путем погружения в расплавленный металл, диффузионным методом, путем распыления, методом плакирования, гальваническим путем и т.д.
Для нанесения покрытия путем погружения детали в расплавленный ме-
талл применяют металлы, имеющие невысокую температуру плавления: цинк,
олово, свинец. При покрытии деталь на некоторое время погружают в расплав-
239
ленный металл, затем вынимают и охлаждают на воздухе. В результате такой обработки поверхность детали покрывается защитным слоем металла.
При диффузионном методе покрытие получается за счет диффузии ато-
мов металла из внешней среды в поверхность детали, насыщения поверхност-
ного слоя детали атомами металлов и химического взаимодействия с ним с об-
разованием устойчивых против коррозии соединений.
В промышленности получили применение следующие виды диф-
фузионных покрытий: азотирование, алитирование, хромирование и силициро-
вание, описание которых дано в гл. IX.
Получение гальванических покрытий основано на электролизе водных растворов солей того металла, который служит для покрытия. Преимуществом гальванического метода по сравнению с покрытием путем погружения детали в расплавленный металл является легкая управляемость процессом, экономное расходование металла покрытия, отсутствие нагрева.
В промышленности применяют следующие виды гальванических покры-
тий: цинкование; кадмирование; лужение; никелирование; меднение; хромиро-
вание; свинцевание.
Если металл покрытия, например цинк, имеет электродный потенциал более низкий (более отрицательный), чем у железа, то он предохраняет железо не только механически, но и электрохимически. Такое покрытие называется
анодным.
Если металл покрытия, например олово, хром, имеет более поло-
жительный потенциал, чем железо, то он защищает железо только механически и поэтому в случае повреждения происходит разрушение основного металла.
Такое покрытие называется катодным.
Покрытие путем распыления заключается в том, что расплавленный ме-
талл, например цинк, кадмий, распыляют сжатым воздухом и набрызгивают на
240
поверхность детали. Этот метод целесообразно применять для покрытия круп-
ных деталей, которые трудно обрабатывать другими методами.
Покрытие методом плакирования получается прокатной заготовки с на-
ложенными на нее листами другого металла, в результате чего получается би-
металл. Так как соединение заготовки с листом происходит при нагреве и под давлением, то получается хорошее, прочное их сцепление. Практически железо плакируют медью, нержавеющей сталью; дуралюмин плакируют чистым алю-
минием.
Защита протекторами. Сущность этого метода заключается в том, что к защищаемой детали, находящейся в электролите, присоединяется металл с бо-
лее низким электрохимическим потенциалом, чем потенциал металла детали.
Присоединяемый металл, называемый протектором, является анодом и разру-
шается, а деталь является катодом и коррозии не подвергается. В качестве про-
тектора для стальных конструкций обычно применяют цинк.
Защита неметаллическими покрытиями. Этот метод заключается в механи-
ческом нанесении на поверхность металла красок и лаков. Широкое примене-
ние лакокрасочных покрытий объясняется тем, что они дешевы, не требуют расхода цветных металлов и применяются для защиты от коррозии любых кон-
струкций.
Недостатком лакокрасочных покрытий является их способность растрес-
киваться и пропускать влагу.
Наиболее распространенными красками являются масляные и эмалевые.
Защита обработкой коррозионной среды. Этот метод защиты заключается
в введении в коррозионную среду веществ, замедляющих коррозию. Такие ве-
щества называются ингибиторами. Например, добавка в воду в охладительной системе двигателя внутреннего сгорания небольшого количества (2-3 г/л)
хромпика практически устраняет коррозию.