
3656
.pdf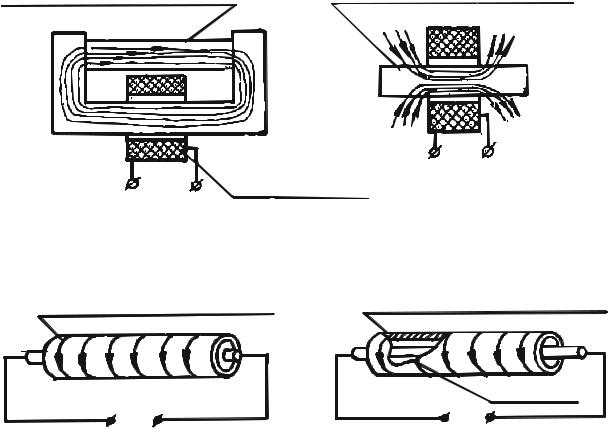
Намагничиваемая деталь |
Намагничиваемая деталь |
|
Соленоид
Электромагнит
Рис. 1. Схемы намагничивания деталей
Намагничиваемая деталь |
Намагничиваемая деталь |
|
Электрод
Рис. 2. Схемы бесполюсного намагничивания
Порядок выполнения работы
Технологический процесс контроля деталей магнитным дефектоскопом состоит из следующих операций.
1)Проверить сопротивление изоляции токоведущих частей дефектоскопа (не менее 2 МОм) и надежность заземления металлических частей дефектоскопа.
2)Проверить качество выявления дефекта по контрольному эталону, имеющему дефект, по четкости проявления трещины судят об исправном действии дефектоскопа и о качестве магнитной смеси.
3)Подготовить деталь к магнитному контролю, т. е. очистить ее до металлического блеска от смазки, пыли, краски, коррозии.
4)Произвести дефектоскопию контролируемой детали и ее размагничивание.
Технологическая оснастка
Для данной работы используются:
-магнитный дефектоскоп типа МД12ПШ;
-мегаомметр типа М1101;
-контрольный эталон;
11
- магнитная смесь – ферромагнитный порошок (мягкая сталь, кузнечная окалина, окись железа в пылевидном состоянии) и органическое масло. На один литр жидкости рекомендуется добавить 200 г мягкой стали или 125–175 г порошка из окиси железа.
Результаты контроля занести в табл. 1.
|
|
Таблица 1 |
|
Результаты контроля |
|
|
|
|
Контролируемая деталь |
Эскиз детали с указанием места |
Браковочный признак |
|
нахождения выявленных дефектов |
|
|
|
|
|
|
|
Заключение. Сделать вывод о пригодности дефектоскопов и дефектных деталей к дальнейшей эксплуатации или восстановлению.
Контрольные вопросы
1.Какие способы намагничивания детали вы знаете? В чем их различие, для отыскания каких трещин они применяются?
2.Какие виды дефектоскопии применяют для контроля состояния деталей? Перечислите достоинства каждого из них.
3.Какие существуют способы намагничивания деталей?
4.В чем заключается подготовка детали к магнитной дефектоскопии?
5.Какой материал используется в качестве искателя дефекта?
ЛАБОРАТОРНАЯ РАБОТА № 3
ИССЛЕДОВАНИЕ РАБОТЫ И РЕГУЛИРОВКА ФОРСУНКИ ДИЗЕЛЯ
Цель работы: ознакомление с технологическим процессом проверки и регулировки собранной форсунки и необходимым для этого оборудованием.
Объект испытания: собранные форсунки тепловозных двигателя типа Д100.
Содержание работы и общие сведения по теме
Установлено, что на качество распыливания и количество топлива, подаваемого форсункой закрытого типа в цилиндр заметное влияние оказывает износ деталей распылителя.
12
Так, например, нарушение притирки между иглой и конусом приводит к ухудшению его распыливания и сгорания и к образованию нагара на поршнях и его кольцах, загоранию отверстий распылителя, а также приводит к подтеканию топлива и, в конечном счете, к перерасходу топлива. Увеличение зазора между иглой и корпусом распылителя сказывается на количестве топлива, поступающего в цилиндр, так как часть его вытекает через этот зазор.
В результате износа конусных контактирующих поверхностей иглы и корпуса распылителя увеличивается подъем иглы. В этом случае игла после отсечки топлива под воздействием пружины садится на место с большой скоростью и быстро разбивает рабочую часть конуса корпуса.
Порядок выполнения работы
Технологический процесс проверки работы и регулировки собранной форсунки состоит из следующих операций.
1)Герметичность стенда проверяют перед постановкой на него форсунки. Для этого сначала насосом прокачивают топливо, чтобы удалить воздух из трубок, а затем между конусным штуцером и винтом стойки зажимают заглушку. Когда давление топлива в системе стенда достигает 400 кг/см2, подкачку топлива насосом прекращают. После этого в течение 5 мин наблюдают за показаниями манометра стенда. Если за это время давление понизится с 400 до 350 кг/см2, герметичность стенда считается достаточной. Эту операцию повторяют дважды. За действительную герметичность стенда принимают среднеарифметическую величину двух испытаний.
2)Для контроля герметичности запорного конуса-распылителя форсунку ставят на стенд, отворачивают болт (чтобы ослабить пружину форсунки) и делают несколько впрысков топлива для удаления воздуха из системы подкачки. Постепенно зажимая пружину форсунки и подкачивая насосом топливо создают давление 400 кг/см2. Такое давление поддерживают в течение 1–2 минут, периодически подкачивая топливо насосом. Если за это время на кончике распылителя не появится капля топлива, то качество притирки иглы к корпусу распылителя считается удовлетворительным. Проверку повторяют дважды.
3)О величине износа цилиндрической части иглы и отверстия распылителя косвенно судят по гидравлической плотности распылителя, измеряемой в секундах. За гидравлическую плотность распылителя условно принято считать время падения давления в системе стенда на 50 кг/см2 от принятого начального давления. Гидравлическая плотность распылителя определяется следующим образом. Ослабив затяжку пружины форсунки, делают несколько впрысков топлива. Затем увеличивают затяжку пружины форсунки, пока давление в системе стенда не достигнет 400 кг/см2. После этого подкачку топлива прекращают и следят за понижением его давления. По секундомеру засекают время, в течение которого давление топлива в системе стенда
13
понизится с 330 до 280 кг/см2 (при проверке форсунки дизеля типа Д100). Эта операция повторяется дважды. Среднеарифметическое двух измерений принимается за действительную гидравлическую плотность распылителя контролируемой форсунки.
4)Затяжку пружины форсунки (или давление начала подъема иглы) регулируют поворотом регулировочного болта (или пробки) таким образом, чтобы при медленном нажатии на рычаг стенда впрыск топлива произошел (игла начала подниматься) при давлении 210+5 кг/ см2 (для форсунки дизеля типа Д100).
5)Качество распыливания и отсечки топлива форсункой контролируют визуально. Для этого в минуту делают примерно 30 равномерных впрысков топлива. Нормально работающая форсунка впрыскивает топливо в туманнообразном виде, длина и форма струй из всех ее впрыскивающих отверстий одинакова. Начало и конец каждого впрыска сопровождается четким и резким звуком, факел топлива как бы отсекается от распылителя. Кроме того, после каждых 4–6 впрысков на кончике распылителя форсунки не должна появляться капля топлива. Подтекание топлива в виде капель или «подвпрысков» слабых струй указывает на неудовлетворительное распыливание и плохую отсечку топлива форсункой.
Наглядным признаком правильной сборки форсунки служит так называемый «дробящий впрыск», т. е. частые, следующие один за другим впрыски топлива, возникающие при медленном опускании рычага стенда.
Технологическая оснастка
Работу форсунок проверяют на стенде типа А106.02 для испытания форсунок. Стенд типа А106.02, принципиальная схема которого показана на рис. 1,
представляет собой сварной стол, верх которого покрыт дюралюминиевым листом. На столе смонтированы топливный бак с указанием уровня топлива, насос высокого давления с ручным приводом и стойка с зажимом для монтажа контролируемой форсунки.
Топливо из бака 1 через отстойник 7 и фильтр вторичной (тонкой) очистки 2 поступает в насос высокого давления 6. При прокачке насоса рычагом топливо нагнетается в коллектор 3, откуда по трубке и зажиму поступает к форсунке 4. Коллектор служит одновременно для закрепления манометра и спуска топлива из системы стенда.
Топливо, распыленное форсункой, улавливается сборником 5, верхняя часть которого, выполненная из прозрачного органического стекла, может перемещаться в вертикальном положении.
Стенд универсальный, на нем можно проверять форсунки дизелей типов Д100, Д50, М750 и Д6. В бак стенда заливают чистое отфильтрованное дизельное топливо.
14

К вентиляционной системе
Рис. 1. Принципиальная схема стенда А106.02 для проверки работы форсунки
Результаты испытаний
Все полученные при проверке герметичности запорного конуса, гидравлической плотности распылителя, затяжки пружины форсунки, качества распылителя и отсечки топлива и другие данные фиксируются в карте контроля (табл. 1), в которой также указываются допуски на испытания, установленные Правилами ремонта тепловоза.
Таблица 1
Результаты испытаний
Заключение. Действительная величина гидравлической плотности распылителя, качество распыливания и отсечки топлива и другие данные сравниваются с установленными Правилами ремонта тепловозов. После этого дается заключение о состоянии контролируемой форсунки. При необходимости приводятся рекомендации по регулировке параметров, выходящих за пределы допусков.
15
Контрольные вопросы
1.Перечислите основные неисправности форсунок. Что оказывает влияние на качество и количество подаваемого топлива форсункой?
2.Каковы основные контролируемые параметры форсунки?
3.В каких случаях форсунки снимают с дизеля для проверки качества распыливания топлива и регулирования затяжки пружины?
4.По каким основным причинам происходит подтекание или плохое качество распыливания топлива форсункой?
5.Состояние каких поверхностей оценивают при проверке герметичности запорного конуса?
6.Состояние каких поверхностей оценивают при проверке гидравлической плотности распылителя?
7.Как влияет на рабочий процесс ДВС качество распыления топлива?
8.Как влияет на величину плотности распылителя температура топлива?
ЛАБОРАТОРНАЯ РАБОТА № 4
ИСПЫТАНИЯ ЭЛЕКТРОПНЕВМАТИЧЕСКИХ АППАРАТОВ ТЕПЛОВОЗОВ
Цель работы: ознакомление с технологическим процессом испытания электропневматических аппаратов и необходимым для этого оборудованием.
Объект испытания: электропневматические вентили, контакторы.
Содержание работы и общие сведения по теме
Впроцессе эксплуатации тепловозов встречаются такие неисправности электрических аппаратов, как подгар, оплавление контактов и медных шунтов, повреждения катушек, пропуск воздуха электропневматическими вентилями и пневматическими цилиндрами. Подгар и оплавление контактов вызываются плохим прилеганием, чрезмерным их износом и недостаточным нажатием, неисправностью подвижной системы, дугогасительных катушек и скоплением грязи на контактных поверхностях.
При проверке аппаратов производят внешний осмотр и проверку механических и электрических параметров.
При внешнем осмотре выявляют степень изношенности деталей, состояние изоляционных и декоративных покрытий, выводных зажимов и крепежа. Проверка механических параметров содержит: измерение силы нажатия контактов и величины провала, определение надежности механического привода, испытание герметичности манжет и клапанов.
Впроверку электрических параметров входит: измерение сопротивления катушек, тока срабатывания и отпуска, проверка настройки, сопротивления изоляции.
Электрические испытания аппаратов производят на специальных стендах.
16
Порядок выполнения работы
Технологический процесс испытания электропневматических аппаратов тепловозов состоит из следующих операций.
1.Для испытания электропневматических вентилей необходимо: а) открыть кран КР1;
б) открыть крышку на столе стенда и установить в колодку(стойку)
пневмозажима гнездо в соответствии с типом испытуемого вентиля; в) в гнездо установить испытуемый вентиль, предварительно подключив
соответствующим жгутом его катушку к розетке Х1 (катушка). Далее, придерживая вентиль, включить тумблер 51 «Сеть», при этом загорится сигнальная лампа Н1 «Сеть», а затем включить тумблер 53 «Прижим»;
г) включить тумблер 52 «Включение аппарата» и маховичком автотрансформатора Т1 «Регул. напряжение» установить требуемое напряжение по вольтметру РУ1 «Напряжение»;
д) отключить тумблер 52 «Включение аппарата»; е) при давлении в воздушной магистрали 1,0 МПа (по манометру МН1
отрегулировать давление после открытия крана КР4 «Магистраль стенда» по манометру МН2 «Замер падения давления» на 0,5 МПа (5 кгс/см2). Открыть кран КР2 «Испытание вентиля», и, включив тумблер 32 «Включение аппарата», произвести испытания вентиля
сконтролем давления по манометру МН2 «Замер падения давления».
2.Для проверки вентиля на герметичность (на утечку) предварительно необходимо проверить давление по манометру МН1, затем открыть кран КР4 «Магистраль стенда» далее отрегулировать давление регулятором РД с контролем по манометру МН2, затем включить тумблер 82 «Включение аппарата» и кран КР2 «Испытание вентиля». Контролировать утечку по манометру МН2 «Замер падения давления» с выдержкой определенного времени.
3.Испытание вентилей производить согласно технологических инструкций на их ремонт ( ТИ258 и др.) или в соответствии с ГОСТ 9219-88.
4.Для проведения испытания контактора необходимо:
а) установить контактор на скобы с левой стороны стенда; б) подключить катушку вентиля контактора соответствующим жгутом к
розетке Х1 «Катушка», а вторым жгутом (при необходимости) подключить блокконтакты к розетке Х2 «Блок-контакты»;
в) подключить вентиль контактора к воздушной сети стенда соответствующим шлангом;
г) далее все операции по проведению испытаний контактора проводятся аналогично испытаниям вентиля, имея ввиду, что следует открывать кран КРЗ «Испытания контакторов» вместо крана КР2.
17

5. Испытания реверсора, клапана песочницы и т. п. проводятся аналогично испытаниям контактора, при этом учесть, что реверсор устанавливать рядом со стендом, а клапан песочницы – на столе стенда на специальных подставках, изготовленных по местным условиям.
Технологическая оснастка
Для проведения данной работы применяют стенд типа А2238.
Стенд типа А2238 позволяет проводить испытания электропневматических аппаратов (электропневматических вентилей, клапанов, реверсоров, контакторов), позволяющих определить неисправность и качество проведенного ремонта. Стенд позволяет проводить испытания в соответствии с требованиями ГОСТ 9219-88 и технологической инструкции ТИ258. Стенд представляет собой металлический каркас сварной конструкции, на передней вертикальной панели которого расположены основные аппараты управления и контроля, а также три крана, необходимые для проведения испытаний электропневматических вентилей или электропневматических контакторов (аппаратов).
Принципиальная схема стенда представлена на рис. 1.
Рис. 4.1. Принципиальная пневматическая схема стенда для испытания электропневматических аппаратов тепловозов
18

На столе находится регулятор давления, которым устанавливают требуемое давление воздуха при испытании аппарата. Под крышкой стола находится пневмозажим, в который через сменные гнезда устанавливают испытуемые электропневматические вентили. Сменные гнезда предусмотрены для установки вентилей следующих типов: ВВ-1, ВВ-2 (ВВ-2А), ВВ-3, ВВ-32, ВВ-1313 (ВВ-1415, ВВ-1715), EV-51 (тепловозов ЧМЭ2 и ЧМЭ3). При необходимости испытаний вентилей других типов гнезда изготовить по местным условиям.
На передней вертикальной панели установлены аппараты и приборы, назначение и характеристики которых приведены в табл. 1.
Таблица 1
Назначение и характеристика приборов и аппаратов, входящих в конструкцию стенда типа А2238
Обозначение |
Наименование, тип и основные |
Функциональное назначение |
|
параметры |
|||
|
|
||
|
|
|
|
Н1 |
Лампа (зеленая) «Сеть» |
Сигнализация о включении стенда к сети 220В |
|
|
|
|
|
Н3,Н4 |
Лампы (белые) «Контакт 1», «Контакт 2» |
Сигнализация о срабатывании блок-контактов |
|
|
|
|
|
РА1 |
Амперметр М42100 кл.1,5 0-1 А «Ток» |
Контроль тока срабатывания аппарата |
|
|
|
|
|
РА1 |
Вольтметр М42100 кл.1,5 0-150 А «Ток» |
Контроль напряжения испытуемого аппарата |
|
|
|
|
|
S1 |
Тумблер ТВ1-2 «Сеть» |
Включение стенда в сеть |
|
|
|
|
|
S2 |
Тумблер ТВ1-1 «Включение аппарата» |
Включение цепи испытания аппарата |
|
|
|
|
|
S3 |
Тумблер ТВ1-1 «Прижим» |
Включение вентиля пневмозажима |
|
|
|
|
|
F1 |
Предохранитель (2А) |
Сетевой предохранитель стенда |
|
|
|
|
|
F2 |
Предохранитель (2А) |
Защита цепи испытуемых аппаратов |
|
|
|
|
|
T1 |
Автотрансформатор АОСН-2-220-82 |
Регулировка напряжения испытуемого |
|
|
«Регулировка напряжения» |
аппарата |
|
|
|
|
|
X1 |
Розетка ШР20П4ЭГ8 |
Розетка для подключения жгута к катушке |
|
|
«Катушка» |
испытуемого аппарата |
|
|
|
|
|
X2 |
Розетка ШР20П4ЭГ8 |
Розетка для подключения жгута к блок- |
|
|
|
контактам испытуемого аппарата |
|
|
|
|
|
МН1 |
Манометр МТП-3-1 МРа-2,5 |
Давление на входе |
|
|
|
|
|
МН2 |
Манометр МП4-У кл.1,51 МПа |
Замер падения давления испытуемого |
|
|
|
аппарата |
|
|
|
|
|
МН3 |
Манометр МТП-3-1 МРа-2,5 |
Давление испытуемого аппарата |
|
|
«Срабатывание аппарата» |
|
|
|
|
|
|
МН4 |
Манометр МП -0,5 МПа |
Давление в цилиндре фиксации испытуемого |
|
|
|
аппарата |
|
|
|
|
Результаты испытаний. Контролю подвергаются 3–4 типа электропневматических аппарата, бывшие в эксплуатации. Все полученные при проверке значения контролируемых параметров (ток срабатывания, напряжение, давление) фиксируются в табл. 1, в которой также указывают допуски на испытания, установленные Правилами ремонта тепловоза.
19
|
|
|
|
Таблица 2 |
|
|
Контролируемые параметры электропневматических аппаратов |
||||
|
|
|
|
|
|
Тип |
Ток |
Напряжение |
Давление |
Проверка длины |
|
испытуемого |
|
||||
электрического |
срабатывания |
испытуемого |
стержня впускного |
|
|
аппарата, МПа |
|
||||
аппарата |
аппарата, А |
аппарата, В |
клапана, мм |
|
|
(кгс/см2) |
|
||||
|
|
|
|
|
|
ВВ-32 |
|
|
|
|
|
|
|
|
|
|
|
ПК-753Б |
|
|
|
|
|
|
|
|
|
|
|
Допуск |
|
|
|
|
|
|
|
|
|
|
|
Заключение. Найденные действительные величины контролируемых параметров электропневматических аппаратов сравнить с установленными Правилами ремонта тепловозов. После чего сделать заключение о состоянии контролируемого электропневматического аппарата.
Контрольные вопросы
1.Каковы основные неисправности электрических аппаратов? Перечислите способы определения и устранения повреждений.
2.Какие бывают типы электрических контактов, и каковы их основные параметры?
3.Какие существуют приводы электрических аппаратов?
4.Какие реле применяют на тепловозах? Каковы их функции? Какие могут возникнуть неисправности и способы их устранения?
ЛАБОРАТОРНАЯ РАБОТА № 5
МОБИЛЬНЫЙ ПРИБОР ДИАГНОСТИКИ ЭЛЕКТРИЧЕСКИХ МАШИН И АППАРАТОВ «ДОКТОР-060Z»
Цель работы: ознакомление с применяемым на ремонтных заводах и в депо мобильным прибором диагностики электрических машин и аппаратов «ДОКТОР-060Z»
Объект испытания: электрические машины и аппараты.
Содержание работы и общие сведения по теме
Мобильный прибор диагностики электрических машин и аппаратов «Доктор-060Z» (далее прибор) предназначен для контроля параметров выявления дефектов обмоток тяговых электродвигателей и другого электрооборудования тягового подвижного состава железнодорожного транспорта.
20