
Збірник 04
.pdf
ПЕРСПЕКТИВНІ ТЕХНОЛОГІЇ ТА ПРИЛАДИ
вирішення якої неможливе без обґрунтованого вибору розрахункової моделі та методів її дослідження.
Виклад основного матеріалу дослідження. В теорії поверхневого пластичного деформування (ППД) прийнято використовувати два методи дослідження напруженого стану: метод ліній ковзання та метод кінцевих елементів. Розглянемо метод ліній ковзання [4]. Він дозволяє не тільки обраховувати зусилля необхідні для деформації, але і повністю визначати поля напружень та швидкості їх розповсюдження в перерізах деформованого матеріалу, також за допомогою цього методу можна аналізувати локальні явища, які зазвичай є основними при вирішенні задач проектування технологічних операцій ППД. Існуючі аналітичні рівняння для реалізації методу ліній ковзання являються складними математичними задачами, тому в теорії оброблення металу тиском використовуються в основному графічні методи побудови ліній ковзання. При цьому в якості граничних умов для напружень використовуються умови якими володіє передня безконтактна межа ОД, тобто профіль який не відповідає реальному профілю хвилі деформації. Реальний профіль ОД в процесі ППД вигладжування виникає під впливом двох технологічних рухів: обертання деталі (n) та подачі (S).
Оскільки метод ліній ковзання дозволяє вирішувати задачі в площинній проекції, то важливим чинником є вибір головної площини, тобто площини перпендикулярної до осі якої відсутні деформації. Назвемо осьовий переріз заготовки – площиною подач, а тангенціальний переріз, який перпендикулярний до його осі, площиною частот. Співвідношення складових тензора швидкості деформації по вказаних площинах в теорії ППД досліджено на недостатньому рівні. Під час досліджень виявлено ряд ознак, які дозволяють обирати головну площину заготовки в ході зміцнювально-вигладжувального оброблення. До них відносяться: 1) залишкові осьові напруження в 1,5…2 рази більші, ніж тангенціальні; 2) пластична хвиля, що виникає перед інструментом має кільцеву форму, та переміщується в напрямку подачі; 3) висота хвилі в напрямку вектора частоти обертання заготовки (n) значно менша, ніж в напрямку вектора подачі (S). Таким чином, введено припущення, що поле напруження в рамках плоско деформованого стану потрібно будувати в площині вектора подач (S). Розглянемо приклад такого рівняння.
Поле напружень утворюється двома ортогональними групами ліній ковзання (рис. 1), які в кожній точці своєї дотичної площини мають максимальне значення напруження. Лінія першої групи (α-лінія) відхиляється вправо на кут π/4 від напряму зони напружень першого роду σ1, а β-лінія відхиляється вліво на аналогічний кут. Кут нахилу дотичної до α-лінії відраховується в додатному напрямку від осі абсцис, яку на (рис. 1) позначено θ.
Рис. 1. Графічна інтерпретація ортогональних |
Рис. 2. Статистично можливе поле напружень в |
груп ліній ковзання |
процесі ППД |
Під час дослідження плоско-пластичного потоку, в якому деформація в напрямку осі z рівна нулю, напруження σz, буде одним із головних напружень, тобто: z 0, де 0,5 z .
Пластична плинність матеріалу характеризується: |
|
|
|
|
|
||||
а) умовами рівноваги |
|
|
|
|
|
|
|
|
|
|
|
x |
xy |
0; |
xy |
|
|
x |
0; |
|
x |
y |
x |
y |
|
||||
|
|
|
|
|
(1) |
||||
|
|
|
|
|
|
|
|
|
|
б) умовою пластичності |
x y 2 4 xy |
|
|
|
|
|
|||
|
4k 2 |
|
|
(2) |
|||||
|
|
|
|
|
|
; |
|
|
|
|
|
101 |
|
|
|
|
|
|
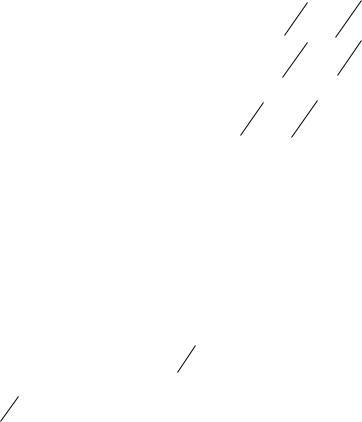
ПЕРСПЕКТИВНІ ТЕХНОЛОГІЇ ТА ПРИЛАДИ
в) умовою співвісності напружень та швидкостей деформації
|
|
|
|
|
|
|
vx |
|
|
vy |
y |
|
|||
|
|
|
|
|
|
|
|
|
|
|
|||||
|
x |
x |
|
|
|
|
|
x |
|
; |
|||||
|
|
2 |
xy |
|
|
v |
x |
|
|
vy |
|
||||
|
|
|
|
|
|
|
|
||||||||
|
|
|
|
|
|
|
|
|
y |
|
x |
|
|||
|
|
|
|
|
|
|
|
|
|
|
|
|
|||
|
г) умовою нестискання |
|
|
|
|
|
|
|
|
|
|
|
|
|
|
|
|
|
vx |
x |
|
vy |
y |
0; |
|
||||||
|
|
|
|
|
|
|
|
|
|||||||
|
|
|
|
|
|
|
|
|
|
|
|
|
|||
де x |
та y – нормальні складові напруження; |
|
xy – дотичні складові напруження; k –постійна |
пластичної деформації; vx, vy – складові швидкостей деформації; x, y – координати характерних точок.
Рівняння (2) справедливе, якщо система рівнянь складових напружень має наступний вигляд:
|
|
|
|
|
|
|
|
y |
k sin 2 ; |
|
|||
|
|
|
|
|
|
|
|
|
k sin 2 ; |
|
|||
|
|
|
|
|
|
|
|
|
|
||||
|
|
|
|
|
|
|
|
x |
k cos 2 . |
|
|
||
|
|
|
|
|
|
|
|
|
|
|
|||
|
|
|
|
|
|
|
|
xy |
|
|
|
|
(3) |
|
|
|
|
|
|
|
|
|
|
|
|
|
|
Рівняння (1) та (3) зводяться до системи двох нелінійних диференціальних рівнянь, які |
|||||||||||||
характеризують обидві групи ліній ковзання: |
|
|
|
|
|
||||||||
|
|
|
|
|
|
|
|
|
|
sin 2 |
|
0 ; |
|
|
|
|
|
|
2k cos 2 |
|
|
||||||
|
|
|
|
|
|
x |
|
|
|
x |
|
|
|
|
|
|
|
|
|
|
|
|
|
y |
|
||
|
|
|
|
cos 2 |
|
0 . |
|
|
|
|
|
||
|
2k sin 2 |
|
|
|
|
|
|
|
|
||||
|
x |
|
x |
|
|
|
|
|
|
|
|
|
|
|
|
|
y |
|
|
|
|
|
|
Ці рівняння доцільно зводити до співвідношень Генкі:
y |
|
tg ; |
y |
|
сtg ; |
|||
|
x |
|
x |
|||||
|
|
|
|
|||||
лінія |
|
|
лінія |
|
|
|||
|
|
|
|
|
|
|||
|
|
const . |
|
|
const . |
|||
|
|
|
|
|||||
|
|
|
|
|
|
|||
2k |
|
|
2k |
(4) |
||||
|
|
|
|
|
|
Рівняння (4) вказують на те, що в будь-якій точці поля напружень відомі параметри ξ і η, а в загальному полі напруження можна визначити значення σ. Таким чином, дане рівняння зводиться до ряду простих задач, які задовольняються тими чи іншими граничними умовами.
Розглянемо розв’язання такої задачі застосованої до процесу поверхневого пластичного деформування заготовки із матеріалу ШХ15 ГОСТ 2591-2006.
На першому етапі обмежимося побудовою статично можливого поля напружень, яке виникає в площині подачі інструменту (S) в процесі вигладжування циліндричної заготовки індентором, який має профільний радіус Rпр (рис. 2).
Статичним вважають поле напружень, яке можливо побудувати незалежно від поля швидкостей зміцнення.
В ході оброблення попереду інструменту, який має в площині подачі профільний радіус Rпр виникає хвиля, безконтактний профіль якої зображено лінією 0,0 – 11,11. Точка 0,0 визначає межу осередку деформації металу попереду інструменту. Точки 11,11 (та співпадаюча з нею точка 11,17) і 0,28 – крайні точки дуги контакту. Граничні умови для напружень в будь-якому контурі визначаються як:
0,5arccos kn m ;
n k sin 2 ,
де ψ – кут між нормаллю до контуру і віссю x; σn, τn – нормальна та дотична складові напружень відповідно; m – ціле число.
Наявність двох варіантів розв’язання для значень σ і θ, що задовольняють умову плинності, пояснюється квадратичним характером останнього. Для вибору знака, який характеризує напруження, необхідно додаткові умови, які вказуються в процесі постановки задачі.
102

ПЕРСПЕКТИВНІ ТЕХНОЛОГІЇ ТА ПРИЛАДИ
З рівняння (3) справедливим буде висновок, що поле напружень біля межі ОД, вільної від дії сили, визначається тільки формою цієї межі. Так як на відрізку 0,0 – 11,11 напруження σn=τn=0, то з
(3) стає очевидним, що на ньому k, 4. Знак «-» перед k взято з механічних міркувань, оскільки вздовж лінії 0,0 – 11,11 відбувається стискання. Ця умова являється першою граничною умовою для напружень стиску. Отже, α та β-лінії підходять до вільної межі 0,0 – 11,1 під кутом π/4.
Використовуючи цю граничну умову, в області 0,0 – 11,7 – 0,11 та розв’язавши задачу Коші, можна визначити значення x, y, σ, θ у вузлах сітки ліній ковзання. В області 0,11 – 11,11 – 11,17 – 0,17 лінії ковзання утворюють відцентровий сегмент, всередині якого значення x, y, σ, θ у вузлах сітки визначаються розв’язками окремого випадку початкової характеристики задачі. Кут φ при вершині сегмента залежить від кута γ між β-лінією 11,17 – 0,17 та профільним радіусом інструменту Rпр:
0,5arccos 2 , |
(6) |
де µ – коефіцієнт тертя між інструментом та матеріалом |
що деформується. Відповідно, |
|
3 |
, |
|
4 |
|||
|
(λ – кут між відрізком 0,0 – 11,11 та профільним радіусом індентора Rпр в точці |
||
|
|
||
1,11). |
|
Рівняння (6) є другою граничною умовою. Область 0,17 – 11,17 – 0,28 являється областю змішаних граничних умов. З однієї сторони, її визначають умови на відрізку 11,17 – 0,17, а з іншої – умови на межі профільного радіусу інструменту, які характеризуються рівнянням (6). Значення x, y, σ, θ у вузлах сітки в області 0,17 – 11,17 – 0,28 визначаються розв’язком змішаної задачі. Напруження в будь-якій точці поля у відповідності з рівнянням (6) визначаються кутом повороту α-лінії під час руху від вільної межі до профільного радіусу інструменту (наприклад, від точки 2,2 до точки 2,26). Характер розподілу головних напружень та епюра контактних напружень показані на рис. 3.
Рис. 3. Розподіл та епюр головних контактних напружень в зоні контакту «індентор-заготовка»
Повертаючись до аналізу результатів розрахунків нормальних напружень σn на відрізку де контактують інструмент та заготовка, для зручності аналізу виразимо їх як межу плинності матеріалу при зсуві k. Як видно з рис. 2, контактні напруження під час вирішення задачі пластичності змінюються в межах від 4,99 до 5,19k. Проте контактні напруження при вирішенні пружної задачі розподіляються по еліптичному контуру, тобто мають принципово інший характер. Внаслідок такого розподілу виникає питання, як кількісно визначити величину k, зважаючи на те що, в ході ППД
відбувається зміцнення металу. Припустимо що, k HB5,22 H 5,31 (Hμ – мікротвердість по Мейеру).
Справедливим буде твердження, що середнє напруження в зоні контакту інструменту та заготовки під час ППД буде рівним мікротвердості Hμ. Ці значення для операції вигладжування циліндричних поверхонь з матеріалу (сталь ШХ15) індентором з профільним радіусом Rпр=2,5 мм наведено в табл. 1.
Таблиця 1
Значення середнього напруження σn сер в зоні контакту інструменту та заготовки
Радіальне навантаження Py, Н |
50 |
100 |
150 |
200 |
250 |
300 |
350 |
Площа контакту F, мм2 |
0,44 |
0,55 |
0,85 |
1,1 |
1,47 |
1,86 |
2,32 |
Середнє напруження σn сер, Н/мм2 |
1,81 |
1,81 |
1,76 |
1,81 |
1,70 |
1,72 |
1,72 |
103
ПЕРСПЕКТИВНІ ТЕХНОЛОГІЇ ТА ПРИЛАДИ
З табл. 1 очевидно, що значення σn сер мало залежать від силового режиму вигладжування і співпадає з величиною Hμ для досліджуваного матеріалу. Обґрунтування цієї залежності виходить з результатів, що отримані під час виконання операцій ППД, які здійснювалась в діапазоні сил Py=200…250 H, які відповідають оптимальній інтенсивності деформації. Отже в першому наближенні для визначення сили вигладжування Py розрахункова схема може базуватись на гіпотезі про ідеально пластичне тіло та лінії ковзання. Отримання більш точного значення σn сер з метою більш точного розрахунку радіальної сили вигладжування Py з практичної точки зору недоцільне, тому що, виникають великі похибки під час визначення площі контакту F.
Виновок. Важливим науковим та практичним результатом є виявлення залежності між головною силою вигладжування Py та середніми напруженнями стиску σn сер і мікротвердістю Hμ поверхневого шару, що відкриває нові можливості для створення методик прогнозування експлуатаційних властивостей поверхневого шару в залежності від силового режиму зміцнювальновигладжувальної операції.
Інформаційні джерела
1.Балтер М.А. Упрочнение деталей машин / Балтер М.А. - М.: Машиностроение, 1978. - 184с.
2.Демкин Н.Б. Контактирование шероховатых поверхностей. - М.: «Наука», 1969 - 227 с.
3.Смелянский В.М. Механика упрочнения деталей поверхностным пластическим деформированием. - М.: Машиностроение, 2002. - 300с.
4.Томленов А.Д. Теория пластических деформаций металлов. - М.: Металлургия, 1972 - 408 с.
УДК 621.9.048
В.П. Симонюк, О.В. Шокун Луцький національний технічний університет
МУФТИ В ПРИЛАДОБУДУВАННІ
Наведено основні типи муфт, їх різновиди та характеристики, описано їхні переваги та недоліки, особливості при застосуванні в приладобудуванні.
Приведены основные типы муфт, их разновидности и характеристики, позитивные и негативные их стороны, особенности при использовании в приборостроении.
The main types of couplings, their varieties and characteristics, their positive and negative sides, especially when used in the instrument are described.
Ключові слова: Муфта, механізм, напiвмуфта, пристрій, з’єднання.
Муфтою називається пристрій для з'єднання кінців валів або для з'єднання валів з вільно розміщеними на них деталями (зубчасті колеса, зірочки і т.д.). Муфти призначені для передачі обертаючого моменту без зміни його значення і напрямку. У ряді випадків муфти додатково поглинають вібрації і поштовхи, охороняють прилад від аварій при перевантаженнях, а також використовуються для вмикання і вимикання робочого механізму машини без зупинки двигуна.
Різноманіття вимог, пропонованих до муфт, і різні умови їхньої роботи обумовили створення великої кількості конструкцій муфт, що класифікують за різними ознаками на групи:
- за принципом дії:
постійні муфти, що здійснюють постійне з'єднання валів між собою; зчіпні муфти, що допускають зчеплення і розчеплення валів під час роботи;
самокеровані муфти, що автоматично роз'єднують вали при зміні заданого режиму роботи машини;
- за характером роботи:
тверді муфти, що передають разом із обертаючим моментом вібрації, поштовхи та удари; пружні муфти, що амортизують вібрації, поштовхи та удари при передачі обертаючого моменту
завдяки наявності пружних елементів - різних пружин, гумових втулок та ін.
У приладобудуванні, як і у машинобудуванні використовують муфти дуже різноманітних конструкцій. Найбільш часто вживані муфти стандартизовані.
104

ПЕРСПЕКТИВНІ ТЕХНОЛОГІЇ ТА ПРИЛАДИ
Важливими показниками конструкцій муфт є частота обертання, габаритні розміри, маса і момент інерції. Стандартні муфти не розраховують, а підбирають за обертальним. Лише в деяких випадках у разі потреби виконують перевірочні розрахунки.
Глухі муфти з'єднують співвісні вали в одну лінію. Вони відносяться до постійних муфт та застосовуються в тихохідних приводах. З різних видів глухих муфт найбільше поширення одержали втулкові та фланцеві муфти.
Рис. 1. Втулкова муфта |
Рис.2 Фланцева муфта |
Рис.3 Неточності монтажу валів |
Втулкова муфта – найпростіша з глухих муфт, суцільна і насаджується на кінці валів (рис. 1), які підлягають з'єднанню. З'єднання суцільної втулки з валами може здійснюватись за допомогою штифтів, шпонок або за допомогою шліців. При монтажі або демонтажі муфти виникає потреба у відносному осьовому зміщенні валів. Тому для втулкових муфт не використовують посадки з гарантованим натягом.
Штифти для з’єднання втулки з валами виготовляють із сталей 45, 50.
Міцність муфти визначається міцністю її з'єднання з валами, а також міцністю самої втулки. Фланцеві муфти складаються з двох напівмуфт із фланцями, стягнутими болтами (рис.2),
причому половина болтів установлена з зазором, а інша — без зазору.
Фланцеві муфти призначені для жорсткого з'єднання двох співвісних валів утворюючи при цьому один вал. Для того щоб цей складений вал залишався прямолінійним, необхідна чітка співвісність його частин і пригонка напівмуфт, так як є ймовірність вигину вала, його биття, створення вібрацій та поява додаткових навантажень на опори.
Фланцеві муфти прості по конструкції, надійні в роботі, можуть передавати великі моменти. Вони широко поширені в машинобудуванні. В приладобудуванні, хоча і використовуються, широкого розповсюдження не знайшли.
Компенсаційні тверді муфти відносяться до постійних муфт і призначені для з'єднання валів з компенсацією радіальних (рис.3, а), осьових (рис.3,б) та кутових (рис.3, в) зсувів унаслідок неточності виготовлення і монтажу.
Компенсація відхилень від співвісності валів досягається за рахунок рухливості твердих деталей муфти. Ці муфти зменшують додаткові навантаження на вали і підшипники, викликані відхиленнями від співвісності валів. Найбільше поширення з групи компенсаційних муфт одержали зубчасті та ланцюгові.
Зубчаста муфта (рис.4) складається з двох обойм 1 із внутрішніми зубами евольвентного профілю, що зчіплюються з зубами втулок 2, посаджених на кінці валів. Обойми з'єднані між собою болтами, вставленими в отвори без зазору.
Зубчасті муфти компенсують радіальні, осьові і кутові зсуви валів за рахунок бічних зазорів у зачепленні та виготовлення зубів втулок сферичними. Компенсація відхилень від співвісності валів супроводжується ковзанням зубів.
Рис.4. Зубчаста муфта: 1-обойма; 2-втулка |
Рис.5 Ланцюгова муфта |
Зубчасті муфти широко застосовуються для з'єднання горизонтальних важконавантажених валів. Ці муфти надійні в роботі, мають невеликі габарити. При роботі зуби отримують перемінні контактні напруження і напруження згину. Зубчасті муфти підбирають по більшому діаметру кінців з’єднаних валів.
105

ПЕРСПЕКТИВНІ ТЕХНОЛОГІЇ ТА ПРИЛАДИ
Ланцюгова муфта складається з двох напівмуфт-зірочок, що мають однакове число зубів (рис.5), охоплених загальним ланцюгом та захисним кожухом. Застосовуються ланцюги роликові однорядні й двохрядні, а також зубчасті.
Перевага ланцюгових муфт полягає в простоті конструкції та обслуговування, відносно невеликі габарити. При монтажі й демонтажі не потрібно осьового зсуву вузлів.
Через наявність зазорів у шарнірах ланцюга й у з’єднанні його із зірочками ланцюгові муфти мають значні люфти. Тому їх не застосовують у реверсивних приводах (реверс буде супроводжуватись ударами).
Компенсаційні тверді муфти в приладобудуванні використовують рідко. Основна причина цьому полягає в їхній інерційності.
Пружні муфти відносяться до постійних муфт. Основна частина цих муфт - пружний елемент який передає обертаючий момент від однієї напівмуфти до іншої.
Пружні муфти, що пом'якшують поштовхи й удари служать засобом захисту від резонансних крутильних коливань, що виникають унаслідок нерівномірного обертання; допускають порівняно великі зміщення осей з’єднаних валів.
|
Рис.7. Основні типи металічних пружних |
|
елементів муфт: а- циліндричні пружини; б- |
Рис.6 Основні типи гумових пружних елементів |
змієподібні пластинчасті пружини; в— стрижні, |
муфт |
пластини і пакети пластин, розташовані по |
|
утворюючій і по радіусу; г — пакети розрізних |
|
гільзових пружин |
Основною характеристикою пружних муфт є твердість або (зворотна їй величина) податливість та здатність демпфірування, тобто здатність перетворювати в теплоту енергію при деформації пружних елементів муфти.
За конструкцією пружні муфти різноманітні. По матеріалу пружних елементів вони поділяються на дві групи: муфти з неметалічними пружними елементами (зазвичай гумовими) (рис.6) і муфти з металевими пружними елементами (рис.7).
Муфта пружна втулково-пальцева (МПВП) складається з двох дискових напівмуфт (рис.8), в одній з яких у конічних отворах закріплені з’єднувальнi пальці з надягнутими гофрованими гумовими втулками.
Унаслідок невеликої товщини гумових втулок муфта має малу податливість, компенсуючи незначні зсуви валів. Радіальний і кутовий зсуви валів знижують довговічність гумових втулок, навантажуючи вали додатковою радіальною згинаючою силою
Робота муфти супроводжується втратами, що оцінюються к.к.д. η = 0,95...0,97.
Рис.8. Муфта пружна втулково-пальцева
106

ПЕРСПЕКТИВНІ ТЕХНОЛОГІЇ ТА ПРИЛАДИ
Муфта МПВП широко застосовується для з'єднання машин з електродвигунами при передачі малих і середніх обертаючих моментів. Вона проста у виготовленні. Зовнішня поверхня напівмуфт може використовуватися як гальмівний барабан. Муфту підбирають по стандарту. В приладобудуванні застосовуються рідко.
Зчіпні (керовані) муфти служать для швидкого з'єднання і роз'єднання валів при працюючому двигуні. Застосовуються при чіткій співвісності валів. За принципом роботи поділяються на кулачкові та фрикційні. Усі зчіпні муфти повинні легко і швидко включатися при незначній силі, а також мати незначне нагрівання і невелике спрацювання при частих перемиканнях.
Кулачкові муфти складаються з двох напівмуфт із кулачками на торцевих поверхнях (рис.9). При включенні кулачки однієї напівмуфти входять у западини іншої, створюючи тверде зчеплення. При переключенні муфти одна напівмуфта пересувається уздовж вала по напрямній шпонці або шліцах за допомогою механізму керування муфтою.
Рис.9. Кулачкова муфта
Основні елементи муфт - кулачки різних профілів (рис.10): прямокутного (а), трапецеїдального (б), трикутного (в) відповідно для великих, середніх і малих навантажень. Асиметричний профіль кулачків (рис.10, г) застосовують у нереверсивних механізмах для полегшення включення муфти. Число кулачків приймають Z = 3...60 у залежності від значення обертаючого моменту Т і бажаного часу включення, зі збільшенням якого Z зменшується.
Рис.10. Профілі кулачків муфт зчеплення
Недоліком кулачкових муфт є неможливість включення на швидкому ходу. Кулачкові муфти прості у виготовленні і малогабаритні. Застосовуються в механізмах, де повинно бути забезпечене постійне передаточне число, а також при передачі великих обертаючих моментів.
Фрикційна муфта - це керована муфта, що передає обертовий момент за рахунок сил тертя, що виникають на робочих поверхнях деталей муфти. Вони служать для плавного зчеплення валів на ходу при довільних швидкостях обертання.
Під час вмикання фрикційних муфт обертаючий момент на веденому валу зростає поступово і пропорційно збільшенню сили взаємного притискання поверхонь тертя. Це дозволяє з'єднувати вали під навантаженням і зі значною початковою різницею їх кутових швидкостей. У процесі вмикання муфта пробуксовує, а розгін веденого вала відбувається плавно без ударів. Фрикційна муфта може виконувати також функції запобіжного пристрою через можливе проковзування при перевантаженнях приводу.
Фрикційні муфти за формою робочих поверхонь бувають таких видів: дискові, робочими поверхнями яких є плоскі торцеві поверхні дисків; конусні, робочі поверхні яких мають конічну форму; циліндричні, що мають циліндричну робочу поверхню.
Зчіпні муфти в приладобудуванні широкого розповсюдження не знайшли.
Самокеровані муфти призначені для автоматичного зчеплення і розчеплення валів при зміні заданого режиму роботи машини. Самокеровані муфти розрізняють: за напрямком обертання – обгінні; за кутовою швидкістю – відцентрові; за моментом – запобіжні.
Обгінні муфти, або муфти вільного ходу, служать для передачі обертального моменту в одному напрямку. Найбільше поширення одержала роликова муфта (рис.11).
Ця муфта складається з двох напівмуфт, одна з яких має форму кільця, а друга – форму зірочки з вирізами для роликів. Для швидкого включення муфти ролики віджимаються пружинами.
107

ПЕРСПЕКТИВНІ ТЕХНОЛОГІЇ ТА ПРИЛАДИ
При передачі обертаючого моменту ролики заклинюються між напівмуфтами в частині вирізу, що звужується, утворюючи тверде зчеплення. Якщо з якої-небудь причини кутова швидкість веденого вала перевищить кутову швидкість ведучого, то внаслідок обгону ролики розклинюються, викочуються в розширену частину вирізу і муфта автоматично виключиться. При зупинці ведучого вала ведений вал продовжує обертатися.
Рис.11. Обгінна роликова муфта
Обгінні роликові муфти працюють безшумно, допускаючи велику частоту включень. Критерієм працездатності роликових муфт є контактна міцність робочих поверхонь роликів і напівмуфт.
Відцентрова муфта, призначена для автоматичного зчеплення (або розчеплення) валiв при досягненнi ведучим валом заданої швидкостi обертання. Може використовуватись як зчiпна (цилiндрична) або запобжна муфта.
Вiдцентровi муфти можуть застосовуватись:
для полегшення керування (зчеплення i розчеплення муфти відбувається автоматично при досягненi певної частоти обертання);
для розгону механiзмiв машин, якi мають значнi моменти інерції, двигунами з малими пусковими моментами;
для пiдвищення плавностi пуску; для запобiгання значного розгону.
Запобіжні муфти захищають кiнематичний ланцюг вiд статичних або динамiчних навантажень, перегрiву або недопустимого збiльшення швидкостi. При перевищеннi установленої границi обертового моменту ланцюговий вузол муфти або розриває кiнематичний ланцюг, або переходить в режим пропускання.
Інформаційні джерела
1.Детали и механизмы приборов: Справочник / Б.М. Уваров, В.А. Бойко, В.Б. Подаревский, Л.И. Власенко. – К.: Техніка, 1987. – 343 с.
2.Справочник конструктора точного приборостроения / Г.А. Веркович, Е.Н. Головенкин, В.А. Голубков и др.; Под общ. ред. К.Н. Явленского, Б.П. Тимофеева, Е.Е. Чаадаевой. – Л.: Машиностроение, 1989. – 792 с.
3.Устюгов І.І. Деталі машин. – К.:«Вища школа», 1984. – 306 с.
4.Заблонский К.И. Детали машин. – К.:«Вища школа», 1985. – 428 с.
5.Детали машин: Атлас. /Под ред. Д.Н.Решетова. – М.:«Машиностроение», 1988. – 270 с.
УДК 622.24.051.55
Р. С. Яким Дрогобицький державний педагогічний університет ім. Івана Франка
ПІДВИЩЕННЯ ДОВГОВІЧНОСТІ ВІДКРИТИХ ОПОР ТРИШАРОШКОВИХ БУРОВИХ ДОЛІТ ДЛЯ БУРІННЯ МІЦНИХ ТА ОСОБЛИВО МІЦНИХ ПОРІД
У статті проаналізовано працездатність відкритих опор тришарошкових бурових доліт для буріння міцних та особливо міцних порід. Встановлений взаємозв’язок між конструкторськотехнологічними, фізико-механічними показниками елементів опор та їх експлуатаційними показниками. Рекомендується при проектуванні складальних операцій опор доліт 244,5ОК-ПГВ (формуванні селективних груп) враховувати не тільки геометричні параметри тіл кочення, але й їх твердість, яка для даного типорозміру опор повинна бути в межах HRC58-59.
108
ПЕРСПЕКТИВНІ ТЕХНОЛОГІЇ ТА ПРИЛАДИ
Ключові слова: працездатність, бурове долото, опора, підшипник кочення, тіла кочення, твердість
В статье проанализирована работоспособность открытых опор трехшарошечных буровых долот для бурения крепких и особо крепких пород. Установлена связь между конструкторскотехнологическими, физико-механическими показателями элементов опор качения и их эксплуатационными показателями. Рекомендуется при проектировании сборочных операциях опор долот 244,5ОК-ПГВ (формировании селективных групп) учитывать не только геометрические параметры тел качения, но и их твердость, которая для данного типоразмера опор должна бить в границах HRC58-59.
Ключевые слова: работоспособность, буровое долото, опора, подшипник качения, тела качения, твердость.
In the article the efficiency of open bearings of three-cone rock bits for hard and especially hard rocks drilling is analyzed. The interconnection between design-technological, physical-mechanical parameters of bearing components and their operational indices is determined. For designing of 244,5ОК-ПГВ rock bit bearings assembling operations it is recommended to take into account not only geometrical parameters of bodies of rolling but also their hardness, which must be within HRC58-59 for bearings given standard size.
Key words: efficiency, rock bit, bearing, rolling (-contact) bearing, bodies of rolling, hardness
Постановка проблеми. Сьогодні для буріння свердловин широко застосовують тришарошкові бурові долота з опорою ролик-кулька-ролик та осьовими підшипниками ковзання „п’ята – підп’ятник” і „упорний торець цапфи лапи – упорний торець шарошки”. Для буріння міцних і особливо міцних порід шарошки таких доліт мають вставне твердосплавне породоруйнівне оснащення. Особливо важкі умови експлуатації цих бурових доліт висувають комплекс вимог, як до конструкції елементів опор і породоруйнівного оснащення, так і до матеріалів і їх зміцнення. Відтак, поряд із підвищенням ефективності вставного породоруйнівного оснащення шарошок, існує проблема підвищення довговічності підшипників опор. Зокрема, корозивне середовище, що містить абразив, а також навантаження на долото 250кН і більше та частота його обертання 1с-1 спричинюють до різкого зниження довговічності, як радіальних підшипників кочення, так і осьових підшипників ковзання. Тому вивчення шляхів ефективного підвищення довговічності відкритих опор тришарошкових бурових доліт має важливе практичне значення для вітчизняного долотобудування.
Аналіз останніх досліджень і публікацій. Значний вклад у розв’язання окресленої проблеми здійснено в роботах таких вчених, серед яких, Барильник В.М. [1], Богомолов Р.М. [2], Виноградов О.М. [3], Жидовцев М.О. [4], Журавльов А.М. [5], Кацов К.Б. [6], Неупокоєв В.Г. [7], Петрина Ю.Д. [8], Посташ С.А. [9], Пяльченков В.О. [10], Римар О.М. [11], Торгашов А.В. [12], Lin Yu [13] та ін.
Оскільки автори по різному оцінюють переважаючий вплив того чи іншого чинника умов експлуатації чи конструкції долота, або виготовлення підшийків кочення опори, існують суперечливі рекомендації стосовно напрямку підвищення їх довговічності.
Якісний аналіз розподілу навантаження між підшипниками опори шарошки описаний в [10, 14] показує, що навантаження між підшипниками розподіляється нерівномірно. В основному навантаження сприймається тільки двома підшипниками – кульковим і великим роликовим, або кульковим і малим роликовим підшипниками. При довільному варіанті навантаження найбільше навантаження сприймає кульковий замковий підшипник. Що підтверджується умовами втрати працездатності сучасних опор тришарошкових бурових доліт призначених для розбурювання особливо міцних порід. Тут виявлена низька стійкість до зношування і руйнування замкового кулькового підшипника. Зафіксовано: розколювання тіл кочення, деформацію на біговій доріжці лапи з утворенням другої бігової доріжки, люфти і зміщення в осьовому напрямку шарошки, руйнування бурта замкового кулькового підшипника.
Відтак, у основному, вдосконалення конструкції роликових підшипників зводиться до зменшення контактних напружень в елементах опори. Ефективний спосіб підвищення довговічності опори – видозміна конструкції роликів і бігових доріжок [1, 4, 11, 15 - 17]. Зокрема в [1, 11] обґрунтовано зміни до конструкції бігових доріжок і тіл кочення, тим не менше такі конструкції виявилися нетехнологічними при спробі їх освоєння виробництвом. В роботах [4, 16] описано розроблені і випробувані долота з опорою на конічних роликових підшипниках кочення. Однак такі конструкції опор вимагали доопрацювання для забезпечення нормальної роботи роликових рядів. Зауважимо, що і сьогодні тривають дослідження з розробки опор з конічними роликами, зокрема в
109
ПЕРСПЕКТИВНІ ТЕХНОЛОГІЇ ТА ПРИЛАДИ
[17] описані параметри такої конструкції із сепаратором, що повинен стабілізувати роботу роликів. Тим не менше, відсутність експериментальних даних для оцінки працездатності доліт з такою опорою в реальних умовах, не дозволяє з констатувати ефективність та практичну придатність даної пропозиції. Практика показує, що найбільш доцільним та технологічним є зміна форми тіла кочення, а саме застосування бомбінованих роликів в опорах доліт [15].
Сьогодні існує тенденція у зменшенні зазорів у опорі та підвищенні точності оброблення поверхонь бігових доріжок, а також виконання осьових підшипників ковзання із зносостійких та теплостійких матеріалів, що дозволяють забезпечувати нормальну роботу роликових рядів [2, 5, 13]. Тим не менше, при роботі долота спряжені елементи опор зазнають пошкоджень і руйнуються, через які виникають зазори. Тому стоїть питання у підвищенні міцності та зносостійкості контактуючих елементів, що може суттєво відтермінувати утворення небезпечних зазорів в опорі. Вирішенню таких питань присвячено роботи [3, 6, 8, 18], в яких обґрунтовані основні підходи до вибору долотних сталей та їх зміцнення.
Існує також комплексний підхід до вирішення проблеми підвищення довговічності відкритих опор доліт, основні засади якого висвітлені в роботах [2 - 4, 6, 7, 19, 12]. У цих роботах, зокрема, обґрунтовано, що всі етапи створення тришарошкових бурових доліт, – від проектування до виготовлення, істотно визначають експлуатаційні їх показники. Зокрема, вибір невідповідних плавок долотних сталей, їх недосконала технологія механічного оброблення і зміцнення може нівелювати ефективність найдосконалішої конструкції. Одночасно сучасні підходи до вирішення конструкторсько-технологічних задач, проектування, конструювання, підготовки виробництва визначають техніко-економічний рівень спроможності освоєння й виготовлення долотним виробництвом високоякісних конструкцій тришарошкових бурових доліт.
Невирішені частини проблеми. Аналізом даних експлуатації тришарошкових доліт з відкритою опорю встановлено, що долота часто недопрацьовують через заклинювання шарошок. Відомо, що такий стан речей пов'язаний, як із особливостями конструкції опор, так і з недостатньою зносостійкістю й контактною витривалістю елементів підшипників опори. Тим не менше, долота з однаковими конструкціями опор виявляють різні експлуатаційні показники. Як показано в роботах [3, 6, 8, 18, 19] це пов’язано із фізико-механічними і експлуатаційними показниками застосовуваних долотних сталей та особливостями їх зміцнення. Незважаючи на значний багатолітній досвід виготовлення тришарошкових бурових доліт, вітчизняне долотобудування наштовхується на низку проблем пов’язаних з браком надійних даних про взаємозв’язок між конструкторськотехнологічними, фізико-механічними показниками елементів опор та їх експлуатаційними показниками. Зокрема, поряд зі численними даними про експлуатаційні показники деталей доліт виготовлених із різних долотних сталей і зміцнених на заданий розподіл фізико-механічних показників цапф лап, відсутні дані про експлуатаційні показники опор у яких застосовують тіла кочення з різними показниками твердості.
Метою дослідження є вивчення працездатності відкритих опор тришарошкових доліт і встановлення взаємозв’язку між конструкторсько-технологічними, фізико-механічними показниками елементів опор та експлуатаційними показниками доліт для буріння міцних та особливо міцних порід. З цією метою досліджено вплив структури і параметрів розподілу твердості елементів підшипників кочення опор на їх експлуатаційні показники.
Основні результати дослідження. З метою встановлення низьких показників наробітку тришарошкових бурових доліт 244,5ОК-ПГВ, опори яких заклинили протягом 10-18 годин роботи поставлені стендові випробовування долота з цієї партії. Буріння здійснювали на вибої зі сталі 10. Робоче навантаження на долото дорівнювало 1800 кН, а число обертів ротора – 60 об/хв. Охолоджуючим середовищем доліт була технічна вода, яка подавалася в опори. Для виведення долота на робочий режим буріння, навантаження на долото збільшували ступенями, – до 15 кН і 80 кН, при яких долото працювало по одній годині. Встановлений час наробітку до заклинювання опор дорівнював 16 год. Тут початкове зростання значення крутного моменту і підклинювання шарошки зафіксовані на 13 год роботи долота. Причиною припинення випробовувань було заклинювання шарошок № І і № ІІ.
Аналізом встановлено, що в опорах секцій № І і № ІІ бурового долота відбулося катастрофічне зношування спряжених поверхонь в осьовому напрямку. Найбільшого зносу, деформації та руйнувань зазнали бурти цапфи лапи. Це спричинило руйнування і заклинювання роликових підшипників. Також виявлені руйнування елементів замкового підшипника кочення, зокрема зламування замкового пальця.
110