
Збірник 04
.pdfПЕРСПЕКТИВНІ ТЕХНОЛОГІЇ ТА ПРИЛАДИ
Лазери IV класу небезпеки розмішують в окремих ізольованих приміщеннях і забезпечують дистанційне управління їх роботою.
Обов’язково потрібно враховувати утворення супутніх чинників. Їх виникнення залежить від потужності випромінювання конструктивних особливостей лазерних установок, фізико-хімічних властивостей матеріалів, що обробляються, санітарно-технічного обладнання технологічних лазерних установок і виробничих приміщень. Робота лазерних установок супроводжується шумом, який може досягати 70-80 дБ, а також мають місце звукові імпульси з рівнем інтенсивності 100-120 дБ, які виникають внаслідок переходу світлової енергії в механічну в місцях дотику променя з поверхнею, що обробляється, або за рахунок роботи механічних елементів установки.
У приміщеннях, де розміщені лазери, влаштовують механічну припливно-витяжну вентиляцію для видалення можливих токсичних газів, пари і пилу. Для захисту від шуму використовують заходи звукопоглинання і звукоізоляції установок.
Якщо заходи колективного захисту не дають повної гарантії від опромінення і не забезпечують вимог санітарних правил, вдаються до засобів індивідуального захисту. До 313, що забезпечують безпечні умови праці при роботі з лазерами, відносяться спеціальні окуляри, щитки, що забезпечують зниження опромінення очей до ГДР.
При роботі з лазерами необхідно забезпечити такі умови праці, за яких не перевищуються гранично допустимі рівні опромінення очей і шкіри. Заходи безпеки полягають у влаштуванні захисних екранів, каналізації лазерного випромінювання по світловодах, використанні захисних окулярів. Захисні окуляри слід ретельно підбирати залежно від робочої довжини хвилі лазерного світла, а їх спектр пропускання необхідно перевіряти. Окуляри мають ефективно стримувати випромінювання лазера, однак не бути надто темними. Для захисту від розсіяного випромінювання, крім використання окулярів, застосовують спеціальне фарбування або обробку стін лабораторії, а також огородження екранами [5].
При використанні лазерів видимого діапазону потрібні спеціальні попереджувальні світлові табло або надписи під час роботи з лазерами. Для безперервних лазерів потужністю 1-5 мВт бажане виконання ряду заходів, серед яких: захист очей; робота в спеціальному приміщенні; обмеження шляху променя; попереджувальні світлові табло. При застосуванні лазерів середньої потужності ці заходи є обов’язковими, а для потужних лазерів, крім названих заходів, необхідно контролювати приміщення і систему оповіщення, забезпечувати дистанційне вмикання, управління роботою і блокування живлення.
Для гігієнічної оцінки умов праці за шкідливістю виробничих чинників при роботі з джерелами лазерного випромінювання, керуються нормативними документами, що регламентують величину ГДК або ГДР відповідних чинників [5].
Основними законодавчими документами при оцінці умов праці з оптичними квантовими генераторами є: "Санітарні норми і правила улаштування і експлуатації лазерів"; методичні рекомендації "Гігієна праці при роботі з лазерами" і т. ін.
Всі лазери мають бути марковані знаком лазерної безпеки за ГОСТ 12.1.040-83 "Лазерна безпека. Загальні положення".
Методи і апаратура дозиметричного контролю лазерного випромінювання наведені в ГОСТ 12.1.031-81 "ССБТ. Лазери. Методи дозиметричного контролю лазерного випромінювання".
Роботи, щодо обслуговування лазерних установок відносяться до робіт з шкідливими умовами праці. Відповідно до наказу МОЗ, працюючі на цих видах робіт мають проходити попередні і періодичні медичні огляди 1 раз на рік.
Безпечні умови праці з лазерним устаткуванням забезпечуються сукупністю заходів, які залежать в першу чергу від класу лазера.
Щодо профілактики ураження лазерним випромінюванням, то вона включає систему заходів інженерно-технічного, планувального, організаційного і санітарно-гігієнічного характеру.
Наростаючі темпи досліджень в галузі лазерної техніки відкриють можливості створення нових типів лазерів зі значно поліпшеними характеристиками, що дозволить розширити області їх застосування в приладобудуванні. Але паралельно потрібно враховувати й безпечність таких нових технологій.
Інформаційні джерела
1.Застосування лазерів. За редакцією д-ра техн. Наук В.П. Тичинського, видавництво "Світ", Москва 1974.
2.Крилов К.І. Застосування лазерів у машинобудуванні та приладобудуванні. / Крилов К.І., Прокопенко В.Т., Митрофанов О.С. - Л.: Машинобудування. Ленінгр.отд-ня, 1978.
21
ПЕРСПЕКТИВНІ ТЕХНОЛОГІЇ ТА ПРИЛАДИ
3.Тарасов Л.В. Лазери і їх застосування. / Тарасов Л.В. Навчальний посібник для ПТУ. М.: Радіо і зв’язок, 1983.
4.Основи охорони праці. / В. В. Березуцький, Т. С. Бондаренко, Г. Г. Валенко та ін. - За заг. ред. В. В. Березуцького. Навч. посіб. – 2-ге вид., перероб. і доп. – Х.: Факт, 2007. – 480 с.
5.Геврик Є. О. Охорона праці: Навчальний посібник для студентів вищих навчальних закладів. / Геврик Є. О. - К.: Ельга, Ніка-Центр, 2003. - 280 с.
6.Москальова В. М. Основи охорони праці. Підручник. / Москальова В. М./ - К.: Професіонал,
2005.- 666 с.
УДК 621.906
Гордєєв О.Ф., Четвержук Т.І.
Луцький національний технічний університет
МЕТОДИКА ВИЗНАЧЕННЯ ТОЧНІСНОЇ НАДІЙНОСТІ ВУЗЛІВ ВЕРСТАТА
Стики в верстатних системах визначають до 80% точнісну надійність верстата. В роботі викладені підходи щодо оцінки стиків на якісні показники верстатної системи(ВС). Запропонована математична модель ідентифікації впливу стиків на похибку обробки. Розроблено програмне забезпечення STYK, яке дозволяє визначати диференційний вплив всіх стиків на точність обробки.
Розглянута методика моделювання та автоматизації процесів ідентифікації деформаційних характеристик стиків металорізальних верстатів за їх характеристикам в технологічному робочому просторі. Реалізований принцип дозволяє зменшити загальні витрати і час на забезпечення технологічної надійності верстата в процесі його експлуатації. Запропонована методика визначення балансу зміщень елементів пружної системи забезпечує зручну і надійну ідентифікацію деформаційних властивостей стиків вузлів верстата.
Ключові слова: надійність, жорсткість, похибка, стик, моделювання, ідентифікація, деформації, баланс.
Стыки в станочных системах определяют до 80 % точностную надежность станка. В работе изложены подходы к оценке стыков на качественные показатели станочной системы (СС). Предложенная математическая модель идентификации влияния стыков на погрешность обработки. Разработано программное обеспечение STYK , которое позволяет определять дифференциальное влияние всех стыков на точность обработки.
Рассмотренная методика моделирования и автоматизации процессов идентификации деформационных характеристик стыков металлорежущих станков, по их характеристикам в технологическом рабочем пространстве. Реализованный принцип позволяет уменьшить общие затраты и время на обеспечение технологической надежности станка в процессе его эксплуатации. Предложенная методика определения баланса смещений элементов упругой системы обеспечивает удобную и надежную идентификацию деформационных свойств стыков узлов станка.
Ключевые слова: надежность, жесткость, погрешность, стык, моделирование, идентификация, деформации, баланс.
The joints in machine tool system determine the accuracy to 80 % reliability of the machine. The article approaches in evaluating joints on quality indicators Machining System (MS). A mathematical model to identify the influence of joints on error processing. The software STYK, which allows to determine the differential impact of all joints for precision machining.
The technique of modeling and automated identification of deformation behavior of joints of machine tools for its technological characteristics of the workspace. Realized principle can reduce overall costs and time to ensure the technological reliability of the machine during its operation . The proposed method of determining the balance shifts elements elastic system provides a convenient and reliable identification of the deformation properties of joints nodes machine.
Keywords: reliability, rigidity, accuracy, joint, modeling, identification, strain, balance.
Постановка проблеми. Розглянемо проблему на прикладі визначення погрішності розміру деталі при обробці різцем з револьверного супорта на токарно-револьверному автоматі мод. 1Б118. Для аналізу використаємо результати дослідження технологічної надійності токарно-револьверних
22
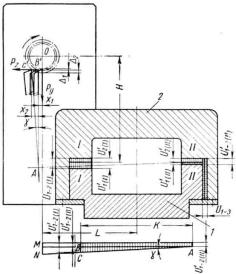
ПЕРСПЕКТИВНІ ТЕХНОЛОГІЇ ТА ПРИЛАДИ
автоматів мод. 1Б118 Мелітопольського верстатобудівного заводу, які наведені в роботи А.С. Пронікова.
Оскільки більшість робіт, що виконуються на автоматах, проводяться інструментом з револьверного супорта, то необхідно знати величину віджимання каретки револьверного супорта в різних напрямах.
На жорсткість револьверних супортів нових верстатів впливають зазори в місцях сполучення направляючих і каретки, жорсткість деталей (клин і підтримуючі планки), що легко деформуються, чистота і точність обробки зв'язаних деталей і якість складальних робіт.
При перевірці револьверних супортів на 25 верстатах було встановлено розсіяння жорсткості. При перевірці сумарної жорсткості вузлів автомата (шпиндель—суппорт) по ГОСТ 1178—65 виходить значення жорсткості для декількох вузлів одночасно, а не кожного окремо, що утрудняє підвищити жорсткість окремого вузла. Крім того, комплексна перевірка виключає цанговый затиск, що робить великий вплив на жорсткість вузла шпинделя.
Основний зміст дослідження. Жорсткість автоматів в роботі визначалася по методиці точіння ступінчастого валу (виробничий метод). Для визначення жорсткості верстатів виробничим методом застосовується жорстке облямовування, деформаціями якого нехтують. Тому оброблювану деталь використовують для визначення жорсткості технологічної системи. При дослідженні жорсткості автоматів віджимання деталі враховані, а жорстке облямовування замінене оброблюваним прутком діаметром 18 мм. Силу різання і жорсткість при виробничому методі визначають по емпіричних рівняннях. Цей метод забезпечує можливість достатньо точно визначати сили різання, а динамічну жорсткість jd системи в радіальному напрямі можна визначити з рівняння
J |
|
|
P |
|
2(Py 2 Py1 ) |
|
|
д |
|
|
|
|
|||
|
D2 |
D1 |
|
||||
|
|
|
|
||||
|
|
|
|
(1) |
|||
|
|
|
|
|
|
|
де - деформація вузла; Ру2 — сила різання при глибині різання t2 = 2,1 мм; Ру1 — сила різання при глибині різання t1 = 0,1 мм; D2 — фактичний діаметр валу після проточування при глибині різання t2 = 0,1 мм; Dx — фактичний діаметр валу після проточування при глибині різання t1 = 2,1 мм.
Збільшення радіальної сили різання при зміні глибини різання від t1 = 0,1 мм до t2 = 2,1 мм веде до збільшення віджимань всіх ланок технологічної системи, у тому числі і тарованого облямовування з різцем, а отже, і збільшенню діаметру D2 оброблюваної сходинки. Динамічна жорсткість верстата в роботі нижче сумарною (шпиндель—револьверный супорт) статичною і складає jd = 2,60 Н/мкм при jст = 4,12 Н/мкм .
Зв'язок статичної і динамічної жорсткості може бути виражена через коефіцієнт динамічності
К: |
|
|
K jcm |
/ jä . |
(2) |
|
|
Рис. 1. Схема визначення погрішності розміру деталі при обробці різцем з револьверного супорта: 1
— станина верстата; 2 — каретка револьверного супорта; І — передні горизонтальні направляючі станини і каретки; ІІ — задні горизонтальні направляючі станини і каретки.
23

ПЕРСПЕКТИВНІ ТЕХНОЛОГІЇ ТА ПРИЛАДИ
Динамічні віджимання системи більше статичних, тому коефіцієнт динамічності К > 1. Залежно від режиму різання геометрії і способу кріплення деталі коефіцієнт динамічності може змінюватися від 1,25 до 1,9. При дослідженні жорсткості шпинделя встановлено, що радіальна жорсткість шпинделя з урахуванням підшипників і цангового затиску знаходиться в межах jш = 7,0 Н/мкм. Радіальна і осьова жорсткість безпосередньо шпинделя відповідно складають 3,0—4,0 і 7,15—7,5 Н/мкм. Радіальна жорсткість вузла шпинделя унаслідок наявності цангового затиску змінюється у великих межах за один оборот (від 1,4 до 2,5 разу) і складає 1,25 — 1,85 Н/мкм.
Дослідження показали, що на втрату точності верстатів від зношення при експлуатації залишається 20—25% допуску. При експлуатації автоматів резерв точності дуже малий і буде скоро витрачений і автомат почне давати відмови по точності. Це дозволило зробити висновок про те, що для підвищення точності нових автоматів і тривалого її збереження при експлуатації необхідно в першу чергу підвищити точність виготовлення автоматів з посилюванням приймальних норм точності на 30—35%, а існуючу методику перевірки сумарної статичної жорсткості вузлів верстата згідно Гост 1178—65 слід доповнити повузловою перевіркою з посилюванням допустимих віджимань.
Таким чином, бачимо:
1)похибка обробки визначається ланцюгом із чотирьох послідовно з’єднаних сполучень: а) горизонтальні направляючи станини - каретка корпусу револьверного супорта, б) револьверний супорт — опори револьверної головки, в) втулка фіксатора револьверної головки - фіксатор; г) шпиндельний вузол (ШВ);
2)похибка обробки визначається для трьох параметрів в статичному режимі: діаметрального розміру, погрішностей форми у повздовжньому і поперечному перерізах, але в залежності від мети випробувань кількість їх може збільшуватися;
3)похибки обробки змінюються з часом із-за зносу сполучених поверхонь стиків і змінюються від умов різання (сили, вібрації тощо);
4)похибки стиків та їх деформації по різному впливають на усі види похибок обробки, як за величиною, так і за характером цього впливу.
Аналіз результатів розглянутого дослідження дозволяє констатувати наступне:
1)регламентована проста стандартна перевірка сумарної жорсткості вузлів верстата дозволяє отримати значення сумарних похибок і жорсткості для декількох вузлів одночасно, але вона утрудняє визначення внеску кожного окремого вузла у загальний баланс, тобто «слабких місць» ТПС;
2)для підвищення точності нових верстатів і тривалого її збереження при експлуатації необхідно в першу чергу підвищити точність їх виготовлення з посилюванням приймальних норм точності на 30—35%, а існуючу методику перевірки сумарної статичної жорсткості вузлів верстата згідно Гост 1178—65 слід доповнити повузловою перевіркою з посилюванням допустимих віджимань;
3)пружні деформації елементів ТПС та знос спряжень досить задовільно визначаються за допомогою існуючих методик їх аналітичного розрахунку;
4)прогнозування точністної надійності в процесі експлуатації верстатів вимагає регулярного проведення трудомістких і дорогих експериментальних випробувань, що знижує їх ефективність.
Це визначає напрямок вдосконалення загальної методики досліджень, який можна позначити наступним:
методика повинна бути зручною і не трудомісткою;
методика повинна дозволяти визначення внеску кожного окремого стику ТПС у загальний баланс погрішностей;
методика повинна мінімізувати витрати на проведення експериментальних випробувань; методика повинна бути ефективною і гарантувати необхідний рівень достовірності і точності
прогнозування технологічної надійності верстата в процесі його експлуатації.
Обґрунтування припущень і методики: Методика, яка пропонується, ґрунтується на теорії особливостей (В.І. Арнольд) і теорії фракталів (Б. Мандельброт і А.Д. Морозов ). Розглянемо такий приклад.
Нехай маємо L стиків Sl, l 1, L , які знаходяться у розмірному ланцюзі впливу на кінцеву узагальнену сумарну похибка Y (розмір, похибка форми, шорсткість поверхні, тощо) і які
|
|
|
|
|
|
|
|
|
|
характеризуються діаграмами |
віджимань |
yl |
( pi ), l 1, L; i 1, I, |
де рі – дискретні |
рівні |
||||
|
|
|
|
|
|
||||
навантажень з постійним кроком |
рі = const прирощення навантаження таким що рі+1 = рі + |
р. Тут |
24
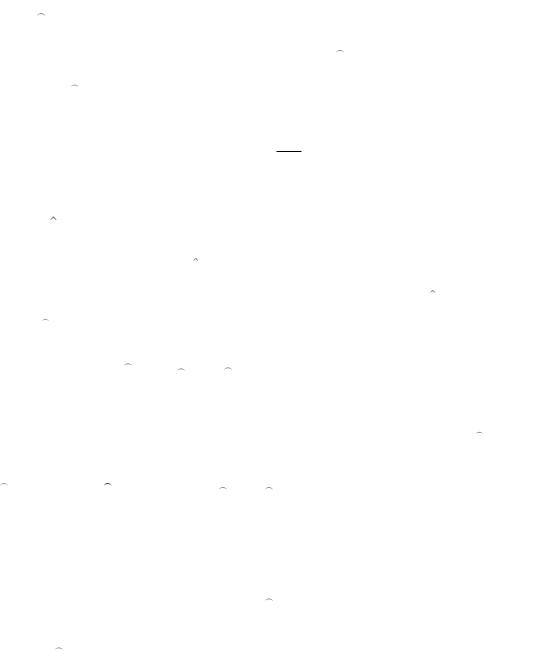
ПЕРСПЕКТИВНІ ТЕХНОЛОГІЇ ТА ПРИЛАДИ
мається на увазі, що навантаження є узагальненими і можуть мати різноманітну природу (сила різання, температурний тиск, амплітуда вібрацій тощо). До того ж вони приведені до точки технологічної системи верстата (ТСВ), в якої визначається кінцева похибка Y, а навантаження, що прикладені до l – го стику, перераховуються за передатнім числом розмірного ланцюгу, як це показано на рис. 1.
Початкова діаграма віджимань після макроприроблення поверхонь стику може бути достатньо точно апроксимованою регресією поліномом ступеню k:
|
y ( p) b |
|
b |
p b |
p2 ... b |
pk ( p), |
|
|
|
l |
l 0 |
l1 |
l 2 |
lk |
|
(3) |
|
|
|
|
|
|
|
|
||
|
|
|
|
|
|
|
|
|
де blk |
|
|
|
|
|
|
y ( p) |
|
- – коефіцієнт при члені k - го порядку в регресії оцінки віджимань l |
в l – му стику; |
|||||||
p |
- адитивна помилка регресії |
y ( p) |
. |
|
|
|
|
|
|
l |
|
|
|
|
|
||
|
|
|
|
|
|
|
|
Поведінка кожного l – го стику схильна до певних змін, які відбуваються або у часі (знос, прироблення, тощо), або по положенню (зміна схеми навантаження в процесі обробки, положення
сили різання, тощо) із дискретним кроком спостережень Δtr, r 1, R . Величина цих змін власне притаманна для поверхонь кожного l – го стику, і вона може описуватися теоретичною, або регресійною залежністю вигляду:
z |
l |
(r) c 0 |
c 1 r c 2 r2 (r), |
|
|
|||||
|
l |
l |
|
|
|
l |
|
, |
(4) |
|
|
|
|
|
|
|
|||||
|
|
|
|
|
|
|
|
|
||
де сrj – коефіцієнт регресії (або апроксимації) тренду z l |
(r) порядку 0, 1, 2 (індекс у знаменнику) за |
|||||||||
|
|
|
|
|
|
r |
|
|
|
|
номером поточного кроку r у рядах динаміки , |
r 1, R |
; |
- адитивна помилка регресії |
z l (r) . |
||||||
|
|
|
|
|||||||
Таким чином, оцінка Yl внеску стику Sl |
в узагальнену похибку Y із врахуванням (1) і (2) |
|||||||||
становить: |
|
|
|
|
|
|
|
|
|
|
|
|
Yl |
l |
z (r) y ( p), |
|
|
||||
|
|
|
|
|
l |
|
l |
|
|
(5) |
|
|
|
|
|
|
|
|
|
|
де l - коефіцієнт передавання похибки l – го стику, який визначається із розмірного ланцюга.
При адитивному додаванні погрішностей від l стиків |
оцінка загальної погрішності Y |
||
визначиться із формули: |
|
|
|
L |
L |
|
|
Y ( p, r) Yl |
( p, r) l |
z (r) y (r). |
|
l 1 |
l 1 |
l |
l |
|
(6) |
При обробці на верстаті партії деталей можемо отримати усереднене спостережене значення погрішності Y ( p) при навантаженні р і конкретному значенні r, або, якщо ввести спостереження у часі r, то маємо часовий ряд Y ( p, r) .
Постає питання, яким чином із (6) отримати значення Yl ( p, r) , тобто визначити внесок кожного l–го стику у загальний баланс Y похибки обробки? У такій постановці завдання набуває
вигляду задачі ідентифікації Yl ( p, r) . На основі її розв’язування можна ставити завдання як прогнозування технологічної надійності верстата, так і діагностики стану його стиків.
З цього погляду, процес деформацій ПС МРВ, якій досліджується уявляється як класична «чорна скринька», а головною задачею дослідження є виявлення функціональних зв’язків між вхідними і вихідними сигналами цього об’єкту у вигляді (рис. 2).
У загальному випадку навантаження pl можуть діяти по різних координатах, впливаючи на той самий параметр точності Y. Так, при обробці різцем з револьверного супорта на стик горизонтальних направляючої станини і каретки діють 6 загальних силових фактора: три складових сили різання і три моменти від сил різання по координатах.
25

ПЕРСПЕКТИВНІ ТЕХНОЛОГІЇ ТА ПРИЛАДИ
Позначимо координату впливу силового фактору індексом «і». Тоді сумарну похибка від дії силового фактору Р по усіх координатах на усі Sl стики розмірного ланцюгу можна визначити із формулі:
I |
I |
I |
I |
L |
|
Y Yi |
Wi ( p1i p2i ... pLi ) w1i |
( p1i ) w2i ( p2i ) ... wLi ( pLi ) wl i ( pl i ), |
|
||
i 1 |
i 1 |
i 1 |
i 1 |
l 1 |
(7) |
де рlі - силові фактори в стиках Sl |
від впливу Р по і – ої координаті; уlі - складова похибки у стику Sl |
від впливу Р по і – ої координаті; Yi - складова результуючої похибки від впливу Р по і – ої
координаті; Y - сумарна похибка від впливу Р по усіх координатах; wl i ( pl i ) - оператор перетворення силового фактору рlі у стику Sl в складову уlі похибки Yi .
Стик S1 |
|
Стик S2 |
|
|
Стик SL |
|
|
|
|
|
|
|
|
|
|
|
|
|
|
|
р1 |
|
|
р2 |
|
|
рL |
|
|
|
|
|
|
|
«Чорна скринька»
Рис. 2. Початкова структурна схема розв’язування задачі виявлення впливу навантажень pl у стиках верстата на сумарну похибка Y
З метою зменшення інформаційної ентропії «чорної скриньки» проводиться декомпозиція загальної задачі за параметрами та за структурою. На відміну від вихідної структури (рис. 2), в якій вихідний сигнал y містить змішаний вплив вхідних сигналів p1, p2,…, pL, на наступному етапі
|
|
|
|
|
|
сигнали у поділяються, але кожен з сигналів |
yl , |
l 1, L |
також містить змішаний вплив вхідних |
||
|
|
|
|||
сигналів p1, p2,…, pL. Тобто Yi формується сума складових погрішностей yli усіх стиків Sl |
від |
||||
впливу Р по кожної і – ої координаті. |
|
|
|
|
|
Після декомпозиції початкової задачі із |
врахуванням багатокоординатності впливу |
Р |
структурна схема на рис. 2 прийме вигляд рис 3. |
|
|
|
Для ідентифікації «чорної скриньки» у тому вигляді, який наданий на рис. 2 було розроблено |
|
спеціальну методику, яка заснована на трьох основних припущеннях: |
|
|
1) |
складова похибки yli, які виникають в Sl від впливу Р по кожної і – ої координаті є незалежними; |
|
2) |
yli pl i |
plj 0, i j |
відсутні змішанні впливи окремих факторів рli на уlі, тобто |
; |
|
3) |
дійсний принцип суперпозиції, тобто сумарна похибка від дії |
силового фактору Р по усіх |
координатах на усі Sl стики розмірного ланцюгу можна визначити як просту суму |
|
з (5). |
|||||||
Разом з допущеннями вводяться також додаткові умови: |
|
|
|||||||
процес, що вивчається, є динамічним, тобто |
|
|
|
|
|
|
|
||
p p |
t ; y y x t , l |
|
, i |
|
|
|
|||
1, L |
1, I |
|
|
||||||
li |
li |
li |
li |
|
, |
(8) |
|||
|
|
|
|
|
|
|
|
де t – час, або параметр, якій пов'язаний із дискретним параметром r; процес не є марковським, тобто має так звані властивості післядії.
26
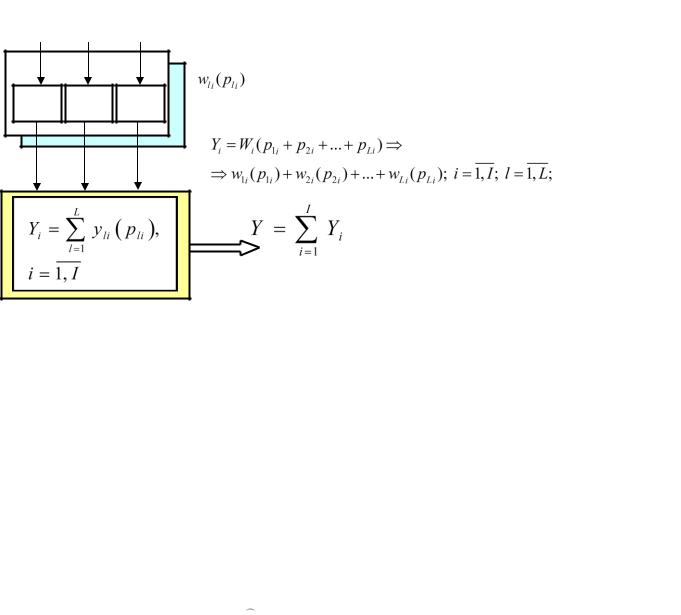
ПЕРСПЕКТИВНІ ТЕХНОЛОГІЇ ТА ПРИЛАДИ
Ці припущення і додаткові умови є такими, що спостерігаються у реальності, і вони дозволяють побудувати математичну модель ідентифікації у вигляді системи лінійних ортогональних рівнянь.
р1 |
|
р2і |
|
pLі |
|
|
|
|
|
Wi |
|
w2i |
wLi |
y1i |
y2i |
|
yLi |
рlі - силові фактори в стиках Sl від впливу по і – ої координаті; уlі - складова похибки у стику Sl від впливу по і – ої координаті;
Yi - складова результуючої похибки від впливу по і – ої координаті; Y - сумарна похибка від впливу по усіх координатах;
- оператор перетворення силового фактора у стику Sl в складову похибки уlі
Рис. 3. декомпозиція структурної схеми розв’язування задачі виявлення впливу навантажень pli у стиках верстата на сумарну похибка Y.
|
Основна ідея, яка покладена у методику, є у тому, |
pli t |
має власні особливості, |
тобто крива |
|||||||||||||||||
|
|
|
|||||||||||||||||||
зміни |
pli t |
має якби мовити власну фрактальність. |
Природно вважати, |
що ця фрактальність |
|||||||||||||||||
|
|
||||||||||||||||||||
відобразиться із власним, притаманним тільки їй, спотворенням на складову похибки |
yli pli (t) |
у |
|||||||||||||||||||
|
|
||||||||||||||||||||
стику |
Sl за |
|
|
|
|
|
wli pli |
(t) |
. |
Залишається |
тільки |
підібрати згідно |
прийнятим |
||||||||
перетвореннями |
|
||||||||||||||||||||
припущенням і додатковим умовам найбільш вдали перетворення |
wli |
pli (t) |
для формули (6). |
|
|||||||||||||||||
|
|
|
|||||||||||||||||||
|
Математична модель процедури визначення балансу зміщень. У процесі моделювання за |
||||||||||||||||||||
базисну математичну модель була прийнята загальна формула обчислення |
сумарної похибки у |
||||||||||||||||||||
вигляді: |
|
|
|
|
|
|
|
|
|
|
|
|
|
|
|
|
|
|
|
||
|
|
|
|
|
|
|
|
|
|
L |
|
I |
|
c 1 r c 2 r2 ylip p |
, |
|
|
||||
|
|
|
|
|
|
|
|
|
Y c 0 |
|
|
||||||||||
|
|
|
|
|
|
|
|
|
|
l 1 |
i 1 |
li |
li |
|
li |
li |
|
|
|
||
|
|
|
|
|
|
|
|
|
|
|
|
|
|
|
|
|
(9) |
||||
|
|
|
|
|
|
|
|
|
|
|
|
|
|
|
|
|
|
|
|
||
де |
c |
, 0,1, 2 |
|
|
|
|
|
|
|
|
|
|
|
|
|
|
|
|
|||
li |
|
|
- коефіцієнти тренду (по r) залежних змінних порядку l за номером точки r у ряду |
||||||||||||||||||
|
|
|
|
|
|
|
|
|
|
|
|
|
|
|
|
|
|
|
|
|
|
|
|
|
|
|
|
|
ylip pli |
|
|
|
|
|
|
|
|
|
|
|
|
|
|
динаміки, |
r 1, R |
; |
– розрахункові залежні змінні, складові похибки у стику Sl |
від впливу |
|||||||||||||||||
|
|
|
|
|
|||||||||||||||||
|
|
|
|
|
|
|
p |
|
|
|
|
|
|
|
|
|
|
|
|
|
|
по і – ої координаті ; |
li |
– факторні (незалежні) змінні - силові фактори в стиках Sl від впливу по і – |
|||||||||||||||||||
ої координаті. |
|
|
|
|
pli отримуються із нелінійної регресії xj на yk аналізом спостережених |
||||||||||||||||
|
Залежні змінні |
ylip |
|||||||||||||||||||
даних у вигляді поліноміальної моделі k - го порядку. |
|
|
|
|
|
|
|
|
|
||||||||||||
|
Відповідно до структурної схеми декомпозиції (див. рис. 3) ідентифікація математичної моделі |
виконується поетапно для кожної і – ої координати навантаження Рі. Ціль її – визначення модальних |
|||||
|
c |
|
ylip p |
li |
|
параметрів |
li |
, які враховують тренд регресії |
|
вигляду (9) шляхом мінімізації суми |
|
|
|
|
27

|
|
|
|
ПЕРСПЕКТИВНІ ТЕХНОЛОГІЇ ТА ПРИЛАДИ |
|
|
|
|
||||||||
квадратів відхилень |
ylip pli |
|
|
|
|
|
yli pli |
за період |
1, 2,..., R |
, що |
||||||
|
|
від його спостереженого значення |
|
|
|
|||||||||||
аналізується за критерієм МНК: |
|
|
|
|
|
|
|
|
|
|
||||||
|
R I |
|
c 1 r c 2 r2 ylip p |
yli p |
|
|
2 |
|
|
|
|
|
||||
|
|
|
min; c Dli ;l 1, L . |
|
||||||||||||
Wi c 0 |
|
|
|
|||||||||||||
|
r 1 i 1 |
li |
li |
|
li |
li |
|
li |
|
cli |
li |
|
|
|
(10) |
|
|
|
|
|
|
|
|
|
|
|
|
|
|
|
|
|
|
|
|
|
|
|
c |
|
|
|
|
|
|
|
|
|
|
|
Підбір коефіцієнтів |
li |
проводиться за фрактальними особливостями фактичних значень |
||||||||||||||
yli p |
|
|
|
|
|
|
|
|
|
|
|
|
|
|
|
|
li |
|
. У даному |
випадку |
мінімізація |
проводиться з |
використанням |
скалярної |
функції (7), а |
||||||||
|
|
найкраще наближення визначається шляхом пошуку мінімуму цієї функції в просторі параметрів
c |
D |
|
|
|
|
|
|
|
|
|
|
|
|
|
|
|
|
|
|
|
|
|
|
|
|
|
li |
|
i |
. |
|
|
|
|
|
|
|
|
|
|
|
|
|
|
|
|
|
|
|
|
|
|
|
|
|
|
|
|
|
|
|
|
|
|
|
|
|
|
|
|
|
|
|
|
|
|
|
|
||
|
|
|
|
|
|
|
|
|
|
|
|
|
|
|
|
|
|
|
|
|
|
|
|
|
|
|
|
|
Допустима область рішень Dі |
для кожного і – ої координати являє собою множину точок |
|||||||||||||||||||||||
c |
Ò |
0 |
|
1 |
2 |
|
|
|
|
|
|
|
|
|
|
|
|
|
|
|
|
|
|
|||
|
c |
|
,c ,c ;l |
1, L |
; i |
1, I |
|
|
|
|
|
|
|
|
|
|
||||||||||
kj |
|
|
|
li |
|
li |
li |
|
|
|
|
|
|
|
із 3L - |
вимірного простору параметрів E 3L. |
|
|||||||||
|
|
|
|
|
|
|
|
|
|
|
|
|
|
|
|
|
||||||||||
|
|
|
|
|
|
|
|
|
|
|
Ò |
E3L : C |
|
C C |
|
|
|
|
|
|
|
|||||
|
|
|
|
|
|
|
|
|
|
|
|
|
|
|||||||||||||
|
|
|
|
|
|
|
|
D C |
|
|
; l 1, L; 0, 2 |
|
||||||||||||||
|
|
|
|
|
|
|
|
|
i |
|
li |
|
|
|
|
li |
|
li |
li |
|
|
|
|
|
|
|
|
|
|
|
|
|
|
|
|
|
|
|
|
|
|
|
|
|
|
|
|
|
|
||||
|
|
|
|
|
|
|
|
|
|
|
|
|
|
|
|
|
|
|
|
|
|
|
|
|
, |
(11) |
C , C |
|
|
|
|
|
|
|
|
|
|
|
|
C |
. |
|
|
|
|
|
|||||||
де |
li |
|
|
li |
- відповідно нижній і верхній межи варіювання |
li |
|
|
|
|
|
|||||||||||||||
|
|
|
|
|
|
|
|
|
|
|
|
|
|
|
|
|
|
|
|
|
|
|
||||
|
|
Таким чином задача зводиться до багатопараметричної задачі умовної мінімізації з досить |
||||||||||||||||||||||||
складною |
|
поверхнею пошуку, |
для |
якої не можна |
застосувати |
жодного аналітичного |
методу |
розв’язування. Тому для ідентифікації параметрів моделі використовується обчислювальна процедура, що одержала назву методу комплексів (метод Бокса), яку довелося модифікувати з умовами особливості даної задачі.
Висновки:
викладені методичні підходи до оцінки впливу стиків на якісні показники технологічної системи;
розроблено математичну модель ідентифікації впливу окремих стиків на похибка верстата при конкретному технологічному процесі;
розроблено та обґрунтовано доцільність використання програмного забезпечення Styk, яке дозволяє визначати диференційний вплив усіх стиків на точність обробки, та на основі результатів моделювання прогнозувати технологічну надійність, діагностувати стан стиків, та пропонувати заходи щодо вдосконалення властивостей пружної системи верстата.
Інформаційні джерела
1.Демкин Н.Б. Контактирование шероховатых поверхностей. М.: Изд-во «Наука», 1962. – 246 с.
2.Кудинов В.А. Динамика станков. М.: машиностроение, 1967 – 360 с.
3.Рыжов Э.В. Контактная жесткость деталей машин. М.: Машиностроение, 1966. – 163с.
4.Пуш А. В. Шпиндельные узлы. Качество и надежность. М.: Машиностроение, 1992 – 288 с.
УДК 681.31:621.941.236
В.Ю. Денисюк Луцький національний технічний університет
МОДЕЛЮВАННЯ ЗВ’ЯЗКІВ ПАРАМЕТРІВ МІКРОРЕЛЬЄФУ ПОВЕРХНІ З ТЕХНОЛОГІЧНИМИ ЧИННИКАМИ ФОРМОУТВОРЮЮЧИХ ТОКАРНО-АВТОМАТНИХ ОПЕРАЦІЙ
Наведено методику моделювання процедур формоутворення поверхонь для забезпечення характеристик якості деталей, що дозволяє вирішувати серію прикладних задач з розробки і оптимізації технології точіння заготовок типу тіл обертання на токарно-автоматних операціях.
28

ПЕРСПЕКТИВНІ ТЕХНОЛОГІЇ ТА ПРИЛАДИ
Моделирование связей параметров микрорельефа поверхности с технологическими факторами формообразующих токарно-автоматных операций. Приведена методика моделирования процедур формообразования поверхностей для обеспечения характеристик качества деталей, что позволяет решить серию прикладных задач по разработке и оптимизации технологии точения заготовок типа тел вращения на токарно-автоматных операциях.
Modeling parameters relations surface microrelief with technological factors formative on turningautomatic operations. The technique of modeling of procedures form-formation the surface for maintenance performances quality of details represented which allows to decide a series of applied problems for want to development and optimization of technology turning of bars such as a solid of revolution on turningautomatic operations.
Прагнення керувати якістю виробів на стадії проектування технологічних процесів механічної обробки деталей висуває вимогу моделювання процесу формування параметрів якості, у тому числі шорсткості і хвилястості. Найбільшу актуальність здобуває прогнозування параметрів якості на фінішних операціях, оскільки технологічні дефекти надалі виправити не можна [1, 2, 3]. Обробка на токарних верстатах найчастіше стає фінішною операцією, чому сприяє висока точність сучасних верстатів із ЧПК, висока стійкість різального інструменту, методи вибору оптимальних режимів різання, що забезпечують точіння практично без наростоутворення, припіків, вібрацій.
Керування параметрами якості можливо як на стадії проектування технології при підготовці виробництва, так і в процесі безпосереднього керування технологічними процесами й операціями [4]. Аналіз і оптимізація варіантів технології на стадії її проектування важливі, оскільки при цьому скорочуються терміни вибору оптимального варіанту, знижуються витрати на підготовку виробництва нових виробів і спрощуються технічні засоби, що безпосередньо керують металорізальним устаткуванням. Для здійснення прогнозу на стадії підготовки виробництва й автоматичного керування параметрами якості в процесі обробки необхідна побудова математичної моделі формування параметрів якості.
На геометричну точність і мікрорельєф поверхні деталі в процесі механічної обробки впливає велика кількість факторів: швидкість різання v, глибина різання t, подача s, геометрія і ступінь притуплення інструмента, твердість матеріалу деталі, особливості технологічної системи, спрацювання устаткування, точність приладів і методів вимірювання параметрів точності, шорсткості та хвилястості [5, 6, 8].
Дослідження ряду авторів [2, 3, 5, 6] показує, що рівень впливу окремих чинників невеликий і практично не контролюється сучасними вимірювальними приладами. Аналіз значимості технологічних і конструктивних чинників дозволяє для побудови формалізованої моделі процесів встановити рівень їх впливу на точність і мікрорельєф і мінімізувати модель.
Проведені дослідження припускають утворення нерівностей під час точіння в результаті переміщення різця відносно заготовки відповідно до кінематики точіння і коливань в напрямку дії радіальної складової Ру сили різання. При цьому різець переносить профіль своєї вершини в плані на оброблювану заготовку [7].
На рис. 1 показана схема точіння заготовки на одношпиндельному токарному автоматі поздовжнього точіння, до затискної цанги якого прикладена зумовлена її дисбалансом збуджуюча
сила P t P0C0 t , амплітудне значення якої визначається за залежністю [7]:
P M |
|
2 r |
(1) |
0 |
д |
д , |
де Мд – маса дисбалансу, rд – відстань маси дисбалансу від осі обертання, ω – кругова частота обертання цанги.
Для наступних розрахунків використовуємо параметри наведені на рис. 1: а – відстань від місця закріплення заготовки до місця прикладення радіальної складової сили різання; Μц – маса цанги; Μс
– маса супорта; Μ0 та Q0 – згинальний момент та поперечна сила розподіленого навантаження q0 елемента одиничної довжини в довільному перетині на відстані x; C0, C1, C2, C3, C4, C5 – жорсткості різця, затискної цанги, додаткового пристосування, супорта, шпинделя, підшипників. У зв’язку з наявністю нерівномірних переміщень заготовки від вершини різця в процесі точіння буде змінюватися і глибина різання t, а відповідно, і сила Ру. Виходячи з такого представлення, жорсткість
різця: |
|
|
|
C0 Py |
t |
. |
(2) |
|
|
29

ПЕРСПЕКТИВНІ ТЕХНОЛОГІЇ ТА ПРИЛАДИ
Рис. 1. Схема точіння заготовки на дношпиндельному токарному автоматі поздовжнього точіння
За наявності зазначених силових впливів пружне переміщення будь-якої точки заготовки y1
може бути представлене у вигляді: |
|
|
|
|
|
|
|
|
|
|
|
y y K |
x Q K |
x M |
K |
x 2 EI |
|
||||||
1 |
0 |
1 |
|
0 |
2 |
|
|
0 |
3 |
|
|
Q K |
x 3EI P K x a 3 EI cos t, |
(3) |
|||||||||
0 |
4 |
|
|
|
|
0 |
4 |
|
|
|
|
|
|
|
|
|
|
|
|
||||
де Κ1, K2, K3, Κ4 – функції Крилова: |
m 2 |
EI 0,25 |
|
|
|
||||||
|
|
|
|
, m – маса елемента заготовки одиничної |
довжини; І – момент інерції поперечного перерізу заготовки; Е – модуль пружності.
Переміщення вершини різця y2 у напрямку дії сили Ру представлено у вигляді гармонійної
функції часу того ж періоду, що і збуджуюча сила: |
x cos t |
|
|
y2 y2 |
. |
(4) |
|
0 |
|
||
|
|
||
Шукані взаємні переміщення yi заготовки yi1 і вершини різця yi2, що визначають утворені під |
|||
час точіння нерівності поверхні, представляємо як |
|
|
|
yi yi1 |
yi 2 . |
|
(5) |
Мікрорельєф поверхні моделюється накладенням на масив переміщень деталі {yі} профілю вершини інструмента в плані, що представлений на рис. 2.
Послідовність висот нерівностей шорсткої поверхні, що імітує профілограму, утвориться шляхом додавання до обчислених раніше масивів переміщень {yі} масиву нерівностей {hj}, отриманого при накладенні на переміщення yi профілю вершини інструмента в плані, що приблизно описується дугою радіуса rр (рис. 3). Відстань між відгинаннями yi і yi+1 вибирають рівним кроку подачі S для точіння. Розрахунок проводили в такий спосіб: визначали ординати точок U1 і U2, розташованих у середині кроку, і, виходячи з безперервності профілю, вибирали меншу ординату U,
що приймали за hj. З геометричних міркувань: |
|
|
|
|
|
|
|
|
|
|||
hj yi rp |
|
yi S 2 8rp ; h |
|
|
|
|
|
|||||
rp2 S 2 4 |
j 1 |
y |
S 2 8r h |
j min |
; |
|||||||
|
|
|
|
|
|
|
|
i 1 |
p |
|
||
|
h |
y S 2 |
32r h |
|
y |
S 2 32r . |
|
(6) |
||||
|
j 1 |
|
i |
p j |
1 |
|
|
i 1 |
|
p |
|
Рис. 2. Схема створення нерівностей під час точіння, де М-М – траса зняття профілограми; yi і yi+1 – величини взаємних переміщень заготовки та інструмента
30